|
(21), (22) Заявка: 2003137848/04, 04.06.2002
(24) Дата начала отсчета срока действия патента:
04.06.2002
(30) Конвенционный приоритет:
04.06.2001 (пп.1-8) US 60/295,619
(43) Дата публикации заявки: 20.04.2005
(46) Опубликовано: 27.01.2007
(56) Список документов, цитированных в отчете о поиске:
US 3931305 А, 06.01.1976. US 3064044 А, 13.11.1962. GB 1152575 А, 21.05.1969. RU 2137753 C1, 20.09.1999.
(85) Дата перевода заявки PCT на национальную фазу:
05.01.2004
(86) Заявка PCT:
US 02/17498 (04.06.2002)
(87) Публикация PCT:
WO 02/098836 (12.12.2002)
Адрес для переписки:
129010, Москва, ул. Б.Спасская, 25, стр.3, ООО “Юридическая фирма Городисский и Партнеры”, пат.пов. Е.Е.Назиной, рег. № 517
|
(72) Автор(ы):
ЛИН Роберт (US), О МЕАДХРА Руаири Сеосамх (US), ШЕППАРД Роналд Бафорд (US)
(73) Патентообладатель(и):
ИСТМАН КЕМИКАЛ КОМПАНИ (US)
|
(54) СПОСОБ ПОЛУЧЕНИЯ ОЧИЩЕННОЙ ТЕРЕФТАЛЕВОЙ КИСЛОТЫ
(57) Реферат:
Изобретение относится к усовершенствованному способу получения и выделения кристаллической терефталевой кислоты, содержащей менее чем 150 мас. млн.ч. п-толуольной кислоты, от массы терефталевой кислоты, который предусматривает стадии: (1) загрузку (i) пара-ксилола, (ii) водной реакционной уксуснокислой среды, содержащей растворенные в ней компоненты катализатора окисления, и (iii) газ, содержащий кислород, в первую под давлением зону окисления, в которой происходит жидкофазное экзотермическое окисление пара-ксилола, в которой температура и давление внутри первого под давлением реактора окисления поддерживают от 150 до 180°С и от 3,5 до 13 абсолютных бар; (2) удаление из верхней части первого реактора пара, содержащего упаренную водную уксуснокислую реакционную среду и газ, обедненный кислородом, включающий диоксид углерода, инертные компоненты и менее чем 9 объемных процентов в расчете на неконденсируемые компоненты пара, кислорода; (3) удаление из нижней части первого реактора окисленного продукта, включающего: (i) твердую и растворенную терефталевую кислоту и продукты неполного окисления и (ii) водную уксуснокислую реакционную среду, содержащую растворенный катализатор окисления; (4) загрузку (i) окисленного продукта со стадии (3) и (ii) газа, содержащего кислород, во вторую под давлением зону окисления, в которой проходит жидкофазное, экзотермическое окисление продуктов неполного окисления, при этом температуру и давление во втором под давлением реакторе окисления поддерживают от 185 до 230°С и от 4,5 до 18,3 абсолютных бар; (5) удаление из верхней части второго реактора пара, содержащего испаренную водную уксуснокислую реакционную среду и газ, обедненный кислородом, включающий диоксид углерода, инертные компоненты и менее чем 5 объемных процентов в расчете на неконденсируемые компоненты пара, кислорода; (6) удаление из нижней части второго реактора второго окисленного продукта, включающего: (i) твердую и растворенную терефталевую кислоту и (ii) водную, реакционную среду уксусной кислоты, содержащую растворенный катализатор окисления; (7) отделение терефталевой кислоты от (ii) водной реакционной уксуснокислой среды стадии (6) для получения терефталевой кислоты, содержащей менее чем 900 мас. млн.ч. 4-карбоксибензальдегида и п-толуольной кислоты; (8) растворение терефталевой кислоты, полученной на стадии (7), в воде для образования раствора, содержащего от 10 до 35 мас.% растворенной терефталевой кислоты, содержащей менее чем 900 мас. млн.ч. 4-карбоксибензальдегида и п-толуольной кислоты по отношению к массе присутствующей терефталевой кислоты, при температуре от 260 до 320°С и давлении, достаточном для подержания раствора в жидкой фазе, и введение в контакт раствора с водородом в присутствии катализатора гидрирования с получением раствора гидрированного продукта; (9) загрузку раствора стадии (8) в зону кристаллизации, включающую множество соединенных в серии кристаллизаторов, в которых раствор подвергают испарительному охлаждению с регулируемой скоростью путем значительного понижения давления и температуры, для инициирования кристаллизации терефталевой кислоты, при этом давление раствора в конце зоны кристаллизации является атмосферным или ниже; (10) конденсацию растворителя, упаренного из кристаллизаторов, и возврат конденсированного растворителя в зону кристаллизации путем подачи части конденсированного растворителя в линию удаления продукта кристаллизатора, из которого удаляют растворитель в виде пара; (11) выделение твердой кристаллической терефталевой кислоты, содержащей менее чем 150 мас. млн.ч. п-толуольной кислоты в расчете на массу терефталевой кислоты, разделением твердое вещество-жидкость при атмосферном давлении. Способ позволяет получать целевой продукт в улучшенной кристаллической форме. 7 з.п. ф-лы, 2 ил., 3 табл.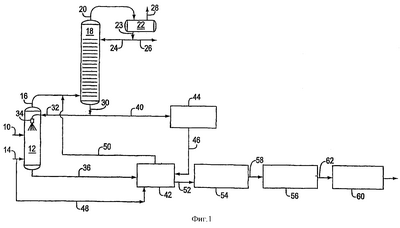
Данное изобретение относится к новому способу получения очищенной терефталевой кислоты путем новой комбинации стадий, начинающихся с окисления диалкилбензольного соединения, такого как п-ксилол. Конкретнее данное изобретение относится к получению очищенной терефталевой кислоты на основе способа окисления, в котором вначале диалакилбензольное соединение окисляют до терефталевой кислоты при помощи двухстадийного способа, использующего определенные условия для получения терефталевой кислоты, имеющей большую чистоту, и затем терефталевую кислоту очищают гидрированием и выделяют при помощи нового способа кристаллизации.
Ароматические дикарбоновые кислоты, такие как терефталевая кислота и изофталевая кислота, представляют огромный интерес с коммерческой точки зрения и широко используются для получении различных полиэфирных полимеров, таких как волокнообразующие и формовочные типы полиэфиров. Терефталевая кислота (ТФК) является одним из основных строительных блоков при получении линейных полиэфирных смол, используемых в производстве полиэфирных пленок, упаковочных материалов и бутылок. ТФК, используемая при производстве таких полиэфирных смол, должна удовлетворять определенным требованиям минимальной чистоты. Условие чистоты терефталевой кислоты относится, в первую очередь, к отсутствию значительного содержания 4-карбоксибензальдегида (4-КБА) и п-толуольной кислоты, которые присутствуют в значительных количествах в неочищенных марках коммерчески доступной терефталевой кислоты. Как КБА, так и толуольная кислота являются продуктами частичного окисления, образуемыми при производстве ТФК каталитическим окислением п-ксилола. Очищенная форма также означает отсутствие окрашенных частиц, которые придают характерный желтый оттенок неочищенному материалу. Окрашенные частицы являются ароматическими соединениями, имеющими структуры бензилов, флуоренонов и/или антрахинонов. 4-КБА и п-толуольная кислота частично препятствуют полимеризации, поскольку приводят к обрыву цепи в течение реакции конденсации между терефталевой кислотой и этиленгликолем при получении поли(этилентерефталата) (ПЭТ).
Неочищенная терефталевая кислота может быть очищена гидрированием. В обычном способе гидрирования неочищенную терефталевую кислоту растворяют в воде при повышенной температуре и давлении и гидрируют для превращения 4-КБА в п-толуольную кислоту. Гидрирование также превращает окрашенные частицы в неокрашенные соединения. Одним из ограничений в развитии способа выделения очищенной терефталевой кислоты из гидрированного жидкого раствора является приемлемое содержание 4-КБА и п-толуольной кислоты в конечном продукте. Например, очищенная терефталевая кислота (ТФК) обычно содержит менее чем 150 мас. млн.ч. п-толуольной кислоты. В способах выделения для получения очищенной терефталевой кислоты используют множество способов разделения твердое вещество – жидкость, включая кристаллизацию, центрифугирование, фильтрацию и их комбинацию.
