(21), (22) Заявка: 2004113285/15, 29.04.2004
(24) Дата начала отсчета срока действия патента:
29.04.2004
(43) Дата публикации заявки: 10.10.2005
(45) Опубликовано: 10.05.2006
(56) Список документов, цитированных в отчете о поиске:
SU 747868 A1, 15.07.1980. RU 2117687 C1, 20.08.1998. SU 91412 A1, 01.01.1951. US 5961946 А, 05.10.1990. JP 08-159430 А, 21.06.1996. JP 56-041293 А, 17.04.1981. SU 1201294 A1, 30.12.1985. SU 1703673 A1, 07.01.1992. RU 2174911 C1, 20.10.2001. КАСАТКИН А.Г. Основные процессы и аппараты химической технологии. – М.: Госхимиздат, 1961, с.338-340, 362-370.
Адрес для переписки:
121165, Москва, Г-165, а/я 15, ООО “ППФ-ЮСТИС”, пат. пов. А.Б. Груниной, рег. № 401, Л.С. Пилишкиной, рег. № 895
|
(72) Автор(ы):
Иваненко Владимир Сергеевич (RU), Митропольский Павел Владимирович (RU), Шелепугин Дмитрий Николаевич (RU)
(73) Патентообладатель(и):
Закрытое акционерное общество НПФ “ЭКОТЕХ” (RU)
|
(54) СПОСОБ ПОЛУЧЕНИЯ САЖИ ИЗ РЕЗИНОВЫХ ОТХОДОВ
(57) Реферат:
Изобретение может быть использовано в химической промышленности. Резиновые отходы подвергают термическому разложению в реакторе в парогазовой среде. Продукты разложения разделяют на парогазовые продукты и твердый углеродный остаток, из которого выделяют металл путем магнитной сепарации, а затем измельчают. Парогазовые продукты после отделения твердого углеродного остатка конденсируют, выделяют масло, которое подвергают термическому разложению на сажу и газы при 900-2000°С. Газы термического разложения масла сжигают, и продукты сгорания используют в качестве теплоносителя для внешнего обогрева реактора при разложении резиновых отходов. Парогазовые продукты после выделения масла сжигают совместно с измельченным углеродным остатком при коэффициенте избытка воздуха 0,4-0,9, Продукты сгорания фильтруют, выделяют сажу. Снижается энергоемкость процесса, обеспечивается полная переработка отходов, улучшается экология за счет уменьшения образования токсичных соединений. 3 з.п. ф-лы, 1 ил.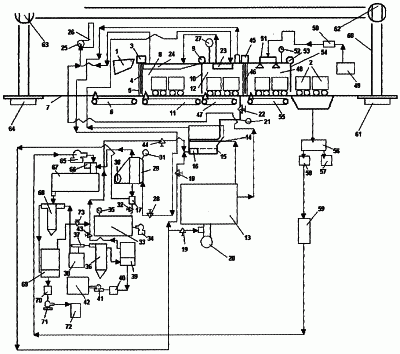
Изобретение относится к технологии переработки отходов и может быть применено в химической промышленности для производства сажи, а также в резиновой промышленности для получения ингредиентов резиновых смесей.
Известен способ переработки отходов путем пиролиза и разделения продуктов пиролиза на твердую, жидкую и газообразную фазы. Твердую фазу обрабатывают водяным паром с получением окиси углерода и водорода, а газообразную фазу частично отводят для поддержания процесса пиролиза (см. Алексеев Г.М., Петров В.Н., Шпильфогель П.В. Индустриальные методы санитарной очистки городов. Л.: Стройиздат, 1983, с.14-15).
Недостатками данного способа являются высокий расход энергии на переработку, что обусловлено высокой температурой процесса (1500°С), большие выбросы вредных газообразных веществ в окружающую среду.
Известен способ переработки резиновых отходов, включающий их термическое разложение в парогазовой среде, разделение продуктов разложения на твердые и газообразные, подачу твердых продуктов разложения в печь активации при одновременной подаче в печь активации водяного пара в количестве 0,8-1,6 кг на 1 кг твердых продуктов разложения, вывод из печи активации газообразной смеси при массовом соотношении в смеси (3-0,6):1 водяного пара и газов активации и использование их в качестве парогазовой среды для разложения отходов, подачу в печь активации одновременно с подачей твердых продуктов разложения и водяного пара резиновых отходов в количестве 0,05-0,20 кг отходов на 1 кг твердых продуктов (см. патент РФ №2174911, опубл. БИ, 2001, №29).
