(21), (22) Заявка: 2005135214/06, 15.11.2005
(24) Дата начала отсчета срока действия патента:
15.11.2005
(46) Опубликовано: 10.06.2007
(56) Список документов, цитированных в отчете о поиске:
DE 2626446 A1, 15.12.1977. GB 1254407 A, 24.11.1971. RU 2236047 C1, 10.09.2004. RU 2229176 C2, 20.05.2004.
Адрес для переписки:
142100, Московская обл., г. Подольск, ул. Железнодорожная, 24, ФГУП “Научно-исследовательский институт Научно-производственное объединение “Луч”
|
(72) Автор(ы):
Курбаков Сергей Дмитриевич (RU), Черников Альберт Семенович (RU), Голубев Игорь Евгеньевич (RU), Кадарметов Игорь Мунирович (RU)
(73) Патентообладатель(и):
Федеральное государственное унитарное предприятие “Научно-исследовательский институт Научно-производственное объединение “Луч” (RU)
|
(54) СПОСОБ ПОЛУЧЕНИЯ МИКРОТВЭЛОВ ЯДЕРНОГО РЕАКТОРА
(57) Реферат:
Изобретение относится к области ядерной энергетики, в частности к микротвэлам ядерного реактора с четырехслойным защитным покрытием. На топливные микросферы последовательно осаждают слои покрытия в кипящем слое. Первый слой низкоплотного пироуглерода осаждают пиролизом ацетилена с концентрацией в смеси с аргоном 50 об.% при температуре 1450°С. 85-95% второго слоя из высокоплотного пироуглерода осаждают пиролизом смеси ацетилена с концентрацией в смеси с аргоном 40,0-43,0 об.% и пропилена с концентрацией в смеси с аргоном 30,0-27,0 об.% при температуре 1300°С, а 5-15% покрытия осаждают пиролизом пропилена с концентрацией в смеси с аргоном 5,0-10,0 об.% с добавкой 0,5-1,5 об.% метилтрихлорсилана. Третий слой из карбида кремния осаждают пиролизом метилтрихлорсилана с концентрацией в смеси водород-аргон 2,5-3,0 об.% при температуре 1500°С. После осаждения проводят его обработку в водороде при температуре 1750-1800 С в течение 20-30 мин. 90-95% четвертого слоя осаждают пиролизом смеси ацетилена с концентрацией в смеси с аргоном 40,0-43,0 об.% и пропилена с концентрацией в смеси с аргоном 30,0-27,0 об.% при температуре 1300°С. А после осаждения 90-95% толщины пироуглеродного покрытия четвертого слоя 5-10% покрытия осаждают пиролизом пропилена с концентрацией в смеси с водородом 3,0-5,0 об.%. Данное техническое решение позволяет повысить ресурс эксплуатации микротвэлов ядерного реактора за счет уменьшения повреждаемости покрытий на стадии их изготовления и эксплуатации. 1 табл., 6 ил.
Изобретение относится к области ядерной энергии, в частности к микротвэлам высокотемпературных газоохлаждаемых реакторов (ВТГР) повышенной безопасности эксплуатации.
Одним из путей повышения безопасности эксплуатации ядерных реакторов является применение тепловыделяющих элементов (твэлов), в которых топливо локализовано в микрообъеме сферических частиц из делящегося материала, каждая из которых имеет защитное покрытие из неделящегося материала с характеристиками, оптимизированными в соответствии с типом реактора и условиями его эксплуатации [Котельников Р.Б., Башлыков С.Н., Каштанов А.И., Меньшикова Т.С. Высокотемпературное ядерное топливо. Изд. 2-е. М.: Атомиздат, 1978, 432 с.].
Независимо от вида конструкции твэлов ядерное топливо во всех типах ВТГР находится в форме микросферических частиц со слоями защитного покрытия так называемых микротвэлов-МТ.
В МТ современных ВТГР число защитных слоев на топливной микросфере (ТМ), как правило, не превышает четырех (фиг.1):
– первый – низкоплотный (буферный) слой пироуглерода (РуС);
– второй – внутренний высокоплотный изотропный РуС;
– третий – карбидокремниевый (SiC);
– четвертый – наружный высокоплотный изотропный РуС.
Основной задачей буферного РуС является обеспечение свободного объема газообразных продуктов деления (ГПД) и распухающей под облучением ТМ, уменьшение температурных напряжений вследствие различий коэффициента линейного температурного расширения материала ТМ и последующих покрытий, а также предохранение внутреннего РуС и SiC слоя от повреждения осколками деления.
Внутренний высокоплотный изотропный РуС является барьером для ГПД и большинства твердых продуктов деления (ТПД). Его задачей является защита слоя SiC от воздействия осколков деления и защита ТМ от проникновения хлора при осаждении слоя SiC.
