(21), (22) Заявка: 2004132572/28, 11.11.2004
(24) Дата начала отсчета срока действия патента:
11.11.2004
(43) Дата публикации заявки: 27.04.2006
(46) Опубликовано: 10.04.2007
(56) Список документов, цитированных в отчете о поиске:
RU 2184373 C1, 27.06.2002. RU 2062394 C1, 20.06.1996. SU 1748052 A1, 15.07.1982. Неразрушающий контроль и диагностика. Справочник под редакцией В.В.Кинева. – М.: Машиностроения, 1995, с.434. US 5970438 А, 19.10.1999. US 4173139 А, 06.11.1979.
Адрес для переписки:
109125, Москва, 2-й Саратовский пр., 5, кв.49, А.Ф. Гетману
|
(72) Автор(ы):
Махутов Николай Андреевич (RU), Тутнов Александр Александрович (RU), Гетман Александр Федорович (RU), Ловчев Владимир Николаевич (RU), Гуцев Дмитрий Федорович (RU), Кураков Юрий Александрович (RU), Драгунов Юрий Григорьевич (RU), Зубченко Александр Степанович (RU), Григорьев Михаил Владимирович (RU), Калиберда Инна Васильевна (RU), Нигматулин Булат Искандерович (RU), Карзов Георгий Павлович (RU), Васильев Владимир Георгиевич (RU), Просвирин Анатолий Владимирович (RU), Конев Юрий Николаевич (RU), Тутнов Антон Александрович (RU), Гетман Юлия Васильевна (RU)
(73) Патентообладатель(и):
Закрытое акционерное общество “Координационный центр по надежности, безопасности и ресурсу оборудования и трубопроводам атомных электростанций” (КЦНБРАС) (RU)
|
(54) СПОСОБ ДОВЕДЕНИЯ ИЗДЕЛИЯ ДО ЗАДАННОГО УРОВНЯ КАЧЕСТВА, НАДЕЖНОСТИ И БЕЗОПАСНОСТИ С УЧЕТОМ МЕТОДИКИ КОНТРОЛЯ (ВАРИАНТЫ)
(57) Реферат:
Изобретение относится к области неразрушающего контроля и может быть использовано при изготовлении, монтаже и эксплуатации изделий современного машино- и приборостроения. Согласно заявленному решению задают требования к надежности и безопасности изделия, который надо обеспечить, затем определяют уровень дефектности изделия до контроля или после контроля и ремонта выявленных дефектов, затем определяют требования к достоверности метода и средств неразрушающего контроля с учетом указанных характеристик. В случае группы однотипных изделий требования к методике и средства контроля определяют на одном из изделий, затем контролируют всю группу. Технический результат заключается в достижении заданных характеристик надежности и безопасности изделия за счет специальной процедуры подбора достаточного и оптимального для данного изделия метода и технических средств неразрушающего контроля с последующим контролем изделия и ремонтом выявленных дефектов. 5 н. и 4 з.п. ф-лы, 4 ил.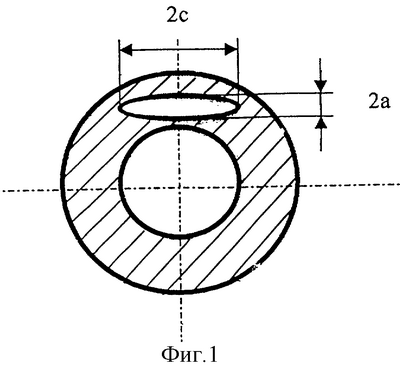
Область применения изобретения – изготовление, монтаж и эксплуатация изделий современного машино- и приборостроения, включая транспорт (автомобильный, авиационный, железнодорожный, водный), энергетику (тепловую, атомную и др.), нефтехимию, в том числе нефте-, газо- и продуктопроводы, сосуды и хранилища, общее машиностроение и т.п.
Из уровня техники известен способ доведения изделия до заданного уровня качества, надежности и безопасности, согласно которому проводится неразрушающий контроль изделия. Контроль проводится либо сразу после изготовления изделия, например правила “Оборудование и трубопроводы атомных энергетических установок. Сварные соединения и наплавка. Правила контроля ПН АЭ Г-7-010-89”, утвержденные постановлением Госатомэнергонадзором СССР от 11 мая 1989, либо в период эксплуатации, например “Правила устройства и безопасной эксплуатации оборудования и трубопроводов атомных энергетических установок” ПН АЭ Г-7-008-89. Далее по результатам контроля устраняются обнаруженные в изделии дефекты.
Однако данные способы не позволяют подобрать метод неразрушающего контроля и определить характеристики технических средств, которые были бы достаточными для данного конкретного изделия и которые позволили бы осуществлять контроль с достаточной достоверностью и качеством, что не позволяет выявить в изделии дефекты с достаточной точностью и, следовательно, приводит к низким качеству и надежности изделия.
Технический результат предлагаемого изобретения заключается в увеличении количества выявляемых дефектов изделия за счет подбора достаточного для данного изделия метода неразрушающего контроля и определения наиболее оптимальных характеристик технических средств, которыми будет осуществляться неразрушающий контроль.
Технический результат достигается следующим образом.
Первый вариант. Способ доведения изделия до заданного уровня качества, безопасности и надежности с учетом методики контроля, заключающийся в том, что определяют изделие, качество, надежность и безопасность эксплуатации которого нужно обеспечить, осуществляют неразрушающий контроль (НК) данного изделия и устраняют выявленные дефекты. Задают требования к качеству, надежности и безопасности изделия, определяют требования к методу и техническим средствам контроля, для этого: с учетом реальных эксплуатационных нагрузок и условий определяют для изделия размеры критических и допустимых в эксплуатации несплошностей, а также нормы дефектов изделия при изготовлении, в координатах “lg[P]- “, где [Р] – заданная вероятность существования дефекта размером и более, – характеристический размер дефекта, строят нормативную кривую состояния изделия [Р( * )], где  – характеристический размер дефекта, задаваемый в интервале характеристических размеров дефектов от до максимально возможного в данном изделии дефекта, вероятность существования которых рассматривается, результаты первого НК представляют в виде гистограммы в координатах (Nобн; ), где Nобн – число обнаруженных при контроле дефектов, – характеристический размер дефекта, полученную гистограмму аппроксимируют уравнением Nобн( )=A -n{1-(1- )exp[- ( – 0)]- } или
Nобн( )=А’exp(-n’ ){1-(1- )ехр[- { – 0)]- },
где А, А’, n, n’, , – постоянные, которые определяют из условия максимального приближения уравнения Nобн( ) к результатам контроля, представленным в виде гистограммы, 0 – минимально доступный для выявления характеристический размер дефекта.
Определяют исходную дефектность Nисх=f( ) по формуле
Nисх=А -n или Nисх=A’ехр(-n’ ),
исходную дефектность разделяют на достоверную часть и вероятностную часть.
На график, на котором нанесена нормативная кривая состояния изделия, наносят вероятностную часть кривой исходной дефектности Рисх( * ), отражающую вероятность существования дефекта с характеристическим размером * где * – характеристический размер дефекта, задаваемый в интервале характеристических размеров дефектов от до макс, вероятность существования которых рассматривается.
Количественные требования к методу и техническим средствам НК для повторного контроля оценивают уравнением выявляемости дефектов Рвод( )=1-(1- )exp[- ( – 0)]- или в первом приближении, при этом Рвод( )=1-ехр-[ ( – 0)]
значение постоянной определяют как большее значение по уравнениям:
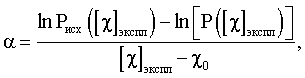
где 0 – минимальный размер дефекта, выявленного данным методом контроля; 0 должен быть меньше, чем допустимый дефект при изготовлении; кр – характеристический размер критического дефекта, [ ]экспл – допустимый размер дефекта при эксплуатации по расчетам механики разрушения, Р[ ]экспл – нормативная характеристика надежности изделия, задаваемая по вероятности существования в нем дефектов, больше допустимых в эксплуатации, [P( кр)] – нормативная характеристика безопасности изделия, задаваемая как вероятность существования в нем хотя бы одного дефекта, размер которого равен или более критического, Рисх( кр) – вероятность существования в изделии дефекта, равного или больше кр; Рисх([ ]экспл) – вероятность существования в изделии дефекта, равного или большего [ ]экспл.
Определив требования, которым должен удовлетворять метод и средства НК, осуществляют их подбор, для этого:
изготавливают тест-образец для доводимого изделия, изготовленный образец контролируют различными методами и техническими средствами НК, определяют для каждого метода и технических средств вероятность выявления дефектов как соотношение количества выявленных дефектов Nвыявл к количеству заложенных дефектов Nзал, метод и средства НК считают удовлетворяющим определенным ранее требованиям к ним, когда вероятность выявления дефектов данным методом и средствами в изделии будет равна или более определенного количественного требования,
по результатам второго контроля устраняют выявленные дефекты.
Технический результат достигается также следующим образом.
Второй вариант. Способ доведения изделия до заданного уровня качества, надежности, безопасности с учетом методики контроля, заключающийся в том, что определяют изделие, качество, надежность и безопасность эксплуатации которого нужно обеспечить, осуществляют неразрушающий контроль (НК) данного изделия и устраняют выявленные дефекты. Задают требования к качеству, надежности и безопасности изделия.
