(21), (22) Заявка: 2005127451/03, 01.09.2005
(24) Дата начала отсчета срока действия патента:
01.09.2005
(46) Опубликовано: 27.03.2007
(56) Список документов, цитированных в отчете о поиске:
SU 715096 А, 25.02.1980. SU 319343 А, 07.01.1972. SU 1200974 A, 30.12.1985. US 5002233 А, 26.03.1991. US 5272861 A, 28.12.1993. GB 2016951 A, 26.09.1979. GB 2210290 A, 07.06.1989. FR 2823452 A1, 18.10.2002.
Адрес для переписки:
105173, Московская обл., г. Балашиха, мкр. 1 Мая, 10, кв.55, В.И.Стяжкину
|
(72) Автор(ы):
Стяжкин Владимир Иванович (RU)
(73) Патентообладатель(и):
Стяжкин Владимир Иванович (RU), Общество с ограниченной ответственностью Научно-технический центр “ФЕРММАШ” (ООО НТЦ “ФЕРММАШ”) (RU)
|
(54) РОТОР ИЗМЕЛЬЧИТЕЛЯ МАТЕРИАЛОВ
(57) Реферат:
Изобретение предназначено для измельчения различных материалов. Ротор содержит приводной диск, по периферии которого перпендикулярно к его плоскости равномерно по окружности вращения расположены оси, на которых с возможностью поворота относительно диска закреплены радиально установленные в исходном положении молотки, жестко скрепленные со своими осями, кинематически связанными между собой посредством поворотного кольца с пазами под каждой осью и кулачков, закрепленных на осях с размещением в соответствующих пазах. У паза задняя стенка образует с его передней стенкой двугранный угол и установлена с возможностью взаимодействия с осью в крайнем рабочем положении кольца, а кулачок в пазу установлен с возможностью взаимодействия с задней стенкой паза в исходном положении кольца и с передней стенкой паза – в рабочем положении кольца. Изобретение позволяет снизить материалоемкость, энергоемкость и повысить эффективность работы ротора. 1 з.п. ф-лы, 7 ил.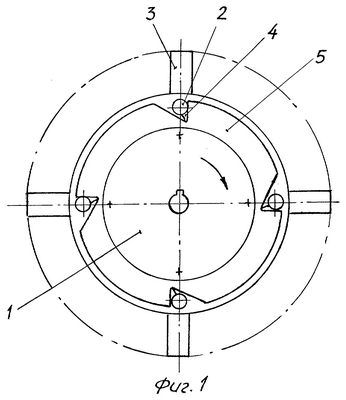
Изобретение относится преимущественно к области сельского хозяйства и может быть использовано при механизации трудоемких процессов на животноводческих фермах и комплексах для измельчения материалов (сено, солома) с целью использования в качестве корма (подстилки) для сельскохозяйственных животных отходов производства при утилизации, для получения мульчирующих материалов в растениеводстве, а также в других областях хозяйственной деятельности, например, для измельчения стеблей и корней лекарственных растений в медицине и ветеринарии, для измельчения сыпучих материалов строительного назначения.
В технике известны роторы для измельчения материалов различного назначения, выполненные в виде приводного диска с жестко закрепленными по окружности вращения измельчающими элементами ножевого или молоткового типа (см., например, ротор измельчителя по авторскому свидетельству на изобретение BG № 39472, МПК А 01 F 29/00, 1986 г.).
Недостатком таких устройств является возникновение динамических ударных нагрузок на ротор при измельчении неоднородных по физико-механическим свойствам материалов (размер частиц, плотность и т.п.) из-за жесткой связи измельчающих элементов с приводным диском, а также возможность заклинивания ротора при перегрузках.
Наиболее близким по технической сущности и достигаемому техническому результату к заявляемому объекту является дисковый ротор измельчителя, включающий приводной диск, по периферии которого перпендикулярно к его плоскости равномерно по окружности вращения расположены оси, на которых с возможностью поворота относительно диска установлены шарнирные молотки (см., например, дисковый ротор молотковой дробилки по авторскому свидетельству на изобретение СССР № 715096, МПК В 02 С 13/284, БИ № 6, 1980 г. – прототип).
В известном устройстве при шарнирном соединении с осями диска молотки в исходном положении занимают неопределенное произвольное положение, что в момент начала работы ротора вызывает его угловое ускорение в режиме возрастания момента инерции в процессе поворота молотков из произвольного в радиальное положение, что приводит к перегрузке привода ротора, а также вызывает вибрацию ротора из-за нарушения его балансировки.
