|
(21), (22) Заявка: 2003108877/15, 13.06.2002
(24) Дата начала отсчета срока действия патента:
13.06.2002
(30) Конвенционный приоритет:
18.01.2002 (пп.1-25) JP 2002-10196
(43) Дата публикации заявки: 27.07.2004
(46) Опубликовано: 10.02.2007
(56) Список документов, цитированных в отчете о поиске:
JP 60-73267 А, 25.04.1985. ЕР 690116 A1, 03.01.1996. JP 4-55316 А, 24.02.1992. RU 2079066 C1, 10.05.1997.
(85) Дата перевода заявки PCT на национальную фазу:
31.03.2003
(86) Заявка PCT:
JP 02/05933 (13.06.2002)
(87) Публикация PCT:
WO 02/103259 (27.12.2002)
Адрес для переписки:
103735, Москва, ул. Ильинка, 5/2, ООО “Союзпатент”, пат.пов. А.П.Агурееву
|
(72) Автор(ы):
ЯНАГИТАНИ Такагими (JP), НОЗАВА Хоситеру (JP), КАГАВА Кацунори (JP)
(73) Патентообладатель(и):
КОНОСИМА КЕМИКАЛ КО., ЛТД (JP)
|
(54) РЕГЕНЕРАТИВНЫЙ МАТЕРИАЛ И РЕГЕНЕРАТОР НА ОСНОВЕ ОКСИСУЛЬФИДА РЕДКОЗЕМЕЛЬНОГО МЕТАЛЛА
(57) Реферат:
Изобретение относится к регенеративному материалу на основе оксисульфида редкоземельного металла и регенератору, в котором используют такой материал. Регенеративный материал на основе оксисульфида редкоземельного металла отвечает общей формуле R2O2S, где R представляет собой, по меньшей мере, один из редкоземельных элементов, выбранных из группы, состоящей из La, Се, Pr, Nd, Sm, Eu, Gd, Tb, Dy, Ho, Er, Tm, Yb, Lu, а также Y. Регенератор с насадкой из регенеративного материала на основе оксисульфида редкоземельного металла содержит оксисульфид редкоземельного металла общей формулы R2O2S, где R представляет собой, по меньшей мере, один из редкоземельных элементов, выбранных из группы, состоящей из La, Се, Pr, Nd, Sm, Eu, Gd, Tb, Dy, Но, Er, Tm, Yb, Lu, а также Y. Результат изобретения: разработка регенеративного материала, обладающего высокой теплоемкостью в области температур жидкого гелия и высокой устойчивостью к тепловым ударам и вибрациям, и регенератора, предназначенных для охлаждения ниже температур порядка 4-7 К, а также подходящих для охлаждения до температур ниже 2-4 К, и увеличение срока службы регенеративного материала в регенераторах. 2 н. и 23 з.п. ф-лы, 17 табл., 8 ил.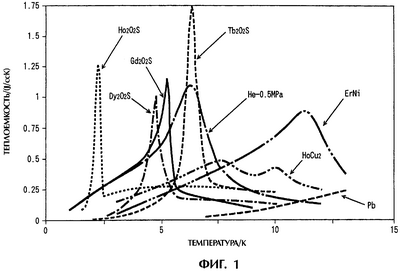
Область техники, к которой относится изобретение
Настоящее изобретение относится к регенеративному материалу на основе оксисульфида редкоземельного металла и регенератору, в котором используют такой материал. Главным образом, настоящее изобретение относится к регенеративному материалу и регенератору, обладающим высокой теплоемкостью при температурах около 4,2 К, требующихся для сжижения газообразного Не, без образования абразивной пыли при работе холодильника.
Уровень техники
Жидкий гелий требуется для охлаждения сверхпроводящих магнитов, сенсоров и т.п., а для сжижения газообразного Не требуется аномально высокая работа сжатия, в связи с чем для этой цели требуется холодильник большого размера. Однако трудно использовать холодильники крупного размера для мелких устройств, в которых используется явление сверхпроводимости, например таких, как линейные моторные вагоны (linear motor car) или MRI (магнитно-резонансный индукционный анализатор). Следовательно, необходим высокопроизводительный холодильник небольшого размера, способный создавать температуру жидкого гелия (4,2 К).
Эффективность охлаждения, низшая достигаемая температура и т.п. холодильника небольшого размера зависят от природы регенеративных материалов, наполнителей регенератора. Такие регенеративные материалы необходимы для обеспечения достаточно высокой теплоемкости и высокого кпд теплообмена для гелия или другого хладагента, пропускаемого через холодильник. Такие традиционные металлические регенеративные материалы, как Pb, характеризуются резким падением теплоемкости при температурах около 10 К и ниже. Учитывая это обстоятельство, были разработаны регенеративные материалы, содержащие такие редкоземельные интерметаллические соединения, как HoCu2 или ErNi (JP 2609747, USP 5449416). Как показано на фигуре 1, эти материалы обладают высокой теплоемкостью при температурах 20 К-7 К, однако их теплоемкости сильно падают при температуре ниже 7 К. Кроме этого, необходимо, чтобы регенеративные материалы обладали устойчивостью к ударным тепловым воздействиям и вибрациям, имеющим место при работе холодильных устройств.
Сущность изобретения
Основная цель настоящего изобретения заключается в разработке регенеративного материала, обладающего высокой теплоемкостью в области температур жидкого гелия и высокой устойчивостью к тепловым ударам и вибрациям, а также в создании регенератора, использующего такой регенеративный материал.
Вторая цель настоящего изобретения состоит в разработке регенеративного материала и регенератора, предназначенных для охлаждения ниже температур порядка 4-7 К.
Другая цель настоящего изобретения заключается в создании регенеративного материала и регенератора, подходящих для охлаждения до температур ниже 2-4 К.
Еще одна цель настоящего изобретения заключается в увеличении срока службы регенеративного материала в регенераторах.
Регенеративный материал
Регенеративный материал настоящего изобретения включает оксисульфид редкоземельного металла, отвечающий общей формуле R2O2S®, в которой R означает один, два или более типов редкоземельных элементов, выбранных из группы, состоящей из La, Се, Pr, Nd, Sm, Eu, Gd, Tb, Dy, Ho, Er, Tm, Yb и Lu, а также Y. Предпочтительный редкоземельный элемент представляет собой, по крайней мере, один элемент из группы, включающей Gd, Tb, Dy, Но и Er, более предпочтительный редкоземельный элемент представляет собой Gd или Tb.
Так, например, если оксисульфид редкоземельного металла представляет собой Gd2-xTbxO2S (x=0,2-2), то температура, при которой он обладает максимальной удельной теплоемкостью, может изменяться в интервале от значений, близких к 6 К, до значений, близких к 4 К. В интервале значений х=1,6-2, предпочтительно, 1,8-2, и более предпочтительно, 1,9-2, температура, при которой наблюдается максимальное значение его удельной теплоемкости, существенно выше температуры, при которой проявляется максимальная удельная теплоемкость Gd2O2S. В том случае, когда такой регенеративный материал используют в комбинации с регенеративным материалом, включающим Gd в качестве основного редкоземельного металлического компонента, большие значения удельной теплоемкости проявляются в широком температурном интервале 4-7 К, и такая комбинация регенеративных материалов особенно подходит для охлаждения до температуры жидкого гелия.
Поскольку оксисульфиды Но и Dy обладают максимальной удельной теплоемкостью при более низкой температуре, чем оксисульфиды Gd, они особенно подходят для охлаждения до температур порядка 2-4 К. Так, например, когда регенеративный материал, включающий Gd в качестве основного компонента редкоземельных элементов, располагают со стороны высоких температур, а регенеративный материал, содержащий оксисульфид Но или Dy, располагают со стороны пониженных температур, охлаждение до температур вплоть до 4 К может быть достигнуто с использованием регенеративного материала, включающего Gd в качестве основного компонента редкоземельных элементов, а охлаждение до 4 К и ниже может достигаться с использованием регенеративного материала, включающего Но или Dy в качестве основного компонента редкоземельных элементов; в результате может осуществляться эффективное охлаждение до температуры 4К и ниже.
Оксисульфиды редкоземельного металла предпочтительно использовать в виде гранул, более предпочтительно, при среднем размере частиц гранул 50-1000 мкм. Предпочтительные гранулы имеют средний размерный коэффициент порядка 3 и ниже, а их относительная плотность, предпочтительно, составляет 96% и выше. Оксисульфид редкоземельного металла в виде гранул имеет предпочтительный средний размер зерна 100 мкм или менее, шероховатость поверхности в расчете на максимальную высоту Rmax гранул составляет, предпочтительно, 10 мкм или менее, а избыточное содержание серы в гранулах, предпочтительно, составляет 10000 массовых ч/млн или менее. Предпочтительно, когда объемная удельная теплоемкость гранул имеет максимальное значение при 2-7 К.
Введение компонентов для повышения ударной вязкости
Предпочтительно, присадку, содержащую оксид, карбид или нитрид, на основе, по крайней мере, одного представителя группы, состоящей из щелочно-земельных металлов, переходных металлов, и элементов 3b и 4b групп периодической системы, включая подгруппу В и исключая подгруппу С, добавляют к оксисульфиду редкоземельного металла в количестве 0,05-30 мас.%. Количество присадки выражают таким образом, чтобы одна массовая часть присадки в 100 массовых частях регенеративного материала составляла 1 мас.%.
Предпочтительная присадка представляет собой, по крайней мере, один представитель группы, включающей AI2О3, ZrO2, муллит, Si3N4, Sialon, TiN, AIN, BN, SiC и TiC, более предпочтительно, по крайней мере, один представитель группы, состоящей из ZrO2, муллита, Si3N4, Sialon, TiN, AIN, BN, SiC и TiC. Муллит представляет собой соединение состава xAI2O3·ySiO2 (х:y=3:2-2:1), a Sialon представляет собой нестехиометрическое соединение Si, AI, О и N.
Предпочтительно, присадка представляет собой оксид на основе, по крайней мере, одного щелочноземельного металлического компонента, выбранного из группы, включающей Mg, Са, Sr и Ва.
Предпочтительно, присадка представляет собой оксид, по крайней мере, одного переходного металла из группы, включающей элементы с атомными номерами 22(Ti)-31(Ga) и 72(Hf).
В керамических микроструктурах оксисульфидного регенеративного материала на основе редкоземельного металла, предпочтительно, образуется основная фаза R2O2S и вторая фаза, содержащая присадку и отличающаяся от основной фазы.
Регенератор
Регенеративный материал на основе оксисульфида редкоземельного металла загружают в цилиндр или аналогичный сосуд с получением регенератора. Оксисульфиды редкоземельного металла демонстрируют хорошие значения удельных теплоемкостей при 7К или ниже, и в том случае, когда регенеративный материал, включающий HoCu2 в качестве основного компонента, размещают на высокотемпературной стороне регенеративного материала, на основе оксисульфида редкоземельного металла, можно осуществлять охлаждение до 7 К при помощи HoCu2, a охлаждение до 7 К и ниже может осуществляться с помощью регенеративного материала на основе оксисульфида редкоземельного металла; причем охлаждение до 7 К и ниже может осуществляться с высокой эффективностью.
