(21), (22) Заявка: 2005116120/02, 27.05.2005
(24) Дата начала отсчета срока действия патента:
27.05.2005
(46) Опубликовано: 20.07.2006
(56) Список документов, цитированных в отчете о поиске:
RU 2165348 C1, 20.04.2001. SU 612754 A2, 30.06.1978. DE 3144468 A1, 01.07.1982. DE 3228014 A1, 10.03.1983.
Адрес для переписки:
129090, Москва, ул. Гиляровского, 5, ООО “Инсмат технология”, Ген.директору г-ну А.И.Звирину, для г-на В.А.Иванова
|
(72) Автор(ы):
Вязалов Сергей Юрьевич (RU), Трачук Аркадий Владимирович (RU), Чеглаков Андрей Валерьевич (RU), Курочкин Александр Васильевич (RU), Павлов Владимир Васильевич (RU), Писарев Александр Георгиевич (RU), Метельский Евгений Михайлович (RU), Солдатченков Виктор Сергеевич (RU), Чекмарев Виктор Афанасьевич (RU), Климов Алексей Иванович (RU), Мочалов Александр Игоревич (RU), Ашкиназий Яков Михайлович (RU), Чеглаков Валерий Анатольевич (RU), Журавлев Андрей Владимирович (RU)
(73) Патентообладатель(и):
Научно-исследовательский институт Гознака (RU)
|
(54) СПОСОБ ПОЗИЦИОНИРОВАНИЯ ИНСТРУМЕНТА В КООРДИНАТНОЙ СИСТЕМЕ ОТСЧЕТА СТАНКА АВТОМАТИЗИРОВАННОГО ГРАВИРОВАЛЬНОГО КОМПЛЕКСА
(57) Реферат:
Изобретение относится к машиностроению и может быть использовано при обработке изделий со сложным рельефом формируемого на поверхности функционального слоя заготовки рисунка гравюры на станках с системой ЧПУ. Технический результат – повышение точности обработки. Перед формированием реперной координатной системы X1Y1Z1 осуществляют коррекцию управляющих программ системы ЧПУ на отклонение от плоскостности рабочей поверхности функционального слоя заготовки, которую предварительно закрепляют на установочной поверхности устройства для пространственной ориентации и пространственно ориентируют вдоль плоскости XY. Для этого производят оцифровку по координатам “z” множества расположенных с заданным шагом точек этой поверхности на участке оцифровки, форма и площадь которого регламентируется формой и площадью формируемого на этой поверхности рисунка гравюры. Оцифровку начинают с наиболее удаленной от центра участка оцифровки точки и продолжают посредством сканирования участка оцифровки средствами измерения с обеспечением регистрации значений координаты “z” в каждой точке оцифровки и автоматической коррекции управляющих программ ЧПУ по результатам оцифровки. Реперную координатную систему X1Y1Z1 формируют от начальной точки оцифровки, функционально являющейся нулевой точкой этой системы, координаты которой перед началом обработки уточняют посредством обеспечения механического контакта вершины закрепленного в шпинделе инструмента с рабочей поверхностью функционального слоя заготовки в этой точке. При этом позиционирование и отсчет перемещений инструмента в процессе формирования фрагментов объемного рисунка гравюры в функциональном слое заготовки ведут от упомянутой нулевой точки реперной системы X1Y1Z1 согласно управляющим программам системы ЧПУ с учетом их дополнительной коррекции по результатам оцифровки. 2 з.п. ф-лы, 4 ил.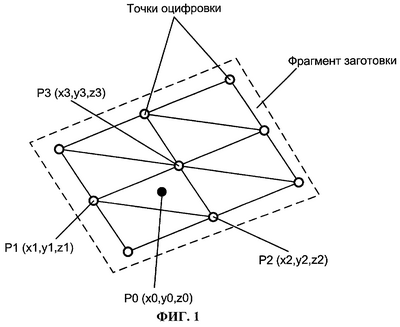
Изобретение относится к области машиностроения и может быть, преимущественно, использовано при автоматизированной механической обработке изделий со сложным пространственным профилем фрагментов рисунка законченной гравюры, формируемой посредством обработки строганием (строгальным резцом) на рабочей поверхности функционального слоя заготовки (например, металлографских модельных форм) на прецизионных металлорежущих (строгальных) станках с системой числового программного управления (ЧПУ).
Из уровня техники известны способы позиционирования инструмента (т.е. его вершины и режущей кромки) в координатной системе отсчета металлорежущего станка, заключающиеся в том, что датчик регистрации касания (перемещения которого отслеживаются отсчетной системой станка) подводят к режущей кромке инструмента (как правило – к его вершине) и фиксируют момент касания датчика с инструментом, при этом фиксируемое пространственное положение вершины инструмента функционально является нулевой точкой (точкой отсчета) в координатной системе отсчета станка (Ю.И.Кузнецов и др. “Оснастка для станков с ЧПУ”, справочник, М.: Машиностроение, 1990 г., с.477-487).
Из уровня техники известен также способ позиционирования инструмента в координатной системе отсчета станка с ЧПУ, заключающийся в том, что инструмент перемещают в соответствующую исходную позицию, где с помощью оптической системы индексации положения регистрируют достижение его вершиной заданной точки отсчета путем совмещения упомянутой вершины с реперной точкой реперной системы станка (автономно формируемой в пространстве оптической системой индексации положения) и вывода изображения процесса совмещения на экран посредством объективов. После завершения вышеописанного процесса совмещения координатную система отсчета станка обнуляют (адаптируют к координатной системе отсчета станка) по соответствующей (в данном случае – одной) координате и отсчет дальнейших перемещений инструмента ведут от упомянутой реперной точки, функционально адаптируемой с нулевой точкой отсчета упомянутой координатной системы отсчета станка (SU, 612754, кл. В 23 Q 15/22, 1978 г.).
К недостаткам рассмотренных выше способов позиционирования вершины инструмента в координатной системе отсчета станка следует отнести их ограниченные функциональные возможности, ввиду того, что данные известные из уровня техники способы (вследствие использования их лишь для определенных видов обработки, в частности – для прецизионной расточки отверстий) способны обеспечить необходимую точность позиционирования вершины режущей кромки инструмента в координатной системе отсчета станка лишь по одной координате. То есть рассматриваемые способы не приемлемы в тех случаях, когда для обеспечения заданной точности обработки необходимо обеспечить коррекцию положения вершины инструмента в координатной системе отсчета станка по трем координатам. Например, при обработке на прецизионных строгальных станках металлографских форм со сложным пространственным профилем микрорельефа (формируемого в функциональном слое заготовки) в ортогональной трехкоординатной системе отсчета.