К недостаткам данного способа следует отнести высокую энергоемкость процесса и большие выбросы из печи активации в окружающую среду вредных продуктов сгорания.
Известен способ переработки резиновых отходов, заключающийся в термическом разложении отходов в две стадии, на первой из которых отходы разлагают при температурах 400-500°С до выделения летучих продуктов и углеродного остатка, затем летучие продукты разлагают во втором реакторе до дисперсного углерода (сажи) и газов (см. Богданов И.Ф. и др. Получение сажи из изношенных резиновых изделий. “Производство шин РТИ и АТИ”, ЦНИИТЭ-нефтехим, М., 1974, №8, с.25).
К недостаткам данного способа следует отнести высокую энергоемкость процесса, большие выбросы продуктов сгорания в окружающую среду, потери ценного сырья – дисперсного углерода (сажи).
Наиболее близким к предлагаемому изобретению является принятый нами за прототип способ получения сажи (авт. свид. СССР №747868, опубл. БИ, 1980, №26).
Указанный способ включает пиролиз твердого углеродсодержащего сырья – отходов полимерных композиций при 400-1500°С с образованием твердого углеродного остатка и выделением парогазовых продуктов и последующее измельчение углеродного остатка в потоке парогазовых продуктов при 350-400°С, пиролиз отходов ведут парогазовой смесью, в качестве которой используют парогазовую смесь, содержащую, об.%:
Перегретый водяной пар |
35-50 |
Двуокись углерода |
5-10 |
Окись углерода |
1-3 |
Кислород |
0,1-2,0 |
Азот |
Остальное |
Парогазовые продукты пиролиза отходов подвергают термическому разложению при 1400-1500°С.
К недостаткам данного способа следует отнести большой расход энергии, обусловленный высокой температурой пиролиза (до 1500°С), а также большие выбросы вредных веществ в окружающую среду при термическом разложении парогазовых продуктов.
Задачей предлагаемого изобретения является снижение энергоемкости и уменьшение количества вредных выбросов в окружающую среду в процессе получения сажи из резиновых отходов.
Поставленная задача решается тем, что в способе получения сажи из резиновых отходов, включающем их термическое разложение в реакторе в парогазовой среде, разделение продуктов разложения на парогазовые продукты и твердый углеродный остаток, измельчение углеродного остатка, согласно изобретению из парогазовых продуктов конденсации выделяют масло и подвергают его термическому разложению предпочтительно при Т=900-2000°С на сажу и газы, а парогазовые продукты после выделения масла сжигают совместно с измельченным углеродным остатком предпочтительно при коэффициенте избытка воздуха 0,4-0,9 и путем фильтрации из продуктов сгорания выделяют сажу. Предварительно перед измельчением из углеродного остатка путем магнитной сепарации выделяют металл. Газы термического разложения масла сжигают и продукты сгорания используют в качестве теплоносителя для внешнего обогрева реактора.
Предварительное выделение масла из парогазовых продуктов позволяет получить сырье, которое отвечает всем требованиям, необходимым для производства высококачественной сажи. Выделенное из летучих продуктов масло содержит большое количество (60-80 мас.%) ароматических углеводородов и поэтому имеет низкую удельную теплоту разложения, вследствие чего снижаются (в сравнении с прототипом) энергозатраты на процесс получения сажи и повышается выход целевого продукта (сажи).
При термическом разложении масла в диапазоне температур Т=900-2000°С образуются сажа и горючие газы, количество которых достигает 50-70 масс.% от количества масла. Для снижения удельных энергозатрат на процесс получения сажи и предотвращения выбросов вредных веществ в окружающую среду горючие газы сжигают и продукты сгорания используют для обогрева реактора, в котором осуществляют термическое разложение резиновых отходов на парогазовые продукты и углеродный остаток.