Оксисульфидные регенеративные материалы, содержащие Gd в качестве основного компонента редкоземельных элементов, демонстрируют максимальные значения удельной теплоемкости при 5-4 К, а их удельные теплоемкости при 7-5 К имеют недостаточные значения. Поэтому, предпочтительно, чтобы оксисульфидный регенеративный материал, содержащий Tb, в качестве основного компонента его редкоземельных элементов, располагался на высокотемпературной стороне оксисульфидного регенеративного материала, содержащего Gd в качестве основного компонента. Что касается охлаждения до 4 К и ниже, то первым размещают оксисульфидный регенеративный материал, содержащий Gd в качестве основного компонента его редкоземельных элементов, а оксисульфидный регенеративный материал, содержащий Но или Dy в качестве основного компонента редкоземельных элементов, располагают на низкотемпературной стороне предыдущего слоя. Охлаждение до 2-4 К осуществляют, например, для усиления чувствительности рентгеновского детектора в результате охлаждения анализатора полупроводников при пропускании рентгеновского или иного излучения, а также для предварительной стадии охлаждения адиабатического размагничивающегося холодильника.
Ниже приводятся разъяснения, касающиеся представления о редкоземельных элементах оксисульфидов редкоземельных металлов. Оксисульфидный регенеративный материал на основе Gd, или материал, в котором Gd является основным компонентом, подразумевает, что Gd составляет 50 атомных % или более от содержания металлических компонентов. Так, например, как показано в Таблице 1, Gd1Tb1O2S обладает удельной теплоемкостью на низкотемпературной стороне, равной теплоемкости Gd2O2S, и этот материал скорее похож на Gd2O2S, чем на Tb2O2S. Что касается Tb, Dy, Но и т.п., то оксисульфид любого из перечисленных элементов или оксисульфид, содержащий указанные элементы в качестве основного компонента, подразумевает, что 80 атом % или более от содержания металлических компонентов приходится на один из указанных элементов. Так, например, даже при замене 10% металлических компонентов оксисульфида на другой элемент удельная теплоемкость полученного оксисульфида не будет сильно отличаться от исходного значения.
Характеристики рефрижерации
Регенеративные материалы на основе оксисульфидов редкоземельных металлов подвергаются магнитно-фазовому переходу в области 7-2 К и обладают теплоемкостями, превосходящими в 2-5 раз теплоемкости таких традиционных регенеративных материалов, как HoCu2 или ErNi. Соответственно, регенеративные материалы на основе оксисульфидов редкоземельных металлов обладают высокими характеристиками рефрижерации в криогенной окружающей среде в области температур 4,2 К, и достигаемые в их присутствии минимальные температуры имеют более низкие значения, чем в присутствии традиционных регенеративных материалов. Таким образом, используя регенеративные материалы на основе оксисульфидов редкоземельных металлов, легко получить регенераторы малого размера, обладающие высокой эффективностью охлаждения. Регенеративный материал в соответствии с настоящим изобретением может применяться для сверхпроводящих магнитов, рефрижераторов для охлаждения MRI и т.п. Кроме этого, в результате выбора типа редкоземельных элементов и использования нескольких редкоземельных элементов может быть достигнута желаемая температура перехода магнитной фазы, и может быть расширен интервал максимальных значений удельной теплоемкости в области температуры перехода магнитной фазы. При использовании гранул регенеративного материала на основе оксисульфида редкоземельного металла может быть снижено сопротивление переноса хладагента и повышена кажущаяся плотность регенеративного материала. Кроме этого, в результате понижения шероховатости поверхности гранул предотвращается образование пыли и увеличивается срок службы регенеративного материала.
Необходимо, чтобы регенераторы обладали сплошным интервалом удельной теплоемкости от высокотемпературной стороны до низкотемпературной стороны и широким интервалом значений удельной теплоемкости в области желаемой температуры охлаждения. Первое из этих условий является характеристикой, требуемой для эффективного охлаждения до желаемой температуры, а второе – характеристикой, которая позволяет выбирать (желаемую) целевую температуру из широкого интервала значений. Поскольку регенеративные материалы на основе оксисульфидов редкоземельных металлов обладают низкими значениями удельных теплоемкостей при 7 К и выше, желательно располагать такой регенеративный материал, как HoCu2, с высокотемпературной стороны регенеративного материала на основе оксисульфида редкоземельного металла. Поскольку регенеративный материал на основе одного оксисульфида редкоземельного металла обеспечивает лишь узкий интервал распределения удельных теплоемкостей, желательно получить слоевой регенеративный материал на базе оксисульфида редкоземельного металла для низких температур и другой – для высоких температур, в результате чего такие материалы в целом обеспечивают сплошной интервал значений удельных теплоемкостей. Поскольку оксисульфиды, содержащие Gd в качестве основного компонента, не обладают достаточными удельными теплоемкостями при 6-7 К, желательно обеспечить наличие на его высокотемпературной стороне оксисульфида, включающего Tb в качестве основного компонента. Что касается охлаждения до 4 К и ниже, то желательно обеспечить наличие оксисульфида, включающего Но и Dy в качестве основных компонентов на низкотемпературной стороне оксисульфида, содержащего Gd в качестве основного компонента.
Приготовление регенеративного материала на основе оксисульфида редкоземельного металла
Оксисульфид редкоземельного металла получают, например, путем помещения порошка оксида редкоземельного металла в реакционную трубку и ее нагревания, пропуская через указанную трубку газ, содержащий атомы серы в степени окисления -2, например, H2S или СН3SH. Предпочтительная температура такой реакции составляет 500-800°С (773,15-1073,15 К), более предпочтительно, 600-700°С (873,15-973,15 К). При температурах ниже 500°С (773,15 К) для завершения реакции требуется длительное время. Предпочтительная продолжительность реакции составляет 1-9 часов, более предпочтительно, 1-3 часа.
Регенеративный материал желательно использовать в виде гранул. Такая форма делает регенеративный материал более устойчивым к сжатию во время его загрузки в регенератор и к тепловым перегрузкам и вибрациям в ходе использования, а также предотвращает образование пыли. Особенно предпочтительно использовать гранулы сферической формы. Предпочтительно, чтобы величина среднего отношения наибольшего размера к наименьшему размеру гранул (среднее размерное соотношение) имела значение 3 или менее, и, более предпочтительно, 2 или менее, а еще более предпочтительно было близким к 1, другими словами, чтобы использовались истинные сферы. Оксисульфиды редкоземельных металлов становятся более хрупкими материалами, чем редкоземельные металлические соединения, при среднем размерном соотношении выше 3 гранулированный оксисульфид редкоземельного металла проявляет тенденцию к разрушению. Кроме этого, при среднем размерном соотношении, превышающем 3, возникают трудности, связанные с однородной загрузкой гранул в регенератор.
Предпочтительный средний размер частиц гранул катализатора составляет 50-1000 мкм. Если средний размер частиц меньше 50 мкм, то плотность упаковки имеет высокое значение, что затрудняет проход Не хладагента через регенератор и приводит к ухудшению эффективности теплообмена. Если средний размер частиц превышает 1000 мкм, то уменьшается площадь контакта с хладагентом (Не), что также приводит к снижению эффективности теплообмена. Следовательно, предпочтительный средний размер частиц составляет 50-1000 мкм, более предпочтительно, 100-700 мкм и наиболее предпочтительно, 100-300 мкм.
Предпочтительно, когда относительная плотность гранул регенеративного материала составляет 96% или выше, более предпочтительно, 98% и выше, наиболее предпочтительно, 99% и выше; желательно, чтобы она была близка к теоретической плотности. При относительной плотности менее 96% уменьшается механическая прочность гранул из-за наличия большого числа пустот.
Для повышения механической прочности гранул, предпочтительно, чтобы средний размер гранул составлял 10 мкм или менее, более предпочтительно, 50 мкм или менее и наиболее предпочтительно, 10 мкм и менее и 1 мкм и выше. Механическая прочность уменьшается при среднем размере зерна гранул выше 100 мкм.
Неправильная поверхность гранул приводит к потере механической прочности. В связи с этим, предпочтительно, чтобы шероховатость поверхности гранул составляла, например, 10 мкм или менее в расчете на максимальную высоту стандартов (Rmax) описанных в JIS BO601.
Предпочтительное избыточное содержание серы в гранулах составляет 10000 мас. частей/млн или менее, более предпочтительно, 5000 мас. частей/млн или менее, и наиболее предпочтительно, 2000 мас. частей/млн или менее. При большом содержании серы в гранулах может наблюдаться ингибирование спекания, что, в свою очередь, приводит к снижению механической прочности. Регулирование избыточного содержания серы может легко осуществляться, например, путем регулирования расхода H2S во время сульфуризации редкоземельного оксида.
Гранулы могут быть приготовлены из порошкообразного оксисульфида редкоземельного металла разнообразными способами. Так, например, для этой цели может использоваться гранулирование в барабане, комбинация экструзии и гранулирования в барабане, гранулирование в псевдоожиженном слое, сушка распылением, или прессование по шаблону. Желательно придавать гранулам сферическую форму. После формирования, гранулы сортируют по оптимальному размеру частиц и/или оптимальному размерному отношению путем просеивания, классификации по форме и т.п. Порошкообразный оксид редкоземельного металла можно с успехом гранулировать любым из перечисленных способов, после чего проводят сульфуризацию. Условия сульфуризации идентичны тем, что применяют при использовании оксидного порошкообразного материала.
Сформованные частицы оксисульфида редкоземельного металла подлежат спеканию. Для предотвращения окисления оксисульфида редкоземельного металла, предпочтительно проводить спекание в вакууме (10-3 торр или ниже), либо в атмосфере такого инертного газа, как аргон или азот. Предпочтительная температура спекания составляет 1100-1600°С (1373,15-1873,15 К), а продолжительность спекания составляет 1-10 часов.
Если после спекания проводят HIP обработку, то получают более компактные гранулы, обладающие повышенной механической прочностью. Спекание с HIP обработкой проводят в атмосфере аргона и предпочтительная температура такой обработки составляет 1473,15-1773,15 К при давлении 50-200 МПа.
Для того чтобы шероховатость гранул имела значение, например, 10 мкм или менее в расчете на максимальную высоту Rmax стандарта, спекшиеся гранулы предпочтительно полировать. Для этого гранулы регенеративного материала и абразивный материал помещают, например, в технологический сосуд. При необходимости туда же добавляют обрабатывающую жидкость. К сосуду или технологическому сосуду прилагается рабочее усилие, приводящее к движению, обеспечивающему полировку за счет движения абразива и среды относительно друг друга. Для этой цели могут использоваться, например, такие способы, как роторная барабанная отделка, отделка в барабанной центрифуге с движущимся слоем, вибрационная барабанная отделка, гидроотделка, возвратно-поступательная чистовая обработка, или линейная чистовая обработка в псевдоожиженным слоем.
Краткое описание чертежей
На фигуре 1 показаны теплоемкости регенеративных материалов на основе оксисульфида редкоземельного металла, гелия и традиционных регенеративных материалов.
Фигура 2 изображает температурную зависимость теплоемкостей регенеративных материалов настоящего изобретения на основе оксисульфидов редкоземельного металла, представляющих обогащенный гадолинием Gd2-xTbxO2S.
Фигура 3 изображает температурную зависимость теплоемкостей регенеративных материалов настоящего изобретения на основе оксисульфидов редкоземельного металла, представляющих собой обогащенный Tb Gd2-xTbxO2S.
Фигура 4 изображает теплоемкости Ho-Dy композитных редкоземельных оксисульфидных регенеративных материалов.
Фигура 5 изображает конструкцию традиционного регенератора (а) и регенератора (b) варианта настоящего изобретения.
