|
(21), (22) Заявка: 2005139811/28, 21.12.2005
(24) Дата начала отсчета срока действия патента:
21.12.2005
(43) Дата публикации заявки: 27.06.2007
(46) Опубликовано: 10.11.2007
(56) Список документов, цитированных в отчете о поиске:
RU 2032162 C1 27.03.1995. SU 1295283 A1 07.03.1987. SU 1696843 A1 07.12.1991. JP 2002296125 A 09.10.2002.
Адрес для переписки:
03680, г. Киев-142, ул. Кржижановского, 3, Институт проблем материаловедения им. И.Н. Францевича Национальной академии наук Украины
|
(72) Автор(ы):
Бякова Александра Викторовна (UA), Мильман Юлий Викторович (UA), Власов Андрей Алексеевич (UA), Чугунова Светлана Ивановна (UA), Гончарова Ирина Вадимовна (UA), Голубенко Алексей Анатольевич (UA)
(73) Патентообладатель(и):
Институт проблем материаловедения им. И.Н. Францевича Национальной академии наук Украины (UA)
|
(54) СПОСОБ ОПРЕДЕЛЕНИЯ ОСТАТОЧНЫХ НАПРЯЖЕНИЙ
(57) Реферат:
Изобретение относится к испытательной технике. Сущность: вдавливают пирамидальный индентор в поперечное сечение покрытия или слой материала до получения отпечатка твердости при ориентации его диагоналей ортогонально направлению действия остаточных напряжений. Регистрируют усилие вдавливания, измеряют после разгрузки геометрические параметры отпечатка, с учетом которых определяют остаточные напряжения. Испытания проводят с использованием стандартного пирамидального индентора Кнупа с основанием в виде ромба. Вдавливание индентора осуществляют в двух соседних областях покрытия или слоя материала при усилии вдавливания, превышающем критическое значение. Получают два отпечатка твердости с взаимно перпендикулярной ориентацией длинных диагоналей и, с учетом проведенных измерений, определяют значения твердости по отпечаткам, в которых длинная диагональ ориентирована соответственно параллельно HK1 и перпендикулярно НК2 направлению действия остаточных напряжений. Величину остаточных напряжений находят геометрически по разности значений твердости (HK1 и НК2) с использованием нормировочного графика, построенного независимым методом в координатах (HK1-HK2)- . Технический результат: расширение функциональных возможностей способа, снижение трудоемкости и повышение его точности. 1 з.п. ф-лы, 5 ил, 1 табл.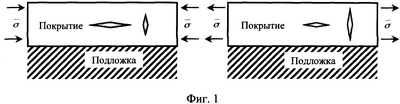
Изобретение относится к области механических испытаний материалов и может быть использовано для определения остаточных напряжений, являющихся суперпозицией структурных и термических напряжений, в керамических и металлических покрытиях с толщиной h l0-2 мм. Способ также применим для проведения испытаний в поверхностных и внутренних слоях из металлических и неметаллических материалов для определения остаточных напряжений, возникающих под воздействием фазовых превращений термического и/или механического воздействия.
Известен способ определения остаточных напряжений в поверхностных слоях металлических изделий с помощью рентгеновских лучей (Биргер И.А. Остаточные напряжения. – М.: Машиностроение. – 1963. – с.55-67, 74-79), в соответствии с которым пучок рентгеновских лучей, направленный на поверхность металла, отражается от атомных решеток кристаллов, что приводит к интерференции и образованию колец Дебая-Шерера, ширина, которых зависит от уровня напряжений.
Недостатками способа является низкая точность определения напряжений, необходимость использования специального дорогостоящего оборудования и специальных помещений, а также его экологическая вредность.
