(21), (22) Заявка: 2004118702/02, 18.08.2004
(24) Дата начала отсчета срока действия патента:
18.08.2004
(43) Дата публикации заявки: 27.01.2006
(46) Опубликовано: 20.06.2006
(56) Список документов, цитированных в отчете о поиске:
RU 2171160 C1, 27.07.2001. RU 2099163 C1, 20.12.1997. JP 4202611 А, 23.07.1992. FR 2656244 А1, 28.06.1991.
Адрес для переписки:
124617, Москва, Зеленоград, а/я 41, В.А. Подольскому
|
(72) Автор(ы):
Ахметшин Марсиль Робертович (RU), Ахметшин Ринат Робертович (RU), Лапковский Сергей Иванович (BY), Подольский Владимир Антонович (RU), Ткаченко Вячеслав Аркадьевич (RU), Шейнерт Виктор Александрович (BY)
(73) Патентообладатель(и):
Ахметшин Марсиль Робертович (RU), Ахметшин Ринат Робертович (RU), Подольский Владимир Антонович (RU), Ткаченко Вячеслав Аркадьевич (RU)
|
(54) СПОСОБ ПРОИЗВОДСТВА МЕТАЛЛИЧЕСКОГО ВОЛОКНА
(57) Реферат:
Изобретение относится к металлургии, к изготовлению металлического волокна, фибры, шерсти. Металл подают в зону диспергирования. Формируют из него в окружении динамического слоя газа дискретные частицы расплава металла и одновременно преобразуют динамический слой в парогазовую смесь. Формирование дискретных частиц расплава металла производят в два этапа. На первом этапе электродуговым способом разрушают, по крайней мере, один из электродов, формируя поток дискретных частиц расплава металла, и производят их дробление путем соударения на скорости от 500 до 1100 м/с с поверхностью вращающегося дискового диспергатора под углом от 4 до 90 градусов относительно плоскости вращения. На втором этапе агломерируют полученные дискретные микрочастицы расплава металла до схожих размеров на поверхности вращающегося дискового диспергатора за счет одновременного воздействия на них парогазовой смесью и полем механических сил вращающегося дискового диспергатора. Полученные частицы преобразуют в жидкие структуры металлического волокна посредством воздействия на них полем механических сил вращающегося дискового диспергатора. Охлаждают волокно до отвержденного состояния на поверхности соосно вращающегося дискового кристаллизатора, снабженного средством регулирования температуры его рабочей поверхности, и удаляют его с рабочей поверхности. Обеспечивается автокалибровка дискретных частиц волокна и стабилизация процесса производства. 5 з.п. ф-лы, 3 ил.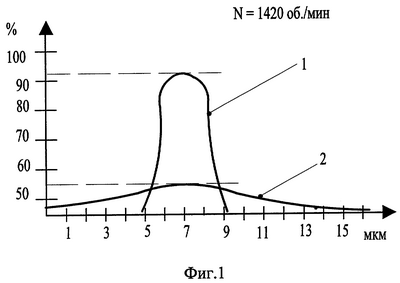
Изобретение относится к области металлургии, а конкретно к способам промышленного производства металлического, преимущественно стального, волокна (фибры, металлической шерсти).
Известен способ [1] получения быстро закаленного металлического волокна (фибры) из расплава, в котором вращающийся в вертикальной плоскости цилиндрический кристаллизатор с регулируемой температурой рабочей поверхности вводится рабочей кромкой в соприкосновение с расплавом, формируемым в термически изолированной ванне, снабженной ограничительным элементом.
Недостатком известного способа-аналога является то, что его реализация требует использования значительной по размеру термически изолированной ванны для размещения в ней расплава металла и поддержания в этом расплаве металла заданной температуры перегрева. Из-за наличия соответствующей открытой площади контакта зеркала расплава металла с атмосферой происходит химическое взаимодействие (поверхностное окисление) расплава металла и существенное ухудшение качества производимого металлического волокна (фибры). Это ухудшение обусловлено тем, что продукты окисления при попадании в зону взаимодействия расплава металла и рабочей поверхности цилиндрического кристаллизатора разрушают мениск между поверхностью расплава металла и уже отвержденной фиброй на рабочей поверхности кристаллизатора. Соответственно этому происходит быстрое образование на рабочей поверхности цилиндрического кристаллизатора гарнисажа, приводящего к выбросам капель расплава из теплоизолированной ванны. Кроме этого, вращающийся в поверхностном слое расплава металла цилиндрический кристаллизатор вызывает возникновение в нем волнообразования, приводящего к неконтролируемой флуктуации глубины погружения кристаллизатора, что увеличивает разброс геометрических параметров (в первую очередь разброс по толщине) производимого металлического волокна (фибры).