Неочищенная терефталевая кислота, полученная первоначальным окислением диалкилбензольного соединения, обычно п-ксилола, обычно имеет общее содержание 4-КБА и п-толуольной кислоты от 150 до 1100 мас. млн.ч. в расчете на присутствующие твердые вещества. Неочищенная терефталевая кислота также содержит меньшие количества, например в диапазоне от 20 до 200 мас. млн.ч., характерных желтых соединений. Эти соединения представляют собой окрашенные ароматические соединения, имеющие структуры бензила, флуоренона и/или антрахинона, которые получаются в результате побочных реакций сочетания, протекающих при окислении п-ксилола. Необходимо очищать неочищенную терефталевую кислоту при ее использовании в качестве исходного материала для получения полиэфирных волокон, при котором необходима очищенная терефталевая кислота (ТФК) в качестве исходного материала.
Такой способ очистки обычно включает комбинацию неочищенной терефталевой кислоты, выделенной из процесса окисления, с водой для образования ее суспензии, которую нагревают для растворения неочищенной терефталевой кислоты и примесей в воде и получения водного раствора. Этот раствор затем переносят на стадию восстановления, в которой раствор вводят в контакт с водородом в присутствии гетерогенного катализатора, обычно палладия на углеродной подложке, при повышенной температуре, такой как от 200 до 375°С, для очистки ТФК. Стадия гидрирования превращает различные окрашенные частицы, присутствующие в неочищенной терефталевой кислоте, в бесцветные продукты. Примесь 4-КБА превращается в п-толуольную кислоту.
Последующее отделение и выделение продукта терефталевой кислоты могут быть осуществлены при помощи различных способов разделения твердое вещество – жидкость. Метод стадийной равновесной кристаллизации является одним из способов разделения. В таком способе выпаривание контролируют регулированием противодавления в многократных стадиях кристаллизации для контроля скорости, с которой кристаллизуется поток, прошедший гидрирование. Для терефталевой кислоты считается, что ударное охлаждение потока, прошедшего гидрирование, до температуры ниже 165°С способствует совместному осаждению (сокристаллизации) примесей, в особенности п-толуольной кислоты, которые загрязняют ТФК продукт.
Патент США 3931305 раскрывает, что основным фактором, определяющим концентрацию примесей в продуктовой терефталевой кислоте, является самая низкая температура, до которой мгновенно охлаждают поток, прошедший гидрирование. Концентрация примеси в меньшей степени зависит от скорости, с которой охлаждают поток, прошедший гидрирование. С этой целью рекомендуют, чтобы основная часть терефталевой кислоты кристаллизовалась при температуре выше, чем от 160 до 182°, которая является предельной температурой, при которой сокристаллизация п-толуольной кислоты становится критической. Если в потоке терефталевой кислоты, прошедшем гидрирование, концентрация п-толуольной кислоты составляет от 500 до 6000 мас. млн.ч., то рекомендуется проводить фильтрацию после кристаллизации при температуре от 121 до 149°С для получения в ТФК продукте концентрации п-толуольной кислоты 150 мас. млн.ч. или ниже. Другие способы выделения используют эффективную фильтрацию, промывание и способы высушивания в температурном диапазоне от 100 до 205°С для уменьшения осаждения п-толуольной кислоты.
Настоящее изобретение относится к способу получения очищенной ТФК, начинающегося с окисления п-ксилола. Настоящее изобретение предлагает способ получения и выделения кристаллической терефталевой кислоты, содержащей менее чем 150 мас. млн.ч. п-толуольной кислоты от веса терефталевой кислоты, со стадиями, включающими:
(1) загрузку (i) диалкилбензольного соединения, (ii) реакционной водной уксуснокислой среды, содержащей растворенные в ней компоненты катализатора окисления, и (iii) газа, содержащего кислород, в первую под давлением зону окисления, в которой происходит жидкофазное экзотермическое окисление диалкилбензольного соединения, в которой температура и давление внутри первого под давлением реактора окисления поддерживают при от 150 до 180°С и от около 3,5 до 13 абсолютных бар – bara (от примерно 50 до 189 фунтов на квадратный дюйм – psia);
(2) удаление из верхней части первого реактора пара, содержащего испаренную реакционную водную уксуснокислую среду и газ, обедненный кислородом, включающий диоксид углерода, метан, инертные компоненты и менее чем 9 объемных процентов в расчете на неконденсируемые компоненты пара, кислорода;
(3) удаление из нижней части первого реактора окисленного продукта, включающего (i) твердую и растворенную терефталевую кислоту и продукты неполного окисления и (ii) водную, уксуснокислую реакционную среду, содержащую растворенный катализатор окисления;
(4) загрузку (i) окисленного продукта со стадии (3) и (ii) газа, содержащего кислород, во вторую под давлением зону окисления, в которой проходит жидкофазное, экзотермическое окисление продуктов неполного окисления, при этом температуру и давление во втором под давлением реакторе окисления поддерживают при температуре от 185 до 230°С и от примерно 4,5 до 18,3 bara (примерно от 65 до 265 psia);
(5) удаление из верхней части второго реактора пара, содержащего испаренную водную уксуснокислую реакционную среду и газ, обедненный кислородом, включающий диоксид углерода, метан, инертные компоненты и менее чем 5 объемных процентов в расчете на неконденсируемые компоненты пара, кислорода;
(6) удаление из нижней части второго реактора второго окисленного продукта, включающего (i) твердую и растворенную терефталевую кислоту и (ii) водную, уксуснокислую реакционную среду, содержащую растворенный катализатор окисления;
(7) отделение терефталевой кислоты от (ii) водной уксуснокислой реакционной среды со стадии (6) с получением терефталевой кислоты, содержащей примеси 4-карбоксибензальдегида и п-толуольной кислоты с содержанием в общем от 400 до 900 мас. млн.ч.;
(8) растворение терефталевой кислоты, полученной на стадии (7), в воде с образованием раствора, содержащего от 10 до 35 мас.% растворенной терефталевой кислоты, при температуре от 260 до 320°С и давлении, достаточном для подержания раствора в жидкой фазе, и введение во взаимодействие раствора с водородом в присутствии катализатора гидрирования с получением раствора гидрированного продукта;
(9) загрузку раствора стадии (8) в зону кристаллизации, включающую множество последовательно соединенных кристаллизаторов, в которых раствор подвергается испарительному охлаждению с регулируемой скоростью путем значительного понижения давления и температуры, для инициирования кристаллизации терефталевой кислоты, при этом давление раствора в конце зоны кристаллизации является атмосферным или ниже;
(10) конденсацию растворителя, выпаренного из кристаллизаторов, и возврат конденсированного растворителя в зону кристаллизации в точку, следующую за кристаллизатором, из которого он был получен;
(11) выделение твердой кристаллической терефталевой кислоты, содержащей менее чем 150 мас. млн.ч. п-толуольной кислоты в расчете на вес терефталевой кислоты, разделением твердое вещество-жидкость при атмосферном давлении.
Способ по настоящему изобретению обеспечивает по крайней мере два значительных преимущества. Во-первых, первичное и вторичное окисления, описанные в стадиях (1)-(7), приводят к получению терефталевой кислоты, в которой общее содержание 4-карбоксибензальдегида и п-толуольной кислоты составляет менее чем 900 мас. млн.ч. Такое пониженное содержание примесей делает возможным более эффективное гидрирование, которое может позволить уменьшать размер аппарата для гидрирования и/или время контакта загружаемого раствора в зоне гидрирования. Во-вторых, поскольку общее содержание 4-карбоксиальдегида и п-толуольной кислоты, загружаемых в реактор гидрирования, меньше, чем 900 мас. млн.ч. в растворе продукта гидрирования будет меньше п-толульной кислоты (по сравнению с известными способами очистки). В результате число и размер кристаллизаторов для выделения и очистки терефталевой кислоты могут быть уменьшены и кристаллизация может быть упрощена. Также количество материала, т.е. водного раствора, содержащего растворенные примеси, который должен быть удален из производственной системы, уменьшается, поскольку содержание п-толуольной кислоты становится ниже. Другим преимуществом нового способа является наличие стадии (10), в которой растворитель упаривают из по крайней мере одного из кристаллизаторов, составляющих зону кристаллизации, и конденсируют и рециркулируют в одну из последующих стадий кристаллизации. Преимущества, обеспечиваемые этой стадией, включают выделение терефталевой кислоты в улучшенной кристаллической форме с меньшим количеством «мелочи», т.е. мелких кристаллов или частиц ТФК, которые могут вызывать проблемы при работе и транспортировке ТФК. Другим преимуществом является то, что выделение продукта проводят при атмосферном или почти атмосферном давлении.