Слой SiC является основным диффузионным барьером для ТПД, а также обеспечивает прочность покрытия в целом. Экспериментальные исследования показывают, что целостность слоя SiC обеспечивает удержания практически всех (может быть за исключением изотопов серебра) осколков деления на требуемом уровне.
Наружный высокоплотный изотропный РуС является дополнительным диффузионным барьером и защищает слой SiC от механических повреждений при последующих технологических операциях с МТ.
В процессе облучения в МТ происходит ряд физических и химических превращений, которые могут вызвать разрушение SiC слоя и покрытия в целом, что приведет к повышенной утечке продуктов деления. При нормальных условиях эксплуатации большинства ВТГР (температура облучения 900-1300°С, флюенсе быстрых нейтронов 4·1021 н/см2) и глубоком выгорании топлива основными факторами, определяющими разрушение покрытия МТ, являются:
I. Развитие механических напряжений в силовых слоях покрытия под облучением.
II. Химическое взаимодействие продуктов деления с материалом покрытий (окисление РуС, взаимодействие SiC, например, с палладием и т.д.).
III. Повреждающее воздействие облучения на материалы покрытий.
IV. Наличие исходных дефектов в покрытии после изготовления МТ, а также остаточных напряжений в слоях покрытий и на границе между слоями, вызывающих образование дополнительных дефектов при их размещении в твэле и на ранних стадиях облучения, особенно в условиях термоциклирования, градиента температуры и нейтронного потока.
Известен способ, согласно которому первый буферный слой РуС осаждают на ТМ в кипящем слое при температуре пиролиза 1500°С из ацетилена (C2H2), а второй высокоплотный изотропный РуС из ацетилен-пропиленовой смеси при 1100-1300°С (Пат. США №3554783, МПК 7 G21C 3/00).
Известен способ, согласно которому высокоплотный изотропный пироуглерод осаждают в кипящем слое путем пиролиза пропана, пропилена (С3Н6) или бутадиена при температуре 1250-1300°С (Пат. Франции №1593145, МПК 7 G21C 3/00).
Известен способ, согласно которому слой карбида кремния осаждают в кипящем слое при температуре 1650±25°С и концентрации метилтрихлорсилана (СН3SiCl3) в водороде 2,5 об.% (Voice E.H., Scott V.C. The formation and structure of silicon carbide pyrolytically deposited in afluidized bed of microspheres, – In.: Special Ceramics 5, Eds P. Popper at al. The British Ceramic Research Assoc., 1972, p.1-32).
Известен способ осаждения четырехслойного покрытия в кипящем слое ТМ, согласно которому первый буферный РуС получают за счет пиролиза С2Н2 при температуре 1250°С, второй высокоплотный изотропный РуС получают за счет пиролиза C2H2-С3Н6 смеси при температуре 1300°С, третий SiC слой получают за счет пиролиза СН3SiCl3 при температуре 1500°С и четвертый высокоплотный изотропный РуС получают за счет пиролиза С2Н2-С3Н6 смеси при температуре 1300°С (Huschka H., Vugen P. Coated fuel particles: requirements and status of fabrication ethnology. – Nuclear Technology, V.35, September, 1977, p.238-245).
Недостатком перечисленных способов является то, что при осаждении четырехслойного покрытия на ТМ с использованием указанных условий получения индивидуальных слоев возможно неконтролируемое повреждение хрупкого карбида кремния отдельных МТ в партии частиц. Вероятность повреждения SiC слоя в отдельных МТ существенно возрастает при наличии остаточных напряжений в материале покрытия, а также ростовых дефектов, особенно на внешней поверхности карбидокремниевого слоя.
Наиболее близким аналогом-прототипом предложенному техническому решению является способ, согласно которому в кипящем слое ТМ при 1450°С и концентрации С2Н2 50 об.% осаждают первый буферный слой РуС, при 1300°С из смеси C2H2 (40-43 об.%) и С3Н6 (30-27 об.%) осаждают второй высокоплотный изотропный слой РуС, при температуре 1500°С из смеси CH3SiCl3 с водородом осаждают третий слой карбида кремния, четвертый высокоплотный изотропный слой РуС осаждают по режиму второго слоя (Пат. ФРГ №2626446, МПК 7 С23С 11/02).
Недостатком данного способа, так же как и предыдущих, является возникновение в процессе осаждения остаточных напряжений в четырехслойном покрытии, которые являются причиной повреждаемости SiC слоя (фиг.2) и четвертого РуС (фиг.3) отдельных МТ в большом массиве частиц на стадии изготовления. Влияние остаточных напряжений сказывается уже на ранних стадиях облучения, что выражается в повреждениях SiC слоя в виде расслоений (фиг.4) и в отслоении локальных участков второго РуС слоя от SiC (фиг.5), ограничивая ресурс эксплуатации МТ.
