|
(21), (22) Заявка: 2005139438/03, 19.12.2005
(24) Дата начала отсчета срока действия патента:
19.12.2005
(43) Дата публикации заявки: 27.06.2007
(46) Опубликовано: 27.11.2007
(56) Список документов, цитированных в отчете о поиске:
RU 2261923 C1, 10.10.2005. SU 1458005 A1, 15.02.1989. SU 1225495 A3, 15.04.1986. RU 2175022 C1, 20.10.2001. RU 97111630 A, 27.05.1999. RU 2131780 C1, 20.06.1999. RU 2097565 С1, 27.11.1997. US 1710522 A, 23.04.1929. US 1951341 A, 20.03.1934. ФОМИН Я.И., “Технология обогащения марганцевых руд”, Москва, “Недра”, 1981, с.13-16, 60-61, 232-237.
Адрес для переписки:
119017, Москва, Старомонетный пер., 31, ФГУП ВИМС, патентная лаб.
|
(72) Автор(ы):
Иванков Сергей Иванович (RU), Кушпаренко Юрий Сергеевич (RU), Любимова Елена Ивановна (RU), Жосан Владимир Анатольевич (RU), Голева Рита Владимировна (RU), Мельников Михаил Евгеньевич (RU), Юбко Валерий Михайлович (RU)
(73) Патентообладатель(и):
Федеральное государственное унитарное предприятие “Всероссийский научно-исследовательский институт минерального сырья им. Н.М.Федоровского (ФГУП ВИМС) (RU)
|
(54) СПОСОБ ПЕРЕРАБОТКИ КОБАЛЬТОНОСНЫХ ЖЕЛЕЗО-МАРГАНЦЕВЫХ ОКЕАНИЧЕСКИХ ОБРАЗОВАНИЙ (ЕГО ВАРИАНТЫ)
(57) Реферат:
Изобретение относится к области обогащения полезных ископаемых и может быть использовано при переработки кобальтоносных железо-марганцевых океанических образований (корок и конкреций), добываемых со дна мирового океана и содержащих помимо марганца, кобальта и железа также никель, медь, благородные и редкие металлы. Способ переработки кобальтоносных железо-марганцевых океанических образований включает дробление, измельчение, классификацию и последующие выделения марганца и цветных металлов. По первому варианту способа после классификации из фракции -0,5+0,074 мм осуществляют выделение марганца и цветных металлов гравитационным обогащением на концентрационном столе, с последующей трехстадийной магнитной сепарацией легкой фракции концентрационного стола. При этом напряженность магнитного поля сепаратора на первой стадии составляет от 3500 до 4000 эрстед, на второй от 6500 до 7200 эрстед и на третьей от 8000 до 8200 эрстед, причем марганец и цветные металлы извлекают в магнитную фракцию третьей стадии. По второму варианту способа классификацию осуществляют на фракции -12+0,5 и -0,5+0,074 мм, а выделение марганца и цветных металлов осуществляют из полученных фракций гравитационным обогащением на отсадочных машинах из фракции -12+0,5 мм и на концентрационных столах из фракции -0,5+0,074 мм. При этом марганец и цветные металлы извлекают в легкие фракции гравитационного обогащения, которые направляют на химико-металлургическую доводку. Процесс переработки по обоим вариантам способа осуществляют в модуле на дне океана. Технический результат – повышение извлечения в коллективный концентрат марганца, кобальта, никеля и меди, снижение экологической напряженности дна Мирового океана, сокращение объема материала, поднимаемого со дна океана. 2 н.п. ф-лы, 2 ил., 2 табл.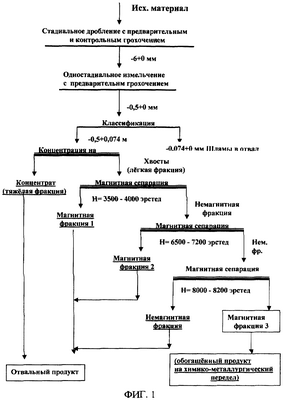
(56) (продолжение):
CLASS=”b560m”Справочник по обогащению руд черных металлов/Под ред. ШИНКОРЕНКО С.Ф, Москва, “Недра”, 1980, с.338-340.