Фиг.1 и 2 являются схемами технологического процесса, иллюстрирующими систему осуществления принципов способа по настоящему изобретению. Хотя настоящее изобретение допускает исполнение в различных формах, на фиг.1 и 2 и далее подробно описано предпочтительное исполнение изобретения. Настоящее раскрытие должно рассматриваться как иллюстрация изобретения, однако, не ограничивающаяся конкретным описанным исполнением.
Со ссылкой на фиг.1, стадия (1) нового способа может проводиться в первой зоне окисления, включающей резервуар реактора 12. Загружаемая смесь, включающая диалкилбензольное соединение, такое как п-ксилол, водная уксусная кислота и пригодный катализатор окисления, подают в первый реактор окисления 12 через трубопровод 10. Реакционная уксуснокислая среда или загружаемый растворитель обычно содержит вплоть до 15 мас.% воды. Если желательно, диалкилбензольное соединение и/или уксуснокислый растворитель, содержащий компоненты катализатора, могут быть загружены в реактор 12 через множество точек вдоль стенки реактора 12. Газ, содержащий молекулярный кислород, под давлением непрерывно загружают через трубопровод 14, в реактор 12 через или рядом с основанием колоннообразного реакционного сосуда. Газ, содержащий кислород, например кислород, воздух, обогащенный кислородом, или предпочтительно воздух обычно загружают через или вблизи от основания колоннообразного реакционного сосуда. Скорость потока газа, содержащего кислород, в реактор 12 регулируют для поддержания объемного процента кислорода от 2 до 9, предпочтительно от 2 до 5 (рассчитанного по сухому составу, не содержащему растворитель) в выходящем газе, который выходит из реактора через трубопровод 16. Реагенты в реакторе 12 поддерживают при повышенном давлении, достаточном для поддерживания содержащейся летучей реакционной среды в значительной степени в жидком состоянии при температуре реакции. Температура и давление внутри реактора 12 составляют от 150 до 180°С и примерно от 3,5 до 13 bara (примерно от 50 до 189 psia), предпочтительно от 155 до 165°С и примерно от 5,2 до 6,9 bara (примерно от 75 до 100 psia).
Реактор 12 обычно представляет собой колончатый, под давлением, реакционный сосуд для окисления, в котором проходит жидкофазное экзотермическое окисление диалкилароматического соединения газом, содержащим кислород, в присутствии катализатора окисления. Первая зона окисления может включать один реактор или множество реакторов, расположенных параллельно. Реакционная среда, содержащаяся в реакторе 12, таким образом включает газ, содержащий кислород, диалкилбензольное соединение, которое должно быть окислено до продуктовой терефталевой кислоты, катализатор и водный уксуснокислый растворитель. Количество присутствующей воды обычно не превышает 15 мас.%, предпочтительно от 4 до 6 мас.%, на основе воды и уксусной кислоты. Обычно цилиндрический первый сосуд для окисления имеет отношение высоты к диаметру в диапазоне от 3 до 20.
Каталитические системы, которые могут использоваться в способе окисления включают каталитическую систему, обычно используемую для жидкофазного окисления алкилароматического углеводорода. Пригодная каталитическая система, включает смесь соединений или комплексов кобальта, марганца и брома, растворимых в водной уксусной кислоте. Атомное отношение комбинации Co:Mn:Br в каталитических элементах предпочтительно находится в диапазоне 5 – 40:1,0:4 – 40, более предпочтительно атомное отношение Co:Mn:Br 16 – 40:1,0:16 – 40.
Во время реакции окисления экзотермическое тепло реакции, генерируемое окислением диалкилбензольного соединения, отводят из реактора 12 путем испарения частиц жидкой реакционной среды. В соответствии со стадией (2) настоящего способа упаренная жидкая реакционная среда (отходящий газ) вместе с технологическим газом, обедненным кислородом, содержащим незначительное количество продуктов разложения и соединений, содержащих бром, понимается вверх через реактор 12 и подается через трубопровод 16 в конденсирующую систему, такую как водная колонна 18. Конденсируемые компоненты паров, собирающиеся в колонне 18, состоят, в первую очередь, из уксуснокислого растворителя, затем возвращают в реактор 12 через трубопроводы 30 и 32 и распылительную головку 34.
Как показано на фиг.1, верхние водные пары выходят из верхней части водоудаляющей колонны 18 через трубопровод 20 и подаются в холодильник 22. Состав конденсируемых компонентов водных паров, собирающихся в холодильнике 22, известных как дистиллят, более чем на 98% является водой. Часть дистиллята возвращается в виде флегмы в зону фракционирования колоны 18 через трубопроводы 23 и 24. Оставшийся дистиллят удаляют через трубопроводы 23 и 26. Неконденсируемые компоненты выпускают через выход 28 из производственной системы или они могут быть перенесены, если желательно, в устройства для контроля очистки для дополнительной обработки.
Дистиллированная жидкость на дне, включающая частично обезвоженный уксуснокислый растворитель, например уксусную кислоту, содержащая от 4 до 12 мас.% воды, выходит через нижнюю часть водоудаляющей колонны через трубопровод 30. Часть частично обезвоженного растворителя рециркулируют непосредственно в реактор 12 через трубопровод 32. Это количество изменяется от 10 до 100%. Частично обезвоженный растворитель загружают в реактор 12 через одно или более распыляющих сопел 34, которые могут быть расположены ниже выходного трубопровода 16 или выше разделения фаз газ/жидкость содержания реактора 12. Другая часть частично обезвоженного растворителя может быть удалена через трубопровод 40. Часть или вся конденсированная уксусная кислота может быть возвращена в реактор 12 через загрузочный поток 10.
В действии, первый под давлением реактор окисления 12 производит продукт терефталевой кислоты, который труднорастворим в водном технологическом растворителе и удаляется через нижнее выходное отверстие, расположенное в или рядом с основанием реактора, в виде суспензии в растворителе, который также содержит растворенные компоненты катализатора. Процесс окисления в реакторе 12 также приводит к получению побочных продуктов в виде монокарбоновых кислот, таких как 4-карбоксибензальдегид и п-толуольная кислота. По крайней мере часть этих монокарбоновых кислот являются твердыми веществами, которые могут содержаться в кристаллах терефталевой кислоты. Обычно эти монокарбоновые кислоты присутствуют в виде 4-карбоксибензальдегида и п-толуольной кислоты в количестве 900 мас. млн.ч. Эти монофункциональные соединения являются нежелательными побочными продуктами, поскольку они действуют как терминаторы полимерной цепи и, таким образом, могут приводить к образованию низкомолекулярных полиэфиров, таких как поли(этилентерефталат), получаемый из терефталевой кислоты и этиленгликоля.
В соответствие со стадиями (3) и (4) способа по изобретению суспензию продукта терефталевой кислоты и побочных монокарбоновых продуктов непрерывно удаляют в виде суспензии в водном технологическом уксуснокислом растворителе, который также содержит растворенный катализатор, из нижней части реактора 12 и переводят через трубопровод 36 во вторую под давлением зону окисления, показанную на фиг.1 как реактор 42. Вторая зона окисления может быть одним, перемешиваемым реактором, как показано на фиг.1 или двумя или более перемешиваемыми реакторами, которые могут быть расположены параллельно или последовательно. Водный уксуснокислый растворитель обычно содержит от 5 до 12 мас.% воды по отношению к массе воды и алифатической, карбоновой кислоты. Газ, содержащий молекулярный кислород, также загружают через трубопровод 48 во второй реактор окисления 42, в котором побочные продукты 4-карбоксибензальдегид и п-толуольную кислоту дополнительно окисляют до желаемой терефталевой кислоты. Как и в случае загрузки в первый реактор окисления, газ, содержащий кислород, может быть кислородом, воздухом, обогащенным кислородом, или, предпочтительно, воздухом. Газ, содержащий кислород, обычно загружают через или около дна второго реактора окисления 42 выше поверхности жидкости, содержащейся в реакторе.
