|
(21), (22) Заявка: 2005121462/02, 07.07.2005
(24) Дата начала отсчета срока действия патента:
07.07.2005
(46) Опубликовано: 27.04.2007
(56) Список документов, цитированных в отчете о поиске:
ГАСИК М.И. и др. Теория и технология электрометаллургии ферросплавов. М., СП Интермет Инжиниринг, 1999, с.353-356. SU 521340 А, 15.07.1976. SU 1097699 А, 15.06.1984. RU 2148102 C1, 27.04.2000. WO 90/15165 A1, 13.12.1990. EP 0652296 A1, 10.05.1995.
Адрес для переписки:
162600, Вологодская обл., г. Череповец, пр. Луначарского, 5, ЧГУ, ректору В.С. Грызлову
|
(72) Автор(ы):
Хисамутдинов Николай Егорович (RU), Козлов Геннадий Сергеевич (RU), Шаталов Сергей Викторович (RU)
(73) Патентообладатель(и):
Череповецкий государственный университет (ЧГУ) (RU)
|
(54) СПОСОБ ВЫПЛАВКИ УГЛЕРОДИСТОГО ФЕРРОМАРГАНЦА
(57) Реферат:
Изобретение относится к металлургии и может быть использовано при производстве ферросплавов. Осуществляют загрузку в плавильный агрегат шихты, состоящей из марганецсодержащего сырья, флюса, углеродистого восстановителя, восстановительную плавку, выпуск шлака и ферромарганца из печи. В качестве плавильного агрегата используют тигельную индукционную печь с шахтной надставкой, при этом используют шихту фракционным размером 0-5 мм и фракцией 0-1,6 мм, которую дополнительно окусковывают или пакетируют, и ее количество не должно превышать 50% от общей массы шихты, причем перед загрузкой в печь шихту смешивают в следующем соотношении компонентов, мас.%: углеродистый восстановитель 11,8-15,9; флюс 7,9-14,0; марганецсодержащее сырье остальное. Добавки флюсов обеспечивают отношение (CaO+MgO)/SiO2 в конечном шлаке равное 1,35-1,80 и содержание Al2О3 8-20% в шлаке перед присадкой в него алюминия. Перед выпуском шлака в него присаживают алюминий в количестве, обеспечивающем получение содержания Al2О3 в конечном шлаке 13,0-30,0%. Изобретение позволяет выплавлять углеродистый ферромарганец с высокой степенью извлечения марганца 93-97% путем уменьшения его потерь с отвальным шлаком и улетом. 2 з.п. ф-лы, 3 табл., 5 ил.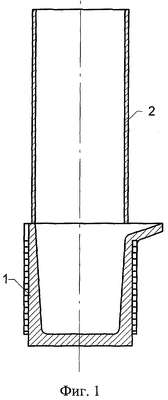
Изобретение относится к области черной металлургии и может быть использовано при производстве ферросплавов, в частности при производстве углеродистого ферромарганца.
Известен способ получения лигатуры методом алюминотермии (авт.св. SU №1713964, МКИ: С 22 С 33/04, 1992 г.), включающий загрузку в электропечь шихты, состоящей из марганецсодержащих, кремнийсодержащих материалов, флюсовых добавок, проплавление, восстановление алюминием и выпуск расплава, шихту совместно с алюминием загружают в тигель индукционной печи, предварительно нагретый до 900°С, а после проплавления шихты расплав выдерживают в тигле в течение 5-10 мин при 1400-1450°С.
Недостатками данного способа является использование дорогостоящего восстановителя – алюминия и получение сплава с низким содержанием марганца.
Известен способ выплавки ферромарганца в индукционной печи (авт.св. СССР №521340, МКИ: С 22 С 33/04, 1976 г.), включающий предварительную выплавку передельного силикомарганца в руднотермической электропечи, заливку силикомарганца в индукционную печь, нагрев расплава до 1550 -1600°С и последующие присадки смеси марганцевой руды и извести.
Недостатками указанного способа являются сложность (двухстадийность), вследствие этого высокая энергоемкость процесса и потери марганца в улет (испарение) 6-10%, при производстве передельного силикомарганца.
