|
(21), (22) Заявка: 2005136320/12, 22.11.2005
(24) Дата начала отсчета срока действия патента:
22.11.2005
(46) Опубликовано: 27.08.2007
(56) Список документов, цитированных в отчете о поиске:
RU 2174911 C1, 20.10.2001. RU 2211144 C2, 27.08.2003. RU 2186295 C2, 27.07.2002. RU 2251483 C2, 10.05.2005. RU 2245247 C2, 27.01.2005. RU 2212430 C1, 20.09.2003. RU 95107474 A1, 15.05.1995. US 4284616 A, 18.08.1981. BE 786454 A, 16.11.1972. LV 12890 A, 20.10.2002.
Адрес для переписки:
656066, г.Барнаул, ул. Глушкова, 30, кв.48, С.В.Горбунову
|
(72) Автор(ы):
Горбунов Сергей Владимирович (RU)
(73) Патентообладатель(и):
Горбунов Сергей Владимирович (RU)
|
(54) УСТРОЙСТВО ДЛЯ ПЕРЕРАБОТКИ ОТХОДОВ
(57) Реферат:
Изобретение относится к устройствам для переработки отходов и может быть использовано для переработки резиновых отходов, пластмассовых изделий, мусора и т.п. Устройство для переработки отходов включает реактор с устройством загрузки исходного сырья и системой трубопроводов, соединяющих реактор с конденсатором и охладителем. Реактор устройства смонтирован в полости нагревательной печи. Устройство снабжено механизмом подачи в нагревательную печь не сконденсировавшегося и выходящего из нагревательной печи газа, выполненным в виде двух замкнутых контуров. Один из контуров состоит из реактора, конденсатора, гидравлического затвора и насоса в цепочке оборудования возврата не сконденсировавшегося газа. Второй контур состоит из нагревательной печи, выходящего из нее трубопровода со входом пара, нагревателя и реактора. Оба контура и система подачи в нагревательную печь природного газа связаны с блоком управления. Устройство позволяет уменьшить количество вредных выбросов в атмосферу и имеет небольшую энергоемкость. 1 ил.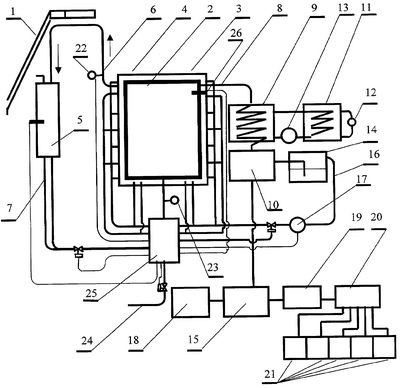
Изобретение относится к устройствам для переработки отходов и может быть использовано для переработки резиновых отходов, пластмассовых изделий, мусора и др. с уменьшенным количеством вредных выбросов.
Известен способ и устройство для получения бензина, дизельного топлива и сажи из отходов резины и/или отходов пластмассовых изделий (см. патент РФ №2142494, опубл. 10.12.99 г). Устройство содержит пиролизный аппарат, в который через питатель загружают исходные материалы, после чего в аппарате винтовой мешалкой материалы перемешиваются и подаются в аппарат каталитического крекинга, причем аппарат для десульфирования или дехлорирования включает абсорбционный аппарат, содержащий основание и абсорбционный аппарат с неподвижным слоем катализатора.
Известное устройство работает следующим образом. После загрузки исходных материалов и завершения пиролизной реакции получившуюся сажу удаляют спиральной мешалкой из пиролизного реакционного сосуда. Другие получившиеся вещества газовой фазы, имеющие более низкую молекулярную массу, подвергают в резервуаре десульфированию и/или денитрации, и/или дехлорированию. Оставшаяся сера, азот и хлор удаляются при прохождении через неподвижный слой катализатора, при этом одновременно проводится первичный каталитический пиролиз. Материалы газовой фазы помещают в аппарат для каталитического крекинга. Вещества, полученные каталитическим крекингом, разделяют, получая желаемые продукты. Винтовая мешалка, расположенная в пиролизном реакторе, согласно изобретению снижает коксование реагирующих веществ и усиливает проводимость тепла. В изобретении используется специальный катализатор, увеличивающий срок его службы.