Наиболее близким по технической сущности и достигаемому результату является способ изготовления металлического волокна из расплава [2], принятый в качестве ближайшего аналога. В соответствии со способом-прототипом на профилированную поверхность вращающегося в горизонтальной плоскости первого дискового кристаллизатора, установленного соосно второму дисковому кристаллизатору, рабочая поверхность которого охватывает первый из них в той же плоскости, из сопла питателя, снабженного средствами подогрева находящегося в нем расплава металла, равномерно наносят слой расплава металла, перегретый на 4-18% относительно температуры его отверждения. При этом полем механических сил вращающегося первого дискового кристаллизатора из нанесенного слоя расплава металла формируют дискретные жидкие структуры металлического волокна, причем сообщают им скорость перемещения на второй дисковый кристаллизатор в интервале от 0,5 до 148 м/с. При ударном контакте с рабочей поверхностью второго дискового кристаллизатора дискретные жидкие структуры металлического волокна отверждаются с темпом охлаждения от 3,3 до 25,7 на его оребренной в интервале значений от 1,06 до 482 поверхности. Процесс диспергации и отверждения металлического волокна производят в окружении динамического слоя инертного газа, в качестве которого применяют аргон, или гелий, либо их смесь. Для увеличения коррозионной стойкости произведенного металлического волокна за счет пассивации его поверхности до отверждения в динамический слой инертного газа вводят аэрозоль от 4 до 60% об. из частиц цинка (с размерами, находящимися в интервале значений от 0,05 до 1,2 мкм), при этом частицы цинка в аэрозоли содержатся в количестве от 16 до 48% об.
Недостатком способа-прототипа является то, что между рабочей охлаждаемой поверхностью вращающегося дискового диспергатора и областью налитого на него из сопла питателя расплава металла неконтролируемо формируется прослойка гарнисажа. Это обстоятельство вносит сильное возмущающее воздействие на образование дискретных жидких структур металлического волокна, которые, по-существу, формируются за счет отрыва капель расплава металла в поле механических сил вращающегося дискового диспергатора от налитого слоя расплава металла. Помимо образования динамических температурных градиентов в вертикальной плоскости, отрицательно сказывающихся на однородности вязкости расплава металла (и, соответственно, изменяющих усилия капельного отрыва), сплошная динамически неоднородная пленка гарнисажа существенно изменяет адгезионные свойства поверхности, контактирующей с расплавом металла, и формируемыми из него дискретными жидкими структурами металлического волокна.
Результат этого проявляется в невоспроизводимости основных параметров дискретных жидких структур металлического волокна, равно как и в разбросе характеристик изготовленного металлического волокна в целом, особенно в интервале длин металлического волокна от 30 мкм до 50 мм.
В основу изобретения положена задача повышения уровня воспроизводимости гранулометрических параметров (веса, габаритов, морфологического и фазового состава) изготовляемого металлического волокна, т.е. стабилизация процесса его производства.
Техническим результатом настоящего изобретения является обеспечение условий автокалибровки дискретных жидких структур металлического волокна на поверхности вращающегося дискового диспергатора до их перемещения на рабочую поверхность кристаллизатора.