Скорость потока газа, содержащего кислород, в реактор 42 может регулироваться, оставаясь на величине от 0 до 5, предпочтительно от 0 до 1 объемного процента кислорода (рассчитанного на сухой состав, не содержащий растворитель) в отходящем газе, который выходит из реактора через трубопровод 50. Скорость потока газа, содержащего кислород, в ректор 42 обычно составляет от 0,001 до 3 объемных процентов, предпочтительно от 0,001 до 2 объемных процентов скорости потока газа, содержащего кислород, в реактор 12. Небольшое количество воздуха, загружаемого во второй реактор окисления 42, ограничивает окислительное разложение уксуснокислого растворителя, дополнительно облегчая превращение побочных продуктов монокарбоновых кислот в терефталевую кислоту.
Первый реактор окисления, описанный выше, осуществляет в значительной степени все окисления, хотя и действует при умеренном давлении и температуре. Основным препятствием при достижении достаточной конверсии диалкилбензольного соединения в терефталевую кислоту в первичной окисляющей системе являются ограничения массопередачи, связанные с диффузией кислорода к частично окисленным продуктам, находящимся или содержащимся в терефталевой кислоте, т.е. частично окисленные побочные продукты монокарбоновых кислот могут быть заключены в кристаллы терефталевой кислоты. Поэтому достаточно легко окислить большую часть диалкилбензольного соединения до терефталевой кислоты даже при умеренных условиях. Однако для достижения в достаточной мере полной конверсии необходимо преодолеть эти ограничения массопередачи. Действие первой зоны окисления при умеренных условиях давления и температуры может помочь в образовании небольших или тонкоизмельченных кристаллов, которые могут быть растворены и перекристаллизованы во второй зоне окисления. Когда небольшие или тонкоизмельченные кристаллы растворяют во второй зоне окисления, сокристаллизованные побочные продукты оказываются доступными для дальнейшего окисления.
Материалы во втором реакторе окисления 42 поддерживают при повышенном давлении, достаточном для поддержания содержащейся летучей реакционной среды в значительной степени в жидком состоянии при температуре реакции. Температура и давление внутри реактора 12 равны от 185 до 230°С и от примерно 4,5 до 18,3 bara (примерно от 65 до 265 psia), предпочтительно от 205 до 215°С и от примерно 13,4 до 17,2 bara (примерно от 195 до 250 psia). Тепло, требуемое для функционирования второй зоны окисления, может быть обеспечено подачей парофазного растворителя во второй реактор окисления, позволяя парофазному растворителю конденсироваться. Парофазный растворитель обычно будет находиться при давлении, достаточном, чтобы позволить пару пройти во второй реактор окисления и обеспечить достаточную подачу тепла к содержимому второго реактора окисления. Например, частично обезвоженная уксусная кислота может загружаться из водоудаляющей колонны 18 в испаритель кислоты 44 через трубопроводы 30 и 40. Испаритель кислоты 44 переводит частично обезвоженную уксусную кислоту до температуры и давления, достаточного для подержания заданной температуры внутри второго реактора окисления 42. Конструкция испарителя уксусной кислоты обычно требует присутствия жидкости для переноса тепла, такой как Dowtherm, или потока высокого давления, который может использоваться для испарения уксусной кислоты. Пар уксусной кислоты переносится из кислотного испарителя 44 во второй реактор окисления 42 через трубопровод 46.
Отходящий газ, включающий упаренную жидкую реакционную среду совместно с технологическим газом, обедненным кислородом, содержащим незначительное количество продуктов разложения и соединений, содержащих бром, удаляют из верхней части или верха второго реактора окисления 42 и загружают через трубопроводы 50 и 16 в конденсирующую систему, такую как водная колонна 18. Конденсируемые компоненты потока отходящего газа состоят в первую очередь из уксуснокислого растворителя, который может быть выделен, как описано выше.
Продукт терефталевой кислоты удаляют из второго реактора окисления 42 в виде суспензии в водном технологическом уксуснокислом растворителе, который также содержит растворенные компоненты катализатора, через трубопровод 52. Суспензия, удаляемая из реактора 42, обычно включает от 20 до 40 мас.% твердых веществ и содержит менее чем всего 900 мас. млн.ч. на основе массы присутствующих твердых веществ, продуктов неполного окисления и, в первую очередь, 4-карбоксибензальдегид и п-толуольную кислоту. Общее содержание 4-карбоксибензальдегида и п-толуольной кислоты обычно находится в диапазоне от 400 до 900 мас. млн.ч.
Суспензионный продукт из второго реактора окисления 42 (второй окисленный продукт) может быть охлажден до введения в систему разделения твердое вещество/жидкость и, при желании, в систему для сушки твердых веществ. Предпочтительно суспензионный продукт из второго реактора окисления 42 загружают в зону мгновенного упаривания, в которой температуру и давление второго окисленного продукта понижают мгновенным упариванием. Зона мгновенного упаривания может содержать один или, предпочтительно, множество сосудов для мгновенного упаривания, в которых суспензионный продукт охлаждают ступенчатым или последовательным упариванием путем уменьшения давления. Как показано на фиг.1, для охлаждения суспензии трубопровод 52 входит в первый сосуд 54 для мгновенного испарения. Из него трубопровод 58 идет во второй сосуд для мгновенного испарения 56. Первый и второй сосуды для мгновенного испарения 54 и 56 обеспечивают ступенчатое уменьшение давления из реактора 42. Это ступенчатое или последовательное уменьшение давления служит двум целям. Во-первых, оно устраняет необходимость нагнетания между узлами. Во-вторых, адиабатическое испарение при понижении давления между реактором 42 и первым испарительным сосудом 54 позволяет выступать первому испарительному сосуду 54 в качестве испарительного кристаллизатора. Средний размер кристаллов терефталевой кислоты может увеличиться в первом испарительном сосуде 54. Пар из обоих испарительных сосудов 54 и 56 может быть направлен в холодильник (не показан). Первый испарительный сосуд 54 может функционировать при температуре от 170 до 190°С и давлении от примерно 2,4 до 5,2 bara (примерно от 35 до 75 psia). Поток суспензии из первого испарительного сосуда 54 загружают во второй испарительный сосуд 56, который представляет собой другой адиабатический испарительный резервуар при температуре от 60 до 100°С и давлении от 0,3 до 0,8 bara (примерно от 5 до 12 psia). Хотя на фиг.1 показаны два испарительных сосуда, для охлаждения и кристаллизации может использоваться как больше, так и меньше двух, или может использоваться другой способ охлаждения.
Охлажденную суспензию переносят через трубопровод 62 в зону разделения твердое вещество/жидкость 60, в которой твердую терефталевую кислоту отделяют от водного уксуснокислого растворителя/реакционной среды при использовании стандартных способов разделения жидкость/твердое вещество. После разделения осадок терефталевой кислоты на фильтре промывают, например, охлажденной уксусной кислотой из водоудаляющей колонны 18. Влажный осадок на фильтре может быть высушен для выпаривания остаточной уксусной кислоты в осадке на фильтре. Высушенный продукт получают из устройства для разделения твердое вещество/жидкость 60. Состав этого продукта в значительной степени такой же, как и состав твердых веществ, присутствующих в суспензии продукта из второй реакционной зоны 42.
Очистка второго окисленного продукта в соответствии со стадией (6) по настоящему способу, включает гидрирование второго окисленного продукта для превращения 4-карбоксибензальдегида в п-толуольную кислоту и окрашенных частиц или предшественников окрашенных частиц в неокрашенные соединения. Ссылаясь на фиг.2, вода и второй окисленный продукт (СТА) загружают в сосуд для растворения СТА 160. Раствор обычно включает от 10 до 35 мас.% твердой терефталевой кислоты в водном растворителе, предпочтительно от 25 до 35 мас.% терефталевой кислоты в водном растворителе. Раствор терефталевой кислоты получают нагреванием растворителя или суспензии терефталевой кислоты до температуры, которая достаточна для растворения терефталевой кислоты до желаемой концентрации, например при температуре в диапазоне от 260 до 320°С. При температуре в диапазоне от 260 до 320°С при использовании растворителя, такого как вода, необходимо поддерживать раствор при повышенном давлении, например давлении в диапазоне от примерно 46,9 до 113 абсолютных бар – bara (680-1640 фунтов на квадратный дюйм (psia)).