Известен способ выплавки марганцевых сплавов углеродотермическим восстановлением марганца, железа и других элементов из руды и добавок, содержащих эти элементы в окисной форме (авт.св. СССР №443102, МКИ: С 22 С 33/00, С 22 С 7/06, 1974 г.), когда в конце плавки поднимают один, два или более электродов и в образовавшиеся подэлектродные полости вводят смесь кремнийсодержащих материалов и флюсов.
Недостатком данного способа является получение сплава с высоким содержанием кремния порядка 18% и потери марганца в улет 3-10%.
Известен способ, принятый за прототип, выплавки углеродистого ферромарганца в рудовосстановительной печи флюсовым способом (Гасик М.И., Лякишев Н.П. Теория и технология электрометаллургии ферросплавов. – М.: СП Интермет Инжиниринг, 1999 г., стр.353-356), включающий загрузку в плавильный агрегат шихты, состоящей из марганцевого сырья, углеродистого восстановителя, флюса, восстановительную плавку, выпуск шлака и ферромарганца из печи.
Недостатками данного способа являются низкое извлечение марганца в сплав (до 80%), обусловленное улетом марганца (11-20%) и его потерями с отвальным шлаком (более 13%), а также невысокая скорость процесса, связанная с большим размером шихтовых материалов (5-150 мм).
Задачей изобретения является повышение степени извлечения марганца в сплав путем уменьшения его потерь с отвальным шлаком и улетом.
Указанная задача достигается тем, что в способе выплавки углеродистого ферромарганца, включающем загрузку в плавильный агрегат шихты, состоящей из марганцевого сырья, флюса, углеродистого восстановителя, восстановительную плавку, выпуск шлака и ферромарганца из печи, согласно изобретению в качестве плавильного агрегата используют тигельную индукционную печь с шахтной надставкой, при этом шихту загружают фракционным размером 0-5 мм, а шихту фракцией 0-1,6 мм дополнительно окусковывают или пакетируют и ее количество не должно превышать 50% от общей массы шихты, причем перед загрузкой в печь шихту смешивают в следующем соотношении компонентов, мас.%:
Углеродистый восстановитель |
11,8-15,9 |
Флюсы |
7,9-14,0 |
Марганецсодержащее сырье |
Остальное. |
Кроме того, добавки флюсов обеспечивают отношение (СаО+MgO)/SiO2 в конечном шлаке, равное 1,35-1,80, и содержание Al2О3 в шлаке перед присадкой Al в количестве 8-20%.
Кроме того, перед выпуском шлака в него присаживают алюминий в количестве, обеспечивающем получение содержания Al2О3 в конечном шлаке 13,0-30,0%.
Использование для выплавки ферромарганца индукционной печи с шахтной надставкой позволяет снизить улет марганца с 11-20% (по прототипу) до 0,5-1,8%.
Предварительное смешение компонентов шихты перед загрузкой в печь позволяет увеличить скорость и полноту протекания восстановительных процессов.
Использование материалов, размер фракций которых более 5 мм, в данном процессе нецелесообразно из-за снижения производительности печи, т.к. увеличение фракционного размера шихтовых материалов приводит к уменьшению площади реакционной поверхности, вследствие чего восстановительные процессы сильно замедляются и возрастает продолжительность плавки.
Применение материалов фракцией меньше 1,6 мм приводит к выбросам их из печи. Окомкование или пакетирование материалов с размером фракций меньше 1,6 мм предотвращает выбросы. С увеличением доли “мелочи” в шихте (шихтовые материалы размер фракций которых <1,6 мм) от 0 до 50% возрастает степень извлечения марганца в сплав, это происходит из-за увеличения площади реакционной поверхности шихтовых материалов, вследствие чего возрастает скорость и полнота протекания восстановительных процессов. Последующее увеличение доли “мелочи” в шихте приводит к снижению степени извлечения марганца из-за увеличивающихся выбросов шихты, фракцией менее 1,6 мм из печи. При использовании в качестве восстановителя как антрацита, так и угля марки Ж степень извлечения марганца возрастает на промежутке от 0 до 50% “мелочи” в шихте, а на промежутке от 50 до 100% “мелочи” в шихте степень извлечения марганца снижается.