Указанный технический результат достигается тем, что в способе производства металлического волокна, включающем подачу металла в зону диспергирования, формирование из него в окружении динамического слоя газа дискретных частиц расплава металла, преобразование дискретных частиц расплава металла в жидкие структуры металлического волокна посредством воздействия на них полем механических сил вращающегося дискового диспергатора, охлаждение жидких структур металлического волокна до отвержденного состояния на поверхности соосно вращающегося дискового кристаллизатора, снабженного средством регулирования температуры его рабочей поверхности, и последующее удаление отвержденного металлического волокна с этой рабочей поверхности, причем одновременно с формированием дискретных частиц расплава металла динамический слой газа преобразуют в парогазовую смесь, а собственно формирование дискретных частиц расплава металла производят в два этапа, на первом из которых электродуговым способом разрушают, по крайней мере, один из электродов, формируя таким образом поток дискретных частицы расплава металла в широком интервале размеров, и производят их дробление путем соударения на скорости от 500 до 1100 м/с с поверхностью вращающегося дискового диспергатора под углом от 4 до 90 градусов относительно плоскости вращения, а на втором этапе агломерируют полученные дискретные микрочастицы расплава металла до схожих размеров на поверхности вращающегося дискового диспергатора за счет одновременного воздействия на них парогазовой смесью и полем механических сил вращающегося дискового диспергатора. Имеет значение металл в зону диспергирования подавать в твердом агрегатном состоянии.
Желательно также динамический слой газа преобразовывать в парогазовую смесь с содержанием от 0,1 до 30% об. диспергируемого металла.
Предпочтительно также газ парогазовой смеси выбирать из ряда: инертный газ и/или восстановительный газ.
Целесообразно восстановительный газ выбирать из ряда: водород, пропан, бутан, метан.
Желательно инертный газ выбирать из ряда: аргон, гелий.
Известен способ использования эффекта оплавления концов сближаемых электродов (с образованием электрической дуги) для формирования потока брызг металлического расплава и последующего осаждения их на поверхность (авт.свид. СССР №438648, кл. 49/3, 21.11.1950 г.).
Однако данный способ предназначен для металлизации поверхности и в нем не раскрывается (т.е. из изложенной в охранном документе информации не следует) возможность использования металлизируемой поверхности для последующей автокалибровки взаимодействующего с поверхностью потока дискретных жидких структур металлического расплава.
Поэтому есть основания утверждать то, что выявленный экспериментально факт автокалибровки жидких металлических структур является новым и неизвестным, а заявленный в связи с его техническим воплощением способ как объект изобретения соответствует критериям “новизна” и “изобретательский уровень”.
Заявленное новое техническое решение иллюстрируется следующими чертежами:
на фиг.1 представлены сравнительные графики разброса габаритных размеров (ширины) металлического волокна, произведенного в соответствии со способом-прототипом и в соответствии с предложенным способом;
на фиг.2 представлены сравнительные графики разброса габаритных размеров (длины) металлического волокна, произведенного в соответствии со способом-прототипом и в соответствии с предложенным способом;
на фиг.3 схематично изображена установка для производства металлического волокна.
Перечень позиций
1. Распределение размеров металлического волокна, произведенного предложенным прототипом.
2. Распределение размеров металлического волокна, произведенного способом-прототипом.
3. Трайб-аппарат.
4. Расходуемый электрод.
5. Зона формирования электрической дуги.
6. Источник электрического питания дуги.
7. Дисковый диспергатор.
8. Дисковый кристаллизатор.
9. Газовая рампа.
10. Газовый трубопровод.
11. Распылитель газа.
12. Форсунки газового распылителя.
13. Рабочая поверхность кристаллизатора.
14. Узел регулирования температуры.
15. Шланги подачи хладагента.
16. Канал жидкостного охлаждения.
17. Хладагент.
18. Цепь питания электродов.
19. Приводы вращения.
20. Нерасходуемый электрод.
21. Канал откачки парогазовой смеси.
ПРИМЕР 1. Для подачи металла в зону диспергации в твердом агрегатном состоянии в приданный установке трайб-аппарат 3 (фиг.3) заряжают стальную проволоку (расходуемый электрод 4 (фиг.3)) диаметром 2 мм, предварительно устанавливают скорость ее подачи в зону формирования электрической дуги 5 (фиг.3), равной 0,1 м/с, и задают напряжение холостого хода источника электрического питания дуги 6 (фиг.3), равное 60 В. В этом случае на дуговом промежутке будет поддерживаться напряжение в пределах 25-30 В и ток дуги не превысит 480-500 А.