Кроме того, в известном устройстве после выхода шарнирно подвешенного на оси молотка из зоны силового контакта с материалов при вращении диска возникает раскачивание молотка относительно оси подвеса под действием силы инерции вращения молотка, смещающей по окружности диска центр масс молотка то в одну, то в другую сторону относительно радиуса вращения оси молотка, что приводит к разбалансировке ротора и возникновению вибрации при его вращении.
При последующем попадании в зону контакта с материалом молотка, раскачивающегося относительно оси подвеса, возможно технологическое воздействие на молоток в сторону увеличения его углового отклонения при совпадении частоты внешнего воздействия с частотой колебаний молотков, что приводит к потере работоспособности ротора при складывании молотков в указанном режиме тангенциальной рабочей нагрузки на молотки.
Раскачивание центра масс шарнирно подвешенных на осях молотков в режиме разбалансировки ротора вызывает при работе с материалом колебания радиальной нагрузки на ось ротора и возникновение вибрации, разрушающей привод ротора.
Шарнирная подвеска молотка на оси не обеспечивает возможность передачи достаточного по силе ударного воздействия молотка на материал, что требует увеличения инерционной массы молотков и их кинетической энергии, а значит, приводит соответственно к увеличению материалоемкости ротора и повышению энергоемкости выполняемого им рабочего процесса.
Задачей настоящего изобретения повышение устойчивости рабочего вращения ротора в условиях периодической ударной нагрузки, исключение разбалансировки ротора и возникновение вибрации при его работе, а также снижение энергоемкости его рабочего процесса с достижением такого технического результата, при котором за счет наличия кинематической связи всех молотков в ударном воздействии одного молотка на измельчаемый материал участвует инерционная масса всех молотков ротора одновременно с сохранением возможности поворота молотка в рабочей зоне ротора относительно радиуса вращения оси молотка при создании условий, предотвращающих возможность колебательного движения молотка относительно точки подвеса после его выхода из рабочей зоны ротора, что исключает возможность разбалансировки ротора и возникновение вибрации при его работе, снижает инерционную массу каждого молотка с сохранением способности активного воздействия ротора на материал со снижением при этом энергоемкости процесса измельчения.
Решение поставленной технической задачи достигается тем, что в роторе измельчителя материалов, включающем приводной диск, по периферии которого перпендикулярно к его плоскости равномерно по окружности вращения расположены оси, на которых с возможностью поворота относительно диска установлены шарнирные молотки, последние в исходном положении установлены радиально и жестко скреплены со своими осями, кинематически связанными между собой посредством размещенного на диске поворотного кольца с пазами под каждой осью и кулачков, закрепленных на осях и размещенных в соответствующих пазах со смещением в сторону рабочего вращения диска своей вершины относительно продольной оси молотка, при этом у паза передняя по ходу указанного вращения стенка расположена в плоскости радиального сечения диска с возможностью взаимодействия с осью в исходном положении ее молотка для блокировки его углового смещения относительно исходного положения в сторону указанного вращения, задняя стенка паза образует с его передней стенкой двугранный угол и установлена с возможностью взаимодействия с осью в крайнем рабочем положении кольца, а кулачок в пазу установлен с возможностью взаимодействия с задней стенкой паза в исходном положении соответствующего молотка и с передней стенкой паза – в его рабочем положении.
У ротора угол при вершине двугранного угла выбран из условия
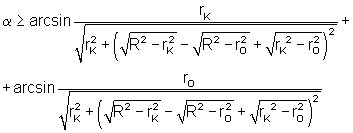
а длина рабочих участков образующей передней стенки паза lП и его задней стенки lЗ – из условий
и

где rK – радиус собственной окружности вращения вершины кулачка, м;
R – радиус окружности вращения центра осей молотков с диском;
rO – радиус окружности вращения оси молотка относительно диска, м.
Установка шарнирных молотков в исходном положении вдоль радиуса диска при их жестком соединении со своими осями обеспечивает возможность осуществления жесткой кинематической связи молотков при совмещении центра масс ротора с осью вращения ротора, что препятствует изменению момента инерции ротора при ускорении на холостом ходу, исключает разбалансировку ротора при ускорении его вращения на холостом ходу перед началом работы, а также при работе с материалом в условиях тангенциальной нагрузки.