Изобретение относится к области обогащения полезных ископаемых и может быть использовано при переработке кобальтоносных железо-марганцевых океанических образований, добываемых со дна мирового океана и содержащих помимо марганца, кобальта и железа также никель, медь, благородные и редкие металлы. Среди полезных ископаемых океана кобальтоносные железо-марганцевые корковые образования (КЖМК) представляют собой самостоятельный промышленный рудный тип, имеющий огромное экономическое и политическое значение.
Известен способ переработки образований (КЖМК), включающий измельчение, восстановительный обжиг и гидрометаллургическую переработку сырья с получением марганца, кобальта и никеля (см. «Геология и минеральные ресурсы мирового океана, Интерморгео, Варшава, 1990, стр.646-648»). Недостатком этого способа являются значительные энергетические затраты на обжиг и сушку исходного измельченного материала, а также необходимость переработки 100% массы материала по химико-металлургической технологии.
Наиболее близким по технической сущности и достигаемому результату к описываемым изобретениям является способ переработки кобальтоносных железо-марганцевых океанических образований, включающий дробление, измельчение, классификацию и последующие выделения марганца и цветных металлов (см. Патент России №2261923, кл. С22В 3/08 от 31.05.2004 г.).
К недостаткам известного способа следует отнести невысокие технологические показатели процесса и необходимость вовлечения в переработку всей массы исходного материала.
Технической задачей изобретений является создание технологии переработки кобальтоносных железо-марганцевых океанических образований на основе предварительного глубокого обогащения с получением коллективного концентрата для последующего химико-технологического процесса при снижении его массы в 2,5-3 раза.
Поставленная техническая задача решается таким образом, что в способе переработки кобальтоносных железо-марганцевых океанических образований по I варианту, включающем дробление, измельчение, классификацию и последующие выделения марганца и цветных металлов, последнее осуществляют предварительным гравитационным обогащением на концентрационном столе из фракции -0,5+0,074 мм с последующей трехстадийной магнитной сепарацией легкой фракции концентрационного стола, при этом напряженность магнитного поля сепаратора на первой стадии составляет от 3500 до 4000 эрстед, на второй – от 6500 до 7200 эрстед и на третьей – от 8000 до 8200 эрстед, а марганец и цветные металлы извлекают в магнитную фракцию третьей стадии.
В способе переработки кобальтоносных железо-марганцевых океанических образований по II варианту, включающем дробление, измельчение, классификацию и последующее выделение марганца и цветных металлов, последнее осуществляют предварительным гравитационным обогащением на отсадочных машинах из фракции -12+0,5 мм и на концентрационных столах из фракции -0,5+0,074 мм, при этом марганец и цветные металлы извлекают в легкие фракции гравитационного обогащения, которые направляют на химико-металлургическую доводку.
Процесс переработки по I и II вариантам проводят в модуле на дне океана.
Сущность изобретения заключается в следующем:
После операции дробления, измельчения и классификации каждый класс крупности исходного материала поступает на гравитационное обогащение с использованием процесса концентрации на столе КЦ-30 с перечисткой концентратов и контрольным обогащением хвостов. При этом в тяжелую фракцию переходят минералы субстрата, а в легкую (хвосты стола) фракцию минералы с повышенным содержанием марганца и цветных металлов.
Результаты гравитационного обогащения классифицированного материала на концентрационном столе позволяют сделать следующие выводы:
– извлечение марганца (и соответственно цветных металлов) в легкую фракцию концентрационного стола, направляемую на магнитную сепарацию, при обогащении всех трех классов высокое (78-81%), однако с понижением тонины помола степень концентрации ценных компонентов снижается с 20 до 11%;
– при обогащении крупных классов (0,5+0,3 мм.) и (-0,3+0,15 мм) обогащенный марганцем (и соответственно кобальтом и др. цветными металлами) продукт (конечные хвосты концентрационного стола) практически в два раза богаче исходного при содержании железа на уровне исходного;
– при обогащении мелкого класса (-0,15+0,044 мм) наблюдается лишь незначительное повышение содержания марганца в легкой фракции концентрационного стола на 3-4% по сравнению с исходным материалом;
– при разработке принципиальной схемы обогащения исходного материала рекомендуется на концентрационный стол направлять более широкий по крупности класс -0,5+0,074 мм.