Отсутствие же в рассматриваемом известном способе позиционирования такой возможности (т.е. возможности коррекции пространственного положения вершины инструмента по трем координатам ортогональной системы координат) ведет к значительному снижению точности обработки, ввиду изменения геометрии формируемого профиля (особенно в случае нарезания, например, криволинейных профильных канавок на поверхности изделия), поскольку изменяется пространственная ориентация вершины и, соответственно, режущей кромки инструмента относительно исходной (нулевой) точки отсчета координатной системы станка.
Наиболее близким по технической сущности к заявленному объекту изобретения является способ позиционирования инструмента в координатной системе отсчета станка автоматизированного гравировального комплекса, заключающийся в следующем. Формируют ортогональную реперную координатную систему X1Y1Z1. Осуществляют пространственную координатную привязку ее нулевой точки к нулевой точке ортогональной координатной системы XYZ отсчета станка, пространственно адаптированной с исходными управляющими программами системы числового програмного управления (ЧПУ), посредством которых формируют фрагменты объемного рисунка гравюры в функциональном слое заготовки, которую закрепляют и позиционируют на установочной поверхности устройства для пространственной ориентации относительно плоскости XY координатной системы XYZ. А также осуществляют операции фотографирования передней поверхности режущей части инструмента, позицирования его вершины по трем координатам относительно нулевой точки сформированной реперной системы X1Y1Z1 и коррекции по координатам «x1» и «y1» проходящей через эту вершину продольной оси инструмента относительно параллельной оси Z или Z1 действительной оси вращения шпинделя станка с обеспечением визуального отображения результатов упомянутых операций фотографирования, позиционирования и коррекции на экране монитора управляющего механизмами перемещения станка компьютера и координатной адаптации этих результатов с управляющими программами системы ЧПУ посредством оптико-электронной измерительной системы. Данная система включает телевизионный компьютерный микроскоп, который стационарно закрепляют на основном столе станка таким образом, что главная оптическая ось его объектива ориентирована по направлению возвратно-поступательного перемещения основного стола станка вдоль осей Х или X1 соответствующих координатных систем и координатно адаптирована с нулевой точкой координатной системы X1Y1Z1. Для этого режущую часть инструмента вводят в поле зрения объектива упомянутого микроскопа. Его вершину совмещают с перекрестием ортогональных осей на экране монитора, которое расположено на главной оптической оси упомянутого объектива, и осуществляют поворот шпинделя шпиндельной бабки станка на угол в пределах 360°. А позиционирование и отсчет перемещений инструмента в процессе формирования фрагментов объемного рисунка гравюры в функциональном слое заготовки ведут от упомянутой нулевой точки реперной системы X1Y1Z1 согласно управляющим программам системы ЧПУ с учетом коррекции по координатам «x1» и «y1» упомянутой продольной оси инструмента относительно действительной оси вращения шпинделя станка (RU патент №2165348).
К недостаткам данного известного из уровня техники способа следует отнести недостаточную точность позиционирования для целей повышения качества и точности обработки изделий со сложным пространственным профилем микрорельефа рисунка формируемой (в функциональном слое заготовки) гравюры. Объясняется это, во-первых, тем, что в данном известном способе не предусматривается осуществление коррекции управляющих программ системы ЧПУ на отклонение от плоскостности рабочей поверхности функционального слоя заготовки по результатам оцифровки по координатам «z» множества, расположенных с заданным шагом, точек этой поверхности на участке оцифровки (форма и площадь которого регламентируется формой и площадью формируемого на этой поверхности рисунка гравюры). А, во-вторых, тем, что реперная координатная система (в частности, ее нулевая точка) формируется в отрыве от рабочей поверхности функционального слоя заготовки.
В результате этого позиционирование и отсчет перемещений инструмента в процессе формирования фрагментов объемного рисунка гравюры в функциональном слое заготовки ведут от сформированной нулевой точки реперной системы X1Y1Z1 согласно управляющим программам системы ЧПУ без учета их дополнительной коррекции по результатам оцифровки.
При этом следует учесть, что точность обработки является наиболее важным критерием качества, например, для металлографских модельных форм, используемых, например, в процессе изготовления денежных знаков и иных ценных бумаг, поскольку за счет этого параметра обработки, как правило, обеспечиваются дополнительные степени защиты от подделки упомянутых ценных изделий.
В основу заявленного способа позиционирования инструмента в координатной системе отсчета станка автоматизированного гравировального комплекса была положена задача обеспечения (с помощью известных из уровня техники средств) упрощения технологии прецизионного позиционирования вершины и, соответственно, режущей части инструмента в трехкоординатной системе отсчета при повышении точности позиционирования для целей повышения качества и точности обработки изделий со сложным пространственным профилем микрорельефа рисунка формируемой (в функциональном слое заготовки) гравюры.