Температурный диапазон Т=900-2000°С термического разложения масла обусловлен тем, что при температуре ниже 900°С масло практически не разлагается, т.е. при снижении температуры процесса разложения ниже 900°С резко снижается скорость термического разложения масла, а при увеличении температуры выше Т=2000°С резко увеличивается количество газообразных продуктов разложения масла, в результате чего снижается выход сажи и увеличивается количество газа, который необходимо сжигать, что приводит к увеличению выбрасываемых в окружающую среду продуктов сгорания газов термического разложения масла.
Парогазовые продукты после выделения масла содержат горючие газы и водяной пар и имеют удельную теплоту сгорания в пределах (зависит от вида резиновых отходов, количества выделенного масла и содержания водяного пара) от 4 до 30 МДж/кг. Смешивание летучих продуктов с углеродным остатком (имеет удельную теплоту сгорания в пределах от 15 до 50 МДж/кг) и сжигание этой смеси при недостатке воздуха в циклонном реакторе получения сажи позволяет удалить из углеродного остатка соединения серы и остаточные летучие продукты, получить качественную сажу.
При этом в результате реакций взаимодействия водяного пара, который содержится в парогазовых продуктах, с углеродом остатка происходит развитие удельной поверхности, в результате чего улучшаются качественные показатели получаемого продукта (сажи).
При сжигании смеси парогазовые продукты разложения – углеродный остаток необходимо подавать воздух в количестве 0,4-0,9 от теоретически необходимого для данной смеси, которое определяется стандартными методами (предварительным расчетом) на основании удельной теплоты сгорания смеси и содержания горючих элементов: углерода, водорода, серы.
Снижение количества воздуха ниже 0,4 от теоретически необходимого приведет к невозможности зажигания смеси парогазовые продукты разложения – углеродный остаток и остановке процесса выделения сажи из углеродного остатка.
Повышение количества воздуха в смеси выше 0,9 от теоретически необходимого приведет к резкому росту количества полностью сгораемой смеси и резкому снижению образования продукта неполного сгорания смеси – сажи, т.е. нарушится процесс выделения сажи и увеличится количество выделяющейся при сгорании теплоты, которую необходимо утилизировать, в противном случае система сжигания смеси перегреется и работоспособность ее нарушится.
На чертеже приведена схема установки, на которой реализуют способ получения сажи из резиновых отходов.
Установка содержит бункер-накопитель 1, вагонетки 2, привод 3 смещения заслонки, заслонку 4, установленную в шлюзовом затворе 5, толкатель 6 для перемещения вагонеток по рельсовому пути 7, камеру 8 загрузки, снабженную рубашкой 24, поворотный механизм 9 для поднятия поворотной заслонки 10, толкатель 11 для подачи вагонеток в камеру 12 термического разложения (реактор), парогенератор 13, оборудованный горелкой 20 с краном подачи топлива 19, пароперегреватель 14, установленный в топке 15; горелку 16, подключенную к емкости 17 через кран 18, датчик 21 температуры перегрева пара, кран 22 подачи пара в камеру 12 термического разложения, нагревательную рубашку 23 камеры 12 термического разложения, дымосос 25, подключенный к дымовой трубе 26, датчик 27 температуры, установленный в камере 12 термического разложения, кран 28 для регулирования вывода парогазовых продуктов разложения из камеры 12 термического разложения в теплообменник 29, воздуходувку 30, подключенную к теплообменнику 29, датчик 31 температуры, установленный в теплообменнике 29, кран 32 для регулирования количества подачи топлива в циклонный реактор 33, вентилятор 34, подключенный к циклонному реактору 33, датчик 35 температуры, установленный в реакторе 33, холодильник 36, оборудованный насосом 37 для подачи воды, емкость 38 с водой, фильтр 39 сажи, подключенный к микроизмельчителю углеродного остатка 40, вентилятор 41 для пневмотранспорта измельченного углеродного остатка, подключенный к накопителю 42 углерода, краны 43 и 44, подключенные к фильтру 39 и топке 15, привод 45 поворотной заслонки 46, толкатель 47, установленный в камере 12 термического разложения, камеру 48 охлаждения, емкость 19 с водой, оборудованную насосом 50 с распылителем 51 воды; датчик 52 температуры охлаждения, установленный в камере 48 охлаждения, поворотный механизм 53 с заслонкой 54, толкатель 55, установленный в камере 48 охлаждения, сепаратор 56 твердого остатка, снабженный накопителем 57 для металла и мельницей 58 для измельчения углеродного остатка, накопитель 59 измельченного углеродного остатка; рельсовый путь 60, оборудованный поворотными платформами 61, 62, 63, 64 для возврата вагонеток к месту загрузки, воздуходувку 65 с эжектором 66, подключенным к циклонному реактору 67, холодильник 68, подключенный через фильтр 69 к микроизмельчителю 70 сажи, воздуходувку 71, подключенную к микроизмельчителю 70 и накопителю 72 сажи, кран 73 регулировки подачи газов, подключенный к фильтру 69 и топке 15.