Последующий процесс магнитной сепарации осуществляется в пределах напряженности магнитного поля от 3500 до 8200 эрстед в три стадии. При проведении исследований на каждом классе крупности было уставлено, что в немагнитную фракцию выделяются легкие минералы фазы субстрата, а сильно магнитную фракцию (от 3500 до 5000 эрстед) – железистые образования с пониженным содержанием марганца и цветных металлов, в слабомагнитную фракцию (от 7200 до 8200 эрстед) – более богатый марганцем и цветными металлами продукт.
Анализ результатов трехстадийной магнитной сепарации обогащенных продуктов концентрационного стола (по классам крупности) позволяет установить следующее:
– в диапазоне напряженности магнитного поля сепаратора от 3500 до 5500 эрстед из всех трех классов крупности удалось выделить отвальные по марганцу и цветным металлом хвосты, содержащие от 3,2 до 5,4% марганца (магнитная фракция) с низкими потерями в них ценных компонентов (0,7-2,0% от руды);
– немагнитные фракции от всех классов крупности представляют собой отвальные хвосты с содержанием марганца от 1,5 до 3,0%, с потерями в них ценных компонентов (0,1 до 0,5% от руды);
– в диапазоне напряженности магнитного сепаратора от 5500 до 7200 эрстед из класса -0,5+0,3 мм выделен промежуточный марганцевый продукт с содержанием 10,6% марганца и цветным металлам 1,5% (от руды);
– в диапазоне напряженности магнитного сепаратора от 7200 до 8200 эрстед выделен наиболее богатый по марганцу и цветным металлампродукт (слабомагнитная фракция) с содержанием марганца в среднем 20% и кобальта 0,53% при извлечении 65-70% от руды, соответственно направляемой на химико-металлургическую переработку.
В результате проведенных исследований было установлено, при определенном минеральном составе океанических корковых образований (отсутствие слабомагнитных марганцевых минералов) выделение марганца и цветных металлов осуществляют из фракции -12+0,5 мм гравитационным обогащением на отсадочных машинах, а из фракции -0,5+0,074 мм – на концентрационных столах, при этом марганец и цветные металлы извлекают в легкие фракции гравитационного обогащения (II вариант).
С целью сокращения в 3,5-4,0 раза объема поднимаемого со дна океана и обогащенного материала, содержащего марганец и цветные металлы для последующего химико-металлургического процесса, а также снижения экологической напряженности дна Мирового океана переработку исходного материала по обоим вариантам осуществляют в модуле на дне океана.
Пример конкретной реализации изобретения поясняется со ссылкой на графический материал, где на фиг.1 изображена схема и основные параметры процессов переработки кобальтоносных железомарганцевых океанических образований (вариант I).
Исследования производились на представительной пробе содержащей 10,5% марганца, 0,27% кобальта, 0,24% никеля и 0,08% меди. После операций дробления, измельчения и классификации фракция -0,5+0,074 мм поступала на предварительное гравитационное обогащение с использованием концентрационного стола. Легкая фракция концентрационного стола поступала на трехстадиальную магнитную сепарацию, при этом напряженность магнитного поля на первой стадии составляла 3500-4000 эрстед, на второй – 6500-7200 эрстед и на третьей – 8000-8200 эрстед. В результате трехстадиальной магнитной сепарации марганец и цветные металлы извлекают в магнитную фракцию на третьей стадии.
В табл.1 приведены данные, подтверждающие обоснованность описываемого изобретения – способа переработки кобальтоносных железомарганцевых океанических образований (по первому варианту) в сравнении с аналогом и прототипом (опыты 1 и 2). Анализ полученных результатов показывает, что только при оптимальных условиях описываемого способа (опыты 3, 4, 5) достигается высокое извлечение в коллективный концентрат марганца (63-67%), кобальта (63-69%), никеля (77-90%) и меди (56-61%) при минимальном его выходе 30-35% (по массе), поступающем на химико-металлургическую доводку до товарных продуктов. При выходе за нижние пределы оптимальных значений (опыт 6 и 9) технологические показатели значительно снижаются, а при выходе за верхние пределы (опыты 7 и 8 ) практически не изменяются.
