|
(21), (22) Заявка: 2005120227/06, 30.06.2005
(24) Дата начала отсчета срока действия патента:
30.06.2005
(46) Опубликовано: 10.02.2007
(56) Список документов, цитированных в отчете о поиске:
RU 2144995 C1, 27.01.2000. RU 2038513 C1, 27.06.1995. ШТОДА А.В. и др. Конструкция авиационных двигателей. ВВИА, 1959, с.114-117. SU 1792123 A1, 20.05.1995. RU 2219359 C1, 20.12.2003. US 5160251 A, 03.11.1992. DE 3617403 A, 04.12.1986.
Адрес для переписки:
105118, Москва, пр-кт Буденного, 16, ФГУП “Московское машиностроительное производственное предприятие “Салют”, ПЛО, С.Е. Кирееву
|
(72) Автор(ы):
Имаев Тахир Фатехович (RU), Родин Евгений Валерьевич (RU)
(73) Патентообладатель(и):
Федеральное государственное унитарное предприятие “Московское машиностроительное производственное предприятие “Салют” (RU)
|
(54) УЗЕЛ ОПОРЫ ГАЗОТУРБИННОГО ДВИГАТЕЛЯ
(57) Реферат:
Изобретение относится к энергетическому и транспортному машиностроению, в частности к системам смазки подшипниковых опор газотурбинных двигателей, и может быть использовано для подачи масла в подшипники, например межроторные подшипники высокотемпературных авиационных газотурбинных двигателей. Техническим результатом, на достижение которого направлено заявляемое изобретение, является повышение надежности работы подшипника и, следовательно, всего двигателя путем улучшения условий смазки подшипника и его охлаждения и обеспечение повышения ресурса двигателя. Указанный технический результат достигается тем, что узел опоры газотурбинного двигателя содержит подшипник с роликом, внутренним кольцом и сепаратором, причем узел опоры выполнен с возможностью подвода масла к подшипнику, а во внутреннем кольце подшипника дополнительно выполнен, по меньшей мере, один канал для подвода масла к беговой дорожке внутреннего кольца подшипника, причем для канала выполняется отношение 20°  90°, где – угол между осью канала и осью вращения подшипника. Для подшипника узла опоры выполняется соотношение B/L=1,1-5,0, где В – ширина сепаратора, L – ширина ролика. В узле опор газотурбинного двигателя подвод масла к беговой дорожке внутреннего кольца подшипника может быть осуществлен в выполненные во внутренней обойме подшипника канавки выхода шлифовального круга. 1 з.п. ф-лы, 2 ил.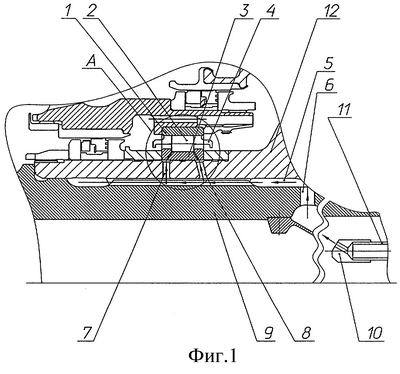
Изобретение относится к энергетическому и транспортному машиностроению, в частности к системам смазки подшипниковых опор газотурбинных двигателей, и может быть использовано для подачи масла в подшипники, например межроторные подшипники высокотемпературных авиационных газотурбинных двигателей.
Широко известны различные устройства для подачи масла к опорам подшипников от общей маслосистемы газотурбинного двигателя (ГТД), содержащие маслоподводящие форсунки струйного типа. Каждая форсунка содержит корпус с форсуночным каналом подвода масла к рабочим органам подшипника, соединенный с масляной магистралью двигателя, причем отверстия форсуночных каналов имеют расчетный размер в соответствии с требованиями и условиями смазки (Штода А.В. и др. «Конструкция авиационных двигателей», изд. ВВИА, 1959 г., с.114-117).
Данные конструкции оправдывают себя для двигателей, работающих в режимах невысоких температур.
Однако подшипниковые опоры роторов, особенно роторов турбин современных высокотемпературных газотурбинных авиадвигателей подвергаются воздействию температур порядка 300°С из-за подвода к ним тепла от горячих газов работающего двигателя, а после его останова – от нагретых до высокой температуры массивных деталей турбины.
Известен узел опоры газотурбинного двигателя, содержащий подшипник с роликом, внутренним кольцом и сепаратором, соединенный каналами подвода масла с валом. В этом решении используется подшипник, содержащий так называемый сепаратор «с крылышками», а также каналы, выполненные во втулке и позволяющие осуществлять подвод масла к подшипнику (патент РФ №2038513, МПК 6: F 04 D 29/04, дата публикации 1995.06.27) – аналог.
Недостатком данного решения является: то, что масло не попадает на внутреннее кольцо подшипника, а захватывается «крылышками» сепаратора, выполняющими функцию улавливания масла. Таким образом, смазываются только ролики и внешнее кольцо подшипника, что не обеспечивает эффективную смазку подшипника и отвод тепла.