Поставленная задача достигается за счет того, что в способе позиционирования инструмента в координатной системе отсчета станка автоматизированного гравировального комплекса, заключающемся в том, что формируют ортогональную реперную координатную систему X1Y1Z1; осуществляют пространственную координатную привязку ее нулевой точки к нулевой точке ортогональной координатной системы XYZ отсчета станка, пространственно адаптированной с исходными управляющими программами системы числового програмного управления (ЧПУ), посредством которых формируют фрагменты объемного рисунка гравюры в функциональном слое заготовки, которую закрепляют и позиционируют на установочной поверхности устройства для пространственной ориентации относительно плоскости XY координатной системы XYZ; а также осуществляют операции фотографирования передней поверхности режущей части инструмента, позицирования его вершины по трем координатам относительно нулевой точки сформированной реперной системы X1Y1Z1 и коррекции по координатам «x1» и «у1» проходящей через эту вершину продольной оси инструмента относительно параллельной оси Z или Z1 действительной оси вращения шпинделя станка с обеспечением визуального отображения результатов упомянутых операций фотографирования, позиционирования и коррекции на экране монитора управляющего механизмами перемещения станка компьютера и координатной адаптации этих результатов с управляющими программами системы ЧПУ посредством оптико-электронной измерительной системы, включающей телевизионный компьютерный микроскоп, который стационарно закрепляют на основном столе станка таким образом, что главная оптическая ось его объектива ориентирована по направлению возвратно-поступательного перемещения основного стола станка вдоль осей Х или X1 соответствующих координатных систем и координатно адаптирована с нулевой точкой координатной системы X1Y1Z1; для этого переднюю поверхность режущей части инструмента вводят в поле зрения объектива упомянутого микроскопа, его вершину совмещают с перекрестием ортогональных осей на экране монитора, которое расположено на главной оптической оси упомянутого объектива, и осуществляют поворот шпинделя шпиндельной бабки станка на угол в пределах 360°; при этом позиционирование и отсчет перемещений инструмента в процессе формирования фрагментов объемного рисунка гравюры в функциональном слое заготовки ведут от упомянутой нулевой точки реперной системы X1Y1Z1 согласно исходным управляющим программам системы ЧПУ с учетом коррекции по координатам «x1» и «у1» упомянутой продольной оси инструмента относительно действительной оси вращения шпинделя станка, согласно изобретению перед формированием реперной координатной системы X1Y1Z1 осуществляют коррекцию управляющих программ системы ЧПУ на отклонение от плоскостности рабочей поверхности функционального слоя заготовки, которую предварительно закрепляют на установочной поверхности устройства для пространственной ориентации и пространственно ориентируют вдоль плоскости XY; для чего производят оцифровку по координатам «z» множества расположенных с заданным шагом точек этой поверхности на участке оцифровки, форма и площадь которого регламентируется формой и площадью формируемого на этой поверхности рисунка гравюры; оцифровку начинают с наиболее удаленной от центра участка оцифровки точки и продолжают посредством сканирования участка оцифровки средствами измерения с обеспечением регистрации значений координаты «z» в каждой точке оцифровки и автоматической коррекции управляющих программ ЧПУ по результатам оцифровки; реперную координатную систему X1Y1Z1 формируют от начальной точки оцифровки, функционально являющейся нулевой точкой этой системы, координаты которой перед началом обработки уточняют посредством обеспечения механического контакта вершины закрепленного в шпинделе инструмента с рабочей поверхностью функционального слоя заготовки в этой точке; при этом позиционирование и отсчет перемещений инструмента в процессе формирования фрагментов объемного рисунка гравюры в функциональном слое заготовки ведут от упомянутой нулевой точки реперной системы X1Y1Z1 согласно управляющим программам системы ЧПУ с учетом их дополнительной коррекции по результатам оцифровки.
Оптимально упомянутые операции фотографирования передней поверхности режущей части инструмента, позицирования его вершины по трем координатам относительно нулевой точки сформированной реперной системы X1Y1Z1 и коррекции по координатам «x1» и «у1» проходящей через эту вершину продольной оси инструмента относительно параллельной оси Z или Z1 действительной оси вращения шпинделя станка посредством оптико-электронной измерительной системы осуществляют в прямом и теневом свете, для чего упомянутую измерительную систему оснащают экраном, расположенным в поле зрения объектива телевизионного компьютерного микроскопа позади зоны ввода инструмента в это поле, а также двумя осветителями, один из которых устанавливают с возможностью осуществления подсветки экрана, а другой – передней поверхности режущей части инструмента.
Целесообразно предварительное позиционирование закрепленной заготовки посредством устройства для пространственной ориентации перед оцифровкой осуществлять посредством определения и регистрации соответствующими средствами измерения значений координат «z», по меньшей мере, трех, не лежащих на одной прямой, точек рабочей поверхности функционального слоя заготовки и последующего выравнивания в диапазоне допустимых отклонений величин этих значений посредством регулировочных узлов устройства для пространственной ориентации заготовок.
Совершенно очевидно, что каждая операция патентуемого способа в отдельности и средства для реализации соответствующих операций рассматриваемого способа широко известны из уровня техники. Однако поставленная задача может быть решена исключительно за счет отраженной в формуле изобретения совокупности известных операций (технически реализованных известными средствами), выполняемых в строго определенной последовательности.
Следовательно, отраженная в формуле изобретения совокупность известных из уровня техники признаков обеспечивает в патентуемом объекте изобретения синергетический результат за счет определенной взаимосвязи этих признаков.
Проведенный заявителем анализ уровня техники, включающий поиск по патентным и научно-техническим источникам информации и выявление источников, содержащих сведения об аналогах заявленного изобретения, позволил установить, что заявителем не обнаружен аналог, характеризующийся признаками и связями между ними, идентичными всем существенным признакам заявленного изобретения, а выбранный из перечня выявленных аналогов прототип, как наиболее близкий по совокупности признаков аналог, позволил выявить совокупность существенных, по отношению к усматриваемому заявителем техническому результату, отличительных признаков в заявленном объекте, изложенных в формуле изобретения.
Следовательно, заявленное изобретение соответствует критерию патентоспособности НОВИЗНА по действующему законодательству.
Для проверки соответствия заявленного изобретения требованию критерия патентоспособности ИЗОБРЕТАТЕЛЬСКИЙ УРОВЕНЬ был проведен дополнительный поиск известных технических решений, с целью выявления признаков, совпадающих с отличительными от прототипа признаками заявленного изобретения, результаты которого показывают, что заявленное изобретение не следует для специалиста явным образом из известного уровня техники, поскольку из уровня техники, определенного заявителем, не выявлено влияние предусматриваемых существенными признаками заявленного изобретения преобразований на достижение усматриваемого заявителем технического результата.
В частности, заявленным изобретением не предусматриваются следующие преобразования известного объекта-прототипа:
– дополнение известного объекта каким-либо известным признаком, присоединяемым к нему по известным правилам, для достижения технического результата, в отношении которого установлено влияние именно таких дополнений;
– замена какого-либо признака известного объекта другим известным признаком для достижения технического результата, в отношении которого установлено влияние именно такой замены;
– исключение какого-либо признака известного объекта с одновременным исключением обусловленной наличием этого признака функции и достижением при этом обычного для такого исключения результата;
– увеличение количества однотипных признаков в известном объекте для усиления технического результата, обусловленного наличием в объекте именно таких признаков;
– выполнение известного объекта или его части из известного материала для достижения технического результата, обусловленного известными свойствами материала;
– создание объекта, включающего известные признаки, выбор которых и связь между ними осуществлены на основании известных правил и достигаемый при этом технический результат обусловлен только известными свойствами признаков этого объекта и связей между ними.