Определяют требования к методу и техническим средствам контроля, для этого: с учетом реальных эксплуатационных нагрузок и условий определяют для изделия размеры критических и допустимых в эксплуатации несплошностей, а также нормы дефектов изделия при изготовлении. В координатах “lg[P]- “, [Р] – заданная вероятность существования дефекта размером и более, – характеристический размер дефекта, строят нормативную кривую состояния изделия. Изготавливают тест-образец для доводимого изделия. Тем же методом НК, что и проведенный НК изделия, проводится контроль тест-образца для доводимого изделия. Результаты контроля сравнивают с реальными дефектами, заложенными в тест-образец, для каждого характеристического размера дефекта определяют соотношение “число обнаруженных в тест-образце дефектов Nобн то ( ) разделить на число заложенных в тест-образец дефектов Nзал то( )”, которое характеризует вероятность обнаружения дефекта данного характеристического размера Рвод( ): Рвод( )=Nобн( )/Nзал то( ).
Определяют исходную дефектность изделия Nисх( )=f( ), как отношение числа обнаруженных при контроле изделия дефектов данного характеристического размера Nобн изд( ) к вероятности выявления дефектов данным методом НК,
Nисх( )=Nобн изд( )/Рвод( ),
исходную дефектность разделяют на достоверную часть и вероятностную часть.
На график, на котором нанесена нормативная кривая состояния изделия, наносят вероятностную часть кривой исходной дефектности Рисх( * ), где * – характеристический размер дефекта, задаваемый в интервале характеристических размеров дефектов от до макс, вероятность существования которых рассматривается.
Количественные требования к методу и средствам неразрушающего контроля для повторного контроля оценивают уравнением выявляемости дефектов Pвод( )=1-exp[- ( – 0)], при этом значение постоянной определяют как большее из дух значений по уравнениям:
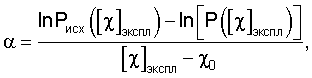
где 0 – минимальный размер дефекта, выявленного данным методом контроля; 0 должен быть меньше, чем допустимый дефект при изготовлении; кр – характеристический размер критического дефекта, [ ]экспл – допустимый размер дефекта при эксплуатации по расчетам механики разрушения, [Р([ ] [ ]экспл)] – нормативная характеристика надежности изделия, задаваемая по вероятности существования в нем дефектов, равных или больше допустимых в эксплуатации, [Р(  кр)] – нормативная характеристика безопасности изделия, задаваемая как вероятность существования в нем хотя бы одного дефекта, размер которого равен или более критического, [Р( [ ]изг)].
Определив требования, подбирают удовлетворяющие им метод и технические средства НК, для этого:
используют ранее изготовленный тест-образец для доводимого изделия, этот образец контролируют различными методами и техническими средствами НК, определяя для каждого метода и технических средств вероятность выявления дефектов как соотношение количества выявленных дефектов Nвыявл к количеству заложенных дефектов Nзал, метод и средства НК считают удовлетворяющим определенным ранее требованиям, когда вероятность выявления дефектов данным методом и средствами в изделии будет равна или более определенного количественного требования,
по результатам второго контроля устраняют выявленные дефекты.
Технический результат достигается также следующим образом.
Третий вариант. Способ доведения изделия до заданного уровня качества, безопасности, надежности с учетом методики контроля, заключающийся в том, что определяют изделие, качество, надежность и безопасность эксплуатации которого нужно обеспечить, осуществляют неразрушающий контроль (НК) данного изделия и устраняют выявленные дефекты. Задают требования к качеству, надежности и безопасности изделия.
Определяют требования к методу и техническим средствам контроля, для этого: с учетом реальных эксплуатационных нагрузок и условий определяют для изделия размеры критических и допустимых в эксплуатации несплошностей, а также нормы дефектов изделия при изготовлении. В координатах “lg[P]- “, где [Р] – заданная вероятность существования дефекта размером и более, – характеристический размер дефекта, строят нормативную кривую состояния изделия, результаты контроля представляют в виде гистограммы в координатах (Nобн; ) где Nобн – число обнаруженных при контроле дефектов, – характеристический размер дефекта. Полученную гистограмму аппроксимируют уравнением Nобн( )=A -n{1-(1- )exp[- { – 0)]- },
где А, n, , – постоянные, которые определяют из условия максимального приближения уравнения Nобн, ( ) к результатам контроля, представленным в виде гистограммы;
0 – минимально доступный для выявления характеристический размер дефекта.
Определяют исходную дефектность Nисх по формуле
Nисх=А -n.
Определяют вероятность обнаружения дефекта по формуле
Рвод=1-(1- )ехр[- ( – 0)]- .
Определяют остаточную дефектность Nост= ( ) как разность исходной дефектности Nисх( ) и числа обнаруженных при контроле изделия дефектов Nобн изд( ),
остаточную дефектность разделяют на достоверную часть и вероятностную часть.
На график, на котором нанесена нормативная кривая состояния изделия, наносят вероятностную часть кривой остаточной дефектности Рост( * ), отражающую вероятность существования дефекта с характеристическим размером * где * – характеристический размер дефекта, задаваемый в качестве нижней границы интервала характеристических размеров дефектов, вероятность существования которых рассматривается.
Количественные требования к методу и средствам неразрушающего контроля для повторного контроля оценивают уравнением выявляемости дефектов Рвод( )=1-ехр[- ( – 0)], при этом значение постоянной определяют как большее значение по уравнениям:
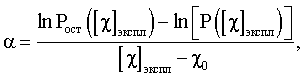
где кр – характеристический размер критического дефекта, [ ]изг – допустимый размер дефекта при эксплуатации по расчетам механики разрушения, [Р[ [ ]экспл)] – нормативная характеристика надежности изделия, задаваемая по вероятности существования в нем дефектов, больше допустимых в эксплуатации, [P(  кр)] – нормативная характеристика безопасности изделия, задаваемая как вероятность существования в нем хотя бы одного дефекта, размер которого равен или более критического, Рост( [ ]изг) – вероятность существования в изделии дефектов, равных или больше [ ]экспл после ремонта выявленных дефектов; Рост(  кр) – вероятность существования в изделии дефектов, равных или больше кр после ремонта выявленных дефектов.
Определив требования, которым должны удовлетворять метод и средства НК, приступают к их подбору, для этого:
изготавливают тест-образец для доводимого изделия, этот образец контролируют различными методами и техническими средствами НК, определяя для каждого метода и технических средств вероятность выявления дефектов как соотношение количества выявленных дефектов Nвыявл к количеству заложенных дефектов Nзал, метод и средства НК считают удовлетворяющим определенным ранее требованиям, когда вероятность выявления дефектов данным методом и средствами в изделии будет равна или более определенного количественного требования,
по результатам первого и второго контроля устраняют выявленные дефекты.
Технический результат достигается также следующим образом.
Четвертый вариант. Способ доведения изделия до заданного уровня качества, надежности, безопасности, заключающийся в том, что определяют изделие, качество, надежность и безопасность эксплуатации которого нужно обеспечить, осуществляют неразрушающий контроль (НК) данного изделия и устраняют выявленные дефекты. Задают требования к качеству, надежности и безопасности изделия. Определяют требования к методу и техническим средствам следующего контроля, для этого: с учетом реальных эксплуатационных нагрузок и условий определяют для изделия размеры критических и допустимых в эксплуатации несплошностей, а также нормы дефектов изделия при изготовлении, в координатах “lg[P]- “, [Р] – заданная вероятность существования дефекта размером и более, – характеристический размер дефекта, строят нормативную кривую состояния изделия. Изготавливают тест-образец для доводимого изделия, тем же методом НК, что и проведенный НК изделия, проводится контроль тест-образца для доводимого изделия. Результаты контроля сравнивают с реальными дефектами, заложенными в тест-образец. Для каждого характеристического размера дефекта определяют соотношение “число обнаруженных в тест-образце дефектов Nобн то( ) разделить на число заложенных в тест-образец дефектов Nзал то( )”, которое характеризует вероятность обнаружения данного характеристического размера дефекта Pвод( ): Рвод=Nобн то( )/Nзал то( ).
Определяют исходную дефектность изделия Nисх как отношение числа обнаруженных при контроле изделия дефектов данного размера Nобн изд( ) к вероятности выявления дефектов данным методом НК
Nисх( )=Nобн изд( )/Рвод( ).
Определяют остаточную дефектность Nост= ( ) как разность исходной дефектности Nисх( ) и числа обнаруженных при контроле изделия дефектов Nобн изд( ),
остаточную дефектность разделяют на достоверную часть и вероятностную часть.
На график, на котором нанесена нормативная кривая состояния изделия, наносят вероятностную часть кривой исходной дефектности Рисх( * ), отражающую вероятность существования дефекта с характеристическим размером * где * – характеристический размер дефекта, задаваемый в интервале характеристических размеров дефектов от до макс, вероятность существования которых рассматривается.