Устанавливают частоту вращения (по часовой стрелке) дискового диспергатора 7 (фиг.3), выполненного из высокотемпературной керамики (диаметром 80 мм), равной 1420 об/мин, что примерно соответствует линейной скорости его рабочей кромки около 8,1 м/с.
Для отверждения металлического волокна используют соосно установленный дисковому диспергатору 7 (фиг.3) с внешней его стороны, но вращающийся против часовой стрелки дисковый кристаллизатор 8 (фиг.3), выполненный с углом раскрытия конуса при вершине конической поверхности, равным 120 градусов. Устанавливают скорость вращения дискового кристаллизатора 8 (фиг.3), равной 3000 об/мин.
Над рабочими поверхностями обоих дисков 7 (фиг.3) и 8 (фиг.3) формируют с применением газовой рампы 9 (фиг.3), примыкающего к нему трубопровода 10 (фиг.3), газовых распылителя 11 (фиг.3). и форсунок 12 (фиг.3) динамический слой аргона толщиной около 180-210 мм, задавая расход аргона не менее 12 л/мин. В этом случае рабочая поверхность 13 (фиг.3) дискового кристаллизатора 8 (фиг.3) выполнена из электротехнической меди M1 с шероховатостью поверхности не более 0,5.
Затем приводят в действие узел регулирования температуры 14 (фиг.3) рабочей поверхности обоих дисков 7 (фиг.3) и 8 (фиг.3), осуществляя подачу по шлангам 15 (фиг.3) в выполненные каналы 16 (фиг.3) жидкостного охлаждения выбранного хладагента 17 (фиг.3). Расход хладагента (в данном случае была выбрана техническая с водоподготовкой воды) устанавливают не менее 5 л/с.
Замыкают цепь питания электродов 18 (фиг.3) и одновременно запускают в работу трайб-аппарат 3 (фиг.3). Непрерывно разрушаемый электрической дугой подающийся валками-приводами трайб-аппарата 3 (фиг.3) расходуемый электрод 4 (фиг.3), являющийся источником расплава металла (нерасходуемый электрод 20 выполнен из вольфрама и в силу этого не подвергается оплавлению), в процессе интенсивного оплавления создает поток дискретных частиц расплава и наряду с этим добавляет в динамический слой аргона пары металла. Со скоростью 1100 м/с поток дискретных частиц расплава металла бомбардирует поверхность вращающегося дискового диспергатора 7 (фиг.3) под углом 78-90 градусов относительно плоскости его вращения с расстояния 35 мм. При столкновении с указанной поверхностью происходит дробление дискретных частиц расплава металла на микрокапли (составляющие примерно величину 0,2-0,5 мкм) и их захват адсорбировавшимся слоем металла, сформировавшимся из образовавшейся парогазовой смеси состава “аргон-пары металла”, в которой присутствует 30% об. металлического пара. Вследствие динамического ударного взаимодействия потока дискретных частиц расплава металла с поверхностью вращающегося дискового диспергатора 7 (фиг.3) удается избежать образования на его рабочей поверхности сплошного слоя гарнисажа. Следует отметить, что действие поля механических сил вращающегося дискового диспергатора 7 (фиг.3) существенно слабее действия адгезионных сил, сил трения с поверхностью и газовой средой на захваченные рабочей поверхностью микрокапли жидкого металла, но по мере их агломерации с другими аналогичными образованиями и под воздействием парогазовой смеси, когда жидкий агломерат расплава металла достигает критического значения, поле сил вращающегося дискового диспергатора 7 (фиг.3) сбрасывает “закритический” агломерат расплава металла, по сути дела представляющий собой автокалиброванную жидкую структуру металлического волокна, на рабочую поверхность 13 (фиг.3) вращающегося дискового кристаллизатора 8 (фиг.3), а отработанная парогазовая смесь откачивается по каналу откачки 21 (фиг.3). После отверждения готовое металлическое волокно (фибра) удаляется с рабочей поверхности 13 (фиг.3) полем сил вращающегося дискового кристаллизатора 8 (фиг.3) в сборник готовой продукции.