Следовательно, заявленное изобретение соответствует требованию критерия патентоспособности ИЗОБРЕТАТЕЛЬСКИЙ УРОВЕНЬ по действующему законодательству.
Таким образом, вышеизложенные сведения свидетельствуют о выполнении при использовании заявленного изобретения следующей совокупности условий:
– объект, воплощающий заявленное изобретение при его осуществлении, предназначен для использования в промышленности, а именно в области обработки изделий резанием на прецизионных металлорежущих станках (например – строгальных);
– для заявленного объекта изобретения в том виде, как оно охарактеризовано в независимом пункте нижеизложенной формулы изобретения, подтверждена возможность его осуществления с помощью вышеописанных в заявке или известных из уровня техники на дату приоритета средств и методов;
– объект, воплощающий заявленное изобретение при его осуществлении, способен обеспечить достижение усматриваемого заявителем технического результата.
Следовательно, заявленное изобретение соответствует требованию критерия патентоспособности ПРОМЫШЛЕННАЯ ПРИМЕНИМОСТЬ по действующему законодательству.
Изобретение иллюстрируется графическими материалами.
Фиг.1 – схема оцифровки фрагмента рисунка гравюры.
Фиг.2 – алгоритм оцифровки участка рабочей поверхности заготовки контактными средствами измерения (т.е. контактным методом) посредством индуктивного датчика.
Фиг.3 – оптико-электронная измерительная система.
Фиг.4 – условная схема коррекции по координатам «x1» и «у1» продольной оси инструмента (проходящей через его вершину) относительно действительной оси вращения шпинделя станка (параллельной оси Z или Z1).
Техническая сущность патентуемого способа позиционирования инструмента в координатной системе отсчета станка (преимущественно, для обработки изделий строганием) автоматизированного гравировального комплекса заключается в следующем.
Перед формированием реперной координатной системы X1Y1Z1 осуществляют коррекцию исходных управляющих программ системы ЧПУ (например, типа CNC модели Sinumerik 840Di) на отклонение от плоскостности рабочей поверхности функционального слоя заготовки. При этом заготовку предварительно закрепляют на установочной поверхности устройства для пространственной ориентации и ориентируют вдоль плоскости XY ортогональной координатной системы XYZ отсчета станка.
Для осуществления упомянутой коррекции исходных управляющих программ производят оцифровку по координатам «z» множества (расположенных с заданным шагом) точек рабочей поверхности функционального слоя заготовки на участке оцифровки, форма и площадь которого регламентируется формой и площадью формируемого на этой поверхности рисунка гравюры. Оцифровку начинают с наиболее удаленной от центра участка оцифровки точки и продолжают посредством сканирования участка оцифровки средствами измерения с обеспечением регистрации значений координаты «z» в каждой точке оцифровки (точность оцифровки в плоскости поверхности функционального слоя заготовки обеспечивается в пределах порядка 20…30 мкм) и автоматической коррекции управляющих программ ЧПУ по результатам оцифровки.
Оцифровка рабочей поверхности функционального слоя заготовки является технологической операцией, необходимой для корректного формирования рисунка гравюры на этой поверхности. Как правило, поверхность заготовки имеет плавное изменение геометрии (в частности, высоты неровностей относительно плоскости XY координатной системы отсчета станка). Чтобы учесть это изменение производится вышеупомянутая оцифровка заготовки. Для этого могут применяться различные известные из уровня техники средства измерения, которые делятся на контактные и бесконтактные. Например, индуктивный датчик, используемый в рассматриваемом автоматизированном гравировальном комплексе, является контактным. К бесконтактным средствам измерения относятся, например, интерферометры и лазерные измерители. Последние имеют важное преимущество перед контактными, поскольку нет необходимости подъема/опускания датчика над поверхностью заготовки, для того чтобы не повредить ее зеркальную рабочую поверхность в процессе сканирования. Однако стоимость лазерного измерителя значительно выше стоимости контактного датчика.
Другим недостатком контактного измерителя является наличие в нем инерционного элемента (т.е. пружины), что требует соответствующего учета (в частности – определения временного интервала выдержки для погашения колебательных процессов) при регистрации измеряемого значения.
Оцифровка заготовки осуществляется с помощью установленного в гнездо держателя инструмента (т.е. шпинделя шпиндельной бабки станка) индуктивного датчика, подключенного к индуктивному преобразователю. Индуктивный преобразователь имеет аналоговый выход, на котором формируется выходной сигнал в виде уровня напряжения. Выходной сигнал подается на один из входов платы аналогово-цифрового преобразования (АЦП), установленной в персональной электронно-вычислительной машине (ПЭВМ) системы ЧПУ.
Для избежания помех, в том числе, вырабатываемых импульсным источником питания индуктивного преобразователя, подключение производится по дифференциальной схеме.
На входе платы АЦП максимальному значению (верхняя граница диапазона) соответствует напряжение +5 В, а минимальному (нижняя граница диапазона) -5 В. Разрядность АЦП составляет 12 бит. Таким образом, при максимальном входном диапазоне ±5 В, дискретность составит 0.0025 В, следовательно, при максимальном диапазоне измерений индуктивного преобразователя ±100 мкм дискретность измерений составит 0.05 мкм (что на два порядка превышает точность позиционирования по координате Z, обеспечиваемая непосредственно станком).
Таким образом, для организации процесса оцифровки необходимо:
– определить габариты формируемого на рабочей поверхности функционального слоя заготовки рисунка гравюры;
– назначить величину шага между соседними точками оцифровки;
– сформировать набор кадров (команд) для их отработки на станке;
– определить время выдержки, необходимое для погашения колебательных воздействий пружины индуктивного датчика на результат измерения;
– организовать последовательный обход каждой из точек оцифровки (т.е. сканирование участка оцифровки).
Шаг между соседними точками оцифровки выбирается исходя из плотности элементов рисунка гравюры и качества рабочей поверхности функционального слоя используемой заготовки.
Формирование набора кадров (команд) подразумевает создание последовательности команд для организации процесса оцифровки. Так как применяется контактное средство измерения (т.е. индуктивный датчик), то существует необходимость для поднятия индуктивного датчика над рабочей поверхностью функционального слоя заготовки при его перемещении (в процессе сканирования) к следующей точке оцифровки.
