|
(21), (22) Заявка: 2004135785/28, 06.12.2004
(24) Дата начала отсчета срока действия патента:
06.12.2004
(46) Опубликовано: 27.06.2006
(56) Список документов, цитированных в отчете о поиске:
КАРПОВ Л.П. Профилактика разрушений и новые технологии термообработки. М.: Машиностроение, 2003, с.69. SU 310761 A1, 01.01.1971. RU 2130608 С1, 20.05.1999. ЕР 0125988 A1, 21.11.1984.
Адрес для переписки:
624200, Свердловская обл., г. Лесной, ФГУП “Комбинат “Электрохимприбор”, патентная служба
|
(72) Автор(ы):
Карпов Леонид Павлович (RU)
(73) Патентообладатель(и):
Федеральное государственное унитарное предприятие “Комбинат “Электрохимприбор” (RU)
|
(54) СПОСОБ ОПРЕДЕЛЕНИЯ ПОТЕРИ ЗАПАСА ПЛАСТИЧНОСТИ СТАЛИ ПРИ МАРКИРОВКЕ ДЕТАЛЕЙ ЭЛЕКТРОГРАФОМ
(57) Реферат:
Использование: в машиностроении и измерительной технике. Сущность изобретения: на разрушенных деталях определяется глубина электроприжога, изготавливается партия пластинчатых образцов из такой же стали и такой же твердости, что на деталях, или из пружинной стали, половина партии образцов “маркируется” электроприжогом (прижигается полоска). Образцы испытываются на гиб-перегиб с участием в изломе электроприжога, по усредненным результатам числа циклов гиб-перегиба оценивают потерю запаса пластичности в процентах. Технический результат: определение потери запаса пластичности с непосредственным участием в зоне разрушения образца электроприжога в полном его объеме по ширине и глубине, повышение эффективности анализа и технологичности способа. 1 з.п. ф-лы, 1 ил., 2 табл.
Изобретение относится к области машиностроения и может использоваться при изготовлении стальных высокопрочных деталей с их маркировкой. Маркировка деталей назначается с целью обозначить партию, например, термообработки, изготовления, испытания и т.д. Известны различные способы маркировки, в частности клеймением, электрографом. Маркировка электрографом заключается в нанесении знаков на поверхность детали путем электроискрового прижога металла. При этом возможен разогрев и перезакалка стали с повышением ее твердости и появлением хрупкости, возможно легирование стали в зоне разогрева. То и другое снижает пластичность стали. Потеря пластичности, как известно, может привести к неожиданным разрушениям деталей.
Известны способы определения потери пластичности стали при электроискровом прижоге, например, сравнением твердости нетравящейся зоны прижога и сердцевины. Так, например, маркировали электрографом шпильки из стали 25Х17Н2Б-Ш, термообработанные на микротвердость 372 HV0,2. Глубина прижога составляла 0,025-0,074 мм. Микротвердость нетравящейся верхней зоны равнялась 432 HV0,2, переходной зоны 401 HV0,2. Степень прижога по микротвердости равна (432-372/432).100%=13,8%.
Другой пример описан на с.69 книги: Л.П.Карпов “Профилактика разрушений и новые технологии термообработки. М.: Машиностроение. 2003.” При электроискровом прижоге тарельчатых пружин из стали 60С2А твердость равнялась 700 HV при твердости сердцевины, равной 556 HV.
Степень прижога составляла 20,6%. Однако сравнение твердости, оценка повышения микротвердости в зоне электроприжога являются косвенными способами оценки потери пластичности, исходящими из общего положения снижения пластичности стали с ростом твердости.
За прототип взят способ оценки степени прижога, описанный в указанной книге (с.69).
Недостатки прототипа: потеря пластичности оценивается косвенно, по возрастанию твердости зоны прижога, механическое воздействие на всю зону электроприжога, как это происходит при разрушении деталей, не выполняется.
Задача изобретения: предложить способ нанесения маркировки и механического испытания с оценкой потери запаса пластичности стали именно в зоне маркировки, включая зону электроприжога.
Технический результат: определение потери запаса пластичности с непосредственным участием в зоне разрушения образца электроприжога в полном его объеме по ширине и глубине, повышение эффективности анализа причин неожиданных разрушений и профилактики разрушений, проектирование надежной технологии изготовления деталей, повышается технологичность способа и возможно применение при любой, самой малой, глубине прижога.
Поставленная задача решается тем, что способ определения потери запаса пластичности стали при маркировке деталей электрографом включает определение поверхностной твердости и глубины прижога деталей, твердости сердцевины деталей, определение степени прижога и изготовление образцов из такой же стали и такой же твердости, что на деталях.
При этом изготавливают партию пластинчатых образцов из исследуемой или пружинной стали, закаливают образцы с отпуском до твердости, равной твердости деталей, делят партию на две части, детали одной из них “маркируют”, т.е. наносят продольную полоску прижога, обеспечивая глубину прижога и применяемый материал иглы электрографа такими же, как при маркировке деталей, испытывают образцы всей партии до разрушения методом многократного гиб-перегиба с фиксированием числа циклов, обеспечивая разрушение поперек полоски прижога, усредняют результаты числа циклов в каждой части образцов и по ним рассчитывают потерю запаса пластичности, как отношение разницы среднего числа циклов двух частей образцов к числу циклов образцов немаркированных, в процентах.
Образцы пружинной стали изготавливают поперечными из ленты толщиной 0,5-0,6 мм с шириной 10 мм (вдоль проката) и длиной 60-70 мм, продольную полоску прижога наносят длиной 8-12 мм, испытывают в зажимах с радиусом 7,5 мм, вылетом образца до поводка 30 мм, шириной щели поводка 1,5 мм, частотой 3 с на один цикл гиб-перегиба.
