|
(21), (22) Заявка: 2005104869/04, 24.02.2005
(24) Дата начала отсчета срока действия патента:
24.02.2005
(46) Опубликовано: 20.09.2006
(56) Список документов, цитированных в отчете о поиске:
RU 2051894 C1, 10.01.1996. WO 8606063 A1, 23.10.1986. SU 1479450 A1, 15.05.1989.
Адрес для переписки:
119991, Москва, ул. Косыгина, 4, Институт химической физики РАН, патентный отдел
|
(72) Автор(ы):
Арутюнов Владимир Сергеевич (RU), Рудаков Валерий Михайлович (RU), Савченко Валерий Иванович (RU), Шеверденкин Евгений Викторович (RU)
(73) Патентообладатель(и):
Институт химической физики им. Н.Н. Семенова РАН (ИХФ РАН) (RU), Арутюнов Владимир Сергеевич (RU), Рудаков Валерий Михайлович (RU), Савченко Валерий Иванович (RU), Шеверденкин Евгений Викторович (RU)
|
(54) СПОСОБ ПРОИЗВОДСТВА ФОРМАЛЬДЕГИДА
(57) Реферат:
Изобретение относится к способу производства формальдегида, включающему окисление углеводородсодержащего газа кислородсодержащим газом при повышенных температуре и давлении, последующее охлаждение реакционной смеси и отделение целевого жидкого продукта. В качестве углеводородсодержащего газа используют этансодержащий газ, в том числе природный, и попутные газы с содержанием этана не менее 10%. При этом этансодержащий газ, предварительно сжатый до 2-5 МПа и нагретый до 280-450°С, и сжатый до давления не ниже давления этансодержащего газа кислородсодержащий газ раздельно подают в смесители последовательно расположенных реакционных зон реактора до содержания кислорода в реакционных зонах 2-10% об. Реакционную смесь непрерывно охлаждают через стенку либо непосредственно в процессе окисления, либо перед ее подачей в последующую реакционную зону до температуры не выше 450°С. В качестве кислородсодержащего газа используют воздух, кислород или обогащенный кислородом воздух. Технический результат – увеличение выхода формальдегида, упрощение технологии процесса и снижение энергетических затрат. 1 з.п. ф-лы, 1 табл., 1 ил.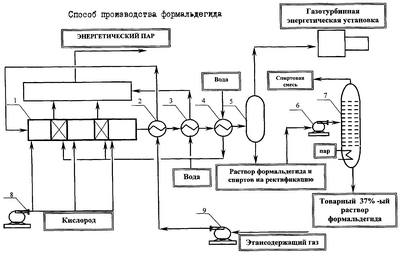
Изобретение относится к области органической химии, а именно к технологии производства формальдегида прямым окислением углеводородсодержащего газа, и может быть использовано в химической и газодобывающей промышленности.
Природный газ, по прогнозам, будет основным углеводородным ресурсом не только для энергетики, но и для химической промышленности XXI века. Однако его использование в качестве химического сырья вызывает ряд серьезных проблем, связанных с разработкой рентабельных процессов получения из него химических продуктов. Современная газохимия пока не способна серьезно конкурировать с существующими процессами на основе нефтяного сырья. Создание высокорентабельных одностадийных процессов получения ценных химических продуктов, в том числе формальдегида, из углеводородных газов позволило бы совершить серьезный прорыв в этой области, превратив природный газ в сырье для получения и других химических продуктов.
В настоящее время основным промышленным способом получения формальдегида является каталитическое дегидрирование метанола (Огородников С.К. «Формальдегид», Л., «Химия», 1984). Так как сам метанол получают каталитическим превращением синтез-газа (смеси СО и H2), полученного паровой конверсией метана, производство формальдегида является сложным многостадийным каталитическим процессом.