Алгоритм оцифровки рабочей поверхности функционального слоя заготовки можно представить в виде, как показано на фиг.2, графических материалов.
Схема оцифровки фрагмента участка оцифровки рабочей поверхности функционального слоя заготовки представлена на фиг.1 графических материалов (изображен фрагмент заготовки с нанесенной на него сеткой оцифровки).
Коррекция управляющих программ системы ЧПУ на отклонение от плоскостности рабочей поверхности функционального слоя заготовки (коррекция по координате Z) учитывает неровности рабочей поверхности функционального слоя заготовки (на которой производится формирование рисунка гравюры). По результатам оцифровки вносятся соответствующие изменения в исходную управляющую программу по координате Z.
Для расчета действительной координаты (z0) произвольной токи (Р0) (расположенной на участке оцифровки) между точками оцифровки формируются треугольные плоскости, позволяющие определить необходимое приращение (dz) по координате Z.
Согласно фиг.1 графических материалов:
– точка Р0 – это точка, для которой производится коррекция управляющей программы по координате Z;
– набор точек P1, P2 и Р3 определяют ближайшую плоскость, охватывающую точку Р0, для которой производится коррекция.
Для определения приращения (dz) по координате Z составляется система уравнений:
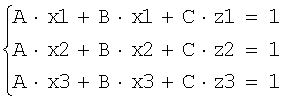
Решив систему уравнений, величину приращения (dz) по координате Z можно рассчитать по формуле:
dz=А·х0+В·y0+С,
таким образом, новое значение (z ) по координате Z в точке (х0, y0) будет равно:
z =z0+dz.
После осуществления операции оцифровки и соответствующей коррекции исходных управляющих программ системы ЧПУ формируют ортогональную реперную координатную систему X1Y1Z1.
Реперную координатную систему X1Y1Z1 формируют от начальной точки (x1=0, у1=0, z1=0) оцифровки (функционально являющейся нулевой точкой этой системы), координаты которой (перед началом обработки) уточняют посредством обеспечения механического контакта вершины инструмента (закрепленного в шпинделе станка) с рабочей поверхностью функционального слоя заготовки в этой точке с последующей адаптацией реперной координатной системы X1Y1Z1 с нулевой точкой отсчета исходных управляющих программ.
Упомянутую адаптацию осуществляют через пространственную координатную привязку нулевой точки координатной системы X1Y1Z1 к нулевой точке ортогональной координатной системы XYZ отсчета станка, пространственно адаптированной с нулевой точкой отсчета исходных управляющих программ системы числового програмного управления (ЧПУ).
Исходные управляющие программы предназначены для формирования фрагментов объемного рисунка гравюры в функциональном слое заготовки, которую (как ранее указывалось) предварительно закрепляют и позиционируют на установочной поверхности устройства для пространственной ориентации относительно плоскости XY координатной системы XYZ. Исходные управляющие программы для формирования рисунка гравюры на рабочей поверхности функционального слоя изделия составляется (базируется) от некоторой исходной точки формируемого рисунка гравюры, координаты которой программно адаптированы с вышеупомянутой нулевой точкой отсчета реперной координатной системы X1Y1Z1.
После завершения формирования и соответствующей привязки реперной координатной системы X1Y1Z1 к нулевой точке отсчета управляющих программ осуществляют позиционирование непосредственно режущей части инструмента (в частности, его вершины) относительно нулевой точки отсчета управляющих программ, координатно адаптированной с координатной системой XYZ станка (т.е. с нулевой точкой этой системы).
Для этого осуществляют операции фотографирования передней поверхности режущей части инструмента, позицирования его вершины по трем координатам относительно нулевой точки сформированной реперной системы X1Y1Z1 и коррекции по координатам «x1» и «у1» проходящей через эту вершину продольной оси инструмента относительно параллельной оси Z или Z1 действительной оси вращения шпинделя станка. При этом обеспечивают визуальное отображение результатов упомянутых операций фотографирования, позиционирования и коррекции на экране монитора управляющего механизмами перемещения станка компьютера, а также координатную адаптации этих результатов с управляющими программами системы ЧПУ.
Для реализации этих процессов используют оптико-электронную измерительную систему. Данная система включает телевизионный компьютерный микроскоп 1, который стационарно закрепляют на основном столе станка таким образом, что главная оптическая ось его объектива 2 ориентирована по направления возвратно-поступательного перемещения основного стола станка вдоль осей Х (или X1) соответствующих координатных систем и координатно адаптирована с нулевой точкой координатной системы X1Y1Z1.
Таким образом, переднюю поверхность режущей части инструмента (резца 3) вводят в поле зрения объектива 2 упомянутого микроскопа 1, его вершину совмещают с перекрестием ортогональных осей на экране монитора, которое расположено на главной оптической оси упомянутого объектива 2, и осуществляют поворот шпинделя шпиндельной бабки станка на угол в пределах 360°.
Резец 3 вводится в область поля зрения объектива 2 телевизионного микроскопа 1 в ручном режиме после его заточки и установки в рабочий шпиндель станка. Поворот шпинделя вокруг его оси, по меньшей мере, на угол в 360° осуществляется для выявления величины радиального смещения в плоскости XY (или X1Y1) вершины резца 3 (или продольной оси, проходящей через эту вершину, что равнозначно) относительно реальной оси вращения шпинделя. Поправка на величину выявленного смещения вводится в исходную программу ПЭВМ системы ЧПУ с соответствующей коррекцией этой программы в отношении данного конкретного инструмента (резца 3).
Иными словами, в ручном режиме вершина резца 3 корректируется по центру оптических осей объектива телевизионного микроскопа 1 (визуально отображенных на экране монитора ПЭВМ в увеличенном масштабе), перекрестие которых изначально координатно адаптировано с нулевой точкой отсчета исходных управляющих программ.
В процессе технологического цикла обработки (т.е. после заданного числа отработанных управляющих программ или их файлов) инструмент может автоматически (посредством откорректированной исходной программы ПЭВМ) вводиться в координатно зафиксированную (вышеописанными методами) точку, расположенную в поле зрения телевизионного микроскопа (т.е. точку, совпадающую с перекрестием ортогональных оптических осей объектива) для фотографирования режущей части инструмента с целью обеспечения контроля ее качества и оценки пригодности инструмента для дальнейшей обработки. После каждого фотографирования инструмент возвращается (также в автоматическом режиме) в ту же точку рабочей поверхности заготовки, на которой был прерван технологический цикл обработки.