Фигура 6 демонстрирует охлаждающую способность традиционного регенератора (а) и регенераторов вариантов воплощения настоящего изобретения (b) и (с).
Фигура 7 демонстрирует относительные охлаждающие способности традиционного регенератора и регенератора согласно варианту воплощения настоящего изобретения.
Фигура 8 изображает теплоемкости керамических материалов формулы GdxTb2-xO2S.
Предпочтительные варианты воплощения настоящего изобретения
В этом разделе описываются некоторые варианты технические решения настоящего изобретения и приводятся сравнительные примеры.
Регенеративные материалы загружали в регенератор под давлением 100 кПа и определяли сопротивление переносу газообразного гелия по разнице давления на входе и выходе из регенератора. Среднее размерное соотношение определяли по микрофотографиям гранул после спекания и с помощью устройства, распознающего изображение, измеряли соотношение между наибольшим и наименьшим линейными размерами. Степень образования пыли определяли визуальным осмотром регенеративного материала, удаленного из регенератора, и оценкой соотношения разрушенных гранул. Содержание избыточной серы определяли путем сравнения содержания Gd определенного химическим анализом и содержания серы, полученного анализом на сгорание. Полученные значения выражали в мас. частях/млн.
Приготовление оксисульфидов и их теплоемкости. 10 г оксида гадолиния со средним размером частиц 0,46 мкм, определенным методом Фишера, загружали в кварцевую ванночку, которую помещали в кварцевый трубчатый реактор. Через трубку пропускали газообразный H2S с объемной скоростью 0,2 л/мин и оксид гадолиния реагировал с пропускаемым газом в течение 2 часов при 650°С (923,15 К). При исследовании продуктов реакции методом рентгеновской дифракции наблюдался лишь пик оксисульфида гадолиния, Gd2O2S. Следовательно, выход редкоземельного оксида в этой реакции составляет 100%. Полученный порошкообразный Gd2O2S формовали в диски диаметром 12 мм под давлением 30 МПа. Эти диски прессовали на гидростатическом прессе при давлении 200 МПа, после чего их спекали при атмосферном давлении в среде аргона, при 1500°С (1773,15 К) в течение 6 часов с получением образцов Gd2O2S (вариант 1).
Определенная по методу Архимеда плотность подвергнутого спеканию Gd2O2S согласно варианту 1 составила 99,9% от теоретического значения. Средний размер зерен продукта, рассчитанный по следующей формуле, составил 3,2 мкм:
d=1,56C (MN)
(где: d – средний размер зерна; С – длина свободно-проведенной линии на изображении высокого разрешения, полученном методом SEM и т.п.; N – число кристаллических зерен в свободно проведенной линии; М – кратность увеличения изображения).
В результате сравнения содержания Gd, определенного химическим анализом, с содержанием серы, определенным методом сгорания, было установлено избыточное содержание серы в спеченном Gd2O2S варианта 1, составившее 100 мас. частей/млн.
Теплоемкость спеченного Gd2O2S, согласно варианту 1, показана на фигуре 1, а его температура перехода магнитной фазы и теплоемкость при этой температуре представлены в Таблице 1. Помимо теплоемкости подвергнутого спеканию Gd2O2S на фигуре 1 показаны теплоемкости Tb2O2S, Dy2O2S и Ho2O2S, и для сравнения приведены теплоемкость гелия (Не – 0,5 МПа) и теплоемкости Pb, ErNi и HoCu2, представляющих собой традиционные регенеративные материалы. Регенеративный материал, представляющий собой Gd2O2S по варианту 1, имел температуру перехода магнитной фазы в области 5 К и его теплоемкость при этой температуре составила 1,2 J/cc.K; теплоемкость регенеративного материала Gd2O2S в 3-5 раз выше теплоемкостей таких традиционных регенеративных материалов, как HoCu2 или ErNi в области температуры жидкого гелия.
Таблица 1 Температуры перехода магнитной фазы |
Образец |
Состав |
Температура перехода магнитной фазы/К |
Теплоемкость /J/ сс.К |
Воплощение 1 |
Gd2O2S |
5,2 |
1,2 |
Воплощение 2 |
HO2O2S |
2,2 |
1,25 |
|
Dy2O2S |
4,6 |
1,0 |
Воплощение 3 |
Gd1,8Tb0,2O2S |
4,8 |
0,84 |
|
Gd1Tb1O2S |
4,2 |
0,61 |
|
Tb1,8Gd0,2O2S |
5,3 |
1,3 |
|
Tb2O2S |
6,3 |
1,7 |
Воплощение 4 |
Dy1,8HO0,2O2S |
4,3 |
0,8 |
|
HO1,8Dy0,2O2S |
2,4 |
0,85 |
Воплощение 5 |
Gd1,8Y0,2O2S |
4,6 |
0,75 |
|
Gd1,8La0,2O2S |
4,6 |
0,85 |
|
Gd1,8Ce0,2O2S |
4,7 |
0,74 |
|
Gd1,8Pr0,2O2S |
4,7 |
0,69 |
|
Gd1,8Nd0,2O2S |
4,8 |
0,77 |
|
Gd1,8Sm0,2O2S |
4,8 |
0,63 |
|
Gd1,8Eu0,2O2S |
4,9 |
0,76 |
|
Gd1,8Dy0,2O2S |
4,9 |
0,82 |
|
Gd1,8Ho0,2O2S |
4,9 |
0,71 |
|
Gd1,8Er0,2O2S |
5 |
0,81 |
|
Gd1,8Tm0,2O2S |
5 |
0,73 |
|
Gd1,8Yb0,2O2S |
5,1 |
0,76 |
|
Gd1,8Lu0,2O2S |
5,2 |
0,8 |
Оксид гадолиния, Gd2O3, согласно варианту 1, использовали без сульфуризации для получения спеченного материала в условиях, используемых в варианте 1 (сравнительный пример 1). Температура перехода магнитной фазы этого образца была близка 1 К, при чрезвычайно низкой теплоемкости в области 4,2 К.
Оксид гольмия со средним размером частиц 0,36 мкм и оксид диспрозия со средним размером частиц 0,6 мкм подвергали сульфуризации, формованию, гидростатическому прессованию и спеканию в условиях реализации варианта 1 с получением спеченного HO2O2S и спеченного Dy2O2S (вариант 2). Теплоемкости таких, подвергнутых спеканию, материалов показаны на фигуре 1, а их температуры перехода магнитной фазы и теплоемкости при таких температурах представлены в Таблице 1, соответственно. Эти материалы обладают более высокими теплоемкостями в широком интервале температур в области температуры жидкого гелия, чем HoCu2 и ErNi.
Композитные оксисульфиды
Смесь порошка оксида гадолиния, используемого в варианте 1, и порошка оксида тербия со средним размером частиц 0,69 мкм подвергали сульфуризации, формованию, гидростатическому прессованию и спеканию в условиях, аналогичных используемым в варианте 1 с получением гадолиний-тербиевых оксисульфидов (GdxTb2-xO2S) (вариант 3). Снимали рентгенограммы указанных четырех типов спеченных материалов, составы которых менялись в интервале 0 х 2 (х=0,2, 1,0, 1,8 и 2,0). При х=2,0 наблюдался лишь пик, соответствующий Tb2O2S. Для х=0,2 наблюдались два пика 1,0 и 1,8, соответствующие твердому раствору GdxTb2-xO2S, которые не относились ни к Gd2O2S, ни к Tb2O2S. Теплоемкости системы GdxTb2-xO2S варианта 3 представлены в Таблице 1. При уменьшении величины х до 1,8 и затем до 1 наблюдалось понижение теплоемкости во время магнитно-фазового перехода, тогда как температура магнитно-фазового перехода сдвигается в низкотемпературную сторону интервала для Gd2O2S, увеличивается ширина пика удельной теплоемкости и значение теплоемкости превышает соответствующее значение для Gd2O2S при температуре жидкого гелия. С другой стороны, как следует из Таблицы 1 и фигуры 3, при приближении состава композиции к Tb2O2S наблюдается температурный сдвиг магнитно-фазового перехода в высокотемпературную область интервала для Gd2O2S.
В общем случае, магнитное взаимодействие редкоземельных магнитных атомов в кристалле зависит от межатомного расстояния. Если имеют дело с совершенным кристаллом и межатомные расстояния магнитных атомов идентичны, то магнитное взаимодействие может быть выражено одним параметром, а магнитная спиновая система кристалла в целом характеризуется резким фазовым переходом. В этом случае, как и в случае варианта 1, из-за фазового перехода пик, соответствующий удельной теплоемкости, возрастает и становится более острым. С другой стороны, как это имеет место в варианте 3, в том случае, когда несколько редкоземельных элементов находятся в состоянии твердого раствора, межатомные расстояния магнитных атомов локально изменяются и происходят локальные возмущения кристаллического поля, что в результате приводит к потере однородности магнитного взаимодействия кристалла в целом. В результате магнитно-фазовый переход магнитных спинов в кристалле претерпевает локальные возмущения и пик, соответствующий удельной теплоемкости рассеивается в некотором температурном интервале, что приводит к уширению пика удельной теплоемкости. В системах, содержащих гадолиний, это сопровождается сдвигом температуры магнитно-фазового перехода в сторону повышенных температур, а в системах, содержащих Gd, Tb и Dy, температура магнитно-фазового перехода сдвигается в область пониженных температур.
Порошок оксида гольмия и порошок оксида диспрозия, используемые в варианте 2, смешивали друг с другом, и полученную смесь подвергали сульфуризации, формованию, гидростатическому прессованию и спеканию, аналогично варианту 1, с получением спеченных диспрозий-гольмиевых композитных оксисульфидов, DyxHo2-xO2S (вариант 4). Теплоемкости таких спеченных материалов показаны на фигуре 4, а их температуры магнитно-фазового перехода и их теплоемкости при таких температурах представлены в Таблице 1. Температуры магнитно-фазовых переходов, имеющие промежуточные значения в сравнении с температурами для Dy2O2S и Ho2O2S, успешно достигаются в результате изменения значения х, и наблюдается большее уширение пика, соответствующего удельной теплоемкости, чем в случае с Dy2O2S и Ho2O2S.
Оксид гадолиния (90 мол.%) и оксиды (10 мол.%) таких редкоземельных элементов, как Y, La, Се, Pr, Nd, Sm, Eu, Dy, Er, Tm, Yb и Lu обрабатывали по методике, описанной в варианте 3 с получением спеченных композитных оксисульфидов редкоземельных металлов (вариант 5). Соответствующие им температуры (Тc) магнитно-фазового перехода и теплоемкости при таких температурах указаны в Таблице 1. При использовании различных композитных оксисульфидов могут быть достигнуты различные температуры магнитного фазового перехода и величина пика удельной теплоемкости может изменяться в соответствии с температурой магнитного фазовового перехода. Редкоземельные оксиды, используемые в вариантах 3 и 5, обрабатывали по методике, описанной для варианта 3, но без проведения стадии сульфуризации, с получением спеченных материалов (сравнительный пример 2). Теплоемкости таких материалов в области 4,2 К имели чрезвычайно низкие значения.
