|
(21), (22) Заявка: 2005115622/02, 23.05.2005
(24) Дата начала отсчета срока действия патента:
23.05.2005
(46) Опубликовано: 10.02.2007
(56) Список документов, цитированных в отчете о поиске:
RU 2104450 C1, 10.02.1998. RU 2048662 C1, 20.11.1995. US 4577326 А, 18.03.1986.
Адрес для переписки:
455048, Челябинская обл., г. Магнитогорск, ул. Завенягина, 1, кв.337, И.В. Портновой
|
(72) Автор(ы):
Ячиков Игорь Михайлович (RU), Морозов Александр Прокопьевич (RU), Портнова Ирина Васильевна (RU)
(73) Патентообладатель(и):
Ячиков Игорь Михайлович (RU)
|
(54) СПОСОБ ЭЛЕКТРОПЛАВКИ В ДУГОВОЙ ПЕЧИ ПОСТОЯННОГО ТОКА
(57) Реферат:
Изобретение относится к области электрометаллургии и может быть использовано для нагрева, плавки, рафинирования и легирования черных и цветных металлов, для плавки шлаков и флюсов, а также для перемешивания их расплавов в миксерах, печах-ковшах и агрегатах комплексной доводки сплавов. Управление параметрами дуги и источника электропитания осуществляют наложением пульсаций на общий ток дуги и подачей в межэлектродный промежуток пульсирующего потока плазмообразующего газа через сквозное осевое отверстие в сводовом электроде, причем частоты пульсаций общего тока дуги и потока плазмообразующего газа выбирают в диапазоне 0,1-10 Гц и принимают равными десятикратной частоте изменения величин токов в замкнутых электрических цепях между сводовым и подовыми электродами, а в период легирования в пульсирующий поток плазмообразующего газа вводят порошкообразные лигатуры через сводовый электрод. Изобретение обеспечивает интенсивное и полное перемешивание во всем объеме и на поверхности ванны расплава, уменьшает тепловые нагрузки на подовые электроды с увеличением их надежности и срока службы, что позволяет уменьшить время на осуществление отдельных стадий обработки расплава и увеличить межремонтную кампанию печи. 1 табл., 2 ил.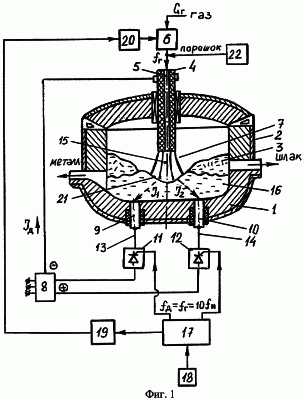
Изобретение относится к области электрометаллургии, в частности к способам переплавки или рафинирования в электрической дуге, конкретно в дуговых печах постоянного тока, и может быть использовано для нагрева, плавки, рафинирования и легирования черных и цветных металлов и сплавов, для плавки шлаков и флюсов, а также для перемешивания их расплавов в миксерах, печах-ковшах и агрегатах комплексной доводки сплавов.
Известен способ электроплавки в дуговой печи постоянного тока, включающий загрузку печи, расплавление шихты за счет прохождения тока между сводовым и подовыми электродами, рафинирование и легирование образующегося расплава при перемешивании за счет пропускания тока по замкнутым электрическим цепям между сводовым и подовыми электродами с возбуждением в расплаве поля электромагнитных сил, периодическое изменение величины тока с регламентированной частотой и со сдвигом фаз в каждой цепи, с одновременным изменением поля электромагнитных сил, прекращение прохождения тока через расплав, слив расплава (см. пат. РФ №2048662, F 27 В 3/08, С 22 В 9/21, 1995).
