|
(21), (22) Заявка: 2003101322/06, 08.06.2001
(24) Дата начала отсчета срока действия патента:
08.06.2001
(30) Конвенционный приоритет:
09.06.2000 US 09/591,654
(43) Дата публикации заявки: 10.08.2004
(46) Опубликовано: 27.03.2007
(56) Список документов, цитированных в отчете о поиске:
US 5657643 А, 19.08.1997. US 4541852 А, 17.09.1985. RU 2137066 C1, 10.09.1999. GB 1323831 A, 18.07.1973. US 5036671 A, 06.08.1991.
(85) Дата перевода заявки PCT на национальную фазу:
09.01.2003
(86) Заявка PCT:
GB 01/02520 (08.06.2001)
(87) Публикация PCT:
WO 01/94865 (13.12.2001)
Адрес для переписки:
191036, Санкт-Петербург, а/я 24, “НЕВИНПАТ”, пат.пов. А.В.Поликарпову
|
(72) Автор(ы):
ХОФФАРТ Шон Д. (US), ПРАЙС Брайан К. (US)
(73) Патентообладатель(и):
Блэк энд Витч Притчард, Инк. (US)
|
(54) СПОСОБ ПОВЫШЕНИЯ ЭФФЕКТИВНОСТИ И РЕГУЛИРУЕМОСТИ ПРОЦЕССА С ЗАМКНУТЫМ КОНТУРОМ И СМЕШАННЫМ ХЛАДАГЕНТОМ ДЛЯ ОХЛАЖДЕНИЯ ГАЗООБРАЗНОГО МАТЕРИАЛА И СИСТЕМА ДЛЯ ЕГО ОСУЩЕСТВЛЕНИЯ
(57) Реферат:
Способ повышения эффективности и регулируемости процесса с замкнутым контуром и смешанным хладагентом для охлаждения газообразного материала в диапазоне температур от свыше 94°С до ниже приблизительно -129°С включает повышение температуры сжиженного газообразного материала, полученного в зоне охлаждения, до температуры от -129°С до -154°С, снижение давления сжиженного газообразного материала, полученного в зоне охлаждения с целью понижения температуры этого материала до значения ниже, чем -154°С, и получения испарившегося газа, отделение преобладающей части упомянутого испарившегося газа от упомянутого по существу сжиженного газообразного материала в сепараторном резервуаре, нагревание части испарившегося газа до температуры от 4°С до 54°С, сжатие части нагретого испарившегося газа до давления, превышающего давление газообразного материала, поступающего в зону охлаждения, и смешивание части сжатого нагретого испарившегося газа с газообразным материалом, подаваемым в зону охлаждения. Изобретение обеспечивает повышенную эффективность и регулируемость процесса. 2 н. и 7 з.п. ф-лы, 4 ил., 1 табл.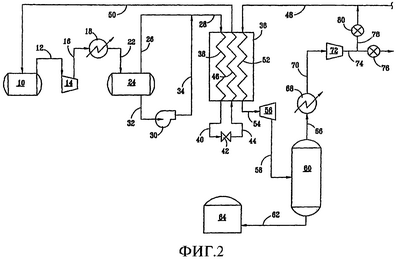
Область, к которой относится изобретение
Настоящее изобретение относится к процессу с замкнутым контуром и одним смешанным хладагентом, в котором производительность процесса может быть повышена путем соответствующего выбора температуры сжиженного газообразного материала, получаемого в этом процессе.
Краткое описание известных технических решений
Природный газ в последнее время находит широкое применение, благодаря чистоте продуктов его сгорания и удобству его использования. Многие источники природного газа расположены в отдаленных районах, трудно доступных для любых потребителей газа. При отсутствии трубопроводов для транспортирования природного газа в районы потребления добытый природный газ для транспортирования в такие районы часто перерабатывают в сжиженный природный газ (СПГ). Одной из отличительных особенностей предприятия по производству СПГ являются значительные капитальные затраты. Предприятие для сжижения природного газа включает несколько основных систем, предназначенных для переработки газа с целью очистки от примесей, его сжижения, охлаждения, а также силовые установки и оборудование для хранения и отгрузки сжиженного газа. Стоимость этих систем может варьироваться в широких пределах, однако, как правило, стоимость холодильной системы такого предприятия может составлять до 30% общей суммы затрат. Высокая стоимость систем для охлаждения СПГ обусловлена необходимостью сильного охлаждения природного газа для его сжижения. В типичном случае избыточное давление в потоке природного газа может составлять от приблизительно 250 фунт/дюйм2 до приблизительно 1500 фунт/дюйм2 (1,72-10,34 МПа), а его температура – от 40°F до приблизительно 120°F (4-49°С). Природный газ, основным компонентом которого является метан, не может быть переведен в жидкое состояние путем только повышения его давления, как это имеет место в случае более тяжелых углеводородов, применяемых в качестве энергоносителей. Критическая температура метана равна -82,5°С (-116,5°F); это означает, что метан можно превратить в жидкость только при температуре ниже указанной, независимо от давления. Поскольку природный газ обычно представляет собой смесь газов, он сжижается в пределах некоторого температурного диапазона. Критическая температура природного газа лежит обычно в пределах от приблизительно -121°F до приблизительно -80°F (от -85°С до -62°С). Природные газы распространенных составов сжижаются под атмосферным давлением в диапазоне температур от приблизительно -265°F до приблизительно -247°F (от -165°С до -155°С). Поскольку холодильное оборудование составляет столь значительную долю в общей стоимости установки для производства СПГ, предпринимаются значительные усилия для снижения затрат на охлаждение.
