|
(21), (22) Заявка: 2003100051/11, 09.01.2003
(24) Дата начала отсчета срока действия патента:
09.01.2003
(30) Конвенционный приоритет:
10.01.2002 FI 20020045
(43) Дата публикации заявки: 10.07.2004
(46) Опубликовано: 27.01.2007
(56) Список документов, цитированных в отчете о поиске:
DE 1903668 А, 20.08.1970. DE 3739422 А, 26.05.1988. US 3578053 А, 11.05.1971. RU 2144861 С1, 27.01.2000.
Адрес для переписки:
191186, Санкт-Петербург, а/я 230, “АРС-ПАТЕНТ”, пат.пов. В.М.Рыбакову, рег. № 90
|
(72) Автор(ы):
ЕРОМЯКИ Пентти Юхани (FI), ПИРХОНЕН Юха (FI)
(73) Патентообладатель(и):
НОКИАН РЕНКААТ ОЙЙ (FI)
|
(54) ШИП ПРОТИВОСКОЛЬЖЕНИЯ С МЕТАЛЛОКЕРАМИЧЕСКИМ ЭЛЕМЕНТОМ
(57) Реферат:
Изобретение относится к автомобильной промышленности и касается шипов противоскольжения, устанавливаемых в предварительно выполненные отверстия протектора шин транспортных средств, включающего определенное количество элементов рисунка. Шипы противоскольжения содержат корпус, в котором имеются нижний фланец и стержневая часть. Нижний фланец образует внутреннюю головку, устанавливаемую в элемент рисунка протектора шины, стержневая часть образует наружную головку, направленную наружу из элемента рисунка протектора. Указанный шип включает один продолговатый металлокерамический элемент. Металлокерамический элемент имеет пятиугольную форму в поперечном сечении, перпендикулярном продольной оси шипа. В результате увеличивается сила сцепления шин со скользкой дорогой. 9 з.п. ф-лы, 11 ил.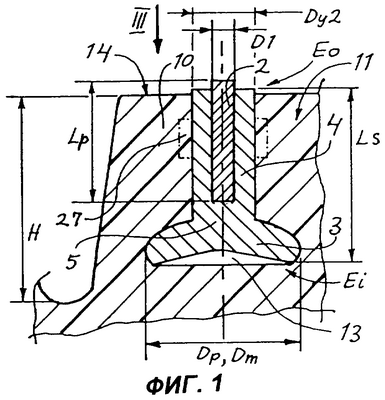
Область техники, к которой относится изобретение
Изобретение касается шипа противоскольжения, устанавливаемого в предварительно выполненные отверстия протектора шин транспортных средств, включающего определенное количество элементов рисунка, располагаемых друг за другом по меньшей мере по окружности шины. Шип имеет определенную длину и включает корпус с нижним фланцем и стержневой частью, которые имеют максимальный диаметр меньше длины шипа, при этом нижний фланец образует внутреннюю головку, устанавливаемую в элемент рисунка протектора шины, а стержневая часть образует наружную головку, направленную наружу из элемента рисунка протектора. Шип также содержит закрепленный в корпусе и проходящий от упомянутой наружной головки внутрь стержня один продолговатый металлокерамический элемент, имеющий длину в направлении продольной оси шипа и поперечные размеры, значительно меньшие указанного максимального диаметра. Изобретение касается шипов противоскольжения, устанавливаемых в заранее выполненные для них отверстия, отличающихся от описанного шипа тем, что они включают указанный корпус и металлокерамический элемент, определяющий его форму.
Уровень техники
Обычно шип противоскольжения образуется из твердосплавного круглого штыря, крепящегося к круглому корпусу, в котором имеется стержневая часть, выступающая на сторону протектора шины, и фланцевая нижняя часть, направленная к каркасу шины. Эти шипы противоскольжения вдавливаются в имеющиеся в протекторе предварительно изготовленные отверстия для получения шипованной шины. В таком типе шипов сила сцепления основана на проникновении имеющейся в шипе твердометаллической части в дорожную поверхность, на величину которой влияет, в частности, выступ головки шипа по отношению к уровню поверхности протектора шины. В таких шипах противоскольжения недостатком является склонность к округлению наружной головки шипов во время использования, что ухудшает вхождение шипов в дорожную поверхность и, таким образом, их силу сцепления. Для улучшения силы сцепления шипов в публикации DE-2804939 описана конструкция шипа, в которой поперечное сечение шипа, параллельное плоскости протектора, имеет V-образную форму и в которой из шины наружу выходят выступы в виде ласточкиного хвоста. Шип, однако, не имеет нижнего фланца. Такая конструкция, возможно, улучшает силу сцепления, однако, так как описанные шипы имеют в направлении протектора толщину обычного шипа, но значительно их длиннее, то масса описанных в данной публикации шипов значительно больше массы традиционных круглых шипов. В результате этого при движении возникает высокий уровень шума, сильный износ дорожного покрытия и большие нагрузки на шину, способные вызвать ее повреждение.