Для реализации способа выполняют операции
1. Делают анализ глубины и степени прижога на деталях, разрушенных при маркировке, или подлежащих профилактике разрушения.
2. Изготавливают партию пластинчатых образцов из стали такой же марки, из которой изготовлены детали, или пружинной размерами (0,5×10×60) мм. Размер 10 мм вдоль проката.
3. Образцы закаливают на мартенсит и отпускают до твердости, равной твердости деталей.
4. Партию образцов делят на 2 части.
5. Одну часть образцов “маркируют”, проведя полоску шириной 0,6-0,8 мм, длиной 8-12 мм вдоль размера 60 мм по центру ширины 10 мм в зоне предстоящего разрушения на гиб-перегиб. Материал иглы электрографа и глубину прижога обеспечивают, как при маркировке деталей.
6. Испытывают образцы той и другой части до разрушения, идущего поперек образца через полоску прижога, методом гиб-перегиба с частотой 3 с на 1 цикл. Режимы испытания подбирают, обеспечивая достаточную базу числа циклов с целью сравнения пластичности образцов с маркировкой и без нее. Например, для поперечных пластин из стали 65Г берут зажимы с радиусом 7,5 мм, вылет до поводка 30 мм, щель поводка 1,5 мм. Записывают число циклов.
7. Усредняют результаты каждой части образцов и находят потерю запаса пластичности, как отношение разницы числа циклов образцов не маркированных и маркированных к числу циклов образцов не маркированных, в процентах.
Способ проверен практически при анализе потери запаса пластичности от маркировки электрографом тарельчатых пружин. Пластинчатые образцы изготовили из стали 65Г, после закалки от 810°С и отпуска при 420°С, образцы имели твердость 453 HV. Прижог выполнили электрографом с графитовой иглой (фиг.1) на глубину 0,015 мм. Результаты испытания – в таблице 1. Потеря запаса пластичности составляет
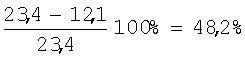
Таблица 1 Пример потери запаса пластичности от маркировки электрографом образцов стали 65Г, отпущенных после закалки при 420°С |
Часть партии образцов |
Маркировка |
Пластичность, циклов |
Среднеквадратическое отклонение, циклов |
По образцам |
Среднее |
Без маркировки |
20 |
21 |
23,4 |
2,17 |
1-я |
21 |
26 |
25 |
24 |
23 26 |
23 25 |
2-я |
Электрографом с графитовой иглой |
6 |
13 |
12,1 |
3,69 |
13 |
19 |
11 14 12 |
8
13 |
После отпуска при 520°С на твердость 337 HV (таблица 2) потеря запаса пластичности от электроприжога составляет
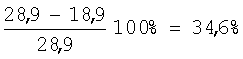
т.е. меньше, чем в первом случае, т.к. твердость сердцевины деталей меньше.
Таблица 2 Потеря запаса пластичности от маркировки электрографом образцов стали 65Г, отпущенных после закалки при 520°С |
Часть партии образцов |
Маркировка |
Пластичность циклов |
Среднеквадратическое отклонение, циклов |
По образцам |
Среднее |
1-я |
Без маркировки |
32 |
33 |
28,9 |
2,95 |
39 |
26 |
26 31 |
26 27 |
2-я |
Электрографом с графитовой иглой |
22 |
20 |
18,9 |
4,04 |
16 |
21 |
18 |
17 |
22 26 |
13 14 |
Технический результат изобретения заключается в возможности определения потери запаса пластичности в зоне с непосредственным участием электроприжога в полном его объеме (ширина, глубина). Это существенно повышает объективность оценки причины охрупчивания стали, эффективность мероприятий по профилактике разрушений высокопрочных деталей, способствует проектированию надежной технологии изготовления деталей. Предложенный способ технологичнее, чем сравнением твердости, т.к. при малой глубине прижога определение его твердости на поперечном микрошлифе затруднительно или невозможно (поверхность прижога имеет грубую шероховатость), тогда как механическое испытание вполне возможно в любом случае.
Формула изобретения
1. Способ определения потери запаса пластичности стали при маркировке деталей электрографом, включающий определение поверхностной твердости и глубины прижога деталей, твердости сердцевины деталей, определение степени прижога, изготовление образцов, отличающийся тем, что изготавливают партию пластинчатых образцов, закаливают образцы с отпуском до твердости, равной твердости деталей, делят партию на две части, образцы одной из них “маркируют”, т.е. наносят продольную полоску прижога, обеспечивая глубину прижога и применяемый материал иглы электрографа такими же, как при маркировке деталей, испытывают образцы всей партии до разрушения методом многократного гиб-перегиба с фиксированием числа циклов, обеспечивая разрушение поперек полоски прижога, усредняют результаты числа циклов в каждой части образцов и по ним рассчитывают потерю запаса пластичности как отношение разницы среднего числа циклов двух частей образцов к числу циклов образцов немаркированных в процентах.
2. Способ по п.1, отличающийся тем, что образцы пружинной стали изготавливают поперечными из ленты толщиной 0,5-0,6 мм с шириной 10 мм (вдоль проката) и длиной 60-70 мм, продольную полоску прижога наносят длиной 8-12 мм, испытывают в зажимах с радиусом 7,5 мм, вылетом образца из зажимов до поводка 30 мм, шириной щели поводка 1,5 мм, частотой 3 с на один цикл гиб-перегиба.
РИСУНКИ
|
|