Раствор терефталевой кислоты загружают в реактор гидрирования 110, в котором раствор подвергают жидкофазному гидрированию введением в контакт жидкого раствора с водородом в присутствии катализатора гидрирования, например благородного металла группы VIII на материале носителя катализатора, чтобы вызвать гидрирование значительного количества примесей в другие соединения. Например, флуореноны и 4-КБА переводят в флуорены и п-толуольную кислоту, соответственно. Принимая, что при этом проходит в значительной степени полная конверсия 4-КБА в п-толуольную кислоту и предполагая, что загружаемый в реактор гидрирования раствор терефталевой кислоты имеет общее содержание 4-КБА и п-толуольной кислоты менее чем 900 мас. млн.ч., например от 400 до 900 мас. млн.ч., содержание собственно п-толуольной кислоты в продуктовом потоке из реактора гидрирования 110 будет меньше, чем 900 мас. млн.ч. в расчете на присутствующую терефталевую кислоту.
Температура продуктового потока гидрирования обычно находится в диапазоне от 260 до 320°С. Поток гидрированного продукта загружают через клапан 130 и трубопровод 131 в зону кристаллизации, включающую множество или последовательность параллельно соединенных кристаллизационных стадий, которые функционируют вместе для уменьшения температуры после кристаллизационного потока до более низкой температуры, обычно от 75 до 150°, чаще от 90 до 110°С. Уменьшению температуры сопутствует параллельное выпадение терефталевой кислоты из раствора в форме белого кристаллического твердого вещества. Кристаллическую терефталевую кислоту в окончательной стадии кристаллизации отделяют от растворителя при использовании обычного устройства для разделения твердое вещество-жидкость, такого как центрифуга или роторный вакуумный фильтр. Зона кристаллизации может содержать от двух до восьми, предпочтительно от трех до шести, более предпочтительно от четырех до пяти, кристаллизаторов или кристаллизационных стадий. Число кристаллизационных стадий, используемых в способе, может влиять на качество конечного продукта. Правильная установка температуры последовательности соединенных в серии кристаллизационных стадий может увеличить чистоту конечного продукта с точки зрения п-толуольной кислоты.
Множество кристаллизационных стадий включает первую и последнюю стадии. Температура в пределах первой кристаллизационной стадии обычно находится в диапазоне от 200 до 260°С и температура в пределах последней кристаллизационной стадии обычно находится в диапазоне от 80 до 100°С. Температура функционирования кристаллизационных стадий может становиться последовательно ниже от первой к последней стадии. На последней кристаллизационной стадии получают очищенную суспензию терефталевой кислоты, которая содержит в расчете на твердое вещество меньше, чем 150 мас. млн.ч. п-толуольной кислоты. В соответствии с настоящим изобретением, терефталевая кислота кристаллизуется в первой кристаллизационной стадии путем охлаждения гидрированного загружаемого потока испарительным охлаждением с регулируемой скоростью (или мгновенным испарением) путем уменьшения давления (по сравнению с давлением загружаемого потока) внутри первого кристаллизатора или первой кристаллизационной стадии. Растворитель, удаляемый в виде пара из кристаллизатора, конденсируется, и его часть или весь конденсируемый растворитель возвращают в кристаллизационную зону в точке после кристаллизатора, из которого пар растворителя был удален. Дополнительную ароматическую дикарбоновую кислоту кристаллизуют во второй кристаллизационной стадии при второй температуре, меньшей, чем первая температура, при этом давая возможность растворителю испаряться. Растворитель или конденсируется из паров растворителя, получаемых в предшествующем кристаллизаторе, и/или может добавляться чистый растворитель во вторую кристаллизационную стадию.
Каждая из множества кристаллизационных стадий имеет удельный массовый расход материалов, входящих и выходящих из кристаллизационной стадии. Удельный массовый расход материала, входящего в кристаллизационную стадию, может составлять от 0,7 до 1,3 удельного массового расхода материала, выходящего из последней кристаллизационной стадии. Предпочтительно удельный массовый расход материала, входящего в первую кристаллизационную стадию, в значительной степени равен удельному массовому расходу материала, выходящего из последней кристаллизационной стадии.
Каждая кристаллизационная стадия способа по изобретению имеет множество сходных эксплутационных элементов, включающих следующие основные компоненты:
1. Кристаллизационный блок или сосуд (кристаллизатор), оснащенный устройствами для перемешивания, такими как одна или более крыльчаток;
2. Линия подачи сырья в кристаллизатор;
3. Линия удаления продукта из кристаллизатора;
4. Линия удаления дистиллята растворителя или пара из кристаллизатора, ведущая к холодильнику, в котором часть или весь пар растворителя конденсируется;
5. Линия загрузки растворителя ниже точки или части кристаллизационной зоны для подачи конденсированной жидкости в холодильник.
Кристаллизационный блок представляет собой хорошо перемешиваемый сосуд, содержащий суспензию кристаллов терефталевой кислоты. Растворитель обычно является водой, насыщенной терефталевой кислотой при рабочей температуре кристаллизатора. Рабочая температура каждого кристаллизационного блока в сочетании с температурой и концентрацией подаваемого потока, определяет, насколько много терефталевой кислоты будет кристаллизоваться на каждой стадии. Для того чтобы кристаллизовать значительную часть терефталевой кислоты, нужно понижать температуру в точке, в которой растворимость терефталевой кислоты в водном растворителе уменьшается, что приводит к кристаллизации большего количества терефталевой кислоты. Независимое регулирование давления определяет рабочую температуру кристаллизационных блоков. Регулирование давления может быть осуществлено путем регулирования противодавления в кристаллизационных блоках при использовании, например, но не ограничиваясь, клапана в паропроводе.
В результате пониженного давления (по отношению к давлению загружаемого потока в кристаллизационный блок) растворитель испаряется и удаляется из кристаллизационного блока в виде пара, таким образом приводя к концентрированию раствора. Часть терефталевой кислоты осаждается, кристаллизуясь на кристаллах, уже присутствующих в сосуде, и часть терефталевой кислоты образует зародыши кристаллизации в качестве отдельных новых кристаллов. Количество терефталевой кислоты, которое переносится из жидкой фазы в твердую фазу, зависит от рабочей температуры (регулируемой уменьшением давления) кристаллизатора и равновесной насыщенной концентрацией ТФК при этой температуре.
Обычно загрузку в первый кристаллизатор подают ниже поверхности суспензии, в ней содержащейся, в направлении дна сосуда, где гидростатический напор максимальный. Повышенная температура в этой точке кристаллизационного блока и окружающая жидкость исключают избыточное мгновенное испарение. В кристаллизационных блоках присутствуют устройства для перемешивания, такие как крыльчатки. При вводе потока продукции из реактора гидрирования в первый кристаллизационный блок в зону достаточного перемешивания, может быть уменьшено локальное перенасыщение, которое способствует образованию мелких (или тонкодисперсных) кристаллов. Продуктовый поток непрерывно удаляют из каждого кристаллизационного блока. Продуктовый поток предпочтительно удаляют из хорошо перемешиваемой зоны кристаллизационного блока так, что содержимое продуктового потока представляет среднее общего содержимого внутри каждого кристаллизационного блока. Продуктовый поток загружают в последовательные или последующие кристаллизационные стадии, работающие при более низкой температуре, предпочтительно в хорошо перемешиваемую зону следующего кристаллизационного блока. Поскольку каждый последующий кристаллизационный блок работает при более низкой температуре, часть терефталевой кислоты, остающаяся в растворе, кристаллизуется, указанная часть определяется равновесной концентрацией терефталевой кислоты при рабочей температуре второго кристаллизационного блока 124.
Как указано выше, дистиллят растворителя или пар непрерывно удаляют из первой и последующих кристаллизационных стадий и переносят в холодильник для охлаждения и конденсации пара. Часть или весь пар может быть конденсирован в этой точке. Дополнительно переохлаждение пара до температуры в значительной степени ниже точки кипения может также осуществляться внутри холодильника. Весь или часть конденсированного растворителя рециркулируют в кристаллизационную зону в точке вслед за кристаллизатором, из которого растворитель был удален в виде пара. Предпочтительно конденсированный растворитель рециркулируют в кристаллизационную зону подачей конденсированного растворителя в линию удаления продукта кристаллизатора, из которого растворитель удаляли в виде пара. Любой конденсированный растворитель, невозвращенный или нерециркулированный в кристаллизационную зону, может быть использован в другом месте системы очистки терефталевой кислоты, например, при получении водного раствора, подаваемого в реактор гидрирования. Конечный кристаллизационный блок служит для удержания суспензии, аккумулируя суспензию перед стадией разделения твердое вещество-жидкость. Второй и последующий кристаллизаторы действуют сходным образом с первым кристаллизационной стадией.