Большой интерес вызывают процессы прямого, минуя стадию получения синтез-газа, газофазного окисления метана в метанол и формальдегид при высоких давлениях. Процесс окисления проводят при давлениях до 10 МПа и температурах 400-450°С в трубчатых реакторах при относительно низких начальных концентрациях кислорода с последующим охлаждением газожидкостной смеси и отделением жидких продуктов, из которых ректификацией выделяют метанол и формальдегид (Арутюнов B.C., Крылов О.В. «Окислительные превращения метана», М.: «Наука», 1998, с.130-145). Однако низкая степень конверсии метана за проход через реактор, не превышающая 3-5%, и соответственно, низкий выход метанола и формальдегида, сдерживают практическое внедрение метода получения формальдегида прямым окислением метана.
Известны способы получения формальдегида как путем каталитического окислительного дегидрирования метанола кислородом воздуха (Огородников С.К. «Формальдегид», Л.: «Химия», 1984), так и путем прямого парциального окисления метана (Арутюнов B.C., Крылов О.В. «Окислительные превращения метана», М.: «Наука», 1998, с.130-145).
Наиболее близким техническим решением является способ получения формальдегида, описанный в (RU 2051894 C1, C 07 C 47/048, 21.02.1992), включающий окисление природного газа воздухом в полученной путем непосредственного смешения природного газа и воздуха газовоздушной смеси, содержащей 1-4% об. кислорода при температуре 300-400°С и давлении 3-10 МПа, в которую дополнительно вводят воздух на участке реактора с максимальным разогревом, последующее охлаждение реакционной смеси и отделение целевого жидкого продукта, который преимущественно состоит из метанола. Жидкий продукт затем подогревают до 100-120°С и подвергают окислительному дегидрированию в присутствии серебряного катализатора.
Недостатками известного способа-прототипа являются низкий выход формальдегида и необходимость проведения процесса при высоком давлении, что требует больших энергозатрат. Для повышения выхода формальдегида потребовалось введение стадии каталитического дегидрирования, что привело к усложнению технологии.
Задачей изобретения является разработка такого способа получения формальдегида прямым окислением углеводородсодержащего газа, который позволит существенно увеличить выход формальдегида, упростить технологию процесса и значительно снизить энергетические затраты.
Решение поставленной задачи достигается предлагаемым способом производства формальдегида, включающим окисление углеводородсодержащего газа кислородсодержащим газом при повышенных температуре и давлении, последующее охлаждение реакционной смеси и отделение целевого жидкого продукта, в котором согласно изобретению в качестве углеводородсодержащего газа используют этансодержащий газ, в том числе природный, и попутные газы с содержанием этана не менее 10% об., при этом этансодержащий газ, предварительно сжатый до 2-5 МПа и нагретый до 280-450°С, и сжатый до давления не ниже давления этансодержащего газа кислородсодержащий газ раздельно подают в смесители последовательно расположенных реакционных зон реактора до содержания кислорода в реакционных зонах 2-10% об., а реакционную смесь непрерывно охлаждают через стенку либо непосредственно в процессе окисления, либо перед ее подачей в последующую реакционную зону до температуры не выше 450°С.
В качестве кислородсодержащего газа можно использовать воздух, кислород или обогащенный кислородом воздух.
Главное отличие предложенного способа от известного (прототипа) заключается в том, что в качестве исходного углеводородсодержащего газа используют этансодержащий газ. Другими существенными отличиями являются параметры процесса и осуществление непрерывного съема тепла в каждой реакционной зоне через их стенки, что позволяет вести процесс при регулируемой по длине реактора температуре.
Исследования, проведенные при разработке данного способа, показали, что в отличие от парциального окисления сухого природного газа (метана) при парциальном окислении этана и смесей метана с этаном при концентрации этана более 10% об., при относительно низких давлениях – порядка 2 МПа – удается получать высокий выход формальдегида. Его концентрация в жидких продуктах окисления этана достигает 30% вес. по сравнению с 5-8% при окислении метана. Нами было обнаружено, что при окислении этана выход формальдегида, в отличие от окисления метана, проходит через максимум при содержании кислорода примерно 4-5% об. Это позволило разработать условия процесса, максимально увеличивающие степень конверсии углеводорода за проход через реактор. Было также установлено, что при снижении давления от 5-6 МПа до 2-3 МПа (при одинаковой температуре) выход и процентное содержание формальдегида в жидких продуктах окисления остаются почти постоянными, что позволило существенно снизить в предлагаемом способе такой высокоэнергоемкий параметр процесса, как давление.