По второму варианту пример конкретной реализации изобретения поясняется со ссылкой на чертежи, где на фиг.2 изображена схема переработки кобальтоносных железо-марганцевых океанических образований (на той же пробе, что и по первому варианту). После операций дробления, измельчения и классификации фракция -12+0,5 мм направлялись на гравитационное обогащения методом отсадки, а фракция -0,5+0,074 мм на концентрационный стол. В результате проведения процесса обогащения марганец и цветные металлы извлекают в легкие фракции гравитационных методов.
В табл.2 приведены данные, подтверждающие обоснованность описываемого изобретения – способа переработки кобальтоносных железо-марганцевых океанических образований (по второму варианту) в сравнении с аналогом и прототипом (опыты 1 и 2). Анализ полученных результатов показывает, что только при оптимальных условиях описываемого способа (опыты 3) достигается высокое извлечение в коллективный концентрат марганца (63,8%), кобальта (66,0%),никеля (86,6%) и меди (57,7%) при минимальном его выходе 33% (по массе), поступающем на химико-металлургическую доводку до товарных продуктов.
Таким образом, использование описываемого изобретения решает проблему комплексной переработки кобальтоносных железо-марганцевых океанических образований за счет высокого извлечения марганца, кобальта, никеля и меди в коллективный концентрат, поступающий на химико-металлургическую переработку до товарных продуктов, при одновременном снижении его выхода (по массе) до 30-35%
Таблица 1 Сравнительные результаты переработки кобальтоносных железо-марганцевых океанических образований по аналогу, прототипу и изобретению (вариант 1) |
Опыт №1 |
Продукты переработки |
выход |
Содержание |
Извлечение |
Условия опыта |
Mn |
Co |
Ni |
Cu |
Mn |
Со |
Ni |
Cu |
Концентрат обогащения на металлургический передел |
80,0 |
12,0 |
0,29 |
0,26 |
0,19 |
95,5 |
85,9 |
86,7 |
90,0 |
По способу аналога |
Хвосты |
20,0 |
2,25 |
0,19 |
0,16 |
0,04 |
4,5 |
14,1 |
13,3 |
10,0 |
Шламы |
0 |
0 |
0 |
0 |
0 |
0 |
0 |
0 |
0 |
Исходный материал |
100,0 |
10,5 |
0,27 |
0,24 |
0,08 |
100,0 |
100,0 |
100,0 |
100,0 |
Опыт №2 |
Продукты переработки |
выход |
Содержание |
Извлечение |
Условия опыта |
Mn |
Co |
Ni |
Cu |
Mn |
Со |
Ni |
Cu |
Концентрат обогащения на металлургический передел |
64,0 |
14,0 |
0,32 |
0,29 |
0,1 |
85,3 |
75,9 |
77,3 |
80,0 |
По способу прототипа |
Хвосты |
19,0 |
5,7 |
0,25 |
0,20 |
0,05 |
4,3 |
6,7 |
6,5 |
7,0 |
Шламы |
7,0 |
6,5 |
0,26 |
0,24 |
0,08 |
10,4 |
17,4 |
16,2 |
13,0 |
Исходный материал |
100,0 |
10,5 |
0,27 |
0,24 |
0,08 |
100,0 |
100,0 |
100,0 |
100,0 |
Опыт №3 |
Продукты переработки |
выход |
Содержание |
Извлечение |
Условия опыта |
Mn |
Co |
Ni |
Cu |
Mn |
Со |
Ni |
Cu |
Концентрат обогащения на металлургический передел |