В публикации DE-2161261 описываются призматические, в особенности, имеющие форму прямоугольника шипы противоскольжения, которые изготовлены из такого композитного материала, в котором внутри пластика имеется большое количество корундовых гранул, и эти шипы крепятся клеем или привариванием к сплошной и идущей по окружности шины пластиковой ленте. Эти шипы противоскольжения вулканизированы в резину протектора шины в процессе изготовления шины. Такой способ позволяет получить относительно легкие шипы противоскольжения, однако опыт показывает, что во время эксплуатации, т.е. при движении на шипованных вышеописанным способом шинах, шипы в целом, равно как и корундовые гранулы, легко отрываются от самого материала, и что такой материал шипов сам по себе весьма быстро изнашивается. В результате сила сцепления даже новой шины является небольшой и продолжает уменьшаться в процессе использования.
В публикациях US-5458174 и US-5897177 описаны шипы противоскольжения, в корпусе которых не имеется нижнего фланца, а корпус шипа является стальным и имеет винтовую форму. Этот корпус винтовой формы включает остроконечную резьбу для закручивания в протектор шины и шестигранную винтовую головку, позволяющую производить закручивание и выкручивание. В соответствии с публикацией US-5458174 в головку этого винтообразного стального корпуса запаян карбидный штырь, а в соответствии с публикацией US-5897177 сверху наружной головки винтообразного стального корпуса запаяна или заварена масса износостойких карбидных частиц. Эти шипы должны устанавливаться путем вкручивания в такую поверхность протектора шины, в которой не имеется предварительно выполненных отверстий. Шипы противоскольжения вышеописанного типа имеют многие недостатки. Во-первых, острая головка корпуса приводит во время использования к разрушению находящегося вокруг него резинового материала и дальнейшему продавливанию шипа, что может еще больше повредить каркасные части шины. Во-вторых, выдерживающий износ карбидный материал является весьма тонким в перпендикулярном к наружной поверхности протектора направлении, поэтому во время использования он сразу изнашивается, описанные в US-5897177 частицы отрываются сразу после начала езды или спустя короткое время вследствие описанного в US-5458174 короткого штыря. После этого шип больше не способствует сцеплению шины. В этой связи отмечается, что только у полностью стальных “шипов” или их аналогов практически не наблюдается положительного эффекта с точки зрения силы сцепления колеса транспортного средства, по меньшей мере, если сравнивать ныне используемые шипы с твердометаллическим штырем или шип иного типа, изготовленный из чрезвычайно твердого материала.
В публикациях WO-96/28310 и ЕР-0864449 описаны шипы противоскольжения, основанные на другом принципе работы. Согласно этим публикациям шипы противоскольжения располагаются таким образом, что их выступ от уровня поверхности протектора шины равен нулю или весьма мал, поэтому при вращении колеса с постоянной скоростью между шипом и поверхностью дороги контакт отсутствует или происходит лишь очень легкое касание, а существенный контакт шипа с поверхностью дороги возникает только при изменении скорости. В соответствии с указанной международной публикацией шипы полностью состоят из твердого металла или содержат конусообразный твердосплавный элемент, их форма в направлении протектора или форма поперечного сечения является круглой, а торцевая часть – ровной. Масса таких шипов примерно в два раза превышает, например, максимальную массу, допускаемую существующими в Финляндии нормами. Кроме того, испытания показали, что сила сцепления описанных в данной публикации шипов чрезвычайно нестабильна, другими словами, сила сцепления или отсутствует, либо она настолько велика, что шипы отрываются от шин. Помимо этого, наружный выступ этих шипов достаточно быстро увеличивается во время использования, что в любом случае приводит к отрыву шипов вскоре после начала их использования. В указанной европейской публикации описывается, например, состоящий полностью из металлокерамического материала элемент противоскольжения, который имеет по существу пластинчатую форму, поэтому по меньшей мере общая толщина стержневой части шипа противоскольжения в направлении протектора шины не превышает одной трети ширины стержневой части в направлении протектора, нижняя часть шире стержневой части и/или отделена от стержневой части шейкой, нижняя часть по указанной ширине главным образом является прямой для обеспечения наклона элемента противоскольжения.
В патентной публикации DE 1903668 описан шип, наиболее важное свойство которого заключается в обеспечении теплоизоляции между центральным элементом из твердого материала и корпусом шипа. Теплоизоляция может быть реализована в виде воздушного зазора или пластмассы с низкой теплопроводностью, предпочтительно эпоксидной смолы. Этот воздушный зазор или пространство для размещения изолирующей пластмассы образовано за счет выполнения элемента из твердого материала с поперечным сечением круговой, треугольной или четырехугольной формы.
В патентной публикации DE 3739422 раскрыт так называемый пустотелый шип, включающий в себя полую втулку и смещаемый в осевом направлении штырь из твердого материала, снабженный подошвой и расположенный в осевой проточке втулки. Штырь из твердого материала определяет максимальную длину шипа и имеет на своей наружной поверхности осевые ребра. В альтернативном варианте штырь может иметь звездообразное поперечное сечение. Количество ребер составляет от 3 до 7. Такая форма штыря выбрана из расчета обеспечения более надежного смещения штыря относительно втулки, представляющей собой корпус шипа.