Согласно изобретению, получение сажи из резиновых отходов осуществляют следующим образом.
Из бункера-накопителя 1 в вагонетки 2 загружают разрезанные на куски резиновые отходы. С помощью привода 3 смещают в сторону заслонку 4 шлюзового затвора 5 и толкателем 6 по рельсовому пути 7 заталкивают вагонетки 2 в камеру 8 загрузки, после чего заслонкой 4 закрывают вход в камеру 8 загрузки.
Далее с помощью поворотного механизма 9 поднимают заслонку 10 камеры 8 загрузки и с помощью толкателя 11 по рельсовому пути заталкивают вагонетки 2 в камеру 12 термического разложения. Опускают заслонку 10.
После установки вагонеток 2 в камере 12 термического разложения от парогенератора 13 в пароперегреватель 14, размещенный в топке 15, подают водяной пар. Одновременно в горелку 16 топки 15 из емкости 17 через кран 18 подают жидкое топливо (масло) и сжигают его.
Жидкое топливо также подают через кран 19 в горелку 20 парогенератора. Водяной пар, проходя через пароперегреватель 14, нагревается до температуры 600-750°С (температуру нагрева пара контролируют по показаниям датчика 21).
Перегретый водяной пар через кран 22 подают в камеру 12 термического разложения. Продукты сгорания топлива в топке 15 при температуре 900-1100°С подают в рубашку 23 камеры 12 термического разложения и далее в рубашку 24 камеры 8 загрузки. Из рубашки 24 камеры 8 загрузки продукты сгорания с помощью дымососа 25 выводят в дымовую трубу 26.
Низкотемпературные продукты сгорания (Т=200-250°С) топлива из парогенератора 13 подают в дымовую трубу 26.
Проходя через рубашку 23 камеры 12 термического разложения, продукты сгорания топлива нагревают стенки камеры 12, от которых тепло передается резиновым отходам, которые при нагреве до 270-280°С начинают претерпевать термическое разложение на парогазовые продукты и углеродный остаток. Температуру в камере 12 контролируют по показаниям датчика 27.
Парогазовые продукты через кран 28 поступают в теплообменник 29. В теплообменнике 29 в результате теплообмена с потоком воздуха, продуваемым с помощью воздуходувки 30, происходит охлаждение парогазовых продуктов до температуры 200°С, что контролируют по показаниям датчика температуры 31.
Часть парогазовых продуктов конденсируется и поступает в емкость 17. Из емкости 17 через кран 32 конденсат (масло) подают в циклонный реактор 33, куда одновременно с помощью вентилятора 34 нагнетают воздух. В циклонном реакторе 33 сжигают парогазовые продукты при коэффициенте избытка воздуха 0,4-0,9 и температуре 900-2000°С. Тепло, выделившееся при сгорании части парогазовых продуктов, вызывает термический распад оставшихся парогазовых продуктов с сажи. Температуру в реакторе 33 контролируют по показаниям датчика 35 и регулировкой подачи воздуха от вентилятора 34 (увеличивают подачу при снижении температуры и уменьшают подачу воздуха при росте температуры) устанавливают температуру в диапазоне 900-2000°С. Поток продуктов сгорания и сажи из реактора 33 выводят в холодильник 36, куда с помощью насоса 37 из емкости 38 распыляют воду, в результате чего температура продуктов сгорания и сажи снижается. Охлажденную смесь из холодильника 36 подают в фильтр 39, где из газового потока выделяют сажу, которую подают в микроизмельчитель 40, а затем пневмотранспортом с помощью вентилятора 41 сажу подают в накопитель 42.
