|
(21), (22) Заявка: 2005102673/02, 03.02.2005
(24) Дата начала отсчета срока действия патента:
03.02.2005
(43) Дата публикации заявки: 10.07.2006
(46) Опубликовано: 10.08.2007
(56) Список документов, цитированных в отчете о поиске:
Журнал “Кузнечно-штамповое производство”, №4, 1986, с.40. SU 1311892 A1, 23.05.1987. SU 1183333 A1, 07.10.1985. RU 2127195 C1, 10.03.1999. ЕР 0157509 А1, 09.10.1985. US 4881430 A, 21.11.1989.
Адрес для переписки:
601900, Владимирская обл., г. Ковров, ул. Труда, 4, ОАО “Завод им. В.А. Дегтярева”, ОПЛИР
|
(72) Автор(ы):
Афонин Борис Владимирович (RU), Воронин Павел Вячеславович (RU), Горбачев Александр Евгеньевич (RU)
(73) Патентообладатель(и):
Открытое акционерное общество “Завод им. В.А. Дегтярева” (RU)
|
(54) СПОСОБ ПОЛУЧЕНИЯ ЗАГОТОВОК ДАМАССКОЙ СТАЛИ
(57) Реферат:
Способ может быть использован для изготовления оружия (клинков, сабель, ножей и т.д.), а также для изготовления инструмента для обработки различных материалов (кожи, пластмассы, древесины). Полученные механической обработкой пластины разных марок стали обезжиривают и, чередуя, собирают в стопку. Стопку сжимают в приспособлении, конструктивные элементы которого имеют разные коэффициенты линейного расширения. Приспособление со стопкой пластин помещают в печь и получают монолитную заготовку путем диффузионной сварки в безокислительной среде с двумя изотермическими выдержками. Проводят свободную ковку полученной монолитной заготовки. Способ позволяет обеспечить качество сварки и получить цельную заготовку дамасской стали независимо от химического состава стали свариваемых пластин. 1 ил.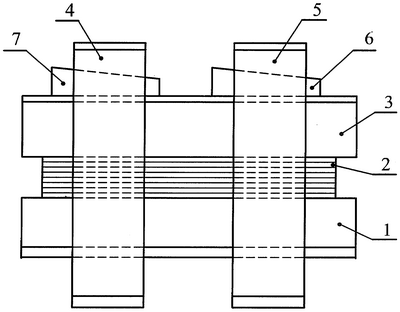
Изобретение относится к области машиностроения и может быть использовано для изготовления оружия (клинков, сабель, ножей и т.д.), а также для изготовления инструмента для обработки различных материалов (кожи, пластмассы, древесины).
Известен способ получения заготовок дамасской стали, при котором пластины (полосы, прутки) из разных типов стали складываются в стопку, стопку нагревают, затем проковывают, при этом пластины свариваются между собой (см. журнал “Кузнечно-штамповочное производство”, 1986 г., №4, стр.40). Способ взят за прототип.
Недостатки способа в том, что трудно сварить ковкой разные по химическому составу, имеющие неодинаковые коэффициенты линейного расширения, стали в один пакет, необходимо точно выдерживать температуру нагрева, режимы ковки и охлаждения, использовать флюсы, знать технологию их применения, а ковку производят с определенной силой и частотой.
Задачей предлагаемого изобретения является создание новой технологии получения дамасской стали с резким ее упрощением, с одновременным снижением трудоемкости и себестоимости, кординальным сокращением ручного труда и возможности постановки получения изделий из дамасской стали на поток.
Технический результат, получаемый при осуществлении изобретения, заключается в надежном обеспечении качества сварки, получении цельной заготовки без внутренних дефектов независимо от химического состава сталей свариваемых пластин с заведомо известными режимами свободной ковки сваренной заготовки без использования специальных флюсов.
Указанный технический результат достигается тем, что в способе получения заготовок дамасской стали, включающем сборку пластин разных марок стали в стопку и последующую свободную ковку, новым является то, что перед ковкой получают монолитную заготовку путем соединения пластин диффузионной сваркой в безокислительной среде с двумя изотермическими выдержками с использованием приспособления для сжатия, выполненного с различными коэффициентами линейного расширения его конструктивных элементов.
На основании вышеизложенного можно сделать вывод о том, что предлагаемое изобретение обладает “новизной” и “изобретательским уровнем”.
Способ осуществляется следующим образом.