Предлагаемый способ осуществляют на производственной установке, принципиальная схема которой приведена на чертеже. Реактор 1 имеет три реакционные зоны. Этансодержащий газ из питающего трубопровода сжимают компрессором 9 до нужного давления (2-5 МПа) и направляют в межтрубное пространство рекуперативного теплообменника «газ-газ» 2, в котором его нагревают до заданной температуры (280-450°С) и с этой температурой подают в смеситель первой реакционной зоны реактора 1. Кислородсодержащий газ сжимают компрессором 8 до давления не ниже давления этансодержащего газа и направляют в смесители первой, второй и третьей реакционных зон реактора 1. В реакционных зонах температуру реакционной смеси либо поддерживают постоянной – не выше 450°С – за счет непрерывного съема тепла через стенку, либо реакционную смесь охлаждают (через стенку) перед ее подачей в последующую реакционную зону. Съем тепла можно проводить, например, водяным конденсатом с образованием пара. Реакционную смесь из третьей реакционной зоны реактора 1 подают в трубное пространство рекуперативного теплообменника 2, а затем в паровой котел 3. За счет охлаждения газового потока в реакционных зонах реактора 1 и после него в паровом котле 3 вырабатывается энергетический пар с давлением 16 атм. Далее реакционную смесь охлаждают в теплообменнике 4 до температуры 25°С и подают в сепаратор 5. Газовую фазу из сепаратора 5 направляют на газотурбинную энергетическую установку, вырабатывающую электроэнергию за счет сжигания непрореагировавшего углеводородсодержащего газа. Сконденсировавшиеся жидкие продукты насосом 6 подают на ректификационную колонну 7, на которой выделяют товарный 37%-ный раствор формальдегида и метанол-этанольную смесь
Приводим примеры осуществления предложенного способа. Параметры процесса, выход и состав полученных продуктов представлены также в таблице.
Пример 1. Этансодержащий газ из питающего трубопровода, содержащий 94,2% об. этана, сжимают компрессором 9 (до давления 3,0 МПа и направляют в межтрубное пространство рекуперативного теплообменника «газ-газ» 2, в котором его нагревают до 450°С, и с этой температурой подают в смеситель первой реакционной зоны реактора 1. Воздух сжимают компрессором 8 до давления 3,1 МПа и направляют в смесители первой, второй и третьей реакционных зон реактора 1 при начальной концентрации кислорода 2% об. Во всех реакционных зонах поддерживают температуру реакционной смеси ниже 450°С за счет непрерывного съема тепла через стенку водяным конденсатом с образованием пара. Реакционную смесь из третьей реакционной зоны реактора 1 подают в трубное пространство рекуперативного теплообменника 2, а затем в паровой котел 3. За счет охлаждения газового потока в реакторе и после него в паровом котле 3 вырабатывается энергетический пар с давлением 16 атм. Далее реакционную смесь охлаждают в теплообменнике 4 до температуры 25°С и подают в сепаратор 5. Газовую фазу из сепаратора 5 направляют на газотурбинную энергетическую установку, вырабатывающую электроэнергию за счет сжигания непрореагировавшего углеводородсодержащего газа. Сконденсировавшиеся жидкие продукты насосом 6 подают на ректификационную колонну 7, на которой выделяют 37%-ный раствор формальдегида и метанол-этанольную смесь. Полный выход жидких продуктов составляет 54 кг/1000 м пропущенного газа. Концентрация формальдегида в жидких продуктах составляет 26% вес., а его выход составляет 14 кг/1000 м3 пропущенного газа.