В патентной публикации JP 2000273309 описан эластичный шип, образованный полым корпусом в виде втулки и цилиндрическим элементом, размещенным внутри этого корпуса. Между цилиндрическим элементом и корпусом в виде втулки имеется воздушный зазор, а цилиндрический элемент проходит через весь корпус таким образом, что он упирается своей полусферической подошвой непосредственно в резину протектора шины. Соответственно, также имеет место пустотелый шип с теплоизоляцией между центральным цилиндрическим элементом и окружающим корпусом в виде втулки. В публикации описаны различные формы поперечного сечения цилиндрического элемента, направленные на обеспечение указанного теплоизолирующего воздушного зазора. Корпус в виде втулки изготовлен из эластичного материала типа эпоксидной смолы, нейлона, полиамида, полиизоцианата, полисульфида или фенольной смолы. Центральный цилиндрический элемент изготовлен из вязкоупругой смеси полимеров, компонентами которой могут быть полиакрилонитрил, поливинилхлориды, полиуретан, сополимер винилхлорида, сополимер этиленвинилхлорида, сополимер этиленвинилацетата, поливинилацетат, полистирол или политетрафторэтилен. Таким образом, в данной публикации по сути не раскрыт шип противоскольжения, что само по себе понятно, поскольку одна из задач известного решения заключается в предотвращении выскабливания дорожного покрытия.
Сущность изобретения
Целью изобретения является создание описанного выше шипа противоскольжения, который обеспечил бы колесам транспортного средства большую силу сцепления особенно при езде по льду. Задачей, таким образом, является создание шипов, которые, будучи установленными в шины, обеспечили бы короткие тормозные пути, быстрый разгон и эффективное боковое сцепление при движении на поворотах. Второй целью изобретения является создание такого шипа противоскольжения, свойства которого сохранялись бы наиболее полно независимо от количества ускорений и торможений. Третьей целью изобретения является создание такого шипа противоскольжения, свойства которого сохранялись бы наиболее полно до конца износа шины и шипа противоскольжения в ходе эксплуатации. Четвертой целью изобретения является создание такого шипа противоскольжения, масса которого, по меньшей мере, существенно не превышала бы массу ныне использующихся шипов, а изнашивающее воздействие которого на талую дорожную поверхность по меньшей мере не было бы значительно выше, чем у ныне используемых шипов. Еще одной целью изобретения является создание такого шипа, который может быть установлен в шину в любом положении, т.е. для обеспечения хорошей силы сцепления шип не требовалось бы поворачивать вокруг средней линии для установки по длине шипа ни в какое определенное положение по отношению к окружному направлению шины.
Вышеизложенные недостатки могут быть устранены, а вышеперечисленные цели могут быть достигнуты с помощью шипа противоскольжения, устанавливаемого в предварительно выполненные отверстия протектора шин транспортных средств, включающего определенное количество элементов рисунка, следующих друг за другом по окружности шины. Согласно изобретению шип имеет определенную длину и содержит корпус с нижним фланцем, который образует внутреннюю головку, устанавливаемую в элемент рисунка шины, и стержневой частью, которая образует наружную головку, направленную наружу из элемента рисунка, причем максимальный диаметр упомянутого нижнего фланца и стержневой части меньше длины шипа. Шип далее содержит закрепленный в корпусе и проходящий от указанной наружной головки внутрь стержневой части один продолговатый металлокерамический элемент, имеющий определенную длину в направлении продольной оси шипа и поперечные размеры, существенно меньшие упомянутого максимального диаметра.
Удалось неожиданно обнаружить, что шины транспортного средства, оснащенные шипами противоскольжения, обеспечивают исключительно превосходные характеристики сцепления при торможении и ускорении за счет использования в них таких шипов противоскольжения, каждый из которых оснащен соответствующим изобретению металлокерамическим элементом, поперечное сечение которого, перпендикулярное продольной оси шипа, имеет пятиугольную форму.
Металлокерамический элемент, таким образом, является пятиугольным в поперечном сечении, перпендикулярном продольной оси шипа противоскольжения, и обычно прямым или стержнеобразным по длине шипа противоскольжения. При таком выполнении в металлокерамическом элементе каждого шипа шины независимо от износа элемента постоянно имеются острые углы, какой-либо из которых при попадании в лед под воздействием вращения колеса всегда разбивает поверхность льда. В результате во льду образуется углубление или подобная вмятина, с которой металлокерамический элемент шипа способен осуществить сцепление, уменьшая тем самым движение шипа противоскольжения вдоль поверхности льда. Поскольку в шине имеется большое число шипов, некоторые из которых одновременно находятся во взаимодействии с ледяной поверхностью дороги, эффективность увеличения силы сцепления соответствующего изобретению шипа противоскольжения, или своего рода “трения” шины, является значительной. Особо следует отметить, что при увеличении числа углов, например, до восьми, в результате чего элемент противоскольжения напоминает небольшой восьмиугольный стержень, характеристики шипа противоскольжения соответствуют в пределах точности измерения ныне используемым шипам подобного типа, в которых форма металлокерамического элемента соответствует форме небольшого круглого стержня. Путем дальнейшего изменения формы сторон имеющего восемь или более углов металлокерамического элемента, например, в выпуклую форму характеристики сцепления шипа невозможно более улучшить, поэтому характеристики шипа противоскольжения будут в пределах точности измерения соответствовать ныне используемым шипам подобного типа, в которых форма металлокерамического элемента соответствует форме небольшого круглого стержня. Особо следует также отметить, что путем уменьшения числа углов лишь на один, т.е. до четырех, в результате чего металлокерамический элемент напоминает небольшой квадратный или прямоугольный стержень, либо на два, т.е. до трех, в результате чего металлокерамический элемент напоминает небольшой треугольный стержень, шипы противоскольжения становятся ориентирующими. Это означает, что шипы при установке должны поворачиваться в определенное положение вокруг их средней линии таким образом, что, например, диагонали между углами четырехугольных металлокерамических элементов устанавливаются по окружности шины и, соответственно, в боковом направлении протектора, что делает установку, по меньшей мере, сложной и длительной. Если не учитывать положения, характеристики шины, имеющей такие шипы, в среднем соответствуют характеристикам шины, в которой имеются обычные шипы противоскольжения, содержащие круглые металлокерамические элементы. В отношении же треугольных металлокерамических элементов, если один угол находится в эффективном положении по основному направлению движения, результатом является то, что другая сторона угла является поперечной и неэффективной, поэтому способность металлокерамического элемента входить в лед может быть хуже, чем способность вхождения шипа, имеющего круглый металлокерамический элемент. Характеристики содержащей такие шипы шины в среднем соответствуют характеристикам шины, в которой имеются шипы противоскольжения, содержащие обычные круглые металлокерамические элементы.