Гранулы регенеративного материала
Порошок Gd2O2S, полученный в варианте 1 изобретения, формовали в сферические частицы путем гранулирования в барабане, и полученные в результате гранулы просевали через два типа нейлоновых сит (сито А: (отверстие 308 мкм) и сито В (отверстие 190 мкм)). Просеянные гранулы прокатывали на зеркально обработанной железной плите, расположенной под углом 25°. Вальцованные гранулы регенерировали для проведения классификации по размеру. Средний размер частиц и среднее размерное отношение 100 гранул составило 0,25 мм и 1,1, соответственно. Средний размер частиц и среднее размерное отношение гранул Gd2O2S измеряли по изображению, полученному с помощью видео системы с широким обзором.
Полученные гранулы Gd2O2S загружали в алюминиевый тигель, и гранулы помещали в печь для обжига и подвергали спеканию при атмосферном давлении. Затем печь полностью вакуумировали и заполняли аргоном для спекания гранул в атмосфере инертного газа. Температура спекания составила 1500°С (1773,15 К) при продолжительности операции 6 часов. В результате получали желаемый регенеративный материал на основе Gd2O2S. Плотность полученного регенеративного материала измеряли с помощью пикнометра и она составила 99,2% от теоретической. Средний размер зерна и содержание серы имели значения, идентичные тем, что были получены в варианте 1.
Нейлон и алюминиевый шлам с концентрацией 10 мас.% помещали в технологический сосуд, после чего в сосуд вводили Gd2O2S регенеративный материал с целью обработки поверхности методом отделки во вращающемся барабане и получения гранул регенеративного материала (вариант 6). При обработке в течение 6 часов шероховатость поверхности гранул составила 1 мкм. Шероховатость поверхности измеряли с помощью сканирующего туннельного микроскопа (STMметр шероховатости поверхности). Полученный регенеративный материал на основе Gd2O2S загружали в охлаждающую секцию GM рефрижератора при скорости загрузки, которая обеспечивала максимальное заполнение. Затем газообразный Не, имеющий теплоемкость 25 J/K, подвергали циклу GM замораживания, который непрерывно повторяли в течение 500 часов при массовой объемной скорости 3 г/сек и давлении газа 16 атм. К этому моменту измеряли сопротивление проходу газообразного Не через регенерационную секцию. С момента начала операции не отмечалось увеличения указанного сопротивления. Через 1000 часов непрерывной операции Gd2O2S регенеративный материал вынимали и подвергали исследованию. Мелкоизмельченных гранул найдено не было.
Указанные ниже образцы готовили сульфуризацией, формованием, классификацией, спеканием и полировкой гранул из оксисульфидов редкоземельных металлов в условиях, аналогичных условиям варианта 6. Условия приготовления были аналогичными тем, что использовались в варианте 6, за исключением некоторых пунктов, отмеченных ниже. Образцам присваивали последовательные номера, начиная с номера 1, относящегося к варианту 1.
Гранулы получали в условиях, аналогичных применяемым в варианте (воплощении) 6, за исключением того, что изменяли угол наклона железной плиты. После этого гранулы спекали и полировали (образцы 2 и 3). Гранулы, оставшиеся после классификации по размеру в воплощении 6, с размерным отношением выше 3, подвергали спеканию и полировали (образец 4). Сопротивление проходу газообразного гелия и степень образования пыли для каждого из образцов оценивали в рамках цикла операции GM охлаждения, используемого в воплощении 6. Полученные результаты представлены в Таблице 2. В том случае, когда средний размерный коэффициент был менее 3, были получены хорошие результаты, аналогичные воплощению 6. В том случае, когда средний размерный коэффициент имел значение больше 3, сопротивление прохождению газообразного гелия увеличивалось на 30-40% через 500 часов непрерывной эксплуатации. Через 1000 часов непрерывной операции количество сильно измельченных гранул достигало 20-30%.
Таблица 2 Влияние размерного коэффициента |
Образец |
Угол при классификации /° |
Средний размерный коэффициент |
Увеличение сопротивления проходу гелия |
Степень |
1 |
25 |
1,1 |
Нет |
отсутствие проблем |
2 |
30 |
1,3 |
Нет |
” |
3 |
40 |
1,8 |
Нет |
” |
4 |
– |
3,2 |
Увеличение на 30-40% через 500 ч пробега |
20-30% гранул разрушались через 1000 ч пробега |
Условия спекания
Спеченные гранулы получали в условиях, аналогичных используемым в варианте 6, за исключением того, что температуру спекания или продолжительность спекания меняли с целью изменения размера гранул (образцы 5-9). Влияние изменений диаметра гранул на сопротивление проходу газообразного гелия и степень образования пыли оценивали с помощью GM рефрижераторного цикла, используемого в варианте 6. Полученные результаты представлены в Таблице 3. Хорошие результаты были получены для гранул с размером зерна 100 мкм и менее, образцы 1 и 5-7. Однако в случае образцов 8 и 9 с размерами гранул, превышающими 100 мкм, сопротивление переносу газообразного Не повышалось на 20-30% через 500 часов непрерывной работы, а количество сильно разрушенных гранул возрастало до 10-15% через 1000 часов непрерывной работы.
Таблица 3 Условия и длительность спекания |
Образец |
Т-ра спекания /К |
Продолжительность спекания, час |
Средний размер гранул, мкм |
Увеличение сопротивления потоку Не |
Степень образования пыли |
1 |
1773,15 |
6 |
3,7 |
Нет |
Отсутствие проблем |
5 |
1823,15 |
6 |
23 |
« |
« |
6 |
1873,15 |
6 |
85 |
« |
« |
7 |
1873,15 |
3 |
37 |
« |
« |
8 |
1923,15 |
6 |
110 |
На 20-30% через 500 часов работы |
Разрушение 10-15% гранул |
9 |
1873,15 |
15 |
121 |
На 20-30% через 500 часов работы |
Разрушение 10-15% гранул |
Шероховатость поверхности
Время обработки поверхности изменяли с целью достижения различной шероховатости поверхности. Зависимость сопротивления проходу газообразного Не и степени образования пыли от шероховатости поверхности оценивали в GM рефрижераторном рабочем цикле, используемом в варианте 6. Полученные результаты представлены в Таблице 4. При шероховатости поверхности 10 мкм и менее, что имело место при использовании образцов 1, 10 и 11, были получены хорошие результаты. Если шероховатость поверхности превышала 10 мкм, как в случае образца 12, сопротивление проходу газообразного Не повышалось на 20-30% через 500 часов непрерывной работы, а количество сильно измельченных гранул возрастало до 15-20% через 1000 часов непрерывной работы.
Таблица 4 Влияние шероховатости поверхности и длительности ее обработки |
Образец |
Длительность обработки поверхности /час |
Шероховатость поверхности/мкм |
Увеличение сопротивления потоку Не |
Степень образования пыли |
1 |
6 |
1 |
нет |
Отсутствие |
|
|
|
|
проблем |
10 |
4 |
5 |
« |
« |
11 |
2 |
8 |
« |
« |
12 |
0 |
12 |
На 20-30% |
Разрушение |
|
|
|
через 500 |
15-20% |
|
|
|
часов работы |
гранул |
Влияние избыточной серы
Скорость потока при сульфуризации меняли с целью получения различных порошков Gd2O2S. Полученные порошки гранулировали и спекали по методике варианта 6. Содержание избыточной серы оказывает влияние на относительную плотность, а также на сопротивление потоку газообразного Не и степень образования пыли. Сопротивление потоку газообразного Не и степень образования пыли оценивали с помощью GM рефрижераторного рабочего цикла, используемого в варианте 6. Полученные результаты представлены в Таблице 5. При относительной плотности гранул 96% и выше, как в случае использования образцов 1, 13 и 14, были получены хорошие результаты. При относительной плотности гранул менее 96%, как в случае использования образца 15, сопротивление проходу газообразного Не возрастало до 15-20% через 500 часов непрерывной работы, а что касается разрушения гранул через 1000 часов непрерывной работы, то количество сильно разрушенных гранул возрастало до 5-10%. Предпочтительное значение относительной плотности гранул составляет 96% или выше, а избыточное содержание серы 10000 мас. частей/млн. Более предпочтительное значение относительной плотности составляет 98% или выше при избыточном содержании серы 5000 мас. ч./млн или менее. Наиболее предпочтительное значение относительной плотности гранул составляет 99% или выше при избыточном содержании серы 1000 мас. ч/млн или менее.
Таблица 5 Влияние количества избыточной серы |
Образец |
Расход H2S, (л/мин) |
Содержание серы/мас. ч/ млн |
Относительная плотность/% |
Увеличение сопротивления потоку Не |
Степень образования пыли |
1 |
0,2 |
1000 |
99,2 |
Нет |
Отсутствие |
|
|
|
|
|
Проблем |
13 |
1 |
5000 |
98,2 |
« |
« |
14 |
1,25 |
7000 |
97,6 |
« |
« |
15 |
2,5 |
12500 |
95,1 |
На 15-20% через 500 часов работы |
Разрушение 5-10% гранул |
Охлаждающая способность (хладопроизводительность)
Рефрижераторные характеристики регенеративного материала на основе Gd2O2S, полученного в варианте 6, и регенеративного материала Gd1,8Tb0,2O2S, полученного способом, аналогичным используемому в варианте 6, изучали с использованием холодильника регенераторного типа с импульсной трубкой с мощностью 3,3 кВт. В таком холодильнике предусматривали наличие двух регенераторов. В качестве регенератора первой стадии стороны с повышенной температурой использовали Pb, a регенеративный материал загружали в регенератор второй стадии. На фигуре 5(а) изображена традиционная конструкция генератора второй стадии. В регенератор загружали Pb, ErNi и HoCu2 в порядке уменьшения температуры и при объемном соотношении 2:1:1. Традиционные характеристики охлаждения представлены на Фигуре 6(а). Выходная мощность такого рефрижератора при 4,2 К составляла 165 МВт, а низшее значение достигаемой температуры при холостой работе составляло 2,9 К.
С другой стороны, 25 об.% HoCu2 регенеративного материала с низкотемпературной стороны такого регенератора заменяли Gd2O2S регенеративным материалом или Gd1,8Tb0,2S регенеративным материалом с целью исследования полученных в результате рефрижераторных характеристик. Конструкция регенератора, согласно такому техническому решению, изображена на Фигуре 5(В). Рефрижераторные характеристики Gd2O2S регенеративного материала показаны на Фигуре 6(b), а рефрижераторные характеристики Gd1,8Tb0,2S регенеративного материала показаны на Фигуре 6(с). При использовании Gd2O2S регенеративного материала выходная мощность при 4,2 К составила около 300 МВт, а низшая достигаемая температура в холостом режиме составляла около 2,7 К. При использовании Gd1,8Tb0,2S регенеративного материала выходная мощность при 4,2 К составила около 340 МВт, а низшая достигаемая температура в холостом режиме составляла около 2,65 К.
Относительные значения хладопроизводительности регенераторов, в которых использовали Gd2O2S и Gd1,8Tb0,2S регенеративные материалы, показанные на фигурах 6(b) и 6(с), представлены на фигуре 7, причем хладопроизводительность традиционного регенератора принята за 1.
Хладопроизводительность при 4,2 К регенератора с Gd2O2S регенеративным материалом (пунктирная линия) примерно вдвое превосходит соответствующее значение для традиционного регенератора, а при понижении температуры коэффициент повышения хладопроизводительности повышался и достигал значения 4 при 3 К. Хладопроизводительность Gd1,8Tb0,2S регенеративного материала (сплошная линия b) была выше в два и более раз при 4,2 К, а с уменьшением температуры коэффициент повышения хладопроизводительности повышался и достигал значения 4,5 при 3 К.