Для сжижения природного газа применяются различные холодильные циклы, из которых тремя наиболее обычными являются: каскадный цикл, где используются несколько однокомпонентных хладагентов и теплообменников, расположенных последовательно и обеспечивающих постепенное понижение температуры газа до температуры сжижения; расширительный цикл, где газ, находящийся под высоким давлением, расширяется с понижением давления и соответствующим понижением температуры; и многокомпонентные холодильные циклы, где для сжижения природного газа используются многокомпонентные хладагенты и теплообменники специальной конструкции.
Природный газ во многих случаях подвергают сжижению также с целью его хранения вблизи мест потребления, например в густонаселенных районах, где в зимний период может возникнуть потребность в природном газе, превышающая возможности подачи по существующим трубопроводным системам. В таких случаях сжиженный природный газ может храниться в резервуарах, подземных хранилищах и т.п., обеспечивающих возможность его подачи в периоды пикового спроса. Установки для сжижения газа для целей такого хранения могут иметь несколько меньшую производительность по сравнению с установками, используемыми для сжижения природного газа в отдаленных районах с целью его транспортирования в районы потребления и т.п.
Другие газы также подвергают сжижению, хотя несколько реже. Эти газы можно сжижать, применяя процессы, упомянутые выше.
Ранее для сжижения различных веществ, таких как природный газ, применяли процессы, описанные, например, в патенте США 4033735, выданном 5 июля 1977 г. на имя Леонарда К.Свенсона (Leonard К.Swenson), и в патенте США 5657643, выданном 19 августа 1997 г. на имя Брайана С.Прайса (Brian С.Price); эти патенты упомянутыми ссылками включены в полном их объеме в настоящее описание. В таких процессах применяют один смешанный хладагент. Эти процессы обладают многими преимуществами перед другими процессами, такими как каскадный, поскольку для них требуется менее дорогостоящее оборудование, и они легче поддаются контролю и регулированию, чем каскадные процессы. К сожалению, расход энергии в процессах со смешанным хладагентом несколько больше, чем в каскадных системах.
В каскадных системах, таких как в системе, описанной в патенте США 3855810, выданном 24 декабря 1974 г. на имя Саймона и др. (Simon et al.), используют, как правило, несколько зон охлаждения, где для обеспечения охлаждения испаряют хладагенты с последовательно понижающимися температурами кипения. В таких системах наиболее высококипящий хладагент, отдельно или в сочетании с другими хладагентами, как правило, сжимают, конденсируют и отделяют для охлаждения в первой зоне охлаждения. Затем давление сжатого охлажденного наиболее высококипящего хладагента резко снижают, получая поток холодного хладагента, используемый для охлаждения сжатого наиболее высококипящего хладагента в первой зоне охлаждения. В этой первой зоне охлаждения можно охлаждать также некоторые более низкокипящие хладагенты с последующей их конденсацией и направлять их на испарение для выполнения функции охладителя во второй или последующей зоне охлаждения и т.п. Таким образом, сжатию подвергают, главным образом, наиболее высококипящий хладагент, что обеспечивает некоторое повышение эффективности сжатия по сравнению со случаем, когда необходимо сжать весь поток одного смешанного хладагента. Однако, как указано выше, такие процессы требуют более дорогостоящего оборудования.
С учетом меньшей стоимости оборудования и меньшей трудности управления при использовании процессов со смешанным хладагентом постоянно ведутся работы в области усовершенствования такого процесса, направленные на снижение энергопотребления и достижение повышенной гибкости и универсальности процесса.
Краткое описание изобретения
В соответствии с настоящим изобретением предлагается способ повышения эффективности и регулируемости процесса с замкнутым контуром и смешанным хладагентом для охлаждения газообразного материала в диапазоне температур от свыше 200°F (94°С) до ниже приблизительно -200°F (-129°С) с получением по существу сжиженного газообразного материала в замкнутом холодильном контуре, содержащем одну трехканальную зону охлаждения.
