|
(21), (22) Заявка: 2005103153/02, 09.02.2005
(24) Дата начала отсчета срока действия патента:
09.02.2005
(46) Опубликовано: 20.02.2007
(56) Список документов, цитированных в отчете о поиске:
WO 00/60297 A1, 12.10.2000. RU 2025499 C1, 30.12.1994. RU 2086872 C1, 10.08.1997. SU 1838037 A3, 30.08.1993.
Адрес для переписки:
101990, Москва, Петроверигский пер., 4, ООО “Агентство по защите интеллектуальной собственности” Ермакова, Столярова и партнеры”, пат.пов. И.А.Столяровой
|
(72) Автор(ы):
ШУМАХЕР Эвальд Антонович (DE), Хлопонин Виктор Николаевич (RU), ШУМАХЕР Эдгар Эвальдович (DE), ФРАНЦКИ Рената Эвальдовна (DE), Белитченко Анатолий Константинович (MD), Деревянченко Игорь Витальевич (MD), Савьюк Александр Николаевич (MD), Зинковский Иван Васильевич (RU)
(73) Патентообладатель(и):
Техком Импорт Экспорт ГмбХ (DE)
|
(54) СПОСОБ ОПОРОЖНЕНИЯ МЕТАЛЛОПЛАВИЛЬНОЙ ЕМКОСТИ ОТ ОСНОВНОЙ ЧАСТИ ЖИДКОГО МЕТАЛЛА ЧЕРЕЗ ВЫПУСКНОЕ ОТВЕРСТИЕ В ДОННОЙ ПОВЕРХНОСТИ ЕМКОСТИ И МЕТАЛЛОПЛАВИЛЬНАЯ ЕМКОСТЬ
(57) Реферат:
Изобретение относится к производству металла в черной и цветной металлургии, конкретно к производству стали в дуговых сталеплавильных печах. В способе перед началом опорожнения емкости осуществляют подъем уровня входа металла в выпускное отверстие и сохраняют это положение до окончания опорожнения емкости, после чего восстанавливают исходное положение уровня этого входа, при этом потоки уходящего металла отделяют от поднимающихся к входу в выходное отверстие потоков металла стенкой, величина которой определяет величину подъема уровня входа металла в выходное отверстие. На химический состав жидкого металла воздействуют путем подачи легирующих элементов в потоки металла, покидающего емкость, которую осуществляют совместно с подачей нейтрального или инертного газа. Металлоплавильная емкость содержит стержень с возможностью его вертикального перемещения, вплоть до вывода за пределы емкости. Стержень расположен оппозитно выпускному отверстию и внизу выполнен в форме стаканоподобной полости, в которой жестко, на перемычках закреплена надставка со сквозным отверстием и имеет центральное отверстие для подачи легирующих элементов и нейтрального или инертного газа в потоки уходящего газа. Надставка выступает за пределы стержня, высота этого выступа наряду с высотой надставки и толщиной слоя шлака определяют количество металла, оставляемого в емкости. Изобретение позволяет улучшить качество металла за счет гарантированного исключением попадания печного шлака в металл в ковше, оперативной внепечной обработке металла в ковше (дефосфорации, азотирования, науглероживания), снижения расхода легирующих элементов. 2 н. и 16 з.п. ф-лы, 14 ил.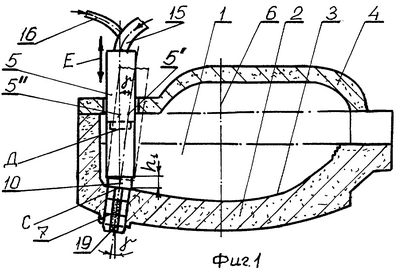
Изобретение относится к производству металла в черной и цветной металлургии и представлено на примере производства стали в дуговых сталеплавильных печах (ДСП).
Заключительной стадией производства металла в металлоплавильной емкости является опорожнение емкости от жидкого металла. Эту операцию выполняют различными способами, при этом широко распространен, особенно в ДСП, вертикальный выпуск металла через выпускное отверстие в дне емкости. Применительно к ДСП в последние годы распространенным приемом стало опорожнение металлоплавильной емкости от основной части металла с оставлением меньшей части жидкого металла в емкости. (См., например, журнал “Электрометаллургия”, №1, 2000, с.46).
Составной частью процесса производства жидкого металла является формирование шлака, играющего важную роль в получении металла заданного химического состава. Шлак, имея более низкую плотность в сравнении с жидким металлом, располагается сверху ванны металла. Важной технической задачей является максимальное исключение попадания печного шлака в ковш, успешное решение которой в значительной мере зависит от реализуемого способа опорожнения металлоплавильной емкости от металла, от конструктивного исполнения самой емкости, особенно в части обеспечения выпуска металла.
Известен способ опорожнения металлоплавильной емкости от жидкого металла через сливное окно (см., например, патент РФ №2025499 С 21 С 5/52; F 27 B 3/14. Опубл. в Бюл. №24; 30.12.94).
Основными недостатками известного способа является, во-первых, значительные затраты времени на опорожнение емкости, во-вторых, невозможность исключения попадания печного шлака с металлом в ковш.
Известен способ опорожнения металлоплавильной емкости от жидкого металла путем донного выпуска, в том числе с использованием эксцентрикового выпускного отверстия в дне емкости (ЕВТ – технология, см., например, “Металлургический завод и технология”, МРТ – 11, перев. на русский 2002 г., Штефан Лемке, Петер Майерлинг, Петер Монхайм и др. “Технические решения для производства стали”, с.26).
Этот известный способ опорожнения металлоплавильной емкости от жидкого металла получил широкое распространение на ДСП.
Известному способу присущи следующие недостатки.
1. Не решена техническая задача образования VORTEX (закручивание потока металла), что затрудняет отсечение шлака от жидкого металла в процессе опорожнения емкости.
2. Жидкий металл в районе эксцентрикового выпуска имеет пониженную температуру, что удлиняет продолжительность плавки, так как требует подогрева металла.
Известен способ опорожнения металлоплавильной емкости от жидкой стали с помощью системы ИРИС (по инфракрасному излучению (см., например, журнал “Сталь” №11, 2004 г., с.36).
Основной недостаток этого известного способа состоит в попадании части шлака в жидкий металл ковша в процессе выпуска (этот недостаток отмечен там же).
Известен способ опорожнения металлоплавильной емкости от основной части жидкого металла, включающий опускание потоков металла, покидающего емкость, ниже уровня его входа в выпускное отверстие, вплоть до донной поверхности в этой части емкости, последующее перемещение вдоль донной поверхности и подъем этих потоков металла до и выше уровня входа в выпускное отверстие и выпуск металла через это отверстие, при этом опускающиеся и поднимающиеся потоки металла разделены стенкой, между торцом которой и донной поверхностью емкости предусмотрен зазор, связывающий опускающиеся и поднимающиеся потоки металла (см., например, международный патент WO 00/60297 F 27 D 3/14, F 27 B 3/19 от 12.10.2000 г. с приоритетом от 01.04.1999 г. В реферате “Перспективы развития технологии выплавки стали в дуговых печах к 2010 г.”, в журнале “Новости черной металлургии за рубежом”, №1, 2001, с.40 приведены преимущества этого известного способа и схема его реализации. Аббревиатура системы – “FAST”).
По существенным признакам этот известный способ наиболее близок предлагаемому, поэтому принят за прототип.