В предпочтительном варианте осуществления изобретения пятиугольное поперечное сечение металлокерамического элемента, который образует корпус или закреплен в корпусе, имеет стороны, размеры которых в плоскости, перпендикулярной продольной оси шипа, по существу одинаковы между собой. В случае закрепленного в корпусе металлокерамического элемента его пятиугольное поперечное сечение имеет углы, максимальный радиус закругления которых предпочтительно составляет 0,5 мм или 0,2 мм. Корпус, окружающий металлокерамический элемент, в поперечном сечении, которое перпендикулярно продольной оси шипа, предпочтительно имеет круглую или по меньшей мере по существу закругленную форму.
В следующем варианте осуществления изобретения поперечное сечение пятиугольного металлокерамического элемента имеет вогнутые стороны или по существу прямые стороны. Поперечное сечение образующего корпус или закрепляемого в корпусе металлокерамического элемента предпочтительно имеет стороны, минимальные внешние углы между которыми составляют 245° или 250°, а металлокерамический элемент может быть закреплен в корпусе припоем или клеем, или заливкой в корпус, или конусной запрессовкой. В наружной головке корпус шипа может включать верхнюю чашку, диаметр которой не превышает диаметр нижнего фланца и которая отделена от нижнего фланца сужением, а также включать в этой головке в основном цилиндрическую верхнюю часть, диаметр которой существенно меньше, чем диаметр нижнего фланца. Указанная цилиндрическая верхняя часть предпочтительно снабжена одним или несколькими кольцевыми выступами.
Краткий перечень фигур чертежей
На фиг.1 и 2 показан первый вариант расположения шипов противоскольжения на поверхности протектора шины транспортного средства, в которых имеются соответствующие изобретению укрепленные в корпусе металлокерамические элементы, в продольных разрезах шипов противоскольжения по плоскостям I-I и II-II фиг.3 и 4 соответственно.
На фиг.3-6 показаны шипы по фиг.1 и 2 снаружи в продольном разрезе, в результате чего видны соответствующие изобретению некоторые различные формы крепящихся в шипах металлокерамических элементов, со стороны III и IV фиг.1 и 2 соответственно.
На фиг.7 в продольном разрезе по плоскости VI-VI фиг.8 показан другой вид реализации шипов противоскольжения в протекторе шины транспортного средства с образующим корпус шипа металлокерамическим элементом.
На фиг.8 со стороны плоскости VII фиг.7 показан шип по фиг.7 сверху по длине шипа противоскольжения, в результате чего в поперечном сечении видна некая форма металлокерамического элемента, полностью образующего шип.
На фиг.9 в том же разрезе, что и на фиг.1 и 2, в общих чертах показан вариант крепления соответствующего изобретению металлокерамического элемента в корпусе шипов противоскольжения.
На фиг.10 показан фрагмент угла соответствующего изобретению металлокерамического элемента, закрепленного в шипе, в том же разрезе, что и на фиг.3 и 6 в зоне V, но в увеличенном масштабе.
На фиг.11 показан один из возможных протекторов шин транспортного средства, включающий элементы рисунка протектора и разделяющие элементы пазы, а также вариант расположения шипов противоскольжения на поверхности данного протектора перпендикулярно протектору в направлениях III и IV по фиг.1 и 2.