Известен способ определения остаточных напряжений в покрытиях (Яковчук Ю.Е., Лоскутов В.Ф., Чернега С.М. Установка для определения остаточных напряжений в диффузионных слоях. Заводская лаборатория, 1984, №7), в соответствии с которым плоский образец (2×7×55 мм) с покрытием подвергают электролитическому травлению по одной плоскости (7×55 мм). В результате этого происходит уменьшение толщины покрытия на одной стороне образца и, как следствие, достигается нарушение равновесия, что приводит к деформации образца путем изгиба. В процессе стравливания измеряют деформацию образца, а остаточные напряжения определяют при известном модуле Юнга с учетом регистрируемой стрелы прогиба.
Указанный способ имеет следующие недостатки: низкую точность, обусловленную изменением напряженного состояния оставшейся части покрытия при удалении части покрытия в результате стравливания; невозможность определения остаточных напряжений с учетом действующих в покрытии структурных напряжений; высокую трудоемкость и низкую технологичность, обусловленную большой длительностью испытаний (4-8 часов) и трудностью подбора режима травления вследствие высокой коррозионной стойкости большинства материалов, используемых для защитных поверхностных слоев (например, карбидов, нитридов, боридов и т.п.); высокую токсичность, обусловленную присутствием в составе травителей концентрированных кислот, щелочей и т.п.
По технической сути и достигаемому эффекту наиболее близким к заявляемому является способ определения остаточных напряжений (Бякова А.В., Горбач В.Г. Власов А.А., Грушевский Я.Л. Патент России, МКИ5 G01N 3/00, №2032162, 11.10.91, БИ №9, опубл. 27.03.95), по которому в поперечное сечение испытуемого покрытия статически вдавливают острый пирамидальный индентор при ортогональной ориентации диагоналей отпечатка относительно направления действия остаточных напряжений до образования отпечатка твердости с развивающимися от его вершин хрупкими трещинами. После разгрузки измеряют геометрические параметры отпечатка, а геометрические параметры трещин измеряют раздельно в двух взаимно перпендикулярных направлениях, оценивают их топологию, определяют равновесное и эффективное значения вязкости разрушения соответственно параллельно и перпендикулярно действию остаточных напряжений и рассчитывают величину с учетом действительных линейных размеров зерна покрытия. Для построения эпюры величину остаточных напряжений определяют в нескольких точках поперечного сечения покрытия на различном расстоянии Y от его внешней границы, а величину остаточных напряжений в точке, полученной при условии Y=0, определяют с учетом значения полученного при вдавливании индентора в поверхность покрытия. Способ может использоваться для проведения испытаний в поверхностных слоях из прочных материалов с соотношением Е 200 ГПа, G 50 ГПа G/E* 0,24 [Е*=Е(1- )/(1+ )(1-2 )];  0,33; Н /Е 0,01.
Недостатками способа являются: невозможность достижения образования отпечатка твердости с хрупкими трещинами при вдавливании индентора в металлические покрытия или слои материала; невозможность получения отпечатка твердости с хрупкими трещинами при вдавливании индентора в поперечное сечение тонких керамических покрытий (10-2 мм); высокая трудоемкость способа, обусловленная необходимостью определения линейного размера действительного зерна покрытия методами количественного металлографического анализа; низкая точность, обусловленная трудностями определения положения конца трещин, развивающихся у вершин отпечатка твердости в керамическом материале, что может привести к ошибке при установлении их топологии по соотношению с/а (где а – половина длины диагонали отпечатка индентора Виккерса, с – длина трещины от центра отпечатка до ее конца), которое необходимо для правильного выбора расчетных формул при определении равновесного и эффективного значений вязкости разрушения, входящих в конечное соотношение для расчета остаточных напряжений 
Таким образом, существующий уровень техники не позволяет корректно определять остаточные напряжения в процессе вдавливания пирамидального индентора в покрытие.