Наличие кинематической связи всех молотков посредством размещенного на диске жесткого поворотного кольца с пазами под каждой осью и кулачков, закрепленных на осях и размещенных в соответствующих им пазах, обеспечивает угловое отклонение осей нерабочих молотков относительно радиального к диску исходного положения при угловом смещении оси работающего молотка под действием тангенциальной нагрузки, что создает возможность участия инерционной массы всех молотков в реализации ударного воздействия на материал рабочего молотка и возврат с сохранением балансировки ротора всех молотков в исходное положение после выходе рабочего молотка из зоны измельчения.
Закрепление кулачка на оси со смещением его вершины относительно продольной оси соответствующего молотка в сторону рабочего вращения диска обеспечивает поворот всех молотков в одну и ту же сторону, обратную вращению ротора, под действием тангенциальной нагрузки на рабочий молоток и создание молотками совместного противодействия действию рабочей нагрузки при опоре на кинематически связывающее их жесткое кольцо.
Расположение у паза кольца передней по ходу вращения ротора стенки в плоскости радиального сечения диска с возможностью опоры стенки на ось в исходном положении ее молотка исключает возможность поворота молотка относительно исходного положения в сторону вращения диска после выхода молотка из рабочей зоны, что в принципе исключает возникновение колебаний молотка в нерабочей зоне относительно точки его подвеса на диске.
Расположение задней стенки паза кольца с образованием двугранного угла с его передней стенкой ограничивает поворот кольца относительно оси вращения ротора только в пределах возможного угла поворота активного молотка относительно оси собственного вращения, что обеспечивает поворот всех молотков ротора практически на одинаковый угол и его синхронное изменение в условиях колебаний рабочей нагрузки из-за неравномерной плотности материала в зоне измельчения при сохранении балансировки ротора.
Установка задней стенки паза с возможностью опоры на ось молотка в крайнем рабочем положении кольца ограничивает угол поворота кольца в сторону вращения диска и соответственно рабочий угол отклонения продольной оси рабочего молотка от исходного положения, что обеспечивает функционирование в переменном диапазоне скоростей молотков их жесткой кинематической связи посредством кольца и кулачков их осей.
Установка кулачка в пазу с возможностью его взаимодействия с наклонной задней стенкой паза в исходном положении соответствующего молотка гарантирует возврат молотка под действием инерции вращения в исходное положение после его рабочего отклонения в результате соударения с измельчаемым материалом.
Установка кулачка в пазу с возможностью его взаимодействия с передней стенкой паза в рабочем положении соответствующего молотка обеспечивает передачу усилия, воспринимаемого рабочим молотком, одновременно всем нерабочим молоткам посредством жесткого кольца, что усиливает противодействие ротора действию нагрузки и повышает степень последовательного силового воздействия молотков на материал.
Выбор угла при вершине двугранного угла стенок паза из условия
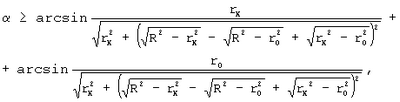
при длине рабочего участка задней стенки паза lЗ, выбранной из условия
,
где rK – радиус собственной окружности вращения вершины кулачка;
R – радиус окружности вращения центра осей молотков с диском;
rO – радиус окружности вращения оси молотка относительно диска, определяет предельный угол поворота кольца, соответствующий максимальному рабочему углу поворота молотка от исходного положения до его положения, допускающего вывод кулачка из паза в случае столкновения молотка с инородным телом, попавшим в измельчаемый материал, что препятствует заклиниванию ротора и поломке молотка.
Выбор длины рабочего участка образующей передней стенки паза lП из условия
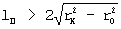
обеспечивает выход кулачка оси рабочего молотка из зацепления с кольцом при случайном столкновении молотка с инородным телом, а также обеспечивает под действием инерции вращения молотка обратный вход кулачка в соответствующий ему паз кольца после ликвидации препятствия с возвратом молотка в исходное положение.
Сущность предлагаемого технического решения поясняется графическими материалами, где
на фиг.1 представлен общий вид ротора в исходном положении (вид с торца);
на фиг.2 – поперечный разрез ротора, представленного на фиг.1;
на фиг.3 – поперечный разрез ротора во втором примере конструктивного исполнения;
на фиг.4 – общий вид ротора в рабочем положении;
на рис.5 – молоток в исходном положении при холостом вращении ротора;
на рис. 6 – молоток при предельном отклонении под нагрузкой в рабочем положении ротора;
на фиг.7 – расчетная схема для обоснования условий выбора значений параметров , lП и lЗ.