Недостатком известного способа электроплавки является ограничение возможности повышения производительности, связанное с тем, что в процессе перемешивания расплава образуются застойные слабоперемешиваемые области в поверхностных слоях, удаленных от центра ванны. Наличие застойных зон уменьшает полноту перемешивания и ухудшает однородность химического состава металла во всем объеме ванны. Интенсивность перемешивания только за счет изменения поля электромагнитных сил в расплаве лимитирована значительными токовыми нагрузками на подовые электроды, которые приводят к их преждевременному износу и размыванию расплавом футеровки в области подовых электродов, а также к ограничению требуемой мощности дугового разряда, что снижает возможность повышения производительности электроплавки. Кроме того, по данному способу электроплавки в периоды рафинирования и легирования расплава различие физических свойств материалов, составляющих шихту, а также шлака и лигатур, приводит к тому, что при переключении с одной замкнутой цепи на другую наблюдаются значительные плотности тока в расплаве непосредственно над подовыми электродами, через которые протекает ток. Поэтому в этих областях образуются сильные струи и локальные вихри перегретого расплава, направленные из-под пятна дугового разряда на подину и резко увеличивающие тепловые нагрузки на подовые электроды, что снижает срок их службы и, в целом, производительность дуговой печи. При реализации данного способа электроплавки увеличивается площадь контакта расплава с подовыми электродами, что повышает возможность попадания в расплав частиц от разрушения подовых электродов в виде неконтролируемых примесей и их взаимодействие с легирующими присадками с ухудшением качества выплавляемого металла. Для удаления вредных примесей необходимо дополнительное время на рафинирование, приводящее к снижению общей производительности.
Наиболее близким к предлагаемому изобретению является способ электроплавки в дуговой печи постоянного тока, включающий загрузку шихты в печь и создание электрического контакта между сводовым электродом и шихтой. При включении источника электропитания идет плавление шихты дугой при протекании общего тока через замкнутые электрические цепи, включающие сводовый электрод, межэлектродный промежуток, шихту, образующийся расплав, подовые электроды с токоподводами и источник электропитания. При управлении параметрами дуги и источника электропитания осуществляется нагрев, рафинирование и легирование расплава с его перемешиванием, которое происходит за счет возбуждения в расплаве поля электромагнитных сил от протекания тока через расплав. Периодическое изменение величины тока происходит в замкнутых электрических печах с регламентированной частотой и с соответствующим увеличением интенсивности поля электромагнитных сил в расплаве (см. пат. РФ 2104450, F 27 В 3/08, С 22 В 9/21, 1998).
Недостатком известного способа является то, что повышение производительности электроплавки путем интенсификации перемешивания возможно только при повышении силы тока дуги или увеличении количества подовых электродов для создания силовых воздействий силы тока на расплав. Однако интенсивность перемешивания за счет увеличения силы тока лимитирована значительными токовыми нагрузками на подовые электроды, что приводит к их преждевременному износу и размыванию расплавом футеровки в области подовых электродов, а также к ограничению требуемой мощности дугового разряда и производительности обработки. При этом в период расплавления шихты на подине печи и на периферии ванны расплава в течение длительного времени остаются куски непроплавившейся шихты из-за низкой интенсивности процессов тепломассообмена в этот период, что снижает производительность печи. Поэтому интенсификация перемешивания по известному способу реализуется только при увеличении количества подовых электродов, но при этом увеличивается площадь контакта расплава с подовыми электродами, что повышает возможность попадания частиц от их разрушения в расплав в виде вредных примесей и требует дополнительного времени на рафинирование, приводящее к снижению производительности электроплавки. Увеличение количества подовых электродов повышает время простоя печи, связанное с их ремонтом и заменой, снижает надежность работы подины и повышает вероятность прорыва металла из печи, что также снижает производительность процесса электроплавки. Переключение дуги на замкнутые цепи между сводовым и подовыми электродами снижает стабильность горения дуги и приводит к неравномерному износу сводового электрода и футеровки печи, что дополнительно снижает производительность печи.
Задачей, на решение которой направлен заявляемый способ, является повышение производительности печи при постоянстве вводимой мощности за счет интенсификации процесса перемешивания расплава.
Технический эффект от использования предлагаемого способа достигается обеспечением интенсивного и полного перемешивания во всем объеме и на поверхности ванны расплава. Также уменьшаются тепловые нагрузки на подовые электроды с увеличением их надежности и срока службы. В целом, комплексное перемешивание и снижение нагрузки на подовые электроды обеспечивают уменьшение необходимого времени на осуществление отдельных стадий обработки расплава и увеличение межремонтной кампании печи, что повышает производительность электроплавки.
