(21), (22) Заявка: 2004112300/02, 23.04.2004
(24) Дата начала отсчета срока действия патента:
23.04.2004
(43) Дата публикации заявки: 27.10.2005
(46) Опубликовано: 27.03.2007
(56) Список документов, цитированных в отчете о поиске:
SU 614867 А, 07.06.1978. RU 2093288 C1, 20.10.1997. RU 2025161 C1, 30.12.1994. US 2992473 A, 18.07.1961.
Адрес для переписки:
180002, г.Псков, ул. Юбилейная, 14, кв. 69, А.М.Парамонову
|
(72) Автор(ы):
Парамонов Андрей Михайлович (RU)
(73) Патентообладатель(и):
Парамонов Андрей Михайлович (RU)
|
(54) СПОСОБ ИЗГОТОВЛЕНИЯ ТРУБ
(57) Реферат:
Изобретение относится к способу изготовления труб с различной или одинаковой толщиной стенок. Задача изобретения – расширение функциональных возможностей, упрощение технологии и оборудования. Способ включает протягивание трубной заготовки через волоку или протягивание и прокатку. Сначала производят сплющивание начальной трубы и уменьшение толщины стенок с коэффициентом уменьшения в пределах от 1 до 20 протягиванием через волоки или протягиванием через волоки и прокаткой между вальцами начальной трубы с обеспечением соприкосновения внутренних стенок обрабатываемой трубы, после чего обработанную трубу профилируют, придавая ей заданный профиль в каждом поперечном сечении. Возможно осуществление сплющивания трубы только на некоторых участках. Возможно проведение термообработки. Изобретение обеспечивает возможность получения труб с различной толщиной стенок, изменяющейся как в поперечном сечении трубы, так и по ее длине, с различным профилем поперечного сечения трубы, а также труб с очень тонкими стенками. 6 з.п. ф-лы, 9 ил.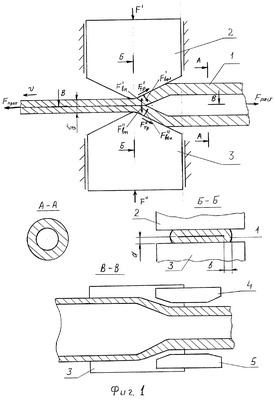
Изобретение, способ изготовления труб, относится к обработке металлов давлением, а точнее к производству труб, в том числе и тонкостенных, с разной или одинаковой толщиной стенок различного профиля поперечного сечения, и может быть использовано в приборостроении при изготовлении чувствительных элементов.
Известен способ деформации полой заготовки на оправке рядом последовательно расположенных вращающихся головок с телами качения, с постоянным отношением удельной энергии по очагам деформации, по определенной зависимости (RU № 2025161, 1992.07.07).
Недостатки этого способа заключаются в том, что:
1) можно получить только трубы большого диаметра и маленькой длины, так как необходимо вставлять внутрь трубы оправку ограниченной длины;
2) можно получить только трубы с одинаковой толщиной стенки и только круглого профиля за счет того, что форма образуется телами качения при их вращении вокруг оси трубы;
3) низкая производительность за счет ограничения скорости вращения головок с телами качения и их подачи вдоль оси трубы.
4) использование сложного и дорогостоящего инструмента.
Также известен способ производства тонкостенных трубчатых изделий обкатыванием (RU №2018397, 1991.02.25). Для этого трубчатую заготовку деформируют обкатывающим инструментом на коническом пуансоне. Со стороны наименьшего диаметра рабочего участка пуансон имеет калибрующий участок, выполненный из двух противоположно направленных конических участков и с расположенным между ними цилиндрическим участком, диаметр которого равен наибольшему диаметру конического рабочего участка. Заготовка деформируется обкатыванием на пуансоне матрицей, наклоненной под небольшим углом к оси пуансона и получающей движение кругового обкатывания от специального механизма. После этого пуансон с заготовкой выводят из матрицы и осуществляют съем отштампованного изделия с пуансона, перемещая вниз толкатель относительно пуансона. При этом одновременно производится раздача изделия. Раздача осуществляется коническим участком калибрующего элемента, обращенным к наименьшему диаметру конического рабочего участка пуансона, а калибровка отверстия – цилиндрическим участком калибрующего элемента, диаметр которого равен наибольшему диаметру конического рабочего участка пуансона. В результате внутренняя поверхность изделия приобретает цилиндрическую форму, наружная – коническую.
