|
(21), (22) Заявка: 2005127009/02, 26.08.2005
(24) Дата начала отсчета срока действия патента:
26.08.2005
(43) Дата публикации заявки: 10.03.2007
(46) Опубликовано: 27.09.2007
(56) Список документов, цитированных в отчете о поиске:
ТЕХНОЛОГИЯ ПРОКАТНОГО ПРОИЗВОДСТВА. Справочник, т.2, под редакцией Зюзина В.И., М., Металлургия, 1991 с.544-561. SU 1343632 А, 25.03.1985. SU 1047566 А, 15.10.1983. DE 4129988 А, 30.04.1992.
Адрес для переписки:
162600, Вологодская обл., г. Череповец, ул. Мира, 30, ОАО “Северсталь”, Заместителю технического директора-главного инженера – начальнику ЦТРК А.А. Немтинову
|
(72) Автор(ы):
Скорохватов Николай Борисович (RU), Глухов Владимир Васильевич (RU), Савиных Анатолий Федорович (RU), Смирнов Владимир Сергеевич (RU), Костылев Сергей Николаевич (RU), Голованов Александр Васильевич (RU), Тихонов Сергей Михайлович (RU), Савченко Владимир Сергеевич (RU), Орехов Денис Михайлович (RU), Хребтов Игорь Михайлович (RU)
(73) Патентообладатель(и):
Открытое акционерное общество “Северсталь” (ОАО “Северсталь”) (RU)
|
(54) СПОСОБ ЛИСТОВОЙ ПРОКАТКИ И УСТРОЙСТВО ДЛЯ ЕГО РЕАЛИЗАЦИИ
(57) Реферат:
Способ и устройство предназначены для повышения производительности процесса широкополосовой прокатки за счет снижения времени прокатки каждой заготовки. Центровка каждой заготовки перед входом в черновую группу клетей, производимая в ходе транспортировки по рольгангу, осуществляется за счет совмещения ее продольной оси с осью рольганга без остановки движения. На нижнюю лицевую поверхность заготовки воздействуют поперечными усилиями, ориентированными в направлении оси рольганга со стороны того края рольганга, к которому заготовка получила смещение при транспортировке. В широкополосовом прокатном стане, содержащем нагревательную печь, подающий рольганг с цилиндрическими роликами, группу черновых клетей и группу чистовых клетей на цилиндрической поверхности 5…10 роликов подающего рольганга, расположенных перед входом в первую клеть черновой группы, выполняют винтовые проточки трапециевидной конфигурации, сужающиеся к дну, с углом наклона боковой стенки к цилиндрической поверхности 30…60°, шириной по дну проточки 0,05…0,15 диаметра ролика, глубиной 0,025…0,05 диаметра ролика и с шагом 0,6…1,2 этого диаметра. Необходимые усилия воздействия на заготовки создаются за счет того, что с одного края ролика винтовые проточки выполняют по левой резьбе, а с другого – по правой резьбе, сходящимися к центру ролика, и каждый ролик устанавливают на рольганге таким образом, что с правой по направлению прокатки стороны рольганга расположен край ролика с левой резьбой, а с левой стороны – край с правой резьбой. 2 н.п. ф-лы, 3 ил., 1 табл.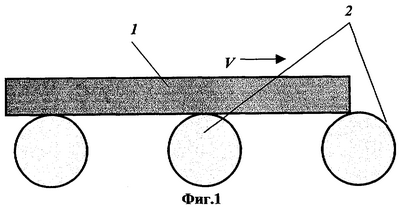
Изобретение относится к области обработки металлов давлением, в частности к технологии и оборудованию листовой прокатки на широкополосовом стане.
Известен способ листовой прокатки на широкополосовом стане, включающий транспортировку заготовки по подающему рольгангу от нагревательных печей на участок черновой группы стана, центровку заготовки, промежуточное обжатие нагретой заготовки в клетях черновой группы стана, с последующим обжатием заготовки до получения полосы заданного размера в клетях чистовой группы стана (1).