Поставленная задача решается тем, что в известном способе электроплавки, включающем загрузку шихты в печь, создание электрического контакта между сводовым электродом и шихтой, включение источника электропитания, плавление шихты дугой при протекании общего тока через замкнутые электрические цепи, включающие сводовый электрод, межэлектродный промежуток, шихту, образующийся расплав, подовые электроды с токоподводами и источник электропитания, управление параметрами дуги и источника электропитания, нагрев, рафинирование и легирование расплава с его перемешиванием за счет возбуждения в расплаве поля электромагнитных сил от протекания тока через расплав, периодическое изменение величины тока в замкнутых электрических цепях с регламентированной частотой и с соответствующим увеличением интенсивности поля электромагнитных сил в расплаве, управление параметрами дуги и источника электропитания осуществляют наложением пульсаций на общий ток дуги и подачей в межэлектродный промежуток пульсирующего потока плазмообразующего газа через сквозное осевое отверстие в сводовом электроде, причем частоты пульсаций общего тока дуги и потока плазмообразующего газа выбирают в диапазоне 0,1-10 Гц и принимают равными десятикратной частоте изменения величин токов в замкнутых электрических цепях между сводовым и подовыми электродами, а в период легирования в пульсирующий поток плазмообразующего газа вводят порошкообразные лигатуры через сводовый электрод.
Известно наложение пульсаций на ток дуги в способах термообработки и сварки металлов (см. Вагнер Ф.А. Оборудование и способы сварки пульсирующей дугой. – М.: Энергия, 1980. – 180 с.). При этом организация пульсирующего тока дуги предназначена для улучшения качества сварочного шва и уменьшения термонапряжений в свариваемом металле.
В предлагаемом способе электроплавки наложение пульсаций на ток дуги предназначено для обеспечения полноты перемешивания металла на поверхности и в объеме расплава. Это позволяет интенсифицировать процессы тепло- и массообмена между дугой и ванной расплава и повысить производительность электроплавки.
Известно использование пульсирующего потока плазмообразующего газа при обработке расплавов (см. Семкин И.Г., Коптев А.П., Морозов А.П. Внепечная плазменная металлургия. – Магнитогорск: МГТУ, 2000. – С.315-321). При этом пульсирующая плазменная продувка позволяет увеличить площадь межфазной границы высокотемпературный газ – расплав за счет более эффективного диспергирования последнего, а также ускорить химические процессы рафинирования и легирования.
В предлагаемом способе электроплавки применение дополнительной подачи через сводовый электрод, выполненный со сквозным осевым отверстием, в межэлектродный промежуток пульсирующего потока плазмообразующего газа, наряду с известными эффектами, позволяет увеличить скорость гетерогенных металлургических процессов, лимитированных массопереносом через ламинарный пограничный слой. В этих условиях обеспечивается непрерывная турбулизация пограничного слоя, а следовательно, и минимальное сопротивление для подвода реагентов к металлу и отводу газообразных продуктов реакций рафинирования, с увеличением степени использования реагентов и повышением производительности электроплавки.
Отличительные признаки, характеризующие подачу через сводовый электрод пульсирующего потока плазмообразующего газа в смеси с порошкообразными лигатурами, в известных технических решениях не обнаружены. Такая организация ввода лигатур обеспечивает эффективный нагрев и плавление частиц с повышением степени их усвоения и снижением времени перемешивания на усреднение химического состава металла за счет пульсаций в зоне растворения, что повышает производительность электроплавки.
Отличительные признаки, характеризующие поддержание частот пульсаций общего тока дуги и потока плазмообразующего газа в диапазоне 0,1-10 Гц, равных десятикратной частоте изменения величины тока в замкнутых цепях между сводовым и подовыми электродами, в известных технических решениях не обнаружены. При такой организации процесса электроплавки возникают резонансные явления от взаимодействия потоков с поверхности ванны и приходящих из объема расплава, генерируемых при совместном действии пульсаций тока дуги, пульсирующего потока плазмообразующего газа и переменного поля электромагнитных сил. В таком резонансном режиме достигается сверхэффект по интенсификации процесса перемешивания расплава и повышается производительность электроплавки.