Способ включает повышение температуры по существу сжиженного газообразного материала, полученного в зоне охлаждения процесса с замкнутым контуром и смешанным хладагентом, до значения от приблизительно -200°F до приблизительно -245°F (от -129°С до -154°С); снижение давления упомянутого по существу сжиженного газообразного материала, полученного в зоне охлаждения, с целью понижения температуры этого материала до значения ниже чем приблизительно -245°F (-154°С) и получения испарившегося газа; отделение по меньшей мере преобладающей части упомянутого испарившегося газа от упомянутого по существу сжиженного газообразного материала в сепараторном резервуаре; нагревание по меньшей мере части упомянутого испарившегося газа до температуры от 4°С (40°F) до 54°С (130°F); сжатие по меньшей мере части упомянутого нагретого испарившегося газа до давления, превышающего давление упомянутого газообразного материала, поступающего в зону охлаждения; и смешивание по меньшей мере части упомянутого сжатого нагретого испарившегося газа с упомянутым газообразным материалом, подаваемым в упомянутую зону охлаждения.
В одном из вариантов способа упомянутым газообразным материалом может быть природный газ.
В одном из вариантов способа давление упомянутого по существу сжиженного газообразного материала снижают до величины менее 345 кПа (50 фунт/дюйм2), предпочтительно – менее 69 кПа (10 фунт/дюйм2).
Кроме того, изобретение включает способ повышения эффективности и регулируемости процесса с замкнутым контуром и смешанным хладагентом для охлаждения газообразного материала в диапазоне температур от свыше 200°F (94°С) до ниже приблизительно -200°F (-129°С) путем теплообмена с одним смешанным хладагентом в замкнутом холодильном контуре, включающий сжатие газообразного смешанного хладагента для получения сжатого газообразного смешанного хладагента; охлаждение упомянутого сжатого смешанного хладагента; подачу упомянутого охлажденного сжатого смешанного хладагента в зону охлаждения и охлаждение упомянутого сжатого смешанного хладагента в упомянутой зоне охлаждения для получения по существу жидкого смешанного хладагента; пропускание упомянутого по существу жидкого смешанного хладагента через расширительный клапан для получения низкотемпературного хладагента; подачу упомянутого низкотемпературного хладагента в теплообменный контур в противотоке с упомянутым охлажденным сжатым смешанным хладагентом и упомянутым газообразным материалом для получения упомянутого по существу жидкого смешанного хладагента, по существу сжиженного газообразного материала и газообразного смешанного хладагента; способ включает доведение температуры упомянутого сжиженного газообразного материала до значения от приблизительно -200°F до приблизительно -245°F (от -129°С до -154°С); снижение давления упомянутого сжиженного газообразного материала с целью понижения температуры этого материала до значения ниже чем приблизительно -245°F (-154°С) и получения испарившегося газа; отделение по меньшей мере преобладающей части упомянутого испарившегося газа от упомянутого сжиженного газообразного материала; нагревание по меньшей мере части упомянутого испарившегося газа до температуры выше приблизительно 40°F (4°С); сжатие по меньшей мере части упомянутого нагретого испарившегося газа до давления, превышающего давление упомянутого газообразного материала, поступающего в зону охлаждения; и смешивание по меньшей мере части упомянутого сжатого нагретого испарившегося газа с газообразным материалом, подаваемым в упомянутую зону охлаждения.
Изобретение включает также процесс с замкнутым контуром и одним смешанным хладагентом для охлаждения газообразного материала в диапазоне температур от свыше 200°F (94°С) до ниже приблизительно -200°F (-129°С) путем теплообмена с одним смешанным хладагентом в замкнутом холодильном контуре, включающий сжатие газообразного смешанного хладагента для получения сжатого газообразного смешанного хладагента; охлаждение упомянутого сжатого смешанного хладагента для получения охлажденного газообразного смешанного хладагента; подачу упомянутого охлажденного сжатого смешанного хладагента в зону охлаждения и дальнейшее охлаждение упомянутого сжатого смешанного хладагента для получения по существу жидкого смешанного хладагента; пропускание упомянутого жидкого смешанного хладагента через расширительный клапан для получения низкотемпературного хладагента; подачу упомянутого низкотемпературного хладагента в теплообменный контур в противотоке с упомянутым охлажденным сжатым смешанным хладагентом и упомянутым газообразным материалом для получения упомянутого по существу жидкого смешанного хладагента, охлажденного по существу сжиженного газообразного материала с температурой от приблизительно -200°F до приблизительно -245°F (от -129°С до -154°С) и газообразного смешанного хладагента; возврат упомянутого газообразного смешанного хладагента на сжатие; снижение давления упомянутого по существу сжиженного газообразного материала с целью дальнейшего понижения его температуры до значения ниже приблизительно -245°F (-154°С) и получения испарившегося газа; отделение по меньшей мере преобладающей части упомянутого испарившегося газа от упомянутого сжиженного газообразного материала для получения отделенного испарившегося газа; нагревание по меньшей мере части упомянутого отделенного испарившегося газа до температуры выше приблизительно 40°F (4°С) для получения нагретого отделенного испарившегося газа; сжатие по меньшей мере части упомянутого нагретого отделенного испарившегося газа до давления, превышающего давление упомянутого газообразного материала, поступающего в зону охлаждения, для получения сжатой части газа; и смешивание по меньшей мере части упомянутой сжатой части упомянутого нагретого отделенного испарившегося газа с упомянутым газообразным материалом.
