(21), (22) Заявка: 2004113907/02, 05.05.2004
(24) Дата начала отсчета срока действия патента:
05.05.2004
(43) Дата публикации заявки: 27.10.2005
(46) Опубликовано: 20.06.2006
(56) Список документов, цитированных в отчете о поиске:
SU 852517 A1, 07.08.1981. SU 1151439 A1, 23.04.1985. SU 837826 A1, 15.06.1981. RU 2113971 С1, 27.06.1998. SU 1272172 A1, 23.11.1986. US 4805429 A, 21.02.1989.
Адрес для переписки:
426069, Удмуртия, г.Ижевск, ул. Студенческая 7, ИжГТУ
|
(72) Автор(ы):
Исупов Максим Георгиевич (RU)
(73) Патентообладатель(и):
Государственное образовательное учреждение высшего профессионального образования Ижевский государственный технический университет (RU)
|
(54) СПОСОБ КОНТРОЛЯ ПРОЦЕСССА СТРУЙНО-АБРАЗИВНОЙ ОБРАБОТКИ
(57) Реферат:
Изобретение относится к контролю процессом струйно-абразивной обработки поверхностей деталей и может быть использовано в машиностроении при нанесении смазочных микрокарманов заданной глубины. Способ включает определение скорости удара абразивных частиц по поверхности вращаемого, а затем неподвижного контрольного образца с последующим измерением глубины лунок. Контрольный образец изготавливают из того же материала, с той же твердостью, что и обрабатываемую деталь. Вращают контрольный образец и подают в зону его вращения абразив с помощью пневматического сопла, установленного перпендикулярно плоскости вращения. Измеряют глубину лунок 0, которую получают при линейной скорости вращения V0 на радиусе точки удара абразивных частиц, определяемой по формуле (1). Производят струйно-абразивную обработку неподвижного образца абразивными частицами того же состава. При этом измеряют глубину лунок 1 и определяют скорость удара V1 по формуле (2). Осуществляют струйно-абразивную обработку детали. Определяют по формуле (3) давление на входе струйно-абразивного сопла Р3, обеспечивающего получение лунок заданной глубины. В результате обеспечивается заданная глубина смазочных микрокарманов. 2 ил.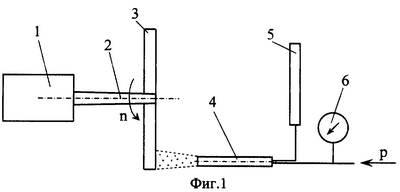
Изобретение относится к способам контроля процессом струйно-абразивной обработки поверхностей деталей и может найти применение в машиностроении, например при нанесении смазочных микрокарманов заданной глубины на поверхности трения струйно-абразивным способом.
Известен способ измерения скорости удара абразивных частиц [1], в котором измерение скорости производится с помощью скоростной киносъемки.
Недостатками аналога являются необходимость иметь скоростную камеру и достаточно сложная технология работы с ней.
В качестве прототипа выбран способ контроля и управления процессом струйно-абразивной обработки поверхностей деталей [2], заключающийся в том, что в качестве контролируемого параметра выбирают рабочие скорости и контроль осуществляют, сопоставляя рабочие и критические скорости (критическая скорость – скорость разрушения абразивных частиц) в зависимости от чистоты обрабатываемой поверхности. Управление процессом осуществляют путем измерения лунок, скорости и твердости при контрольных испытаниях и действительного технологического процесса.
Недостатком прототипа является то, что в нем не приведена конкретная методика измерения скорости удара частиц по обрабатываемой поверхности, вследствие чего описываемый в прототипе способ не может быть использован, например, для назначения скорости удара абразивных частиц при производстве смазочных микрокарманов струйно-абразивным способом.
Технической задачей, стоящей перед автором, является задача обеспечения заданной глубины смазочных микрокарманов в зависимости от размера абразивных частиц и твердости металла обрабатываемой поверхности.
Технический результат достигается тем, что контроль струйно-абразивной обработки осуществляется путем определения скорости удара (формула (1)) абразивных частиц по поверхности контрольного образца, вращаемого относительно его центра, с измерением числа оборотов n, подачи абразива в зону вращения контрольного образца с последующим измерением глубины лунок 0 и радиуса r точки удара абразивных частиц по контрольному образцу.
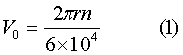
Контрольный образец изготовлен из того же материала, что и обрабатываемая деталь, и имеет ту же твердость. Подача абразива в зону вращения контрольного образца осуществляется с помощью пневматического сопла, установленного перпендикулярно плоскости вращения контрольного образца. Скорость подачи абразивных частиц обеспечивает преодоление динамического напора воздуха от вращения контрольного образца. Далее получают лунки глубиной 1 от удара абразивных частиц того же состава, на том же контрольном образце при струйно-абразивной обработке. Скорость удара определяют по формуле
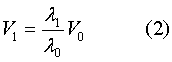
где
1 – глубина лунки от удара абразивных частиц при струйно-абразивной обработке;
0 – глубина лунок от удара абразивных частиц при вращении контрольного образца.