Задачей предлагаемого изобретения “Способ определения остаточных напряжений” является расширение функциональных возможностей способа, снижение трудоемкости и повышение его точности за счет проведения испытаний с применением пирамидального индентора Кнупа с основанием в виде ромба, вдавливания индентора в двух соседних точках поперечного сечения покрытия или слоя материала при усилии вдавливания, превышающем критическое значение , получения двух отпечатков при ориентации их диагоналей ортогонально направлению действия остаточных напряжений и взаимно перпендикулярной ориентацией длинных диагоналей, с учетом выполненных измерений определяют значения твердости НК по отпечаткам, в которых длинная диагональ ориентирована соответственно параллельно HK1 и перпендикулярно НК2 направлению действия остаточных напряжений, величину остаточных напряжений находят геометрическим путем по разности значений твердости (HK1 и НК2) с использованием нормировочного графика, построенного независимым методом в координатах (HK1-НК2)- 
Величину остаточных напряжений определяют с учетом значений твердости, которые получают в нескольких сечениях покрытия, находящихся на различном расстоянии друг от друга.
Сущность изобретения заключается в том, что в известном способе, по которому в поперечное сечение покрытия статически вдавливают пирамидальный индентор до образования отпечатка твердости при ориентации его диагоналей ортогонально направлению действия остаточных напряжений, регистрируют усилие вдавливания и измеряют после разгрузки геометрические параметры отпечатка, с учетом которых определяют остаточные напряжения, согласно изобретению испытания проводят с использованием стандартного пирамидального индентора Кнупа с основанием в виде ромба, вдавливание индентора осуществляют в двух соседних точках покрытия или слоя материала при усилии вдавливания, превышающем критическое значение Pc, получают отпечатки твердости с взаимно перпендикулярной ориентацией длинных диагоналей, и, с учетом проведенных измерений, определяют значения твердости (НК) по отпечаткам, в которых длинная диагональ ориентирована соответственно параллельно (HK1) и перпендикулярно (НК2) направлению действия остаточных напряжений, а величину остаточных напряжений находят геометрически по разности значений твердости (HK1 и НК2) с использованием нормировочного графика, построенного независимым методом в координатах (HK1-НК2)- 
Кроме того, распределение остаточных напряжений по сечению толстых покрытий или слоев материала находят с учетом значений твердости (HK1 и НК2), которые получают в нескольких сечениях, находящихся на различном расстоянии (Y) друг от друга.
Заявляемый способ реализуют следующим образом. Испытания проводят на образцах с покрытиями и/или поверхностными или внутренними слоями, сформированными любым известным способом, в которых возникают остаточные напряжения за счет фазовых превращений, образования морфологической текстуры, а также возникают в результате термических и/или механических воздействий. В поперечном сечении такого образца изготавливают металлографический шлиф путем сошлифовки части материала и последующей полировки и/или электрополировки.
Затем в поперечном сечении покрытия или слоя материала проводят вдавливание индентора Кнупа и регистрируют усилие вдавливания Р.
Механические испытания осуществляют на стандартных микротвердомерах типа ПМТ-3 или металлографических микроскопах, например микроскопе “Neophot”, оснащенном соответствующей приставкой для испытаний на микротвердость. В процессе испытаний образец располагают таким образом, чтобы в отпечатке твердости, полученном после вдавливания индентора и разгрузки, диагонали были ориентированы ортогонально действующим остаточным напряжениям например, в поперечном сечении образца с плоскопараллельными поверхностями – ортогонально его внешней границе так, как это показано на схеме (фиг.1).
При этом, вначале образец располагают таким образом, чтобы в одной части отпечатков твердости длинная диагональ располагалась параллельно действующим остаточным напряжениям При таком варианте испытаний размер длинной диагонали отпечатка индентора, полученного при принятом усилии вдавливания, контролируется структурным состоянием покрытия или слоя материала. Затем образец поворачивают таким образом, чтобы в другой части отпечатков длинная диагональ располагалась перпендикулярно действующим остаточным напряжениям При таком расположении образца размер длинной диагонали отпечатка индентора дополнительно контролируется остаточными напряжениями, действующими в покрытии.