Ротор измельчителя материалов содержит приводной диск 1, по периферии которого равномерно по окружности вращения в отверстиях перпендикулярно к плоскости диска установлены поворотные оси 2, на каждой из которых закреплен один или несколько молотков 3, в исходном положении расположенных по радиусу диска 1, а также кулачок 4, у которого вершина обращена к оси вращения диска 1 и смещена в сторону рабочего вращения диска 1 относительно продольной оси молотка 3 в его исходном положении.
Оси 2 кинематически связаны между собой посредством жесткого поворотного кольца 5, установленного на диске 1 с возможностью ограниченного поворота вокруг оси диска 1 и снабженного для этого под каждой осью 2 пазами, в которых размещены кулачки 4. Каждый паз кольца 5 образован передней в направлении вращения диска 1 стенкой 6, расположенной в плоскости радиального сечения кольца 5 и задней стенкой 7. Стенки 6 и 7 установлены с образованием между собой двугранного угла .
В первом наименее материалоемком примере конструктивного исполнения ротора (фиг.1, 2) кольцо 5 установлено сбоку от диска 1 с его торцевой стороны, при этом для удобства сборки и разборки диск может быть выполнен составным – состоящим из двух жестоко связанных между собой (резьбовое соединение, заклепки и т.п.) частей, на одной из которых установлены оси 2, а на другой кольцо 5. Для посадки диска 1 на приводной вал в центральной части диска 1 выполнено посадочное отверстие со шпоночной канавкой, либо могут быть использованы любые известные в технике элементы закрепления (ступица с фиксирующим винтом и т.п).
Во втором примере симметричного в продольном направлении конструктивного исполнения ротора (фиг.3, 4) кольцо расположено в центральной части ротора в пределах габарита диска 1, при этом диск 1 также может быть выполнен составным – состоящим из двух крайних и размещенной между ними центральной частей с расположением осей 2 на крайних, а кольца 5 на центральной части диска 1.
В исходном положении молотка 3 передняя стенка 6 паза в исходном положении кольца 5 взаимодействует с осью 2, а задняя стенка 7 паза взаимодействует с осью 2 в крайнем рабочем положении кольца 5 после поворота кольца 5 в сторону рабочего вращения ротора, при этом кулачок 4 в пазу установлен с возможностью взаимодействия с задней стенкой 7 паза в исходном положении соответствующего молотка 3 и с передней стенкой 6 – в рабочем положении молотка 3 и кольца 5.
Условие для определения угла получено из следующих геометрических соображений на основании фиг.7.
В исходном положении ротора продольная ось молотка 3 в его исходном положении совмещена с радиусом диска, соединяющим центр О диска и центр O1 оси 2 (отрезок ОО1), образующая передней стенки 6 каждого паза кольца 5 в его исходном положении располагается по радиусу диска ОВ и касается оси 2 при взаимодействии в точке В с образованием прямоугольных треугольников O1BO и O1BA, образующая задней стенки паза 7 занимает положение АС и не касается оси 2, а вершина кулачка 4 (точка А), удаленная от центра O1 оси 2 на расстояние O1A, совмещена с вершиной двугранного угла ВАС= между передней стенкой 6 и задней стенкой 7 паза кольца 5.
При повороте рабочего молотка 3 под действием материала происходит угловое смещение продольной оси молотка 3 относительно прямой ОО1 в противоположную к вращению ротора сторону с поворотом под действием кулачка 4 кольца 5 в сторону вращения ротора.
Так как максимальный рабочий угол поворота кольца 5 должен допускать при дальнейшем повороте молотка 3 выход кулачка 4 из контакта с передней стенкой 6 (в случае соударения молотка 3 с инородным телом), то при максимальном угле поворота кольца вокруг центра О в крайнем рабочем положении кольца 5 вершина кулачка 4 касается образующей передней стенки 6 в т.В1 с образованием прямоугольного треугольника OO1B1, вершина двугранного угла из исходного положения в т.А после поворота кольца 5 переходит в положение m.A1 с образованием прямоугольного треугольника O1B1A1, образующая АС задней стенки паза 7 занимает положение A1C1 и касается оси 2 в т.D с образованием прямоугольного треугольника O1DA1, a двугранный угол между стенками 6 и 7 равен сумме углов 1= O1A1B1 и 2= O1A1D. Для обеспечения возможности выхода кулачка 4 из контакта со стенкой 6 при соударении молотка 3 с инородным телом необходимо, чтобы   1+ 2.