Очищенные в фильтре от сажи газы содержат горючие составляющие и поэтому эти газы из фильтра через кран 43 и кран 44 подают в топку 15 и сжигают. Сжигание газов в топке позволяет полезно использовать теплоту сгорания газов и предотвратить их выброс в окружающую среду.
Углеродный остаток разложения резиновых отходов выводят из камеры 12 термического разложения. Для этого с помощью привода 45 поднимают заслонку 46 и с помощью толкателя 47 по рельсовому пути вагонетки 2 выводят в камеру 48 охлаждения, после чего заслонку 46 опускают. Из емкости 49 с водой насосом 50 в распылитель 51 подают воду. Вода распыляется над вагонетками 2 и охлаждает углеродный остаток до температуры 120-150°С. Температуру охлаждения контролируют по показаниям датчика 52. После охлаждения углеродный остаток в вагонетках выводят из камеры 48 охлаждения.
Для этого с помощью поворотного механизма 53 поднимают заслонку 54 камеры 48 охлаждения, включают толкатель 55 и перемещают вагонетки 2 к месту выгрузки.
Опрокидывают вагонетки 2 (поворачивают укрепленный на горизонтальной оси кузов вагонетки), и углеродный остаток выгружают в сепаратор 56, где отделяют металл от самого углеродного остатка. Металл подают в накопитель 57, а углеродный остаток подают в мельницу 58, размалывают и выгружают в накопитель 59. Вагонетки 2 после разгрузки по рельсовому пути 60 через поворотные платформы 61, 62, 63 и 64 перемещают к бункеру-накопителю 1, загружают и подают в камеру 8 загрузки.
Из накопителя 59 пневмотранспортом с помощью воздуходувки 65 углеродный остаток подают через эжектор 66 в циклонный реактор 67.
Одновременно из теплообменника 29 парогазовые продукты после отделения масла подают в реактор 67 и смесь (парогазовые продукты – углеродный остаток) сжигают при избытке воздуха 0,4-0,9 от теоретически необходимого, т.е. того количества воздуха, которое необходимо для полного сгорания данной смеси. Количество воздуха, подаваемого на сжигание смеси, регулируют с помощью эжектора 66.
В реакторе 67 протекает неполное сгорание смеси, в результате чего за счет выделяющейся теплоты происходит термическое разложение углеводородов, содержащихся в парогазовых продуктах, выделяется сажа и газы.
Углеродная составляющая твердого остатка частично сгорает, а частично нагревается до температуры 1000-1900°С, и при этом из углеродного остатка удаляются сернистые соединения и развивается поверхность остатка за счет реагирования углерода с водяным паром, который содержится в парогазовых продуктах. Таким образом, из углеродного остатка получают сажу. Из реактора 67 продукты сгорания в смеси с сажей подают в холодильник 68, куда одновременно из емкости 38 подают воду и распыляют ее.
Охлажденную смесь далее подают в фильтр 69, где путем фильтрации отделяют сажу и подают ее в микроизмельчитель 70, из которого пневмотранспортом с помощью воздуходувки 71 сажу загружают в накопитель 72.
Очищенные от сажи газы (парогазовая смесь) через кран 73 и 44 подают в топку и сжигают.
Изобретение иллюстрируется следующими примерами.
Пример 1
Из бункера-накопителя 1 в вагонетки 2 загружают разрезанные на куски резиновые отходы, например изношенные шины в количестве 2000 кг (по 1000 кг в каждую вагонетку). С помощью привода 3 смещают в сторону заслонку 4 шлюзового затвора 5 и толкателем 6 по рельсовому пути 7 заталкивают вагонетки 2 в камеру 8 загрузки, после чего заслонкой 4 закрывают вход в камеру 8 загрузки. Далее с помощью поворотного механизма 9 поднимают заслонку 10 камеры 8 загрузки и с помощью толкателя 11 по рельсовому пути 7 заталкивают вагонетки 2 в камеру 12 термического разложения. Опускают заслонку 10. После установки вагонеток 2 в камере 12 термического разложения от парогенератора 13 в пароперегреватель 14, размещенный в топке 15, подают водяной пар (Т=140°С) с расходом 710,2 кг/ч. Одновременно в горелку 16 топки 15 из емкости 17 через кран 18 подают жидкое топливо (масло) с расходом 120 кг/ч и сжигают его.