Для реализации предложенного способа используют устройство (широкополосовой прокатный стан), содержащее нагревательную печь, подающий рольганг с цилиндрическими роликами, группу черновых клетей с установленными перед ними направляющими линейками и группу чистовых клетей (1, 2).
Использование известного способа прокатки на широкополосовом стане характеризуется необходимостью центровки заготовки (совмещения продольной оси заготовки с осью рольганга) перед входом в черновую группу, после транспортировки по рольгангу. Для проведения этой операции на практике применяют специальные направляющие линейки. При отсутствии центровки возможно смещение заготовки к краю рольганга при входе в черновую группу клетей. При входе в валки вертикальной клети такое смещение приводит к перекосу заготовки в очаге деформации, а при входе в валки горизонтальной клети – к неравномерному обжатию и появлению поперечной разнотолщинности после прокатки. На центровку каждой заготовки направляющими линейками перед входом в первые клети черновой группы затрачивают от 5 до 10 сек, что, в конечном счете, отрицательно сказывается на суточной производительности стана. Это обуславливает актуальность разработки способа листовой прокатки и устройства для его реализации, обеспечивающего повышение производительности стана за счет проведения центровки заготовки перед входом в черновую группу клетей, без остановки ее поступательного движения по рольгангу.
Известен прием транспортировки листов на рольганге при прокатке на широкополосовых станах с их центровкой, производимой в процессе транспортирования (без остановки движения) посредством воздействия на нижнюю лицевую поверхность проката поперечными усилиями, ориентированными в направлении оси рольганга со стороны того края рольганга, к которому заготовка получила смещение при транспортировке (3).
Желаемым техническим результатом является повышение производительности процесса широкополосовой прокатки за счет снижения времени прокатки каждой заготовки благодаря центровке этой заготовки перед входом в черновую группу клетей, производимой в ходе ее транспортировки по рольгангу.
Для решения этой задачи в известном способе листовой прокатки, включающем транспортировку заготовки по подающему рольгангу от нагревательных печей на участок черновой группы стана, центровку заготовки, промежуточное обжатие нагретой заготовки в клетях черновой группы стана, с последующим обжатием заготовки до получения полосы заданного размера в клетях чистовой группы стана, указанный технический результат достигается тем, что в процессе транспортировки заготовки по подающему рольгангу производят совмещение ее продольной оси – центровку с осью рольганга без остановки движения, при этом на нижнюю лицевую поверхность указанной заготовки воздействуют поперечными усилиями, ориентированными в направлении оси рольганга со стороны того края рольганга, к которому заготовка получила смещение при транспортировке, посредством роликов рольганга, имеющих винтовые проточки трапециевидной конфигурации, сужающиеся к дну, с углом наклона боковой стенки к цилиндрической поверхности 30…60°, шириной по дну проточки 0,05…0,15 диаметра ролика, глубиной 0,025…0,05 диаметра ролика и с шагом 0,6…1,2 диаметра ролика.
Для реализации указанного способа в известном устройстве для листовой прокатки, содержащем нагревательную печь, подающий рольганг с цилиндрическими роликами, группу черновых клетей и группу чистовых клетей, указанный технический результат достигается тем, что на цилиндрической поверхности 5…10 роликов подающего рольганга, расположенных перед входом в первую клеть черновой группы, выполнены винтовые проточки трапециевидной конфигурации, сужающиеся к дну, с углом наклона боковой стенки к цилиндрической поверхности 30…60°, шириной по дну проточки 0,05…0,15 диаметра ролика, глубиной 0,025…0,05 диаметра ролика и с шагом 0,6…1,2 диаметра ролика, причем с одного края ролика винтовые проточки выполнены по левой резьбе, а с другого – по правой резьбе, сходящимися к центру ролика, и каждый ролик установлен на рольганге таким образом, что с правой стороны по направлению прокатки стороны рольганга расположен край ролика с левой резьбой, а с левой стороны – край с правой резьбой.