Известному способу присущи следующие существенные недостатки, исключающие его успешное применение для высокоэффективного опорожнения металлоплавильной емкости от основной части жидкого металла при одновременной обработке металла в ковше, воздействующей на химический состав стали:
во-первых, выпуск основной части жидкого металла вынесен за пределы рабочего пространства емкости, что автоматически приводит к охлаждению выпускаемого металла, к необходимости его подогрева;
во-вторых, реализация способа требует наличия в емкости дополнительного выпускного отверстия для полного опорожнения емкости от оставшегося жидкого металла и шлака, необходимого, например, при остановке работы емкости;
в-третьих, в способе не предусмотрен ввод в жидкий металл, покидающий емкость, элементов, изменяющих его свойства в ковше;
в-четвертых, реализация способа требует повышенной высоты (порядка 200 мм) над уровнем дна емкости канала для прохождения жидкого металла из емкости в сторону входа в выпускное отверстие. Последнее автоматически приводит к необходимости дополнительного подъема высоты уровня расположения входа металла в выпускное отверстие, что уменьшает объем металла, способного покинуть емкость;
в-пятых, реализация способа не позволяет учесть влияния изменения плотности и толщины слоя шлака от плавки к плавке на процессе опорожнения емкости, так как конструктивные элементы емкости для осуществления способа выполнены стационарными, без возможности оперативной замены, в то время как плотность шлака зависит от его химсостава (см., например, В.И.Явойский и др. “Металлургия стали”, 1983 г., стр.51), а толщина слоя шлака – от технологии ведения плавки и марки производимой стали;
в-шестых, при реализации способа отсутствует механизм предотвращения попадания печного шлака в металл на начальной стадии опорожнения емкости (попавшего в металл и поступившего в каналы выпуска металла на начальной стадии расплавления шихты).
Предлагаемый способ опорожнения металлоплавильной емкости от основной части жидкого металла через выпускное отверстие в донной поверхности емкости свободен от указанных недостатков. В нем выпуск жидкого металла осуществляют непосредственно из рабочего пространства печи, что исключает переохлаждение выпускаемого металла. Отсутствует необходимость наличия в емкости дополнительного выпускного отверстия. Предусмотрен ввод в жидкий металл, покидающий емкость, элементов, изменяющих свойства металла при нахождении в ковше. Обеспечено существенное снижение высоты зазора, необходимой для прохождения металла в выпускное отверстие. Предусмотрена коррекция в реализации способа в зависимости от предполагаемых химсостава (плотности) и толщины слоя шлака.
Получение указанных технических результатов обеспечено благодаря тому, что в известном способе опорожнения металлической емкости от жидкого металла, включающем опускание потоков металла, покидающего емкость, ниже уровня его входа в выпускное отверстие, вплоть до донной поверхности в этой части емкости, последующее перемещение вдоль донной поверхности и подъем этих потоков металла до и выше уровня входа в выпускное отверстие и выпуск металла через это отверстие, при этом опускающиеся и поднимающиеся потоки металла разделены стенкой, между торцом которой и донной поверхностью емкости предусмотрен зазор, связывающий опускающиеся и поднимающиеся потоки металла по изобретению перед началом опорожнения емкости поднимают уровень входа металла в выпускное отверстие над исходным его положением в донной поверхности емкости и сохраняют поднятое положение до окончания опорожнения емкости, от основной части металла, при этом потоки уходящего металла отделяют от поднимающихся потоков металла стенкой, высота которой определяет величину подъема уровня входа металла в выпускное отверстие, а после того как процесс опорожнения прекратится, восстанавливают исходное положение уровня этого входа, оставляя в емкости меньшую часть металла. При этом в потоки металла, входящие в выпускное отверстие, подают элементы, воздействующие на химический состав жидкого металла, при этом подачу осуществляют с одновременной подачей в эти потоки металла инертного или нейтрального газа. Подачу элементов в жидкий металл осуществляют ниже поднятого уровня входа в выпускное отверстие. Осуществляют предварительный подогрев инертного или нейтрального газа. Кроме того, до начала опорожнения емкости прокачивают инертный или нейтральный газ через металл, расположенный над выпускным отверстием и в зазорах, предназначенных для прохода металла из емкости в выпускное отверстие, при этом после окончания прокачивания давление газа сохраняют до начала выпуска металла. Помимо этого, перед загрузкой емкости шихтой устройство, обеспечивающее подъем уровня входа металла в выпускное отверстие, выводят за пределы возможного контакта устройства с шихтой.
Известна конструкция металлоплавильной емкости, позволяющая опорожнять емкость от основной части жидкого металла через сливное окно (см., например, указанный патент РФ №2025499).
Известной конструкции присущи существенные недостатки, уже проанализированные при анализе способа.
Известна конструкция металлоплавильной емкости, содержащая устройства для опорожнения от основной части жидкого металла через выпускное отверстие с вертикальным выпуском металла (см., например, уже упомянутый патент WO 00/60297, F 27 D 3/14, F 27 B 3/19 от 12.10.2000). Известная конструкция емкости выполнена в форме фигурной в плане чаши, сверху изолированной от окружающей среды строением рамной конструкции с образованием рабочего пространства емкости. Строение рамной конструкции печи может образовывать сводную крышу емкости, может обеспечивать подачу в емкость шихты в виде подогретого лома.
Указанная известная конструкция металлоплавильной емкости по существенным признакам наиболее близка предлагаемой, поэтому принята за прототип.
Известной конструкции металлоплавильной емкости, реализующей известный из этого же патента способ опорожнения емкости от части жидкого металла, присущи существенные недостатки, подробно проанализированные при рассмотрении способа опорожнения емкости, так как наряду с приемами реализации способа эти недостатки обусловлены конструктивным исполнением самой емкости.
Предлагаемая металлоплавильная емкость для осуществления предлагаемого способа ее опорожнения от основной части жидкого металла свободная от указанных недостатков. Конструктивное исполнение предлагаемой металлоплавильной емкости позволяет реализовать перечисленные приемы предлагаемого способа с организацией выпуска металла непосредственно из рабочего пространства емкости с гарантированным исключением попадания печного шлака в ковш; исключает необходимость наличия в печи двух выпускных отверстий; предусматривает ввод в металл, покидающий емкость, элементов, изменяющих свойства металла при нахождении в ковше; обеспечивает коррекцию движения потоков металла в зависимости от предполагаемого химсостава (плотности) и толщины шлака; исключает появление завихрения металла и шлака.