К недостаткам известного устройства можно отнести сложность конструкции установки, ограниченные технологические возможности и возможность загрязнения атмосферы.
Известен способ переработки резиновых отходов и устройство для его осуществления – прототип. См. описание изобретения к заявке №95107474 от 15.05.95 года «Способ переработки резиновых отходов».
Устройство для реализации способа переработки резиновых отходов содержит камеру с заслонками, реактор с решеткой, парогенератор с пароперегревателем, который с помощью крана и трубопровода соединен с реактором. Паропровод выхода продуктов разложения с краном, холодильник для отделения масла, трубопровод и эжектор для подачи твердых продуктов разложения, охладитель, сепаратор, накопитель металла, пресс, насос, шлюзовую камеру, теплообменник, горелку, транспортер, емкость для масла, датчик температуры. В шлюзовую камеру при открытой заслонке подают резиновые отходы, которые при открывании промежуточной заслонки при закрытой шлюзовой камере попадают в реактор и задерживаются на его решетке. Затем в реактор подают перегретый водяной пар (300-600°С). Пар нагревает отходы, которые разлагаются с выделением летучих (газообразных), которые в смеси с паром поступают по трубопроводу в холодильник, где за счет охлаждения конденсируется масло, а газовую составляющую направляют в эжектор, где последняя смешивается с потоком перегретого водяного пара. Полученная смесь поступает в реактор. Твердые продукты разложения отходов подаются в дробилку, где их размалывают, затем в размолотые отходы подают насыщенный водяной пар, который охлаждает продукты разложения, а сам нагревается и подается в эжектор и сепаратор, где происходит отделение металла от углеродистого остатка. Металл при помощи транспортера из сепаратора подают в накопитель, а углеродистый остаток – в пресс. Одновременно из холодильника в пресс подают газы, которые, проходя через теплообменник нагреваются и, проходя через смесь углеродистого остатка, нагревают ее до температуры 100-500°С. Далее газы попадают в газомазутную горелку, где сжигаются, а нагретая спрессованная в брикеты масса подается в накопитель. Масло, выделяемое в холодильнике, насосом подается накопитель и в топливную смесь и горелку, обеспечивающую работу парогенератора. Масло с помощью насоса подают в шлюзовую камеру, куда одновременно подают очередную порцию отходов.
Известная конструкция устройства достаточная сложная, имеет большую энергоемкость.
Техническим результатом изобретения является устранение недостатков прототипа, в частности расширение технологических возможностей устройства, уменьшение вредных выбросов в атмосферу, снижение энергоемкости процесса и упрощение конструкции устройства.
Заявленный технический результат достигается тем, что в устройстве для переработки отходов, включающего реактор с устройством загрузки исходного сырья и системой трубопроводов, соединяющих реактор с конденсатором и охладителем, согласно изобретению, реактор устройства смонтирован в полости нагревательной печи, устройство снабжено механизмом подачи в нагревательную печь не сконденсировавшегося и выходящего из нагревательной печи газа, выполненным в виде двух замкнутых контуров, один из которых – реактор, конденсатор, гидравлический затвор, насос в цепочке оборудования возврата не сконденсировавшегося газа, второй – нагревательная печь, выходящий из нее трубопровод, со входом пара и нагревателем и реактор, при этом оба контура и система подачи в нагревательную печь природного газа связаны с блоком управления.