Недостатки этого способа заключаются в том, что:
1) можно получить только трубы большого диаметра и маленькой длины, так как внутри трубы необходимо располагать пуансон ограниченной длины;
2) можно получить только трубы с одинаковой толщиной стенки и только круглого профиля за счет того, что заготовка деформируется обкатыванием на пуансоне матрицей вокруг оси трубы;
3) низкая производительность за счет возвратно-поступательного движения инструмента и наличия холостых ходов.
4) использование сложного и дорогостоящего инструмента.
Наиболее близок к предлагаемому способу изготовления труб способ, используемый в настоящее время во всем Мире (В.Я.Шапиро, В.И.Уральский. Бухтовое волочение труб. М.: Металлургия, 1972 г.)
Начальную трубу получают прошивкой прутка или продольной сваркой из полюсы. Затем ее подвергают термической обработке в специальной установке, в которой ее нагревают с подачей инертного газа снаружи и внутри трубы и охлаждают. После производится чередование волочения (протягивания) трубы и термической обработки до получения определенных параметров трубы, диаметра и толщины стенки.
Волочение трубы производят по следующей схеме:
1) внутрь трубы вводиться смазка и вставляется самоустанавливающаяся оправка;
2) конец трубы осаживается вручную до определенного диаметра, чтобы он проходил в отверстие волоки;
3) осаженный конец пропускается сквозь волоку и закрепляется на тянущем барабане;
4) производится волочение трубы осадкой с самоустанавливающейся оправкой внутри трубы. На стенку трубы действуют усилия: снаружи – со стороны рабочих поверхностей волоки, изнутри – со стороны рабочих поверхностей самоустанавливающейся оправки. При этом происходит уменьшение наружного диаметра трубы (вытяжка по диаметру q) и толщины стенки (вытяжка по стенке t), где t× q= – вытяжка за переход, как правило, она находится в пределах 1,3…1,5. 3а одно протягивание (переход) происходит вытяжка по стенке t=1,05…1,2 и вытяжка по диаметру q=1,1…1,25. За несколько переходов вытяжкой с самоустанавливающейся оправкой получают трубу из стали 12Х18Н10Т с наружным диаметром 2,6 мм и толщиной стенки 0,135 мм. Меньший диаметр и меньшую толщину стенки получить не удается, так как процесс становится нестабильным и происходит разрыв трубы.
5) Дальше производится ряд переходов волочения осадкой (без самоустанавливающейся оправки), при этом происходит незначительное утонение стенки и уменьшение диаметра. Минимальные размеры трубы, которые удается получить: наружный диаметр 0,36 мм и толщина стенки 0,09 мм. Причем с уменьшением наружного диаметра трубы происходит относительное увеличение толщины стенки.
Недостатки этого способа заключаются в том, что:
1) можно получить только трубы, ограниченные минимальным наружным диаметром (0,36 мм) и минимальной толщиной стенки (0,09 мм), меньше которых процесс протягивания становится нестабильным и происходит обрыв трубы;
2) можно получить только трубы с одинаковой толщиной стенки и только круглого профиля за счет того, что заготовка деформируется инструментами, имеющими форму тел вращения;
3) используется сложный и дорогостоящий инструмент на каждый промежуточный диаметр трубы и толщину стенки. Для этого используется определенная волока и определенная самоустанавливающаяся оправка,
4) сложная термическая обработка, так как внутрь трубы необходимо подавать инертный газ.
Технической задачей, на решение которой направлено изобретение, является:
1) значительное упрощение способа изготовления труб, в том числе и манометрических, а также упрощение оснастки и оборудования, используемого для их производства;
2) возможность получать трубы с различной толщиной стенок, изменяющихся как в данном поперечном сечении трубы, так и по ее длине;
3) возможность получать трубы с различным профилем поперечного сечения трубы;
4) изготавливать трубы с очень тонкими стенками, которые существующими способами получить невозможно;
5) возможность получать трубы с чередующимися участками недеформированной трубы и участков трубы заданной длины, на которых производится обработка, то есть изменение толщины стенки и профиля;
6) упрощение термической обработки;
7) уменьшение себестоимости трубных изделий при высоком качестве.