Количественные требования к методу неразрушающего контроля для повторного контроля оценивают уравнением выявляемости дефектов Рвод( )=1-ехр[- ( – 0)], при этом значение постоянной определяют как большее значение по уравнениям:
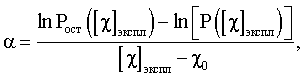
где 0 – минимальный размер дефекта, допущенного для выявления; как правило, 0 меньше допустимого дефекта в изготовлении; кр – характеристический размер критического дефекта, [ ]экспл – допустимый размер дефекта при эксплуатации по расчетам механики разрушения, [Р( [ ]экспл)] – нормативная характеристика надежности изделия, задаваемая по вероятности существования в нем дефектов, больше допустимых в эксплуатации, [Р(  кр)] – нормативная характеристика безопасности изделия, задаваемая как вероятность существования в нем хотя бы одного дефекта, размер которого равен или более критического, Рост( [ ]изг) – вероятность существования в изделии дефектов, равных или больше [ ]экспл после ремонта выявленных дефектов; Рост(  кр) вероятность существования в изделии дефектов, равных или больше кр после ремонта выявленных дефектов.
Определив требования, подбирают удовлетворяющие им метод и технические средства НК, для этого:
используют тест-образец для доводимого изделия, этот образец контролируют различными методами и техническими средствами НК, определяя для каждого метода и технических средств вероятность выявления дефектов как соотношение количества выявленных дефектов Nвыявл к количеству заложенных дефектов Nзал, метод и средства НК считают удовлетворяющим определенным ранее требованиям, когда вероятность выявления дефектов данным методом и средствами в изделии будет равна или более определенного количественного требования.
По результатам второго контроля устраняют выявленные дефекты.
В частном случае при осуществлении способа доведения изделия до заданного уровня качества, надежности, безопасности при проведении НК радиационным методом используют тест-образец для радиационного контроля для доводимого изделия.
Технический результат достигается также следующим образом.
Пятый вариант. Способ доведения до заданного уровня качества, надежности и безопасности с учетом методики контроля группы однотипных изделий, заключающийся в том, что определяют группу однотипных изделий, качество, надежность и безопасность которых необходимо обеспечить. Задают требования к качеству, надежности и безопасности названной группы. Выбирают одно любое изделие из данной группы. Осуществляют НК выбранного изделия любым методом НК. По результатам проведенного контроля определяют требования к методу и техническим средствам неразрушающего контроля, обеспечивающего требуемый уровень надежности и безопасности изделия. После того как определили требования к средствам и методам НК, осуществляют их подбор. Подобранными средствами и методом НК осуществляют НК всей группы однотипных изделий и по результатам этого контроля ремонтируют изделия.
Изобретение пояснено чертежами:
фиг.1 – трубопровод энергетической установки;
фиг.2 – кривая нормативного состояния изделия и вероятностные кривые исходной и остаточной дефектности;
фиг.3 – результаты контроля и кривые исходной и остаточной дефектности;
фиг.4 – кривые вероятности обнаружения дефектов (1 – при первом контроле, 2 – требуемая кривая вероятности обнаружения дефектов, обеспечивающая нормативный уровень качества, надежности, безопасности).
Способ осуществляется следующим образом.
Первый вариант. Определяют изделие, качество, надежность и безопасность эксплуатации которого нужно обеспечить.
Для выбранного изделия задаются требования к его качеству, надежности, безопасности – т.е. задается вероятность существования в нем дефектов, определяющих его качество, надежность и безопасность (задается его качество, надежность, безопасность или нормативные требования к его качеству, надежности и безопасности). Надо отметить, что дефекты, определяющие качество – это дефекты, размеры которых находятся в интервале от размеров минимальных доступных для выявления дефектов (поискового) до размеров дефектов, допустимых при изготовлении и выше; дефекты, определяющие надежность – это дефекты, размеры которых находятся в интервале от браковочного при изготовлении до допустимого при эксплуатации и выше; дефекты, определяющие безопасность – от допустимых при эксплуатации до критических размеров и выше.
Эта вероятность задается исходя из социально-экономических требований к надежности и безопасности изделия с учетом возможностей современного уровня техники и может быть названа нормативными требованиями к качеству, надежности и безопасности изделия.
Для того чтобы обеспечить заданный (нормативный) уровень качества, надежности и безопасности изделия, необходимо определить требования к методу неразрушающего контроля, которым будет контролироваться указанное изделие и по результатам которого будет произведено устранение содержащихся в изделии дефектов.
Требования к методу неразрушающего контроля (далее – метод НК) определяют следующим образом.
С учетом реальных эксплуатационных нагрузок и условий определяют для изделия методами механики разрушения размеры несплошностей:
– критических размеров,
– допустимых в эксплуатации размеров,
– а также по действующим нормативным документам и/или ТУ на изготовление допустимые размеры несплошностей при изготовлении (нормы дефектов изделия при изготовлении).
В координатах “lg[P]- “, где [Р] – вероятность существования дефекта размером и более, – характеристический размер дефекта, строят нормативную кривую состояния изделия [Р( * )], где * – характеристический размер дефекта, задаваемый в интервале характеристических размеров дефектов от до максимально возможного в данном изделии дефекта, вероятность существования которых рассматривается. Нормативная кривая состояния изделия характеризует заданную (нормативную) вероятность существования дефектов в диапазоне от допустимых дефектов при изготовлении до критических размеров дефектов.
Выбирают имеющийся в распоряжении штатный или интересующий метод НК. Проводят контроль изделия данным методом НК.
Результаты контроля представляют в виде гистограммы в координатах (Nобн; ), где Nобн – число обнаруженных при контроле дефектов, – характеристический размер дефекта (как правило, в качестве характеристического размера дефекта выбирают линейный размер дефекта, или комбинацию линейных размеров дефекта, или площадь дефекта, или объем дефекта).
Полученную гистограмму аппроксимируют уравнением Nобн( )=A -n{1-([1- ])exp[- ( – 0)]- } или Nобн( )=А’exp(-n’ ){1-(1- )ехр[- ( – 0)]- },
где А, А’, n, n’, , – постоянные, которые определяют из условия максимального приближения уравнения Nобн( ) к результатам контроля, представленным в виде гистограммы. При этом в первом приближении может быть принята равной нулю ( =0);
0 – минимально доступный для выявления характеристический размер дефекта, может быть приравнен поисковому дефекту.
Определяют исходную дефектность (дефектность – общее количество дефектов в изделии с учетом распределения по типам, размерам, расположению; исходная дефектность – общее количество дефектов в изделии до контроля и ремонта выявленных дефектов) Nисх=f( ) по формуле
Nисх=А -n, или Nисх=А’ехр(-n’ ).
Исходную дефектность разделяют на достоверную часть   д и вероятностную часть (вероятностностная часть исходной дефектности – та часть исходной дефектности, которая характеризуется вероятностью существования дефектов в изделии меньшей единицы) > д, где – характеристический размер дефекта, д – характеристический размер дефектов на границе между достоверной и вероятностной частями.
д определяется из где max – максимально возможные размеры дефектов в данном изделии.
Вероятностная часть кривой исходной дефектности характеризует вероятность существования дефектов размером или больше в изделии; определяют по формуле .
Вероятностная часть является характеристикой состояния изделия. Чем выше значения вероятности существования дефекта, тем ниже качество изделия, тем ниже его надежность и безопасность.
На график, на котором нанесена нормативная кривая состояния изделия, наносят вероятностную часть кривой исходной дефектности Рисх( * ), отражающую вероятность существования дефекта с характеристическим размером * где * – характеристический размер дефекта, задаваемый в интервале характеристических размеров дефектов от до макс, вероятность существования которых рассматривается.
Из экспериментальных данных известно (например [1]), что вероятность обнаружения дефектов любым методом НК можно аппроксимировать уравнением Рвод( )=1-ехр[- ( – 0)]. Постоянную находят из условия, что после контроля и ремонта выявленных дефектов с использованием искомых методов и технических средств НК вероятностная часть кривой остаточной дефектности изделия должна достигнуть нормативной кривой состояния изделия. Указанное условие имеет вид Рисх( * )·[1-Рвод( )] [Р( * )], где Рисх( * ) – вероятностная часть исходной дефектности изделия до контроля искомыми средством и методом НК), [Р( * )] – нормативное значение состояния изделия, * – характеристический размер дефекта, задаваемый в интервале характеристических размеров дефектов от до макс, вероятность существования которых рассматривается.
На практике константу определяют как большую величину по результатам решения двух уравнений для двух реперных точек нормативной кривой состояния изделия (тех точек, по которым строили данную кривую), а именно: для точки, характеризующей вероятность существования дефекта размером, не меньше критического характеристического размера кр, и точки, характеризующей вероятность существования дефекта размером, не меньше допустимого в эксплуатации характеристического размера [ ]экспл.
Рисх( * )·{1-Рвод( )}=[Р( * )],
Рисх( * [ ]экспл)·{1-Рвод([ ]экспл)=[Р( * [ ]экспл)].