Жидкое топливо также подают через кран 19 в горелку 20 парогенератора.
Водяной пар, проходя через пароперегреватель 14, нагревается до температуры 700°С (температуру нагрева пара контролируют по показаниям датчика 21).
Перегретый водяной пар через кран 22 подают в камеру 12 термического разложения. Продукты сгорания топлива в топке 15 при температуре 1100°С подают в рубашку 23 камеры 12 термического разложения в количестве 1540 кг/ч (при сгорании 1 кг топлива образуется 12,8 кг продуктов сгорания). Проходя через рубашку камеры термического разложения продукты сгорания охлаждаются до температуры 600°С. При этом количество тепла, передаваемого от продуктов сгорания в камеру термического разложения, составит величину:
Qпрод.сгорания=Mпрод.сгоранияCпрод.сгорания(T2-T1)=1540 кг/ч·1,34 кДж/кгС(1100°С-600°С)=1031800 кДж/ч,
где Мпрод.сгорания – количество продуктов сгорания, кг/ч;
Спрод.сгорания – удельная теплоемкость продуктов сгорания, кДж/кгС;
T1 и Т2 – температура входа продуктов сгорания в рубашку 23 камеры 12 термического разложения и температура выхода их из рубашки 23.
Далее продукты сгорания с Т=600°С из рубашки 23 камеры 12 термического разложения подают в рубашку 24 камеры 8 загрузки. Проходя через рубашку 24 камеры загрузки, продукты сгорания охлаждаются от Т=600°С до Т=250°С. При этом тепло охлаждения расходуется на нагрев камеры 8 загрузки, теплопотери и нагрев вагонеток 2 с отходами. Количество тепла охлаждения продуктов сгорания в нашем случае будет равно:
Qпрод.сгорания2=Мпрод.сгоранияCпрод.сгорания(T3-T4)=1540 кг/ч·1,34 кДж/кгС(600°С-250°С)=722260 кДж/ч,
где Т3-Т4 – температура входа продуктов сгорания в рубашку 24 камеры 8 загрузки и температуры выхода их из рубашки 24.
Пусть в установившемся режиме, когда камера 8 загрузки и камера 12 термического разложения нагреты до температуры 250°С и 600°С соответственно, величина теплопотерь в камере 8 загрузки равна 40%, а в камере 12 термического разложения равна 20% от количества подводимого в камеру тепла. В этом случае на нагрев вагонеток с отходами будет расходоваться за 1 ч следующее количество тепла продуктов сгорания:
1. В камере загрузки: (722260 кДж/ч)·0,6=433356 кДж/ч=Q1.
2. В камере термического разложения: (1031800 кДж/ч)·0,8=825440 кДж/ч=Q2.
Пусть вес каждой вагонетки 2 с отходами составляет 2000 кг (1000 кг весит сама тележка и 1000 кг весят отходы). Удельная теплоемкость резиновых отходов Ср.отходов=1,4 кДж/кгС. Удельная теплоемкость материала вагонеток Ср.вагонеток=0,5 кДж/кгС. Начальная температура вагонеток с отходами Т=20°С. Вагонетки с отходами находятся в камере 8 загрузки 120 мин (2 ч). В этом случае вагонетки с отходами нагреются до температуры:
Tнагр1=2Q1/(Cp.отходовMотходов+Ср.вагонетокMвагонеток)+20°C=(2·433356 кДж/ч)/{(1,4 кДж/кгС·2000 кг+0,5 кДж/кгС·2000 кг)}+20°С=248°С,
где Мвагонеток – масса вагонеток;
Q1 – количество тепла, подводимого в камеру 8 загрузки от продуктов сгорания в течение 1 ч;
Q2 – количество тепла, подводимого в камеру 12 термического разложения от продуктов сгорания в течение 1 ч.
Из рубашки 24 камеры 8 загрузки продукты сгорания с помощью дымососа 25 выводят в дымовую трубу 26.
Низкотемпературные продукты сгорания (Т=200-250°С) топлива из парогенератора 13 подают в дымовую трубу 26.