Сущность изобретения поясняется чертежами, где на фиг.1 изображена схема дуговой печи постоянного тока; на фиг.2 – диаграммы изменения основных параметров электроплавки.
Способ электроплавки в дуговой печи постоянного тока осуществляется следующим образом.
На подину 1 (фиг.1) печи 2 загружают шихту 3. Через сводовый электрод 4 со сквозным осевым отверстием 5 с помощью электромеханического пульсатора 6 подают пульсирующий поток газа в межэлектродный промежуток 7. Сводовый электрод 4 опускают вниз до возникновения электрического контакта между ним и шихтой 3. Включают источник электропитания 8 с подачей напряжения на сводовый электрод 4 и на подовые электроды 9 и 10, ориентированные в горизонтальной плоскости под углом друг к другу, через регуляторы тока 11 и 12 (например, тиристорные) и токоподводы 13 и 14, расположенные под подиной 1 печи 2. Плавление шихты 3 осуществляют дугой 15, возникающей при протекании тока через по крайней мере две замкнутые электрические цепи, включающие сводовый электрод 4, межэлектродный промежуток 7, шихту 3, образующийся расплав 16, подовые электроды 9 или 10, токоподводы 13 или 14, регуляторы тока 11 или 12, и источник электропитания 8. Рафинирование расплава 16 проводят наведением шлака на его поверхности, а легирование – введением лигатур. Нагрев, рафинирование и легирование расплава 16 проводят одновременно с его перемешиванием, осуществляемым тремя методами. Во-первых, перемешивание расплава 16 происходит при возникновении двух замкнутых цепей (по числу подовых электродов 9 и 10). Первую цепь образуют источник электропитания 8, сводовый электрод 4, дуга 15, расплав 16, подовый электрод 9, токоподвод 13 и регулятор тока 11. Вторую цепь образуют те же источник электропитания 8, сводовый электрод 4, дуга 15, расплав 16, а также подовый электрод 10, токоподвод 14 и регулятор тока 12. При наличии нескольких (более двух) подовых электродов 9 и 10 и, соответственно, нескольких замкнутых электрических цепей, изменение тока в них производится со сдвигом фаз в каждой цепи относительно других. В соответствии с выбранной частотой (fи) регуляторы 11 и 12 изменяют токи, проходящие через подовые электроды 9 (I1) и 10 (I2), в течение всего времени горения дуги 15, в том числе во время расплавления шихты 3 и образования и перемешивания расплава 16, с амплитудой изменения, соответственно, I1max-I1min и I2max-I2min (фиг.2). Управление изменением тока на регуляторах тока 11 и 12 осуществляется с помощью микропроцессорного блока управления 17, регулируемого блоком задания 18. При этом в каждый момент времени ток (Iд), протекающий через расплав 16, равен сумме токов (I1+I2), проходящих через подовые электроды 9 и 10. Причем токи в расплаве 16, взаимодействуя с собственным магнитным полем, возбуждают поле электромагнитной силы, которое периодически меняется во времени, в соответствии с изменением тока в подовых электродах 9 и 10. Меняющееся поле электромагнитных сил приводит к возникновению в расплаве 16 периодически изменяющихся гидродинамических течений, которые существуют в течение всего времени горения дуги 15 и обеспечивают перемешивание. Второй метод перемешивания осуществляется подачей пульсирующего потока плазмообразующего газа в дугу 15 через сквозное отверстие 5 в сводовом электроде 4 с помощью электромеханического пульсатора 6. Регулирование частоты (fг) пульсаций потока плазмообразующего газа осуществляется подачей управляющего сигнала с микропроцессорного блока управления 17 через формирователь импульсов 19 на исполнительный механизм 20 электромеханического пульсатора 6. Амплитуда изменения расхода газа Gг задается в диапазоне Gг max-Gг min (Фиг.2). Пульсирующий поток плазмообразующего газа нагревается в дуге 15 и оказывает газодинамическое воздействие на расплав 16 с образованием колеблющейся лунки 21 и поверхностных потоков, обеспечивающих эффективное перемешивание верхних слоев расплава 16. Третий метод перемешивания осуществляется наложением пульсаций на общий ток дуги 15, предпочтительно с крутым фронтом импульса, например прямоугольным. Изменение частоты (Iд) и амплитуды пульсаций общего тока (Iд max-Iд min) производится регуляторами тока 11 и 12, соединенных