(21), (22) Заявка: 2005130624/06, 03.10.2005
(24) Дата начала отсчета срока действия патента:
03.10.2005
(43) Дата публикации заявки: 10.04.2007
(46) Опубликовано: 20.11.2007
(56) Список документов, цитированных в отчете о поиске:
RU 2216679 C1, 20.11.2003. RU 2253659 C2, 10.06.2005. RU 2047454 C1, 10.11.1995. SU 817143 A, 30.03.1981. SU 449105 A, 02.06.1975.
Адрес для переписки:
420111, г.Казань, ул. Лобачевского, 2/31, Н.М. Якупову
|
(72) Автор(ы):
Якупов Нух Махмудович (RU), Якупов Самат Нухович (RU), Мифтахутдинов Ильяс Ханафеевич (RU), Мифтахутдинов Алик Ильясович (RU)
(73) Патентообладатель(и):
Институт механики и машиностроения Казанского научного центра Российской академии наук (RU), Якупов Нух Махмудович (RU)
|
(54) СПОСОБ РЕМОНТА ТРЕЩИН В ТОНКОСТЕННЫХ ОБОЛОЧЕЧНЫХ КОНСТРУКЦИЯХ
(57) Реферат:
Изобретение относится к трубопроводному транспорту и используется для предотвращения развития и ремонта трещин в стенках трубопроводов большого диаметра, газгольдеров, резервуаров, оболочечных и пластинчатых конструкций, выполненных из металла, стекла, полимеров. На тонкостенный корпус оболочечной конструкции устанавливают крепежные элементы из сплава с “эффектом памяти формы”, например из нитинола или из предварительно растянутого полимера, например оргстекла или поликарбоната. Крепежные элементы приклеивают высокопрочными клеями, например, производства ВИ-АМ с обоих концов трещины. При нагревании крепежных элементов происходит перераспределение поля напряжения в области трещины, уменьшение разрывающих усилий в вершине трещины с возможностью получения первоначальной формы оболочечной конструкции. Улучшает работу конструкции, устраняет необходимость предварительного сверления сквозных отверстий. 1 з.п. ф-лы, 3 ил.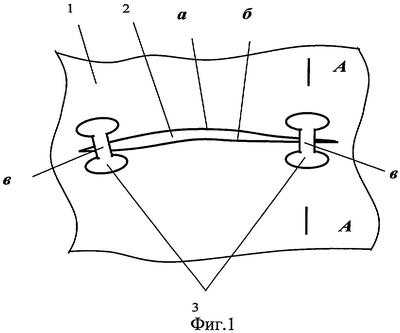
Изобретение относится к области эксплуатации трубопроводов, в том числе трубопроводов большого диаметра, газгольдеров, градирен и других оболочечных и пластинчатых конструкций, выполненных из металла, стекла, полимеров, и может применяться для ремонта трещин в их стенках.
Известны способы торможения усталостных трещин с нормальным отрывом в элементах конструкций, заключающиеся в том, что путем перегрузки конструкции в ней создают увеличение пластически деформированной зоны перед вершиной трещины, причем увеличение пластически деформированной зоны осуществляют приложением к берегам трещины нагрузок, которые направлены параллельно фронту трещины во взаимно противоположные стороны (Патент РФ №2047454, М. Кл. В23Р 6/00, опубл. 10.11.95 г., бюл. №17 – 2000).
Однако надежность и работоспособность таких способов торможения трещин вызывают сомнения, а сам способ неприменим для ремонта оболочек, наполненных жидкостью или газом.
Известны способы соединения трубопроводов небольшого диаметра за счет применения разрезных втулок из сплавов с «эффектом памяти формы» (ЭПФ), внутренний диаметр которых меньше наружного диаметра сопрягаемых изделий. Такую втулку окунают в жидкий азот, заставляя его расшириться, потом надевают на концы труб, после нагрева до комнатной температуры втулка образует прочное соединение («Техника-молодежи», №3, 1986. – С.65, рис.10).
Недостатком таких способов соединения является невозможность ремонта повреждений в стенках труб большого диаметра и емкостей больших габаритов.
Существуют также способы срезания оголовок железобетонных свай с помощью хомута, выполненного из сплава с «эффектом памяти формы», снабженного электронагревателем. Первоначальный диаметр хомута устанавливают меньше диаметра сваи (в течение 1 часа при температуре 500°С). Затем хомут охлаждают и пластически деформируют больше диаметра поперечного сечения срезаемой сваи. Далее хомут свободно надевают на оголовок сваи, включают электронагреватель, и хомут при температуре срабатывания, сокращая свой диаметр, разрушает оголовок сваи и оголяет арматуру (Авторское свидетельство СССР №817143, М. Кл. Е02D 9/00, опубл. 30.03.81, бюл. №12).