Суммарное количество тепла, необходимого для термического разложения отходов в камере 12, определяется следующим образом:
Qобщ=Qнагр+Qразд+Qпотерь,
т.е. Qобщ=1,2{(Cp.отходовMотходов(T2-T1)+Cр.вагонетокMвагонеток(T2-T1)+qMотходов)}.
Qобщ=1,2{(1,4 кДж/кг·2000 кг(450°С-248°С)+0,5 кДж/кгС·2000 кг(450°С-248°С)+600 кДж/кг 2000 кг)}=2361120 кДж,
где Qобщ – общее количество необходимого для термического разложения тепла;
Qнагр – тепло нагревания отходов и вагонеток до 450°С;
Qразд – тепло, затрачиваемое на разложение отходов;
Qпотерь – тепловые потери, составляющие 20% от тепла нагревания и разложения;
q – удельное тепло разложения, составляющее для резиновых отходов 600 кДж/кг;
Мотходов – масса отходов;
T1 и T2 – начальная и конечная температура вагонеток с отходами.
Так как часть тепла (за 2 ч будет подведено 1650880 кДж) подводится через стенки реактора, то количество тепла (2361120-1650880) кДж=710240 кДж необходимо подвести с перегретым паром. Следовательно, расход перегретого пара Gпара(Твхода=700°С, а Твыхода=450°С, Спара=2 кДж/кгС) составит величину:
Gпара={(710240 кДж)/2 кДж/кгС(700°С-450°С)}/2 ч=710,2 кг/ч.
Проходя через рубашку 23 камеры 12 термического разложения, продукты сгорания топлива нагревают стенки камеры 12, от которых тепло передается резиновым отходам, которые при нагреве до 280°С начинают претерпевать термическое разложение на парогазовые продукты (50% от массы резиновых отходов, т.е. в нашем случае выход парогазовых продуктов составит 1000 кг) и углеродный остаток. Температуру в камере 12 контролируют по показаниям датчика 27.
Парогазовые продукты через кран 28 поступают в теплообменник 29. В теплообменнике 29 в результате теплообмена с потоком воздуха, продуваемым с помощью воздуходувки 30, происходит охлаждение парогазовых продуктов до температуры 200°С, что контролируют по показаниям датчика 31 температуры. Часть парогазовых продуктов конденсируется и поступает в емкость 17. Пусть в нашем случае конденсируется 75% парогазовых продуктов, т.е. 0,75·500 кг/ч=375 кг/ч (процесс конденсации парогазовых продуктов протекает 2 ч). Теплота конденсации данных продуктов составляет 300 кДж/кг, а теплоемкость их в газообразном состоянии 3 кДж/кгС.
В этом случае в теплообменнике 29 в результате охлаждения и конденсации части парогазовых продуктов выделится следующее количество тепла:
Q=Cп.пMл.п(Tвх.п.п+Tвых.п.п)+qконд.п.пMп.п=3 кДж/кгС·375 кг/ч(450-200)°С+300 кДж/кг·375 кг/ч=393750 кДж/ч,
где Сп.п – удельная теплоемкость парогазовых продуктов;
Мл.п – масса парогазовых продуктов;
Твх.п.п и Твых.п.п – температура входа парогазовых продуктов в теплообменник и температуры выхода их из теплообменника;
qконд.п.п – удельная теплота конденсации парогазовых продуктов.
Данное количество тепла в теплообменнике 21 передается охлаждающему воздуху, который используют для обогрева помещения, где находится установка.
Из емкости 17 через кран 32 конденсат (масло) подают в циклонный реактор 33 с расходом 375 кг/ч-70 кг/ч-69 кг/ч=236 кг/ч, куда одновременно с помощью вентилятора 34 нагнетают воздух. 70 кг/ч масла сжигают в топке 15. Масло в количестве 69 кг/ч сжигают в парогенераторе для получения 710,2 кг/ч рабочего водяного пара.
В циклонном реакторе 33 сжигают конденсат (масло) при недостатке воздуха и температуре 900°С. Тепло, выделившееся при сгорании части масла, вызывает термический распад оставшегося масла с образованием сажи и газов (горючих газов с теплотой сгорания 24 МДж/кг).