На фиг.1 представлены результаты замера ширины металлического волокна, произведенного двумя способами, подтверждающие явление автокалибровки жидких структур металлического волокна на поверхности вращающегося дискового диспергатора 7 (фиг.3) в отсутствие стационарного сплошного слоя гарнисажа.
ПРИМЕР 2. Как и в предыдущем примере 1, в трайб-аппарат 3 (фиг.3) заряжают проволоку – это расходуемый электрод 4 (фиг.3), диаметр которого составляет 3 мм. В качестве материала проволоки выбирают латунь. Предварительно устанавливают скорость подачи латунной проволоки в зону формирования электрической дуги 5 (фиг.3), равной 0,15 м/с, и задают напряжение холостого хода источника электрического питания дуги 6 (фиг.3), равного 65 В. В этом случае на электрическом дуговом промежутке будет поддерживаться напряжение в пределах 29-31 В и ток дуги не превысит 500-520 А.
Устанавливают частоту вращения (по часовой стрелке) дискового диспергатора 7 (фиг.3), из высокотемпературной керамики диаметром 68 мм, равной 800 об/мин, что примерно соответствует линейной скорости на его рабочей кромке около 5,6 м/с.
Для отверждения металлического волокна используют установленный соосно диспергатору извне и вращающийся в том же направлении дисковый кристаллизатор 8 (фиг.3) с углом раскрытия конуса при вершине конической поверхности, равном 100 градусов. С использованием блока управления работой приводов вращения 19 (фиг.3) устанавливают скорость вращения дискового кристаллизатора 8 (фиг.3), равной 4500 об/мин.
Над рабочими поверхностями обоих дисков 7 (фиг.3) и 8 (фиг.3) посредством подачи газа из газовой рампы 9 (фиг.3) по газовому трубопроводу 10 (фиг.3) через газовый распылитель 11 (фиг.3), снабженный форсунками 12 (фиг.3), формируют динамический слой бутана толщиной не менее 150 мм, задавая расход бутана примерно 2,0 л/мин. В этом примере в качестве материала рабочей поверхности дискового кристаллизатора 13 (фиг.3) использована углеродистая конструкционная сталь марки Ст.1.
Затем приводят в действие узел регулирования температуры 14 (фиг.3) рабочей поверхности обоих дисков включением подачи по соответствующим шлангам 15 (фиг.3) в выполненные в них каналы жидкостного охлаждения 16 (фиг.3) хладагента 17 (фиг.3). Расход хладагента (в данном случае использован фреон) устанавливают не менее 12 л/с.
Замыкают цепь питания электродов 18 (фиг.3) и одновременно запускают приводы трайб-аппарата 3 (фиг.3). Непрерывно разрушаемый электрической дугой подающийся валками-приводами трайб-аппарата 3 (фиг.3) расходуемый электрод 4 (фиг.3), являющийся источником расплава металла, в процессе интенсивного оплавления создает поток дискретных частиц расплава и наряду с этим добавляет в динамический слой бутана пары металла. Нерасходуемый электрод 20 (фиг.3) выполнен из вольфрама (пруток диаметром 25 мм) и поэтому не вносит свой вклад в изменение состава динамического газового слоя. Со скоростью 500 м/с поток дискретных частиц расплава металла бомбардирует рабочую поверхность вращающегося дискового диспергатора 7 (фиг.3) под углом от 20 до 90 градусов относительно плоскости его вращения с расстояния 40 мм. При столкновении с указанной поверхностью происходит дополнительное дробление дискретных частиц расплава металла на микрокапли (составляющие примерно величину 0,08-0,12 мкм) и их захват адсорбировавшимся слоем металла, сконденсированном из ранее образовавшейся парогазовой смеси состава “бутан-пары металла”, в которой присутствует 17% об. металлического пара. Вследствие динамического ударного взаимодействия потока дискретных частиц расплава металла с рабочей поверхностью вращающегося дискового диспергатора 7 (фиг.3) исключается образование на этой поверхности сплошного слоя гарнисажа. Однако действие поля механических сил вращающегося дискового диспергатора и в этом существенно слабее действия адгезионных сил, сил трения с поверхностью и газовой средой на захваченные поверхностью диспергатора 7 (фиг.3) микрокапли жидкого металла, но по мере их агломерации с другими аналогичными образованиями и под воздействием парогазовой смеси, когда жидкий агломерат расплава металла достигает критического значения, поле сил вращающегося дискового диспергатора сбрасывает “закритический” агломерат расплава металла, по сути дела представляющий собой автокалиброванную жидкую структуру металлического волокна, на рабочую поверхность 13 (фиг.3) вращающегося дискового кристаллизатора 8 (фиг.3).