Введем обозначения: радиус собственной окружности вращения вершины кулачка 4 относительно центра O1 rК=O1A=O1B1, радиус окружности вращения центра осей молотков с диском R=ОО1, радиус окружности собственного вращения оси молотка относительно диска rО=O1D-O1B.
Из прямоугольного треугольника O1BO на основании теоремы Пифагора
, а из треугольника O1BA
.
Откуда ОА=ОА1=ОВ-АВ= .
Из прямоугольного треугольника OO1B1 по теореме Пифагора
.
Поскольку B1A1=OB1-OA1, то
.
В прямоугольном треугольнике О1A1B1:

поэтому

т.е.

В прямоугольном треугольнике O1A1D:
,
т.е.
.
С учетом этого
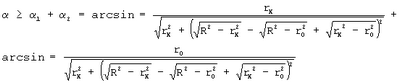
Условие для определения длины образующей lП передней стенки 6 паза получено из следующих соображений.
Для поворота кольца 5 в пределах максимального рабочего угла необходимо, чтобы образующая передней стенки 6 касалась оси 2 в т.В при исходном положении кольца 5, а образующая задней стенки 7 – в т.D в крайнем рабочем положении кольца 5 после его поворота.
В случае соударения рабочего молотка 3 с препятствием (инородное тело в материале) после выхода у оси 2 кулачка 4 из контакта его вершины с образующей стенки 6 кольцо 5 под действием инерции вращения остальных молотков возвращается в исходное положение, при котором передняя стенка 6 опирается на ось 2 и касается ее в т.В.
В этом случае после устранения препятствия возврат рабочего молотка 3 в исходное положение под действием инерции собственного вращения возможен только в том случае, если при повороте рабочего молотка 3 в сторону вращения ротора кулачок 4 своей вершиной может касаться образующей передней стенки 6 в ее верхней части – в т.А2 с образованием равнобедренного треугольника AO1A2, т.к. при меньшей длине образующей lП кулачок своей вершиной касается внешней цилиндрической поверхности кольца 5, что исключает всякую возможность повторного западания кулачка 4 в свой паз кольца 5.
По этой причине необходимо, чтобы длина образующей передней стенки 6 lП была больше длины отрезка AA2, равного 2АВ, т.к. треугольник AO1A2 – равнобедренный.
С учетом этого при установленном значении рабочего угла 
.
Условие для определения длины образующей lЗ задней стенки 7 паза получено из следующих соображений.
Контакт образующей задней стенки 7 (отрезок A1C1) с осью 2 (в т.D) в положении кольца 5, определяющем максимальный угол его рабочего поворота (образующая стенки 6 располагается по радиусу OA1) с соблюдением установленного условия для определения величины угла , возможен, когда длина образующей lЗ задней стенки 7 не меньше длины отрезка A1D, т.е. lЗ A1D.
Из прямоугольного треугольника O1A1D:

следовательно,

поэтому
.
Работа ротора измельчителя осуществляется следующим образом.
При рабочем вращении приводного диска (по часовой стрелке, как показано на фиг.1-7) вместе с ним осуществляется вращение в ту же сторону пальцев 2 с молотками 3 и кольца 5 как единого целого, при этом молотки в исходном положении своей продольной осью и передние стенки 6 пазов кольца 5 располагаются радиально относительно диска 1, каждая стенка 6 пазов кольца 5 опирается на свою ось 2 (в т.В), что при взаимодействии вершин кулачков 4 с задними стенками 7 пазов блокирует возможность поворота молотков 3 в сторону рабочего вращения диска 1.
При соударении с материалом в рабочей зоне ротора рабочий молоток 3 отклоняется относительно своего исходного положения на угол, пропорциональный величине нагрузки, в сторону, противоположную рабочему вращению диска 1, при этом кулачок 4 оси 2 при указанном повороте молотка 3 воздействует на переднюю стенку 6 своего паза кольца 5 и этим поворачивает кольцо 5 в сторону рабочего вращения диска 1 на соответствующий угол.