Таким образом, количественные требования к методу и средствам НК для контроля оценивают уравнением выявляемости дефектов Рвод( )=1-ехр[- ( – 0)], при этом значение постоянной определяют как большую величину из двух значений по уравнениям:
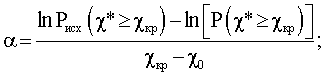
,
где кр – характеристический размер критического дефекта, [ ]экспл – допустимый размер дефекта при эксплуатации по расчетам механики разрушения, [Р( [ ]экспл)] – нормативная характеристика надежности изделия, задаваемая по вероятности существования в нем дефектов, больше допустимых в эксплуатации, [Р(  кр)] – нормативная характеристика безопасности изделия, задаваемая как вероятность существования в нем хотя бы одного дефекта, размер которого равен или более критического.
Определив требования, которым должен удовлетворять метод и средства НК, приступают к их подбору. С этой целью осуществляют следующие операции.
Изготавливают тест-образец для доводимого изделия, (что такое тест-образец для доводимого изделия и как его изготавливают, описано во втором варианте изобретения).
Изготовленный образец контролируют различными методами и техническими средствами НК. Определяют для каждого метода и технических средств вероятность выявления дефектов как соотношение количества выявленных дефектов Nвыявл к количеству заложенных дефектов Nзал.
Когда будет подобран метод и технические средства НК, удовлетворяющие определенным количественным требованиям, осуществляют новый контроль изделия подобранным методом и средствами.
По результатам проведенного контроля устраняют выявленные дефекты.
Проконтролированное и отремонтированное таким образом изделие удовлетворяет заданным требованиям к качеству, безопасности и надежности.
Второй вариант. Определяют изделие, качество, надежность и безопасность эксплуатации которого нужно обеспечить.
Для выбранного изделия задается вероятность существования в нем дефектов, определяющих его качество, надежность и безопасность (задается его качество, надежность, безопасность).
Определяют требования к методу неразрушающего контроля, по результатам контроля которым будет произведено устранение дефектов, следующим образом.
Определяют место наиболее вероятного возникновения технологических и/или эксплуатационных дефектов; с учетом реальных эксплуатационных нагрузок и условий определяют для изделия методами механики разрушения несплошности:
– критических размеров,
– допустимых в эксплуатации размеров,
– а также по действующим нормативным документам и/или ТУ на изготовление допустимые размеры несплошностей при изготовлении (нормы дефектов изделия при изготовлении).
Далее в координатах “IgP- ” строится нормативная кривая состояния изделия.
Изготавливается тест-образец для доводимого изделия. Тест-образец для доводимого изделия – это тест-образец по форме и в масштабе примерно 1:1 к изделию или его наиболее ответственной части (наиболее ответственная часть изделия – это та часть изделия, в которой наиболее вероятно возникновение дефектов (сварные швы, места максимальных эксплуатационных воздействий и т.п. или разрушение которых представляет опасность), тест-образец выполняют из того же материала и по той же технологии, что и изделие (выполнение тест-образца в большем или меньшем масштабе приведет к искажению результатов, так же, как и выполнение его из материала, отличного от материала изделия); в тест-образцы закладывают искусственные дефекты трех типов:
– дефекты, размеры которых лежат в интервале от размеров дефектов, допустимых при эксплуатации, до размеров критических для изделия в режиме эксплуатации дефектов,
– дефекты, размеры которых лежат в интервале от размеров, допустимых при изготовлении дефектов, до размеров дефектов, допустимых при эксплуатации,
– дефекты, размеры которых лежат в интервале от размеров минимальных, доступных для выявления дефектов, до размеров дефектов, допустимых при изготовлении (при этом допустимо, чтобы верхняя граница интервала превышала размеры дефектов, допустимых при изготовлении),
при этом первые два типа дефектов (несплошностей) должны имитировать дефекты эксплуатационной природы, а третьего типа – технологической (эксплуатационные дефекты – дефекты, которые могут развиться от технологических дефектов или зародиться и развиться под действием эксплуатационных нагрузок (трещины усталости, трещины коррозионного растрескивания под напряжением и т.п.), технологические дефекты – это дефекты, возникновение которых связано с особенностями технологии изготовления или монтажа (непровары, несплавления, поры и т.п.)). При этом возможна закладка различного сочетания типов дефектов (одного, любых двух, трех), при необходимости, возможно также изготовление различного числа образцов, в каждом из которых будет заложен один тип дефектов или их различное сочетание.
Все заложенные дефекты должны быть скрытыми от операторов НК, т.е. быть внутренними (подповерхностными) или, если дефект поверхностный, располагаться в месте, недоступном для визуального обнаружения (или иметь размеры, которые невозможно зафиксировать визуально).
Также следует отметить, что дефекты располагают в образце случайным образом, например, нумеруя их и пользуясь таблицами случайных чисел.
Минимальное допустимое расстояние между дефектами определяют исходя из условия существования одиночных дефектов (если закладываются одиночные дефекты) или меньше – для групповых трещин (условия взаимного влияния известны, например, Методические рекомендации МР 108.7-86. М., ЦНИИТМАШ, 1986).
Число дефектов каждого типа должно быть достаточным для статистической обработки результатов, например, не менее 9 шт (При меньшем количестве результаты менее достоверны).
Таким образом, тест-образец для доводимого изделия выполнен в форме изделия или наиболее ответственной его части, из того же материала и по той же технологии, что и изделие. При этом тест-образец содержит одну или более из трех групп расположенных случайным образом дефектов (если дефекты располагать не случайным образом, то это даст возможность оператору предсказывать тип и размеры обнаруженных дефектов в зависимости от их расположения в образце):
– дефекты, размеры которых лежат в интервале от размеров дефектов, допустимых при эксплуатации, до размеров критических для изделия в режиме эксплуатации дефектов,
– дефекты, размеры которых лежат в интервале от размеров, допустимых при изготовлении дефектов, до размеров дефектов, допустимых при эксплуатации,
– дефекты, размеры которых лежат в интервале от размеров минимальных, доступных для выявления дефектов, до размеров дефектов, допустимых при изготовлении (при этом допустимо, чтобы верхняя граница интервала превышала размеры дефектов, допустимых при изготовлении),
при этом первые два типа дефектов (несплошностей) имитируют дефекты эксплуатационной природы, а третьего типа – технологической.
(Любой дефект консервативно можно смоделировать трещиной, а любую трещину можно описать эллипсом с полуосями: короткой а и длинной с.)
Возможны различные варианты закладки дефектов в тест-образец.
В тест-образец закладывают дефекты в виде эллипсов, а соотношение осей эллипса принимают исходя из условия максимальной скорости роста дефекта в эксплуатационном поле напряжений.
В тест-образец закладывают дефекты в виде эллипсов, при этом соотношение осей эллипса принимают произвольное, а в качестве характеризующей размер дефекта величины принимают площадь плоскостного дефекта или площадь проекции объемного дефекта на плоскость вероятного развития дефекта.
В тест-образец закладывают дефекты в виде эллипсов, при этом количество дефектов и соотношение осей эллипса выбирают с использованием математических методов планирования эксперимента, исходя из условия минимизации числа закладываемых дефектов (К.Дэниел. Применение статистики в промышленном эксперименте. М.: Мир, 1979).
В случае, если закладываемые в тест-образец дефекты не имеют форму эллипса, то их схематизируют эллипсами.
Если в качестве метода неразрушающего контроля выбран рентгеновский метод, то возможно изготовление тест-образца для радиационного контроля для доводимого изделия. Тест-образец для радиационного контроля для доводимого изделия – это тест-образец в форме изделия или наиболее ответственной его части, выполненный из того же материала и по той же технологии, что и изделие. В образце выполнено цилиндрическое отверстие. Тест-образец содержит цилиндрический вкладыш, вставляемый в отверстие на скользящей посадке. Во вкладыш заложены искусственные дефекты трех типов:
– дефекты, размеры которых лежат в интервале от размеров дефектов, допустимых при эксплуатации, до размеров, критических для изделия в режиме эксплуатации дефектов,
– дефекты, размеры которых лежат в интервале от размеров, допустимых при изготовлении дефектов, до размеров дефектов, допустимых при эксплуатации,
– дефекты, размеры которых лежат в интервале от размеров минимальных, доступных для выявления дефектов, до размеров дефектов, допустимых при изготовлении (при этом допустимо, чтобы верхняя граница интервала превышала размеры дефектов, допустимых при изготовлении),
при этом первые два типа дефектов (несплошностей) должны имитировать дефекты эксплуатационной природы, а третьего типа – технологической.
Возможна закладка во вкладыш различное сочетание типов дефектов: два любых типа, только один тип, три типа дефектов.
Отверстие для вкладыша выполняется в той части изделия, в которой появление дефектов во время изготовления и эксплуатации наиболее вероятно (сварные швы, места концентрации напряжения и т.п.).
Вкладыш выполняется из того же материала, что и участок тест-образца, в котором выполнено отверстие под вкладыш, и изготовляется по той же технологии, например, если хотят исследовать качество сварного шва, то вкладыш изготавливают из наплавленного металла той же марки электрода, что и сварной шов.
Цилиндрическая форма вкладыша позволяет поворачивать его вокруг своей оси, в результате чего меняется пространственная ориентация заложенных в него дефектов при остающихся постоянными размерах. Что, в свою очередь, позволяет определить выявляемость дефекта в зависимости от его ориентации. Вкладыш изготавливается по свободной посадке.