Признаки выполнения устройства, в котором реактор смонтирован в полости нагревательной печи и устройство снабжено механизмом подачи в нагревательную печь не сконденсировавшегося и выходящего из нагревательной печи газа, выполненным в виде двух замкнутых контуров, один из которых – реактор, конденсатор, гидравлический затвор, насос в цепочке оборудования возврата не сконденсировавшегося газа, второй – нагревательная печь, выходящий из нее трубопровод, со входом пара и нагревателем и реактор, при этом оба контура и система подачи в нагревательную печь природного газа связаны с блоком управления – являются признаками новыми, неочевидными, промышленно выполнимыми и направлены на достижение поставленной изобретением технической задачи расширения технологических возможностей устройства при более простой его конструкции.
На чертеже схематично представлено предлагаемое устройство.
Устройство для переработки отходов состоит из транспортерного загрузчика 1, реактора 2, размещенного в полости 3 нагревательной печи 4. Подогреватель 5 пара и газа смонтирован на кольцевом канале 6 (трубопроводе), выводящем из нагревательной печи отработанные газы и трубопроводе 7 подачи в реактор 2 водяного пара. Кольцевой канал 6 с одной стороны соединен с полостью 3 нагревательной печи 4, а с другой стороны – с полостью реактора 2. Через нагреватель 5 проходит кольцевой канал 6 и трубопровод 7 подвода водяного пара, при этом трубопровод 7 соединен с кольцевым каналом 6 после выхода трубопровода из нагревателя 5. Трубопровод 8 соединяет реактор 2 с конденсатором 9 паров газов, который на выходе из конденсатора 9 соединен с емкостью 10 для сбора конденсата. Для снижения температуры охлаждающей конденсатор жидкости (тосол) конденсатор 9 снабжен холодильником 11 с компрессором 12 и насосом 13 для циркуляции тосола. Емкость 10 для сбора конденсата связана с гидравлическим затвором 14, обеспечивающим улавливание и отделение газовой составляющей от ее мелких частиц и сепаратором 15. Гидравлический затвор 14 при помощи трубопровода 16 связан с насосом 17 механизма подачи газа к горелкам нагревательной печи. Сепаратор 15 связан трубопроводами с емкостями для воды 18, накопительным резервуаром 19 для хранения углеродного продукта, который в свою очередь связан с фракционной колонкой 20 и емкостями 21 для разделенных видов продукции. Трубопровод 6 снабжен двумя датчиками С02 – датчиком 22 на выходе и датчиком 23 на входе. Трубопровод 16 подачи несконденсировавшегося газа, кольцевой канал 6 подачи углекислого газа и трубопровод 24 подачи природного газа снабжены блоком управления 25, при помощи которого осуществляется своевременная подача или отключение от подачи соответствующего газа. Температура в реакторе 2 контролируется при помощи термодатчика 26, связанного с блоком управления 25.
Предлагаемое устройство работает следующим образом.
В реактор 2 загружается заданное количество отходов при помощи транспортерного загрузчика 1. Реактор 2 герметично закрывается. Для того чтобы запустить реактор 2 необходимо его нагреть до температуры 300-500°С. Для этого в нагревательную печь 4 по каналу 24 через форсунки (на чертеже не показаны) подается 2-5% природный газ для подогрева реактора 2, находящегося в полости нагревательной печи 4. При сгорании углеводородного природного газа в полости нагревательной печи 4 происходит получение инертного негорючего газа CO2-углекислого газа, а в реакторе осуществляется пиролиз отходов с образованием в том числе паров углеводородного газа, который после прохождения конденсатора 9, емкости 10 для сбора конденсата и гидравлического затвора 14 насосом 17 подается на сжигание в нагревательную печь 4 для подогрева реактора 2. Перед зажиганием газа в форсунках в нагревательной печи 4 при помощи блока управления 25 включается насос 17 для забора несконденсировавшихся горючих паров углеводородного газа с гидравлического затвора 14 с подачей под давлением газа на форсунки в нагревательную печь 4. При включении насоса 17 происходит забор и подача на форсунки образовавшегося в полости нагревательной печи 4 газа CO2. При этом из полости нагревательной печи 4 