Далее, изобретение охватывает холодильную систему с замкнутым циклом и одним смешанным хладагентом для охлаждения газообразного материала в диапазоне температур от свыше 200°F (94°С) до ниже приблизительно -200°F (-129°С) для получения по существу сжиженного газообразного материала в замкнутом холодильном контуре, содержащем одну зону охлаждения, имеющую три теплообменных канала, включающую сборник для смешанного хладагента; компрессор, вход которого гидравлически соединен с выходом газообразного смешанного хладагента из упомянутого сборника смешанного хладагента; теплообменник, вход которого гидравлически соединен с выходом упомянутого компрессора; сепаратор хладагента, вход которого гидравлически соединен с выходом упомянутого теплообменника; зону охлаждения, содержащую первый канал зоны охлаждения, гидравлически соединенный с выходом газообразного хладагента из упомянутого сепаратора хладагента и с выходом жидкого хладагента из упомянутого сепаратора хладагента; второй канал зоны охлаждения, гидравлически соединенный с источником упомянутого газообразного материала; третий канал зоны охлаждения, расположенный в холодильном аппарате в противотоке с упомянутыми первым и вторым каналами зоны охлаждения; и расширительный клапан, гидравлически соединенный с выходом упомянутого первого канала зоны охлаждения и со входом упомянутого третьего канала зоны охлаждения; линию рецикла хладагента, гидравлически соединенную с выходом упомянутого третьего канала зоны охлаждения и со входом упомянутого сборника смешанного хладагента; линию сжиженного газообразного материала, температура которого составляет от приблизительно -129°С до приблизительно -154°С, гидравлически соединенную с выходом упомянутого второго канала зоны охлаждения; устройство для сброса давления, гидравлически соединенное с упомянутой линией сжиженного газообразного материала и имеющее выход для сжиженного газообразного материала пониженного давления; сепаратор, имеющий вход, гидравлически соединенный с упомянутым выходом для сжиженного газообразного материала пониженного давления, выход для испарившегося газа и выход для сжиженного газообразного материала; теплообменник, имеющий вход, гидравлически соединенный с упомянутым выходом для испарившегося газа, и выход для нагретого до температуры от 4°С до приблизительно 54°С испарившегося газа; и компрессор испарившегося газа, гидравлически соединенный с упомянутым выходом для нагретого испарившегося газа и имеющий выход для рециркулируемого испарившегося газа, гидравлически соединенный с упомянутым вторым каналом зоны охлаждения, и второй выход для испарившегося газа.
Краткое описание чертежей
На Фиг.1 представлен известный процесс с замкнутым контуром и смешанным хладагентом.
На Фиг.2 показан процесс с замкнутым контуром и смешанным хладагентом в соответствии с настоящим изобретением.
На Фиг.3 более подробно представлена секция отвода продуктов в известном процессе, показанном на Фиг.1.
На Фиг.4 более подробно представлена секция отвода продуктов, показанная на Фиг.3.
Описание предпочтительных вариантов осуществления
При описании чертежей соответствующие узлы обозначены одинаковыми позициями. На рисунках не показаны все клапаны, насосы и т.п., необходимые для регулирования потоков, поскольку они не являются необходимыми для описания настоящего изобретения.
На Фиг.1 показана известная холодильная система с замкнутым контуром и одним смешанным хладагентом. Смешанный хладагент засасывается из сборника 10 хладагента и поступает по линии 12 в компрессор 14. В компрессоре 14 смешанный хладагент сжимается, выходит из компрессора по линии 16 и поступает в теплообменник 18, работающий как конденсатор хладагента, в котором смешанный хладагент охлаждается за счет теплообмена с охладителем, таким как вода, воздух и т.п. Затем охлажденный сжатый смешанный хладагент поступает по линии 22 в сепаратор 24 хладагента, где происходит разделение на жидкую фракцию хладагента и газообразную фракцию хладагента. Газообразный хладагент поступает по линии 26 в теплообменник 36 для хладагента и газообразного материала. Жидкий хладагент выходит из сепаратора 24 по линии 32 и поступает в насос 30, с помощью которого его подают по линии 34 в узел соединения с линией 26, а затем по линии 28 для восстановления сжатого смешанного хладагента. Затем смешанный хладагент поступает в теплообменник 36. Сжатый смешанный хладагент проходит через теплообменник 36 по каналу 38 и поступает в выходную линию 40. В теплообменнике 36 смешанный хладагент охлаждается до желаемой температуры, при которой происходит его полное сжижение к моменту выхода из теплообменника в линию 40. В линии 40 хладагент находится под почти таким же давлением, как в линии 28 (за вычетом потери давления на прохождение через канал 38 и линию 40). Смешанный хладагент проходит через расширительный клапан 42, где происходит быстрое испарение жидкого смешанного хладагента в количестве, достаточном для снижения температуры смешанного хладагента до желаемого значения. Желательная температура на выходе теплообменника при сжижении природного газа составляет, как правило, от приблизительно -230°F до приблизительно -275°F (от -145°С до -170°С). В типичном случае эта температура составляет приблизительно -235°F (-148°С). В расширительном клапане 42 происходит понижение давления от приблизительно 50 фунт/дюйм2 до приблизительно 75 фунт/дюйм2 (345-517 кПа). Смешанный хладагент низкого давления при прохождении через канал 46 теплообменника 36 кипит, так что он поступает в линию 50 в газообразном состоянии. При выходе в линию 50 смешанный хладагент испарен практически полностью. Газообразный смешанный хладагент поступает по линии 50 в сборник 10 хладагента. В случае наличия следов жидкого хладагента в линии 50 им дают накапливаться в сборнике 10 хладагента, где они, в конце концов, испаряются и образуют часть смешанного хладагента, поступающего по линии 12 в компрессор 14.