Прецизионная обработка изделий со сложным пространственным профилем обрабатываемой поверхности (например, металлографских форм, рельеф рисунка формируемых на рабочей поверхности функционального слоя заготовки гравюр которых образован упорядоченным множеством профильных канавок различных размеров и геометрических форм, а также иных изделий с повышенными требованиями к точности обработки, в функциональных слоях которых необходимо обеспечить получение рисунка заданной глубины с субмикронным разрешением его структур) требует точного выполнения и сопряжения участков с различной формой и профилем формируемого рельефа. Поскольку размеры используемого для данной обработки инструмента могут быть аттестованы с погрешностью того же порядка, что и технологически заданные допуски на изготовление гравюр, а при смене инструмента, кроме того, возникают дополнительные погрешности положения вершины (и соответственно режущей кромки) инструмента, возникает необходимость после каждой смены инструмента обеспечивать точную проверку фактического положения его вершины (режущей кромки) относительно нулевой точки реперной координатной системы X1Y1Z1 отсчета станка с последующей коррекцией упомянутого фактического положения рабочих элементов инструмента относительно этой координатной системы. Аналогичная ситуация (в отношении необходимости коррекции фактического положения инструмента в координатной системе отсчета станка) может возникнуть и в ряде иных случаев (например, при величине накопленной ошибки перемещения в механизмах позиционирующих узлов станка выше предельно допустимой). Причем при осуществлении обработки изделий со сложной пространственно ориентируемой структурой формируемого рельефа коррекцию положения вершины (режущей кромки) инструмента необходимо осуществлять по трем координатам X1, Y1 и Z1 координатной системы отсчета станка.
Ввиду того, что, согласно изобретению визуальное отображение привязки к сформированной реперной системе X1Y1Z1 станка на экране монитора осуществляется в виде пересекающихся под прямым углом соответствующих осей, при соответствующем программном обеспечении в процессе реализации патентуемого способа позиционирования инструмента можно обеспечить измерение геометрических параметров и электронное фотографирование режущей части инструмента, например, для создание банка данных инструментов и т.п.
В связи с вышеизложенным, целесообразно более подробно рассмотреть вариант реализации способа позиционирования, согласно изобретению, для случая, когда вершина инструмента (а соответственно и его продольная ось, проходящая через эту вершину) изменяет свое пространственное положение (в плоскости Х1Y1 реперной координатной системы станка) при его повороте совместно со шпинделем на угол в пределах 360°. Такое пространственное изменение положения вершины возможно, например, в тех случаях, когда упомянутая вершина смещена, например, на величину «y1» относительно оси вращения шпинделя станка (ориентированной по оси «Z» координатной системы отсчета станка). Для этого случая вначале необходимо определить величину «y» (или «y1», что равнозначно) упомянутого смещения вершины посредством поворота инструмента совместно со шпинделем в поле зрения объектива компьютерного телевизионного микроскопа и произвести визуальную регистрацию процесса поворота на мониторе управляющего компьютера. После чего необходимо осуществить вышеупомянутую коррекцию управляющих программ в соответствии с вычисленной величиной смещения.
Схема определения величины вышеупомянутого смещения вершины инструмента (а соответственно и его продольной оси, проходящей через эту вершину) представлена на фиг.4 графических материалов.
Согласно данной схеме расчет новых значений (X1 и Y1) координат Х и Y вершины резца (или его продольной оси, проходящей через эту вершину) в плоскости XY рассчитывается по следующим формулам:
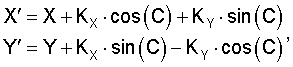
где Ку – величина коррекции по Y. Определяется как середина отрезка [X1, X11]. Знак определяется путем определения положения инструмента относительно оси микроскопа: если при повороте резца из положения 90° в положение 270° инструмент располагается справа, то знак плюс, иначе минус;
Кх – величина коррекции по X. Определяется как длина отрезка [Х2, Х21]. Знак определяется в соответствии со следующим правилом. Если инструмент в положении 0° отклонился от оси поворота вправо, то знак минус, иначе плюс;
X1 – новое значение координаты Х с учетом коррекции;
Y1 – новое значение координаты Y с учетом коррекции;
С – угол поворота инструмента.
Следует учесть, что (согласно данной схеме) движение вдоль плоскости XY осуществляется посредством перемещения стола с заготовкой, а инструмент (или шпиндель) может осуществлять движение только вокруг своей оси.
Такая коррекция управляющих программ снижает в процессе последующей обработки примерно в два раза погрешность, возникающую вследствие эксцентричного расположения вершины инструмента относительно оси поворота шпинделя. Таким образом (согласно заявленного способа) позиционирование и отсчет перемещений инструмента в процессе формирования фрагментов объемного рисунка гравюры в функциональном слое заготовки ведут от упомянутой нулевой точки реперной системы X1Y1Z1 согласно исходным управляющим программам системы ЧПУ с учетом коррекции по координатам «x1» и «y1» продольной оси инструмента (проходящей через его вершину) относительно действительной оси вращения шпинделя станка (параллельной оси Z или Z1), а также коррекции по результатам оцифровки.
Следует отметить, что упомянутые операции фотографирования передней поверхности режущей части инструмента, позицирования его вершины по трем координатам относительно нулевой точки сформированной реперной системы X1Y1Z1 и коррекции по координатам «x1» и «y1» продольной оси инструмента относительно действительной оси вращения шпинделя станка посредством оптико-электронной измерительной системы целесообразно осуществлять в прямом и теневом свете. Для этого упомянутую измерительную систему оснащают отражающим экраном 4, расположенным в поле зрения объектива 2 телевизионного компьютерного микроскопа 1 позади зоны ввода инструмента в это поле, а также двумя осветителями 5 и 6. Один из осветителей 5 в этом варианте реализации способа необходимо устанавливать с возможностью осуществления подсветки экрана, а другой осветитель 6 – с возможностью осуществления подсветки передней поверхности режущей части инструмента.
Данный вариант конструктивного исполнения оптико-электроной измерительной системы изображен на фиг.3 графических материалов заявки.
Данная система стационарно устанавливается на основном столе станка (осуществляющим возвратно-поступательное перемещение вдоль оси Х /или X1/ соответствующих координатных систем станка).