Технический результат, получаемый при осуществлении данного изобретения, заключается в возможности получать трубы с вытяжкой по стенке в пределах от 1 до 20 и с различными или одинаковой толщинами стенок, которые изменяются как в данном поперечном сечении трубы, так и по ее длине; с различным профилем поперечного сечения трубы; с чередующимися мерными участками недеформированной трубы и участков, на которых производится обработка, то есть изменение толщины стенки и профиля поперечного сечения при высоком качестве и низкой себестоимости. Так, получены трубы из стали 12Х18Н10Т с толщиной стенки 0,015 мм при диаметре трубы 0,5…1,2 мм. И возможно получать трубы с толщиной стенки 0,005 мм.
Осуществление способа изготовления труб иллюстрируется фиг.1-9.
На фиг.1 изображены продольные и поперечные сечения трубы в процессе волочения (протягивания) с одновременным сплющиванием трубы.
На фиг.2 изображены продольные и поперечные сечения трубы при повторяющемся процессе волочения.
На фиг.3 изображено продольное сечение трубы в процессе прокатывания с одновременным сплющиванием трубы.
На фиг.4 изображены продольные и поперечные сечения трубы при повторяющемся процессе прокатывания.
На фиг.5 изображены продольные и поперечные сечения трубы с разной толщиной стенки при протягивании через фасонные волоки или прокатывании в фасонных вальцах.
На фиг.6 изображены продольные и поперечные сечения трубы с чередующимися участками протянутой и не протянутой трубы.
На фиг.7 изображены продольные и поперечные сечения трубы с изменяющейся толщиной стенки вдоль оси трубы.
На фиг.8 изображено профилирование обработанной трубы протягиванием через фасонные волоки, то есть придание ей заданного профиля поперечного сечения.
На фиг.9 изображены переходы при профилировании обработанной трубы прокатыванием через ряд фасонных вальцов, то есть придание ей заданного профиля поперечного сечения.
Это достигается тем, что сначала получают трубу одним из известных способов, затем начальная труба 1 предварительно сплющивается (см. фиг.1 и 2), то есть принимает плоскопараллельный профиль поперечного сечения, или сплющивается и деформируется в процессе протягивания через волоки 2 и 3, или в процессе обкатки между вальцами 2 и 3 (см. фиг.3). При этом внутренние стенки трубы соприкасаются. В процессе протягивания на трубу вдоль ее оси действуют протягивающая Fпрот и растягивающая Fраст силы (фиг.1 и 2). Под действием протягивающего усилия труба перемещается в продольном направлении через волоки, где под воздействием сил F’вол и F”вол, которые возникают между рабочими поверхностями волок и участками наружных поверхностей трубы, и сил F’ВН и F”ВН, возникающих между соприкасающимися внутренними противолежащими поверхностями трубы, происходит уменьшение (редуцирование) толщины стенки с вытяжкой по стенке в пределах от 1 до 20.
При этом уменьшение толщины стенок достигается многократным протягиванием (несколько переходов) или многократными протягиванием и прокаткой.
Причем соотношение толщин стенок а и в протянутой трубы на участках, где происходит соприкосновение наружных поверхностей трубы с волоками, и участках, где это соприкосновение не происходит, может колебаться в пределах от 0,5 до 1,2 и зависит от величины растягивающего усилия, углов между формообразующими поверхностями волок и направлением протягивания и величины радиусов поверхностей тел вращения, соединяющих между собой рабочие поверхности волок, и величины сил трения F’тр и F”тр, возникающих между наружными стенками обрабатываемой трубы и рабочими поверхностями волок. Для уменьшения сил трения и повышения качества поверхности трубы используют смазочные вещества. В процессе протягивания и прокатки площадь внутреннего поперечного сечения трубы равна или близка к нулю. При соприкосновении и взаимодействии внутренних стенок трубы не происходит их слипания. Это дает возможность при дальнейшем профилировании трубы придавать ей заданный профиль поперечного сечения с необходимой площадью внутреннего поперечного сечения.
Использование прокатки трубы (фиг.3 и 4), наряду с протяжкой, позволяет изменять толщину стенок трубы и соотношение а и в толщины стенок трубы на участках соприкосновения наружных поверхностей трубы с валками и участков трубы, где это соприкосновение не происходит.
При предлагаемом способе изготовления труб происходит вытяжка обрабатываемой трубы за переход = t× q, где t – вытяжка по стенке (уменьшение толщины стенок трубы), и q – вытяжка по периметру или по диаметру. При данном способе обработки вытяжка обрабатываемой трубы происходит в основном за счет вытяжки по стенке, при этом периметр трубы в поперечном сечении изменяется незначительно.
