|
(21), (22) Заявка: 2005132431/28, 20.10.2005
(24) Дата начала отсчета срока действия патента:
20.10.2005
(46) Опубликовано: 27.06.2007
(56) Список документов, цитированных в отчете о поиске:
RU 1418565 C1, 23.08.1988. RU 2178140 С1, 20.01.2002. RU 2151999 С1, 27.06.2000. US 4198165 A, 15.04.1980.
Адрес для переписки:
603011, г.Нижний Новгород, ул.Журова, 2, ГУП НО ВНИИЖТ, директору Е.С.Ерилину
|
(72) Автор(ы):
Красильников Владимир Сергеевич (RU), Ерилин Евгений Сергеевич (RU), Фогель Александр Львович (RU)
(73) Патентообладатель(и):
Государственное унитарное предприятие Нижегородское отделение-дочернее предприятие Всероссийского научно-исследовательского института железнодорожного транспорта Министерства путей сообщения Российской Федерации (RU)
|
(54) СПОСОБ КОНТРОЛЯ ДИАМЕТРОВ ДЕТАЛИ
(57) Реферат:
Способ контроля диаметров детали включает вращение детали, сканирование ее в поперечной плоскости пучком излучения лазерного источника, фиксацию по границам теневого участка точек касания пучком излучения поверхности детали и определение диаметра по расстоянию между этими точками касания. Измерение диаметров производят в каждом из двух заданных поперечных сечений детали во взаимно перпендикулярных продольных плоскостях детали, вдоль образующей детали в прямом и обратном направлениях перемещают пучок излучения лазерного источника, при этом скорости перемещения пучка излучения и вращения детали синхронизируют с возможностью измерения диаметров в прямом направлении – во время первого полуоборота детали, а в обратном направлении во время второго полуоборота детали, причем пучок излучения лазерного источника, представляет собой ряд параллельных лучей. Технический результат – повышение точности контроля и сокращение времени контроля. 2 ил.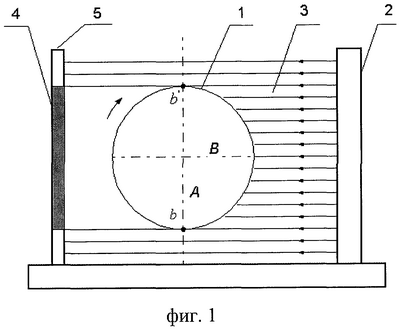
Изобретение относится к измерительной технике и может быть использовано для контроля диаметров деталей, в частности на железнодорожном транспорте, для измерения диаметров рабочих поверхностей колесных осей транспортных средств.
Наиболее близким по технической сущности и достигаемому эффекту является способ контроля диаметров детали (см. авторское свидетельство № 1418565 “Устройство для измерения диаметров детали”, М. кл. 4 G01В 11/08, опубл. 23.08.88. Бюл. № 31) который включает вращение детали, сканирование ее в поперечной плоскости пучком излучения лазерного источника, фиксацию по границам теневого участка точек касания пучком излучения поверхности детали и определение диаметра по расстоянию между этими точками касания.
Недостатком способа является невысокая точность контроля, связанная с погрешностями, вносимыми механическими составляющими устройства, а именно: биением оси вращения детали; неточностью выполнения изгиба световода по дуге окружности и щели в покрытии световода вдоль его образующей; неточностью совмещения оси вращения детали с прямой линией, проходящей через центр сканирования и торец световода; неточностью установки вращающегося зеркала относительно измеряемой детали. Кроме того, в данном способе отсутствует возможность учета конусности и овальности детали.
Другим недостатком способа является невысокая экспрессность контроля большого количества деталей, связанная с затратами времени на вращение детали на полный оборот для контроля диаметра в одном сечении.
Задачей настоящего изобретения являются повышение точности контроля и сокращение времени контроля.
Поставленная задача решается тем, что в способе контроля диаметров детали, включающем вращение детали, сканирование ее в поперечной плоскости пучком излучения лазерного источника, фиксацию по границам теневого участка точек касания пучком излучения поверхности детали и определение диаметра по расстоянию между этими точками касания, измерение диаметров производят в каждом из двух заданных поперечных сечений детали во взаимно перпендикулярных продольных плоскостях детали, вдоль образующей которой в прямом и обратном направлениях перемещают пучок излучения лазерного источника, при этом скорости перемещения пучка излучения и вращения детали синхронизируют с возможностью измерения диаметров в прямом направлении во время первого полуоборота детали, а в обратном направлении во время второго полуоборота детали, причем пучок излучения лазерного источника представляет собой ряд параллельных лучей.