Хотя вышеописанный процесс можно применять для сжижения других газов, чаще всего сжижению подвергают природный газ. Природный газ, как правило, предварительно сушат и обрабатывают с целью удаления примесей, таких как соединения серы, диоксид углерода и т.п. Природный газ поступает в теплообменник 36 по линии 48 и проходит через теплообменник 36 по теплообменному каналу 52. Поток природного газа можно отводить из теплообменника 36 в промежуточной точке и направлять в сепаратор тяжелых жидких компонентов (не показанный на чертеже), где углеводороды, содержащие 6 или более атомов углерода, предпочтительно отделяют и отводят из системы, а природный газ из сепаратора возвращают в последующую часть теплообменного канала 52 теплообменника 36. В некоторых случаях желательно удалять в сепараторе поток углеводородов С2-С5+ для использования в качестве готового продукта или для иных целей. Использование пригодного в данном случае сепаратора тяжелых жидких компонентов и его работа описаны в патенте США 4033735, включенном в настоящее описание вышеприведенной ссылкой. Отделение таких тяжелых компонентов хорошо известно сведущим специалистам. Отделение этих относительно тяжелых компонентов от потока природного газа необходимо в некоторых случаях, когда в природном газе содержатся такие тяжелые компоненты, которые, не будучи удалены, застывали бы в канале 52 в процессе охлаждения природного газа до сжижения. Такие соединения, способные затвердевать в канале 52, удаляют до их полного отсутствия или до присутствия в достаточно незначительном количестве, при котором осаждение твердых веществ в канале 52 не имеет места.
Сжиженный природный газ отводят из теплообменника 36 по линии 54, в типичном случае при температуре от приблизительно -230°F до приблизительно -275°F (от -145°С до -170°С). Затем сжиженный природный газ поступает по линии 54 в расширительный клапан, гидротурбину или иное устройство для сброса давления либо в комбинацию таких устройств, в данном случае изображенное в виде детандера 56, где давление сжиженного природного газа понижается, при этом температура сжиженного природного газа снижается до приблизительно -260°F (-162°С) при давлении приблизительно 1 атм (98 кПа). При этой температуре природный газ пригоден для хранения и сохраняет жидкое состояние при атмосферном давлении и температуре от приблизительно -250°F до приблизительно -260°F (от -156°С до -162°С). Как указано выше, такой процесс описан в патенте США 4033735, включенном в настоящее описание вышеприведенной ссылкой.
Поток материала, отводимый из детандера 56 по линии 58, направляют в сепаратор 60, из которого поток испарившегося газа отводят по линии 66, а сжиженный природный газ поступает по линии 62 в хранилище 64. Поток испарившегося газа, отводимый по линии 66, в типичном случае нагревают в теплообменнике 68 до температуры от приблизительно 40°F до приблизительно 130°F (от 4°С до 54°С), предпочтительно от приблизительно 70°F до приблизительно 120°F (от 21°С до 49°С), и подают в компрессор 72, где сжимают до давления, при котором его можно применять в качестве топливного газа или для иной цели.
В патенте США 5657643, также включенном в настоящее описание вышеприведенной ссылкой, описан усовершенствованный процесс, в котором используют несколько компрессоров и промежуточных холодильников.
В соответствии с настоящим изобретением, как показано на Фиг.2, поток испарившегося газа, поступающий в компрессор 72, сжимают до давления, достаточного для обеспечения возврата части испарившегося газа по линии 78 через вентиль 80 в линию 48, по которой исходный газообразный материал или природный газ поступает в теплообменник 36. Часть нагретого сжатого испарившегося газа отводят по линии 74 через вентиль 76 для применения в качестве топлива или для иной цели.