Пример 2. Этансодержащий газ из питающего трубопровода, содержащий 94,2% об. этана, сжимают компрессором 9 до давления 2,0 МПа и направляют в межтрубное пространство рекуперативного теплообменника «газ-газ» 2, в котором его нагревают до 360°С и с этой температурой подают в смеситель первой реакционной зоны реактора 1. Воздух сжимают компрессором 8 до давления 2,1 МПа и направляют в смесители первой, второй и третьей реакционных зон реактора 1 при начальной концентрации кислорода 10% об. Во всех реакционных зонах температуру реакционной смеси снижают до температуры не выше 450°С перед ее подачей в последующую реакционную зону. Реакционную смесь из третьей реакционной зоны реактора 1 подают в трубное пространство рекуперативного теплообменника 2, а затем в паровой котел 3. За счет охлаждения газового потока в реакторе и после него в паровом котле 3 вырабатывается энергетический пар с давлением 16 атм. Далее реакционную смесь охлаждают в теплообменнике 4 до температуры 25°С и подают в сепаратор 5. Газовую фазу из сепаратора 5 направляют на газотурбинную энергетическую установку, вырабатывающую электроэнергию за счет сжигания непрореагировавшего углеводородного газа. Сконденсировавшиеся жидкие продукты насосом 6 подают на ректификационную колонну 7, на которой выделяют 37%-ный раствор формальдегида и метанол-этанольную смесь. Полный выход жидких продуктов составляет 1240 кг/1000 м3 пропущенного газа. Концентрация формальдегида в жидких продуктах составляет 6% вес., а его выход составляет 15 кг/1000 м3 пропущенного газа.
Пример 3. Этансодержащий газ из питающего трубопровода, содержащий 27,1% об. этана, сжимают компрессором 9 до давления 5,0 МПа и направляют в межтрубное пространство рекуперативного теплообменника «газ-газ» 2, в котором его нагревают до 280°С, и с этой температурой подают в смеситель первой реакционной зоны реактора 1. Воздух сжимают компрессором 8 до давления 5,1 МПа и направляют в смесители первой, второй и третьей реакционных зон реактора 1 при начальной концентрации кислорода 4% об. Во всех реакционных зонах температуру реакционной смеси снижают до температуры не выше 450°С перед ее подачей в последующую реакционную зону. Реакционную смесь из третьей реакционной зоны реактора 1 подают в трубное пространство рекуперативного теплообменника 2, а затем в паровой котел 3. За счет охлаждения газового потока в реакторе и после него в паровом котле 3 вырабатывается энергетический пар с давлением 16 атм. Далее реакционную смесь охлаждают в теплообменнике 4 до температуры 25°С и подают в сепаратор 5. Газовую фазу из сепаратора 5 направляют на газотурбинную энергетическую установку, вырабатывающую электроэнергию за счет сжигания непрореагировавшего углеводородного газа. Сконденсировавшиеся жидкие продукты насосом 6 подают на ректификационную колонну 7, на которой выделяют 37%-ный раствор формальдегида и метанол-этанольную смесь. Полный выход жидких продуктов составляет 90 кг/1000 м3 пропущенного газа. Концентрация формальдегида в жидких продуктах составляет 12% вес., а его выход составляет 11 кг/1000 м3 пропущенного газа.
