|
(21), (22) Заявка: 2005124044/03, 28.07.2005
(24) Дата начала отсчета срока действия патента:
28.07.2005
(46) Опубликовано: 10.02.2007
(56) Список документов, цитированных в отчете о поиске:
RU 2122103 C1, 20.11.1998. RU 2236742 C2, 20.09.2004. SU 960300 A, 23.09.1982. RU 2184797 C1, 10.07.2002. WO 2002/034391 A2, 20.05.2002.
Адрес для переписки:
109544, Москва, ул. Школьная, 35, оф.10, центр “ЮНТЭКС”, пат.пов. Л.Е.Комарову, рег. № 404
|
(72) Автор(ы):
Чуйко Александр Георгиевич (RU)
(73) Патентообладатель(и):
Чуйко Александр Георгиевич (RU)
|
(54) КОРПУС ЭЛЕМЕНТА ПОГРУЖНОЙ УСТАНОВКИ ДЛЯ ДОБЫЧИ НЕФТИ
(57) Реферат:
Изобретение относится к устройствам для добычи нефти и нефтяных жидкостей из скважин, преимущественно к погружным центробежным насосам и электродвигателям. Элемент погружной установки для добычи нефти включает цилиндрический корпус из конструкционной стали с нанесенным на его наружную поверхность покрытием, выполненным посредством напыления порошка с гранулометрическим составом от 10 до 63 мкм, при этом использован порошок со следующим химическим составом, мас.%: углерод – 1,3÷2,0, молибден – 4,0÷5,0, кремний – 0,5÷1,5, никель – 14,0÷20,0, хром – 23,0÷32,0, бор – 0,001÷0,1, марганец – 0,4÷1,2, окись алюминия Al2О3 – 5÷25, железо (основа) – остальное. Толщина покрытия ограничена диапазоном от 100 до 500 мкм. Технический результат – повышение коррозионной стойкости элементов погружной установки, их износостойкости, эластичности покрытия, защиты от электрохимической коррозии, микротвердости покрытия. 1 з.п. ф-лы, 1 ил.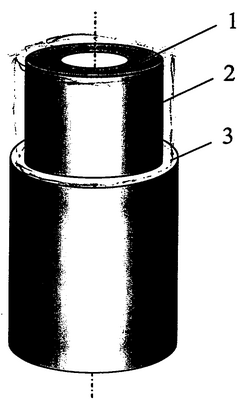
Изобретение относится к устройствам для добычи нефти и нефтяных жидкостей из скважин, преимущественно к погружным центробежным насосам, электродвигателям и насосно-компрессорным трубам.
В процессе опускания в скважину погружного оборудования для добычи нефти (насосов, электродвигателей, гидрозащиты и т.д.) их наружные поверхности интенсивно трутся об обсадную трубу скважины. Глубина скважин достигает нескольких километров. Скважина имеет очень много изгибов. В результате опускания погружного оборудования происходит интенсивное истирание его наружной поверхности. Кроме того, внутри кривой обсадной трубы происходят многократные изгибы (упругое деформирование) погружного оборудования. При этом лакокрасочные покрытия и хрупкие (в том числе толстые) металлические покрытия не выдерживают таких нагрузок – истираются, трескаются, отслаиваются. Таким образом нарушается их герметичность.
Внутри скважины находится пластовая жидкость. Пластовая жидкость в зависимости от ее состава имеет различную агрессивность. Особенно высокой агрессивностью обладают скважины, содержащие сероводород. Чем выше содержание сероводорода, тем агрессивнее среда.
Корпуса погружного оборудования в таких скважинах начинают интенсивно коррозировать. Срок эксплуатации оборудования без покрытия до появления сквозных дырок измеряется от года до двух недель.
Наиболее интенсивная коррозия происходит на корпусе электродвигателя. Это процесс электрохимической коррозии.
Защита от коррозии путем применения лакокрасочных покрытий в данном случае результатов не дает, поскольку в процессе опускания оборудования в скважину оно практически полностью обдирается.
Известен корпус элемента погружной установки для добычи нефти в виде плунжера погружного штангового насоса, содержащий цилиндрическую трубу из конструкционной стали с нанесенным на нее наружную поверхность покрытием из азотированного материала (см. RU 2122103, 20.11.1998).
Такое покрытие повышает износостойкость наружной поверхности корпуса, однако коррозионная стойкость такой поверхности остается низкой, что снижает ресурс работы погружной установки в агрессивной среде.
Защита от коррозии путем применения металлических покрытий является наиболее эффективной. При этом металлические покрытия должны обладать высокой плотностью, высокой адгезией, низким электрохимическим потенциалом по отношению к корпусу оборудования, высокой коррозионной стойкостью, высокой твердостью и износостойкостью, высокой эластичностью. Совокупность перечисленных свойств обеспечивает надежную коррозионную защиту покрытия в скважине.