Определяют давление Р3 сжатого воздуха на входе струйно-абразивного сопла, обеспечивающего получение лунок заданной глубины по формуле
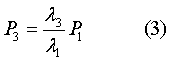
где
Р3 – давление, обеспечивающее получение лунки, заданной глубины;
3 – заданная глубина лунки.
На фиг.1 показана схема установки для определения скорости удара абразивных частиц:
На фиг.2 – лунки на поверхности контрольного образца, полученные при “а” – вращении, “б” – струйно-абразивной обработке.
Установка для измерения скорости удара абразивных частиц (фиг.1) включает в себя двигатель 1, вал 2, контрольный образец 3 (размеры 100×12×2), струйно-абразивное сопло 4, служащее для подачи абразивных частиц в зону обработки, бункер 5 для абразивных частиц и манометр 6 для измерения давления сжатого воздуха, поступающего на вход струйно-абразивного сопла 4.
Измерение скорости удара абразивных частиц, формирующих смазочные микрокарманы заданной глубины, происходит следующим образом. Предварительно изготавливается контрольный образец из того же металла и той же твердости, что и обрабатываемая деталь. Контрольный образец шлифуется с обеих сторон до Ra 0,5 мкм и затем крепится на валу, как показано на фиг.1, после чего приводится во вращение с заданной угловой скоростью. Перпендикулярно плоскости вращения, на расстоянии 5…10 мм от нее, расположен выходной срез струйно-абразивного сопла, на вход которого поступают сжатый воздух и абразивные частицы из бункера 5.
Назначение струйно-абразивного сопла:
– подача абразивных частиц в зону вращения контрольного образца, так как при ее вращении образуется воздушный поток, препятствующий движению абразивных частиц в зону вращения контрольного образца;
– разгон абразивных частиц до рабочих скоростей их удара.
Процесс измерения скорости удара включает в себя следующие действия. После начала вращения контрольного образца на вход струйно-абразивного сопла подаются сжатый воздух и абразивные частицы. Постепенно увеличивая давление на входе струйно-абразивного сопла, достигают такого момента, когда скорость абразивных частиц достаточна для преодоления динамического напора воздуха, создаваемого вращением контрольного образца, и они попадают в поле его вращения. При ударе контрольного образца по абразивным частицам на нем образуются лунки, глубина которых зависит от линейной скорости контрольного образца на радиусе удара r. Линейная скорость вращения образца находится по формуле (1).
После того, как определенная масса абразива (порядка 30 грамм для абразива А14) пройдет через струйно-абразивное сопло, вращение контрольного образца прекращается, он снимается с установки, устанавливается перед срезом струйно-абразивного сопла на расстоянии Х=(2…3)dc, (где dc – диаметр пневматического сопла), соответствующем рабочему расстоянию при струйно-абразивной обработке. В сопло подаются рабочее давление воздуха, предварительно определенное расчетным или опытным путем, и абразивные частицы, в результате чего на контрольном образце (в другом месте) получают пятно контакта струйно-абразивной струи. Контрольный образец с пятнами контакта, полученными при вращении и струйно-абразивной обработке, разрезают в средней части и изготовляют шлифы, по которым на микроскопе измеряют глубины лунок в обоих случаях. Скорость удара при струйно-абразивной обработке определяется по формуле (2), полученной из формулы (4), приведенной в прототипе [2]:
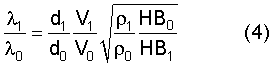
где
d0 – приведенный диаметр частицы абразива при контрольных испытаниях;
0 – удельный вес абразива при контрольных испытаниях;
НВ0 – твердость материала обрабатываемой поверхности при контрольных испытаниях;
1, d1, 1, HB1 – соответствующие параметры действительного технологического процесса (в нашем случае – струйно-абразивной обработки).
Применительно к нашему случаю подкоренное выражение и d1/d0 равны единице. Требуемая величина рабочего давления получается после проведения разового эксперимента и определения параметров n, V0, r, , V1, P1.
Таким образом, для каждой пары абразив – обрабатываемая деталь по приведенному выше способу находится требуемое рабочее давление на входе в струйно-абразивное сопло, обеспечивающее получение смазочных микрокарманов заданной глубины.