Конденсированный растворитель из предшествующей кристаллизационной стадии может быть рециркулирован в непосредственно последующую кристаллизационную стадию или рециркулирован в кристаллизационную стадию, не являющуюся непосредственно последующей кристаллизационной стадией. Как конденсированный растворитель, так и свежий растворитель могут подаваться в одну из последующих кристаллизационных стадий.
Продуктовый поток из любой или всех кристаллизационных стадий может быть разбавлен при использовании разбавляющей жидкости, такой как вода, при температуре, такой же или в значительной степени такой же, как и рабочая температура кристаллизационной стадии, из которой удаляют продуктовый поток. Добавление разбавляющей жидкости к продуктовому потоку оказывает эффект понижения общей концентрации терефталевой кислоты и любых примесей, присутствующих в продуктовом потоке. Если не добавляют разбавляющей жидкости к продуктовому потоку из каждого кристаллизатора, то общая концентрация терефталевой кислоты в каждом продуктовом потоке продолжает повышаться. В способах кристаллизации, в которых разбавляющую жидкость не рециркулируют, продуктовый поток из реактора гидрирования имеет такое разбавление, что способ будет приводить к заранее определенной концентрации твердой терефталевой кислоты после конечной стадии кристаллизации. Таким образом, зная количество жидкости, добавленной и удаленной, и зная количество кристаллизующейся терефталевой кислоты, можно определить концентрацию твердой ТФК. При добавлении разбавляющей воды к продуктовому потоку из каждой кристаллизационной стадии, разбавление, требуемое при начальной загрузке потока, оказывается значительно более низким.
Разбавляющая жидкость, добавляемая к продуктовому потоку, может происходить из многочисленных источников. Во-первых, конденсат из кристаллизационной стадии, из которой удаляют продукт, может быть конденсирован и частично или полностью рециркулирован обратно в продуктовый поток из этой стадии. Во-вторых, может быть использован подающийся свежий растворитель, например вода, в количестве, более чем, менее чем или равном количеству жидкости, удаленной в виде дистиллята. В-третьих, если используется более чем одна кристаллизационная стадия, конденсат из стадии, не являющейся непосредственно предшествующей стадией, может быть рециркулирован в рассматриваемую кристаллизационную стадию. Этот конденсат обычно нагревают до той же температуры, что и рабочая температура предшествующей кристаллизационной стадии.
В каждом случае или часть или весь конденсируемый растворитель рециркулируют в продукт, подаваемый в кристаллизационные стадии, или дополнительный растворитель подают в кристаллизационные стадии, или используют комбинацию этих двух способов. Если присутствуют более чем две кристаллизационные стадии, то процент растворителя, подаваемый в каждую кристаллизационную стадию может изменяться. Например в некоторые кристаллизационные стадии может подаваться количество растворителя, равное количеству испаренного на предшествующей стадии, а в некоторые кристаллизационные стадии растворитель может не подаваться.
Дополнительная точка для возврата разбавляющей воды в систему может быть в той же точке линии переноса между кристаллизаторами. Эта линия обычно содержит клапан для регулирования скорости продуктового потока из одной кристаллизационной стадии в следующую. Резидентное время для кристаллизационной стадии определяется объемом кристаллизационной стадии, деленным на объемную скорость потока суспензии продукта из кристаллизационной стадии. В качестве альтернативы добавлению в линию переноса/линию загрузки, разбавляющую жидкость могут добавлять непосредственно в кристаллизационный блок. В этом случае разбавляющую воду предпочтительно добавляют ниже поверхности жидкости, более предпочтительно в основание кристаллизационного блока в хорошо перемешиваемую зону.
Если весь дистиллят из каждого кристаллизационного блока рециркулируют в продуктовый поток из этого кристаллизационного блока, то концентрация терефталевой кислоты, входящей в кристаллизационные стадии, будет равной вне зависимости от того, находится ли ТФК в жидкой фазе или твердой фазе. Таким образом, начальная концентрация жидкой ТФК в загружаемом потоке будет приблизительно равна концентрации удерживаемых конечных твердых продуктов. Это приводит к тому, что только небольшая часть терефталевой кислоты будет оставаться в растворе и не кристаллизоваться.
По сравнению с последовательными способами кристаллизации терефталевой кислоты, в которых не существует рециркуляции конденсированного растворителя в последующие стадии, поток из реактора гидрирования к первому блоку кристаллизации может быть более концентрированным и иметь более низкую скорость потока. Точно также понижение скоростей потока из одной кристаллизационной стадии в следующую приводит к понижению скоростей продуктового потока. Для поддержания предварительно определенного времени обработки при пониженных скоростях загрузочного потока, нужно уменьшать объем кристаллизационных блоков. При в значительной степени постоянной скорости потока, например более высокая температура в предшествующих и более низкая температура в последующих, кристаллизационные стадии могут иметь в значительной степени равный объем, при этом сохраняя равное время обработки.
В общем, методика выбора температурного профиля для большого числа кристаллизационных стадий состоит в выборе температур, при которых в каждой стадии кристаллизуется меньшая часть терефталевой кислоты по сравнению с предыдущей стадией. Было определено, что этот способ не только позволяет кристаллизовать меньшее количество терефталевой кислоты в каждой последующей стадии, но он также уменьшает загрязнение продукта п-толуольной кислотой. Идеальный случай, в котором этот механизм может привести к наибольшей выгоде, – в серии из бесконечного множества кристаллизационных стадий, аппроксимирующих периодические условия. Предел практического функционирования не позволяет достичь этого. В настоящем изобретении более высокая концентрация терефталевой кислоты в изначальном подаваемом потоке улучшает этот механизм, поскольку более высокие концентрации терефталевой кислоты вызывают кристаллизацию больших количеств терефталевой кислоты при более высоких температурах (в предшествующих стадиях).
Линия удаления продукта из конечного кристаллизатора загружает стандартное устройство для разделения твердое вещество-жидкость для выделения продукта кристаллической терефталевой кислоты, содержащего менее чем 150 мас. млн.ч. п-толуольной кислоты. Поскольку температура последней кристаллизационной стадии может быть меньше, чем нормальная точка кипения растворителя, может использоваться вакуумное фильтрование (вместо фильтрования под давлением). Влажную кристаллическую терефталевую кислоту можно промывать перед загрузкой в сушку. Отфильтрованный маточный раствор и жидкость, использованную для промывки, собирают для повторного использования в стадии гидрирования. Часть отфильтрованной жидкости может быть очищена для уменьшения количества накопленных примесей в системе.
Опять, обращаясь к фиг.2, продукт гидрирования удаляют из реактора гидрирования 110 и подают через клапан 130 в первый кристаллизационный блок 122 в точке ниже поверхности суспензии, содержащейся в сосуде 122, около дна сосуда 122, где гидростатический напор выше. Устройство для перемешивания, такое как крыльчатка 170, располагают в первом кристаллизационном блоке 122 так же, как и в других кристаллизационных блоках. Продуктовый поток постоянно удаляют из первого кристаллизационного блока 122 через трубопровод 140. Продуктовый поток удаляют из хорошо перемешиваемой зоны кристаллизационного блока 122, таким образом, что содержимое продуктового потока представляет собой среднее от всего содержимого этого кристаллизационного блока 122. Продуктовый поток подают через клапан 134 во второй, последующий кристаллизационный сосуд 124, который функционирует при давлении и температуре ниже, чем давление и температура внутри кристаллизатора 122. Продуктовый поток подают в хорошо перемешиваемую зону кристаллизационного блока 124. Поскольку последующий кристаллизационный блок 124 функционирует при более низкой температуре, часть ТФК, остающейся в растворе, кристаллизуется, указанная часть определяется равновесной концентрацией ТФК при рабочей температуре второго кристаллизационного блока 124.