33,0 |
20,0 |
0,56 |
0,61 |
0,15 |
62,9 |
68,4 |
84,0 |
61,9 |
По предложенному способу Фракция -0,5+0,044 На первой стадии 3500 эрстед На второй стадии 6500 эрстед На третьей стадии 8000 эрстед |
Хвосты |
37,0 |
4,6 |
0,10 |
0,02 |
0,02 |
16,2 |
13,8 |
14,7 |
8,1 |
Шламы |
30,0 |
7,3 |
0,16 |
0,10 |
0,08 |
20,9 |
17,8 |
1,3 |
30,0 |
Исходный материал |
100,0 |
10,5 |
0,27 |
0,24 |
0,08 |
100,0 |
100,0 |
100,0 |
100,0 |
Продолжение таблицы 1 |
Опыт №4 |
Продукты переработки |
выход |
Содержание |
Извлечение |
Условия опыта |
Mn |
Co |
Ni |
Cu |
Mn |
Со |
Ni |
Cu |
Концентрат обогащения на металлургический передел |
35 |
19,6 |
0,53 |
0,62 |
0,13 |
66,1 |
68,7 |
90,4 |
56,88 |
По предложенному способу Фракция -0,5+0,044 На первой стадии 3800 эрстед На второй стации 6800 эрстед На третьей стадии 8100 эрстед |
Хвосты |
38 |
4,2 |
0,09 |
0,05 |
0,04 |
15,1 |
12,6 |
7,91 |
19,0 |
Шламы |
27 |
7,8 |
0,19 |
0,18 |
0,08 |
18,8 |
18,7 |
1,69 |
24,125 |
Исходный материал |
100,0 |
10,5 |
0,27 |
0,24 |
0,08 |
100,0 |
100,0 |
100,0 |
100,0 |
Опыт №5 |
Продукты переработки |
выход |
Содержание |
Извлечение |
Условия опыта |
Mn |
Co |
Ni |
Cu |
Mn |
Со |
Ni |
Cu |
Концентрат обогащения на металлургический передел |
31,0 |
22,7 |
0,55 |
0,63 |
0,14 |
67,0 |
63,1 |
81,4 |
54,2 |
По предложенному способу Фракция -0,5+0,044 На первой стадии 4000 эрстед На второй стадии 7200 эрстед На третьей стадии 8200эрстед |
Хвосты |
40,0 |
4,0 |
0,15 |
0,02 |
0,03 |
15,2 |
21,9 |
4,1 |
16,8 |
Шламы |
29,0 |
6,4 |
0,14 |
0,12 |
0,08 |
17,8 |
15,0 |
14,5 |
29,0 |
Исходный материал |
100,0 |
10,5 |
0,27 |
0,24 |
0,08 |
100,0 |
100,0 |
100,0 |
100,0 |
Опыт №6 |
Продукты переработки |
выход |
Содержание |
Извлечение |
Условия опыта |
Mn |
Co |
Ni |
Cu |
Mn |
Со |
Ni |
Cu |
Концентрат обогащения на металлургический передел |
40,0 |
16,4 |
0,45 |
0,53 |
0,11 |
62,5 |
66,7 |
88,3 |
55,0 |
По предложенному способу Фракция -0,5+0,044 На первой стадии 3400 эрстед На второй стадии 6400 эрстед На третьей стадии 7900 эрстед |
Хвосты |
38,0 |
6,0 |
0,16 |
0,02 |
0,05 |
21,6 |
22,7 |
2,5 |
23,0 |
Шламы |
22,0 |
7,6 |
0,13 |
0,10 |
0,08 |
15,9 |
10,6 |
9,2 |
22,0 |
Исходный материал |
100,0 |
10,5 |
0,27 |
0,24 |
0,08 |
100,0 |
100,0 |
100,0 |
100,0 |
Продолжение таблицы 1 |
Опыт №7 |
Продукты переработки |
выход |
Содержание |
Извлечение |
Условия опыта |
Mn |
Co |
Ni |
Cu |
Mn |
Со |
Ni |
Cu |
Концентрат обогащения на металлургический передел |
32,0 |
19,8 |
0,51 |
0,58 |
0,13 |
60,3 |
60,4 |
77,3 |
52,0 |
По предложенному способу Фракция -0,5+0,044 На первой стадии 4100 эрстед На второй стадии 7300 эрстед На третьей стадии 8300 эрстед |
Хвосты |
37,0 |
4,4 |
0,14 |
0,03 |
0,04 |
15,5 |
18,9 |
4,6 |
17,0 |
Шламы |
31,0 |
8,2 |
0,18 |
0,14 |
0,08 |