Разрушение хотя бы одного из трех силовых покрытий приводит к повышению выхода ПД из МТ и тем самым ограничивают ресурс эксплуатации последнего.
Перед авторами предложенного технического решения стояла задача повышения ресурса эксплуатации микротвэла ядерного реактора за счет уменьшения повреждаемости покрытий на стадии осаждения покрытий на ТМ, а также при их эксплуатации.
Поставленная задача решается тем, что на стадии получения микротвэлов ядерного реактора с четырехслойным защитным покрытием, включающей последовательное осаждение на топливные микросферы защитных слоев покрытий в кипящем слое, после осаждения 85-95% толщины пироуглеродного покрытия второго слоя 5-15% покрытия осаждают пиролизом пропилена с концентрацией в смеси с аргоном 5,0-10,0 об.% с добавкой 0,5-1,5 об.% метилтрихлорсилана, после осаждения третьего карбидокремниевого слоя проводят его обработку в водороде при температуре 1750-1800°С в течение 20-30 мин, а после осаждения 90-95% толщины пироуглеродного покрытия четвертого слоя, 5-10% покрытия осаждают пиролизом пропилена с концентрацией в смеси с водородом 3,0-5,0 об.%.
Причинно-следственная связь между существенными признаками и техническим решением заключается в следующем.
При последовательном осаждении каждого из слоев четырехслойного покрытия на ТМ в кипящем слое протекают следующие процессы:
– на стадии осаждения SiC между ним и вторым РуС возникают механические напряжения, обусловленные различиями в коэффициенте линейного термического расширения контактирующих пар. Причем для отдельных МТ из большого массива частиц эти напряжения могут быть существенными. В условиях термоциклирования частиц в кипящем слое это будет приводить к увеличению вероятности повреждения SiC слоя.
При осаждении 5-15% покрытия второго пироуглеродного слоя за счет пиролиза 5,0-10,0% об.% пропилена в смеси с аргоном с добавкой 0,5-1,5 об.% метилтрихлорсилана формируется граничный слой из пироуглерода, легированного кремнием, коэффициент линейного термического расширения которого близок к значению коэффициента линейного термического расширения SiC покрытия.
– при получении SiC слоя в нем возникают остаточные напряжения, релаксация которых в условиях осаждения практически невозможна. В условиях напряженного состояния возрастает вероятность его повреждаемости как в условиях термоциклирования в кипящем слое, так и на ранних стадиях облучения МТ.
Обработка в водороде SiC слоя, когда он является наружным покрытием на частице, при температуре 1750-1800°С в течение 20-30 мин способствует релаксации остаточных напряжений в нем за счет термической ползучести материала.
– наружный РуС слой в составе МТ, выполняя защитные функции по предохранению SiC от механических повреждений, испытывает растягивающие напряжения. Сопротивление на разрыв наружного РуС слоя, в совокупности с другими характеристиками материала, существенно зависит от качества его поверхности, под которой подразумевается отсутствие макровыступов, макропор диаметром более 1000 Å и т.п.
В условиях, когда 5-10% наружного РуС слоя осаждают пиролизом пропилена с концентрацией в смеси с водородом 3,0-5,0 об.%, формируется гладкая, без заметных выступов поверхность с преимущественной концентрацией закрытых пор диаметром 60-200 Å.
Пример осуществления технического решения
На топливные микросферы из диоксида урана диаметром 500 мкм осаждают в кипящем слое при температуре пиролиза 1450°С первый буферный РуС слой из С2Н2-Ar при концентрации С2Н2 50 об.% и суммарном расходе газов 1500 л/ч.
После осаждения требуемой толщины буферного РуС прекращают подачу С2Н2, а частицы поддерживают в состоянии псевдоожижения за счет инертного газа-носителя аргона.
За счет уменьшения подводимой к нагревателю электрической мощности снижают температуру кипящего слоя до 1300°С и подачу в реакционную зону смеси С2Н2 (40 об.%) и С3Н6 (30 об.%) с аргоном при суммарном расходе газов 1500 л/ч осаждают 85-95% требуемой толщины второго РуС слоя. После этого при неизменной температуре прекращают подачу реакционных газов (С2H2 и С3Н6), а остальные 5-15% толщины легированного кремнием второго слоя осаждают пиролизом пропилена в смеси с аргоном 5,0 об.% с добавкой 0,5 об.% метилтрихлорсилана.