Между телевизионной камерой и объективом телевизионного компьютерного микроскопа установлены удлинительные кольца. Оптико-электронная часть измерительной системы фиксируется на двух стойках 8 и 9 с регулируемой высотой. Выбранная высота закрепляется фиксатором 10. Осветители 5 и 6 и экран 4 закреплены на третьей стойке 11 и регулируются по высоте одновременно с оптико-электронной частью.
Телевизионная камера 12 соединяется с компьютером телевизионным кабелем посредством установленной в нем платы видеозахвата, например, модели EZ Capture фирмы Aver Media. В качестве телевизионной камеры 12 может быть использована черно-белая телекамера RC – 583С с встроенным блоком питания, а в качестве осветителей -3 – осветители светодиодные белого света марки “Porta”.
Использование в оптико-электронной измерительной системе отражающего экрана 4 и двух осветителей 5 и 6 позволяет повысить контрастность изображения режущей части инструмента (в особенности ее границ, т.е., режущих кромок) на экране монитора, что повышает качество и эффективность контроля его параметров в режиме автоматического фотографировыания.
Предварительное позиционирование закрепленной заготовки посредством устройства для пространственной ориентации перед оцифровкой осуществляют посредством определения и регистрации соответствующими средствами измерения значений координат «z», по меньшей мере, трех не лежащих на одной прямой точек рабочей поверхности функционального слоя заготовки и последующего выравнивания в диапазоне допустимых отклонений величин этих значений посредством регулировочных узлов устройства для пространственной ориентации заготовок.
При реализации заявленного способа на базе откорректированных исходных управляющих на станке рассматриваемого автоматизированного гравировального комплекса могут выполняться следующие технологические операции:
– строгание канавок различной формы постоянной или переменной глубины (прямолинейные, круговые, синусоидальные, сложной формы) и семейства этих канавок, в том числе пересекающиеся друг с другом;
– сверление отверстий на небольшую глубину (при необходимости).
Строгание прямолинейных канавок постоянной глубины производится следующими способами:
– перемещением основного стола по координате Х с предварительным заглублением резца по координате Z и поворотом поворотного стола вокруг его оси на требуемый угол;
– требуемый угол наклона канавки к оси Х в горизонтальной плоскости вместо поворота поворотного стола может обеспечиваться интерполяцией перемещения по координатам Х и Y с поворотом шпинделя по координате С на этот требуемый угол.
В случае переменной глубины канавки перечисленные перемещения дополняются интерполяцией перемещения резца по координате Z.
Строгание канавок произвольной формы осуществляется перемещением по координатам Х и Y и поворотом резца по координате С таким образом, чтобы передняя грань (поверхность) резца в процессе резания в каждый момент времени была ориентирована по нормали к обрабатываемой дуге в точке резания.
Строгание синусоидальных канавок и канавок сложной геометрической формы производится аналогичным образом, а именно интерполяцией перемещений по координатам X, Y и C, а в случае их переменной глубины – дополнительно и по координате Z.
Сверление отверстий на небольшую глубину для заглубления строгального резца или других целей производится при позиционировании стола по координатам Х и Y с последующим перемещением шпинделя по координате Z при его вращении.
Таким образом, для выполнения перечисленных видов работ (помимо технологических возможностей, непосредственно вытекающих из технических характеристик станка) предусмотрены следующие вспомогательные технологические циклы и приемы, обеспечиваемые конструкцией станка и управляющими программами:
– коррекция положения точек рабочей поверхности функционального слоя заготовки по координате Z с учетом микронеровностей этой поверхности (оцифровка);
– определение положения и координатная привязка рабочей поверхности (т.е. нулевой точки отсчета реперной системы X1Y1Z1) функционального слоя заготовки относительно координатной системы отсчета станка;
– определение погрешностей заточки и установки резца в шпиндель станка и коррекция управляющих программ на основе полученных данных.
В процессе технологического цикла обработки необходимо оперировать следующими правилами перемещения инструмента в материале заготовки.
Во-первых, до начала работы строгальным резцом необходимо совместить ось поворота шпинделя с передней поверхность резца и осью симметрии его профиля на передней поверхности. Это осуществляется по результатам фотографирования режущей части резца с помощью оптико-электронной измерительной системы в ручном режиме вышеописанным методом с последующей корректировкой управляющей программы при наличии радиального смещения соответствующих осей.
Запрещается осуществлять поворот резца по координате «С» при фиксированных значениях координат «X», «Y» на угол более 5 градусов без вывода инструмента. Если такой поворот необходим по форме линии, то резец целесообразно вывести из заготовки, повернуть, и вновь врезаться в материал. При больших углах поворота процедуру необходимо повторить несколько раз (например, через каждые 15…30 градусов).
Поворот резца в материале допускается осуществлять по окружности, радиус которой больше R=(b/2+0,005) мм, где b – ширина передней поверхности резца при вершине.
Целесообразно также рассмотреть системы ЧПУ «Sinumerik-840Di», посредством которой реализуется заявленный способ и соответственно весь технологический цикл обработки.
Система ЧПУ «Sinumerik-840Di» выполнена в конструктиве операторной панели ОР12А на основе промышленного компьютера PCU50 с применением станочного 19 пульта МСР. Логика управления станком реализована с помощью встроенного программируемого контроллера S7-315-2DP. Для управления приводами подач по координатам использован привод «Simodrive 611U». Для обеспечения ввода и вывода дискретных сигналов применены модули РР72/48. Все перечисленные модули связаны друг с другом и системой ЧПУ «Sinumerik-840Di» полевой шиной «ProfiBus DP».
Для нормального функционирования программного обеспечения, реализующего заявленный способ, необходимо наличие следующих технических средств:
– IBM-совместимая машина;
– Система ЧПУ «Sinumerik-840Di»;
– плата АЦП фирмы L-Card L-783;
– индуктивный измеритель;
– плата видеозахвата, совместимая с Video for Windows (VfW) или DirectShow .
К информационной и программной совместимости (для реализации способа) предъявляются следующие требования.
Данная программа должна представлять собой один или несколько самостоятельных исполняемых модулей.
Информационная система должна быть реализована на языке программирования высокого уровня и работать под управлением операционной системы Windows 98/2000/XP.