Сведения, подтверждающие возможность осуществления изобретения
По меньшей мере прежде всего в накачиваемых шинах имеется выполненный из подходящей для данной цели резины, резиновой смеси или резиновых слоев протектор 11, который включает несколько элементов рисунка 10, следующих подряд по меньшей мере по окружности Р, а также разделяющие их поперечные пазы 12. Чаще всего в протекторе 11 также по ширине шины, то есть перпендикулярно плоскости окружности, имеется как минимум два ряда различных элементов рисунка 10. Другими словами, элементы рисунка обычно располагаются по окружности двумя рядами, которые являются параллельными по ширине шины. Кроме этого, элементы рисунка 10 могут соответствующим образом находиться в шахматном порядке или иметь другой целесообразный дизайн для придания шине сцепляющей способности в снегу, слякоти, на мокрой дорожной поверхности и, конечно, на сухой дорожной поверхности. Данные элементы рисунка 10 должны включать достаточно однородную сплошную резиновую часть, которая способна удерживать установленный в элемент рисунка шип противоскольжения и выдерживать силы, возникающие между шипом противоскольжения и протектором 11 шины. Ясно, что в протекторе могут быть и такие элементы рисунка, которые не предназначены для размещения шипов противоскольжения, также как и расположенные по окружности ребра и пазы, мелкие пазы и т.д. В таких вышеперечисленных элементах рисунка 10 шины транспортного средства, т.е. в данном случае протектора 11 так называемой зимней шины, имеются предварительно изготовленные отверстия для шипов 13. Эти отверстия для шипов 13 выполняются обычно в ходе изготовления шины одновременно с элементами рисунка и разделяющими их пазами, а также с другими формами протектора шины. В эти отверстия 13, предварительно выполненные в зимних шинах после их изготовления, до начала использования шины устанавливаются шипы противоскольжения 1 каким-либо уже известным или новым способом.
Шипы противоскольжения 1 включают корпус 5, в котором имеется нижний фланец 3 и стержневая часть 4. Шип противоскольжения имеет полную длину, т.е. длину шипа Ls, и обычно используется в основном перпендикулярно наружной поверхности 14 протектора шины 11, которая имеет ширину не больше чем 50% глубины паза Н, также как примерно 70%-80% от глубины паза Н. Форма нижнего фланца 3 может изменяться как по длине, так и по ширине шипа, как показано на фиг.1-4 и 7. Шипы противоскольжения 1 имеют меньший, чем длина шипа Ls, максимальный диаметр Dm, который обычно определяется нижним фланцем 3. Можно также, хотя и невыгодно, образовать самое широкое место шипа с помощью шайбы, устанавливаемой в месте выхода на наружную поверхность 14 протектора 11 или рядом с ним, в результате чего конструкция будет несколько напоминать шип по фиг.2. В этом случае между шайбой и нижним фланцем должно быть более узкое сужение 15. Такое сужение может использоваться также в том случае, когда нижний фланец 3 определяет максимальный диаметр шипа противоскольжения Dm, как показано на фиг.2. Выгодно, однако, придать корпусу 5 шипа противоскольжения такую форму, которая включает в наружной головке Ео верхнюю чашку 25, диаметр Dy1 которой не превышает диаметр Dp нижнего фланца и которая отделена от нижнего фланца сужением, как показано на фиг.2 и 7. Диаметр Dk сужения 15 значительно меньше, чем диаметр Dy1 верхней чашки и значительно меньше, чем диаметр Dp нижнего фланца, обычно диаметр Dk сужения составляет как минимум 30%, но может быть также примерно на 50% меньше, чем диаметр Dy1 и Dp верхней чашки или нижнего фланца. Сужение 15 обычно также занимает значительное место по длине шипа Ls. Тогда верхняя чашка 25 эффективно предотвращает наклон шипа противоскольжения в элементе рисунка протектора шины во время езды. В качестве альтернативы корпус 5 шипа противоскольжения включает в своей наружной головке в основном цилиндрическую верхнюю часть, диаметр Dy2 которой существенно меньше, чем диаметр Dp нижнего фланца, как показано на фиг 1. Понятно, что цилиндрическая верхняя часть не обязательно должна быть абсолютно прямым цилиндром и может иметь несколько коническую форму с наклоном в любом направлении, например, меньше 20° или не превышающим 10°, либо она может быть в соответствующей степени выпуклой или бочкообразной, или может иметь вмятину, образованную внутрь обратным способом. Можно также использовать в указанной верхней части один или несколько кольцевых выступов 27, которые также значительно меньше нижнего фланца, как обозначено пунктирными линиями на фиг.1.
В первом варианте осуществления изобретения, в котором металлокерамический элемент 2 является отдельным элементом, но крепится в корпусе, корпус 5 обычно имеет круглые или округленные формы в поперечном сечении, перпендикулярном продольной оси шипа. Такой шип противоскольжения может иметь в поперечном сечении полностью круглую или овальную форму или грани, исходя из того, что разница в максимальном и минимальном диаметре в каждой точке по длине шипа достаточно мала. Во втором варианте осуществления изобретения, в котором металлокерамический элемент образует корпус шипа, форма поперечного сечения стержневой части 4 корпуса 5 в соответствии с изобретением является пятиугольной, как показано на фиг.8, в то время как нижний фланец 3 корпуса обычно имеет круглые или округленные формы в поперечном сечении, перпендикулярном продольной оси шипа, также как в первом варианте осуществления. Во втором варианте форма нижнего фланца в поперечном сечении может быть полностью круглая или овальная или она может содержать грани, исходя из того, что разница между максимальным и минимальным диаметром в каждой точке по длине шипа достаточно мала. В обоих вариантах осуществления максимальный диаметр должен превосходить в 1,5 раза или предпочтительно в 1,3 раза минимальный диаметр. Показанные на фигурах формы шипа противоскольжения нельзя рассматривать как ограничивающие изобретение, а соответствующий изобретению металлокерамический элемент может использоваться в принципе в шипах противоскольжения любой формы, когда речь идет о шипе противоскольжения 1, устанавливаемом в элементы рисунка протектора, отличающегося от описанного типа. Нижний фланец 3 шипа противоскольжения, установленный в элемент рисунка 10 протектора, образует внутреннюю головку Ei, устанавливаемую в элемент рисунка протектора 10, а стержневая часть 4 образует наружную головку Ео, направленную наружу. Однако наружная головка Ео выступает от наружной поверхности 14 протектора лишь в незначительно степени, то есть лишь на допустимый размер выступа шипа, который составляет лишь малую долю от длины Ls шипа противоскольжения. Понятно, что отношение выступа шипа к длине шипа изменяется вследствие износа шины и шипа противоскольжения 1 во время использования, поэтому для этого отношения невозможно установить универсальное цифровое значение.