Получение указанных технических результатов обеспечено благодаря тому, что в известной конструкции металлоплавильной емкости для осуществления способа опорожнения емкости от основной части жидкого металла, выполненной в форме фигурной в плане чаши, сверху изолированной от окружающей среды строением рамной конструкции с образованием рабочего пространства емкости, по изобретению через верхнее строение рамной конструкции оппозитно выпускному отверстию проходит стержень из огнеупорного материала, верхний конец которого расположен вне рабочего пространства емкости и от привода стержень имеет возможность осевого перемещения в сторону дна емкости, а нижний конец стержня заканчивается стаканоподобной полостью, в которой на перемычках жестко закреплена по центру стержня надставка, установленная с зазорами между соответствующими зеркальными поверхностями полости и надставки, при этом надставка выполнена с центральным сквозным отверстием, поверхность ее торца выступает за пределы стержня и очертания этой поверхности повторяют очертания донной поверхности в районе входа в выпускное отверстие, высота надставки над поверхностью дна емкости в районе выпускного отверстия равна величине подъема уровня входа металла в выпускное отверстие, а все перечисленные отверстия и зазоры по отдельности, предназначенные для прохода металла из емкости в выпускное отверстие, имеют проходные сечения по меньшей мере равные поперечному сечению выпускного отверстия. Стержень на участке верхний торец – дно стаканоподобной полости имеет сквозное центральное отверстие. При этом для стержня и его соединения с надставкой выполнено следующее соотношение:
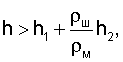
где h – высота надставки; h1 – высота выступа надставки за пределы стержня; h2 – предлагаемая наибольшая высота слоя шлака над металлом в конце выпуска металла из емкости; м и ш – удельный вес металла и шлака соответственно. Причем в нижнем положении стержень плотно без зазоров прилегает выступом надставки к поверхности дна емкости. Кроме того, вход в выпускное отверстие в донной поверхности емкости выполнен в виде отверстия с конической поверхностью и оппозитно надставка снабжена выступом с зеркальной конической поверхностью к этому отверстию. К тому же, путем продольного перемещения стержня созданы условия для вывода надставки в верхнюю часть рабочего пространства емкости, в которой исключен контакт надставки с шихтой. Также, в центре дна стаканоподобной полости стержня имеется выступ, от торца которого до верхней части стержня выполнено центральное сквозное отверстие, соединенное гибкими шлангами с устройствами для подачи твердых материалов разной фракции и инертного или нейтрального газа, при этом на уровне дна стаканоподобной полости это отверстие имеет поперечные каналы, дополнительно соединяющие центральное отверстие с этой полостью. Поперечные каналы выполнены наклонными с понижением от дна стаканоподобной полости в сторону центрального отверстия стержня. Ось стержня перпендикулярна поверхности дна емкости в районе выпускного отверстия. Ось стержня отклонена от вертикали на угол отклонения от вертикали оси выпускного отверстия, при этом обе оси расположены на одной прямой. Сквозное отверстие в надставке состоит из конической и цилиндрической частей, при этом коническая часть является входной, а цилиндрическая – выходной для металла, и диаметр цилиндрической части по меньшей мере равен диаметру выпускного отверстия. Нижняя часть стержня, включающая стаканоподобную полость и закрепленную в ней надставку, выполнена сменной, при этом для смены нижней части стержень снабжен возможностью вывода за пределы рабочего пространства емкости.
Предложена определенная последовательность основных операций при осуществлении разработанного способа опорожнения предлагаемой металлоплавильной емкости от основной части жидкого металла путем переливания в ковш, включающая открытие выпускного отверстия в дне емкости, согласно изобретению, перед открытием выпускного отверстия опускают стержень с надставкой до плотного без зазоров прилегания торцевой поверхности надставки к донной поверхности чаши емкости, оппозитно входу в выпускное отверстие, в процессе этого опускания стержня или после окончания через центральное отверстие в стержне прокачивают инертный или нейтральный газ и в момент прекращения указанного прокачивания газа открывают выпускное отверстие и осуществляют опорожнение емкости, при этом в процессе опорожнения через центральное отверстие в стержне в металл подают элементы, воздействующие на химический состав жидкого металла в ковше и эту подачу элементов сопровождают подачей нейтрального или инертного газа, имеющему к моменту входа в металл температуру, близкую к температуре металла, и давление, по меньшей мере равное атмосферному, а сам процесс опорожнения автоматически прекращается благодаря условию
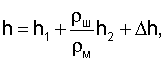
где h – высота надставки; h1 – высота выступа надставки за пределы стержня; h2 – наибольшая высота слоя шлака над металлом в конце выпуска металла; м и ш – удельный вес металла и шлака соответственно; h – в районе выпускного отверстия запас толщины слоя металла, оставляемого в емкости, закрывают выпускное отверстие и меньшую часть металла и весь шлак оставляют в емкости или выпускное отверстие оставляют открытым, надставку продолжают прижимать ко дну емкости и меньшую часть металла выпускают через выпускное отверстие; при открытом выпускном отверстии отводят стержень от донной поверхности и в отдельный ковш выпускают весь шлак и оставшийся металл.
Предлагаемый способ, металлоплавильная емкость для его осуществления и последовательность основных операций при его осуществлении пояснены чертежами на фиг.1-14.
На фиг.1 показана металлоплавильная емкость с верхним строением рамной конструкции в виде сводовой крыши до поворота емкости для ее опорожнения; на фиг 2 приведено положение емкости (без верхнего строения) после ее поворота для опорожнения и в процессе опорожнения от основной части металла; на фиг.3 показана металлоплавильная емкость (без верхнего строения) с эркерным расположением выпускного отверстия; на фиг.4 приведено положение металлоплавильной емкости шахтного типа (без верхнего строения) перед и в процессе опорожнения емкости от основной части жидкого металла; на фиг.5 – основные элементы нижней части вводимого в жидкий металл емкости стержня, обеспечивающие реализацию способа опорожнения емкости; на фиг.6 – разрез А-А на фиг.5; на фиг.7 – вариант расположения на стадии перед выпуском металла основных элементов нижней части вводимого в металл емкости стержня, обеспечивающих реализацию способа опорожнения емкости; на фиг.8 – разрез А-А на фиг.7; на фиг.9 – разрез Б-Б на фиг.7; на фиг.10 – вариант расположения основных элементов нижней части вводимого в металл емкости стержня с его центрированием относительно оси выпускного отверстия в дне емкости; на фиг.11 показан составной стержень со сменяемой нижней частью; на фиг.12 – последовательность основных операций при осуществлении способа; на фиг.13 – схема лабораторной установки (холодной модели), на которой выполнена оценка эффективности приемов реализации предлагаемого способа; на фиг.14 – разрез А-А на фиг.13.
Металлоплавильная емкость имеет рабочее пространство 1 (фиг.1), образованное фигурной в плане чашей 2 с переменной глубиной донной поверхности 3 (фиг.1) и ограниченное сверху от окружающей среды строением рамной конструкции 4. Указанное строение может быть сводовой крышей емкости (как показано на фиг.1) или для шахтных дуговых сталеплавильных печей, рассчитанных на загрузку печи сверху подогреваемым отходящими газами ломом, соответствующее строение рамной конструкции. Для реализации предложенного способа конструкция верхнего строения емкости не имеет принципиального значения. Важно только, что в этом строении предусмотрено место для прохождения стержня 5 на участке строения, асимметричном вертикальной оси 6 емкости и расположенном оппозитно выпускному отверстию 7 в донной поверхности 3 емкости. Необходимо также в конструкции наличие возможности предотвращения воздействия загружаемого лома (шихты) на стержень 5. Продольная ось стержня 5′ может быть сосной с осью выпускного отверстия 7, которое отклонено на угол от вертикальной оси 6 емкости. Продольная ось стержня 5″ может быть расположена вертикально, т.е. образовывать с осью выпускного отверстия 7 угол . Но в обоих рассмотренных случаях расположения оси стержня 5 и оси выпускного отверстия 7 указанные оси пересекаются в точке “С”, в центре входа в выпускное отверстие 7 на донной поверхности 3 (фиг.1-3). На стадии перед опорожнением емкости в выпускном отверстии может находиться закупоривающий его материал, например песок (фиг.7).