На фиг.1 представлен процесс транспортировки заготовки по рольгангу, на фиг.2 – схема действия усилий на нижнюю лицевую поверхность заготовки при смещении ее оси относительно оси рольганга в ходе транспортировки по этому рольгангу, согласно предложенным способу и устройству, на фиг.3 – схема действия усилий на нижнюю лицевую поверхность заготовки после совмещения ее оси с осью рольганга (центровки), согласно предложенным способу и устройству, на фиг.3а – конфигурация проточки, выполняемой на цилиндрической поверхности ролика, согласно предложенным способу и устройству.
Способ листовой прокатки реализуют следующим образом. Нагретую заготовку 1 поступательно перемещают по роликам 2 подводящего рольганга вдоль оси прокатки до входа в черновую группу стана (фиг.1). При транспортировке заготовка 1 может сдвигаться вбок по ширине рольганга S0. Иначе говоря, продольная ось А заготовки 1 может оказаться смещенной на величину относительно продольной оси А0 рольганга (фиг.2). Если заготовка 1 в таком положении входит в клети черновой группы, то готовый прокат характеризуется значительной поперечной разнотолщинностью. Следовательно, заготовку 1 надо без остановки ее движения сместить в направлении центра ролика 2 до совмещения оси А заготовки с осью А0 рольганга для устранения возможности появления разнотолщинности на готовом прокате. Для этого в процессе транспортировки заготовки по упомянутому рольгангу инициируют воздействие на нижнюю лицевую поверхность указанной заготовки 1 поперечных усилий, действующих в направлении оси рольганга со стороны его роликов 2. С этой целью на цилиндрической поверхности 5…10 роликов 2 подающего рольганга, расположенных перед входом в первую клеть черновой группы, выполняют винтовые проточки трапециевидной конфигурации (фиг.3а), сужающиеся к дну. С одного края ролика 2 винтовые проточки выполняют по левой резьбе, а с другого – по правой резьбе, сходящимися к центру ролика, и каждый ролик устанавливают на рольганге таким образом, что с правой по направлению прокатки стороны рольганга расположен край ролика с левой резьбой, а с левой стороны – край с правой резьбой. В данном случае (фиг.2) результирующее поперечное усилие, смещающее заготовку 1 вправо на данном ролике 2, может определяться, как F= F1– F2. По мере смещения заготовки 1 к оси рольганга величина F уменьшается до нуля ( F1= F2) при совпадении осей А0 и А (фиг.3). Таким образом, заготовка 1 одновременно с транспортировкой самопроизвольно занимает центральное положение на рольганге при входе в клети черновой и чистовой группы под действием поперечных усилий со стороны N1 (N2) роликов рольганга. Благодаря этому повышается производительность процесса, так как отпадает необходимость в специальной центровке заготовки перед входом в клети черновой и чистовой группы.
Для реализации предлагаемого технического решения на цилиндрической поверхности не менее N1=5 роликов 2 рольганга, расположенных перед входом в первую клеть черновой группы, выполняют винтовые проточки трапециевидной конфигурации (фиг.3а). Проточки выполняют сужающимися к дну, с углом наклона боковой стенки к цилиндрической поверхности =30…60°, шириной по дну проточки b=0,05…0,15 диаметра ролика D глубиной h=0,025…0,05 диаметра ролика D и с шагом S=0,6…1,2 этого диаметра, причем с одного края ролика винтовые проточки выполняют по левой резьбе, а с другого – по правой резьбе, сходящимися к центру ролика (ось А0). Каждый ролик устанавливают на рольганге таким образом, что с правой по направлению прокатки стороны рольганга расположен край ролика с левой резьбой, а с левой стороны – край с правой резьбой.