с источником электропитания 8 при помощи микропроцессорного блока 17. Пульсирующая дуга 15 оказывает электродинамическое переменное силовое воздействие на расплав 16, складывающееся из скоростного напора потока плазмы, действующего на поверхности лунки 21 в дуговом пятне, и объемной электромагнитной силы, что в сумме обеспечивает дополнительное перемешивание расплава 16. Для повышения производительности электроплавки путем интенсификации перемешивания плавление, нагрев, рафинирование и легирование расплава 16 осуществляют поддерживанием частот пульсаций тока дуги 15 (Iд) и потока плазмообразующего газа (fг), подаваемого через сквозное отверстие 5 сводового электрода 4, десятикратных частоте (fи) изменения величины тока в замкнутых цепях между сводовым электродом 4 и подовыми электродами 9 и 10, т.е. fд=fг=10fи. При этом наблюдаются резонансные явления от совпадения частот fд и fг и стохастического совпадения с ними гармонических составляющих токов I1 и I2, что приводит к взаимодействию объемных и поверхностных потоков расплава 16, генерируемых тремя методами, с получением сверхэффекта по интенсификации процесса перемешивания расплава 16. В зависимости от емкости печи 2, геометрии ванны расплава 16, его электрофизических свойств, номинального значения величины общего тока Iд, максимально допустимой величины длительности одного периода изменения тока и (фиг.2), протекающего через расплав 16, подбирается оптимальная частота fи изменений тока Iд в цепях сводового электрода 4 и подовых электродов 9 и 10 и, соответственно, частоты пульсаций тока fд и плазмообразующего газа fг. Поддержание оптимальной частоты осуществляется блоком задания 18 в диапазоне 0,1-10 Гц. Регулирование частот изменения тока в замкнутых электрических цепях (fи), пульсаций тока (fд) и плазмообразующего газа (fг) предпочтительно в синфазном режиме их изменения. На диаграмме изменения во времени основных параметров электроплавки (фиг.2), построенной для примера при оптимальных частотах, равных 1,0 Гц, показан характер пульсаций расхода плазмообразующего газа Gг и мгновенного значения общего тока Iд в зависимости от изменения величин средних значений тока в замкнутых электрических цепях между сводовым электродом 4 (фиг.1) и, соответственно, подовыми электродами 9 (I1) и 10 (I2). Амплитуда пульсаций общего тока Iд max-Iд min (фиг.2) может быть задана в диапазоне 30-80% от его номинального значения. В период легирования через отверстие 5 (фиг.1) в сводовом электроде 4 с помощью питателя 22 подают в потоке пульсирующего плазмообразующего газа порошкообразную лигатуру. В дуге 15 происходит нагрев и плавление порошка с эффективным усвоением и перемешиванием в расплаве 16. Дальнейшее перемешивание расплава 16 продолжают до получения заданного химического состава. После этого отключают источник электропитания 8, прекращают подачу плазмообразующего газа через сводовый электрод 4, скачивают шлак и сливают готовый расплав 16. В целом, предлагаемый способ повышает производительность печи за счет равномерного по всему объему перемешивания расплава 16, а также устраняет образование устойчивых локальных вихрей над подовыми электродами 9 и 10 и направленной гидродинамической струи в расплаве 16 из дугового пятна дуги 15 на подину 1, что уменьшает износ подовых электродов 9 и 10 и футеровки подины 1 с увеличением их межремонтной кампании. Для интенсификации основных технологических процессов электроплавки рекомендуется использовать наложение пульсаций на ток дуги 15 и поток плазмообразующего газа с максимально возможными коэффициентами модуляции, с частотой пульсации до 10 Гц и скважностью импульсов, равной двум. Таким образом, наложение вынужденных пульсаций на параметры дуги 15 и на поток плазмообразующего газа, подаваемого через сквозное осевое отверстие 5 в сводовом электроде 4, с частотами в диапазоне 0,1-10 Гц, принятыми равными десятикратной частоте изменения величины тока в замкнутых цепях между сводовым 4 и подовыми электродами 9 и 10, оказывает интенсифицирующее воздействие на процессы тепломассопереноса между дугой 15 и компонентом шихты 3, а также на перемешивание ванны расплава 16, и повышает производительность электроплавки.