24,2 |
20,7 |
18,1 |
31,0 |
Исходный материал |
100,0 |
10,5 |
0,27 |
0,24 |
0,08 |
100,0 |
100,0 |
100,0 |
100,0 |
Опыт №8 |
Продукты переработки |
выход |
Содержание |
Извлечение |
Условия опыта |
Mn |
Co |
Ni |
Cu |
Mn |
Со |
Ni |
Cu |
Концентрат обогащения на металлургический передел |
39,0 |
17,0 |
0,49 |
0,60 |
0,12 |
64,6 |
70,8 |
|
58,5 |
По предложенному способу Фракция -0,6+0,05 На первой стадии 3800 эрстед На второй стадии 6800 эрстед На третьей стадии 8100 эрстед |
Хвосты |
37,0 |
5,2 |
0.12 |
0,53 |
0,04 |
18,5 |
16,8 |
|
17,5 |
Шламы |
24,0 |
7,4 |
0,14 |
0,11 |
0,08 |
16,9 |
12,4 |
|
24,0 |
Исходный материал |
100,0 |
10,5 |
0,27 |
0,24 |
0,08 |
100,0 |
100,0 |
100,0 |
100,0 |
Опыт №9 |
Продукты переработки |
выход |
Содержание |
Извлечение |
Условия опыта |
Mn |
Co |
Ni |
Cu |
Mn |
Со |
Ni |
Cu |
Концентрат обогащения на металлургический передел |
33,0 |
18,8 |
0,50 |
0,61 |
0,12 |
59,1 |
61,1 |
83,9 |
49,5 |
По предложенному способу Фракция 10,4-+0,035 На первой стадии 3800 эрстед На второй стадии 6800 эрстед На третьей стадии 8100 эрстед |
Хвосты |
36,0 |
5,6 |
0,18 |
0,01 |
0,04 |
19,4 |
24,0 |
1,9 |
19,5 |
Шламы |
31,0 |
7,3 |
0,13 |
0,11 |
0,08 |
21,5 |
14,9 |
14,2 |
31,0 |
Исходный материал |
100,0 |
10,5 |
0,27 |
0,24 |
0,08 |
100,0 |
100,0 |
100,0 |
100,0 |
Таблица 2 Сравнительные результаты переработки кобальтоносных железо-марганцевых океанических образований по аналогу, прототипу и изобретению (вариант 2) |
Опыт№1 |
Продукты переработки |
выход |
Содержание |
Извлечение |
Условия опыта |
Mn |
Co |
Ni |
Cu |
Mn |
Со |
Ni |
Cu |
Концентрат обогащения на металлургический передел |
80,0 |
12,0 |
0,29 |
0,26 |
0,19 |
95,5 |
85,9 |
86,7 |
90,0 |
По способу аналога |
Хвосты |
20,0 |
2,25 |
0,19 |
0,16 |
0,04 |
4,5 |
14,1 |
13,3 |
10,0 |
Шламы |
0 |
0 |
0 |
0 |
0 |
0 |
0 |
0 |
0 |
Исходный материал |
100,0 |
10,5 |
0,27 |
0,24 |
0,08 |
100,0 |
100,0 |
100,0 |
100,0 |
Опыт №2 |
Продукты переработки |
выход |
Содержание |
Извлечение |
Условия опыта |
Mn |
Co |
Ni |
Cu |
Mn |
Со |
Ni |
Cu |
Концентрат обогащения на металлургический передел |
64,0 |
14,0 |
0,32 |
0,29 |
0,1 |
85,3 |
75,9 |
77,3 |
80,0 |
По способу прототипа |
Хвосты |
19,0 |
5,7 |
0,25 |
0,20 |
0,05 |
4,3 |
6,7 |
6,5 |
7,0 |
Шламы |
7,0 |
6,5 |
0,26 |
0,24 |
0,08 |
10,4 |
17,4 |
16,2 |
13,0 |
Исходный материал |
100,0 |
10,5 |
0,27 |
0,24 |
0,08 |
100,0 |
100,0 |
100,0 |
100,0 |
Продолжение таблицы 2 |
Опыт №3 |
Продукты переработки |
выход |
Содержание |
Извлечение |
Условия опыта |
Mn |
Co |
Ni |
Cu |
Mn |
Со |
Ni |
Cu |
Концентрат обогащения на металлургический передел |
33,0 |
20,3 |
0,54 |
0,63 |
0,14 |
63,8 |
66,0 |
86,6 |
57,7 |
По предложенному способу: Отсадка из фракции-12+0,5 концентрация на столе из фракции-0,5+0,044 |
Хвосты |