При повороте кольца 5 задние стенки 7 остальных пазов воздействуют на кулачки 4 своих осей 2 и этим поворачивают остальные неактивные молотки 3 в сторону углового отклонения рабочего молотка 3. В результате все молотки 3 ротора своей инерционной массой воспринимают ударную нагрузку, приходящуюся на рабочий молоток со стороны измельчаемого материала, что резко снижает величину углового отклонения рабочего молотка, т.к. при наличии кинематической связи всех молотков кинетическая энергия рабочего молотка 3 от соударения с материалом распределяется между всеми молотками ротора одновременно.
При выходе рабочего молотка 3 из рабочей зоны ротора под действием инерции вращения все молотки 3 поворачиваются в исходное положение, располагаясь своей продольной осью радиально к диску 1, при этом в результате воздействия вершины кулачков 4 на задние стенки 6 кольцо 5 поворачивается в исходное положение, при котором оно передними стенками 6 своих пазов опирается на оси 2, что при давлении кулачков 4 на стенки 7 кольца 5 блокирует возможность поворота любого молотка 3 в сторону рабочего вращения диска 1 относительно исходного положения и этим обеспечивает переход кинетической энергии собственного вращения молотков после выхода из-под нагрузки в энергию вращения всего ротора, что исключает возможность возникновения колебаний молотков 3 относительно точки подвеса на осях 2 и раскачивание шарнирного молотка относительно точки подвеса (т.O1).
При соударении с инородным телом рабочий молоток 3 отклоняется от исходного положения на угол /2 и выше вплоть до выхода кулачка 4 из контакта со стенкой 6 паза кольца 5 в его крайнем рабочем положении (T.B1) с последующей установкой кольца 5 в исходное положение. Затем при устранении препятствия под действием инерции вращения рабочий молоток 3 при контакте его кулачка 4 со стенкой 6 своего паза (т.А2) вновь устанавливается в исходное положение после рабочего поворота с последующим возвратом в исходное положение кольца 5 за счет взаимодействия кулачков 4 остальных молотков с задними стенками 7 своих пазов кольца 5.
Предлагаемое техническое решение обеспечивает самоадаптивный процесс изменения инерционной способности молотков ротора с учетом колебаний плотности измельчаемого материала и рабочей нагрузки на ротор с созданием условий, препятствующих возникновению колебаний молотков относительно точки подвеса, что оптимизирует рабочий процесс ротора, исключает разбалансировку ротора в условиях изменения рабочей нагрузки и его перегрузку в рабочем режиме, а также снижает материалоемкость ротора при использовании молотков с уменьшенной инерционной массой.
Формула изобретения
1. Ротор измельчителя материалов, включающий приводной диск, по периферии которого перпендикулярно к его плоскости равномерно по окружности вращения расположены оси, на которых с возможностью поворота относительно диска установлены шарнирные молотки, отличающийся тем, что молотки в исходном положении расположены радиально и жестко скреплены со своими осями, кинематически связанными между собой посредством размещенного на диске поворотного кольца с пазами под каждой осью и кулачков, закрепленных на осях и размещенных в соответствующих пазах со смещением в сторону рабочего вращения ротора своей вершины относительно продольной оси молотка в его исходном положении, при этом у паза передняя по ходу указанного вращения стенка расположена в плоскости радиального сечения диска с возможностью взаимодействия с осью в исходном положении кольца для блокировки углового смещения молотков относительно исходного положения в сторону указанного вращения, задняя стенка паза образует с его передней стенкой двугранный угол и установлена с возможностью взаимодействия с осью в крайнем рабочем положении кольца, а кулачек в пазу установлен с возможностью взаимодействия с задней стенкой паза в исходном положении кольца и с передней стенкой паза – в рабочем положении кольца.
2. Ротор измельчителя по п.1, отличающийся тем, что угол а при вершине двугранного угла выбран из условия
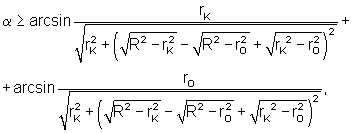
а длина рабочих участков образующей передней стенки паза lП и его задней стенки l3 – из условий
и
,
где rК – радиус собственной окружности вращения вершины кулачка, м;
R – радиус окружности вращения центра осей молотков с диском, м;
rо – радиус окружности вращения оси молотка относительно диска, м.
РИСУНКИ
|