Первый вариант реализации шипа противоскольжения 1 включает закрепленный в корпусе 5 и проходящий от наружной головки Ео внутрь стержневой части 4 один продолговатый металлокерамический элемент 2, имеющий длину Lp в продольном направлении шипа и поперечные размеры D1, D2, которые значительно меньше максимального диаметра шипа противоскольжения Dm. Вышеупомянутые диаметры D1 и D2 шипа противоскольжения означают минимальное и максимальное расстояние между противоположными углами пятиугольника 7, как видно из фиг.3-6, и обычно составляют примерно 2 – 5 мм. Металлокерамический элемент 2 предпочтительно имеет одинаковую толщину по всей своей длине Lp, как показано на фиг.1 и 2, но может также немного сужаться в сторону наружной головки Ео или внутренней головки Ei. Минимальная длина металлокерамического элемента Lp составляет 50% от длины шипа Ls или обычно 60% от длины шипа Ls, а предпочтительно 70% от длины шипа Ls, но обычно менее 90% от этой длины. Второй вариант реализации шипа противоскольжения 1 включает один продолговатый металлокерамический элемент, который одновременно образует корпус шипа противоскольжения, как показано на фиг.7, в результате чего длина шипа Ls равна длине элемента Lp. По меньшей мере один из поперечных размеров D1, D2 металлокерамического элемента шипа противоскольжения, т.е. стержня 4, меньше максимального диаметра Dm, определяемого нижним фланцем шипа. И в этом случае вышеуказанные поперечные размеры D1 и D2 шипа противоскольжения означают минимальное и максимальное расстояние между противоположными углами пятиугольника 7, как видно из фиг.8, и обычно составляют примерно 4 – 15 мм. Металлокерамический элемент 2, т.е. выполненная из твердой керамики стержневая часть шипа 4, предпочтительно имеет по меньшей мере на основной части одинаковую толщину по всей своей длине Lp, как показано на фиг.7, но может также немного сужаться в сторону наружной головки Ео или внутренней головки Ei. В соответствии с изобретением металлокерамический элемент 2 имеет таким образом пятиугольную форму в поперечном сечении, перпендикулярном продольной оси шипа, в результате чего форма металлокерамического элемента 2 соответствует небольшому пятиугольному штырю, который в первом варианте осуществления изобретения главным образом находится внутри корпуса, а во втором варианте осуществления также содержит во внутренней головке нижний фланец, интегрированный в эту головку или выполненный заодно с ней.
Следующее описание металлокерамического элемента касается как первого, так и второго варианта осуществления изобретения, если не указано иное. Другими словами, закрепленный в корпусе металлокерамический элемент и металлокерамический элемент, образующий корпус, имеют одинаковые особенности. Пятиугольное поперечное сечение соответствующего изобретению металлокерамического элемента 2 включает, таким образом, пять углов 7 и стороны между ними 6а или 6b, которые имеют размеры W от каждого данного угла 7 до соседних с ним углов 7 в плоскости, перпендикулярной продольной оси шипа. Эти размеры W сторон 6а, 6b в основном одинаковы в каждом металлокерамическом элементе 2. Форма металлокерамического элемента в поперечном сечении предпочтительно является равносторонним пятиугольником, хотя и допускаются небольшие отклонения до ±10% или, предпочтительно, до ±5%. Вышеуказанные стороны 6а, 6b пятиугольного поперечного сечения металлокерамического элемента 2 могут иметь вогнутую форму 6b, как показано на фиг.3, либо являться в основном прямыми отрезками 6а, как показано на фиг.4 и 8. В последнем случае в каждом отдельном металлокерамическом элементе все стороны являются однотипными. Вышеуказанные стороны 6а, 6b в шестиугольном и семиугольном поперечном сечении металлокерамического элемента 2 являются вогнутыми сторонами 6b, как показано на фиг.5 и 6, в результате чего в каждом отдельном металлокерамическом элементе все стороны являются однотипными. Металлокерамический элемент 2 должен быть, таким образом, в основном симметричным в плоскостях, перпендикулярных продольной оси шипа и в основном параллельной ей продольной оси элемента. Минимальные внешние углы между сторонами 6а, 6b поперечного сечения металлокерамического элемента 2 составляют 245° или предпочтительно 250°. В пятиугольном поперечном сечении внешние углы между прямыми сторонами 6а по природе составляют 252°, что является достаточным значением, чтобы обеспечить грань или угол 7 нужного типа. В шестиугольном и семиугольном поперечном сечении внешние углы между прямыми сторонами 6а составляли бы лишь 240° и 231° соответственно, что, как понимается на данный момент, слишком приближено к развернутому углу, поэтому для таких форм сечения следует использовать вогнутые стороны 6b. В случае вогнутых сторон 6b находящиеся между ними внешние углы измеряются между теми тангенсами, которые определены в тех местах сторон, где перегиб сторон равен нулю, т.е. в точке перегиба. Перегиб является, как известно, производной направляющего угла тангенса поверхности по отношению к длине перегиба и, таким образом, получает нулевое значение в точках изменения направления перегиба, т.е. в точках перегиба и при прямых поверхностях. В этом случае точки перегиба образуются в точках, в которых вогнутые стороны 6b становятся выпуклыми, имеющими закругление R гранями или углами 7. На прямых сторонах 6а перегиб равен нулю, поэтому вышеописанные тангенсы соединяются в стороны, что означает аналогичное с вогнутыми сторонами определение внешних углов . Вогнутые стороны позволяют, таким образом, эффективно увеличить внешние углы . Независимо от формы сторон 6а, 6b, именно форма поперечного сечения пятиугольного металлокерамического элемента 2 рассматривается как самый эффективный вариант осуществления изобретения.