Для создания заготовки дамасской стали выбираем низкоуглеродистую пластичную сталь 10 со средним содержанием углерода 0,1% и инструментальную высокоуглеродистую сталь с содержанием углерода 1% с тем, чтобы получить волнистый узор на поверхности изделия и обеспечить высокий комплекс механических и режущих свойств, высокую твердость и вязкость.
Механической обработкой изготовляют пластины толщиной 2 мм из полос сталей 10 и ХВГ. Более экономично изготовлять пластины из тонкой ленты, что резко снизит трудоемкость изготовления заготовок дамасской стали за счет сокращения операций диффузионной сварки, свободной ковки, разрезки кованных заготовок, шлифовки и т.д. Изготовленные пластины обезжиривают и, чередуя стали 10 и ХВГ, собирают в стопку. Затем стопку подвергают диффузионной сварке в твердом состоянии. Диффузионная сварка в твердом состоянии – способ получения монолитного соединения, образовавшегося вследствие возникновения связей на атомном уровне, появляющихся в результате максимального сближения контактных поверхностей за счет локальной пластической деформации при повышенной температуре, обеспечивающей взаимную диффузию в поверхностных слоях соединяемых материалов. Диффузионная сварка осуществляется в вакууме. Одно из наиболее важных преимуществ диффузионной сварки – высокое качество получаемых сварных соединений. При сварке в вакууме поверхность пластин не только предохраняется от дальнейшего загрязнения, например окисления, что неизменно происходит при кузнечной сварке, но и очищается в результате возгонки или растворения окислов. В результате в местах сварки отсутствуют непровары, поры, окисные включения и другие дефекты. Диффузионная сварка в вакууме фактически единственный надежный способ соединения металлов с разными температурными характеристиками, малопластичных, тугоплавких. нерастворимых друг в друге. В нашем случае для диффузионной сварки стопки пластин, набранных из сталей 10 и ХВГ, спроектировано и изготовлено специальное приспособление, которое поясняется чертежом. На нижнем бруске 1 установлена стопка 2 обезжиренных стальных пластин, на которой размещен верхний брусок 3. Хомуты 4 и 5 схватывают бруски 1 и 3 со стопкой 2 пластин. Между верхним бруском 3 и хомутами 4, 5 вбиты клинья 6 и 7. Хомуты изготовлены из стали 10, бруски и клинья – из стали 12Х18Н10Т. Диффузионная сварка набранных в стопку пластин осуществляется в вакуумной печи СЭВ 3.3/11 следующим образом. Хомуты 4 и 5 устанавливают на расстоянии друг от друга, обусловленном габаритами рабочего пространства печи. На основание хомутов 4 и 5 укладывают нижний брусок 1, на котором размещают собранную стопку 2 пластин. Верхний брусок 3 укладывают на стопку 2 пластин и сжимают стопку 2, вбивая ударом клинья 6 и 7 между верхним бруском 3 и хомутами 4,5. Приспособление со стопкой помещают в печь СЭВ 3.3/11, вакуумируют ее, нагревают приспособление со стопкой пластин до 800°С (температура соответствует критической точке-хомутов АС1), выдерживают 30 минут для выравнивания температуры всех элементов приспособления. Затем нагревают приспособление со стопкой пластин до 1100°С и выдерживают 5-10 минут. Поскольку стопку пластин сжимают ударом перед нагревом, во время нагрева до температуры АС1, во время выдержки при этой температуре и при дальнейшем нагреве до 1100°С за счет того, что конструктивные элементы имеют разные коэффициенты линейного расширения, создается требуемое давление, вследствие которого происходит максимальное сближение контактных поверхностей стальных пластин, зажатых в приспособлении, возникают связи на атомном уровне. В результате после охлаждения приспособления из него извлекают монолитную заготовку высокого качества без внутренних дефектов.