После отверждения готовое металлическое (латунное) волокно удаляется с рабочей поверхности полем сил вращающегося дискового кристаллизатора 8 (фиг.3) в сборник готовой продукции. Отработанная парогазовая смесь откачивается по каналу 21 (фиг.3) для регенерации или утилизации.
На фиг.2 представлены результаты замера длины металлического волокна, произведенного двумя способами (способом-прототипом и предлагаемым способом), служащие подтверждением наличия автокалибровки жидких структур металлического (бронзового) волокна на поверхности вращающегося дискового диспергатора 7 (фиг.3) в отсутствие стационарного сплошного слоя гарнисажа.
ПРИМЕР 3. Аналогично двум другим предыдущим примерам трайб-аппарат 3 (фиг.3) заряжают алюминиевой проволокой (представляющей собой расходуемый электрод 4 (фиг.3), диаметр которой выбирают 6 мм, затем предварительно устанавливают скорость подачи расходуемого электрода 4 (фиг.3) в зону формирования электрической дуги 5 (фиг.3), равной 0,3 м/с, и задают напряжение холостого хода источника электрического питания дуги 6 (фиг.3), равное 52 В. В этом случае на дуговом промежутке будет поддерживаться напряжение в пределах 20-22 В и ток дуги не превысит 400 А.
Устанавливают частоту вращения (по часовой стрелке) дискового диспергатора 7 (фиг.3), изготовленного из высокотемпературной керамики диаметром 40 мм, равной 1200 об/мин.
Для отверждения металлического волокна используют смонтированный соосно дисковому диспергатору 7 (фиг.3), но вращающийся против часовой стрелки, дисковый кристаллизатор 8 (фиг.3), который снабжен углом раскрытия конуса при вершине конической поверхности, равным 60 градусов. Устанавливают скорость вращения дискового кристаллизатора 8 (фиг.3) около 6000 об/мин.
Над рабочими поверхностями обоих дисков 7 (фиг.3) и 8 (фиг.3) из газовой рампы 9 (фиг.3) по газовому трубопроводу 10 (фиг.3) с использованием распылителя 11 (фиг.3), снабженного газовыми форсунками 12 (фиг.3), формируют динамический слой газовой смеси “гелий-водород” толщиной не менее 20 мм, задавая расход смеси примерно 1,5 л/мин. В этом частном случае рабочая поверхность дискового кристаллизатора 13 (фиг.3) выполнена из молибдена с шероховатостью поверхности не более 0,7.
Затем приводят в действие узел регулирования температуры 14 (фиг.3) рабочей поверхности обоих дисков 7 (фиг.3) и 8 (фиг.3) посредством включения подачи по шлангам 15 (фиг.3) в выполненные в них каналы жидкостного охлаждения 16 (фиг.3) используемого хладагента 17 (фиг.3). Расход хладагента (в дранном случае СОЖ) устанавливают не менее 3 л/с.