Возможны различные варианты закладки дефектов в тест-образец.
В тест-образец закладывают дефекты в виде эллипсов, а соотношение осей эллипса принимают исходя из условия максимальной скорости роста дефекта в эксплуатационном поле напряжений.
В тест-образец закладывают дефекты в виде эллипсов, при этом соотношение осей эллипса принимают произвольное, а в качестве характеризующей размер дефекта величины принимают площадь плоскостного дефекта или площадь проекции объемного дефекта на плоскость вероятного развития дефекта.
В тест-образец закладывают дефекты в виде эллипсов, при этом количество дефектов и соотношение осей эллипса выбирают с использованием математических методов планирования эксперимента, исходя из условия минимизации числа закладываемых дефектов.
В случае, если закладываемые в тест-образец дефекты не имеют форму эллипса, то их схематизируют плоскими дефектами, имеющими форму эллипса.
При обработке результатов контролей различия между типами дефектов можно не делать (тип дефекта – это характеристики дефекта, такие как: природа (технологический или эксплуатационный), расположение (поверхностный или подпорверхностный) и т.д., а различать их только по характеристическим размерам. Как правило, в качестве характеристического размера дефекта выбирают линейный размер дефекта, или комбинацию линейных размеров дефекта, или площадь дефекта, или объем дефекта.
Выбирают любой конкретный метод неразрушающего контроля. Данным (выбранным) методом НК проводится контроль тест-образца для доводимого изделия, результаты контроля сравнивают с реальными дефектами, заложенными в тест-образец. Для каждого характеристического размера дефекта определяют соотношение “число обнаруженных в тест-образце дефектов Nобн то( ) разделить на число заложенных в тест-образец дефектов Nзал то( )”, которое характеризует вероятность обнаружения данного характеристического размера дефекта Рвод( ):
Рвод( ):=Nобн то( )/Nзал то( ).
Проводят контроль изделия выбранным методом НК (выбрав какой-либо метод НК, все контроли, как изделия, так и тест-образцов, проводят данным методом).
Определяют исходную дефектность изделия Nисх( )=f( ). Исходная дефектность изделия определяется как отношение числа обнаруженных при контроле изделия дефектов данного характеристического размера Nобн изд( ) к вероятности выявления дефектов данным методом НК.
Nисх( )=Nобн изд( )/Рвод( ).
Исходную дефектность разделяют на достоверную часть    и вероятностную часть > , где – характеристический размер дефекта,  – размер дефектов на границе между достоверной и вероятностной частями.
 определяется из , где max – максимально возможные размеры дефектов в данном изделии.
На график, на котором нанесена нормативная кривая состояния изделия, наносят вероятностную часть кривой исходной дефектности Pисх( * ), отражающую вероятность существования дефекта с характеристическим размером * , где * – характеристический размер дефекта, задаваемый в интервале характеристических размеров дефектов от до макс, вероятность существования которых рассматривается. Рисх определяют по формуле:
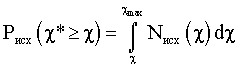
Количественные требования к методу неразрушающего контроля для повторного контроля оценивают уравнением выявляемости дефектов Рвод( )=1-ехр[- ( – 0)], при этом 0 определяют равной чувствительности метода контроля, а значение постоянной определяют как большую величину из двух значений:
где кр – характеристический размер критического дефекта, [ ]экспл – допустимый размер дефекта при эксплуатации по расчетам механики разрушения, [Р( [ )экспл)] – нормативная характеристика надежности изделия, задаваемая по вероятности существования в нем дефектов, больше допустимых в эксплуатации, [Р(  кр)] – нормативная характеристика безопасности изделия, задаваемая как вероятность существования в нем хотя бы одного дефекта, размер которого равен или более критического.
Определив требования к НК, подбирают удовлетворяющие им метод и технические средства НК. С этой целью осуществляют следующие операции.
Тест-образец для доводимого изделия контролируют различными методами и техническими средствами НК, определяя для каждого метода и технических средств вероятность выявления дефектов как соотношение количества выявленных дефектов Nвыявл к количеству заложенных дефектов Nзал.
Когда будет подобран метод НК и технические средства, удовлетворяющие указанным выше количественным требованиям, осуществляют новый контроль изделия подобранными методом и средствами. По результатам этого контроля устраняют выявленные дефекты.
Проконтролированное и отремонтированное таким образом изделие удовлетворяет заданным требованиям к качеству, безопасности и надежности.
Третий вариант. Определяют изделие, качество, надежность и безопасность эксплуатации которого нужно обеспечить.
Для выбранного изделия задается вероятность существования в нем дефектов, определяющих его качество, надежность и безопасность (нормативные требования к его качеству, надежности, безопасности).
Определяют требования к методу неразрушающего контроля, по результатам контроля которым будет произведено устранение дефектов, следующим образом.
С учетом реальных эксплуатационных нагрузок и условий определяют для изделия методами механики разрушения размеры несплошностей:
– критических размеров,
– допустимых в эксплуатации размеров,
– а также по действующим нормативным документам и/или ТУ на изготовление допустимые размеры несплошностей при изготовлении (нормы дефектов изделия при изготовлении).
Далее в координатах “IgP- ” строится нормативная кривая состояния изделия.
Выбирают любой имеющийся в распоряжении или интересующий метод НК. Проводят контроль изделия данным методом НК. Результаты контроля представляют в виде гистограммы в координатах (Nобн; ), где Nобн – число обнаруженных при контроле дефектов, – характеристический размер дефекта.
Полученную гистограмму аппроксимируют уравнением
Nобн( )=A -n{1-(1- )exp[- ( – 0)]- } или
Nобн( )=А’exp(-n’ ){1-(1- )ехр[- { – 0)]- },
где А, А’, n, n’, , – постоянные, которые определяют из условия максимального приближения уравнения Nобн( ) к результатам контроля, представленным в виде гистограммы;
0 – минимально доступный для выявления характеристический размер дефекта.
Определяют исходную дефектность Nисх по формуле
Nисх=А -n, или Nисх=A’ехр(-n’ ).
Также определяют вероятность обнаружения дефекта по формуле
Рвод=1-(1- )ехр[- ( – 0)]- (в первом приближении =0).
Определяют остаточную дефектность (остаточная дефектность – дефектность изделия после устранения выявленных контролем дефектов) Nост= ( ) как разность исходной дефектности Nисх( ) и числа обнаруженных при контроле изделия дефектов Nобн изд( ).
Остаточную дефектность разделяют на достоверную часть    и вероятностную часть (вероятностная часть остаточной дефектности – та часть остаточной дефектности, которая характеризуется вероятностью существования дефектов в изделии, меньшей единицы) > , где – характеристический размер дефекта,  – характеристический размер дефектов на границе между достоверной и вероятностной частями.
 определяется из , где max – максимально возможные размеры дефектов в данном изделии.
Данная вероятностная часть кривой остаточной дефектности характеризует вероятность существования дефектов заданного размера в изделии и определяется по формуле:
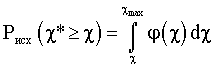
Вероятностная часть кривой является характеристикой состояния изделия. Чем выше значения вероятности существования дефекта, тем ниже качество изделия.
На график, на котором нанесена нормативная кривая состояния изделия, наносят вероятностную часть кривой остаточной дефектности Pост( * ), отражающую вероятность существования дефекта с характеристическим размером * где * – характеристический размер дефекта, задаваемый в диапазоне от до макс.
Количественные требования к методу неразрушающего контроля для повторного контроля оценивают уравнением выявляемости дефектов Рвод( )=1-ехр[- ( – 0)], при этом значение постоянной определяют как большее значение из двух:
где 0 принимают равной чувствительности метода контроля; кр – характеристический размер критического дефекта, [ ]экспл – допустимый размер дефекта при эксплуатации по расчетам механики разрушения, [Р( [ ]экспл)] – нормативная характеристика надежности изделия, задаваемая по вероятности существования в нем дефектов, больше допустимых в эксплуатации, [Р(  )] – нормативная характеристика безопасности изделия, задаваемая как вероятность существования в нем хотя бы одного дефекта, размер которого равен или более критического.
Определив требования, которым должны удовлетворять метод и средства НК, приступают к их подбору. С этой целью осуществляют следующие операции.
Изготавливают тест-образец для доводимого изделия (в случае выбора радиационного метода контроля возможно изготовление тест-образца для радиационного контроля для доводимого изделия). Осуществляют его контроль различными методами НК и различными техническими средствами. Определяют для каждого метода и технических средств НК вероятность выявления дефектов как соотношение количества выявленных дефектов Nвыявл к количеству заложенных дефектов Nзал.
Когда будет подобран метод НК и технические средства, удовлетворяющие указанным выше количественным требованиям, осуществляют новый контроль изделия подобранными методом и средствами. По результатам этого контроля и первого контроля устраняют выявленные дефекты.
Проконтролированное и отремонтированное таким образом изделие удовлетворяет заданным требованиям к качеству, безопасности и надежности.
Четвертый вариант. Определяют изделие, качество, надежность и безопасность эксплуатации которого нужно обеспечить.