Полученную монолитную заготовку подвергают свободной ковке по режиму стали ХВГ, нагрев под ковку 1060-1080°С, окончание ковки 850-870°C, охлаждение замедленное (см”. Марочник сталей и сплавов” под ред. В.Г.Сорокина, Москва, Машиностроение, 1989 г., стр.382). Сталь 10, входящая в состав монолитной заготовки, имеет другие режимы ковки (см. “Марочник сталей и сплавов” под ред. В.Г.Сорокина, Москва, Машиностроение, 1989 г., стр.45). Температура начала ковки 1280-1300°С, температура окончания ковки 690-710°С. Охлаждение умеренное на воздухе. Такой режим ковки для стали ХВГ неприемлим по причинам: усиливается окисление и обезуглераживвание, способность к деформации снижается, а окончание ковки при более низкой температуре и ускоренном охлаждении может привести к образованию трещин. В то же время при температуре 1280-1300°C сталь 10 настолько пластична, что процесс утонеения монолитной заготовки будет происходить в основном за счет стали 10, что неприемлимо. С другой стороны, пластичность стали 10 вполне достаточна для деформирования ее при температуре 1060-1080°С. Температура окончания ковки 850-870°С и замедленное охлаждение не ухудшают качества стали 10. Свободную ковку монолитной заготовки ведут интенсивно, добиваясь максимально возможного ее утончения, при этом, естественно направление волокна в заготовке изменяется самым причудливым образом, так как металл при осадке течет как в длину, так и в ширину. Применение специальных флюсов в нашем случае не требуется. После охлаждения кованную заготовку разрезают на равные части и шлифуют с двух сторон. Затем полученные пластины обезжиривают, укладывают в стопку, зажимают в приспособлении и производят диффузионную сварку по указанному выше режиму в вакуумной печи СЭВ 3.3/11. После охлаждения монолитную заготовку вновь подвергают свободной ковке, но температуру нагрева монолитной заготовки повышают под свободную ковку примерно на 90°С. Температурный режим окончания ковки и скорость охлаждения кованой заготовки не изменяют. Повышение температуры нагрева монолитной заготовки перед второй и последующими операциями свободной ковки связано с процессом диффузии, в первую очередь углерода в направлении сталь ХВР сталь 10. Диффузия углерода происходит как в процессе диффузионной сварки, так и при нагреве заготовки под свободную ковку, причем скорость диффузии углерода высокая, температура нагрева при диффузионной сварке и нагреве под свободную ковку превышает 1000°С. Как показали исследования, содержание углерода в стали 10 повышается примерно на 0,4%, соответственно в стали ХБГ содержание углерода понижается на 0,4% уже после второй диффузионной сварки. Диффузия других элементов незначительна. Поэтому монолитная заготовка после второй диффузионной сварки представляет чередование пластин, близких по химическому составу к стали 50 и стали 6ХВГ. Свободную ковку монолитной заготовки после второй операции диффузионной сварки, естественно, производят по режиму стали 6ХВГ. Температура начала ковки 1150-1170°С. Сталь 50 значительно пластичнее стали 6ХВГ, поэтому свободная ковка стали 50 по режиму стали 6ХВГ не ухудшает ее качества.
После свободной ковки заготовку вновь разрезают на равные части, шлифуют с двух сторон, полученные пластины обезжиривают, собирают в стопку, укладывают стопку в приспособление, зажимают ударом с помощью клиньев, производят диффузионную сварку по указанному режиму. Полученную монолитную заготовку подвергают свободной ковке по режиму стали 6ХВГ. Чередование диффузионной сварки и свободной ковки продолжают до тех пор, пока толщина одного легированного слоя стали в прокованной заготовке будет менее 10 мм. В готовом изделии количество слоев из разных марок стали должно быть не менее 500. В этом случае получают самые затейливые узоры на поверхности изделия, высокие механические и режущие свойства, высокую твердость с большим запасом вязкости после упрочняющей термической обработки. Увеличение слоев в изделии выше 500 улучшает свойства дамасской стали, но возрастает трудоемкость ее изготовления.
После окончания свободной ковки заготовку дамасской стали отжигают по режиму стали 6ХВГ, исправляя структуру сталей. Нагрев 800-810°С, охлаждение 50°град/час до 600°С, затем на воздухе. Отжиг заготовки по режиму стали 6ХВГ благоприятный и для стали 50. После отжига заготовка легко поддается механической обработке.
Предложенный способ позволяет обеспечить качество сварки и получить цельную заготовку дамасской стали независимо от химического состава свариваемых пластин.
Формула изобретения
Способ получения заготовок дамасской стали, включающий сборку пластин разных марок стали в стопку и последующую свободную ковку, отличающийся тем, что перед ковкой получают монолитную заготовку путем соединения пластин диффузионной сваркой в безокислительной среде с двумя изотермическими выдержками с использованием приспособления для сжатия, выполненного с различными коэффициентами линейного расширения его конструктивных элементов.
РИСУНКИ
|
|