|
(21), (22) Заявка: 2005104511/28, 18.02.2005
(24) Дата начала отсчета срока действия патента:
18.02.2005
(46) Опубликовано: 20.11.2007
(56) Список документов, цитированных в отчете о поиске:
SU 1698744 A1, 30.09.1988. Неразрушающий контроль металлов и изделий. Справочник. Под ред. Г.С.САМОЙЛОВИЧА. – М.: Машиностроение, 1976, с.311. SU 1714494 A1, 23.02.1992. SU 1619879 A1, 30.09.1991. SU 1677615 A1, 15.09.1991. JP 62170847 A, 27.07.1987.
Адрес для переписки:
620041, г.Екатеринбург, ГСП-170, ул. С. Ковалевской, 18, ИФМ УрО РАН, патентный отдел, Н.Г. Амроминой, В.И. Пудову
|
(72) Автор(ы):
Пудов Владимир Иванович (RU), Соболев Анатолий Сергеевич (RU), Бланин Валентин Алексеевич (RU)
(73) Патентообладатель(и):
Пудов Владимир Иванович (RU), Соболев Анатолий Сергеевич (RU), Бланин Валентин Алексеевич (RU)
|
(54) УСРОЙСТВО ДЛЯ НАСТРОЙКИ УЛЬТРАЗВУКОВЫХ ПРЕОБРАЗОВАТЕЛЕЙ – ДЕФЕКТОСКОПОВ
(57) Реферат:
Изобретение относится к устройствам для настройки ультразвуковой аппаратуры, предназначенной для неразрушающего контроля качества материалов. Техническим результатам изобретения является универсальность устройства и повышение точности настройки. Устройство для настройки ультразвуковых преобразователей – дефектоскопов изготовлено в виде пластины из малоуглеродистой мелкозернистой стали, содержащее со стороны, противоположной рабочей фронтальной поверхности, прямые ряды отражателей с разными площадями отражения, имитирующие форму и размеры реальных дефектов. При этом отражатели являются угловыми и выполнены в виде зарубок, которые имеют разную глубину и прямоугольную форму. Рабочие площади отражателей имеют форму либо квадратов и изменяются линейно с шагом, равным величине 1,06, или 1,12, или 1,19, или 1,26. Либо рабочие площади отражателей имеют форму прямоугольников и изменяются линейно по длине или ширине с шагом, равным величине 1.06, или 1,12, или 1,19, или 1,26. Причем любой отражатель имеет возможность выполнения функции опорного отражателя. 1 ил.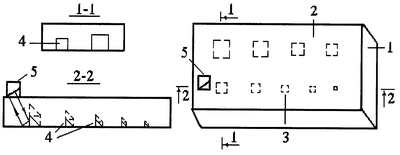
Изобретение относится к области ультразвуковой аппаратуры, предназначенной для неразрушающего контроля качества материалов, в частности для настройки ультразвуковых преобразователей – дефектоскопов.
Эффективность развития производства зависит не только от выпуска продукции высокого качества, но и от высокотехнического обеспечения методами и средствами ее контроля. Из существующих методов проверки качества продукции наиболее экономичными и достаточно информативными являются методы неразрушающего контроля и диагностики. Среди них ведущее положение занимает метод акустической дефектоскопии. Его применимость в разных отраслях производства составляет до 40%. При акустическом методе контроля применяют звуковые частоты от 0,5 до 20 кГц и чаще всего ультразвуковые – от 20 кГц до 30 МГц.
Ультразвуковая аппаратура состоит из электронного блока – дефектоскопа и основного рабочего элемента – электроакустического преобразователя прямого или наклонного типа. Ее настройка осуществляется при помощи устройств – образцов, содержащих набор искусственных моделей дефектов – отражателей разного вида и формы, например, функцию отражателей выполняют цилиндрические отверстия, плоскодонные сверления, пропилы, риски, зарубки и т.д., отображающие геометрию по возможности реальных дефектов типа нарушения сплошности. Наряду с отражателями, предназначенными для преобразователей прямого типа, существуют угловые отражатели – для преобразователей наклонного типа. В них используется так называемый угловой эффект. Это эффект двойного отражения ультразвука от граней угла, образуемого поверхностью искусственного дефекта и поверхностью образца, на которой этот отражатель выполнен.