Слабой стороной таких способов является невозможность крепления хомута к плоским и искривленным поверхностям тонкостенных конструкций.
Известны способы закрепления костных отломков нижней челюсти человека с помощью скоб-фиксаторов, выполненных из сплава с «эффектом памяти формы». По данному способу в каждом отломке просверливают отверстие на расстоянии 10-15 мм от края перелома с учетом направления компрессионных усилий скобы-фиксатора. Затем скобу-фиксатор в течение 10-15 секунд орошают хлорэтилом для придания проектной формы. Скобы-фиксаторы руками или инструментами изгибают в наиболее удобную форму для установки в отверстия, ранее просверленные в костных отломках. В таком положении скобы-фиксаторы закрепляют в челюсти и в течение 20-40 секунд, после чего скобы-фиксаторы воспринимают заданную проектную форму в связи с достижением температуры формовосстановления (Применение сплавов с эффектом памяти формы в стоматологии. / Миргазизов М.З. и др. – М.: Медицина, 1991, – С.81-82, рис.18).
Недостатками таких способов являются необходимость предварительного рассверливания отверстий в костных отломках, ослабляющих конструкцию скрепляемых элементов, образование зоны концентрации напряжения в костной ткани в области отверстия и возможность разрушения костной ткани при ошибках расчета процента формовосстановления скоб-фиксаторов.
Известен также способ неразъемного муфто-клеевого соединения, заключающийся в размещении на концах соединяемых труб термоусаживающей муфты, нанесении на соединяемые поверхности клея, нагревании места контакта соединяемых поверхностей до температуры термоусадки муфты, выдержке при этой температуре до полной термоусадки муфты и отверждения клея, причем внутри труб в месте их соединения устанавливают с натягом центрирующую втулку, жесткость которой в осевом направлении в 2,5-3 раза превышает жесткость в тангенциальном направлении. Центрирующую втулку изготавливают навивкой псевдоленты, представляющей собой жгут стекловолокна, обвивающий две краевые нити (Патент РФ №2216679, М. Кл. F16L 47/02, опубл. 20.11.2003 г.).
Недостатками данного способа являются:
– потребность в центрирующей втулке, что приводит к усложнению всего процесса соединения труб;
– центрирующая втулка уменьшает поперечное сечение внутри трубы и создает дополнительное гидравлическое сопротивление;
– так как втулки должны изготавливаться заранее, следовательно, их надо отливать в специальных формах или опалубках;
– эпоксидная смола при твердении имеет свойство прочно прикрепляться к опалубке, в которой формуется, следовательно, необходимо иметь устоявшееся заводское производство;
– возникает потребность в высокой точности изготовления центрирующей втулки, жесткость которой разная в разных направлениях (в 2,5-3 раза);
– требуется навивка псевдоленты из стекловолокна с определенным углом между жгутом и образующей втулки в 5-10°;
– дороговизна применяемых втулок из термоусаживающихся термореактивных полимерных материалов, т.к. они заранее изготавливаются по сложному составу из дорогих материалов (по патенту №2253659 – до 10 компонентов).
Задачами (целью) изобретения являются упрощение процесса ремонта трещин в тонкостенных конструкциях и подбора размеров крепежного элемента, устранение зоны концентрации напряжения в конструкции в области крепежных элементов и уменьшение разрывающих усилий в вершине трещины.
Указанные задачи достигаются тем, что в способе ремонта трещин в тонкостенных оболочечных конструкциях, включающем операции нанесения на соединяемые поверхности клея, установки крепежных элементов из сплавов с эффектом памяти формы на тонкостенный корпус, нагревания соединяемых поверхностей, выдерживания до полной термоусадки и отверждения клея, крепежные элементы в рабочей части подвергают нагреву до температуры формовосстановления для их срабатывания, после которого края трещины прижимаются друг к другу, швы подвергают дополнительной обработке (заглаживанию и при необходимости – проварке), а также, при необходимости, устанавливают дополнительные закрепляющие планки из обычного металла или полимера сверх трещины. Крепежные элементы выполняют в форме плоских гантелей и приклеивают их на концы трещины, при этом размеры рабочей части сечения гантелей подбирают по формуле

где Fg – площадь рабочей части сечения гантелей;
tm – толщина оболочки конструкции в области трещины;
n – коэффициент, меняющийся в пределах от 1,2 до 3,6, при ширине рабочей части сечения плоских гантелей h (h=ntm);
k – коэффициент, меняющийся в пределах от 0,8 до 0,9;
Em – модуль упругости материала конструкции;
Eg – модуль упругости материала крепежного элемента.
На фиг.1 показан участок поверхности оболочки с трещиной, на которую приклеены крепежные элементы; на фиг.2 представлено сечение А-А по фиг.1.; на фиг.3 представлено сечение Б-Б по фиг.2. На фигурах края (берега) трещины обозначены буквами а и б, а рабочая часть крепежного элемента – буквой в.