Пар растворителя непрерывно удаляют из первого кристаллизационного блока 122 через трубопровод 142 и загружают в теплообменник 150, в котором весь или часть растворителя конденсируется. Переохлаждение пара до температуры в значительной степени ниже точки кипения также может проводится внутри теплообменника. Часть или весь конденсированный растворитель подают в продуктовый поток 140 через клапан 136. Весь конденсированный растворитель, не рециркулированный в продуктовый поток, может быть удален через трубопровод 144. Сосуд второй кристаллизационной стадии 124 функционирует сходным образом с первой кристаллизационной стадией 110 и включает кристаллизационный блок 124, имеющий внутри крыльчатку 172. Продукт удаляют из кристаллизационного блока 124 через трубопровод 146. Испаренный растворитель удаляют из второго кристаллизационного блока 124 и направляют в холодильник 152, в котором испаренный растворитель конденсируют и конденсированный растворитель рециркулируют через клапан 138 и/или удаляют через трубопровод 148. Свежий, дополнительный растворитель, например воду, могут добавлять в последовательную кристаллизационную систему, изображенную на фиг.1, через линию 143 и/или линию 147.
Продукт кристаллизации удаляют из кристаллизатора 124 через трубопровод 146 и переносят через клапан 137 в зону разделения твердое вещество/жидкость 180. Температура в последней кристаллизационной стадии может быть ниже нормальной точки кипения растворителя, что делает возможным разделение твердое вещество-жидкость при помощи фильтрации под вакуумом. В зоне разделения твердое вещество-жидкость 180 удаляют маточный раствор из кристаллического осадка на фильтре в первой зоне. Кристаллический осадок на фильтре затем промывают во второй зоне.
Выгода и преимущества, получаемые от способа настоящего изобретения, включают:
1. Такое же выделение терефталевой кислоты на стадию, как и в предшествующем уровне технологии, может быть получено при установке температур кристаллизационных стадий, более близких друг к другу при более высоких температурах. Этот способ функционирования может минимизировать резкое охлаждение потока постгидрирования в температурном диапазоне, в котором большая часть терефталевой кислоты кристаллизуется из раствора. Использование обычных температур кристаллизации с более чистой неочищенной ароматической дикарбоновой кислотой приводит к тому, что при кристаллизации большее количество ароматической дикарбоновой кислоты кристаллизуется из раствора при обычных температурах.
2. Для заданного резидентного времени и скорости получения объем предшествующих (стоящих выше, ранее по потоку) кристаллизаторов с более высокой температурой и высоким давлением, может быть значительно меньше объема, требуемого согласно известным способам, поскольку начальная концентрация терефталевой кислоты в растворе может быть значительно выше, при этом также приводя к тому же содержанию суспендированного твердого вещества в конечном продуктовом потоке. Меньшие объемы кристаллизаторов приводят к значительному снижению себестоимости.
3. Благодаря возможности отделять кристаллы ароматической дикарбоновой кислоты от маточного раствора при температуре ниже точки кипения растворителя, отпадает необходимость в использовании оборудования для закрытого фильтрования и фильтрования под давлением для осуществления разделения. Это позволяет использовать более эффективные по стоимости устройства для разделения твердое вещество-жидкость, при этом сохраняя эффективное разделение.
Примеры
Способ по данному изобретению далее проиллюстрирован следующими примерами. В примерах части приведены по массе и проценты по массе, за исключением специально оговоренных случаев.
Пример 1
Этот пример показывает способность очищать неочищенную терефталевую кислоту, имеющую концентрацию п-толуольной кислоты 429 мас. млн.ч., до концентрации ниже предела допустимой чистоты для очищенной терефталевой кислоты (150 мас. млн.ч.). Он также показывает, что эта спецификация может быть достигнута выделением терефталевой кислоты при температуре ниже температуры кипения растворителя.
В автоклав высокого давления загружали воду (растворитель) и неочищенную терефталевую кислоту в количестве, приведенном в таблице I для экспериментов 1, 2 и 3. Это количество соответствует примерно 30% раствору терефталевой кислоты в воде. Содержание п-толуольной кислоты в неочищенной терефталевой кислоте составляло 429,37 мас. млн.ч. по отношению к твердому веществу. Содержимое автоклава нагревали до 280°С и выдерживали при этой температуре в течение одного часа, чтобы гарантировать, что все твердые вещества растворились. Для того чтобы имитировать множество последовательно соединенных кристаллизаторов, содержимое автоклава охлаждали до комнатной температуры со скоростью 30°С в час. Затем содержимое автоклава опять нагревали до 60°С, при этой температуре содержимое поддерживали в течение одного часа. Затем автоклав открывали и проводили разделение твердое вещество-жидкость полученных суспензий при 60°С. После охлаждения до 60°С концентрации п-толуольной кислоты в полученном очищенном твердом веществе терефталевой кислоты представлены в таблице I.
Таблица I |
Материал |
Эксперимент 1 |
Эксперимент 2 |
Эксперимент 3 |
Неочищенная терефталевая кислота (части) |
37.5051 |
37.505 |
37.4948 |
Вода (части) |
87.7337 |
87.5131 |
87.4698 |
п-толуольная кислота (мас. млн.ч.) |
429.37 |
429.37 |
429.37 |
п-толуольная кислота (мас. млн.ч.), присутствующая в очищенной терефталевой кислоте (60°С) |
155.71 |
91.66 |
79.12 |
п-толуольная кислота (мас. млн.ч.), присутствующая в очищенной терефталевой кислоте (95°С) |
113.03 |
64.96 |
36.81 |
В двух из трех экспериментов чистота полученных твердых веществ была в пределах 150 мас. млн.ч. максимального содержания п-толуольной кислоты для терефталевой кислоты. Терефталевая кислота, выделенная в эксперименте 1, имела концентрацию п-толуольной кислоты 155,71 мас. млн.ч.
Пример 2
Этот пример показывает влияние температуры выделения на чистоту конечного продукта, части загрузки автоклава при комнатной температуре, полученные в экспериментах 1, 2 и 3 примера 1, отдельно помещали в хорошо перемешиваемый сосуд. Вместо повторного нагревания до 60°С, которое проводилось в примере 1, в примере 2 части повторно нагревали до 95°С и поддерживали при этой температуре в течение 1 часа. Разделение твердое вещество-жидкость проводили при 95°С для получения образцов твердых веществ, которые анализировали на концентрацию п-толуольной кислоты. Результаты также представлены в таблице 1. Как можно видеть выделение при более высокой температуре 95°С приводит к продукту с более низким содержанием п-толуольной кислоты по сравнению с материалом, выделенным при более низкой температуре 60°С. Увеличение чистоты продуктов может достигаться повышением температуры выделения от 60°С, при сохранении температуры разделения твердое вещество-жидкость ниже точки кипения растворителя.
Пример 3
В автоклав высокого давления загружали воду (растворитель) и неочищенную терефталевую кислоту в количестве, приведенном в таблице II для экспериментов 4 и 5. Эти образцы соответствуют примерно 20% раствору неочищенной терефталевой кислоты в водном растворе. Содержание п-толуольной кислоты в твердой неочищенной терефталевой кислоте составляло 429,37 мас. млн.ч. Образцы нагревали до 280°С и выдерживали при этой температуре в течение одного часа, чтобы гарантировать, что все твердые вещества растворились. Образцы охлаждали до комнатной температуры со скоростью 30°С в час. Затем, как было проведено в случае примеров 1 и 2, часть каждого образца нагревали до 60°С и разделяли при этой температуре, а часть каждого образца нагревали до 95°С и разделяли при этой температуре. Концентрация п-толуольной кислоты в полученных твердых веществах представлена в таблице II.
Таблица II |
Материал |
Эксперимент 4 |
Эксперимент 5 |
Неочищенная терефталевая кислота (части) |
25.0104 |
25.0017 |
Вода (части) |
99.9537 |
100.2292 |
п-толуольная кислота (мас. млн.ч.) |
429.37 |
429.37 |
п-толуольная кислота (мас. млн.ч.), присутствующая в очищенной терефталевой кислоте (60°С) |
65.37 |
51.23 |
п-толуольная кислота (мас. млн.ч.), присутствующая в очищенной терефталевой кислоте (95°С) |
40.49 |
44.56 |
В примере 3 использовали большее количество разбавляющего раствора по сравнению с примером 1 (20% против 30%). Неочищенная терефталевая кислота, использованная для примера 1 и примера 2, имела одинаковое содержание п-толуольной кислоты (429,37 мас. млн.ч.). Таким образом, в случае примера 3 в изначально разбавленном растворе содержалось меньше п-толуольной кислоты. Сравнение таблицы II с таблицей I показывает преимущества более низкого содержания п-толуольной кислоты в изначальном растворе с точки зрения чистоты конечного продукта.