В ходе транспортировки заготовки по рольгангу вращение роликов обеспечивает продольное перемещение заготовки. При этом имеет место проскальзывание поверхности ролика относительно поверхности заготовки. Края проточек 3 действуют на нижнюю лицевую поверхность заготовки в процессе этого проскальзывания, формируя силы трения F1 и F2, действующие в поперечном направлении относительно оси рольганга. В случае смещения оси заготовки относительно оси рольганга к его краю (фиг.2) преобладают усилия трения F1, действующие со стороны этого края по направлению к центру рольганга. Под действием этих усилий заготовка в ходе своего продольного движения сдвигается к оси рольганга до совмещения с ней оси заготовки, т.е. в положение (фиг.3), при котором усилия поперечного трения F1 и F2, действующие на правую и левую часть заготовки, взаимно уравновешиваются. В этом случае заготовка занимает на рольганге позицию, требуемую для оптимального входа в клети черновой группы.
Применение способа поясняется примером его реализации. При производстве штрипса толщиной 12 мм из стали 17Г1С использовали заготовку размером 250×1700 мм. Сначала указанную заготовку транспортировали по подводящему рольгангу с диаметром роликов 300 мм к черновой группе стана 2000, используя предложенное техническое решение. После обжатия в черновой группе заготовку обжимали в чистовой группе стана 2000 до размера готовой полосы 12×1650 мм. В целом процесс прокатки производили в обычном режиме.
В рамках проведения опытов для транспортировки заготовки к черновой группе по подводящему рольгангу использовали N1 роликов со встречными спиральными проточками. С одного края ролика винтовые проточки выполняли по левой резьбе, а с другого – по правой резьбе, сходящимися к центру ролика. Каждый ролик устанавливали на рольганге таким образом, что с правой по направлению прокатки стороны рольганга был расположен край ролика с левой резьбой, а с левой стороны – край с правой резьбой.
Результаты прокатки показали, что применение предложенного способа прокатки и устройства для его реализации обеспечивает получение требуемого технического эффекта – повышение производительности стана за счет сокращения времени прокатки, т.е. прокатки без центровки заготовки при ее входе в клети черновой группы. При этом удавалось сохранять высокое качество продукции за счет отсутствия разнотолщинности проката. Установлено, что если винтовые проточки выполнены на цилиндрической поверхности малого числа роликов рольганга (менее 5), то центровка не будет успевать производиться, т.к. время прохождения по ним заготовки слишком мало. В то же время нет смысла использовать значительно большее число роликов с винтовыми проточками, т.к. центровка заготовки на середине рольганга не имеет смысла – даже если заготовка транспортируется по рольгангу будучи смещенной к его краю, это никак не сказывается на качестве продукции и темпе прокатки. Кроме того, при большом числе роликов с винтовыми проточками возрастает вероятность появления задиров на нижней лицевой поверхности заготовки. Трапециевидная конфигурация винтовых проточек объясняется необходимостью избежать застревания в их полости окалины, отслаивающейся от нижней лицевой поверхности заготовки. При слишком малом угле наклона боковой стенки проточки к цилиндрической поверхности ролика и малой ширине проточки по ее дну будет иметь место застревание окалины, тогда как при слишком большом угле край проточки не может эффективно сцепляться с неровностями нижней лицевой поверхности заготовки, что не позволяет получать значительные поперечные усилия, обеспечивающие смещение заготовки. При слишком большой ширине проточки по дну возможно появление отпечатков проточек на нижней лицевой поверхности заготовки, что негативно сказывается на качестве продукции. Слишком большой шаг винтовой проточки не обеспечивает большого числа точек контакта боковой стенки проточки с нижней лицевой поверхностью, достаточного для поперечного смещения заготовки. В то же время при очень малом шаге также возможно появление на нижней лицевой поверхности заготовки задиров и отпечатков проточек. Из полученных данных установлена правильность рекомендаций по выбору величины конструктивных и технологических параметров предложенного способа и устройства. Результаты опытов приведены в табл.1.
