(21), (22) Заявка: 2004138773/02, 30.12.2004
(24) Дата начала отсчета срока действия патента:
30.12.2004
(46) Опубликовано: 27.07.2006
(56) Список документов, цитированных в отчете о поиске:
RU 2178010 С2, 10.01.2002. RU 2169210 C1, 20.06.2001. SU 505751 А, 11.08.1976. GB 2279664 А, 11.01.1995. US 5411646 А, 02.05.1995. JP 5230678 A, 07.09.1993. EP 0479337 A1, 08.04.1992.
Адрес для переписки:
301657, Тульская обл., г. Новомосковск, ул. Вахрушева, 34, кв.27, Б.А. Хоришко
|
(72) Автор(ы):
Хоришко Борис Алексеевич (RU), Марценко Константин Николаевич (RU), Давыдов Алексей Дмитриевич (RU), Земляков Юрий Дмитриевич (RU), Волкович Анатолий Васильевич (RU)
(73) Патентообладатель(и):
Новомосковский институт РХТУ им. Д.И. Менделеева (RU)
|
(54) СПОСОБ ПОЛУЧЕНИЯ ЛИТОГО МАГНЕТИТА
(57) Реферат:
Изобретение относится к области электрохимических производств, в частности к области изготовления анодов для процессов электролиза водных сред с рН 2-14, например, к промышленному электролизу, катодной защите от коррозии внешним током. Техническим результатом является получение литого или намороженного магнетита стехиометрического состава и однофазного по структуре, так как стабильность состава и структуры во времени исключает трещинообразование. Указанный технический результат достигается тем, что способ получения литого магнетита включает заливку расплава магнетита при температуре 1610°С в форму требуемой детали, помещенную в замкнутую емкость, в которую подается смесь CO+CO2 при давлении 1,5-16 атм. 1 ил., 4 табл.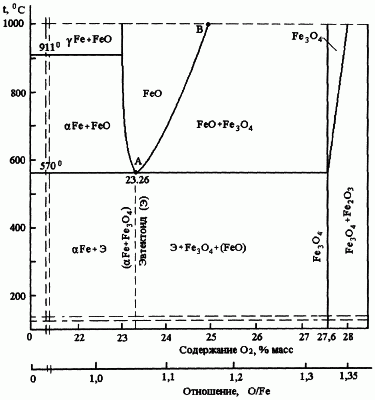
Изобретение относится к области изготовления магнетитовых анодов, применяемых для процессов электролиза водных сред с рН 2-14 и катодной защиты от коррозии.
Аналогами предлагаемого изобретения являются:
1. А.С. №505751 от 11.08.76. Анод для катодной защиты. Авторы: Трусов Г.Н., Коссый Г.Г., Михеев B.C., Гончаренко Б.А.
2. Пат. РФ №2169210 от 25.04.2000. Анод для катодной защиты от коррозии и способ формирования покрытия анода. Авторы: Зорин А.И., Зорин А.А. и др. По совокупности существенных признаков и назначению ближайшим аналогом является:
3. Пат. РФ №2178010 от 01.10.2002. Способ изготовления магнетитовых анодов для системы катодной защиты от коррозии изделий различного назначения. Авторы: Кузьмин Ю.Л., Лащевский В.О., Трощенко В.Н., Медяник Т.Е.
Во всех аналогах, приведенных в [1-3], схожи технические задачи – обеспечение высоких эксплуатационных параметров (коррозионная стойкость, электропроводность, компактность и т.д.), но принципиально разные способы подготовки сырья (шихты) и получения магнетитового сплава.
В способах-аналогах [1, 2] магнетит получают расплавлением гранульной шихты (частицы 5-8 мм), а по способу [3] шихту размалывают до порошка (частицы 1-5 мкм), смешивают со связующим раствором поливинилового спирта, прессуют и спекают.
Магнетитовый порошок прессуют в форме анода при давлении 100÷150 МПа (1-1,5 тнс/см2), после этого заготовки проходят дегазацию при 300°С в вакуумных шкафах при р=10-3÷10-2 мм рт.ст. Спекание осуществляют в вакуумной печи при 1300÷1350°С в течение 6÷10 ч.
Следует отметить, что порошкообразная шихта со спиртом в плавильном производстве недопустима (применяют гранулы, окатыши).
Способы, известные из [1, 2], не обеспечивают высокой электропроводности, достаточной прочности, твердости и целостности анодного материала, выплавляемого из рудного сырья, а по способу из [3] присущи высокая трудоемкость и энергоемкость.