Ось выпускного отверстия 7 может быть расположена вертикально, параллельно вертикальной оси 6 емкости (фиг.4). В этом случае опорожнение металлоплавильной емкости от основной части жидкого металла осуществляют без широко распространенного поворота емкости в сторону выпускного отверстия 7 для придания оси отверстия 7 практически вертикального положения.
Стержень 5 снабжен механизмом осевого перемещения в/от направлении дна 3 емкости, который соединен с верхней частью стержня. Конструктивное исполнение этого механизма перемещения стержня 5 не определяет сущности выполнения операций предлагаемого способа, поэтому здесь этот механизм не рассматривается. В частности, этот механизм может быть расположен вне конструкции металлоплавильной емкости.
Для выполнения приемов предлагаемого способа важно наличие указанного механизма осевого перемещения стержня 5, обеспечение этим механизмом перемещения стержня 5, вплоть до плотного контакта с дном 3 емкости, обеспечение этим механизмом положения “Д” (фиг.1) стержня, когда он находится в рабочем пространстве емкости, но не контактирует с загруженной в емкость шихтой, и обеспечение этим механизмом вывода всего стержня 5 за пределы емкости. Направления перемещения стержня 5 с помощью этого механизма на фиг.1 показаны стрелками “Е”.
Нижняя часть стержня 5 имеет стаканоподобную полость 8 (фиг.5), в которой по центру стержня 5 на перемычках 9 жестко закреплена надставка 10, являющаяся составной частью стержня. При этом в зависимости от параметров выпускного отверстия 7 перемычки 9 могут быть расположены по бокам надставки 10 (фиг.5 и 6) или на верхней торцевой поверхности надставки 10 (фиг.7-9). Возможны и другие варианты расположения перемычек 9. При этом следует иметь в виду, что вариант исполнения и место расположения перемычек 9 влияют на размер проходного сечения для выпускаемого металла, хотя это влияние незначительно и им можно пренебречь.
Надставка 10 на величину h1 (фиг.5, 7, 10 и 11) выступает за пределы торца стержня 5 и имеет высоту h (фиг.5, 7, 10 и 11). Нижняя поверхность “Ж” торца надставки 10 имеет очертания поверхности, идентичные очертанию донной поверхности 3 емкости в районе входа в выпускное отверстие 7. Между зеркальными поверхностями стаканоподобной полости 8 и надставки 10 (т.е. внутренней поверхностью полости 8 и наружной поверхностью надставки 10, а также поверхностью дна полости 8 и наружным торцом надставки 10) имеются зазоры, площадь сечения каждого из которых по меньшей мере равна d2/4, где d – диаметр выпускного отверстия (фиг.5 и 6, 7 и 8, 10).
Надставка 10 выполнена с центральным сквозным отверстием, к тому же это отверстие выполнено из двух частей: конической 11 и цилиндрической 12. Диаметр цилиндрической части d1 d, где d – диаметр выпускного отверстия 7 емкости, при этом предпочтительно d1 d.
Для упрощения операции обеспечения плотного прилегания нижнего торца надставки 10 и донной поверхности 3 в районе входа в выпускное отверстие 7 нижнюю часть надставки 10 выполняют с коническим выступом, соответственно вход в выходное отверстие 7 емкости выполнен в виде отверстия с конической поверхностью (фиг.10).
Для стержня 5, его жесткого соединения с надставкой 10 и их совместного сочленения с входом в выпускное отверстие 7 емкости характерно соотношение

где h – высота надставки 10 (фиг.5, 7 и 10);
h1 – высота выступа надставки 10 за пределы стержня 5 (фиг.1, 4, 5, 7 и 10);
h2 – предлагаемая наибольшая высота слоя шлака над металлом в конце выпуска металла из емкости (фиг.5, 7 и 10);
м и ш – удельный вес металла и шлака соответственно (для шлака – предполагаемый).
Предусмотрено два варианта исполнения стаканоподобной полости 8: с плоским дном (фиг.5) и с выступом 13 по центру дна (фиг.7, 10, 11 и 13), который с зазором входит в отверстие 11 сквозного отверстия надставки 10 и торец выступа 13 расположен ниже верхнего торца надставки 10 так, что по существу выступ 13 входит в коническое отверстие 11 надставки 10 и может входить в цилиндрическое отверстие 12 надставки 10, при этом так, что поперечное сечение образуемого зазора между соответствующими поверхностями отверстия 11 и выступа 13 (отверстия 12 и выступа 13) превышает поперечное сечение выпускного отверстия 7.
От торца выступа 13 и до верхней части стержня 5, по его центру, выполнено сквозное отверстие 14 (фиг.7, 10, 11 и 13). Аналогично выполнен стержень 5 с плоским дном стаканоподобной полости 8 (фиг.5). В верхней части стержня 5 к отверстию 14 подведен гибкий шланг 15 (фиг.1) для подачи в металл, покидающий емкость, элементов, изменяющих химический состав стали в ковше. Эту подачу сопровождают подачей инертного или нейтрального газа через шланг 16. Шланги 15 и 16 соединены с устройствами для подачи соответственно твердых материалов разной фракции и инертного или нейтрального газа. Предусматривают также совместное исполнение шлангов 15 и 16, т.е. подаваемые в жидкий металл элементы поступают совместно с газом из соответствующего контейнера по единому шлангу 15.
Предусмотрен предварительный подогрев газа, при этом в конечном итоге обеспечивают к моменту входа газа в жидкий металл равенство (или несколько ниже) температуры газа температуре жидкого металла. Для этого используют либо индукционный подогрев стальной трубы в верхней части стержня 5, либо концевую часть шланга 16 исполняют металлической с индукционным или другим подогревом, либо металлическую концевую часть шланга 16 обвивают несколько раз вокруг верхней части стержня 5 и только после этого шланг 16 входит в отверстие 14. Для случая подачи элементов, вводимых в жидкий металл, совместно с инертным или нейтральным газом из контейнера по единому шлангу 15, подогрев газа могут осуществлять до объединения подаваемых элементов и газа в единый поток.
Заметим, что для реализации предлагаемого способа не имеет принципиального значения принятый прием подогрева подаваемого газа, важно, чтобы в момент входа в поток металла, покидающего емкость, температура газа была близка к температуре металла, но не превышала ее.
Важно также иметь возможность подачи газа в металл без предварительного подогрева, не считая нагрева газа в процессе прохождения отверстия 14 в стержне 5. В этом случае может быть предусмотрена отдельная ветка для ввода газа в отверстие 14.
Предпочтительно стержень 5 выполняют составным так, что нижняя часть стержня, включающая стаканоподобную полость 8 и закрепленную в ней надставку 10, выполнены сменными (фиг.11). Однако возможно использование сплошных стержней 5, соединенных жестко с надставками 10. В этом случае в эксплуатации емкости используют набор стержней 5 и организуют их систематический ремонт.
Перед и в процессе опорожнения в рабочем пространстве 1 емкости находится жидкий металл 17, над которым расположен шлак 18. До начала опорожнения емкости от основной части жидкого металла выпускное отверстие 7 закрыто перекрывающим устройством (пробкой) 19, а также заполнено, например, песком (фиг.1-4, 7).
В конструкции выступа 13 стержня 5 предусмотрено наличие поперечных каналов 20, связывающих дополнительно центральное отверстие 14 с полостью 8 на уровне дна этой полости (фиг.7, 10, 11 и 13). Каналы 20 могут быть выполнены наклонными (фиг.10) с понижением от дна полости 8 в сторону центрального отверстия 14 стержня 5.