Замыкают цепь питания электродов 18 (фиг.3) и одновременно с этим включают приводы вращения 19 (фиг.3) трайб-аппарата 3 (фиг.3). Происходящее вследствие этого непрерывное разрушение электрической дугой подаваемого валками-приводами трайб-аппарата 3 (фиг.3) расходуемого электрода 4 (фиг.3) является источником расплава металла, в процессе интенсивного оплавления создает поток дискретных частиц расплава и наряду с этим происходит добавление в динамический слой газовой смеси “гелий-водород” пара металла. Со скоростью 650 м/с поток дискретных частиц расплава металла бомбардирует рабочую поверхность вращающегося дискового диспергатора 7 (фиг.3) под углом 4-15 градусов относительно плоскости его вращения с расстояния 150 мм. При столкновении с указанной поверхностью происходит дробление дискретных частиц расплава металла на микрокапли (составляющие величину 3-9,5 мкм) и их захват адсорбировавшимся слоем металла, сконденсированном из образовавшейся парогазовой смеси состава “гелий-водрод-пары металла”, в которой присутствует 0,1% об. металлического пара. Вследствие динамического (и точечного) ударного взаимодействия потока дискретных частиц расплава металла с поверхностью вращающегося дискового диспергатора 7 (фиг.3) удается избежать образования на его поверхности сплошного слоя гарнисажа. Следует отметить, что действие поля механических сил вращающегося дискового диспергатора 7 (фиг.3) существенно слабее действия адгезионных сил, сил трения с поверхностью и газовой средой на захваченные рабочей поверхностью диспергатора 7 (фиг.3) микрокапли жидкого металла, но по мере их агломерации с другими аналогичными образованиями и под воздействием парогазовой смеси, когда жидкий агломерат расплава металла достигает критического значения, поле сил вращающегося дискового диспергатора 7 (фиг.3) сбрасывает “закритический” агломерат расплава металла, по сути дела представляющий собой автокалиброванную жидкую структуру металлического волокна, на рабочую поверхность 13 (фиг.3) вращающегося дискового кристаллизатора 8 (фиг.3).
После отверждения готовое металлическое волокно (фибра, металлическая шерсть) удаляется с рабочей поверхности кристаллизатора 13 (фиг.3) полем сил вращающегося диска кристаллизатора 8 (фиг.3) в сборник готовой продукции.
ИСТОЧНИКИ ИНФОРМАЦИИ
1. Патент США №4262732, МКИ B 22 D 11/06, 1981 г.
2. Патент РФ №2171160, МКИ7 B 22 F 9/10, “Способ центробежного распыления металла и устройство для его осуществления”, 1999 г., авт. Полетаев А.В. и др.
Формула изобретения
1. Способ производства металлического волокна, включающий подачу металла в зону диспергирования, формирование из него в окружении динамического слоя газа дискретных частиц расплава металла, преобразование дискретных частиц расплава металла в жидкие структуры металлического волокна посредством воздействия на них полем механических сил вращающегося дискового диспергатора, охлаждение жидких структур металлического волокна до отвержденного состояния на поверхности соосно вращающегося дискового кристаллизатора, снабженного средством регулирования температуры его рабочей поверхности, и последующее удаление отвержденного металлического волокна с этой рабочей поверхности, отличающийся тем, что одновременно с формированием дискретных частиц расплава металла динамический слой газа преобразуют в парогазовую смесь, а собственно формирование дискретных частиц расплава металла производят в два этапа, на первом из которых электродуговым способом разрушают, по крайней мере, один из электродов, формируя таким образом поток дискретных частиц расплава металла в широком интервале размеров, и производят их дробление путем соударения на скорости от 500 до 1100 м/с с поверхностью вращающегося дискового диспергатора под углом от 4 до 90 градусов относительно плоскости вращения, а на втором этапе агломерируют полученные дискретные микрочастицы расплава металла до схожих размеров на поверхности вращающегося дискового диспергатора за счет одновременного воздействия на них парогазовой смесью и полем механических сил вращающегося дискового диспергатора.
2. Способ по п.1, отличающийся тем, что металл в зону диспергирования подают в твердом агрегатном состоянии.
3. Способ по п.1, отличающийся тем, что динамический слой газа преобразуют в паро-газовую смесь, содержащую от 0,1 до 30 об.% диспергируемого металла.
4. Способ по п.3, отличающийся тем, что газ парогазовой смеси выбирают из ряда инертный газ и/или восстановительный газ.
5. Способ по п.4, отличающийся тем, что восстановительный газ выбирают из ряда водород, пропан, бутан, метан.
6. Способ по п.4, отличающийся тем, что инертный газ выбирают из ряда аргон, гелий.
РИСУНКИ
MM4A – Досрочное прекращение действия патента СССР или патента Российской Федерации на изобретение из-за неуплаты в установленный срок пошлины за поддержание патента в силе
Дата прекращения действия патента: 19.08.2007
Извещение опубликовано: 10.03.2009 БИ: 07/2009
|