Для выбранного изделия задается вероятность существования в нем дефектов, определяющих его качество, надежность и безопасность (нормативные требования к его качеству, надежности, безопасности).
Определяют требования к методу неразрушающего контроля, по результатам контроля которым будет произведено устранение дефектов, следующим образом.
Определяют место наиболее вероятного возникновения технологических и/или эксплуатационных дефектов; с учетом реальных эксплуатационных нагрузок и условий определяют для изделия методами механики разрушения несплошности:
– критических размеров,
– допустимых в эксплуатации размеров,
– а также по действующим нормативным документам и/или ТУ на изготовление допустимые размеры несплошностей при изготовлении (нормы дефектов изделия при изготовлении).
Далее в координатах “IgP- ” строится нормативная кривая состояния изделия.
Изготавливается тест-образец для доводимого изделия. Если в качестве метода неразрушающего контроля выбран рентгеновский метод, то возможно изготовление тест-образца для радиационного контроля для доводимого изделия.
Выбирают любой конкретный метод неразрушающего контроля. Данным (выбранным) методом НК проводят контроль тест-образца для доводимого изделия, результаты контроля сравнивают с реальными дефектами, заложенными в тест-образец. Для каждого характеристического размера дефекта определяется соотношение “число обнаруженных в тест-образце дефектов Nобн то( ) разделить на число заложенных в тест-образец дефектов Nзал то( )”, которое характеризует вероятность обнаружения данного типоразмера дефекта Рвод( ):
Рвод( )=Nобн то( )/Nзал то( ).
Проводят контроль изделия выбранным методом НК (выбрав какой-либо метод НК, все контроли, как изделия, так и тест-образцов, проводят данным методом).
Определяют исходную дефектность изделия Nисх. Исходная дефектность изделия определяется как отношение числа обнаруженных при контроле изделия дефектов данного размера Nобн изд( ) к вероятности выявления дефектов данным методом НК.
Nисх( )=Nобн изд( )/Рвод( ).
Определяют остаточную дефектность Nост= ( ) как разность исходной дефектности Nисх( ) и числа обнаруженных при контроле изделия дефектов Nобн изд( ).
Остаточную дефектность разделяют на достоверную часть   д и вероятностную часть > д, где – характеристический размер дефекта, д – размер дефектов на границе между достоверной и вероятностной частями.
д определяется из , где max – максимально возможные размеры дефектов в данном изделии.
На график, на котором нанесена нормативная кривая состояния изделия, наносят вероятностную часть кривой остаточной дефектности Рост( * ), отражающую вероятность существования дефекта с характеристическим размером * , где * – характеристический размер дефекта, задаваемый в интервале характеристических размеров дефектов от до макс, вероятность существования которых рассматривается. При этом Рост определяется по формуле:
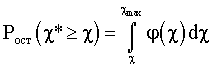
Количественные требования к методу неразрушающего контроля для повторного контроля оценивают уравнением выявляемости дефектов Рвод( )=1-ехр[- ( – 0)], при этом значение постоянной определяют как большее значение по уравнениям:
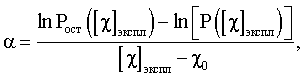
где 0 – чувствительность метода контроля, кр – характеристический размер критического дефекта, [ ]экспл – допустимый размер дефекта при эксплуатации по расчетам механики разрушения, [Р( [ ]экспл)] – нормативная характеристика надежности изделия, задаваемая по вероятности существования в нем дефектов, больше допустимых в эксплуатации, [P(  кр)] – нормативная характеристика безопасности изделия, задаваемая как вероятность существования в нем хотя бы одного дефекта, размер которого равен или более критического.
Определив требования, которым должны удовлетворять метод и технические средства НК, приступают к их подбору. С этой целью осуществляют следующие операции.
Тест-образец для доводимого изделия контролируют различными методами и средствами НК.
Определяют для каждого метода и технических средств НК вероятность выявления дефектов как соотношение количества выявленных дефектов Nвыявл к количеству заложенных дефектов Nзал.
Когда будут подобраны метод и средства НК, удовлетворяющие указанным выше количественным требованиям, осуществляют новый контроль изделия подобранными методом и средствами НК.
По результатам проведенного нового контроля и первого контроля устраняют выявленные дефекты.
Проконтролированное и отремонтированное таким образом изделие удовлетворяет заданным требованиям к качеству, безопасности и надежности.
Пятый вариант.
Группа однотипных изделий – это группа изделий, которые идентичны по геометрическим формам, материалам, из которых они изготовлены, технологиям изготовления и условиям эксплуатации (возможны незначительные отличия между отдельными изделиями группы в пределах требований проектно-конструкторской документации, других технических условий).
Способ доведения до заданного уровня качества, надежности и безопасности с учетом методики контроля группы однотипных изделий заключается в том, что определяют группу однотипных изделий, качество, надежность и безопасность которых необходимо обеспечить. Задают требования к качеству, надежности и безопасности названной группы – поскольку изделия однотипны, требования к каждому отдельному изделию группы будут одинаковы. Выбирают одно любое изделие из данной группы. Осуществляют НК выбранного изделия любым штатным методом. Осуществляют ремонт изделия по результатам проведенного контроля.
Определяют требования к методу и техническим средствам следующего неразрушающего контроля. Следует отметить, что определение требований к методу и средствам контроля проводится любым методом из описанных выше первых двух вариантов способа доведения изделия до заданного уровня качества, надежности и безопасности с учетом методики контроля.
После того как определили требования к средствам и методам НК, осуществляют их подбор. При этом подбор осуществляют так, как описано в приведенных выше вариантах способа доведения изделия до заданного уровня качества, надежности и безопасности.
Подобранными средствами и методом НК осуществляют НК всей группы однотипных изделий и по результатам этого контроля ремонтируют изделия.
Проконтролированные подобранными таким способом средствами и методом изделия группы считаются удовлетворяющими заданным требованиям к их качеству, надежности и безопасности.
Пример. Дан трубопровод энергетической установки (фиг.1).
Любой дефект консервативно можно смоделировать трещиной, а любую трещину можно описать эллипсом с полуосями: короткой а и длинной с.
Определенные методами механики разрушения с учетом условий эксплуатации размеры критических и допустимых в эксплуатации дефектов равны соответственно:
акр=32 мм, aэкспл=12 мм (при а/с=0,5, при данном соотношении осей дефект развивается наиболее быстро),
и допустимый дефект при изготовлении [а]изг=1,5 мм.
В данном примере в качестве характеристического размера дефекта принят размер короткой полуоси эллипса, которым схематизированы дефекты.
при этом при соотношении полуосей дефектов а/с=0,5.
Определяют требования к безопасности трубопровода как условие разрыва трубопровода с вероятностью Рразрыва 10-4, а требования к надежности как существование в трубопроводе дефекта [а]экспл с вероятностью Рдеф.эксплуат=5·10-2. Указанные условия можно записать следующим образом:
[Р(а [а]кр)] 10-4 – условие безопасности,
[Р(а [а]экспл)] 5·10-2 – условие надежности.
Нормативные требования к качеству, надежности, безопасности изделия можно представить графически в виде уравнения [Р(а* а)]=f(a).
Функция f( ) может иметь различный вид. Ниже данная функция принята в виде f(a)=b·10-Da, следовательно, получаем, что [Р(а* а)]=f(a)=b·10-Da.
С учетом размеров допустимых в эксплуатации дефектов, дефектов критического для данного изделия размеров, а также определенных требований к качеству, надежности и безопасности изделия определяют постоянные b и D из системы уравнений:
b·10-D·32=10-4,
b·10-D·12=5·10-2, из которых получается, что b=3,15; D=0,15, a нормативная кривая состояния изделия имеет вид [P(а* а)]=3,15·10-0,15. Это уравнение можно представить графически (фиг.2, кривая 1).
Изготавливают тест-образец для доводимого изделия. В сварной шов этого тест-образца заложено 20 скрытых дефектов типа трещин по технологии, описанной, например, в А.с. 1420519 СССР (Бюл. Изобрет. 1992 г., №6). Дефекты имеют форму эллипса с соотношением полуосей а/с=0.5 и с размерами:
а=30 мм; с=60 мм – 10 шт (дефекты 1 типоразмера);
а=20 мм; с=40 мм – 10 шт (дефекты 2 типоразмера).
Проводят контроль образца имеющимся в распоряжении методом ультразвукового контроля (УЗК). В результате проведенного контроля выявлено:
дефектов 1 типоразмера – 4;
дефектов 2 типоразмера – 3.
С учетом уравнения выявляемости дефектов (вероятности обнаружения дефекта) Рвод(а), принимаемого в виде Рвод(а)=1-ехр[- (а-а0)], где а0 – чувствительность УЗК; а0=1,0 мм;
– коэффициент выявляемости;
а также результатов контроля тест-образца, которые показали, что при а=30 мм Рвод(а=30)=0,4, а при а=20 мм Рвод(а=20)=0,3, определили значение как меньшее из двух значений: =0,0176.
Тем же методом УЗК, что и тест-образец, контролируют изделие.
Результаты контроля представлены в виде гистограммы на фиг.3.