выходит нагретый до температуры 400-500°С газ CO2 и по кольцевому замкнутому каналу 6, на котором установлено два датчика определения содержания CO2, подается в реактор 2. При помощи датчика 22 определяется количество выходящего из нагревательной печи 4 газа CO2, а при помощи датчика 23 определяется количество входящего в реактор 2 газа, смешанного с водяными парами. Водяной пар, проходя по каналу 7 и через подогреватель 5, нагревается до температуры 400-500°С, смешивается с подогретым выходящим из нагревательной печи 4 газом CO2 и подается в реактор 2. Общее количество CO2 в смеси должно быть 65-83,3 об., потому как максимальное содержание газообразных продуктов при термическом разложении отходов с подачей инертных газов ограничивается пределами взрывоопасности таких смесей. Известно (см. Теоретические основы теплотехники. Справочник. Под общей редакцией А.В.Григорьева, В.М.Зорина – 2-е издание, переработка. – М.: Энергоатомиздат, 1988 год, с.378, табл.7.17), что добавка негорючих газов СО2 к горючему газу в определенных соотношениях приводит к исключению возможности зажигания таких смесей. Поскольку в газообразных продуктах (после выделения нефти) содержится в основном метан и его гомологи, то минимальная добавка СО2 с целью исключения воспламенения или взрыва составляет 83,3 об. от объема газообразных продуктов выделяемых отходами в реакторе. Такая цепочка работы пиролизного реактора способствует быстрому внешнему обогреву и подачи в полость реактора СО2 также обеспечивает одновременно внутренний подогрев и снижает взрывоопасность таких смесей. При достижении в реакторе температуры в 300°С начинается минимальная деструкция отходов с повышением температуры отходов до рабочей 500-600°С происходит максимальная деструкция отходов и максимальный выход газообразных продуктов. Выделенный из отходов газ по трубопроводу 8 поступает в конденсатор 9. Проходя через змеевик конденсатора 9, газообразная смесь конденсируется в синтетическую нефть, которая стекает в емкость для сбора конденсата, а остатки несконденсировавшихся газов после конденсатора 9 выходят из емкости 10 и поступают в гидравлический затвор 14. Далее газообразная смесь по трубопроводу 16 под давлением, создаваемым насосом 17, подается на форсунки нагревательной печи 4. Синтетическая нефть из емкости 10 для сбора конденсата подается в сепаратор 15, где происходит разделение на нефть и воду. Затем вода из емкости 18 очищается и поступает по трубопроводу через подогреватель для получения водяного пара. Накопленная в резервуаре 19 нефть передается во фракционную колонку 20, где и происходит ее разложение на фракции, бензин, керосин, солярки, мазут и др.
На заключительном этапе переработки отходов количество несконденсировавшегося газа, подаваемого на форсунки нагревательной печи, снижается и процесс прекращается. Производится удаление отходов из реактора и осуществляется последующая загрузка реактора. Далее работа предлагаемого устройства продолжается с подачи на форсунки нагревательной печи природного газа.
Предлагаемое устройство позволит перерабатывать не только отработанные резинотехнические изделия, но и бытовые отходы.
В настоящее время автором осуществляется разработка технической документации на предлагаемое устройство, после чего будет решаться вопрос об организации производства переработки отходов.
Формула изобретения
Устройство для переработки отходов, включающее реактор с устройством загрузки исходного сырья и системой трубопроводов, соединяющих реактор с конденсатором и охладителем, отличающееся тем, что реактор устройства смонтирован в полости нагревательной печи, устройство снабжено механизмом подачи в нагревательную печь не сконденсировавшегося и выходящего из нагревательной печи газа, выполненным в виде двух замкнутых контуров, один из которых – реактор, конденсатор, гидравлический затвор, насос в цепочке оборудования возврата не сконденсировавшегося газа, второй – нагревательная печь, выходящий из нее трубопровод, со входом пара и нагревателем и реактор, при этом оба контура и система подачи в нагревательную печь природного газа связаны с блоком управления.
РИСУНКИ
|
|