Несоблюдение условий ортогональности, при котором длинная диагональ отпечатка индентора Кнупа ориентирована по отношению к направлению действия остаточных напряжений под некоторым углом , приводит к нарушению осесимметричности поля контактных напряжений в области внедрения индентора и, как следствие, к искажению формы отпечатка, снижая точность способа.
Предварительно проводят две серии испытаний образца при ступенчатом возрастании усилия Р(Р1<Р2…<Рn) при переходе от точки к точке с получением отпечатков твердости Кнупа, в которых длинная диагональ отпечатка ориентирована соответственно параллельно и перпендикулярно направлению действия остаточных напряжений так, как это описано выше. После статического вдавливания индентора и разгрузки для каждой серии отпечатков производят измерение геометрических параметров отпечатков, по которым определяют значения твердости из соотношения (Глазов В.М., Вигдорович В.Н. Микротвердость металлов. М., Металлургиздат, 1962, с.73):
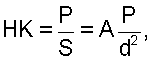
где S – площадь проекции отпечатка;
Р – усилие вдавливания в Н;
D – размер длинной диагонали в м.
После этого строят зависимость твердости (НК) от нагрузки и определяют значения критических нагрузок Pc1 и Рс2 при ориентации длинной диагонали отпечатков соответственно в направлениях параллельном и перпендикулярном направлению действия остаточных напряжений так, как это показано для случая испытаний в покрытии из карбида титана (фиг.2).
После проведения предварительных испытаний в двух соседних точках покрытия или слоя материала проводят вдавливание индентора Кнупа при усилиях, превышающих значения критических нагрузок Pc1 и Рс2, предварительно найденных для соответствующих условий ориентации длинной диагонали отпечатка, после разгрузки производят измерение геометрических параметров отпечатков, с учетом которых проводят определение значений твердости HK1 (при направлении длинной диагонали отпечатка параллельно действию остаточных напряжений) и НК2 (при направлении длинной диагонали отпечатка перпендикулярно действию остаточных напряжений).
Затем определяют разность значений твердости (HK1-HK2), определенных по отпечаткам индентора, у которых длинные диагонали ориентированы соответственно в направлениях параллельном и перпендикулярном направлению действия остаточных напряжений, и с использованием нормировочного графика, построенного независимым методом в координатах (HK1-НК2)- определяют величину остаточных напряжений 
Кроме того, при построении эпюры распределения остаточных напряжений по сечению толстых (более 10-2 мм) покрытий или слоев материала статическое вдавливание индентора Кнупа в двух соседних точках проводят в нескольких его сечениях, расположенных на различном расстоянии (Y) друг от друга. Ориентацию отпечатков индентора Кнупа в двух соседних точках материала при выбранных усилиях вдавливания, превышающих значения критических нагрузок Pc1 и Рс2, а также измерение геометрических параметров отпечатков твердости, определение значений твердости (HK1 и НК2) и величины остаточных напряжений, действующих в каждом сечении покрытия или слоя материала проводят так, как описано выше.
На основании полученных результатов строят эпюру распределения остаточных напряжений по сечению покрытия или слоя материала, где по оси абсцисс откладывают значение Y (расстояние), а по оси ординат – соответствующее этому сечению полученное значение 
Пример 1. Для проведения испытаний изготовили образец из стали У8 в виде параллелепипеда с размерами 2×10×15. На поверхность образца методом химического газофазного осаждения нанесли покрытие из карбида титана TiC при температуре 1050°C в течение 6 часов. После охлаждения образец с покрытием TiC подвергли нормализации путем нагрева под слоем карбюризатора до температуры 820°С с последующим охлаждением на воздухе. Из образца с покрытием изготовили поперечный шлиф по общепринятой методике. На приготовленном шлифе методом металлографического анализа на микроскопе EPIVAL при увеличении 1600× измерили толщину покрытия, которая приведена в таблице.