При использовании процесса с замкнутым контуром и смешанным хладагентом доступная степень сжатия после установки технологического оборудования, как правило, фиксирована. В результате холодильная способность теплообменника 36 оказывается фиксированной вследствие ограничения характеристик установленного компрессорного оборудования. В соответствии с настоящим изобретением при повышении температуры сжиженного газообразного материала или природного газа, отводимого по линии 54, на величину от приблизительно 30°F до приблизительно 75°F (от 16°С до 41°С), в сепараторе 60 отделяется дополнительное количество испарившегося газа. В известных способах необходимо ограничивать температуру потока в линии 54 таким значением, чтобы количество отделяющегося испарившегося газа было равно потребности в топливном газе предприятия по производству СПГ или других потребителей природного газа в районе предприятия. Как правило, такого типа установки для сжижения газа сооружаются в отдаленных районах, где потребление природного газа, кроме расхода на энергоснабжение самого предприятия по производству СПГ, незначительно. Вследствие этого температуру сжиженного природного газа в линии 54 необходимо было поддерживать на относительно низком уровне (от приблизительно -230°F до приблизительно -275°F, т.е. от -145°С до -170°С), чтобы количество испарившегося газа, образующегося при сбросе давления, практически равнялось потребности в природном газе для обеспечения работы предприятия. Для использования испарившегося газа необходимо было отделять его, подогревать до соответствующей температуры и сжимать до давления, пригодного для использования.
Давление природного газа, поступающего в такие сжижающие установки, может варьироваться в широких пределах в зависимости от давления газа в пластах, из которых его добывают, давления, при котором газ транспортируют по трубопроводам подачи, и т.п. В типичных случаях это давление составляет от приблизительно 250 фунт/дюйм2 до приблизительно 1500 фунт/дюйм2 (1,72-10,35 МПа), обычно от приблизительно 400 фунт/дюйм2 до приблизительно 1300 фунт/дюйм2 (2,76-8,97 МПа). При сбросе давления сжиженного природного газа от указанного до очень низкого избыточного давления, составляющего, например, от приблизительно 0 фунт/дюйм2 до приблизительно 50 фунт/дюйм2 (0-345 кПа), предпочтительно от приблизительно 2 фунт/дюйм2 до приблизительно 15 фунт/дюйм2 (14-103 кПа), выделяется значительное количество испарившегося газа. В результате температура сжиженного природного газа после сброса давления понижается приблизительно на 10-70°F (5-39°С). Количество испарившегося газа определяется температурой сжиженного газа при понижении давления. Желательно подбирать температуру сжиженного газа в линии 54 таким образом, чтобы в результате сброса давления испарившийся газ выделялся в количестве, достаточном только для обеспечения потребности предприятия в топливном газе, и чтобы обеспечить температуру сжиженного природного газа в линии 62, по которой его направляют в хранилище, на уровне ниже приблизительно -250°F (-156°C), предпочтительно от приблизительно -250°F до приблизительно -260°F (от -156°C до -162°С) при атмосферном давлении.
Это обстоятельство жестко ограничивает рабочие параметры установки. В случае, если вблизи предприятия нет значительной потребности в испарившемся газе, сжиженный природный газ в линии 54 должен быть охлажден до относительно низкой температуры.
В соответствии с настоящим изобретением температуру потока сжиженного природного газа в линии 54 повышают на величину от приблизительно 30°F до приблизительно 75°F (от 16°С до 41°С), т.е. вместо диапазона температур от приблизительно -230°F до приблизительно -275°F (от -145°С до -170°С) она лежит в диапазоне температур от приблизительно -200°F до приблизительно -245°F (от -129°С до -154°С), так что в детандере 56 СПГ испаряется значительно большее количество природного газа. Предпочтительный температурный диапазон в линии 54 имеет пределы от приблизительно -215°F до приблизительно -235°F (от -137°С до -148°С). Этот поток затем направляют по линии 58 в сепаратор 60, откуда увеличенное количество природного газа (испарившегося газа) отводят по линии 66 и направляют в теплообменник 68. Температуру желательно повышать до соответствующего значения, т.е. в типичном случае до значения от приблизительно 40°F до приблизительно 130°F (от 4°С до 54°С), предпочтительно от приблизительно 70°F до приблизительно 120°F (от 21°С до 49°С), после чего газ подают в компрессор 72. В компрессоре 72, который является компрессором с независимым энергоснабжением и может иметь привод от электродвигателя, газовой турбины и т.п., поток испарившегося газа сжимают до давления, достаточного для использования его в качестве топливного газа и для возврата части испарившегося газа в исходный поток природного газа, поступающего в теплообменник 36 по линии 48.