Так же известен узел опоры газотурбинного двигателя, в котором масло на подшипник с роликом, внутренним кольцом и сепаратором подается следующим образом. Через отверстия, выполненные в цапфе носка турбины низкого давления, масло попадает в кольцевые коллекторы и через форсунки подается в подшипник в осевом направлении (патент РФ №2144995, F 02 C 7/06, дата публикации – 2000.01.27) – прототип.
Недостатком данной конструкции является, то, что масло из форсунок отбрасывается центробежными силами непосредственно на наружное кольцо подшипника, а на внутреннее кольцо подшипника масло попадает в незначительном количестве, недостаточном для обеспечения надежной работы подшипника и двигателя в целом.
Техническим результатом, на достижение которого направлено заявляемое изобретение, является повышение надежности работы подшипника и, следовательно, всего двигателя путем улучшения условий смазки подшипника и его охлаждения и обеспечение повышения ресурса двигателя.
Указанный технический результат достигается тем, что узел опоры газотурбинного двигателя содержит подшипник с роликом, внутренним кольцом и сепаратором, причем узел опоры выполнен с возможностью подвода масла к подшипнику, а во внутреннем кольце подшипника дополнительно выполнен, по меньшей мере, один канал для подвода масла к беговой дорожке внутреннего кольца подшипника, причем для канала выполняется отношение 20°  90°, где – угол между осью канала и осью вращения подшипника.
Для подшипника узла опоры может выполняться соотношение B/L=1,1-5,0, где В – ширина сепаратора, L – ширина ролика.
В узле опор газотурбинного двигателя подвод масла к беговой дорожке внутреннего кольца подшипника может быть осуществлен в выполненные во внутреннем кольце подшипника канавки выхода шлифовального круга.
Заявляемое изобретение характеризуется тем, что для достижения заявляемого технического результата необходимо, чтобы во внутреннем кольце подшипника дополнительно был выполнен, по меньшей мере, один канал для подвода масла к беговой дорожке внутреннего кольца подшипника, причем для канала выполняется отношение 20°  90°, где – угол между осью канала и осью вращения подшипника, причем для подшипника может выполняться соотношение B/L=1,1-5,0, где В – ширина сепаратора, L – ширина ролика, а подвод масла к беговой дорожке внутреннего кольца подшипника может быть осуществлен в выполненные во внутреннем кольце подшипника канавки выхода шлифовального круга.
Такое выполнение обусловлено следующим:
Для обеспечения эффективности смазки подшипника требуется поступление смазки ко всем рабочим поверхностям подшипника, например к ролику подшипника. Внутреннее кольцо подшипника, особенно в случае наличия направляющих бортов находится в зоне масляного «голодания» и для обеспечения ее смазки требуется непосредственный подвод масла на ее рабочую поверхность, что обеспечивается выполнением в ней каналов подвода масла.
Масло поступает по каналам под действием центробежных сил. Эффективность скорости поступления масла зависит от угла между осью канала и осью вращения подшипника, а следовательно, и двигателя.
Выполнение, по меньшей мере, одного из каналов под углом 20°  90°, где – угол между осью канала и осью вращения подшипника, позволяет получить заявляемый технический результат, который может быть оптимизирован тем, что подвод масла непосредственно к внутреннему кольцу подшипника может быть осуществлен в выполненные во внутреннем кольце подшипника канавки выхода шлифовального круга.
Для конкретного подшипника выполненные в нем каналы могут иметь как одинаковый диаметр, так и различные диаметры. Это зависит от конструкции узла опоры ГТД, от рекомендуемого расхода масла через подшипник и от количества каналов, выполненных во внутренней обойме подшипника, причем взаимное радиальное угловое расположение каналов с обеих сторон может быть различным, т.е. оси каналов могут быть расположены как в одной, так и в разных плоскостях.
Выполнение для подшипника узла опоры соотношения B/L=1,1-5,0, где В – ширина сепаратора, L – ширина ролика, позволяет дополнительно обеспечить компактность конструкции всей масляной магистрали и повысить улавливание и удержание масла в подшипнике.
При выполнении угла наклона каналов меньше 20° и больше 90° к оси вращения подшипника приведет к уменьшению надежности подшипника из-за увеличения потерь в скорости и дополнительного расхода масла, а также из-за значительного увеличения габаритов и усложнения всего подшипникового узла.
Для обеспечения более полного улавливания и удержания масла в подшипнике отношение B/L должно быть в пределе от 1,1 до 5,0. Соотношение меньше 1,1 не обеспечит улавливания масла, а при соотношении больше 5,0 масло, не попадая в подшипник, будет вытесняться на слив, что значительно увеличит габариты конструкции и ухудшит прочностные характеристики узла опоры газотурбинного двигателя.