Таким образом, заявленный способ позиционирования инструмента в координатной системе отсчета станка автоматизированного гравировального комплекса может быть, преимущественно, использован при механической прецизионной обработке (например, на прецизионных строгальных станках с системой ЧПУ) изделий со сложным пространственным профилем обрабатываемой поверхности (например, металлографских форм, рельеф рисунка формируемых на рабочей поверхности гравюр которых образован упорядоченным множеством профильных канавок различных размеров и геометрических форм), а также иных изделий с повышенными требованиями к точности обработки, в функциональных слоях которых необходимо обеспечить получение рисунка заданной глубины с субмикронным разрешением его пространственных структур.
Формула изобретения
1. Способ позиционирования инструмента в координатной системе отсчета станка автоматизированного гравировального комплекса, включающий формирование ортогональной реперной координатной системы X1Y1Z1, пространственную координатную привязку ее нулевой точки к нулевой точке ортогональной координатной системы XYZ отсчета станка, пространственно адаптированной с исходными управляющими программами системы числового программного управления (ЧПУ), посредством которых формируют фрагменты объемного рисунка гравюры в функциональном слое заготовки, которую закрепляют и позиционируют на установочной поверхности устройства для пространственной ориентации относительно плоскости XY координатной системы XYZ, фотографируют переднюю поверхность режущей части инструмента, позиционируют его вершины по трем координатам относительно нулевой точки сформированной реперной системы X1Y1Z1 и корректируют по координатам “х1” и “y1” проходящей через эту вершину продольной оси инструмента относительно параллельной оси Z или Z1 действительной оси вращения шпинделя станка с обеспечением визуального отображения результатов упомянутых операций фотографирования, позиционирования и коррекции на экране монитора управляющего механизмами перемещения станка компьютера и координатной адаптации этих результатов с управляющими программами системы ЧПУ посредством оптико-электронной измерительной системы, включающей телевизионный компьютерный микроскоп, который стационарно закрепляют на основном столе станка таким образом, что главная оптическая ось его объектива ориентирована по направлению возвратно-поступательного перемещения основного стола станка вдоль осей Х или X1 соответствующих координатных систем и координатно адаптирована с нулевой точкой координатной системы X1Y1Z1, для чего переднюю поверхность режущей части инструмента вводят в поле зрения объектива упомянутого микроскопа, его вершину совмещают с перекрестием ортогональных осей на экране монитора, которое расположено на главной оптической оси упомянутого объектива, и поворачивают шпиндель шпиндельной бабки станка на угол в пределах 360°, при этом позиционирование и отсчет перемещений инструмента в процессе формирования фрагментов объемного рисунка гравюры в функциональном слое заготовки ведут от упомянутой нулевой точки реперной системы X1Y1Z1 согласно исходным управляющим программам системы ЧПУ с учетом коррекции по координатам “х1” и “y1” упомянутой продольной оси инструмента относительно действительной оси вращения шпинделя станка, отличающийся тем, что перед формированием реперной координатной системы X1Y1Z1 осуществляют коррекцию управляющих программ системы ЧПУ на отклонение от плоскостности рабочей поверхности функционального слоя заготовки, которую предварительно закрепляют на установочной поверхности устройства для пространственной ориентации и пространственно ориентируют вдоль плоскости XY, для чего производят оцифровку по координатам “z” множества расположенных с заданным шагом точек этой поверхности на участке оцифровки, форма и площадь которого регламентируют формой и площадью формируемого на этой поверхности рисунка гравюры, оцифровку начинают с наиболее удаленной от центра участка оцифровки точки и продолжают посредством сканирования участка оцифровки средствами измерения с обеспечением регистрации значений координаты “z” в каждой точке оцифровки и автоматической коррекции управляющих программ ЧПУ по результатам оцифровки, реперную координатную систему X1Y1Z1 формируют от начальной точки оцифровки, функционально являющейся нулевой точкой этой системы, координаты которой перед началом обработки уточняют посредством обеспечения механического контакта вершины закрепленного в шпинделе инструмента с рабочей поверхностью функционального слоя заготовки в этой точке, при этом позиционирование и отсчет перемещений инструмента в процессе формирования фрагментов объемного рисунка гравюры в функциональном слое заготовки ведут от упомянутой нулевой точки реперной системы X1Y1Z1 согласно управляющим программам системы ЧПУ с учетом их дополнительной коррекции по результатам оцифровки.
2. Способ по п.1, отличающийся тем, что упомянутые операции фотографирования передней поверхности режущей части инструмента, позиционирования его вершины по трем координатам относительно нулевой точки сформированной реперной системы X1Y1Z1 и коррекции по координатам “x1” и “y1” проходящей через эту вершину продольной оси инструмента относительно параллельной оси Z или Z1 действительной оси вращения шпинделя станка посредством оптико-электронной измерительной системы осуществляют в прямом и теневом свете, для чего упомянутую измерительную систему оснащают экраном, расположенным в поле зрения объектива телевизионного компьютерного микроскопа позади зоны ввода инструмента в это поле, а также двумя осветителями, один из которых устанавливают с возможностью осуществления подсветки экрана, а другой – передней поверхности режущей части инструмента.
3. Способ по п.1, отличающийся тем, что предварительное позиционирование закрепленной заготовки посредством устройства для пространственной ориентации перед оцифровкой осуществляют посредством определения и регистрации соответствующими средствами измерения значений координат “z”, по меньшей мере, трех не лежащих на одной прямой точек рабочей поверхности функционального слоя заготовки и последующего выравнивания в диапазоне допустимых отклонений величин этих значений посредством регулировочных узлов устройства для пространственной ориентации заготовок.
РИСУНКИ
PD4A – Изменение наименования обладателя патента Российской Федерации на изобретение
(73) Новое наименование патентообладателя:
Федеральное государственное унитарное предприятие «Гознак» (RU)
Адрес для переписки:
115162, Москва, ул. Мытная, д. 19, начальнику отдела интеллектуальной собственности НИИ-филиала ФГУП «Гознак» В.А.Пашинину
Извещение опубликовано: 20.01.2007 БИ: 02/2007
RH4A – Выдача дубликата патента Российской Федерации на изобретение
Дата выдачи дубликата: 05.06.2007
Наименование лица, которому выдан дубликат:
ФГУП «ГОЗНАК» (RU)
Извещение опубликовано: 27.07.2007 БИ: 21/2007
|