В то же время, использование металлических покрытий, не отвечающих перечисленным требованиям не обеспечивает надежной защиты от коррозии. Например, применение утолщенных и хрупких покрытий приводит к их растрескиванию и даже отслаиванию. Малейшей несплошности покрытия (микротрещины, язвы, сквозные поры дыры и т.д.) достаточно, чтобы началась интенсивная коррозия всего корпуса оборудования. При этом в зависимости от электрохимического потенциала процесс коррозии может быть еще более интенсивным по сравнению с оборудованием без металлического покрытия.
Техническая задача, на которую направлено заявленное изобретение – повышение коррозионной стойкости элементов погружной установки, их износостойкости, повышение эластичности покрытия, улучшения защиты от электрохимической коррозии, повышение микротвердости покрытия.
Поставленная задача решается тем, что элемент погружной установки для добычи нефти включает цилиндрический корпус из конструкционной стали с нанесенным на его наружную поверхность покрытием, которое выполнено посредством напыления порошка с гранулометрическим составом от 10 до 63 мкм, при этом использован порошок со следующим химическим составом в указанных процентных соотношениях по массе:
углерод |
1,3÷2,0 |
молибден |
4,0÷5,0 |
кремний |
0,5÷1,5 |
никель |
14,0÷20,0 |
хром |
23,0÷32,0 |
бор |
0,001÷0,1 |
марганец |
0,4÷1,2 |
окись алюминия (Al2О3) |
5÷25 |
железо (основа) |
остальное |
Кроме того, толщина покрытия элемента погружной установки для добычи нефти ограничена диапазоном от 100 до 500 мкм.
Заявленное изобретение поясняется чертежом, на котором показан продольный разрез корпуса элемента погружной установки для добычи нефти.
Корпус элемента погружной установки для добычи нефти содержит цилиндрическую трубу 1 из конструкционной стали с нанесенным на ее наружную поверхность 2 покрытием в виде напыленного слоя 3, включающего, мас.%: углерод – 2,0, молибден – 4,5, кремний – 1,5, никель – 14,0, хром – 23,0, бор -0,1, марганец – 1,2, окись алюминия (Al2О3) – 25, железо (основа) – 28,7.
Толщина покрытия 3 выбрана равной 300 мкм.
Примененный в используемом покрытии, в частности, марганец – раскисляет материал покрытия в процессе распыления порошка, при этом снижается температура плавления порошка и, как следствие, достигается большая эластичность покрытия, повышается адгезия покрытия и его плотность, алюминий – снижает электрохимический потенциал покрытия по отношению к корпусу оборудования, в результате значительно улучшается коррозионная стойкость покрытия, бор – значительно повышает твердость и износостойкость покрытия, остальные компоненты покрытия также способствуют повышению его износостойкости, прочности и степени защиты от коррозии.
Применение порошка с гранулометрическим составом от 10 до 63 мкм обеспечивает высокую плотность покрытия, высокую адгезию покрытия, высокую эластичность покрытия.
Использование смеси металлического порошка с Al2О3 обеспечивает в процессе напыления интенсивную бомбардировку напыляемой поверхности, ее упрочнение наклепом непосредственно в процессе нанесения покрытия и тем самым достигается значительное повышение адгезии и когезии. Кроме того, частично внедренные в материал покрытия мелкие частицы Al2О3 повышают твердость и износостойкость покрытия.
Формула изобретения
1. Элемент погружной установки для добычи нефти, включающий цилиндрический корпус из конструкционной стали с нанесенным на его наружную поверхность покрытием, отличающийся тем, что покрытие выполнено посредством напыления порошка гранулометрическим составом от 10 до 63 мкм, при этом использован порошок со следующим химическим составом, %:
Углерод |
1,3÷2,0 |
Молибден |
4,0÷5,0 |
Кремний |
0,5÷1,5 |
Никель |
14,0÷20,0 |
Хром |
23,0÷32,0 |
Бор |
0,001÷0,1 |
Марганец |
0,4÷1,2 |
Окись алюминия (Al2O3) |
5÷25 |
Железо (основа) |
Остальное |
2. Элемент погружной установки для добычи нефти по п.1, отличающийся тем, что толщина покрытия ограничена диапазоном от 100 до 500 мкм.
РИСУНКИ
QB4A – Регистрация лицензионного договора на использование изобретения
Лицензиар(ы): Чуйко Александр Георгиевич
Вид лицензии*: НИЛ
Лицензиат(ы): Общество с ограниченной ответственностью “ПЛАЗМА”
Договор № РД0021793 зарегистрирован 10.05.2007
Извещение опубликовано: 20.06.2007 БИ: 17/2007
* ИЛ – исключительная лицензия НИЛ – неисключительная лицензия
|
|