Априорно следует отметить особенность оксидов железа, выявленную собственными исследованиями литых магнетитов и сравнительным анализом данных из многих литературных источников по металлоксидной тематике. Основные сведения по фазам, составляющих структуру магнетитовых отливок, приведены в табл.1.
Таблица 1 |
Фаза |
Температура кристаллизации, °С |
Плотность, г/см3 |
Твердость HV, кгс/мм2 |
Основная: |
|
|
|
магнетит, Fe3O4 |
1597 |
5.0÷5.3 |
560÷800 |
Локальные скопления: |
|
|
|
гематит, Fe2O3 |
1560 |
4.9÷5.3 |
500÷900 |
вюстит, FeO |
1370 |
5.7÷5.9 |
560±50 |
Включения: |
|
|
|
феррит, Fe |
1435 |
7.86 |
90÷120 |
Из табл.1 видно, что у магнетита и гематита при одинаковой плотности и близких температурах кристаллизации наблюдается существенно широкий интервал твердости при близких значениях его границ.
Близость температур плавления, плотности и максимальной твердости (HV=800÷900) фаз Fe3O4 и Fe2O3 подтверждается диаграммой Fe-O. Проекция ее низкотемпературной части на плоскость температура-состав представлена на чертеже. Видно, что поля фаз Fe3O4 и Fe2О3 расположены рядом, в узком интервале концентрации кислорода – 27.6÷29.6% масс.
Минимальная твердость магнетита совпадает с номинальной твердостью вюстита.
Если микротвердость литого анода при нагрузках на пирамиду: 20, 50, 100, 500 г показывает стабильно два максимума в интервалах: 500-560 и 800-900 HV (табл.1), то это указывает на двухфазное строение анодного материала. Это подтверждается проведенными металлографическим (по травимости шлифа) и физико-химическим фазовом анализами литых магнетитов.
Сочетание фаз Fe3O4 и Fe2О3 вполне закономерно, они устойчивы при комнатных температурах, что видно на диаграмме Fe-O (см. чертеж). Вюститная же фаза FeO неустойчива в интервале температур 570÷480°С, распадается на смесь, аналогично аустенитно-перлитному (эвтектоидному) превращению в сталях и чугунах при 727°С. Схема распада вюстита известна:

Реакция (1) не зависит от концентрации кислорода, если его меньше 27.6% [поле ( Fe+Fe3O4) слева от вертикали фазы Fe3O4 на диаграмме Fe-O (см. чертеж)].
В общем виде состояние структуры магнетитового анода изменяется по схеме:

где Fe3O4 – магнетит первичный, он выделился из жидкой фазы при 1597°С при концентрации кислорода 27.6% вес.;
(Fe3O4) – магнетит вторичный, образовался из колоний вюстита в интервале 570÷480 С наряду с ферритом Fe, по реакции (1);
(FeO) – остаточный вюстит.
При охлаждении магнетитовой отливки до 570°С резко уменьшается ( 2%) растворимость кислорода в FeO (см. чертеж, линия АВ). Поэтому участки FeO с большей концентрацией железа инициируют при 570°С образования Fe-фазы, а места, более насыщенные кислородом, трансформируются в магнетит вторичный (Fe3O4). Оба эти процесса сопровождаются значительными изменениями соответствующих объемов фаз Fe и Fe3O4, что показано в табл.2.
Таблица 2 |
Показатель |
Исходная фаза, FeO |
Фазы в эвтектоиде |
Fe |
Fe3O4 |
Удельный объем, см3 /г |
0.174 |
0.127 |
0.192 |
Количественное соотношение фаз (из диаграммы FeO по правилу отрезков), г |
1.0 |
0.16 |
0.84 |
Фазовый объем, см3 |
0.174 |
0.0203 |
0.1613 |
Объем эвтектоида, см3 |
– |
0.182 |
Изменение объема эвтектоида относительно FeO, V (%) |
– |
+0.008 (+4.6%) |
Из табл.2 видно, что распад FeO на эвтектоидную смесь Fe+Fe3O4 приводит к увеличению локального объема на 4,6%.
Локальные объемные увеличения при распаде вюстита при 570÷480°С наводят в жестком массиве первичного магнетита большие внутренние напряжения ( II), которые сходны с напряжениями в закаленной стали или белом чугуне (при С 2.14%) от мартенсита. Мартенсит увеличивает объем стали не более 1.2%, а эвтектоид ( Fe+Fe3O4) в оксиде – на 4.6% (табл.2). Следствием больших внутренних напряжений является трещинообразование.
Участки FeO, не распавшиеся по реакции (1) и окруженные эвтектоидом ( Fe+Fe3O4) в сжатом (как бы в спрессованном) состоянии сохраняются до комнатных температур. Аналогом такого остаточного вюстита в магнетите является остаточный аустенит в закаленной заэвтектоидной стали или белом чугуне.