Влияние среднего размера частиц гранул на хладопроизводительность.
Для просеивания использовали сита с различным размером отверстий с целью приготовления гранул регенеративного материала с различным средним размером частиц. Другие условия были аналогичными условиям варианта 6. Рефрижераторные характеристики приготовленных гранул оценивали аналогичным образом. Полученные результаты представлены в Таблице 6. При среднем размере частиц гранул 0,05 мм или выше и 1 мм или ниже, что имеет место в образцах 16-18, высокие выходы были получены при 4,2 К. При средних размерах частиц гранул, вне указанных пределов, как это имеет место в образцах 19 и 20, выходы при 4,2 К снижались. Таким образом, предпочтительные средние размеры частиц гранул составляют 50 мкм или более и 1000 мкм или менее, более предпочтительно, 100-700 мкм и наиболее предпочтительно, 100-300 мкм, и наиболее предпочтительно, 200-300 мм.
Таблица 6. Влияние среднего размера частиц |
Образец |
Средний размер частиц гранул /Мм |
Выход при 4,2 К/мВт |
16 |
0,25 |
300 |
17 |
0,77 |
290 |
18 |
0,071 |
285 |
19 |
1,1 |
200 |
20 |
0,045 |
185 |
Сравнительный пример 3. Регенеративные материалы на основе редкоземельных оксидов
Рефрижераторные характеристики гранул из Gd2О3, которые готовили по методике варианта 6 проводя формование, классификацию и спекание, оценивали аналогичным образом. Выход при 4,2 К составлял около 100 МВт, а низшая достигаемая температура при холостом ходе составляла 3,5 К. Полученные результаты уступали результатам традиционного примера (HoCu2) в двух отношениях – по выходу и по значению низшей достигаемой температуры регенератора.
Добавка
Если говорить об объемном отношении количества HoCu2 регенеративного материала и регенеративного материала на основе оксисульфида редкоземельного металла, то количество HoCu2 составляет 20-80%, а количество оксисульфида редкоземельного металла 80-20%. При расположении оксисульфида на основе Tb на высокотемпературной стороне оксисульфида Gd, предпочтительно, чтобы HoCu2 располагался также на высокотемпературной стороне последнего для сохранения хладопроизводительности вплоть до 7 К. В том случае, когда Gd0,1Tb1,9O2S использовали в качестве оксисульфида, включающего Tb в качестве основного компонента, получали регенеративный материал, пик удельной теплоемкости которого был несколько смещен в низкотемпературную область по сравнению с Tb2O2S, однако другие характеристики такого материалы были аналогичными характеристикам Tb2O2S.
Лучший вариант осуществления изобретения (Добавление модификаторов ударной вязкости)
Далее будут описаны некоторые технические решения, в которых к оксисульфиду редкоземельного металла добавляли такую присадку, как ZrO2 с целью повышения его прочности и увеличения срока службы. Для отличия таких технических решений от вышеописанных воплощений, в которых не добавляли присадку, предлагаемые технические решения обозначались индексами 11-28. Оксисульфиды щелочных металлов, к которым не добавляли присадку, обозначались как примеры 1-12. Соответствующие таблицы идут под номерами 7-17.
Введение присадки не приводит к сильному изменению температур перехода магнитной фазы регенеративного материала на основе оксисульфида щелочноземельного металла по сравнению с материалами без таких присадок. При добавлении присадки в количестве менее 0,05 мас.% возникают проблемы, связанные со сроком службы материала при длительной работе рефрижератора. При добавлении присадки в количестве более 30 мас.% удельная теплоемкость регенеративного материала уменьшается.
При добавлении рассматриваемой присадки, кроме фазы R2O2S, образуется вторая фаза, включающая присадку и имеющая состав, отличающийся от состава основной фазы. В результате будет замедляться рост кристаллического зерна основной фазы и будет повышаться прочность за счет включения второй фазы, обладающей относительно высокой прочностью. Присадки могут рассматриваться как модификаторы ударной вязкости керамических микроструктур оксисульфидов редкоземельных металлов. Предпочтительные присадки включают AI2О3, ZrO2, муллит, Si3N4, Sialon, TiN, AIN, BN, SiC и TiC; особенно предпочтительные присадки включают ZrO2, Si3N4, Sialon, TiN, AIN, BN, SiC и TiC. Помимо указанных присадок, предпочтительными примерами таких материалов могут служить оксиды Mg, Са, Sr и Ва, а также оксиды переходных металлов с атомными номерами 22(Ti)-31(Ga) и 72(Hf). Далее, в целях простоты, такие оксиды упоминаются как оксиды щелочноземельных металлов и оксиды переходных металлов.
При добавлении любой присадки, выбранной из AI2О3, ZrO2, муллита, Si3N4, Sialon, TiN, AIN, BN, SiC, TiC, оксидов щелочноземельных металлов и оксидов переходных металлов, помимо основной фазы R2O2S, образуется вторая фаза, в присутствии которой замедляется рост кристаллических зерен основной фазы и увеличивается прочность регенеративного материала на основе оксисульфида редкоземельного металла. Соответственно, даже при длительной работе рефрижератора, гранулы регенеративного материала не разрушаются и не происходит повреждения герметизирующего или аналогичных элементов рефрижератора.
Для получения регенеративного материала на основе оксисульфида редкоземельного металла, содержащего присадку, такую присадку или ее предшественник добавляют в концентрации 0,05-30 мас.% в порошок общей формулы R2O2S, и полученную смесь формируют в гранулы. Присадку или ее предшественник в виде порошка можно добавлять в сырье, порошок редкоземельного оксида. Газ, содержащий атом серы в степени окисления -2, например, Н2S или СН3SH, пропускают через материал в условиях нагревания, что делает его реакционноспособным в отношении образования оксисульфида. После этого полученный оксисульфид формуют, например, в гранулы. Далее гранулы спекают, например, при 1400-1600°С (1673,15-1873,15 К) в течение 1-10 часов. Полученный регенеративный материал на основе оксисульфида редкоземельного металла имеет относительную плотность 98% или более и средний размер зерна 20 мкм или менее.
Так, например, присадку или ее предшественник добавляют к производимому в промышленности порошкообразному оксиду редкоземельного металла, и полученную смесь перемешивают в шаровой мельнице или аналогичном устройстве. После добавления перемешанный порошок спекают при 1073,15-1273,15 К и спеченным смешанным порошком заполняют реакционную трубку из кварца или аналогичного материала. Затем через полученный порошок пропускают газ, содержащий H2S с целью осуществления сульфуризации. В результате получают порошкообразный оксисульфид желаемого редкоземельного металла. Реакцию сульфуризации можно проводить с использованием порошка редкоземельного оксида, после чего в полученную смесь вводят присадку или ее предшественник.
Закладку регенеративного материала в рефрижератор проводят при давлении 100 кПа, как и ранее. Сравнительные исследования основной фазы R2O2S и второй фазы, имеющей отличия в микроструктуре материала подвергнутого спеканию, проводили методом рентгеновской дифракции, а распределение фазы изучали методом металлографии. Соотношение между основной фазой и второй фазой определяли путем истирания и полировки поверхности спеченного материала, фотографирования образца поверхности с помощью металлографа, измерения отношения с помощью устройства для распознавания изображения и перевода отношения площадей в объемное отношение. Размерный коэффициент гранул определяли путем фотографирования спеченных гранул с помощью микроскопа и измерения отношения между длинным и коротким размерами – с помощью устройства для распознавания изображения. Состояние разрушения гранул определяли визуально путем изучения состояния регенеративного материала, выгруженного из регенератора, и подсчета разрушенных гранул.
Пример 1
Оксисульфид редкоземельного металла получали по методике, описанной для варианта 1 (при скорости программируемого нагрева 473,15 К/час). Соответствующий образец обозначали как пример 1.
Вариант 11 Добавление оксида циркония
Оксид гадолиния, используемый в примере 1, и частично стабилизированный оксид циркония (3Y-ZrO2, 3 мол.% Y2O3 – 97 мол.% ZrO2; этот материал использовали и в последующих экспериментах) помещали в шаровую мельницу и перемешивали в течение 24 часов в среде этанола, используемого в качестве растворителя. Полученный в результате шлам сушили, подвергали обжигу (1173,15 К×3 часа). Проводили реакцию между полученным продуктом и газообразным сероводородом с получением Gd2O2S керамики, содержащей Zr (Gd2O2S, допированный Zr), следуя методике, описанной в примере 1 (гидростатическое прессование при 200 МПа, затем спекание в атмосфере аргона в течение 6 часов при 1773,15 К). Плотность полученного в результате Zr-допированного Gd2O2S установленная методом Архимеда составила 99,9% от теоретического значения, а средний размер зерен составил 1,1-1,5 мкм. В Таблице 7 приведены значения теплоемкости при температуре перехода магнитной фазы (температура, соответствующая наивысшему пику теплоемкости соответствующие количеству добавленного ZrO2) и теплоемкость при 4,2 К. Как можно видеть из таблицы 7 при добавлении ZrO2, происходит уменьшение теплоемкости при температуре перехода магнитной фазы, но в том случае, когда присадку вводят в количестве 30 мас.% и более, теплоемкость при 4,2 К составляет 0,3 J/cc.K или выше. При теплоемкостях выше 0,3 J/cc.K не наблюдалось влияния на охлаждающие характеристики регенератора.
Используемые образцы истирали и полировали и их поверхности исследовали методом рентгеновской дифракции для определения природы фаз. Распределение фаз исследовали с помощью металлографа. Было подтверждено наличие фазы, отличающейся от основной фазы. Такая фаза представляла собой фазу ZrO2 однородно диспергированную в основной фазе. В результате анализа изображения также было установлено, что с увеличением количества добавленного ZrO2 увеличивается количество ZrO2-содержащей фазы. Предполагается, что такая фаза представляет собой осажденный ZrO2, не способный присутствовать в твердом растворе основной фазы. Однако к настоящему времени в этом вопросе нет полной ясности. Естественно, что причиной повышения теплоемкости при 4,2 К с увеличением количества добавленного ZrO2 является образование фазы ZrO2. Эти наблюдения также справедливы при изменении природы редкоземельных элементов. Причина состоит в том, что материал приобретает некоторые свойства, касающиеся микроструктуры керамики и теплоемкости, когда такая вторая фаза, как ZrO2, присутствует в основной фазе R2O2S. Эти свойства не сильно зависят от природы редкоземельных элементов в том случае, когда используют одинаковую добавку.
Таблица 7 Добавление частично стабилизированного ZrO2 |
Образец |
Количество присадки/мас.% |
Теплоемкость при температуре перехода магнитной фазы /J/cc.K |
Теплоемкость при 4,2 K /J/cc.K |
Пример 1 |
Без присадки |
1,2 |
0,50 |
Вариант 11 |
0,1 |
1,2 |
0,50 |
то же |
0,5 |
1,1 |
0,50 |
” |
1 |
1,0 |
0,50 |
” |
10 |
0,89 |
0,48 |
” |
20 |
0,66 |
0,38 |
” |
30 |
0,49 |
0,32 |
” |
40 |
0,38 |
0,23 |
Вариант 12. Добавление оксида алюминия
Gd2O2S керамику, содержащую AI2О3 (AI-допированный Gd2O2S), готовили, используя AI2O3 вместо частично стабилизированного оксида циркония (3Y-ZrO2). В части, касающейся других условий, следовали методике варианта 11. Плотность полученного в результате допированного алюминием Gd2O2S составляла 99,9% от теоретического значения, определенного по методу Архимеда, а средний размер зерен составил 1,1-1,5 мкм. В Таблице 8 приведены значения теплоемкости при температуре перехода магнитной фазы (температура, соответствующая наивысшему пику теплоемкости), соответствующие количеству добавленного AI2O3 и теплоемкость при 4,2 К. Как можно видеть из таблицы 8 при добавлении AI2O3 происходит уменьшение теплоемкости при температуре перехода магнитной фазы, но в том случае, когда присадку вводят в количестве 30 мас.% и более, теплоемкость при 4,2 К составляет 0,3 J/cc.K или выше.