Способ опорожнения металлоплавильной емкости от основной части жидкого металла осуществляют следующим образом.
Рабочее пространство 1 емкости до определенного уровня заполнено жидким металлом 17 и слоем шлака 18 над ним (на фиг.1-4 условно не показано, т.к. эти фигуры не определяют основные положения предлагаемого способа опорожнения емкости от части жидкого металла). Металл 17 и слой шлака 18 толщиной h2 показаны на фиг.5, 7 и 10.
Реализацию способа начинают после того, как шихта в емкости полностью расплавлена, часть шлака скачена и емкость с жидким металлом и оставшимся шлаком готовится к опорожнению.
В этот момент стержень 5 из положения “Д” на фиг.1 приводом перемещения опускают (см. стрелку Е на фиг.1) вниз до плотного без зазоров контакта нижнего торца “Ж” надставки 10 с донной поверхностью 3 емкости в районе выпускного отверстия 7 (фиг.1, 2, 5, 7 и 10).
Благодаря существенному (например, в 2 и более раз) превышению диаметра d1 отверстия 12 надставки 10 над диаметром d выпускного отверстия (d1>d на фиг.5 и 7) и плотному прилеганию нижнего торца “Ж” надставки 10 к донной поверхности 3 емкости обеспечивают гарантированное (беспрепятственное) протекание металла через отверстие 12 в выпускное отверстие 7. Указанным существенным превышением диаметра d1 над d, к тому же, устраняет влияние неточностей (смещений) в процессе установки стержня 5 на процесс опорожнения емкости от жидкого металла.
Эту же задачу решают путем выполнения коническим входа в выпускное отверстие 7 в донной поверхности 3 емкости. Оппозитно надставку 10 снабжают выступом с зеркальной конической поверхностью “Ж” к этому коническому входу (фиг.10).
Металлоплавильную емкость для опорожнения поворачивают, придавая ей положение, приведенное на фиг.2. Опорожнение емкости при отличающемся от фиг.1-3 исполнении донной поверхности 3 осуществляют без поворота емкости (фиг.4).
В обоих случаях реализации способа опорожнения емкости от основной части жидкого металла взаимное расположение металла 17, шлака 18, стержня 5, надставки 10 и выпускного отверстия 7 в донной поверхности 3 емкости обеспечивают таким, как показано на фиг.5, 7 и 10. При этом, в случае поворота емкости, толщина слоя шлака 18 изменяется до величины h2 на фиг.5, 7 и 10, и эту толщину принимают за основу при назначении момента автоматической остановки опорожнения емкости и установлении количества металла, оставляемого в чаше 2 емкости.
Благодаря первоначальному нахождению стержня 5 в положении “Д” рабочего пространства 1 емкости и последующему, до начала опорожнения емкости, нахождению нижней части стержня 5 в жидком металле 17 исключают подстуживающее действие элементов стержня 5 на металл 17 в районе выпускного отверстия 7.
В процессе описанного опускания стержня 5 в ванну металла 17 в отверстия 11 и 12 надставки 10, и 14 стержня 5, а также в зазоры, образованные разностью диаметров d3 полости и d2 надставки и дном полости 8 и верхним торцом надставки 10 поступит металл 17 и шлак 18. Для удаления шлака 18 (вместе с металлом) через отверстие 14 в стержне 5 отверстия 11 и 12 в надставке 10 и указанные зазоры интенсивно прокачивают нейтральный или инертный газ. Нагреваясь от соприкосновения с горячим стержнем 5 и попадая в жидкий металл 17, подаваемый газ расширяется и быстро вытесняет вместе металл 17 и шлак 18, попавшие в эти отверстия и зазоры.
Для ускорения операции опорожнения емкости интенсивную прокачку нейтрального или инертного газа через отверстие 14 в стержне 5 осуществляют в процессе опускания стержня 5, чем исключают попадание шлака в указанные отверстия и зазоры. В обоих случаях газ предварительно не подогревают и обеспечивают давление газа на уровне, не превышающем давление жидкого металла на пробку 19 выпускного отверстия 7. Для упрощения операции интенсивной прокачки газа 2 и удаления шлака возможно применение системы подачи газа в отверстие 14 стержня 5, отдельной от системы подачи этого же газа с элементами, вводимыми в металл для изменения его химического состава.
В обоих случаях прокачки инертного газа давление газа поддерживают на заданном уровне, вплоть до начала опорожнения емкости. Тем самым исключают поступление металла в центральное отверстие 14 и возможное “козление” металла в этом отверстии.
В этот момент открывают перекрывающее устройство (удаляют пробку) 19, тем самым открывают выпускное отверстие 7 и начинают опорожнение емкости. В процессе опорожнения потоки жидкого металла 17 опускаются до донной поверхности 3 емкости, затем перемещаются вдоль донной поверхности в зазоре высотой h1, после чего поднимаются по зазору (d3-d2) на высоту до и выше h, вплоть до дна стаканоподобной полости 8 и окончательно устремляются в отверстия 11 и 12 надставки 10 и из них в выпускное отверстие 7 (описанное показано на фиг.5, 7 и 10 пунктирами со стрелками, указывающими направления движения потоков жидкого металла в процессе опорожнении емкости). Важно, что при описанной организации движения потоков металла исключают появления завихрения металла на входе в выпускное отверстие, так как отсутствует длительное горизонтальное перемещение потоков металла при подходе к входу в выпускное отверстие 7.
Свободное истечение жидкого металла 17 из чаши 2 емкости обеспечивают благодаря тому, что все перечисленные отверстия и зазоры по отдельности, в том числе образованные выступом h1 надставки 10 за пределы стержня 5, через которые проходят потоки металла на пути из чаши 2 емкости в выпускное отверстие 7, имеют площадь проходных сечений по меньшей мере равной, но в основном больше величины поперечного сечения выпускного отверстия 7. Таким образом, при реализации способа в конструкции предусмотрено выполнение условия (фиг.5, 7 и 10):

где d13 – диаметр поперечного сечения выступа 13 на соответствующем расстоянии от его торца.
При реализации условия (2) в последнем неравенстве сопоставляемых площадей проходных сечений обеспечивают по меньшей мере 4-кратное превышение сравниваемых площадей. Этим исключают влияние разряжающего действия струи металла, покидающего отверстие 7 емкости, на устойчивость процесса опорожнения. При необходимости учитывают влияние на выполнение условия (2) перемычек 9. Однако в конструкции предусматривают такой выбор размеров перемычек 9, что они незначительно влияют на выполнение условия (2).
По мере опорожнения чаши 2 емкости уровень металла 17 и шлака 18 непрерывно опускается ко дну 3 емкости, вплоть до наступления момента, когда в соответствии с условием (1) наступит равенство:

где h – в районе выпускного отверстия запас толщины слоя оставляемого металла в емкости, гарантирующий исключение попадания шлака в выпускное отверстие 7.