Использование регулируемых волоков и вальцов с фасонными рабочими поверхностями позволяет получать трубы с заданными толщинами стенок как в пределах заданного поперечного сечении трубы, так и в зависимости от расположения вдоль оси трубы (см. фиг.6 и 7), а также различной формы в поперечном сечении (см. фиг.5).
Это позволяет после последующего профилирования получать трубы с заданными прочностными характеристиками, например манометрическую трубку с рациональным расположением напряжений в поперечном и продольном сечениях трубы при создании давления во внутренней полости и одновременном нагружении трубы внешними силами.
Также при последующем профилировании протянутой трубы можно получать заданный профиль внутреннего поперечного сечения с заданным условным проходом и гидравлическим сопротивлением, что позволяет создавать манометрические пружины с необходимыми коэффициентами торможения и инертности.
Способ изготовления труб реализуется при протягивании через волоки 2 и 3 (см. фиг.1 и 2), которые представляют собой пару волок, из которых одна или обе перемещаются в направляющих во встречных направлениях. Один из волок может быть регулируемым и подвижным или один волок выполнен регулируемым и подвижным, а другой – неподвижным.
Раздвижные волоки позволяют уменьшать или увеличивать величину щели б, через которую производится протягивание трубы, или могут быть раздвинуты так, чтобы заготовка проходила между ними свободно, без деформации. Это позволяет как пропускать технологический конец без его дополнительной обработки, который закрепляется в приспособлении, создающем протягивающее усилие, так и чередовать участки трубы заданной длины, обработанные и необработанные, то есть начальной трубы. Также перемещение волоки в процессе протягивания, изменения растягивающего усилия позволяет получать трубы с изменяющейся толщиной стенок в зависимости от продольного расположения поперечного сечения трубы (фиг.5). От поперечного смещения трубы в волоках в процессе протягивания возможно использование боковых направляющих 4 и 5 (фиг.1). Возможны две схемы обработки трубы. Одностороннее протягивание, когда труба протягивается или прокатывается всегда в одном направлении (рабочий ход), а в обратном направлении перемещается без обработки (холостой ход), и реверсивное, когда труба протягивается или прокатывается с изменением формы в прямом и обратном направлениях, в данном случае холостой ход отсутствует. Чтобы получить заданную толщину стенки производят ее волочение за несколько переходов. При каждом следующем протягивании волоки сдвигают на определенную величину (фиг.2). При обработке пластичных материалов при многократном протягивании и прокатывании с большими усилиями сжатия стенок для предотвращения слипания внутренних поверхностей трубы между собой в трубу предварительно вводят смазочное вещество. Прокатывание трубы 1 (фиг.3), наряду с протяжкой, осуществляется между регулируемыми вальцами 2 и 3 с осями вращения 4 и 5, расположенными в корпусах 6 и 7, которые могут перемещаться в направляющих во встречных направлениях, или один из корпусов может быть жестко закреплен. Процесс прокатывания аналогичен процессу протягивания с тем отличием, что характер и величины сил, действующих на трубу в процессе прокатки, обуславливают увеличение соотношений толщины стенок трубы на участках, где не происходит соприкосновения валков с наружными поверхностями трубы, и толщин стенок, где это соприкосновение происходит. Причем каждый валец может быть регулируемым и подвижным или один валец выполнен регулируемым и подвижным, а другой – неподвижным. Одним прокатыванием не удается существенно уменьшить толщину стенки трубы. Поэтому протягивание является основным элементом в процессе обработки труб, а прокатывание – вспомогательным.
Сочетание процессов протягивания, прокатывания и термообработки труб дает возможность получать трубы с заданными параметрами и характеристиками. Также можно получать трубы с различным профилем и различной толщиной стенок в пределах заданного поперечного сечения (фиг.5), протягивая или прокатывая ее через фасонные валки или вальцы. Для того чтобы получить трубу с заданными физико-химическими, механическими свойствами и с нужными толщинами стенок производят в определенной последовательности протягивание, прокатывание и термическую обработку. После этого трубу профилируют, то есть придают ей определенный профиль поперечного сечения, одинаковый по всей длине или меняющийся вдоль оси трубы. Это можно осуществить различными способами, например:
а) протягиванием через фасонные волоки (фиг.8), при этом происходит сжатие трубы вдоль ребер;
b) прокатыванием через фасонные вальцы (фиг, 9), при этом происходит сжатие трубы вдоль ребер;
с) созданием давления внутри трубы, при этом трубу можно помещать в оправку, ограничивающую размеры ее раздутия;
d) термообработкой, при определенных режимах нагрева и охлаждения происходит раздутие трубы за счет внутренних напряжений внутри металла,
и другими способами.