На фигурах также показан участок поверхности оболочки 1 с трещиной 2, на которую приклеены крепежные элементы 3, выполненные из сплава с «эффектом памяти формы» клеем 4.
Способ ремонта трещин в тонкостенных оболочечных конструкциях осуществляется в следующей последовательности:
а) рассчитывают площадь поперечного сечения рабочей части крепежного элемента 3 и подбирают необходимый крепежный элемент (размеры рабочей части сечения гантелей подбирают по формуле 1);
б) наносится на соединяемые поверхности оболочки 1 с трещиной 2 клей;
в) поперек трещины 2 на стенке оболочки 1 приклеивают клеем 4 с обоих концов трещины крепежные элементы 3 (для металлических стенок – предварительно растянутые нитиноловые или подобные, а для полимерных – предварительно растянутые из оргстекла, поликарбоната или подобные);
в) крепежные элементы 3 в рабочей части в подвергают нагреву до температуры формовосстановления (например, для нитинола марки ТН-1 – до 60°С, для оргстекла 100-120°С, для поликарбоната 120-150°С), при этом после срабатывания крепежных элементов 3, края (берега) трещины а и б прижимаются друг к другу;
г) швы подвергают дополнительной обработке – заглаживанию и, при необходимости, проварке, а также, при необходимости, устанавливают дополнительные закрепляющие планки из обычного металла или полимера сверх трещины.
Пример. Подготовили крепежные элементы (накладки) из органического стекла (ПММА) в виде плоских «гантелей» и нанесли на нее клеящий субстрат.
Подготовили дефектную поверхность, имеющую трещину, также нанеся на нее клеящий субстрат. Можно использовать различные клеи, например Момент, ВИАМ и др.
(Например, клей ВИАМ на полимерной основе имеет прочность на сдвиг 25-40 МПа или 250-400 кг/см2, применяется для склеивания ответственных частей ракетно-космической техники. Существуют и более прочные клеи. Например, на стр.145 книги В.Г.Страданченко, А.А.Шубина «Пластмассы в строительстве», Новочеркасск – 2004: отмечается, что «Клеевые швы, сделанные с помощью синтетических материалов, очень прочны. Прочность склейки настолько велика, что деревянные конструкции, соединенные с… эпоксидными смолами, при предельной нагрузке, разрушаются по цельной древесине». Как известно, прочность древесины составляет 80-100 МПа или 800-1000 кг/см2 и более).
Крепежные элементы клеевой стороной прижали к клеевой части дефектной поверхности с трещиной до полного высыхания клея. После высыхания клея нагрели верхние поверхности крепежных элементов. Крепежные элементы сработали и закрыли шов. Шов подвергли окончательной обработке путем заглаживания.
Технико-экономические преимущества предлагаемого изобретения состоят в следующем:
– происходит перераспределение поля напряжения в области трещины и уменьшение разрывающих усилий в вершине трещины;
– возможность получения первоначальной формы оболочечной конструкции;
– простота подбора размеров крепежного элемента;
– отсутствие предварительно рассверливаемых сквозных отверстий, ослабляющих стенки конструкции;
– отсутствие дополнительных элементов, типа центрирующей втулки и псевдоленты, тем самым не создается дополнительное гидравлическое сопротивление;
– отсутствие зоны концентрации напряжения в конструкции в области крепежных элементов.
Формула изобретения
1. Способ ремонта трещин в тонкостенных оболочечных конструкциях, включающий операции нанесения на соединяемые поверхности клея, установки крепежных элементов из сплавов с эффектом памяти формы на тонкостенный корпус, нагревания соединяемых поверхностей, выдерживания до полной термоусадки и отверждения клея, отличающийся тем, что крепежные элементы в рабочей части подвергают нагреву до температуры формовосстановления для их срабатывания, после которого края трещины прижимаются друг к другу, швы подвергают дополнительной обработке (заглаживанию и при необходимости проварке), а также, при необходимости, устанавливают дополнительные закрепляющие планки из обычного металла или полимера сверх трещины.
2. Способ по п.1, отличающийся тем, что крепежные элементы выполняют в форме плоских гантелей и приклеивают их на концы трещины, при этом размеры рабочей части сечения гантелей подбирают по формуле:
,
где Fg – площадь рабочей части сечения гантелей,
tm – толщина оболочки конструкции в области трещины;
n – коэффициент, меняющийся в пределах от 1,2 до 3,6, при ширине рабочей части сечения плоских гантелей h (h=ntm);
k – коэффициент, меняющийся в пределах от 0,8 до 0,9;
Еm – модуль упругости материала конструкции;
Eg – модуль упругости материала крепежного элемента.
РИСУНКИ
|