Осуществление подвода масла именно через отверстия, выполненные во внутреннем кольце подшипника и выходящие в канавки выхода шлифовального круга, обеспечивает целостность беговой дорожки и направляющих бортов подшипника, что увеличивает ресурс и оптимизирует прочностные характеристики, а следовательно, и надежность работы подшипникового узла.
Заявляемое решение иллюстрируется чертежами, представленными на фиг.1 и 2, где на фиг.1 – узел опоры газотурбинного двигателя (ГТД), на фиг.2 – увеличенный вид А фиг.1.
Узел опоры ГТД, например узел опоры турбины ГТД, включает подшипник 1 с роликом 2, внутренним кольцом 3 и сепаратором с «крылышками» 4, канавки 5, 6 и каналы 7 и 8 подвода масла, вал 9 турбины, форсунку 10, масляный коллектор 11, закрепленный на корпусе опоры турбины, и носок турбины 12. Во внутреннем кольце 3 подшипника дополнительно выполнены каналы 13 и 14, служащие для подвода масла к подшипнику 1. Каналы 13 и 14 выполнены во внутреннем кольце 3 подшипника 1 с образованием между их осями и осью вращения подшипника углов 20°-90°, например 45°. Каналы 13 и 14, выполненные во внутреннем кольце подшипника 1, могут быть соединены с каналами вала 7 и 8 или непосредственно (в случае отсутствия цапфы), или через вал 9 и соответственно через каналы 5 и 6, выполненные в вале 9.
Каналы 13 и 14 могут быть выполнены таким образом, что они соединяют вал 9 с канавками выхода шлифовального круга (проточками) 15 и 16, выполненными во внутреннем кольце 3 и образующими полости между внутренним кольцом 3 подшипника 1 и роликом 2.
Устройство работает следующим образом.
Через форсунку 10 масляного коллектора 11, закрепленного на корпусе опоры турбины, масло под давлением от маслонасоса (на чертеже не показан) подается во внутреннюю полость вала 9, где за счет его конструктивного выполнения, например распорного кольца, формируется масляная ванна. Далее за счет центробежных сил, возникающих от вращения вала 9 турбины, например турбины низкого давления, масло попадает через отверстия в вале 9 в пространство, образованное наружной поверхностью вала и внутренней поверхностью носка 12 турбины низкого давления. Далее масло перемещается в радиальные каналы, выполненные в носке 12 турбины низкого давления под внутренним кольцом 13 подшипника 1.
Далее масло подается во внутреннее кольцо 3 подшипника по каналам 13 и 14, выполненным во внутреннем кольце 3, при этом масло подается под углом к вертикальной оси и попадает на ролик 2 и внутреннее кольцо 3 подшипника, например межроторного подшипника. «Крылышки» сепаратора 4 удерживают масло в подшипнике 1, что повышает эффективность смазки и теплоотдачи.
Преимущество данного решения заключается в следующем:
– масло поступает не только на ролики и внешнее кольцо подшипника, но и в большей степени непосредственно на беговую дорожку внутреннего кольца подшипника, что обеспечивает улучшение смазки по сравнению с прототипом, в котором масло попадает лишь на ролики и внешнее кольцо;
– использование сепаратора с крылышками позволяет более полно использовать масло, так как масло более полно улавливается и удерживается в подшипнике;
– соответственно обеспечивается и более эффективный отвод тепла от колец подшипника, что повышает надежность и ресурс подшипника в узле и двигателя в целом.
Как показали сравнительные испытания узла опоры ГТД с заявляемым подшипником с выполненными во внутреннем кольце каналами и подшипника прототипа (патент РФ №2144995).
Подшипник с 8 каналами (по 4 на сторону) диаметром 1 мм, выполненными под углом 45 градусов к оси вращения подшипника и соотношением B/L=2,5, имеет температуру колец на 10°С ниже, чем у прототипа, и контроль качества рабочих поверхностей заявляемого подшипника и прототипа показал, что подшипник по заявляемому решению имеет меньший износ рабочих поверхностей, что повышает надежность подшипникового узла и ресурс двигателя.
Формула изобретения
1. Узел опоры газотурбинного двигателя, содержащий подшипник с роликом, внутренним кольцом и сепаратором, и выполненный с возможностью подвода масла к подшипнику, отличающийся тем, что во внутреннем кольце подшипника дополнительно выполнен, по меньшей мере, один канал для подвода масла к беговой дорожке внутреннего кольца подшипника, причем для канала выполняется отношение 20°  90°, где – угол между осью канала и осью вращения подшипника, а для подшипника выполняется соотношение B/L=1,1-5,0, где В – ширина сепаратора, L – ширина ролика.
2. Узел опоры по п.1, отличающийся тем, что подвод масла к беговой дорожке внутреннего кольца подшипника осуществляется в выполненные во внутренней обойме подшипника канавки выхода шлифовального круга.
РИСУНКИ
|
|