Из изложенных выше описаний предлагаемого способа изготовления труб, его аналога и прототипа следует, что изобретение дает возможность:
1) значительно упростить способ изготовления труб, в том числе и манометрических, а также оснастку и оборудование используемого для их производства;
2) пропускать технологический конец полой заготовки или заготовки без дополнительной обработки сквозь волоки;
3) получать трубы с различной толщиной стенок, изменяющейся как в данном поперечном сечении трубы, так и по ее длине; с различным профилем поперечного сечения трубы;
4) изготавливать трубы с очень тонкими стенками, которые существующими способами получить невозможно; уменьшение толщины стенок с коэффициентом уменьшения толщины стенки в пределах от 1 до 20.
5) получать трубы с чередующимися участками трубчатой заготовки с недеформированными стенками и участками трубы заданной длинны, на которых производится протягивание через волоки или протягивание и прокатывание между вальцами и формованной трубой; затем обработанную трубу профилируют, придавая заданный профиль в каждом поперечном сечении трубы;
6) упростить термическую обработку за счет того, что отсутствует внутренний объем трубы и нет необходимости заполнять его инертным газом;
7) получить трубы различного профиля;
8) уменьшить себестоимости трубных изделий при высоком качестве;
9) чередовать участки обработанной и необработанной полой заготовки;
10) производить протягивания заготовки с различными характеристиками по ширине и по толщине, используя один комплект волок (пару);
11) реверсировать процесс протягивания, что позволяет увеличить производительность.
Формула изобретения
1. Способ изготовления труб с различной или одинаковой толщиной стенок в поперечном сечении, включающий протягивание через волоки или протягивание через волоки и прокатку, отличающийся тем, что сначала производят сплющивание начальной трубы и уменьшение толщины ее стенок с коэффициентом уменьшения в пределах от 1 до 20 протягиванием через волоки или протягиванием через волоки и прокаткой между вальцами начальной трубы с обеспечением соприкосновения внутренних стенок трубы, после чего обработанную трубу профилируют, придавая ей заданный профиль в каждом поперечном сечении.
2. Способ по п.1, отличающийся тем, что используют регулируемые и подвижные волоки или одну волоку – регулируемую и подвижную, а другую – неподвижную.
3. Способ по п.1, отличающийся тем, что используют регулируемые и подвижные вальцы или один валец – регулируемый и подвижный, а другой – неподвижный.
4. Способ по п.1, отличающийся тем, что уменьшение толщины стенок производят многократным протягиванием через волоки или многократными протягиванием через волоки и прокаткой.
5. Способ по п.1, отличающийся тем, что он дополнительно включает термообработку.
6. Способ по п.1, отличающийся тем, что сплющивание трубы и изменение толщины ее стенок производят на участке трубы заданной длины, после чего следующий участок пропускают без обработки.
7. Способ по п.1, отличающийся тем, что перед сплющиванием во внутреннюю полость начальной трубы вводят смазочное вещество.
РИСУНКИ
TK4A – Поправки к публикациям сведений об изобретениях в бюллетенях “Изобретения (заявки и патенты)” и “Изобретения. Полезные модели”
Напечатано: Адрес для переписки: 180002, г.Псков, ул. Юбилейная,14, кв.69
Следует читать: Адрес для переписки: 180002, г.Псков, 2-й переулок Шабаново, д.3, кв.2
Номер и год публикации бюллетеня: 9-2007
Код раздела: FG4A
Извещение опубликовано: 27.04.2007 БИ: 12/2007
MM4A – Досрочное прекращение действия патента СССР или патента Российской Федерации на изобретение из-за неуплаты в установленный срок пошлины за поддержание патента в силе
Дата прекращения действия патента: 24.04.2007
Извещение опубликовано: 27.07.2008 БИ: 21/2008
NF4A – Восстановление действия патента СССР или патента Российской Федерации на изобретение
Дата, с которой действие патента восстановлено: 20.09.2008
Извещение опубликовано: 20.09.2008 БИ: 26/2008
|