Как только наступит равенство (3), автоматически прекращается опорожнение чаши 2 емкости от основной части жидкого металла 17 с оставлением в чаше 2 емкости всего шлака толщиной h2 и меньшей части металла 17, высота слоя которого над уровнем донной поверхности 3 в районе входа в выпускное отверстие 7 составляет

Воздействие на значение hм осуществляют путем изменения высоты h надставки 10 и ее выступа h1 за пределы стержня 5. Этими изменениями компенсируют влияние плотности ш формируемого шлака 18 и высоты его слоя h2 на выполнение условий (3) и (4). При этом прогнозируют значения ш и h2 очередной (очередных) плавки исходя из химического состава шлака, необходимого для ведения плавки и получения требуемого химсостава и температуры жидкого металла 17. Изменение высоты h и значения h1 (в случае необходимости) осуществляют между плавками, при этом используют исполнение стержня 5 составным, со сменной нижней частью, включающей стаканоподобную полость 8 и закрепленную в ней надставку 10 (фиг.11). Замену нижней части стержня 5 выполняют вне рабочего пространства 1 емкости в течение времени, когда в рабочем пространстве 1 емкости осуществляют расплавление шихты (лома).
Таким образом, описанный процесс замены нижней части стержня 5 не влияет на продолжительность плавки.
Составной частью современной металлургии стала внепечная обработка жидкого металла, в частности в ковше, в который металл поступает из металлоплавильной емкости в соответствии с изложенным выше описанием.
Предлагаемый способ опорожнения металлоплавильной емкости от жидкого металла включает также выполнение приемов воздействия на химический состав металла в ковше путем введения соответствующих элементов в потоки жидкого металла, покидающего емкость, конкретно, в потоки металла, входящего в выпускное отверстие 7.
Для подачи элементов используют шланг 15 и центральное отверстие 14 в стержне 5. Подачу элементов сопровождают подачей инертного или нейтрального газа через шланг 16. При этом газ предварительно подогревают одним из уже рассмотренных приемов. При назначении температуры подогрева газа учитывают его разогрев в процессе прохождения отверстия 14 в стержне 5. В любом случае температуру газа на выходе из отверстия 14 в поток металла обеспечивают равной, но в основном ниже (на 100…200 град) температуры этого металла.
Подогревом газа исключают явление возможного разбрызгивания струи жидкого металла на пути его движения между выходом из выпускного отверстия 7 и входом в ковш. В случае подачи непрогретого газа происходит разбрызгивание указанной струи металла из-за резкого увеличения размеров пузырьков газа, нагреваемого жидким металлом.
В то же время подогревом газа не предусматривают подъема температуры металла, поэтому температуру газа обеспечивают на уже указанном уровне.
Наличие поперечных каналов 20 позволяет иметь над металлом в стаканоподобной полости 8 давление газа, по меньшей мере равное атмосферному. Исполнение поперечных каналов 20 наклонными с понижением от дна стаканоподобной полости 8 в сторону центрального отверстия 14 стержня 5 (фиг.10) облегчает поступление части газа из отверстия 14 в полость 8, в район дна полости. Наилучшие результаты опорожнения емкости обеспечивают, варьируя это давление с учетом опускания уровня металла 17 и шлака 18 по мере опорожнения емкости, при этом к концу опорожнения емкости давление газа принимают на 0,1…0,2 бара выше атмосферного. Причем под наилучшими результатами понимают минимальное влияние газов на процесс опорожнения емкости (на размер сечения струи металла, покидающего отверстие 7) при исключении заполнения металлом центрального отверстия 14 и возможного “козления” металла в этом отверстии.
Описанным наилучшим результатом опорожнения емкости в полной мере отвечает условие, когда давление газа на входе в центральное отверстие 14 стержня равно значению, обеспечивающему (с учетом разогрева в процессе прохождения стержня 5) давление газа на выходе из отверстия 14 несколько большим (на 0,1…0,2 бара) или равным давлению металла на торец выступа 13 стержня 5. Выполнение этого условия необходимого для исключения подъема металла 17 в отверстие 14. Этот подъем имеет место при давлении подаваемого газа меньше давления металла на торец выступа 13.
При реализации описанного способа используют устройства и способы, предотвращающие контакт металла, покидающего емкость, с окружающим воздухом, вплоть до выхода из выпускного отверстия 7; обеспечивают безопасность ведения процессов подготовки, хранения и транспортировки сыпучих материалов, вводимых в сталь.
Реализация настоящего способа при производстве в качестве жидкого металла стали предполагает решение задач десульфурации стали, ее дефосфорацию, безоксидацию, азотирование (или удаление азота), науглероживание, легирование различными элементами, удаление неметаллических включений и др., т.е. совокупность действий, обеспечивающих изменение химического состава стали в процессе ее разливки наряду с улучшением качества.
Важной экономической стороной предлагаемого способа является снижение расхода легирующих элементов при его реализации, особенно склонных к повышенному окислению (например, Al и др.).
Реализация настоящего способа применительно к жидкой стали предполагает работу со следующими элементами в основном в порошкообразном виде:
1) для десульфурации: CaSi, CaC2, CaCN2, CaAl, CaMg, CaSimg, Mg и др. При этом для реакции ошлаковывания возможны комбинации: СаО-CaF2; СаО-Al2О3; СаО-Al2О3-CaF2; СаО-Al; СаО-CaF2-Al; СаО-CaF2-CaSi; СаО-Mg; СаО-CaF2-Mg; СаО и др;
2) для дезоксидации (раскисления): CaSi; CaSiBa; CaSiMn; CaSiMnAl; CaSimgFe; Al и др.;
3) для модификации серы: CaSi; SiZr и др.;
4) для дефосфорации: СаО-CaF2-Fe2О3 в виде смеси;
5) для дезазотирования: FeZr; SiZr и др;
6) для легирования: Si с FeSi75; N с CaCN2 ( 55% CaCN2; 33% СаО; 12% С).
С графитовым порошком:
В с В2О3;
Ni с оксидами никеля;
Мо с оксидами молибдена.
Для ряда порошков из экономических соображений используют фракции:
CaSi – до 0,6 мм;
СаС2 – 0,1…0,6 мм;
CaMg – 0,1…1,5 мм.
При реализации настоящего способа соблюдают известные рекомендации по технике безопасности при работе с сыпучими материалами:
– не допускают возможность местной концентрации мелких фракций;
– исключают доступ открытого пламени, искр или брызг жидкого металла;
– исключают вероятность электростатических разрядов;
– не допускают увлажнения во время хранения и при транспортировке сыпучих материалов газом и др.
Особое внимание этим рекомендациям уделяют при подаче Al, Mg, CaSi и CaC2, в этих случаях в качестве газа используют только Ar.
При реализации настоящего способа учитывают, что ряд порошковых материалов при размере частиц <0,2 мм (и даже 0,5 мм) имеют склонность к образованию взрывоопасных смесей. Реализация настоящего способа невозможна без строго соблюдения известных правил и накопленного опыта по работе с сыпучими материалами, использованием и соблюдением которых гарантируют безопасность осуществления способа.
Меньшую часть оставляемого в чаше 2 металлоплавильной емкости жидкого металла 17 используют для ускорения реализации следующей плавки, перед началом которой емкость возвращают в исходное положение (если осуществляли поворот емкости для ее опорожнения), закрывают выпускное отверстие пробкой 19 (в ряде случаев засыпают основную часть выпускного отверстия 7 сухим песком), поднимают стержень 5 в безопасное от загружаемой в чашу 2 шихты (лома) положение (на фиг.1 положение “Д”), загружают чашу 2 шихтой и осуществляют новую плавку.