Пример осуществления способа
Проводили испытания предложенного способа электроплавки на лабораторной дуговой печи постоянного тока емкостью 20 т. Средний ток дуги 15 устанавливался на уровне 16 кА; среднее напряжение источника электропитания 8, реализуемое на дуге 15, поддерживалось 600 В; средняя активная мощность, подводимая к печи – 9,6 МВт. Периодическое изменение токов I1 и I2, протекающих поочередно через два подовых электрода 9 и 10, осуществлялось с частотой в диапазоне 0,01-1,0 Гц с помощью регуляторов тока 11 и 12, управляемых от блока задания 18 и микропроцессорного блока управления 17, например контроллера фирмы Simens. В качестве регуляторов 11 и 12 использовались автоматические тиристорные переключатели. Подовые электроды 9 и 10 сдвинуты от оси сводового графитового электрода 4 и находятся под некоторым гулом между собой. В процессе электроплавки проводилось плавление стальной шихты 3, нагрев расплава 16 до температуры 1690°С, его рафинирование путем десульфурации основным шлаком и легирование за счет введения в расплав 16 неазотированного ферромарганца, который подавался в виде порошка со средним диаметром частиц 0,5-1,0 мм, транспортируемого пульсирующим потоком плазмообразующим газом через отверстие 5 в сводовом электроде 4. Для получения пульсаций газа использовался электромеханический пульсатор 6 дискового типа с мощностью двигателя 20-3 кВт, а для генерации пульсаций тока дуги 15 – тиристорные регуляторы частоты 11 и 12. Частота пульсаций тока дуги 15 и потока плазмообразующего газа поддерживалась блоком задания 18 в диапазоне 0,1-10 Гц, десятикратной частоте изменения величины тока, протекающего в замкнутых цепях между сводовым 4 и подовыми электродами 9 и 10. Наложение пульсаций на ток дуги 15 и подача плазмообразующего газа через сводовый электрод 4 увеличивают степень турбулизации на поверхности и внутри ванны расплава 16, с образованием стоячих волн, идущих от пульсирующей лунки 21 и отраженных от границ ванны. При этом наложение пульсаций на ток дуги 15 и подача пульсирующего потока плазмообразующего газа через полый сводовый электрод 4 с частотами пульсаций, равных десятикратной частоте изменения величины тока в замкнутых электрических цепях между сводовым электродом 4 и подовыми электродами 9 и 10, приводит к возникновению резонанса между стоячими волнами на поверхности ванны расплава 16 и периодическими потоками от взаимодействия собственного магнитного поля с током дуги 15. В условиях данного резонанса по результатам физического моделирования усиливаются процессы массопереноса, и интенсивность перемешивания расплава 16 возрастает в 2-3 раза. В процессе электроплавки получали нержавеющую сталь марки Х18АГ14, отвечающую среднему химическому составу, %: С – 0,03; Si – 0,6; Mn – 13,5; S – 0,02 и Р – 0,015.
В таблице приведены примеры осуществления предложенного способа, выявляющие эффективность заявленного диапазона частот пульсаций. Из сравнений результатов использования предлагаемого изобретения выявлено, что эффективный диапазон пульсаций Iд и Gг находится в пределах 0,1-10 Гц, а наиболее оптимальной частотой пульсаций является частота 1 Гц. При частоте пульсаций Iд и Gг менее 0,1 Гц и более 10 Гц достигается производительность печи на уровне прототипа.