Известно [4] (Разина Н.Ф. Окисные электроды в водных растворах. – Алма-Ата: Наука, 1982. – 160 с.), что с увеличением содержания вюстита в магнетите удельное электрическое сопротивление оксида железа повышается.
Таким образом, трещинообразование и электропроводность отливки предопределены количеством исходного вюстита в системе FeO+Fe3O4 при температурах выше 570°С (см. чертеж).
Соотношение первичных фаз FeO+Fe3O4 (фиг.) определяется в первую очередь составом шихты, что при плавке будет влиять на дефицит кислорода.
Так, в магнитном железняке [Fe3O4·FeO] (высший сорт промышленной руды) содержится не более 70% Fe, остальные 30% включают оксиды: Al, Cr, Co, Mn, Ni, Mg, Si, из [5]: Музафаров В.Г. Определитель минералов и горных пород. Изд.2-е. Пособие для институтов – М.: Учпедгиз, 1953, 176 с. В «суперконцентрате» (высшая марка агломеризации) содержится 99% железняка. Следовательно, при выплавке анода даже из такого концентрата (шихты) значительная часть кислорода уйдет из расплава в оксидах примесей (их 30%) в шлак. Это значит, что дефицит кислорода неизбежен для железооксидного расплава.
Влияние дефицита кислорода (%) на долю первичного магнетита в смеси FeO+Fe3O4 (см. чертеж), вычисленную по правилу отрезков, показано в табл.3.
Таблица 3 |
Температура, °С |
 |
 |
 |
 |
 |
 |
1000 |
0.83 |
0.60 |
0.43 |
0.22 |
0.03 |
800 |
0.86 |
0.68 |
0.54 |
0.38 |
0.22 |
600 |
0.89 |
0.75 |
0.63 |
0.50 |
0.39 |
570 |
0.90 |
0.76 |
0.65 |
0.52 |
0.42 |
Из табл.3 видно, что при температуре 570°С (начало распада FeO) и дефиците кислорода менее 1.5% масс. отливка является преимущественно магнетитовой (Fe3O4=0.65; FeO=0.35). При дефиците кислорода от 2% и более большая часть объема отливки становится вюститной (доля Fe3O4<0.5).
Закономерно, что нестабильное соотношение фаз Fe3O4/FeO, получаемое при плавке, и непостоянная скорость охлаждения, особенно в интервале 570÷480°С, что связано с массой отливки, будут определять результаты реакции распада FeO. Отсюда следует разброс твердости из-за остаточного вюстита (табл.1) и трещинообразования из-за большего объема эвтектоида (табл.2).
Доказательством такой изменчивости состояния литого магнетита могут служить следующие факты.
В апреле 1982 г. из гранул 5-8 мм искусственного магнетита (катализатора для синтеза аммиака), полученного сжиганием Армко-железа в струе чистого кислорода, были изготовлены микрошлифы. Гранулы отжигались при 600°С, 1 час, залиты были эпоксидом в кольцевую оправку. Шлифовка и полировка исключала образование трещин. Прошло 23 года (примерно 2·105 ч), трещин до сих пор нет.
В октябре 1987 г. были отлиты пробы-бруски диаметром 15 мм длиной 120 мм из расплава 90% магнетитового концентрата, плавленого в 25 кг индукционной печи. Из этой плавки получали и намороженный магнетит. Затравки из Ст3 – прутки диаметром 6 мм и пластины 60×30×2 мм окунали в расплав 5-6 раз до получения слоя магнетита 6-7 мм. Половина образцов от каждой партии (цельных и намороженных) отжигали при 850°С в течение 2 ч.
При вылеживании при t=18÷24°С на открытом воздухе (на подоконнике) первыми через 2-4 дня начали растрескиваться плоские намороженные образцы, отожженные и неотожженные. Спустя год-два появились трещины на цилиндрических образцах. Подложки-затравки все оказались изъедены окалиной.
Из сколов цельных и намороженных магнетитов, отлитых в 1982 г., были изготовлены микрошлифы размерами 20×15×7 мм. в кольцевых оправках с эпоксидом. Изготовлены шлифы в октябре 1987 г. (макро- и микротрещин не было).
При травлении 5% раствором HCl в этиловом спирте четко видна двухфазная структура. Наиболее сильно вытравливаются вюститная фаза и эвтектоид.
Трещины в микрошлифах наплавок начали возникать спустя 2 года (примерно). В настоящее время, т.е. через 18 лет (от отжига) = 1,6·105 ч. Все три образца растрескались. Трещины видны невооруженным глазом: 11 шт. на общей длине шлифов 45 мм с интервалами 3-5 мм.