Пример. Найти технологические режимы получения смазочных микрокарманов на плунжере насоса диаметром 40 мм, материал – сталь 40Х, твердость HRC 52. Используется абразив – электрокорунд белый А14 (размеры частиц 500…600 мкм), требуемая глубина смазочных микрокарманов 20 мкм. Из стали 40Х изготавливается контрольный образец с размерами 100×12×2. Размеры контрольного образца не имеют существенного значения, они могут быть меньше или больше в зависимости от возможности получения требуемой линейной скорости вращения. Толщина контрольного образца выбирается из условия гарантированной прочности и жесткости. Контрольный образец закрепляется на конце вала установки, фиг.1. В качестве привода вала используется шлифовальная машинка “Висма”, скорость вращения которой регулируется от 0 до 8000 об/мин. Устанавливается максимальная скорость вращения (8000 об/мин), которая дает на радиусе 50 мм линейную скорость вращения V0=41,8 м/с, скорость находится по формуле (1).
В бункер струйно-абразивного сопла насыпалось 34 г абразива А14 (электрокорунд белый), количество абразива определялось емкостью бункера. Оно должно быть достаточным, чтобы на контрольном образце площадь смазочных микрокарманов занимала бы не менее 50% поверхности пятна контакта. В этом случае при разрезке контрольного образца по середине пятна контакта примерно половина его длины будет занята смазочными микрокарманами и среднее значение их глубины будет объективным. Для преодоления динамического напора воздуха, возникающего от вращения контрольного образца, на вход струйно-абразивного сопла подавалось избыточное давление 0,2 бар. При этом давлении абразивные частицы преодолевают динамический напор, возникающий от вращения контрольного образца, и поступают в зону его вращения. При давлении 0,2 бар скорость абразивных частиц на выходе из струйно-абразивного сопла равна 12…15 м/сек. Скорость движения абразивных частиц не оказывает влияния на глубину лунки, так как ее направление перпендикулярно плоскости вращения контрольного образца. Тем не менее величина скорости входа абразивных частиц в зону вращения контрольного образца ограничена двумя критериями: первый – при слишком малой скорости абразивные частицы не в состоянии преодолеть динамический напор от вращения контрольного образца, они отбрасываются в сторону, лунки на контрольном образце не образуется. При слишком большой скорости большая часть абразивных частиц успевает пролететь через зону вращения контрольного образца, не касаясь его, и для получения достаточно плотного пятна контакта от воздействия абразивных частиц на контрольном образце необходим их повышенный расход. После того, как весь абразив из бункера был выработан, вращение контрольного образца прекращалось, его снимали с вала (фиг.1) и на нем получали пятно контакта с помощью струйно-абразивного сопла, но уже в другом месте, с измерением давления питания Р1 сжатого воздуха на входе в струйно-абразивное сопло. Затем изготавливались шлифы в том и другом случае и определялась глубина 0 микрокармана, полученного при вращении контрольного образца, и 1, полученного струйно-абразивным способом.
Зная требуемое значение 3 и имея значения 1 и P1, по формуле (3) получают значение рабочего давления сжатого воздуха Р3 на входе в струйно-абразивное сопло, обеспечивающее получение лунок заданной глубины.
Источники информации
1. Меерович М.З. и др. Рациональные режимы дробеструйной очистки чугунных отливок. Ленинградский дом научно-технической пропаганды. Л., 1972 г., с.25.
2. Авторское свидетельство СССР №852517, МПК В 23 С 1/00. Способ контроля и управления процессом абразивоструйной обработки поверхностей деталей.
Формула изобретения
Способ контроля процесса струйно-абразивной обработки, включающий определение скорости удара абразивных частиц по поверхности контрольного образца, отличающийся тем, что скорость удара абразивных частиц по поверхности контрольного образца, вращаемого относительно его центра, определяют путем измерения числа оборотов n, осуществляют подачу абразива в зону вращения контрольного образца с последующим измерением глубины лунок 0 и радиуса r – точки удара абразивных частиц по контрольному образцу
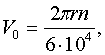
где V0 – линейная скорость вращения;
n – число оборотов контрольного образца (об/мин),
при этом контрольный образец изготавливают из того же материала, с той же твердостью, что и обрабатываемую деталь, подачу абразива в зону вращения контрольного образца осуществляют с помощью пневматического сопла, установленного перпендикулярно плоскости вращения образца, затем получают лунки от удара абразивных частиц того же состава, на том же контрольном образце при струйно-абразивной обработке, при этом определяют скорость удара по формуле

где 1 – глубина лунки от удара абразивных частиц при струйно-абразивной обработке;
0 – глубина лунки от удара абразивных частиц при вращении контрольного образца,
затем определяют давление на входе струйно-абразивного сопла Р3, обеспечивающего получение лунок заданной глубины, по формуле

где P1 – давление на входе струйно-абразивного при струйно-абразивной обработке;
3 – заданная глубина лунки.
РИСУНКИ
MM4A – Досрочное прекращение действия патента СССР или патента Российской Федерации на изобретение из-за неуплаты в установленный срок пошлины за поддержание патента в силе
Дата прекращения действия патента: 06.05.2006
Извещение опубликовано: 27.04.2007 БИ: 12/2007
|