Пример 4 (аналогично известному-прототипу). Природный газ из питающего трубопровода, содержащий 97% об. метана и 2% об. этана, сжимают компрессором 9 до давления 6,0 МПа и направляют в межтрубное пространство рекуперативного теплообменника «газ-газ» 2, в котором его нагревают до 450°С и с этой температурой подают в смеситель первой реакционной зоны реактора 1. Воздух сжимают компрессором 8 до давления 6,1 МПа и направляют в смесители первой, второй и третьей реакционных зон реактора 1 при начальной концентрации кислорода 3,6% об. Реакционную смесь из третьей реакционной зоны реактора 1 подают в трубное пространство рекуперативного теплообменника 2, а затем в паровой котел 3, в котором вырабатывается энергетический пар с давлением 16 атм. Далее реакционную смесь охлаждают в теплообменнике 4 до температуры 25°С и подают в сепаратор 5. Газовую фазу из сепаратора 5 направляют на газотурбинную энергетическую установку, вырабатывающую электроэнергию за счет сжигания непрореагировавшего углеводородного газа. Сконденсировавшиеся жидкие продукты насосом 6 подают на ректификационную колонну 7, на которой выделяют 37%-ный раствор формальдегида и метанол-этанольную смесь. Полный выход жидких продуктов составляет 85 кг/1000 м3 пропущенного газа. Концентрация формальдегида в жидких продуктах составляет 3% вес., а его выход составляет 2,5 кг/1000 м3 пропущенного газа.
Как видно из приведенных примеров, при использовании предложенного способа производства формальдегида удается до 6 раз увеличить выход формальдегида на пропущенный газ по сравнению с известным способом. Процесс эффективно протекает при значительно более низких давлениях, что позволяет существенно снизить энергетические затраты. Заявленный способ позволяет также повысить концентрацию формальдегида в получаемом жидком продукте, что привело к исключению из процесса стадии окислительного каталитического дегидрирования, необходимой в способе-прототипе, и упрощению технологии. Указанные преимущества обеспечивают значительный экономический эффект.
Таблица. |
|
Предложенный способ |
Аналогично известному |
Пример №1 |
Пример №2 |
Пример №3 |
Пример №4 |
Состав исходного углеводородного газа, % об, |
СН4 – 4,9 С2Н6 – 94,2 С3+ – 0,5 N2 – 0,2 CO2 – 0,2 |
СН4 – 4,9 С2Н6 – 94,2 С3+ – 0,5 N2 – 0,2 CO2 – 0,2 |
СН4-72 С2Н6 – 27,1 С3+ – 0,5 N2 – 0,2 CO2 – 0,2 |
СН4 – 97 С2Н6 – 2,0 С3+ – 0,2 N2 – 0,4 CO2 – 0,4 |
Давление в реакторе, МПа |
3,0 |
2,0 |
5,0 |
6,0 |
Температура на входе в реактор, °С |
450 |
360 |
280 |
450 |
Концентрация кислорода относительно метана на входе в реакционные зоны, % об. |
2 |
10 |
4 |
3,6 |
Полный выход жидких продуктов, кг/1000 м3 углеводородного газа. |
54 |
240 |
90 |
85 |
Выход формальдегида, кг/1000 м углеводородного газа. |
14 |
15 |
11 |
2,5 |
Выход спиртов, кг/1000 м углеводородного газа. |
27 |
36 |
26 |
18 |
Концентрация формальдегида в жидких продуктах, % |
26 |
6 |
12 |
3 |
Суммарная концентрация спиртов в жидких продуктах, % |
50 |
15 |
29 |
21 |
Формула изобретения
1. Способ производства формальдегида, включающий окисление углеводородсодержащего газа кислородсодержащим газом при повышенных температуре и давлении, последующее охлаждение реакционной смеси и отделение целевого жидкого продукта, отличающийся тем, что в качестве углеводородсодержащего газа используют этансодержащий газ, в том числе природный и попутные газы, с содержанием этана не менее 10%, при этом этансодержащий газ, предварительно сжатый до 2-5 МПа и нагретый до 280-450°С, и сжатый до давления не ниже давления этансодержащего газа кислородсодержащий газ раздельно подают в смесители последовательно расположенных реакционных зон реактора до содержания кислорода в реакционных зонах 2-10 об.%, а реакционную смесь непрерывно охлаждают через стенку либо непосредственно в процессе окисления, либо перед ее подачей в последующую реакционную зону до температуры не выше 450°С.
2. Способ по п.1, отличающийся тем, что в качестве кислородсодержащего газа используют воздух, кислород или обогащенный кислородом воздух.
РИСУНКИ
|
|