Широкое распространение ультразвуковой диагностики с применением обширного класса аппаратуры привело к созданию различных комплектов настроечных образцов – стандартных, контрольных и т.д. [Неразрушающие методы контроля. Спецификатор различий в национальных стандартах различных стран. Под ред. Киршенбаума В.Я. – М.: Центр Наука и техника, Т.3, 1995. – 245 с.]. Они позволяют определить условную и предельную чувствительность аппаратуры, ее разрешающую способность, мертвую зону преобразователя, точку выхода ультразвуковых колебаний, угла ввода ультразвуковых колебаний, ширину основного лепестка диаграммы направленности и т.д. Однако появление многочисленных образцов, решающих только специфические задачи по настройке и проверке работы ультразвуковой аппаратуры, для конкретного производства и по возможности для реального материала, привело к тому, что одну и ту же аппаратуру затруднительно использовать для разных целей. Эти образцы не предназначены для настройки широкого класса ультразвуковой аппаратуры, поэтому они снижают ее функциональные возможности, а также достоверность и точность результатов диагностики.
Создание настроечных устройств, позволяющих решить проблему повышения уровня и универсальности настройки для широкого класса ультразвуковой аппаратуры, без снижения достоверности и точности результатов диагностики, является актуальной задачей в практике неразрушающего контроля.
Известно многофункциональное устройство в виде пластины из органического стекла марки ТОСП, предназначенное для комплексной проверки и настройки параметров ультразвуковой аппаратуры с наклонным и прямым преобразователем для контроля сварных соединений [ГОСТ 14782-86. Контроль неразрушающий. Соединения сварные. Методы ультразвуковые. – М.: Изд-во стандартов, 1986. – 11 с.].
Устройство содержит со стороны фронтальной поверхности одно сквозное цилиндрическое отверстие – отражатель из разных диаметров 20, 15, 30 мм (для проверки лучевой разрешающей способности аппаратуры с наклонным преобразователем по дальности) и 13 несквозных – диаметром 2 мм, глубиной 25 мм и шагом 5 мм (для определения условной чувствительности аппаратуры), которые параллельны относительно рабочей горизонтальной поверхности и расположены по дуге на расстояниях от 5 до 65 мм; на противоположной стороне рабочей поверхности выполнен сквозной ступенчатый пропил шириной 5 мм, глубиной 7,5 мм и шириной 5 мм, глубиной 5 мм, отстоящий от правой торцевой поверхности на расстояние 25 мм (для проверки лучевой разрешающей способности аппаратуры с прямым преобразователем по дальности), а от левой торцевой поверхности на расстоянии 10 мм выполнен сквозной пропил шириной 35 мм, глубиной 2 мм, под ним на расстоянии 27 мм со стороны фронтальной поверхности выполнен сквозной пропил шириной 2 мм и глубиной 45 мм (для проверки точности работы глубиномера); причем несквозные цилиндрические отражатели имеют плоское дно.
Основной недостаток данного устройства связан с его физико-механическими свойствами, которые в полной мере не соответствуют акустическим характеристикам, реально применяемым на практике материалам из стали [Алешин Н.П., Белый В.Е., Вопилкин А.Х. и др. Методы акустического контроля металлов. – М.: Машиностроение, 1989. – 456 с.].
Устройства из органического стекла, а также из других полимерных материалов из-за относительно быстрого старения и хрупкости не обладают долговременной стабильностью. Поэтому дальнейшее применение этих материалов в качестве рабочих для изготовления устройств по настройке ультразвуковых преобразователей – дефектоскопов становится мало перспективным.
Наибольшее распространение получили устройства, изготовленные из стали, причем для снижения влияния их различия в физико-механических свойствах при настройке ультразвуковой аппаратуры и приближения к акустическим свойствам контролируемых материалов и изделий, были приняты за основу малоуглеродистые стали с мелкозернистой структурой [Ермолов И.Н., Ермолов М.И. Ультразвуковой контроль. Учебник для специалистов первого и второго уровней квалификации – М.: НПО ЦНИИТМАШ, 1993. – 201 с.].