Третий слой карбида кремния осаждают при температуре 1500°С из смеси метилтрихлорсилана с водородом при концентрации СН3SiCl3 2,0 об.% и расхода водорода на псевдоожижение 1600 л/ч. После осаждения требуемой толщины SiC слоя прекращают подачу СН3SiCl3 в реакционную зону. Частицы пребывают в состоянии псевдоожижения в реакционной зоне за счет расхода водорода в количестве 1600 л/ч. После этого за счет увеличения подводимой к нагревателю электрической мощности частицы нагреваются до температуры 1800°С с выдержкой при этой температуре в течение 20-30 мин.
После уменьшения температуры кипящего слоя до 1300°С из смеси С2H2 (40 об.%) и С3Н6 (30 об.%) с аргоном осаждают 90-95% толщины четвертого РуС слоя. Суммарный расход газов при этом составляет 1500 л/ч. Прекращается подача в реакционную зону С2H2 и С3Н6, а суммарный расход компенсируется увеличением подачи водорода. Остальные 5-10% толщины покрытия четвертого слоя при неизменной температуре 1300°С осаждают пиролизом пропилена с концентрацией в смеси с водородом 3,0 об.%.
Сопоставление условий осаждения четырехслойного защитного покрытия и эксплуатационных характеристик МТ, полученных по известному способу, с МТ по предложенному техническому решению приведено в таблице.
Как следует из приведенных в таблице данных, предложенный способ получения микротвэлов ядерного реактора (примеры 2, 3, 4) в сравнении с известным способом (пример 1) обеспечивает повышенный ресурс эксплуатации за счет более высокой радиационной стойкости второго РуС слоя, меньшей повреждаемости SiC и наружного РуС слоев. При запредельных параметрах (примеры 5, 6) эксплуатационные характеристики МТ резко снижаются.
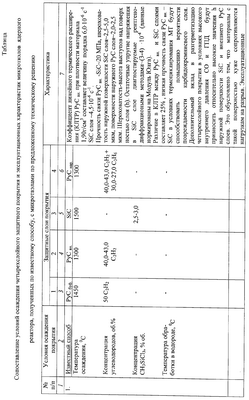
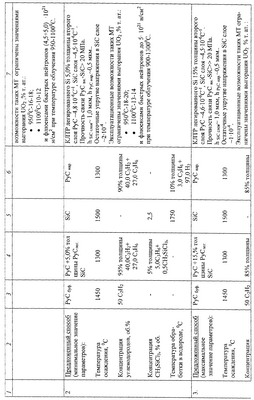
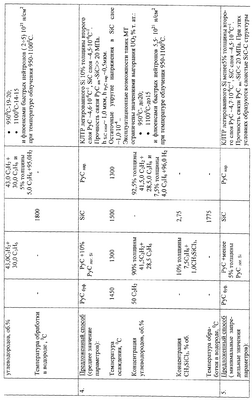
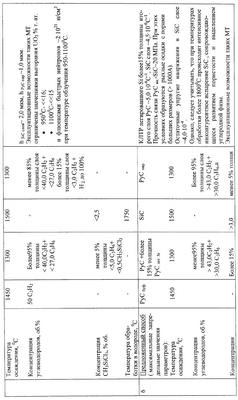

Формула изобретения
Способ получения микротвэлов ядерного реактора с четырехслойным защитным покрытием, включающий последовательное осаждение на топливные микросферы слоев покрытий в кипящем слое, в котором первый слой низкоплотного пироуглерода осаждают пиролизом ацетилена с концентрацией в смеси с аргоном 50 об.% при температуре 1450°С, 85-95% второго слоя из высокоплотного пироуглерода осаждают пиролизом смеси ацетилена с концентрацией в смеси с аргоном 40,0-43,0 об.% и пропилена с концентрацией в смеси с аргоном 30,0-27,0 об.% при температуре 1300°С, третий слой из карбида кремния осаждают пиролизом метилтрихлорсилана с концентрацией в смеси водород-аргон 2,5-3,0 об.% при температуре 1500°С и 90-95% четвертого слоя из высокоплотного пироуглерода осаждают пиролизом смеси ацетилена с концентрацией в смеси с аргоном 40,0-43,0 об.% и пропилена с концентрацией в смеси с аргоном 30,0-27,0 об.% при температуре 1300°С, отличающийся тем, что после осаждения 85-95% толщины пироуглеродного покрытия второго слоя 5-15% покрытия осаждают пиролизом пропилена с концентрацией в смеси с аргоном 5,0-10,0 об.% с добавкой 0,5-1,5 об.% метилтрихлорсилана, после осаждения третьего карбидокремниевого слоя проводят его обработку в водороде при температуре 1750-1800°С в течение 20-30 мин, а после осаждения 90-95% толщины пироуглеродного покрытия четвертого слоя 5-10% покрытия осаждают пиролизом пропилена с концентрацией в смеси с водородом 3,0-5,0 об.%.
РИСУНКИ
|