38,0 |
4,6 |
0,15 |
0,008 |
0,03 |
16,6 |
21,1 |
1,3 |
13,3 |
Шламы |
29,0 |
7,1 |
0,12 |
0,10 |
0,08 |
19,6 |
12,9 |
12,1 |
29,0 |
Исходный материал |
100,0 |
10,5 |
0,27 |
0,24 |
0,08 |
100,0 |
100,0 |
100,0 |
100,0 |
Опыт №4 |
Продукты переработки |
выход |
Содержание |
Извлечение |
Условия опыта |
Mn |
Co |
Ni |
Cu |
Mn |
Со |
Ni |
Cu |
Концентрат обогащения на металлургический передел |
38,0 |
19,1 |
0,52 |
0,58 |
0,11 |
69,1 |
73,2 |
|
52,2 |
По предложенному способу Отсадка из фракции -10+0,4 концентрация на столе из фракции-0,4+0,065 |
Хвосты |
35,0 |
3,9 |
0,11 |
0,54 |
0,05 |
13,1 |
14,8 |
|
20,8 |
Шламы |
27,0 |
6,9 |
0,12 |
0,10 |
0,08 |
17,8 |
12,0 |
|
27,0 |
Исходный материал |
100,0 |
10,5 |
0,27 |
0,24 |
0,08 |
100,0 |
100,0 |
100,0 |
100,0 |
Опыт №5 |
Продукты переработки |
выход |
Содержание |
Извлечение |
Условия опыта |
Mn |
Co |
Ni |
Cu |
Mn |
Со |
Ni |
Cu |
Концентрат обогащения на металлургический передел |
34,8 |
18,9 |
0,50 |
0,57 |
0,11 |
61,2 |
63,0 |
80,7 |
46,7 |
По предложенному способу Отсадка из фракции-13+0,6 концентрация на столе из фракции-0,6+0,085 |
Хвосты |
37,0 |
5,4 |
0,16 |
0,04 |
0,05 |
19,2 |
22,0 |
6,0 |
24,3 |
Шламы |
29,0 |
7,1 |
0,14 |
0,11 |
0,08 |
19,6 |
15,0 |
13,3 |
29,0 |
Исходный материал |
100,0 |
10,5 |
0,27 |
0,24 |
0,08 |
100,0 |
100,0 |
100,0 |
100,0 |
Формула изобретения
1. Способ переработки кобальтоносных железо-марганцевых океанических образований, включающие дробление, измельчение, классификацию и последующие выделения марганца и цветных металлов, отличающийся тем, что после классификации из фракции -0,5+0,074 мм осуществляют выделение марганца и цветных металлов гравитационным обогащением на концентрационном столе с последующей трехстадийной магнитной сепарацией легкой фракции концентрационного стола, при этом напряженность магнитного поля сепаратора на первой стадии составляет от 3500 до 4000 Э, на второй от 6500 до 7200 Э и на третьей от 8000 до 8200 Э, причем марганец и цветные металлы извлекают в магнитную фракцию третьей стадии.
2. Способ переработки кобальтоносных железо-марганцевых океанических образований, включающий дробление, измельчение, классификацию и последующее выделения марганца и цветных металлов, отличающийся тем, что классификацию осуществляют на фракции -12+0,5 и -0,5+0,074 мм, а выделение марганца и цветных металлов осуществляют из полученных фракций гравитационным обогащением на отсадочных машинах из фракции -12+0,5 мм и на концентрационных столах из фракции -0,5+0,074 мм, при этом марганец и цветные металлы извлекают в легкие фракции гравитационного обогащения, которые направляют на химико-металлургическую доводку.
3. Способ по п.1 или 2, отличающийся тем, что процесс переработки осуществляют в модуле на дне океана.
РИСУНКИ
|
|