Наиболее близким по функциональному и техническому решению к предлагаемому устройству является взятое в качестве прототипа устройство для определения условной и предельной чувствительности ультразвуковой аппаратуры по изменению диаметра дефекта [Ермолов И.Н., Ланге Ю.В. Справочник. Ультразвуковой контроль, III том. – М: Машиностроение, 2004. – 860 с.].
Устройство выполнено в виде пластины из стали и содержит со стороны горизонтальной поверхности, противоположной рабочей поверхности, 7 цилиндрических несквозных отверстий – отражателей одинаковой глубины, но с переменными диаметрами от 3 мм до 30 мм, прямой ряд отражателей отстоит от рабочей поверхности устройства на расстоянии 100 мм. Причем отражатели выполнены с переменным шагом и имеют плоское дно.
Данное устройство, предназначенное для настройки аппаратуры с прямым преобразователем, снижает эффективность ее развития, поскольку наибольшее распространение получили преобразователи наклонного типа, уменьшающие вероятность появления ложных эхо-сигналов.
Другие недостатки устройства связаны с ограничением его функциональных возможностей: поскольку не позволяют выявлять чувствительность аппаратуры с учетом изменения глубины залегания дефектов и использовать для проверки и настройки линейности электроакустического тракта преобразователя – дефектоскопа и т.д.
В основу изобретения положена задача повышения эффективности работы ультразвуковой аппаратуры путем создания универсального настроечного устройства с линейным изменением шкалы рабочих площадей дефектов, обеспечивающего в различных условиях эксплуатации аппаратуры достоверность и точность результатов диагностики широкого круга номенклатурных материалов и изделий.
Поставленная задача решается тем, что в известном устройстве, изготовленном в виде пластины из малоуглеродистой мелкозернистой стали, содержащем ряд отражателей, с разным площадями отражения, имитирующие форму и размеры реальных дефектов, согласно изобретению отражатели являются угловыми и выполнены в виде зарубок, которые имеют разную глубину и прямоугольную форму, рабочие площади отражателей имеют форму либо квадратов и изменяются линейно с шагом, равным величине 1,06, или 1,12, или 1,19, или 1,26; либо рабочие площади отражателей имеют форму прямоугольников и изменяются линейно по длине или ширине с шагом, равным величине 1,06, или 1,12, или 1,19, или 1,26; причем все отражатели устройства, включая предпоследний от минимальной рабочей площади отражателя, выполнены опорным отражателем.
Снабжение заявляемого устройства отражателями с линейным изменением шкалы рабочих площадей дефектов, в том числе с изменением по глубине залегания, позволяет проводить настройку и проверку работы и параметров линейности электроакустического тракта ультразвуковой аппаратуры на новом качественном уровне, что обеспечивает повышение эффективности ее работы, достоверность и точность результатов диагностики. Предложенное решение позволяет упорядочить настройку широкого класса ультразвуковой аппаратуры, что обеспечивает единообразие методики ее поверки и существенное расширение областей для ее практического использования, а также диапазон номенклатуры контролируемых материалов и изделий.
На чертеже представлено заявляемое устройство.