Таблица 8 Добавление AI2O3 |
Образец |
Количество присадки/мас.% |
Теплоемкость при температуре перехода магнитной фазы /J/cc.K |
Теплоемкость при 4,2 K/J/cc.K |
Пример 1 |
Без присадки |
1,2 |
0,50 |
Вариант 12 |
0,1 |
1,2 |
0,50 |
” |
0,5 |
1,1 |
0,50 |
” |
1 |
1,0 |
0,50 |
” |
10 |
0,87 |
0,47 |
” |
20 |
0,64 |
0,37 |
” |
30 |
0,48 |
0,33 |
” |
40 |
0,39 |
0,24 |
Вариант 13. Добавление муллита
Gd2O2S керамику, содержащую муллит, готовили, используя муллит 3Al2O3-2SiO2 вместо частично стабилизированного оксида циркония (3Y-ZrO2). Другие условия были аналогичными условиям варианта 11. Кроме этого, вместо частично стабилизированного оксида циркония (3Y-ZrO2), получали Gd2O2S керамику с использованием таких не-оксидных веществ, как Si3N4, Sialon, TiN, AIN, BN, SiC и TiC. Условия получения были такими же, что и в варианте 11, за исключением того, что перед сульфуризацией не проводили кальцинирование. При замене присадки на муллит Si3N4, Sialon, TiN, AIN, BN, SiC и TiC были получены результаты, аналогичные представленным для вариантов 11 и 12, при условии применения одинаковой присадки.
Вариант 14. Добавление СаО.
Gd2O2S керамику, содержащую СаО (Са-допированную Gd2O2S) получали, используя СаО вместо частично стабилизированного оксида циркония (SY-ZrO2). Другие условия были аналогичными используемым в варианте 11. Плотность полученного в результате Са-допированного Gd2O2S составила 99, 9% от теоретического значения, полученного по методу Архимеда, а средний размер зерна составлял 1,9-2,1 мкм. В Таблице 9 приведены значения теплоемкости при температуре перехода магнитной фазы (температура наивысшего пика теплоемкости), соответствующие добавленному количеству СаО, а также теплоемкость при 4,2 К. Как можно видеть из представленных данных, добавление СаО приводит к уменьшению теплоемкости при температуре перехода магнитной фазы, однако при введении добавки в количестве 30% и выше теплоемкость при желаемой температуре, не превышающей 10 К, составляет 0,3 J/cc.K или выше. Образец грунтовали и полировали, и поверхность исследовали методом рентгеновской дифракции для определения типа фаз. Фазовое распределение исследовали с использованием металлографа. Было подтверждено наличие фазы, содержащей СаО, отличной от основной фазы. Эта фаза однородно диспергирована в основной фазе. С увеличением добавленного количества СаО увеличивается количество фазы, содержащей СаО. Предполагается, что такая фаза образуется в результате осаждения СаО, который не может находиться в твердом растворе основной фазы.
Таблица 9 Добавление СаО |
Образец |
Количество присадки/мас.% |
Теплоемкость при температуре перехода магнитной фазы /J/cc.K |
Теплоемкость при 4,2 K/J/cc.K |
Пример 1 |
Без присадки |
1,2 |
0,50 |
Вариант 14 |
0,07 |
1,2 |
0,50 |
” |
0,7 |
1,1 |
0,50 |
” |
1,4 |
1,0 |
0,49 |
” |
14 |
0,88 |
0,47 |
” |
28 |
0,67 |
0,37 |
” |
42 |
0,47 |
0,27 |
Вариант 15
Gd2O2S керамику, содержащую MgO (Mg-допированную Gd2O2S), получали, используя MgO вместо СаО. Другие условия получения были аналогичными используемым в варианте 14. Плотность полученного в результате Mg-допированного Gd2O2S составила 99,9% от теоретического значения, полученного по методу Архимеда, а средний размер зерна составил 1,9-2,2 мкм. Подобно Са-допированной Gd2O2S, теплоемкость при 4,2 составляла 0,3 J/cc.K или более при количестве добавленного MgO 30% или менее.
Вариант 16.
Вместо СаО использовали SrO или ВаО, причем другие условия получения были теми же, что в варианте 14. Результаты, полученные с использованием Sr-допированного Gd2O2S или Ва-допированного Gd2O2S, сравнимы с результатами вариантов 14 и 15.
Вариант 17. Добавление Cr2О3
Cr2О3 использовали вместо частично стабилизированного оксида циркония с получением Gd2O2S керамики (Cr-допированная Gd2O2S). Прочие условия были аналогичными условиям варианта 11. Прочность полученной в результате Cr-допированной Gd2O2S составила 99,9% от теоретического значения, полученного по методу Архимеда, а средний размер зерен составил 2,0-2,3 мкм. В Таблице 10 представлены значения теплоемкости при температуре перехода магнитной фазы (температура наивысшего пика теплоемкости), соответствующие количеству добавленного Cr2O3, а также теплоемкость при 4,2 К. Как можно видеть из Таблицы 10, при введении Cr2О3 теплоемкость при температуре перехода магнитной фазы понижается, но при добавлении Cr2О3 в количестве 30 мас.% или менее теплоемкость при 4,2 К составляет 0,3 J/cc.K или выше. Аналогичные результаты были получены при добавлении в систему любого из переходных оксидов, отличных от Cr2О3. Образцы грунтовали и полировали и их поверхности исследовали методом рентгенофазового анализа с использованием металлографа с целью определения распределения основной и второй фаз. Было установлено, что вторая фаза, отличающаяся от основной фазы, содержащей Cr2О3, однородно распределена в основной фазе.
Таблица 10 Добавление Cr2О3 |
Образец |
Количество присадки/мас.% |
Теплоемкость при температуре перехода магнитной фазы /J/cc.K |
Теплоемкость при 4,2 K/J/cc.K |
Пример 1 |
Без присадки |
1,2 |
0,50 |
Вариант 17 |
0,07 |
1,2 |
0,50 |
” |
0,07 |
1,1 |
0,50 |
” |
1,4 |
1,0 |
0,49 |
” |
14 |
0,85 |
0,46 |
” |
28 |
0,68 |
0,38 |
” |
42 |
0,46 |
0,28 |
Вариант 18
Gd2O2S керамику, содержащую MnO (Mn-допированный Gd2O2S), получали с использованием MnO вместо Cr2О3. Другие условия были аналогичны условиям варианта 17. Плотность полученного в результате Mn-допированного Gd2O2S составляла 99,9% от теоретической плотности, определенной по методу Архимеда, а средний размер зерен составил 2,0-2,3 мкм. Аналогично Cr-допированному Gd2O2S, при добавлении MnO в количестве 30% или менее теплоемкость при 4,3 К составляла 0,3 J/cc.K или выше.
Вариант 19
Регенеративный материал на основе Gd2O2S керамики получали с использованием оксида переходного металла, отличного от Cr2О3 и MnO. Другие условия получения были аналогичными используемым в варианте 17. Результаты испытания полученного регенеративного материала были сравнимы с вариантами 17 и 18.
Вариант 20. Добавление оксида циркония к Gd-Tb композиционным оксисульфидам
Частично стабилизированный оксид циркония (3Y-ZrO2) добавляли к смеси из оксида тербия со средним размером частиц 0,69 мкм и оксида гадолиния, используемого в воплощении 11. Полученную смесь подвергали сульфуризации, формованию, гидростатическому прессованию и спеканию, следуя методике Примера 1, с целью получения гадолиний-тербиевой оксисульфидной керамики, содержащей частично стабилизированный оксид циркония (SY-ZrO2) (Zr-допированный GdxTb2-xO2S). На фигуре 8 представлены теплоемкости GdxTb2-xO2S. В Таблицах 11-13 указаны количества добавленного ZrO2 и теплоемкость при желаемой температуре для различных значений х. Примеры 2-7 относятся к системе GdxTb2-xO2S, не содержащей ZrO2. Как можно видеть из данных, представленных в Таблицах 11-13, значение теплоемкости, равное 0,3 J/cc.K или выше сохраняется в относительно широком интервале температур в области 10К или ниже. При значениях х 1, Zr-допированный GdxTb2-xO2S может использоваться в качестве регенеративного материала в области 4,2 К. При значениях х<0,1 рассматриваемая система может использоваться в качестве регенеративного материала в области 6-7К. Даже при добавлении ZrO2 в количестве до 30 мас.% теплоемкость при любой желаемой температуре в области 10 К или ниже никогда не понижается до значений менее 0,3 J/cc.K. Аналогичные результаты были получены при замене Gd или Tb на такие другие редкоземельные элементы, как Dy или Но.
Таблица 11 Добавление ZrO2 |
Образец |
Количество присадки/мас.% |
Значение х |
Теплоемкость при 4,2 K/J/cc.K |
Пример 2 |
Без присадки |
1,8 |
0,55 |
Вариант 20 |
0,1 |
1,8 |
0,55 |
” |
0,5 |
1,8 |
0,55 |
” |
1 |
1,8 |
0,55 |
” |
10 |
1,8 |
0,51 |
” |
20 |
1,8 |
0,41 |
” |
30 |
1,8 |
0,36 |
” |
40 |
1,8 |
0,26 |
Пример 3 |
Без присадки |
1 |
0,59 |
Вариант 20 |
0,1 |
1 |
0,59 |
” |
0,5 |
1 |
0,59 |
” |
1 |
1 |
0,59 |
” |
10 |
1 |
0,55 |
” |
20 |
1 |
0,43 |
” |
30 |
1 |
0,39 |
” |
40 |
1 |
0,28 |
Таблица 12 Добавление ZrO2 |
Образец |
Количество присадки/мас.% |
Значение х |
Теплоемкость при 4,2 K/J/cc.K |
Пример 4 |
Без присадки |
0,2 |
0,71 |
Вариант 20 |
0,1 |
0,2 |
0,71 |
” |
0,5 |
0,2 |
0,71 |
” |
1 |
0,2 |
0,71 |
” |
10 |
0,2 |
0,68 |
” |
20 |
0,2 |
0,5 |
” |
30 |
0,2 |
0,41 |
” |
40 |
0,2 |
0,29 |
Таблица 13 Добавление ZrO2 |
Образец |
Количество присадки/мас.% |
Значение х |
Теплоемкость при 4,2 K/J/cc.K |
Пример 5 |
Без присадки |
0,1 |
1 |
Вариант 20 |
0,1 |
0,1 |
1 |
” |
0,5 |
0,1 |
1 |
” |
1 |
0,1 |
0,93 |
” |
10 |
0,1 |
0,84 |
” |
20 |
0,1 |
0,64 |
” |
30 |
0,1 |
0,56 |
” |
40 |
0,1 |
0,28 |
Пример 6 |
Без присадки |
0,05 |
1,2 |
Вариант 20 |
0,1 |
0,05 |
1,2 |
” |
0,5 |
0,05 |
1,2 |
” |
1 |
0,05 |
1,1 |
” |
10 |
0,05 |
0,92 |
” |
20 |
0,05 |
0,73 |
” |
30 |
0,05 |
0,51 |
” |
40 |
0,05 |
0,29 |
Пример 7 |
Без присадки |
0 |
0,88 |
Вариант 20 |
0,1 |
0 |
0,88 |
” |
0,5 |
0 |
0,88 |
” |
1 |
0 |
0,88 |
” |
10 |
0 |
0,72 |
” |
20 |
0 |
0,51 |
” |
30 |
0 |
0,42 |
” |
40 |
0 |
0,28 |
Вариант 21
Керамический регенеративный материал готовили с использованием AI2O3, муллита, таких не-оксидных компонентов, как Si3Н4, Sialon, TiN, AIN, BN, SiC, TiC, вместо частично стабилизированного оксида циркония (3Y-ZrO2). Другие условия получения были аналогичными используемым в варианте 20. При использованием GdxTb2-xO2S керамики, модифицированной присадками различной природы, были получены результаты, сравнимые с результатами технического решения 20.