В случае остановки работы металлоплавильной емкости, например, на ремонт чашу 2 освобождают также от меньшей части металла 17 и всего шлака 18, оставленных в чаше 2. Для реализации этой операции емкость дополнительно поворачивают и увеличивают слой металла в районе выпускного отверстия. Далее используют уже описанные условия выполнения равенства (3). Поэтому вначале при сохранении стержня 5 в прижатом ко дну 3 состоянии надставки 10 и открытом выпускном отверстии 7 опорожняют емкость от оставшегося металла. Затем при открытом выпускном отверстии 7 отводят стержень 5 от донной поверхности 3 емкости и в отдельный сосуд (ковш) выпускают из емкости весь шлак 18 и металл 17, толщина слоя которого равна h1+ h. При этом благодаря дополнительному повороту емкости существенно уменьшают объем металла 17, выпускаемого вместе со шлаком 18. Тем самым минимизируют попадание в металл шлака металлоплавильной емкости, т.е. минимизируют потери металла.
В процессе реализации предлагаемого способа опорожнения металлоплавильной емкости от основной части жидкого металла путем переливания металла в ковш с использованием предлагаемой емкости для осуществления этого способа осуществляют следующую последовательность основных операций (фиг.12, где двойной линией обозначены альтернативные приемы выполнения способа):
– перед открытием выпускного отверстия и началом опорожнения емкости от основной части металла опускают стержень с надставкой до плотного без зазоров прилегания торцевой поверхности надставки к донной поверхности емкости, оппозитно выпускному отверстию в этой части донной поверхности, через центральное отверстие в стержне прокачивают инертный или нейтральный газ через металл и шлак, заполнившие зазоры и отверстия стержня и надставки при указанном их опускании, открывают выпускное отверстие и осуществляют опорожнение емкости, при этом в процессе опорожнения через центральное отверстие в стержне в поток металла, проходящий через отверстие в надставке, подают элементы, воздействующие на химический состав жидкого металла в ковше, и эту подачу элементов сопровождают подачей нейтрального или инертного газа, нагретого к моменту входа в металл до температуры, близкой к температуре металла, а сам процесс опорожнения емкости автоматически прекращается при выполнении условия
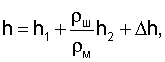
где h – высота надставки; h1 – высота выступа надставки за пределы стержня; h2 – наибольшая высота слоя шлака над металлом в конце выпуска металла; м и ш – удельный вес металла и шлака соответственно, h – в районе выпускного отверстия запас толщины слоя оставляемого металла в емкости, причем меньшую часть металла и весь шлак оставляют в емкости или, при необходимости полного опорожнения емкости, выпускное отверстие 7 оставляют открытым, надставка 10 прижата ко дну 3 емкости, которую (при наличии привода поворота) дополнительно поворачивают, меньшую часть металла 17 выпускают из емкости через выпускное отверстие 7. При открытом выпускном отверстии 7 отводят стержень 5 от донной поверхности 3 и в отдельный ковш выпускают весь шлак 18 и оставшийся металл 17, толщина слоя которого равна h1+ h.
Таким образом, при реализации настоящего способа осуществляют опорожнение емкости от основной части жидкого металла с переливанием этого металла в ковш с гарантированным исключением попадания печного шлака в металл в ковше. При этом в процессе опорожнения емкости от жидкого металла в потоки металла, покидающего емкость, подают совместно с инертным или нейтральным газом все необходимые и достаточные элементы для получения в ковше металла заданного химического состава.
Экономическая эффективность предложенного способа опорожнения металлоплавильной емкости от основной части металла и конструкция емкости для его осуществления проявляется в повышении качества металла за счет гарантированного исключения попадания шлака металлоплавильной емкости в ковш, в оперативной внепечной обработке металла в ковше, в снижении расхода легирующих элементов.
Пример. Холодная модель (фиг.13 и 14) содержит емкость с рабочим пространством 1 и единую с ней чашу 2, стержень 5 со стаканоподобной полостью 8, в которой по центру жестко на перемычках 9 закреплена надставка 10 со сквозным отверстием, состоящим из конической 11 и цилиндрической 12 частей. Диаметр цилиндрического отверстия 12 имеет размер d1=40 мм. В дне 3 чаши 2 выполнено выпускное отверстие 7 диаметром d=19 мм. Таким образом d1=2,1 d. Выпускное отверстие 7 закрыто пробкой 19. Надставка 10 выступает за пределы стержня 5 на h1=9 мм. Высота надставки 10 от дна 3 чаши равна h=26 мм, ее наружный диаметр равен d2=45 мм. Внутренний диаметр полости 8 равен d3=70 мм, расстояние между верхним торцом надставки 10 и дном полости 8 составляет h3=30 мм. Стержень 5 диаметром 25 мм имеет конический выступ 13, торец которого расположен ниже верхнего торца надставки 10 и входит по меньшей мере в коническое отверстие 11. По центру стержня 5 выполнено сквозное отверстие 14 диаметром 10 мм; на уровне дна полости 8 сквозное отверстие 14 имеет поперечные каналы 20. В верхней части стержня 5 расположена воронка 21, к которой подводится воздух через шланг 16. Давление воздуха может варьироваться. Воздух подводили также в центральное отверстие 14. Сверху полость воронки 21 плотно закрыта крышкой 25, через которую проходит стержень 22 с пробкой 23. Воронка 21 наполнена сыпучим материалом 24 (опилки; сахар; соль), окрашенным в красный цвет и просушенным. Чаша 2 выполнена из оргстекла и имеет размеры, приведенные на фиг.13 и 14, обеспечивающие вместимость 56 литров жидкости. В качестве ковша, в который опорожняли чашу 2 через выпускное отверстие, применили сосуд, выполненный из оргстекла, с размерами по ширине 300 мм, по длине 450 мм и по высоте 400 мм. Стержень 5 с надставкой 10 и воронкой 21 имеет возможность свободного перемещения в вертикальном направлении, что отмечено стрелками Е на фиг.13.
В чашу 2 наливали холодную воду в объеме 45 литров, которая имитировала жидкий металл 17. Сверху на воду наливали подкрашенный в зеленый цвет керосин толщиной h2=7 мм (около одного литра), который имитировал шлак 18. Плотность воды м=1,0 г/см3, плотность керосина 0,8 г/см3.
При указанном наполнении чаши 2 пробка 19 закрывала выпускное отверстие 7 и стержень 5 поднят выше уровня слоя керосина 18.
Перед началом опорожнения чаши 2 в воду 17 и керосин 18 опускали стержень 5, непрерывно подавая через шланг 16 от воздушной станции воздух давлением на 0,2 бара выше атмосферного (расход воздуха варьировали от 5 до 40 л/мин). Крышка 25 плотно закрывала воронку 21. Подачу воздуха сохраняли после плотного прилегания нижнего торца Ж надставки 10 ко дну 3 чаши 2 (фиг.13). Имели барботаж воды 17 и керосина 18. Описанным приемом исключали наличие керосина 18 в зазорах стаканоподобной полости 8 и в отверстии 14, попадание которых имело место при опускании стержня 5.
Удаляли пробку 19 и одновременно стержнем 22 поднимали пробку 23 и через выпускное отверстие 7 опорожняли чашу 2 от основной части воды 17.