Результаты испытаний |
Пример |
Материал подложки |
Тип покрытия или слоя материала |
Толщина покрытия или слоя материала, мкм |
Критическая нагрузка, Н |
Расстояние от поверхности, мкм |
Значение твердости, МПа |
МПа |
Pc1 |
Рс2 |
HK1 |
НК2 |
1 |
Сталь У8 |
TiC |
22 |
0.6 |
0.4 |
12 |
1570 |
3150 |
-2070 |
2 |
Сталь Г13 |
Сталь Х18Н10Т |
200 |
0.4 |
0.2 |
50 |
215 |
260 |
-270 |
100 |
220 |
240 |
-135 |
150 |
220 |
230 |
-65 |
3 |
Сталь 15 |
Cu |
100 |
0.2 |
0.1 |
50 |
965 |
945 |
48 |
4 |
Многослойная композиция Мо-Cu |
Cu |
2000 |
0.2 |
0.1 |
1000 |
966 |
940 |
67 |
Затем на микротвердомере ПМТ-3 провели предварительные испытания, которые включали статическое вдавливание стандартной алмазной пирамидой Кнупа в центральной части покрытия так, чтобы диагонали ее отпечатков были ориентированы ортогонально внешней границе покрытия, вдоль которой действуют возникшие остаточные напряжения.
В первой серии испытаний длинную диагональ отпечатков твердости ориентировали параллельно внешней границе покрытия, а во второй серии испытаний – перпендикулярно внешней границе покрытия. В каждой серии испытаний вдавливание индентора Кнупа осуществляли при ступенчатом возрастании усилия Р, Н (0,2<0,4<0,6<0,8<1,0) при переходе от точки к точке. При каждом усилии вдавливания наносили не менее 10 отпечатков твердости. После испытаний измеряли линейный размер длинной диагонали отпечатков в каждой серии с использованием металлографического микроскопа при увеличении 1600×. По результатам измерений определяли в каждой серии среднее значение микротвердости при ступенчатом возрастании усилия вдавливания Р, Н из соотношения
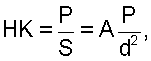
где S – площадь проекции отпечатка;
Р – усилие вдавливания в Н;
d – размер длинной диагонали в м.
Для каждого усилия вдавливания значения твердости усредняли по результатам измерений 10 отпечатков. После этого построили графики зависимости средних значений твердости HK1 и НК2 от усилия вдавливания для каждой серии испытаний (приведены на фиг.2) и определили значения критических нагрузок Pc1 и Рс2 при ориентации длинной диагонали отпечатков соответственно в направлениях параллельном и перпендикулярном внешней границе покрытия, которые составили Pc1=0,6Н, Рс2=0,4Н.
Затем в двух соседних точках покрытия провели вдавливание индентора Кнупа при усилиях, превышающих значения критических нагрузок Pc1=0,6H и Рс2=0,4Н, соответствующих ориентации длинной диагонали отпечатка параллельно и перпендикулярно внешней границе покрытия. После разгрузки измеряли размеры длинных диагоналей отпечатков, с учетом которых определили значений твердости HK1 (при направлении длинной диагонали отпечатка параллельно действию остаточных напряжений) и НК2 (при направлении длинной диагонали отпечатка перпендикулярно действию остаточных напряжений), которые приведены в таблице.
Затем определили разность значений твердости НК1-НК2 и с использованием нормировочного графика в координатах (НК1-НК2)- (приведен на фиг.3), построенного по стреле прогиба при электролитическом травлении образца с покрытием TiC в координатах (HK1-НК2)- определили величину остаточных напряжений (приведена в таблице).