Гистограмма может быть описана кривой 1 на том же чертеже в координатах Nобн-a.
С использованием кривой 1 восстанавливают кривую исходной дефектности Nисх(а) с использованием соотношения , где Рвод(а) определили ранее на тест-образце. Результат представлен в виде кривой 2 на фиг.3 в координатах Nисх(а)-а.
Кривая 2 на фиг.3 может быть аппроксимирована уравнением Nисх=Aa-n- с коэффициентами А=953; n=4,4.
Определяют вероятностную часть исходной дефектности изделия по уравнению:
, при этом границу между вероятностной частью и достоверной частью исходной дефектности а определяют из условия Рисх(а* а)=1.
Определенная указанным образом кривая, характеризующая вероятность существования дефектов в изделии до его контроля, представлена в виде кривой 2 на фиг.2.
Как видно из сравнения кривой 2 с нормативной кривой 1, состояние изделия до контроля является неудовлетворительным.
После ремонта выявленных дефектов остаточная дефектность изделия может быть определена по формуле Nост(a)=Nисх(a)-Nобн(a) и представлена в виде кривой 3 на фиг.3.
Определяют вероятностную часть остаточной дефектности по уравнению:
, при этом границу между вероятностной частью и достоверной частью остаточной дефектности а определяют из условия Рост(а* а)=1.
Определенная указанным образом кривая, характеризующая вероятность существования дефектов в изделии после его контроля и ремонта, представлена в виде кривой 3 на фиг.2.
Из сравнения кривой 3 с нормативной кривой 1 видно, что ремонт выявленных УЗК дефектов не позволил довести состояние изделия до требуемого уровня.
По уравнениям
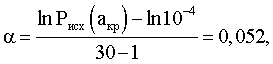

определяют требования к достоверности техническим средствам и методу следующего контроля. Искомая характеристика равна большей из двух величин: иск=0,052. Кривые Рвод(а), имеющие иск=0,052 и =0,0176, показаны на фиг.4.
С использованием тест-образца из числа имеющихся средств и методов НК подбирают такой метод контроля, который удовлетворял бы условию   иск.
После нахождения метода и средства НК, удовлетворяющего указанным условиям, проводят второй контроль. Изделие ремонтируют по результатам первого и второго контроля, что позволяет обеспечить нормативные требования к его состоянию.
Формула изобретения
1. Способ доведения изделия до заданного уровня качества, безопасности и надежности с учетом методики контроля, заключающийся в том, что осуществляют неразрушающий контроль (НК) изделия и устраняют выявленные дефекты, отличающийся тем, что задают требования к качеству, надежности и безопасности изделия, определяют требования к методу и техническим средствам контроля, для этого с учетом реальных эксплуатационных нагрузок и условий определяют для изделия размеры критических и допустимых в эксплуатации несплошностей, а также нормы дефектов изделия при изготовлении в координатах lg[P]- , где [Р] – заданная вероятность существования дефекта размером и более, – характеристический размер дефекта, строят нормативную кривую состояния изделия [Р(   )], где  – характеристический размер дефекта, задаваемый в интервале характеристических размеров дефектов от до максимально возможного в данном изделии дефекта, вероятность существования которых рассматривается, результаты первого НК представляют в виде гистограммы в координатах (Nобн; ), где Nобн – число обнаруженных при контроле дефектов, – характеристический размер дефекта, полученную гистограмму аппроксимируют уравнением Nобн( )=A -n{1-(1- ])exp[- ( – 0)]- } или
Nобн( )=А’exp(-n’ ){1-(1- )ехр[- ( – 0)]- },
где А, А’, n, n’, , – постоянные, которые определяют из условия максимального приближения уравнения Nобн( ) к результатам контроля, представленным в виде гистограммы, 0 – минимально доступный для выявления характеристический размер дефекта,
определяют исходную дефектность Nисх=f( ) по формуле
Nисх=А -n, или Nисх=A’ехр(-n’ ),
исходную дефектность разделяют на достоверную часть и вероятную часть,
на график, на котором нанесена нормативная кривая состояния изделия, наносят вероятностную часть кривой исходной дефектности Рисх(   ), отражающую вероятность существования дефекта с характеристическим размером    , где  – характеристический размер дефекта, задаваемый в интервале характеристических размеров дефектов от до макс, вероятность существования которых рассматривается,
количественные требования к методу и техническим средствам НК для повторного контроля оценивают уравнением выявляемости дефектов Рвод( )=1-(1- )exp[- ( – 0)]- или в первом приближении, при этом Рвод( )=1-ехр[- ( – 0)],
значение постоянной определяют как большее значение по уравнениям
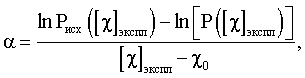
где 0 – минимальный размер дефекта, выявленного данным методом контроля; 0 должен быть меньше, чем допустимый дефект при изготовлении;
кр – характеристический размер критического дефекта, [ ]экспл – допустимый размер дефекта при эксплуатации по расчетам механики разрушения, [Р[ ]экспл] – нормативная характеристика надежности изделия, задаваемая по вероятности существования в нем дефектов, больше допустимых в эксплуатации, [Р( кр)] – нормативная характеристика безопасности изделия, даваемая как вероятность существования в нем хотя бы одного дефекта, размер которого равен или более критического, Рисх( кр) – вероятность существования в изделии дефекта, равного или больше кр; Рисх([ ]экспл) – вероятность существования в изделии дефекта, равного или большего [ ]экспл,
определив требования, которым должен удовлетворять метод и средства НК, осуществляют их подбор, для этого изготавливают тест-образец для доводимого изделия, изготовленный образец контролируют различными методами и техническими средствами НК, определяют для каждого метода и технических средств вероятность выявления дефектов как соотношение количества выявленных дефектов Nвыявл к количеству заложенных дефектов Nзал, метод и средства НК считают удовлетворяющим определенным ранее требованиям к ним, когда вероятность выявления дефектов данным методом и средствами в изделии будет равна или более определенного количественного требования, по результатам второго контроля устраняют выявленные дефекты.
2. Способ доведения изделия до заданного уровня качества, надежности, безопасности по п.1, отличающийся тем, что при проведении НК радиационным методом используют тест-образец для радиационного контроля для доводимого изделия.
3. Способ доведения изделия до заданного уровня качества, надежности, безопасности с учетом методики контроля, заключающийся в том, что осуществляют неразрушающий контроль (НК) изделия и устраняют выявленные дефекты, отличающийся тем, что задают требования к качеству, надежности и безопасности изделия, определяют требования к методу и техническим средствам контроля, для этого с учетом реальных эксплуатационных нагрузок и условий определяют для изделия размеры критических и допустимых в эксплуатации несплошностей, а также нормы дефектов изделия при изготовлении, в координатах lg[P]- , [Р] – заданная вероятность существования дефекта размером и более, – характеристический размер дефекта, строят нормативную кривую состояния изделия, изготавливают тест-образец для доводимого изделия, тем же методом НК, что и проведенный НК изделия, проводится контроль тест-образца для доводимого изделия, результаты контроля сравнивают с реальными дефектами, заложенными в тест-образец, для каждого характеристического размера дефекта определяют соотношение «число обнаруженных в тест-образце дефектов Nобн то( ) разделить на число заложенных в тест-образец дефектов Nзал то( )”, которое характеризует вероятность обнаружения дефекта данного характеристического размера Рвод( ): Рвод( )=Nобн то( )/Nзал то( ),
определяют исходную дефектность изделия Nисх( )=f( ), как отношение числа обнаруженных при контроле изделия дефектов данного характеристического размера Nобн изд( ) к вероятности выявления дефектов данным методом НК,
Nисх( )=Nобн изд( )/Рвод( ),
исходную дефектность разделяют на достоверную часть и вероятностную часть,
на график, на котором нанесена нормативная кривая состояния изделия, наносят вероятностную часть кривой исходной дефектности Рисх(   ), где  – характеристический размер дефекта, задаваемый в интервале характеристических размеров дефектов от до макс, вероятность существования которых рассматривается,
количественные требования к методу и средствам неразрушающего контроля для повторного контроля оценивают уравнением выявляемости дефектов Pвод( )=1-exp[- ( – 0)], при этом значение постоянной определяют как большее из двух значений по уравнениям
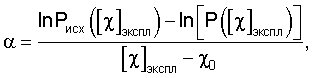
где 0 – минимальный размер дефекта, выявленного данным методом контроля; 0 должен быть меньше, чем допустимый дефект при изготовлении; кр – характеристический размер критического дефекта, [ ]экспл – допустимый размер дефекта при эксплуатации по расчетам механики разрушения, [Р( [ ]экспл)] – нормативная характеристика надежности изделия, задаваемая по вероятности существования в нем дефектов, равных или больше допустимых в эксплуатации, [Р(  кр)] – нормативная характеристика безопасности изделия, задаваемая как вероятность существования в нем хотя бы одного дефекта, размер которого равен или более критического, [Р( [ ]изг)]
определив требования, подбирают удовлетворяющие им метод и технические средства НК, для этого:
используют ранее изготовленный тест-образец для доводимого изделия, этот образец контролируют различными методами и техническими средствами НК, определяя для каждого метода и технических средств вероятность выявления дефектов как соотношение количества выявленных дефектов Nвыявл к количеству заложенных дефектов Nзал, метод и средства НК считают удовлетворяющим определенным ранее требованиям, когда вероятность выявления дефектов данным методом и средствами в изделии будет равна или более определенного количественного требования,
по результатам второго контроля устраняют выявленные дефекты.