В пяти или шести, или семи углах 7 поперечного сечения металлокерамического элемента 2, которые по сути являются гранями, параллельными или почти параллельными продольной оси элемента, имеется относительно малый радиус закругления R, который в закрепленных в корпус 5 отдельных металлокерамических элементах составляет максимально 0,5 мм или 0,2 мм или близок к нулю и соответственно в образующих корпус 5 металлокерамических элементах составляет максимально 1 мм или 0,4 мм, но может приближаться к величинам закругления вышеупомянутых отдельных металлокерамических элементов. Целью такого уменьшения радиуса закругления является достижение в металлокерамическом элементе 2 острых углов или граней, которые эффективно разбивают образующий дорожную поверхность лед или аналогичную поверхность из спрессованного твердого снега при попадании в него шипов противоскольжения 1 и, таким образом, металлокерамических элементов 2 во время вращения колес транспортного средства. Во всяком случае, максимальные значения острых углов 7 металлокерамического элемента или радиусы закругления R граней, перпендикулярных продольной оси шипа и в основном параллельной ей продольной оси элемента, должны составлять 15% или обычно 10%, или предпочтительно 5% от размера W сторон 6а, 6b металлокерамического элемента. Не мешая этому, стороны 6а, 6b металлокерамического элемента могут быть шероховатыми или иначе обработанными, или измененными для улучшения описанного в дальнейшем крепления шипа противоскольжения 5 в корпусе.
Соответствующие изобретению металлокерамические элементы 2, независимо от того, крепятся ли они в корпусе или образуют собой корпус, изготовлены из подходящего материала, т.е. металлокерамического “кермета”, который обычно содержит какой-нибудь из карбидов WC, TiC, TaC, NbC или карбид другого металла, например переходного металла, а также кобальт. Фаза закрепления может также представлять или содержать оксиды металла, нитриды металлов, бориды металлов, силициды металлов и т.д., или комплексные соединения, или какой-либо другой сам по себе известный материал, или новый чрезвычайно твердый материал. Металлокерамические элементы 2 можно изготовить также без кобальта путем использования в качестве матричного материала другого металла или сплава металла, или без использования специального матричного материала. Материалы, в которых частицы прочного и твердого материала связывает какой-либо матричный материал, обычно называются композитами. Металлокерамические элементы изготавливаются из таких материалов с использованием соответствующего метода агломерации, в результате которого весь матричный материал связывает твердое вещество, т.е. частицы фазы закрепления или частицы твердого укрепляющего вещества соединяются прямо друг с другом. Традиционный твердый металл (цементированный карбид) является неким особым случаем этих материалов или металлокерамик. Эти твердые и прочные материалы, а также способы получения их определенной формы, достижение определенной твердости и прочностных характеристик, являются широко известными и постоянно пополняются новыми разработками, поэтому они здесь не рассматриваются.