Пример 2. Для проведения испытаний изготовили образец из стали Г13 в виде шайбы с плоскопараллельными противоположными поверхностями, которая имела диаметр 20 мм и толщину 2 мм. На изготовленный образец по стандартным технологическим режимам, используемым при прямом электронно-лучевом испарении, было нанесено покрытие из стали Х18Н10Т при температуре подложки 300°С. Затем из образца с покрытием изготовили поперечный шлиф по общепринятой методике и измерили толщину покрытия (приведена в таблице) так, как было описано в примере 1. Поперечный шлиф покрытия был подвергнут испытаниям с проведением последующих измерений и графических построений по результатам предварительных испытаний для определения значений критических нагрузок Pc1 и Рc2 так, как это было описано в примере 1. В каждой серии предварительных испытаний вдавливание индентора Кнупа осуществляли при ступенчатом возрастании усилия Р,Н(0,2<0,4<0,6<0,8<1,0<1,2<1,5) при переходе от точки к точке.
Расстояние от поверхности (Y) и усилия вдавливания, которые превышали в испытаниях критические значения Pc1 и Рс2 при ориентации длинной диагонали отпечатка твердости соответственно параллельно и перпендикулярно внешней границе покрытия, приведены в таблице. Величину остаточных напряжений находили графически по разности значений твердости HK1 и НК2, определенных в двух соседних точках покрытия при усилиях, превышающих значения критических нагрузок Pc1 и Рс2 так, как это было описано в примере 1. Для нахождения остаточных напряжений использовали нормировочный график в координатах (HK1-НК2)- (приведен на фиг.4), построенный при испытаниях стали Х18Н10Т на твердость в условиях одноосевого сжатия, при котором индентор Кнупа ориентировали длинной диагональю отпечатка параллельно и перпендикулярно направлению оси нагружения.
Для определения распределения остаточных напряжений по сечению покрытия статическое вдавливание проводили в двух соседних точках на различном расстоянии от поверхности. При испытаниях на каждом уровне для каждой ориентации длинной диагонали отпечатка относительно внешней границы покрытия наносили по 10 отпечатков твердости. Результаты испытаний приведены в таблице.
Пример 3. Для проведения испытаний изготовили образец из стали 15 в виде шайбы с плоскопараллельными противоположными поверхностями, которая имела диаметр 20 мм и толщину 5 мм. На изготовленный образец по стандартным технологическим режимам, используемым при электролитическом меднении, было нанесено медное покрытие при температуре электролита 50°С. Затем из образца с покрытием изготовили поперечный шлиф по общепринятой методике и измерили толщину покрытия (приведена в таблице) так, как было описано в примере 1. Поперечный шлиф покрытия был подвергнут испытаниям с проведением последующих измерений и графических построений по результатам предварительных испытаний для определения значений критических нагрузок Pc1 и Рс2 так, как это было описано в примере 1. В каждой серии предварительных испытаний вдавливание индентора Кнупа осуществляли при ступенчатом возрастании усилия Р, Н (0,1<0,2<0,4<0,6<0,8<1,0) при переходе от точки к точке.
Расстояние от поверхности (Y) и усилия вдавливания, которые превышали в испытаниях критические значения Pc1 и Рс2 при ориентации длинной диагонали отпечатка твердости соответственно параллельно и перпендикулярно внешней границе покрытия, приведены в таблице. Величину остаточных напряжений находили графически по разности значений твердости HK1 и НК2, определенных в двух соседних точках покрытия при усилиях, превышающих значения критических нагрузок Pc1 и Рс2 так, как это было описано в примере 1. Для нахождения остаточных напряжений использовали нормировочный график в координатах (HK1-НК2)- (приведен на фиг.4), построенный при испытаниях меди на твердость в условиях одноосевого сжатия, при котором индентор Кнупа ориентировали длинной диагональю отпечатка параллельно и перпендикулярно направлению оси нагружения.