Устройство изготовлено в виде пластины 1 из малоуглеродистой мелкозернистой стали и содержит с противоположной стороны рабочей фронтальной поверхности 2 прямые ряды отражателей 3 с разным площадями отражения 4, имитирующие форму и размеры реальных дефектов. Отражатели 3 являются угловыми и выполнены в виде зарубок, которые имеют разную глубину и прямоугольную форму. Их рабочие площади отражения 4 имеют форму квадратов и изменяются линейно с шагом, равным величине 1,06, соответствующей последующим изменениям эхо-сигналов, отраженных от каждой поверхности рабочих площадей, на величину в 0,5 дБ в диапазоне от +6 до -20 дБ, который соответствует определенным величинам амплитуд эхо-сигналов, обусловленным определенным размером площадей отражения 4 и их последующим изменениям в диапазоне рассматриваемых дефектов, или шаг изменения рабочих площадей отражателей 3 может быть равен величине 1,12, соответствующей последующим изменениям эхо-сигналов, отраженных от поверхности рабочих площадей, на величину в 1 дБ, а также – величине 1,19 и с последующим изменениям эхо-сигналов на величину в 1,5 дБ в вышеуказанном диапазоне, или – величине 1,26 и с изменениям эхо-сигналов на величину в 2 дБ. Причем все отражатели 3 устройства, включая предпоследний от минимальной рабочей площади отражателя, выполнены опорным отражателем, рабочая площадь 4 которого привязывается непосредственно к размеру реального дефекта материала и служит нулевым параметром при изменении величины амплитуды эхо-сигнала в указанном диапазоне децибел. Кроме этого, рабочие площади 4 отражателей 3 могут иметь форму прямоугольников и изменяются линейно по длине или ширине с шагом равным величине 1,06, соответствующей последующим изменениям эхо-сигналов, отраженных от каждой поверхности рабочих площадей 4, на величину в 0,5 дБ в диапазоне от +6 до -20 дБ, или шаг изменения рабочих площадей отражателей 3 может быть равен величине 1,12, соответствующей последующим изменениям эхо-сигналов, отраженных от поверхности рабочих площадей 4, на величину в 1 дБ, а также – величине 1,19 и с последующим изменениям эхо-сигналов на величину в 1,5 дБ в вышеуказанном диапазоне, или – величине 1,26 и с изменениям эхо-сигналов на величину в 2 дБ.
Пример устройства.
Устройство представляет специально изготовленный из стали 20 образец – пластину размерами 220×80×30 мм. Модель имитатора реального дефекта выполнена в виде углового отражателя с его нормированным размером – площадью отражения в форме квадрата. Дискретный набор дефектов представляет упорядоченный по отношению площадей, выраженному числом nxi децибелов, ряд угловых отражателей изготовленных в виде зарубок, которые имеют разную глубину и прямоугольную форму. Один из отражателей устройства дополнительно выполняет функцию опорного отражателя. Например, площадь опорного отражателя дефекта, согласно нормативными документами или отраслевым стандартам ультразвукового контроля, составляет 7 мм2. Тогда соответственно этой величине выбирают с подобной площадью отражатель, который становится опорным. Исходя из точности настройки аппаратуры, выбираем, при линейном изменении рабочей площади отражателей, шаг, равный величине 1 дБ, что определяет, например, при контроле теплоэнергетического оборудования диапазон изменения размеров дефекта nxi от +4 дБ до -14 дБ.
Таким образом, предложенное устройство для настройки ультразвуковых преобразователей – дефектоскопов позволяет без разработки новой ультразвуковой аппаратуры повысить эффективность ее работы и, как следствие, достоверность и точность результатов диагностики за счет нового подхода в настройке и проверки работы и параметров линейности электроакустического тракта аппаратуры. Одновременно за счет упорядочения в настройке широкого класса ультразвуковой аппаратуры обеспечивается единообразие методики ее поверки параметров и существенное расширение областей для ее практического использования, а также диапазон номенклатуры контролируемых материалов и изделий.
Формула изобретения
Устройство для настройки ультразвуковых преобразователей-дефектоскопов, изготовленное в виде пластины из малоуглеродистой мелкозернистой стали, содержащее со стороны, противоположной рабочей фронтальной поверхности, прямые ряды отражателей с разными площадями отражения, имитирующие форму и размеры реальных дефектов, отличающееся тем, что отражатели являются угловыми и выполнены в виде зарубок, которые имеют разную глубину и прямоугольную форму, рабочие площади отражателей имеют форму либо квадратов и изменяются линейно с шагом, равным величине 1,06, или 1,12, или 1,19, или 1,26, либо рабочие площади отражателей имеют форму прямоугольников и изменяются линейно по длине или ширине с шагом, равным величине 1.06, или 1,12, или 1,19, или 1,26, причем любой отражатель имеет возможность выполнения функции опорного отражателя.
РИСУНКИ
MM4A – Досрочное прекращение действия патента СССР или патента Российской Федерации на изобретение из-за неуплаты в установленный срок пошлины за поддержание патента в силе
Извещение опубликовано: 27.04.2009 БИ: 12/2009
|
|