Вариант 22
Керамические материалы на основе гадолиний-тербиевого оксисульфида (Са-допированный GdxTb2-xO2S) были получены путем замены частично стабилизированного оксида циркония (SY-ZrO2) на любой из оксидов щелочноземельных металлов (MgO, СаО, SrO, ВаО). Прочие условия получения были аналогичны условиям варианта 20. Теплоемкостные характеристики таких керамических материалов демонстрировали тенденции, аналогичные характеристикам Zr-допированного GdxTb2-xO2S, при содержании оксида щелочноземельного металла 30 мас.% или менее.
Вариант 23
Регенеративные материалы на основе гадолиний-тербиевой оксисульфидной керамики (Са-допированный GdxTb2-xO2S) готовили путем замены частично стабилизированного оксида циркония на любой из оксидов переходных металлов (оксиды элементов с атомными номерами 22(Ti)-31(Ga) и 72(Hf)). Прочие условия получения были аналогичны условиям, используемым в варианте 20. Результаты, полученные при использовании таких материалов, были аналогичными результатам в присутствии Zr-допированного GdxTb2-xO2S, содержащего 30 мас.% или более оксида переходного металла.
Вариант 24. Срок службы при непрерывной эксплуатации
Порошки Zr-допированного Gd2O2S (после сульфуризации и до спекания), согласно варианту 11, формовали в сферические частицы путем гранулирования в барабане, и полученные гранулы просевали через два типа фильтрующих сеток (сито А (отверстие: 597 мкм) и сито В (отверстие: 435 мкм)). Просеянные гранулы вальцевали с использованием зеркально обработанной железной плиты, расположенной с наклоном в 25°. Скатившиеся гранулы собирали и подвергали их классификации по размеру. Средний размер частиц 100 гранул составил 0,5 мм. Средний размер частиц Zr-допированного Gd2O2S измеряли по изображению, полученному с использованием широкоформатного видеоскопа.
Полученные гранулы Zr-допированного Gd2O2S загружали в алюминиевый тигель и подвергали спеканию в атмосфере аргона описанным выше способом. Спекание проводили в течение 6 часов при температуре 1500°С. В результате получали регенеративные материалы на основе Zr-допированного Gd2O2S, со средним размером частиц 0,4 мм и средним размерным коэффициентом 1,1. Средний размер частиц и средний размерный коэффициент регенеративных материалов на основе Zr-допированного Gd2O2S измеряли с использованием широкоформатного видеоизображения. Плотность Gd2O2S регенеративных материалов измеренная с помощью пикнометра составила 99,9% от теоретического значения, при среднем размере зерна 1,1-1,5 мкм.
В условиях, аналогичных условиям варианта 6, поверхность регенеративных материалов на основе Zr-допированного Gd2O2S обрабатывали методом роторного галтования. Полученные Zr-допированные Gd2O2S регенеративные материалы загружали в регенератор GM рефрижератора и методом, аналогичным используемому в варианте 6, определяли степень разрушения гранул через 1500, 2500 и 10000 часов непрерывной эксплуатации. Полученные результаты представлены в Таблице 14. Пример 8 относится к керамическим гранулам на основе Gd2O2S, к которым не добавляли ZrO2. В присутствии ZrO2, добавленного в количестве 0,05 мас.% или более, не возникало никаких проблем даже через 10000 часов. При добавлении присадки в количестве 0,01% срок службы генеративного материала практически не изменялся. Полученный результат, по-видимому, связан с отсутствием упрочняющей фазы (фаза ZrO2). Аналогичные закономерности наблюдались при замене Gd на другой редкоземельный элемент, например, на Dy или Но.
Таблица 14 Добавление ZrO2 |
Образец |
Количество добавки /мас.% |
Через 1500 ч работы |
Через 100000 часов работы |
Пример 8 |
Отсутствует |
Разрушено около 5% гранул |
– |
Вариант 24 |
0,01 |
Разрушено около 5% гранул |
– |
” |
0,05 |
Отсутствие |
Отсутствие |
|
|
проблем |
проблем |
” |
0,5 |
” |
” |
” |
1 |
” |
” |
” |
10 |
” |
” |
” |
20 |
” |
” |
” |
30 |
” |
” |
” |
40 |
” |
” |
Вариант 25
Использовали порошки Gd2O2S (после сульфуризации и до спекания), полученные в варианте 12 (AI2O3) и варианте 13 (муллит), причем прочие условия обработки были аналогичными условиям варианта 24. Гранулы непрерывно подвергались GM рефрижерации в ходе рабочего цикла и степень их разрушения оценивали через 1500, 2500 и 10000 часов эксплуатации. Как и в случае керамических гранул из Zr-допированного Gd2O2S, керамические гранулы, содержащие присадку в количестве 0,05 мас.% или более не создавали никаких проблем даже через 10000 часов непрерывной эксплуатации в GM рефрижераторе. Однако при введении в керамические гранулы присадки в количестве менее 0,05 мас.% наблюдалось сильное измельчение гранул через 1500 часов непрерывной эксплуатации.
Вариант 26
Использовали порошки Gd2O2S (к которым добавляли оксиды щелочноземельных металлов), описанные в вариантах 14-16, причем другие условия обработки были аналогичными условиям варианта 24. Гранулы непрерывно подвергались эксплуатации в GM рефрижераторе и степень их разрушения оценивали через 1500, 2500 и 10000 часов работы. Результаты добавления СаО представлены в Таблице 15. Керамические гранулы, к которым добавляли СаО в количестве 0,05 мас.% или более, подвергались сильному разрушению через 10000 часов непрерывной эксплуатации. С другой стороны, гранулы, в которые добавляли СаО в количестве, меньшем 0,05 мас.%, сильно измельчались через 1500 часов непрерывной эксплуатации. Аналогичные закономерности наблюдались при замене СаО на другие оксиды щелочноземельных металлов, например, MgO, SrO, или ВаО, или при замене Gd на другой редкоземельный элемент, например, на Dy или Но.
Таблица 15 Добавление СаО |
Образец |
Количество добавки /мас.% |
Через 1500 ч работы |
Через 2500 ч работы |
Через 100000 часов работы |
Пример 8 |
Без добавки |
примерно 5% разрушение |
– |
|
Вариант 26 |
0,01 |
примерно 5% разрушение |
– |
|
” |
0,07 |
отсутствие |
отсутствие |
примерно 20% |
|
|
проблем |
проблем |
разрушение |
” |
0,7 |
отсутствие |
отсутствие |
примерно 15% |
|
|
проблем |
проблем |
разрушение |
” |
1,4 |
” |
” |
” |
” |
14 |
” |
” |
примерно 10% |
|
|
|
|
разрушение |
” |
28 |
” |
” |
” |
” |
42 |
” |
” |
” |
Вариант 27. Добавление оксидов переходных металлов.
Использовали порошки Gd2O2S, к которым добавляли оксиды переходных металлов в вариантах 17-19, причем другие условия получения были аналогичными условиям варианта 24. Гранулы непрерывно подвергались эксплуатации в GM рефрижераторе и степень их разрушения оценивали через 1500, 2500 и 10000 часов работы. Полученные результаты были аналогичными результатам для гранул, к которым добавляли оксиды щелочноземельных металлов. Керамические регенеративные материалы, к которым добавляли оксид переходного металла в количестве 0,05 мас.% или выше, выдерживали 2500 часов непрерывной эксплуатации, но не выдерживали 10000 часов непрерывной эксплуатации. Керамические регенеративные материалы, в которые добавляли оксид переходного металла в количестве менее 0,05 мас.%, через 1500 часов непрерывной эксплуатации содержали сильно измельченные гранулы. Аналогичные закономерности наблюдались при замене Gd на другой редкоземельный элемент, например, на Dy или Но.
Вариант 28. Срок службы Gd-Tb композитных оксисульфидов
По аналогии с образцами, описанными в варианте 20, изменяя значение «х» и сохраняя другие условия аналогичными варианту 24, получали керамические гранулы, в которые добавляли ZrO2. Степень разрушения гранул, связанную со значением х в GdxTb2-xO2S, оценивали в ходе эксплуатационного цикла GM рефрижерации, используемого в варианте 24. Полученные результаты представлены в Таблице 16. Примеры 9-12 относятся к GdxTb2-xO2S керамическим гранулам, в которые добавляли ZrO2. При изменении коэффициента х в формуле GdxTb2-xO2S керамические гранулы, в которые добавляли 0,05 мас.% или более ZrO2 не создавали проблем даже через 10000 часов непрерывной эксплуатации в GM рефрижераторе. С другой стороны, керамические гранулы, в которые добавляли менее 0,05 мас.% ZrO2 сильно измельчались через 1500 часов непрерывной эксплуатации.
Таблица 16 Добавление ZrO2 |
Образец |
Количество присадки, мас.% |
Значение x |
Через 1500 ч работы |
Через 10000 ч работы |
Пример 9 |
Без присадки |
1,8 |
Разрушено 5% |
– |
Вариант 28 |
0,01 |
1,8 |
Разрушено 5% |
– |
” |
0,05 |
1,8 |
Отсутствие |
Отсутствие |
|
|
|
проблем |
проблем |
” |
0,01 |
1,8 |
Отсутствие |
Отсутствие |
|
|
|
проблем |
проблем |
” |
1 |
1,8 |
Отсутствие |
Отсутствие |
|
|
|
проблем |
проблем |
” |
10 |
1,8 |
” |
” |
” |
30 |
1,8 |
” |
” |
Пример 10 |
Без присадки |
1 |
Разрушено 5% |
– |
Вариант 28 |
0,05 |
1 |
Отсутствие проблем |
Отсутствие проблем |
” |
0,1 |
1 |
Отсутствие |
Отсутствие |
|
|
|
проблем |
проблем |
” |
1 |
1 |
” |
” |
” |
10 |
1 |
” |
” |
” |
30 |
1 |
” |
” |
Пример 11 |
Без присадки |
0,2 |
Разрушено 5% |
– |
Вариант 28 |
0,05 |
0,2 |
Отсутствие проблем |
Отсутствие проблем |
” |
0,1 |
0,2 |
Отсутствие |
Отсутствие |
|
|
|
проблем |
проблем |
” |
1 |
0,2 |
” |
” |
” |
10 |
0,2 |
” |
” |
” |
30 |
0,2 |
” |
” |
Пример 12 |
Без присадки |
0 |
Разрушено 5% |
– |
Вариант 28 |
0,05 |
0 |
Отсутствие проблем |
Отсутствие проблем |
” |
0,1 |
0 |
” |
” |
” |
1 |
0 |
” |
” |
” |
10 |
0 |
” |
” |
” |
30 |
0 |
” |
” |
Выводы, касающиеся действия присадок
В соответствии с изложенным выше, наилучшими свойствами, касающимися срока службы в ходе непрерывной эксплуатации рефрижераторов и значений теплоемкости, обладают керамические гранулы, в которые добавляют любое из следующих веществ, AI2О3, ZrO2, муллит, Si3N4, Sialon, TiN, AIN, BN, SiC и TiC в количестве 0,05-30 мас.%, за ними следуют керамические гранулы, в которые добавлены оксиды любых щелочноземельных металлов (оксиды Mg, Са, Sr и Ва) и оксиды переходных металлов (оксиды элементов с атомными номерами от 22(Ti) до 31(Ga) и 72(Hf) в количестве 0,05-30 мас.%.