Таблица 1 |
№ п/п |
N1 |
H, мм |
° |
В, мм |
S, мм |
Результаты опыта |
1. |
2 |
12 |
45 |
30 |
300 |
Число роликов со спиральными проточками перед черновой группой слишком мало. Заготовка не успевает сместиться на ось рольганга и необходима ее дополнительная центровка линейками. |
2. |
5 |
12 |
45 |
30 |
300 |
Число роликов со спиральными проточками перед черновой группой достаточно для центровки заготовки. Время прокатки сокращается на 5…6 сек/шт. |
3. |
8 |
12 |
45 |
30 |
300 |
Число роликов со спиральными проточками перед черновой группой достаточно для центровки заготовки. Время прокатки сокращается на 5…6 сек/шт. |
4. |
10 |
12 |
45 |
30 |
300 |
Число роликов со спиральными проточками перед черновой группой достаточно для центровки заготовки, но задиры на нижней поверхности еще не появляются. Время прокатки сокращается на 5…6 сек/шт. |
5. |
12 |
12 |
45 |
30 |
300 |
Число роликов со спиральными проточками перед черновой группой достаточно для центровки заготовки. Время прокатки сокращается на 5…6 сек/шт. Однако при большом числе роликов на нижней поверхности заготовки возникают задиры от проточек. |
6. |
8 |
6 |
45 |
30 |
300 |
Глубина спиральных проточек перед чистовой группой слишком мала. Отслаивающаяся с нижней поверхности заготовки окалина быстро забивает полость проточки и ее эффективность снижается, время прокатки не сокращается. |
7. |
8 |
7,5 |
45 |
30 |
300 |
Глубина спиральных проточек перед чистовой группой достаточно велика, чтобы отслаивающаяся с нижней поверхности заготовки окалина не забивала полость проточки. Время прокатки сокращается на 5…6 сек/шт. |
8. |
8 |
15 |
45 |
30 |
300 |
Глубина спиральных проточек перед чистовой группой достаточно мала, чтобы на нижней поверхности заготовки не возникали задиры. Время прокатки сокращается на 5…6 сек/шт. |
9. |
8 |
17 |
45 |
30 |
300 |
Глубина спиральных проточек перед чистовой группой слишком велика. Время прокатки сокращается на 5…6 сек/шт. Однако при такой глубине проточек на нижней поверхности заготовки возникают задиры. |
10. |
8 |
12 |
20 |
30 |
300 |
Угол наклона боковой стенки проточки слишком мал, чтобы обеспечить появление поперечных сил трения, поэтому заготовка не успевает сместиться на ось рольганга и необходима ее дополнительная центровка линейками. |
12. |
8 |
12 |
30 |
30 |
300 |
Угол наклона боковой стенки проточки достаточен, чтобы обеспечить появление поперечных сил трения. Происходит центровка заготовки и время прокатки сокращается на 5…6 сек/шт. |
13. |
8 |
12 |
60 |
30 |
300 |
Угол наклона боковой стенки проточки достаточен, чтобы избежать появления задиров при контакте ролика с поверхностью заготовки. |
14. |
8 |
12 |
70 |
|
300 |
Угол наклона боковой стенки проточки слишком велик, что приводит к появлению задиров при контакте ролика с поверхностью заготовки. |
15. |
8 |
12 |
45 |
12 |
300 |
Ширина проточки слишком мала, что приводит к застреванию в ее полости окалины и снижению эффективности работы. Заготовка не успевает сместиться на ось рольганга и необходима ее дополнительная центровка линейками. |
16. |
8 |
12 |
45 |
15 |
300 |
Ширина проточки достаточна, чтобы не приводить к застреванию в ее полости окалины. Происходит центровка заготовки на рольганге. |
17. |
8 |
12 |
45 |
45 |
300 |
Ширина проточки достаточна, чтобы обеспечить отсутствие отпечатков проточки на нижней поверхности заготовки. |
18. |
8 |
12 |
45 |
50 |
|