В результате процесс опорожнения чаши 2 сопровождался включением в потоки воды 17, покидающей чашу 2 (на фиг.13 направление потоков отмечено пунктирными линиями со стрелками) через выпускное отверстие 7, сухого подкрашенного сахарного песка 24 (на фиг.13 отмечено линией со стрелкой, выходящей из отверстия 14), при этом песок 24 начинал смешиваться с водой 17 и растворяться в ней в момент входа потоков воды в отверстие 11, и процесс их смешивания и растворения продолжался при прохождении отверстия 12 выпускного отверстия 7 и в потоке воды, падающей в сосуд, имитирующий ковш.
Благодаря выполнению в конструкции системы: чаша 2, стержень 5, стаканоподобная полость 8 и надставка 10 и реализации описанных приемов опорожнения чаши 2 процесс опорожнения чаши 2 автоматически прекращался, в чаше 2 оставался весь керосин 18 и меньшая часть воды 17, толщина слоя которой согласно уравнению (4) составила:

При этом сахарный песок (аналогично соль) в процессах указанного перемешивания и растворения практически равномерно в течение 10…15 сек после начала опорожнения чаши 2 окрашивал в красный цвет весь объем воды в сосуде, имитирующем ковш. Последнее свидетельствует о равномерном распределении и растворении сахара (соли) в воде в процессе описанного опорожнения чаши 2 от воды и ее переливания в сосуд, имитирующий ковш.
Формула изобретения
1. Способ опорожнения металлоплавильной емкости от основной части жидкого металла через выпускное отверстие в донной поверхности емкости, включающий опускание потоков металла, покидающего емкость, ниже уровня его входа в выпускное отверстие, вплоть до донной поверхности в этой части емкости, последующее перемещение вдоль донной поверхности и подъем этих потоков металла до и выше уровня входа в выпускное отверстие и выпуск металла через это отверстие, при этом опускающиеся и поднимающиеся потоки металла разделены стенкой, между торцом которой и донной поверхностью емкости предусмотрен зазор, связывающий опускающиеся и поднимающиеся потоки металла, отличающийся тем, что перед началом опорожнения емкости поднимают уровень входа металла в выпускное отверстие над исходным его положением в донной поверхности емкости и сохраняют поднятое положение до окончания опорожнения емкости от основной части металла, при этом потоки уходящего металла отделяют от поднимающихся потоков металла стенкой, высота которой определяет величину подъема уровня входа металла в выпускное отверстие, а после того как процесс опорожнения прекратится, восстанавливают исходное положение уровня этого входа, оставляя в емкости меньшую часть металла.
2. Способ по п.1, отличающийся тем, что в потоки металла, входящие в выпускное отверстие, подают элементы, воздействующие на химический состав жидкого металла, при этом подачу осуществляют с одновременной подачей в эти потоки металла инертного или нейтрального газа.
3. Способ по п.2, отличающийся тем, что подачу элементов в жидкий металл осуществляют ниже поднятого уровня входа в выпускное отверстие.
4. Способ по п.2, отличающийся тем, что осуществляют предварительный подогрев инертного или нейтрального газа.
5. Способ по п.1, отличающийся тем, что до начала опорожнения емкости прокачивают инертный или нейтральный газ через металл, расположенный над выпускным отверстием и в зазорах, предназначенных для прохода металла из емкости в выпускное отверстие, при этом после окончания прокачивания давление газа сохраняют до начала выпуска металла.
6. Способ по п.1, отличающийся тем, что перед загрузкой емкости шихтой устройство, обеспечивающее подъем уровня входа металла в выпускное отверстие, выводят за пределы возможного контакта устройства с шихтой.
7. Металлоплавильная емкость, содержащая фигурную в плане чашу с выпускным отверстием в ее донной поверхности, сверху изолированную от окружающей среды с образованием рабочего пространства, отличающаяся тем, что она снабжена имеющим возможность осевого перемещения стержнем из огнеупорного материала, расположенным оппозитно выпускному отверстию, верхний конец которого расположен вне рабочего пространства емкости, и от привода стержень имеет возможность осевого перемещения в сторону дна емкости, а нижний конец стержня выполнен в форме стаканоподобной полости, в которой на перемычках жестко закреплена по центру стержня надставка, установленная с зазорами между соответствующими зеркальными поверхностями полости и надставки, при этом надставка выполнена с центральным сквозным отверстием, поверхность ее торца выступает за пределы стержня и очертания этой поверхности повторяют очертания донной поверхности в районе входа в выпускное отверстие, при этом высота надставки равна величине подъема уровня входа металла в выпускное отверстие, а все перечисленные отверстия и зазоры по отдельности, предназначенные для прохода металла из емкости в выпускное отверстие, имеют проходные сечения, по меньшей мере равные поперечному сечению выпускного отверстия.
8. Металлоплавильная емкость по п.7, отличающаяся тем, что стержень на участке верхний торец – дно стаканоподобной полости имеет сквозное центральное отверстие.
9. Металлоплавильная емкость по п.7, отличающаяся тем, что высота надставки определена из следующего соотношения
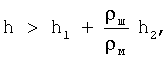
где h – высота надставки; h1 – высота выступа надставки за пределы стержня; h2 – предполагаемая наибольшая высота слоя шлака над металлом в конце выпуска металла из емкости; м и ш – удельный вес металла и шлака соответственно.
10. Металлоплавильная емкость по п.7, отличающаяся тем, что в нижнем положении стержень плотно без зазоров прилегает выступом надставки к поверхности дна емкости.
11. Металлоплавильная емкость по п.7, отличающаяся тем, что вход в выпускное отверстие в донной поверхности емкости выполнен в виде отверстия с конической поверхностью и оппозитно надставка снабжена выступом с зеркальной конической поверхностью к этому отверстию.
12. Металлоплавильная емкость по п.7, отличающаяся тем, что стержень имеет возможность продольного перемещения для вывода надставки в верхнюю часть рабочего пространства емкости, в которой исключен контакт надставки с шихтой.
13. Металлоплавильная емкость по п.7, отличающаяся тем, что стаканоподобная полость в центре дна выполнена с выступом, от торца которого до верхней части стержня выполнено центральное сквозное отверстие, соединенное гибкими шлангами с устройствами для подачи твердых материалов разной фракции и инертного или нейтрального газа, при этом на уровне дна стаканоподобной полости это отверстие посредством поперечных каналов дополнительно соединено с этой полостью.
14. Металлоплавильная емкость по п.13, отличающаяся тем, что поперечные каналы выполнены наклонными с понижением от дна стаканоподобной полости в сторону центрального отверстия стержня.
15. Металлоплавильная емкость по п.7, отличающаяся тем, что ось стержня перпендикулярна поверхности дна емкости в районе выпускного отверстия.
16. Металлоплавильная емкость по п.7, отличающаяся тем, что ось стержня отклонена от вертикали на угол от оси выпускного отверстия, при этом обе оси расположены на одной прямой.
17. Металлоплавильная емкость по п.7, отличающаяся тем, что сквозное отверстие в надставке состоит из конической и цилиндрической частей для выхода металла, при этом коническая часть является входной, а цилиндрическая – выходной, а диаметр цилиндрической части по меньшей мере равен диаметру выпускного отверстия.
18. Металлоплавильная емкость по п.7, отличающаяся тем, что нижняя часть стержня, включающая стаканоподобную полость и закрепленную в ней надставку, выполнена сменной, при этом для смены нижней части стержень снабжен возможностью вывода за пределы рабочего пространства емкости.
РИСУНКИ
|
|