В первом варианте осуществления изобретения после изготовления металлокерамических элементов 2 они крепятся в корпусе 5 шипа противоскольжения 1 или путем запаивания 8а, или путем вклеивания 8b, или путем заливки в корпус 9, или путем конической запрессовки 17. В первом упомянутом случае металлокерамические элементы 2 размещаются в отдельно изготовленные углубления или отверстия 16 корпусов шипов противоскольжения, размеры которых приближаются к размерам металлокерамического элемента таким образом, что металлокерамический элемент устанавливается в правильное положение в корпусе шипа. В данном случае корпус 5 шипа противоскольжения состоит из металла, обычно стали, хотя может использоваться и какой-нибудь легкий сплав металла, такой как алюминиевый сплав. Затем металлокерамический элемент запаивается в корпус шипа 5 подходящим припойным материалом. Металлокерамический элемент 2 может также вклеиваться соответствующим клеем в отдельно изготовленный корпус 5 шипа противоскольжения, при этом корпус шипа может быть изготовлен не только из металла, но и в качестве альтернативы также из пластика или композита специального назначения. Далее, корпус 5 шипа противоскольжения может изготавливаться путем отливки корпуса из подходящего для данной цели материала, например из пластика или металла, или пластикового композита, или металлического композита, вокруг предварительно изготовленного металлокерамического элемента 2. В результате застывания или, например, полимеризации при затвердевании этого залитого расплава или находящегося в жидком состоянии другого заливочного материала возникает соединение между ним и металлокерамическим элементом. Металлокерамический элемент 2 можно также крепить в отверстии 16 корпуса 5 путем приложения усилия или направленного удара с силой F вдоль продольной оси шипа противоскольжения, как видно из фиг.9. В связи с этим металлокерамический элемент имеет несколько конусообразную наружную поверхность 18, такую, что головка, устанавливаемая в наружную головку шипа Ео, шире, чем головка, продвигаемая в направлении внутренней головки Ei, и соответственно отверстие 16 имеет внутреннюю поверхность 19, сужающуюся к внутренней головке шипа Ei, как показано на фиг.9. При достаточно большой силе F металлокерамический элемент 2 закрепляется в отверстии корпуса 5 за счет силы трения и сжимающего усилия. Так как изготовление отверстия 16, поперечное сечение которого полностью соответствует угловатой форме поперечного сечения металлокерамического элемента, может быть сложным, допускается, что для этого способа крепления целесообразно использовать в качестве материала корпуса 5 какой-нибудь относительно мягкий, но упругий материал. Указанные способы крепления сами по себе известны, по крайней мере, в другой связи, поэтому они подробно здесь не излагаются. В качестве материала корпуса 5 шипа противоскольжения можно использовать любой известный или новый подходящий для данной цели материал, а металлокерамический элемент может крепиться в корпусе 5 с помощью любого уже известного или нового подходящего для данной цели способа или материала, которые более подробно в настоящей заявке не описываются.
Во втором варианте осуществления изобретения металлокерамические элементы 2 изготавливаются по выбранной форме шипа противоскольжения, при этом шипы противоскольжения агломерируются из какого-нибудь указанного материала известным или новым способом. Твердые и прочные материалы, а также способы получения их формы и микроструктуры, т.е. твердости и прочности, являются широко известными и постоянно пополняются новыми разработками, поэтому они здесь дальше не рассматриваются.
Формула изобретения
1. Шип противоскольжения, устанавливаемый в предварительно выполненные отверстия протектора шин транспортных средств, включающего определенное количество элементов рисунка, следующих друг за другом по окружности шины, причем шип имеет определенную длину и содержит корпус с нижним фланцем, который образует внутреннюю головку, устанавливаемую в элемент рисунка шины, и стержневой частью, которая образует наружную головку, направленную наружу из элемента рисунка, причем максимальный диаметр упомянутого нижнего фланца и стержневой части меньше длины шипа, а также закрепленный в корпусе и проходящий от указанной наружной головки внутрь стержневой части один продолговатый металлокерамический элемент, имеющий определенную длину в направлении продольной оси шипа и поперечные размеры, существенно меньшие указанного максимального диаметра, отличающийся тем, что поперечное сечение металлокерамического элемента, перпендикулярное продольной оси шипа, имеет пятиугольную форму.
2. Шип по п.1, отличающийся тем, что пятиугольное поперечное сечение металлокерамического элемента, который образует корпус или закреплен в корпусе, имеет стороны, размеры которых в плоскости, перпендикулярной продольной оси шипа, по существу одинаковы между собой.
3. Шип по любому из п.1 или 2, отличающийся тем, что пятиугольное поперечное сечение закрепленного в корпусе металлокерамического элемента имеет углы, максимальный радиус закругления которых составляет 0,5 мм или 0,2 мм.
4. Шип по любому из пп.1-3, отличающийся тем, что корпус, окружающий металлокерамический элемент, в поперечном сечении, которое перпендикулярно продольной оси шипа, имеет круглую или по меньшей мере по существу закругленную форму.
5. Шип по любому из предшествующих пунктов, отличающийся тем, что поперечное сечение пятиугольного металлокерамического элемента имеет вогнутые стороны или по существу прямые стороны.
6. Шип по любому из предшествующих пунктов, отличающийся тем, что поперечное сечение образующего корпус или закрепляемого в корпусе металлокерамического элемента имеет стороны, минимальные внешние углы между которыми составляют 245 или 250°.
7. Шип по любому из предшествующих пунктов, отличающийся тем, что металлокерамический элемент закреплен в корпусе припоем, или клеем, или заливкой в корпус, или конусной запрессовкой.
8. Шип по любому из предшествующих пунктов, отличающийся тем, что в наружной головке корпус шипа включает верхнюю чашку, диаметр которой не превышает диаметр нижнего фланца и которая отделена от нижнего фланца сужением.
9. Шип по любому из пп.1-7, отличающийся тем, что в наружной головке корпус включает в основном цилиндрическую верхнюю часть, диаметр которой существенно меньше, чем диаметр нижнего фланца.
10. Шип по п.9, отличающийся тем, что указанная цилиндрическая верхняя часть снабжена одним или несколькими кольцевыми выступами.
РИСУНКИ
|
|