Разделение твердое вещество-жидкость удаляет твердые вещества из маточного раствора. В таблице III сравниваются концентрации п-толуольной кислоты в маточном растворе для экспериментов, представленных в примере 2 и примере 3, в которых очищенную терефталевую кислоту выделяли при 95°С. При более низкой концентрации используемой неочищенной п-толуольной кислоты в растворе находилось меньшее количество п-толуольной кислоты. Это приводит к более низкому содержанию п-толуольной кислоты в маточном растворе, полученном после разделения твердое вещество-жидкость. Балансировка по массе показывает, что при более низком содержании п-толуольной кислоты в маточном растворе твердый продукт также имеет более низкое содержание п-толуольной кислоты.
Неочищенная терефталевая кислота, использованная для экспериментов 1-5, представленных в таблице III, содержала 429,37 мас. млн.ч. п-толуольной кислоты. Количество разбавителя изменялось. Однако по аналогии можно предположить из таблицы III, что если чистота неочищенного исходного материала увеличивается при сохранении постоянного уровня разбавления, может быть получен более чистый продукт.
Таблица III |
Материал |
Эксперимент 1 |
Эксперимент 2 |
Эксперимент 3 |
Эксперимент 4 |
Эксперимент 5 |
Неочищенная терефталевая кислота |
30% |
30% |
30% |
20% |
20% |
Концентрация п-толуольной кислоты в маточном растворе (при 95°С) |
144.48 |
164.07 |
157.85 |
107.92 |
98.63 |
Формула изобретения
1. Способ получения и выделения кристаллической терефталевой кислоты, содержащей менее чем 150 мас. млн.ч. п-толуольной кислоты, от массы терефталевой кислоты, предусматривающий
(1) загрузку (i) пара-ксилола, (ii) водной реакционной уксусно-кислой среды, содержащей растворенные в ней компоненты катализатора окисления, и (iii) газ, содержащий кислород, в первую под давлением зону окисления, в которой происходит жидкофазное экзотермическое окисление пара-ксилола, в которой температура и давление внутри первого под давлением реактора окисления поддерживают при 150 ÷ 180°С и 3,5 ÷ 13 абсолютных бар;
(2) удаление из верхней части первого реактора пара, содержащего упаренную водную уксусно-кислую реакционную среду и газ, обедненный кислородом, включающий диоксид углерода, инертные компоненты и менее чем 9 об.%, в расчете на неконденсируемые компоненты пара, кислорода;
(3) удаление из нижней части первого реактора окисленного продукта, включающего (i) твердую и растворенную терефталевую кислоту и продукты неполного окисления и (ii) водную уксусно-кислую реакционную среду, содержащую растворенный катализатор окисления;
(4) загрузку (i) окисленного продукта со стадии (3) и (ii) газа, содержащего кислород, во вторую под давлением зону окисления, в которой проходит жидкофазное, экзотермическое окисление продуктов неполного окисления, при этом температуру и давление во втором под давлением реакторе окисления поддерживают при 185 ÷ 230°С и 4,5 ÷ 18,3 абсолютных бар;
(5) удаление из верхней части второго реактора пара, содержащего испаренную водную уксусно-кислую реакционную среду и газ, обедненный кислородом, включающий диоксид углерода, инертные компоненты и менее чем 5 об.%, в расчете на неконденсируемые компоненты пара, кислорода;
(6) удаление из нижней части второго реактора второго окисленного продукта, включающего (i) твердую и растворенную терефталевую кислоту и (ii) водную, реакционную среду уксусной кислоты, содержащую растворенный катализатор окисления;
(7) отделение терефталевой кислоты от (ii) водной реакционной уксусно-кислой среды стадии (6) для получения терефталевой кислоты, содержащей менее чем 900 мас. млн.ч. 4-карбоксибензальдегида и п-толуольной кислоты;
(8) растворение терефталевой кислоты, полученной на стадии (7), в воде для образования раствора, содержащего от 10 до 35 мас.% растворенной терефталевой кислоты, содержащей менее чем 900 мас. млн.ч. 4-карбоксибензальдегида и п-толуольной кислоты по отношению к массе присутствующей терефталевой кислоты, при температуре 260 ÷ 320°С и давлении, достаточном для поддержания раствора в жидкой фазе, и введение в контакт раствора с водородом в присутствии катализатора гидрирования с получением раствора гидрированного продукта;
(9) загрузку раствора стадии (8) в зону кристаллизации, включающую множество соединенных в серии кристаллизаторов, в которых раствор подвергают испарительному охлаждению с регулируемой скоростью путем значительного понижения давления и температуры, для инициирования кристаллизации терефталевой кислоты, при этом давление раствора в конце зоны кристаллизации является атмосферным или ниже;
(10) конденсацию растворителя, упаренного из кристаллизаторов, и возврат конденсированного растворителя в зону кристаллизации путем подачи части конденсированного растворителя в линию удаления продукта кристаллизатора, из которого удаляют растворитель в виде пара; и
(11) выделение твердой кристаллической терефталевой кислоты, содержащей менее чем 150 мас. млн.ч. п-толуольной кислоты в расчете на массу терефталевой кислоты, разделением твердое вещество-жидкость при атмосферном давлении.
2. Способ по п.1, в котором стадии (2) и (5), включают
(2) удаление из верхней части первого реактора пара, содержащего упаренную водную уксусно-кислую реакционную среду и газ, обедненный кислородом, включающий диоксид углерода, метан, инертные компоненты и менее чем 9 об.% кислорода в расчете на неконденсируемые компоненты пара;
(5) удаление из верхней части второго реактора пара, содержащего испаренную водную уксуснокислую реакционную среду и газ, обедненный кислородом, включающий диоксид углерода, инертные компоненты и от 0 до 1 об.% кислорода в расчете на неконденсируемые компоненты пара;
3. Способ по п.2, в котором стадию 1 проводят при 155 ÷ 165°С и 5,2 ÷ 6,9 абсолютных бар в присутствии водной реакционной уксуснокислой среды, содержащей от 4 до 6 мас.% воды, содержащей растворенные в ней компоненты катализатора окисления, включающие кобальт, марганец и бром; при этом вторую под давлением зону окисления стадии (4) поддерживают при температуре и давлении от 205 до 215°С и примерно от 13,4 до 17,2 абсолютных бар; терефталевая кислота на стадии (7) содержит от 400 до 900 мас. млн.ч. п-карбоксиальдегида и п-толуольной кислоты.
4. Способ по п.3, в котором атомное отношение Со:Mn:Br составляет от 5 до 40:1,0:4 до 40.
5. Способ по п.1, в котором второй окисленный продукт стадии (6) загружают в зону мгновенного испарения, в которой температуру и давление второго окисленного продукта уменьшают путем мгновенного испарения.
6. Способ по п.2, в котором второй окисленный продукт стадии (6) загружают в зону мгновенного испарения, включающую (i) первый сосуд для мгновенного испарения, функционирующий при температуре от 170 до 190°С и давлении от 2,4 до 5,2 абсолютных бар и (ii) второй сосуд для мгновенного испарения, функционирующий при температуре от 60 до 100°С и давлении от 0,3 до 0,8 абсолютных бар, в котором температуру и давление второго окисленного продукта уменьшают мгновенным испарением.
7. Способ по п.1, в котором раствор стадии (8) содержит от 25 до 35 мас.% растворенной терефталевой кислоты; раствор продукта гидрирования стадии (8) содержит от 400 до 900 мас. млн.ч. растворенной п-толуольной кислоты по отношению к массе присутствующей терефталевой кислоты, и множество последовательно соединенных кристаллизаторов состоит из от двух до восьми кристаллизаторов.
8. Способ по п.7, в котором температура первого кристаллизатора находится в диапазоне 200 ÷ 260°С и температура последнего кристаллизатора находится в диапазоне 80 ÷ 100°С, и множество последовательно соединенных кристаллизаторов состоит из от трех до шести кристаллизаторов.
РИСУНКИ
|
|