Повышение основности шлака ((СаО+MgO)/SiO2) до 1,35-1,8 приводит к облегчению восстановления марганца в сплав вследствие повышения активности MnO в шлаке, но повышение основности конечного шлака выше 1,80 приводит к чрезмерной его вязкости, из-за чего затормаживается процесс восстановления марганца из шлака и затрудняется выпуск шлака из печи. При основности конечного шлака менее 1,35 степень извлечения марганца в сплав снижается вследствие недостаточной активности MnO в шлаке.
Присадка флюсов, содержащих оксиды алюминия, улучшает жидкотекучесть шлака, повышает активность MnO в шлаке, что приводит к улучшению условий перехода марганца из шлака в металл. При отсутствии этих присадок шлак содержит 4,5-5,5% Al2О3, при этом он густой, малореакционноспособный и последующее восстановление марганца из него будет затруднено. Поэтому повышение содержания Al2О3 в шлаке, перед присадкой в него Al, до 8%, позволяет повысить реакционную способность шлака, повышение содержания Al2О3 выше 20% нецелесообразно, т.к. ведет к увеличению кратности шлака и снижению производительности печи.
Присадка Al в шлак позволяет повысить степень извлечения марганца. По результатам опытных плавок видно, что оптимальное содержание Al2О3 в конечном шлаке составляет 13-30%. При содержании в конечном шлаке менее 13% Al2О3 снижается степень извлечения марганца в сплав и производительность печи. Повышение содержания Al2О3 в конечном шлаке до 30% приводит к максимальному извлечению марганца. Дальнейшее повышение содержания Al2О3 не приводит к возрастанию степени извлечения марганца в сплав.
Способ поясняется следующими фигурами: на фиг.1 показана индукционная печь. На фиг.2 представлена зависимость площади реакционной поверхности шихтовых материалов от размера их фракций (данные приведены для сосуда объемом 5 дм3, цифры у точек показывают площадь реакционной поверхности шихтовых материалов). На фиг.3 показана зависимость степени извлечения марганца от количества мелочи в шихте для разных восстановителей ( – уголь марки Ж, – антрацит). На фиг.4 показана зависимость степени извлечения марганца от основности шлака ((СаО+MgO)/SiO2). На фиг.5 показана зависимость степени извлечения марганца от содержания в конечном шлаке Al2О3.
Способ осуществляется следующим образом.
В разогретый до 800-1600°С графитовый тигель индукционной печи 1, со съемной шахтной надставкой 2, загружают предварительно смешанную шихту фракцией 0-5 мм, шихту фракций 0-1,6 мм подают в печь пакетированной, причем ее количество не должно превышать 50% от общей массы шихты. Размер шахтной надставки выбирают таким образом, чтобы ее объем был в 2-2,5 раза больше объема тигля. Состав загружаемой шихты (мас.%): углеродистый восстановитель 11,8-15,9; флюс 7,9-14,0; марганецсодержащее сырье – остальное. После завершения протекания восстановительных процессов и образования жидкоподвижного шлака в него осуществляют присадку Al. Затем после выдержки в течение 2-3 мин производят выпуск металла и сплава.
Пример осуществления предлагаемого способа.
Подготовка шихтовых материалов к плавке.
Шихтовые материалы (марганецсодержащее сырье, флюс, углеродистый восстановитель) дробились до фракционного размера 0-5 мм и рассеивались по фракциям 0-1,6 и 1,6-5 мм. Затем осуществлялось раздельное смешивание шихтовых материалов выделенных фракций, причем шихтовые материалы фракцией 0-1,6 мм пакетировались.
Плавка. В индукционную тигельную печь ИСТ-016, с шахтной надставкой, загружалась смесь шихтовых материалов фракцией 0-5 мм, состоящая из 200 кг марганцевой руды, 29,8 кг антрацита, 20 кг извести, 1,5 кг боксита. Шихтовые материалы, размер фракций которых был менее 1,6 мм, подавались в печь пакетированными, причем их количество не превышало 50% от общей массы шихты. Химический состав шихтовых материалов приведен в таблице 1. После образования жидкоподвижного шлака в него присадили 5,1 кг алюминия, затем после выдержки в течение 2 мин произвели слив сплава и шлака. В результате плавки продолжительностью 35 мин было получено 102,6 кг сплава и 59,6 кг шлака.