Хладопроизводительность
Рефрижераторные характеристики регенеративных материалов, Zr-допированного Gd2O2S, в который добавлено 10 мас.% ZrO2 (вариант 24), AI-допированного Gd2O2S, в который добавлено 10 мас.% Al2O3 (вариант 25) и Zr-допированного Gd1,8Tb0,2O2S, в которой добавляли 10 мас.% ZrO2 (вариант 28), Gd2O2S без добавок (пример 8) и Gd1,8Tb0,2O2S без добавок, исследовали в двухступенчатом GM рефрижераторе с потреблением энергии 3,4 кВт. В традиционном рефрижераторе, в котором используется Pb, для регенератора первой стадии со стороны повышенной температуры и HoCu2 используется в регенераторе второй стадии, хладопроизводительность при 4,2 К составила 1,31 кВт, а низшая температура, достигаемая на холостом ходу, составляла 2,79 К.
50% HoCu2 со стороны пониженный температур на второй стадии заменяли на такие регенеративные материалы, как Zr-допированный Gd2O2S, в который добавлено 10 мас.% ZrO2 (вариант 24), AI-допированный Gd2O2S, в который добавлено 10 мас.% Al2O3 (вариант 25) и Zr-допированный Gd1,8Tb0,2O2S, в которой добавляли 10 мас.% ZrO2 (вариант 28). После этого измеряли значения хладопроизводительности. Полученные результаты представлены в Таблице 17. Регенеративные материалы рассматриваемых вариантов демонстрировали хладопроизводительности и низшие достигаемые температуры, сравнимые с соответствующими значениями регенеративных материалов на основе оксисульфидов редкоземельных металлов, в которые не добавляли присадок.
Таблица 17 Хладопроизводительности |
Образец |
Тип образца |
Хладопроизводительность (4,2 K)/ватт |
Низшая достигаемая температура/К |
Традиционный |
HoCu2 |
1,31 |
2,79 |
Пример 8 |
Gd2O2S |
1,69 |
2,62 |
Пример 9 |
Gd1,8Tb0,2O2S |
1,73 |
2,61 |
Вариант 24 |
ZrO2-10 мас.%/Gd2O2S |
1,68 |
2,62 |
Вариант 25 |
Al2O3-10 мас.%/Gd2O2S |
1,68 |
2,63 |
Вариант 28 |
ZrO2-10 мас.%/Gd1,8Tb0,2O2S |
1,73 |
2,62 |
Заключение по применению присадок
Как указано выше, наилучшими свойствами, касающимися срока службы в ходе непрерывной эксплуатации рефрижераторов и значений теплоемкости, обладают керамические гранулы, в которые добавляют любое из следующих веществ: Al2O3, ZrO2, муллит, Si3N4, Sialon, TiN, AIN, BN, SiC и TiC в количестве 0,05-30 мас.%, за ними следуют керамические гранулы, в которые добавлены оксиды любых щелочноземельных металлов (оксиды Mg, Са, Sr и Ва) и оксиды переходных металлов (оксиды элементов с атомными номерами от 22(Ti) до 31(Ga) и 72(Hf)) в количестве 0,05-30 мас.%.
Описание технических решений главным образом сконцентрировано на Gdx,8Tb2-xO2S. Другие регенеративные материалы на основе оксисульфидов редкоземельных металлов, к которым добавляют Al2О3, ZrO2, муллит, Si3N4, Sialon, TiN, AIN, BN, SiC или TiC в количестве 0,05-30 мас.%, не создают каких-либо проблем даже через 10000 часов непрерывной эксплуатации GM рефрижератора. При добавлении оксидов любых щелочноземельных металлов (оксиды Mg, Са, Sr и Ва) и оксидов переходных металлов (оксиды элементов с атомными номерами от 22(Ti) до 31(Ga) и 72(Hf)) в количестве 0,05-30 мас.%, соответствующие варианты не создавали каких-либо проблем через 2500 часов непрерывной эксплуатации GM рефрижератора.
Формула изобретения
1. Регенеративный материал на основе оксисульфида редкоземельного металла, включающий оксисульфид редкоземельного металла, отвечающий общей формуле R2O2S, где R представляет собой, по меньшей мере, один из редкоземельных элементов, выбранных из группы, состоящей из La, Се, Pr, Nd, Sm, Eu, Gd, Tb, Dy, Ho, Er, Tm, Yb и Lu, а также Y.
2. Оксисульфидный регенеративный материал по п.1, отличающийся тем, что оксисульфид редкоземельного металла представляет собой Gd2-xTbxO2S, где х составляет 0,2-2.
3. Оксисульфидный регенеративный материал по п.2, отличающийся тем, что значение х в указанном оксисульфиде редкоземельного металла Gd2-xTbxO2S составляет 1,6-2.
4. Оксисульфидный регенеративный материал по п.1, отличающийся тем, что оксисульфид редкоземельного металла представляет собой оксисульфид Но или Dy.
5. Оксисульфидный регенеративный материал по п.1, отличающийся тем, что оксисульфид редкоземельного металла имеет форму гранул.
6. Регенеративный материал на основе оксисульфида редкоземельного металла по п.5, отличающийся тем, что гранулы указанного регенеративного материала на основе оксисульфида редкоземельного металла имеют средний размер частиц 50-1000 мкм.
7. Регенеративный материал на основе оксисульфида редкоземельного металла по п.5, отличающийся тем, что величина среднего значения отношения наибольшего размера к наименьшему размеру указанных гранул имеет значение не более 3.
8. Регенеративный материал на основе оксисульфида редкоземельного металла по п.5, отличающийся тем, что относительная плотность гранул указанного оксисульфида редкоземельного металла имеет значение не менее 96%.
9. Регенеративный материал на основе оксисульфида редкоземельного металла по п.5, отличающийся тем, что средний размер кристаллического зерна гранул оксисульфида редкоземельного металла имеет значение не более 100 мкм.
10. Регенеративный материал на основе оксисульфида редкоземельного металла по п.5, отличающийся тем, что шероховатость поверхности указанных гранул имеет значение не более 10 мкм относительно стандартной максимальной высоты Rmax.
11. Регенеративный материал на основе оксисульфида редкоземельного металла по п.5, отличающийся тем, что избыточное содержание серы в указанных гранулах не превышает 10000 мас.ч./млн.
12. Регенеративный материал на основе оксисульфида редкоземельного металла по п.5, отличающийся тем, что максимальное значение объемной удельной теплоемкости указанных гранул приводится при температуре 7-2 К.
13. Регенеративный материал на основе оксисульфида редкоземельного металла по п.1, отличающийся тем, что присадка, содержащая оксид, карбид или нитрид, по крайней мере, одного члена из группы, включающей щелочноземельные металлы, переходные металлы и элементы 3b и 4b групп Периодической системы, включая В и исключая С подгруппы, добавляется к оксисульфиду редкоземельного металла в количестве 0,05-30 мас.%.
14. Регенеративный материал на основе оксисульфида редкоземельного металла по п.13, отличающийся тем, что оксисульфид редкоземельного металла представляет собой Tb2O2S или композитный оксисульфид редкоземельного металла, включающий Gd или Tb.
15. Регенеративный материал на основе оксисульфида редкоземельного металла по п.13, отличающийся тем, что указанная присадка представляет собой, по меньшей мере, одно соединение, выбранное из группы, состоящей из Al2O3, ZrO2, муллита, Si3N4, Sialon, TiN, AIN, BN, SiC и TiC.
16. Регенеративный материал на основе оксисульфида редкоземельного металла по п.15, отличающийся тем, что указанная присадка представляет собой, по меньшей мере, одно соединение, выбранное из группы, состоящей из ZrO2, Si3N4, Sialon, TiN, AIN, BN, SiC и TiC.
17. Регенеративный материал на основе оксисульфида редкоземельного металла по п.13, отличающийся тем, что указанная присадка представляет собой оксид, по меньшей мере, одного щелочноземельного металла, выбранного из группы, состоящей из Mg, Ca, Sr и Ва.
18. Регенеративный материал на основе оксисульфида редкоземельного металла по п.13, отличающийся тем, что указанная присадка представляет собой оксид, по меньшей мере, одного переходного металлического элемента, выбранного из группы, включающей химические элементы с атомными номерами 22(Ti)-31(Ga) и 72(Hf).
19. Регенеративный материал на основе оксисульфида редкоземельного металла по п.13, отличающийся тем, что регенеративный материал на основе оксисульфида редкоземельного металла содержит основную фазу R2O2S и вторую фазу, включающую указанную присадку в микроструктуре керамики, причем такая вторая фаза отличается от основной фазы.
20. Регенератор с насадкой из регенеративного материала на основе оксисульфида редкоземельного металла, содержащий оксисульфид редкоземельного металла общей формулы R2O2S, где R обозначает, по крайней мере, один редкоземельный элемент, выбранный из группы, состоящей из La, Се, Pr, Nd, Sm, Eu, Gd, Tb, Dy, Ho, Er, Tm, Yb и Lu, а также Y.
21. Регенератор по п.20, отличающийся тем, что HoCu2 в качестве регенеративного материала, работающего при относительно высокой температуре, и регенеративный материал на основе оксисульфида редкоземельного металла в качестве материала, работающего при относительно низкой температуре, послойно загружают в регенератор.
22. Регенератор по п.20, отличающийся тем, что регенеративный материал на основе оксисульфида Tb загружают в слой, предназначенный для работы при относительно высокой температуре, а регенеративный материал на основе оксисульфида Gd загружают в другой слой, предназначенный для работы при относительно низкой температуре.
23. Регенератор по п.22, отличающийся тем, что Но или Dy оксисульфидный регенеративный материал укладывают в виде дополнительного слоя на низкотемпературной стороне слоя регенеративного материала на основе оксисульфида Gd.
24. Регенератор по п.20, отличающийся тем, что присадку, содержащую оксид, карбид или нитрид щелочноземельных металлов, переходных металлов или элементов 3b и 4b групп Периодической системы, включая В и исключая С подгруппы, добавляют в оксисульфид редкоземельного металла в количестве 0,05-30 мас.%.
25. Регенератор по п.24, отличающийся тем, что указанная присадка представляет собой, по крайней мере, одно соединение, выбранное из группы, состоящей из ZrO2, Si3N4, Sialon, TiN, AIN, BN, SiC и TiC.
РИСУНКИ
|
|