4. Способ доведения изделия до заданного уровня качества, надежности, безопасности по п.3, отличающийся тем, что при проведении НК радиационным методом используют тест-образец для радиационного контроля для доводимого изделия.
5. Способ доведения изделия до заданного уровня качества, безопасности, надежности с учетом методики контроля заключающийся в том, что осуществляют неразрушающий контроль (НК) изделия и устраняют выявленные дефекты, отличающийся тем, что задают требования к качеству, надежности и безопасности изделия, определяют требования к методу и техническим средствам контроля, для этого: с учетом реальных эксплуатационных нагрузок и условий определяют для изделия размеры критических и допустимых в эксплуатации несплошностей, а также нормы дефектов изделия при изготовлении, в координатах «lg[P]- », где [Р] – заданная вероятность существования дефекта размером и более, – характеристический размер дефекта, строят нормативную кривую состояния изделия, результаты контроля представляют в виде гистограммы в координатах (Nобн; ), где Nобн – число обнаруженных при контроле дефектов, – характеристический размер дефекта, полученную гистограмму аппроксимируют уравнением Nобн( )=A -n{1-(1- )exp[- ( – 0)]- },
где А, n, , – постоянные, которые определяют из условия максимального приближения уравнения Nобн, ( ) к результатам контроля, представленным в виде гистограммы,
0 – минимально доступный для выявления характеристический размер дефекта,
определяют исходную дефектность Nисх по формуле
Nисх=А -n,
определяют вероятность обнаружения дефекта по формуле
Рвод=1-(1- )ехр[- ( – 0)]- ,
определяют остаточную дефектность Nост= ( ) как разность исходной дефектности Nисх( ) и числа обнаруженных при контроле изделия дефектов Nобн.изд.( ),
остаточную дефектность разделяют на достоверную часть и вероятностную часть,
на график, на котором нанесена нормативная кривая состояния изделия, наносят вероятностную часть кривой остаточной дефектности Рост(   ), отражающую вероятность существования дефекта с характеристическим размером    , где  – характеристический размер дефекта, задаваемый в качестве нижней границы интервала характеристических размеров дефектов, вероятность существования которых рассматривается,
количественные требования к методу и средствам неразрушающего контроля для повторного контроля оценивают уравнением выявляемости дефектов Рвод( )=1ехр[- ( – 0)], при этом значение постоянной определяют как большее значение по уравнениям
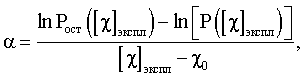
где кр – характеристический размер критического дефекта, [ ]изг – допустимый размер дефекта при эксплуатации по расчетам механики разрушения, [Р( [ ]экспл)] – нормативная характеристика надежности изделия, задаваемая по вероятности существования в нем дефектов, больше допустимых в эксплуатации, – нормативная характеристика безопасности изделия, задаваемая как вероятность существования в нем хотя бы одного дефекта, размер которого равен или более критического, Рост( [ ]изг – вероятность существования в изделии дефектов, равных или больше [ ]экспл после ремонта выявленных дефектов; Рост(  кр) вероятность существования в изделии дефектов, равных или больше кр после ремонта выявленных дефектов,
определив требования, которым должны удовлетворять метод и средства НК приступают к их подбору, для этого:
изготавливают тест-образец для доводимого изделия, этот образец контролируют различными методами и техническими средствами НК, определяя для каждого метода и технических средств вероятность выявления дефектов как соотношение количества выявленных дефектов Nвыявл к количеству заложенных дефектов Nзал, метод и средства НК считают удовлетворяющим определенным ранее требованиям, когда вероятность выявления дефектов данным методом и средствами в изделии будет равна или более определенного количества требования,
по результатам первого и второго контроля устраняют выявленные дефекты.
6. Способ доведения изделия до заданного уровня качества, надежности, безопасности по п.5, отличающийся тем, что при проведении НК радиационным методом используют тест-образец для радиационного контроля для доводимого изделия.
7. Способ доведения изделия до заданного уровня качества, надежности, безопасности заключающийся в том, что осуществляют неразрушающий контроль (НК) изделия и устраняют выявленные дефекты, отличающийся тем, что задают требования к качеству, надежности и безопасности изделия, определяют требования к методу и техническим средствам следующего контроля, для этого с учетом реальных эксплуатационных нагрузок и условий определяют для изделия размеры критических и допустимых в эксплуатации несплошностей, а также нормы дефектов изделия при изготовлении, в координатах lg[P]- , где [Р] – заданная вероятность существования дефекта размером и более, – характеристический размер дефекта, строят нормативную кривую состояния изделия, изготавливают тест-образец для доводимого изделия, тем же методом НК, что и проведенный НК изделия, проводится контроль тест-образца для доводимого изделия, результаты контроля сравнивают с реальным дефектами, заложенными в тест-образец, для каждого характеристического размера дефекта определяют соотношение “число обнаруженных в тест-образце дефектов Nобн то( ), разделить на число заложенных в тест-образец дефектов Nобн то( )”, которые характеризует вероятность обнаружения данного характеристического размера дефекта Pвод( ): Рвод( )=Nобн то( )/Nзал то( ),
определяют исходную дефектность изделия Nисх как отношение числа обнаруженных при контроле изделия дефектов данного размера Nобн изд( ) к вероятности выявления дефектов данным методом НК
Nисх( )=Nобн изд( )/Рвод( ),
определяют остаточную дефектность Nост= ( ) как разность исходной дефектности Nисх( ) и числа обнаруженных при контроле изделия дефектов Nобн изд( ),
остаточную дефектность разделяют на достоверную часть и вероятностную часть,
на график, на котором нанесена нормативная кривая состояния изделия, наносят вероятностную часть кривой исходной дефектности Рисх(   ), отражающую вероятность существования дефекта с характеристическим размером    , где  – характеристический размер дефекта, задаваемый в интервале характеристических размеров от до макс, вероятность существования которых рассматривается,
количественные требования к методу неразрушающего контроля для повторного контроля оценивают уравнением выявляемости дефектов Рвод( )=1-exp[- ( – 0)], при этом значение постоянной определяют как большее значение по уравнениям
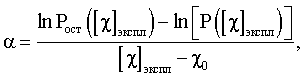
где 0 – минимальный размер дефекта, допущенного для выявления, как правило, 0 меньше допустимого дефекта в изготовлении; кр – характеристический размер критического дефекта, [ ]экспл – допустимый размер дефекта при эксплуатации по расчетам механики разрушения, [Р( [ ]экспл)] – нормативная характеристика надежности изделия, задаваемая по вероятности существования в нем дефектов, больше допустимых в эксплуатации, – нормативная характеристика безопасности изделия, задаваемая как вероятность существования в нем хотя бы одного дефекта, размер которого равен или более критического, Рост( [ ]изг) – вероятность существования в изделии дефектов, равных или больше [ ]экспл после ремонта выявленных дефектов; Рост(  кр) вероятность существования в изделии дефектов, равных или больше кр после ремонта выявленных дефектов, определив требования, подбирают удовлетворяющие им метод и технические средства НК, для этого используют тест-образец для доводимого изделия, этот образец контролируют различными методами и техническими средствами НК, определяя для каждого метода и технических средств вероятность выявления дефектов как соотношение количества выявленных дефектов Nвыявл к количеству заложенных дефектов Nзал, метод и средства НК считают удовлетворяющим определенным ранее требованиям, когда вероятность выявления дефектов данным методом и средствами в изделии будет равна или более определенного количественного требования, по результатам второго контроля устраняют выявленные дефекты.
8. Способ доведения изделия до заданного уровня качества, надежности, безопасности по п.7, отличающийся тем, что при проведении НК радиационным методом используют тест-образец для радиационного контроля для доводимого изделия.
9. Способ доведения до заданного уровня качества, надежности и безопасности с учетом методики контроля группы однотипных изделий, заключающийся в том, что определяют группу однотипных изделий, качество, надежность и безопасность которых необходимо обеспечить, задают требования к качеству, надежности и безопасности названной группы, выбирают одно любое изделие из данной группы, осуществляют НК выбранного изделия любым методом НК, по результатам проведенного контроля определяют требования к методу и техническим средствам неразрушающего контроля, обеспечивающего требуемый уровень надежности и безопасности изделия, после того, как определили требования к средствам и методам НК, осуществляют их подбор, подобранными средствами и методом НК осуществляют НК всей группы однотипных изделий и по результатам этого контроля ремонтируют изделия.
РИСУНКИ
MM4A – Досрочное прекращение действия патента СССР или патента Российской Федерации на изобретение из-за неуплаты в установленный срок пошлины за поддержание патента в силе
Дата прекращения действия патента: 12.11.2006
Извещение опубликовано: 20.06.2008 БИ: 17/2008
|