Пример 4. Для проведения испытаний изготовили образец, представляющий собой многослойную композицию из последовательно чередующихся слоев молибдена и меди в виде шайбы с плоскопараллельными поверхностями, которая имела диаметр 20 мм и толщину 10,4 мм. При этом использовали стандартные технологические режимы, применяемые при прямом электронно-лучевом испарении, при температуре подложки 300°С. Затем из многослойного образца изготовили поперечный шлиф по общепринятой методике и измерили толщину слоев Cu и Мо (приведена в таблице) так, как было описано в примере 1. В поперечном шлифе образца были подвергнуты испытаниям слои меди с проведением последующих измерений и графических построений для определения значений критических нагрузок Pc1 и Рс2 так, как это было описано в примере 1. В каждой серии предварительных испытаний меди вдавливание индентора Кнупа осуществляли при ступенчатом возрастании усилия Р, Н (0,1<0,2<0,4,0,6<0,8<1,0) при переходе от точки к точке. Расстояние от границы слоя (Y) и усилия вдавливания, которые превышали в испытаниях критические значения Pc1 и Рс2 при ориентации длинной диагонали отпечатка твердости соответственно параллельно и перпендикулярно границе раздела слоев, приведены в таблице. Величину остаточных напряжений находили графически по разности значений твердости HK1 и HK2, определенных в двух соседних точках слоя меди при усилиях, превышающих значения критических нагрузок Pc1 и Рс2 так, как это было описано в примере 1. Для нахождения остаточных напряжений использовали нормировочный график в координатах (HK1-HK2)- (приведен на фиг.5), построенный при испытаниях меди на твердость в условиях одноосевого сжатия, при котором индентор Кнупа ориентировали длинной диагональю отпечатка параллельно и перпендикулярно направлению оси нагружения.
Таким образом, предлагаемое решение позволяет: повысить точность определения значений остаточных напряжений с использованием упругопластического внедрения пирамидального индентора Кнупа с основанием в виде ромба в любой части поперечного сечения покрытия или слоя материала и/или построить эпюру остаточных напряжений; расширить функциональные возможности способа путем исключения необходимости реализации контактного разрушения с образованием отпечатка твердости с развивающимися у его вершин хрупкими трещинами и за счет этого осуществить его применение для испытаний как керамических, так и металлических материалов; повысить точность определения остаточных напряжений за счет проведения испытаний при усилии вдавливания Р, превышающем критические значение Рс, и более точной регистрации линейных размеров геометрических параметров (например, размера длинной диагонали) отпечатков индентора Кнупа по сравнению с измерением истинной протяженности хрупких трещин у вершин отпечатка твердости; снизить трудоемкость способа за счет уменьшения количества геометрических параметров, необходимых для его реализации.
Способ может использоваться как в исследовательских целях для оценки механических свойств изделий и создании новых материалов, так и в промышленном производстве, например, в гальванических цехах для контроля качества электролитических покрытий.
Формула изобретения
1. Способ определения остаточных напряжений, включающий вдавливание пирамидального индентора в поперечное сечение покрытия или слоя материала до получения отпечатка твердости при ориентации его диагоналей ортогонально направлению действия остаточных напряжений, регистрируют усилие вдавливания, измеряют после разгрузки геометрические параметры отпечатка, с учетом которых определяют остаточные напряжения, отличающийся тем, что испытания проводят с использованием стандартного пирамидального индентора Кнупа с основанием в виде ромба, вдавливание индентора осуществляют в двух соседних областях покрытия или слоя материала при усилии вдавливания, превышающем критическое значение Рс, получают два отпечатка твердости с взаимно перпендикулярной ориентацией длинных диагоналей и, с учетом проведенных измерений, определяют значения твердости по отпечаткам, в которых длинная диагональ ориентирована соответственно параллельно HK1 и перпендикулярно НК2 направлению действия остаточных напряжений, а величину остаточных напряжений находят геометрически по разности значений твердости (HK1 и НК2) с использованием нормировочного графика, построенного независимым методом в координатах (HK1-HK2)-
2. Способ по п.1, отличающийся тем, что величину остаточных напряжений определяют с учетом значений твердости, которые получают в нескольких сечениях покрытия, находящихся на различном расстоянии друг от друга.
РИСУНКИ
|
|