Примечательно, что трещины преимущественно поперечны намороженным слоям магнетита, а расслоений в нем нет.
Маловероятно, чтобы внешние факторы – напряжения от деформации стареющего эпоксида, окружающего образец, ручная полировка на фетре с химическим травлением (обновление шлифа для просмотра под микроскопом), и хранение на воздухе (в неплотно закрытой банке) – могли вызвать напряжения, разрушающие образцы с достаточно высокой твердостью 600-800 HV.
Вывод однозначный: растрескивание могут вызывать только внутренние напряжения.
Приведенные факты и недостатки отливок, производимых из природного магнетита (рудного концентрата) по способам [1, 2], обусловлены непостоянством количественного соотношения фаз Fe3O4 и FeO до 570°С и нестабильным остаточным вюститом (FeO) ниже 570°С, у которых одна первопричина – дефицит кислорода относительно стехиометрического состава Fe3O4, возникающий в процессе плавки.
При избыточном содержании кислорода в оксиде относительно стехиометрического состава Fe3O4 основным негативным явлением будет резкий рост удельного электрического сопротивления с увеличением количества сверхстехиометрического кислорода [4].
Задачей предлагаемого изобретения являлось получение литого однофазного оксида, близкого по составу к стехиометрическому магнетиту (Fe3O4).
Поставленная задача решается тем, что способ включает плавку исходного материала и заливку в формы (например, анодов), помещенные в автоклаве, автоклав закрывают и подают смесь газов СО+CO2 при давлении от 1,5 до 16 атм.
Стабильность состава и структуры магнетита достигается тем, что в автоклаве при температуре 1610°С в расплав входит кислород, который образуется при диссоциации СО2.
Сравнительные испытания магнетитов включали определение свойств, которые достоверно прогнозируют качество отливки. Измеряли электросопротивление методом двойного моста (R-329) и объемные изменения – по удлинению образца на кварцевом дилатометре (ДКВР). Методы эти описаны в [6]: Лившиц Б.Г., Карпошин B.C., Липецкий Я.Л. Физические свойства металлов и сплавов. Изд.2-е. / Под ред. Б.Г.Лившица. – М.: Металлургия, 1980. – 320 с.
Материал оксидных отливок подвергали количественному химическому анализу на содержание кислорода и железа [7, 8]: Технические условия на катализатор синтеза аммиака гранулированный марки НИАП-08-01 (ТУ 113-03-00209510-88-99); Технические условия на катализаторы диссоциация аммиака для получения защитных атмосфер и восстановительных сред КДА-1А (ТУ 113-03-00209510-88-2001). Исходя из количественного состава оксида, оценивали отклонение от стехиометрии.
Образцы размером 12 мм, длиной 100±5 мм с шлифованными и строго параллельными торцами были изготовлены из литых заготовок, полученных по трем режимам литья (партиям): по способам аналогов [1, 2] и по предлагаемому способу в автоклаве при 1, 5 и 16 атм. В каждой партии было по 7 образцов.
Дилатометрирование проводили прямым измерением абсолютного удлинения при помощи индикатора часового типа (ИЧ) с ценой деления 0.01 мм. Скорость нагревания и охлаждения образца выдерживались в пределах 3÷4°С/мин.
Результаты измерений приведены в табл.4, которые свидетельствуют о положительном эффекте предлагаемого способа.
Таблица 4 |
Способ получения |
Давление газовой атмосферы, атм |
Плавка |
Отклонение стехиометрии, ± оксида Fe3± O4 |
, Ом·см |
Изменение длины образца |
Примечание |
, мм |
% |
По аналогу [1, 2] (атмосфера воздуха) |
1 |
1 |
+0.023 |
0.35 |
+1.51 |
+1.5 |
30% образцов имели трещины |
2 |
2 |
-0.078 |
1.52 |
– |
– |
10% образцов имели трещины |
Предлагаемый способ (атмосфера СО+CO2) |
1 |
3 |
-0.001 |
0.009 |
+0.48 |
+0.5 |
трещин нет |
16 |
3 |
-0.007 |
0.046 |
+0.72 |
+0.7 |
трещин нет |
Формула изобретения
Способ получения литого магнетита, включающий плавку исходного материала и заливку расплавленного материала в форму, отличающийся тем, что для получения стабильного стехиометрического состава магнетита форму с расплавленным материалом помещают в автоклав и обрабатывают при температуре 1610°С в смеси газов СО+СО2 при давлении 1,5-16 атм.
РИСУНКИ
|