Таблица 1 Химический состав шихтовых материалов |
Материалы |
Содержание элементов, % |
|
MnO2 |
MnO |
SiO2 |
Al2O3 |
CaO |
MgO |
P2O5 |
Fe2O3 |
S |
влага |
С |
зола |
выход летучих |
CO2 |
SO3 |
TiO2 |
Na2O |
K2O |
Марганцевая руда |
58,0 |
10.7 |
8.8 |
2.18 |
2,18 |
1,0 |
0,09 |
8,57 |
0,01 |
8,47 |
|
|
|
|
|
|
|
|
Антрацит |
|
|
|
|
|
|
|
|
1,0 |
|
91,2 |
4,8 |
3,0 |
|
|
|
|
|
Зола антрацита |
|
|
28,2 |
15,0 |
7,85 |
3,95 |
0,15 |
33,9 |
|
|
|
|
|
|
7,7 |
0,7 |
1,31 |
1,28 |
Известь |
|
|
1,0 |
1,0 |
92,0 |
2,0 |
|
|
|
1,0 |
|
|
|
3,0 |
|
|
|
|
Боксит |
|
|
9,81 |
61.3 |
2,33 |
|
0,08 |
2,31 |
0,1 |
ост. |
|
|
|
2,7 |
|
|
|
|
Химический состав сплава и шлака приведен в таблицах 2 и 3.
Таблица 2 Химический состав сплава |
|
Содержание элементов, % |
Mn |
Si |
С |
S |
P |
Fe |
Сплав |
81.7 |
0.82 |
5.91 |
0.012 |
0.064 |
остальное |
Таблица 3 Химический состав шлака |
|
Содержание элементов, % |
MnO |
Al2O3 |
CaO |
MgO |
SiO2 |
Шлак |
9,78 |
26,41 |
32,04 |
4,12 |
25,5 |
Анализ данных показывает, что при реализации данного способа можно повысить степень извлечения марганца с 80% (по прототипу) до 93,23%, а при более полном восстановлении марганца из шлака и до 97%, при этом можно использовать марганцевую руду с более низким содержанием марганца, чем в способе, принятом за прототип. Ввиду того что для заявляемого способа пригоден любой твердый углеродистый восстановитель, исключается потребность в дорогостоящем металлургическом коксе.
Таким образом, показано, что по предлагаемому способу можно выплавлять углеродистый ферромарганец с высокой степенью извлечения марганца (93-97%).
Формула изобретения
1. Способ выплавки углеродистого ферромарганца, включающий загрузку в плавильный агрегат шихты, состоящей из марганецсодержащего сырья, флюса, углеродистого восстановителя, восстановительную плавку, выпуск шлака и ферромарганца из печи, отличающийся тем, что в качестве плавильного агрегата используют тигельную индукционную печь с шахтной надставкой, загружают шихту фракционным размером 0-5 мм, при этом шихту фракцией 0-1,6 мм в количестве 50% от общей массы шихты дополнительно окусковывают или пакетируют, а перед загрузкой в плавильный агрегат шихту смешивают в следующем соотношении компонентов, мас.%:
Углеродистый восстановитель |
11,8-15,9 |
Флюсы |
7,9-14,0 |
Марганецсодержащее сырье |
Остальное |
2. Способ по п.1, отличающийся тем, что добавка флюса в шихту обеспечивает отношение (CaO+MgO)/SiO2 в конечном шлаке равным 1,35-1,80 и содержание Al2O3 8-20% в шлаке перед присадкой в него алюминия.
3. Способ по п.1, отличающийся тем, что перед выпуском шлака в него присаживают алюминий, в количестве, обеспечивающим получение содержания Al2O3 в конечном шлаке 13,0-30,0%.
РИСУНКИ
|
|