Ширина проточки слишком велика, что приводит к повышению давления в зоне контакта заготовки и ролика и появлению на нижней поверхности заготовки отпечатков этой проточки, т.е. к появлению брака. |
19. |
8 |
12 |
45 |
30 |
150 |
Шаг проточек слишком мал, что приводит к повышению давления в зоне контакта заготовки и ролика и появлению на нижней поверхности заготовки отпечатков этой проточки, т.е. к появлению брака. |
20. |
8 |
12 |
45 |
30 |
180 |
Шаг проточек достаточен, чтобы обеспечить отсутствие отпечатков проточки на нижней поверхности заготовки. |
21. |
8 |
12 |
45 |
30 |
360 |
Шаг проточек достаточен, чтобы обеспечить появление поперечных сил трения. Происходит центровка заготовки и время прокатки сокращается на 5…6 сек/шт. |
22. |
8 |
12 |
45 |
30 |
400 |
Шаг проточек слишком велик и не обеспечивает появление поперечных сил трения, поэтому центровка не происходит. Заготовка не успевает сместиться на ось рольганга и необходима ее дополнительная центровка линейками. |
Использование предлагаемого способа листовой прокатки и устройства для его реализации позволяет повысить производительность за счет сокращения цикла прокатки при устранении операции центровки заготовки перед входом в клети черновой группы.
Литература
1. Технология прокатного производства. Справочник, т.2, п/ред. В.И.Зюзина, А.В.Третьякова, М., Металлургия, 1991, стр.544-561.
2. Литые прокатные валки. Н.А.Будагьянц, В.Е.Карсский, М., Металлургия, 1983, рис.1.
3. SU, №1343632 А, 30.04.1992, описание изобретения.
Формула изобретения
1. Способ листовой прокатки, включающий транспортировку заготовки по подающему рольгангу от нагревательных печей на участок черновой группы стана, центровку заготовки, промежуточное обжатие нагретой заготовки в клетях черновой группы стана с последующим обжатием заготовки до получения полосы заданного размера в клетях чистовой группы стана, отличающийся тем, что в процессе транспортировки заготовки по подающему рольгангу производят совмещение ее продольной оси – центровку с осью рольганга без остановки движения, при этом на нижнюю лицевую поверхность указанной заготовки воздействуют поперечными усилиями, ориентированными в направлении оси рольганга со стороны того края рольганга, к которому заготовка получила смещение при транспортировке, посредством роликов рольганга, имеющих винтовые проточки трапециевидной конфигурации, сужающиеся к дну, с углом наклона боковой стенки к цилиндрической поверхности 30-60°, шириной по дну проточки 0,05-0,15 диаметра ролика, глубиной 0,025-0,05 диаметра ролика и с шагом 0,6-1,2 диаметра ролика.
2. Устройство для листовой прокатки, содержащее нагревательную печь, подающий рольганг с цилиндрическими роликами, группу черновых клетей и группу чистовых клетей, отличающееся тем, что на цилиндрической поверхности 5-10 роликов подающего рольганга, расположенных перед входом в первую клеть черновой группы, выполнены винтовые проточки трапециевидной конфигурации, сужающиеся к дну, с углом наклона боковой стенки к цилиндрической поверхности 30-60°, шириной по дну проточки 0,05-0,15 диаметра ролика, глубиной 0,025-0,05 диаметра ролика и с шагом 0,6-1,2 диаметра ролика, причем с одного края ролика винтовые проточки выполнены по левой резьбе, а с другого – по правой резьбе, сходящимися к центру ролика, и каждый ролик установлен на рольганге таким образом, что с правой по направлению прокатки стороны рольганга расположен край ролика с левой резьбой, а с левой стороны – край с правой резьбой.
РИСУНКИ
|
|