Использование предлагаемого способа позволяет повысить производительность печи за счет:
– уменьшения длительности всех этапов электроплавки, являющегося следствием интенсификации перемешивания расплава за счет резонансных явлений, обусловленных применением новых технических решений;
– снижения удельного расхода электроэнергии на плавку вследствие уменьшения продолжительности основных технологических процессов, связанных с расплавлением шихты, перегревом, рафинированием и легированием расплава;
– уменьшения числа погасаний дуги за счет повышения стабильности ее горения при обжатии плазмообразующим газом, что снижает непроизводительные простои печи и повышает производительность электроплавки;
– увеличения межремонтной кампании за счет повышения стойкости подовых электродов в связи с уменьшением токовых нагрузок.
№ п/п |
Показатель |
Частота пульсаций общего тока дуги fд и потока плазмообразующего газа (верхняя цифра) и частота изменения величин токов в замкнутых электрических цепях между сводовым и подовым электродами fи (нижняя цифра), Гц |
Степень улучшения при оптимальной частоте fд=fг=1 Гц; fи=10 Гц |
 |
 |
 |
 |
 |
1 |
Продолжительность нагрева и расплавления шихты, мин |
115 |
80 |
85 |
79 |
114 |
Сокращена на 30% |
2 |
Продолжительность рафинирования, мин |
40 |
30 |
20 |
29 |
42 |
Уменьшена в 2 раза |
3 |
Продолжительность легирования расплава, мин |
21 |
12 |
7 |
10 |
20 |
Уменьшена в 3 раза |
4 |
Общая продолжительность плавки, мин |
176 |
122 |
112 |
120 |
170 |
Сокращена на 27% |
5 |
Производительность печи, т/ч |
6,8 |
10,1 |
10,8 |
10,15 |
6,9 |
Увеличилась в 1,6 раза |
6 |
Удельный расход электроэнергии на плавку, кВт-ч/т |
450 |
300 |
286 |
305 |
452 |
Уменьшился в 1,57 раз |
7 |
Угар шихтовых материалов и ферросплавов, % |
1,5 |
1,0 |
1,1 |
0,99 |
1,45 |
Уменьшился на 0,4% |
8 |
Удельный расход ферромарганца, кг/т |
20,8 |
16,2 |
13,2 |
15,9 |
20,5 |
Уменьшился в 1,58 раз |
9 |
Содержание серы в стали, % |
0,021 |
0,01 |
0,008 |
0,01 |
0,02 |
Уменьшилось в 2,63 раза |
10 |
Расход графитизированных электродов, кг/т |
1,5 |
1,3 |
1,11 |
1,3 |
1,5 |
Уменьшился в 1,34 раза |
11 |
Среднестатичтическое число погасаний дуги (за 20 плавок) |
5 |
2 |
1 |
2 |
5 |
Сократилось в 5 раз |
Формула изобретения
Способ электроплавки в дуговой печи постоянного тока, включающий загрузку шихты в печь, создание электрического контакта между сводовым электродом и шихтой, включение источника электропитания, плавление шихты дугой при протекании общего тока через замкнутые электрические цепи, включающие сводовый электрод, межэлектродный промежуток, шихту, образующийся расплав, подовые электроды с токоподводами и источник электропитания, управление параметрами дуги и источника электропитания, нагрев, рафинирование и легирование расплава с его перемешиванием за счет возбуждения в расплаве поля электромагнитных сил от протекания тока через расплав, периодическое изменение величины тока в замкнутых электрических цепях с регламентированной частотой и с соответствующим увеличением интенсивности поля электромагнитных сил в расплаве, отличающийся тем, что управление параметрами дуги и источника электропитания осуществляют наложением пульсаций на общий ток дуги и подачей в межэлектродный промежуток пульсирующего потока плазмообразующего газа через сквозное осевое отверстие в сводовом электроде, причем частоты пульсаций общего тока дуги и потока плазмообразующего газа выбирают в диапазоне 0,1-10 Гц и принимают равными десятикратной частоте изменения величин токов в замкнутых электрических цепях между сводовым и подовыми электродами, а в период легирования в пульсирующий поток плазмообразующего газа вводят порошкообразные лигатуры через сводовый электрод.
РИСУНКИ
|
|