Этот процесс позволяет обеспечить дополнительную производительность путем повышения производительности компрессора 72, который применяется для сжатия возвратного потока. Соответственно, можно работать при повышенной температуре сжиженного природного газа в линии 54, что повышает эффективность теплообменника 36, поскольку движущая сила теплообмена в теплообменнике 36 имеет наименьшую величину при самых низких температурах потока природного газа в теплообменнике 36 и поскольку теплообменная способность теплообменника 36 ограничена имеющейся производительностью компрессора 14. Поскольку тепловая нагрузка на теплообменник 36 снижается при повышении температуры в линии 54, возможно увеличение количества перерабатываемого природного газа при использовании того же оборудования. В результате упомянутого повышения температуры увеличивается количество получаемого испарившегося газа, однако этот газ можно легко возвратить в цикл путем его повторного сжатия и рециркуляции, как описано выше. Это позволяет повысить производительность установленного оборудования путем использования компрессора 72, который можно использовать для сжатия переменных количеств испарившегося газа в зависимости от потребности в топливном газе и т.п. Кроме того, обнаружено, что при использовании способа в соответствии с настоящим изобретением повышается также эффективность процесса.
ПРИМЕР
Сопоставляются процессы, показанные на Фиг.3 и Фиг.4. Процесс, представленный на Фиг.3, является известным процессом, полная схема которого показана на Фиг.1. На Фиг.3 несколько более подробно показана часть схемы, соответствующая секции отвода природного газа. Показан насос 82, включенный в линию 62, и секция обработки природного газа показана схематически в виде позиции 84, а секция обработки хладагента схематически представлена позицией 86.
На Фиг.4 для сравнения представлена более подробно схема процесса в соответствии с настоящим изобретением.
Некоторые характеристики процессов, показанных на Фиг.3 и Фиг.4, сопоставлены в Таблице 1.
Фиг.3 |
Фиг.4 |
Линия |
Температура, °F(°C) |
Давление, фунт/дюйм2 (кПа) |
Линия |
Температура, °F(°C) |
Давление, фунт/дюйм2 (кПа) |
48 |
100 (37,8) |
755 (5209) |
48 |
100 (37,8) |
755 (5209) |
54 |
-239,2 (-150,7) |
745 (5140) |
54 |
-224,7 (-142,6) |
745 (5140) |
58 |
-252,4 (-158,0) |
3 (20,7) |
58 |
-252,4 (-158,0) |
3 (20,7) |
62 |
-252,4 (-158,0) |
3 (20,7) |
62 |
-252,4 (-158,0) |
3 (20,7) |
66 |
-252,4 (-158,0) |
3 (20,7) |
66 |
-252,4 (-158,0) |
3 (20,7) |
70 |
90 (32,2) |
1 (6.9) |
70 |
90 (32,2) |
1 (6,9) |
74 |
105 (40,5) |
785 (5416) |
74 |
105 (40,5) |
785 (5416) |
|
|
|
78 |
105 (40,5) |
785 (5416) |
Из таблицы следует, что в варианте, представленном на Фиг.4, температура в линии 54 повышена. Природный газ поступает в линию 62 при тех же значениях температуры и давления. Аналогично, температура и давление топливного газа в линии 74 также остаются неизменными. В представленном варианте производится то же количество сжиженного природного газа, однако общее энергопотребление при работе по процессу, показанному на Фиг.4, снижается приблизительно на 2,4% по сравнению с процессом, показанным на Фиг.3.
Как указано выше, способ в соответствии с настоящим изобретением является способом повышения эффективности и регулируемости процессов с замкнутым контуром и смешанным хладагентом. Вышеприведенный пример ясно показывает повышенную эффективность процесса, неотъемлемой особенностью которого является то, что при повышенной температуре в линии 54 можно при желании получать в теплообменнике 36 увеличенные количества сжиженного природного газа.
В заключение описания изобретения, выполненного применительно к некоторым предпочтительным вариантам его осуществления, следует отметить, что описанные варианты имеют иллюстративный, а не ограничительный характер, и что возможны многочисленные варианты и модификации настоящего изобретения, не выходящие за его пределы. Многие такие варианты и модификации можно считать очевидными и желательными для сведущих специалистов, ознакомленных с вышеприведенным описанием предпочтительных вариантов осуществления изобретения.