Такое выполнение способа, при котором измерение диаметров производят в каждом из двух заданных поперечных сечений детали во взаимно перпендикулярных продольных плоскостях детали, вдоль образующей которой в прямом и обратном направлениях перемещают пучок излучения лазерного источника, при этом скорости перемещения пучка излучения и вращения детали синхронизируют с возможностью измерения диаметров в прямом направлении во время первого полуоборота детали, а в обратном направлении – во время второго полуоборота детали, причем пучок излучения лазерного источника, представляет собой ряд параллельных лучей, позволяет уменьшить погрешности, вносимые механическими составляющими устройства, сократить время контроля большого количества деталей за счет использования времени одного полного оборота детали для измерения диаметров детали в двух сечениях и в двух взаимно перпендикулярных плоскостях, что, кроме того, путем сравнения диаметров в указанных сечениях и плоскостях дает возможность учитывать конусность и овальность детали и тем самым повысить точность контроля.
На фиг.1 представлено схематическое изображение облучения поверхности детали плоским пучком параллельных оптических лучей лазерного источника излучения.
На фиг.2 – схематическое изображение траектории движения одной из двух точек касания пучком лучей лазерного источника излучения поверхности детали (пунктиром изображена траектория движения той же точки касания обратной стороны поверхности детали при ее повороте на 180°).
Устройство для реализации способа контроля диаметров детали 1 содержит лазерный источник 2 излучения, установленный с одной стороны детали 1 для сканирования пучком 3 ряда параллельных лучей (далее пучок 3 лучей) поверхности детали 1 в ее поперечном направлении. С другой стороны детали 1 для фиксации по границам теневого участка 4 двух точек касания b, b’ или е, е’ пучком 3 лучей поверхности детали 1 по диаметру детали установлен регистратор 5 теневого изображения. На поверхности детали 1 заданы поперечные сечения 6, 7 для определения диаметров D1, D2, D3, D4 по расстоянию между точками касания b, b’ или е, е’.
Способ контроля диаметров детали осуществляют следующим образом.
Деталь 1 вращают с постоянной угловой скоростью. Пучок 3 лучей лазерного источника 2 излучения направляют перпендикулярно продольной оси детали 1. Точки измерения диаметра D цилиндрической поверхности детали 1 являются точками (траектория движения одной из которых показана на фиг.2) касания поверхности детали 1 пучком 3 параллельных лучей. Пучок 3 лучей перемещают из точки а к сечению 6 так, чтобы перед совмещением с этим сечением линейная скорость пучка 3 лучей стала равной заданной скорости. В момент совмещения пучка 3 лучей с сечением 6 регистратором 5 теневого изображения фиксируют значение диаметра D1 детали по точкам (b, b’) касания пучком 3 лучей поверхности детали 1. Это значение соответствует измерению в плоскости А, когда точка b находится в самом низком положении, а точка b’ соответственно в самом высоком положении. Далее, пучок 3 лучей перемещают от сечения 6 в сечение 7. При этом деталь 1 поворачивают на угол 90° в другую взаимно перпендикулярную продольную плоскость В и измерение диаметра D2 по точкам с, c’ происходит в плоскости В в тот момент, когда точка с оказывается в самом низком положении в точке е, а точка с’ – в положении е’. Далее пучок 3 лучей перемещают за пределы интервала между сечениями 5 и 6 до точки d, в которой направление перемещения пучка 3 лучей меняют на обратное. Процесс измерений продолжают во время второй половины оборота детали в ту же сторону. Сначала измеряют значение диаметра D3 в точках е, е’ в сечении 6 в плоскости А, когда точка е оказывается в самом низком положении. После этого пучок 3 лучей перемещают в сечение 6 и измеряют значение диаметра D4 в точках f, f’ в плоскости В, когда точка f находится в самом низком положении. После прохождения пучком 3 лучей сечения 6 процесс измерений прекращают, а пучок 3 лучей доводят до точки а. По измеренным значениям диаметров D1, D2, D3, D4 могут быть вычислены средние диаметры в заданных сечениях и среднее значение диаметра детали, при этом при сравнении диаметров в двух сечениях 6 и 7 определяют наличие конусности, а по максимальному и минимальному значению диаметров в одном сечении 6 (или 7) детали 1 судят об овальности детали.
Формула изобретения
Способ контроля диаметров детали, включающий вращение детали, сканирование ее в поперечной плоскости пучком излучения лазерного источника, фиксацию по границам теневого участка точек касания пучком излучения поверхности детали и определение диаметра по расстоянию между этими точками касания, отличающийся тем, что измерение диаметров производят в каждом из двух заданных поперечных сечений детали во взаимно перпендикулярных продольных плоскостях детали, вдоль образующей которой в прямом и обратном направлениях перемещают пучок излучения лазерного источника, при этом скорости перемещения пучка излучения и вращения детали синхронизируют с возможностью измерения диаметров в прямом направлении во время первого полуоборота детали, а в обратном направлении во время второго полуоборота детали, причем пучок излучения лазерного источника представляет собой ряд параллельных лучей.
РИСУНКИ
|
|