Формула изобретения
1. Способ повышения эффективности и регулируемости процесса с замкнутым контуром и смешанным хладагентом для охлаждения газообразного материала в диапазоне температур от свыше 94°С (200°F) до ниже приблизительно -129°С (-200°F) с получением по существу сжиженного газообразного материала в замкнутом холодильном контуре, содержащем одну трехканальную зону охлаждения, причем упомянутый процесс включает сжатие газообразного смешанного хладагента для получения сжатого газообразного смешанного хладагента; охлаждение упомянутого сжатого смешанного хладагента; подачу упомянутого охлажденного сжатого смешанного хладагента в зону охлаждения и охлаждение упомянутого сжатого смешанного хладагента в упомянутой зоне охлаждения для получения по существу жидкого смешанного хладагента; пропускание упомянутого по существу жидкого смешанного хладагента через расширительный клапан для получения низкотемпературного хладагента; подачу упомянутого низкотемпературного хладагента в теплообменный контур в противотоке с упомянутым охлажденным сжатым смешанным хладагентом и упомянутым газообразным материалом в зоне охлаждения для получения упомянутого по существу жидкого смешанного хладагента, по существу сжиженного газообразного материала и газообразного смешанного хладагента; упомянутый способ включает:
a) повышение температуры по существу сжиженного газообразного материала, полученного в зоне охлаждения, до температуры от -129°С (-200°F) до -154°С (-245°F);
b) снижение давления упомянутого по существу сжиженного газообразного материала, полученного в зоне охлаждения, с целью понижения температуры этого материала до значения ниже -154°С (-245°F) и получения испарившегося газа;
c) отделение, по меньшей мере, преобладающей части упомянутого испарившегося газа от упомянутого по существу сжиженного газообразного материала в сепараторном резервуаре;
d) нагревание, по меньшей мере, части упомянутого испарившегося газа до температуры от 4°С (40°F) до 54°С (130°F);
e) сжатие, по меньшей мере, части упомянутого нагретого испарившегося газа до давления, превышающего давление упомянутого газообразного материала, поступающего в упомянутую зону охлаждения; и
f) смешивание, по меньшей мере, части упомянутого сжатого нагретого испарившегося газа с упомянутым газообразным материалом, подаваемым в упомянутую зону охлаждения.
2. Способ по п.1, где упомянутым газообразным материалом является природный газ.
3. Способ по п.2, где давление упомянутого по существу сжиженного газообразного материала снижают до величины менее 345 кПа (50 фунт/дюйм2).
4. Способ по п.3, где давление упомянутого по существу сжиженного газообразного материала снижают до величины менее 69 кПа (10 фунт/дюйм2).
5. Способ по п.1, где температуру упомянутого по существу сжиженного газообразного материала снижают, по меньшей мере, до -156°С (-250°F).
6. Способ по п.1, где температуру упомянутого по существу сжиженного газообразного материала снижают, по меньшей мере, до -162°С (-260°F).
7. Система с замкнутым циклом и одним смешанным хладагентом для охлаждения газообразного материала в диапазоне температур от свыше 94°С (200°F) до ниже -129°С (-200°F) для получения по существу сжиженного газообразного материала в замкнутом холодильном контуре, содержащем одну зону охлаждения, имеющую три теплообменных канала, содержащая:
a) сборник для смешанного хладагента;
b) компрессор, вход которого гидравлически соединен с выходом газообразного смешанного хладагента из упомянутого сборника смешанного хладагента;
c) теплообменник, вход которого гидравлически соединен с выходом упомянутого компрессора;
d) сепаратор хладагента, вход которого гидравлически соединен с выходом упомянутого теплообменника;
e) зону охлаждения, содержащую первый канал зоны охлаждения, гидравлически соединенный с выходом газообразного хладагента из упомянутого сепаратора хладагента и с выходом жидкого хладагента из упомянутого сепаратора хладагента; второй канал зоны охлаждения, гидравлически соединенный с источником упомянутого газообразного материала; третий канал зоны охлаждения, расположенный в холодильном аппарате в противотоке с упомянутыми первым и вторым каналами зоны охлаждения; и расширительный клапан, гидравлически соединенный с выходом упомянутого первого канала зоны охлаждения и со входом упомянутого третьего канала зоны охлаждения;
f) линию рецикла хладагента, гидравлически соединенную с выходом упомянутого третьего канала зоны охлаждения и со входом упомянутого сборника смешанного хладагента;
g) линию сжиженного газообразного материала, температура которого составляет от приблизительно -129°С до приблизительно -154°С, гидравлически соединенную с выходом упомянутого второго канала зоны охлаждения;
h) устройство для сброса давления, гидравлически соединенное с упомянутой линией сжиженного газообразного материала и имеющее выход для сжиженного газообразного материала пониженного давления;
i) сепаратор, имеющий вход, гидравлически соединенный с упомянутым выходом для сжиженного газообразного материала пониженного давления, выход для испарившегося газа и выход для сжиженного газообразного материала;
j) теплообменник, имеющий вход, гидравлически соединенный с упомянутым выходом для испарившегося газа, и выход для нагретого до температуры от 4°С до приблизительно 54°С испарившегося газа; и
k) компрессор испарившегося газа, гидравлически соединенный с упомянутым выходом для нагретого испарившегося газа и имеющий выход для рециркулируемого испарившегося газа, гидравлически соединенный с упомянутым вторым каналом зоны охлаждения, и второй выход для испарившегося газа.
8. Система по п.7, где упомянутый компрессор содержит несколько компрессоров.
9. Система по п.7, где упомянутым газообразным материалом является природный газ.
РИСУНКИ
|
|