В нашем случае часть масла распадается с образованием сажи (образуется 40% от массы масла, т.е. 236 кг/ч·0,4=94,4 кг/ч), часть масла сгорает (25% от массы масла, т.е. 236 кг/ч·0,25=59 кг/ч), остальная часть масла (35% от массы масла, т.е. 236 кг/ч. 0,35=82,6 кг) термически разлагается с образованием горючих газов с теплотой сгорания 24 МДж/кг.
Температуру в реакторе 33 контролируют по показаниям датчика 35 и регулировкой подачи воздуха от вентилятора 34 (увеличивают подачу при снижении температуры и уменьшают подачу воздуха при росте температуры) устанавливают температуру 900°С. Поток продуктов сгорания и сажи из реактора 33 выводят в холодильник 36, куда с помощью насоса 37 из емкости 38 распыляют воду, в результате чего температура продуктов сгорания и дисперсного углерода снижается до Т=150°С. Охлажденную смесь из холодильника 36 подают в фильтр 39, где из газового потока выделяют сажу в количестве 94,4 кг/ч, которую подают в микроизмельчитель 40, а затем пневмотранспортом с помощью вентилятора 41 сажу подают в накопитель 42.
Очищенные в фильтре от сажи газы в количестве 82,6 кг/ч+755,2 кг/ч (продукты сгорания 59 кг/ч масла)=837,8 кг/ч из фильтра через кран 36 и кран 13 подают в топку 15 и сжигают. Сжигание газов в топке позволяет полезно использовать теплоту сгорания газов и предотвратить их выброс в окружающую среду.
Поскольку теплота сгорания газов составляет 2,4 МДж/кг и сжигают их 837,8 кг/ч (это эквивалентно по теплоте сгорания сжиганию 50 кг масла с удельной теплотой сгорания 40 МДж/кг), то количество сжигаемого масла в топке 15 снижают на 50 кг/ч и устанавливают равным (120 кг/ч-50 кг/ч)=70 кг/ч. Углеродный остаток разложения резиновых отходов в количестве 1000 кг выводят из камеры 12 термического разложения. Для этого с помощью привода 45 поднимают заслонку 46 и с помощью толкателя 47 по рельсовому пути вагонетки 2 выводят в камеру 48 охлаждения, после чего заслонку 46 опускают. Из емкости 49 с водой насосом 50 в распылитель 51 подают воду. Вода распыляется над вагонетками 2 и охлаждает углеродный остаток и вагонетки до температуры 120°С. Температуру охлаждения контролируют по показаниям датчика 52.
В результате охлаждения углеродного остатка и вагонеток от Т=450°С до Т=120°С в охладителе снимается следующее количество тепла:
Qохладителя=Cy.oMу.о(450°C-120°C)+Cр.вагонетокMвагонеток(450°C-120°C)=0,8 кДж/кгС·1000 кг/ч·330°С+0,5 кДж/кгС 2000 кг·330°С=594000 кДж/ч.
где Qохладителя – снимаемое в охладителе тепло;
Су.о – теплоемкость углеродного остатка;
Му.о – масса углеродного остатка.
Известно, что на нагрев и испарение 1 кг воды (начальная температура воды равна 20°С) необходимо следующее количество тепла:
Qи.воды=Ср.воды(100°С-20°С)Мводы+rфМводы=4,18 кДж/кгС·80°С·1 кг+2250 кДж/кг·1 кг=2584,4 кДж.
где Qи.воды – количество тепла, необходимое для испарения 1 кг воды;
Мводы – масса воды;
rф – теплота испарения воды;
Ср.воды – удельная теплоемкость воды.
Таким образом, для охлаждения вагонеток с углеродистым остатком необходимо следующее количество воды:
Мводы=Qохладителя/Ои.воды=(594000 кДж/ч)/(2584,4 кДж/кг)=229,8 кг/ч.
После охлаждения углеродный остаток в вагонетках выводят из камеры 48 охлаждения. Для этого с помощью поворотного механизма 53 поднимают заслонку 54, включают толкатель 55 и перемещают вагонетки 2 к месту выгрузки.
Опрокидывают вагонетки 2, и углеродный остаток выгружают в сепаратор 56, где отделяют металл от самого углеродного остатка. Металл 200 кг подают в накопитель 57, а углеродный остаток 800 кг подают в мельницу 58, размалывают и выгружают в накопитель 59. Вагонетки 2 после разгрузки по рельсовому пути 60 через поворотные платформы 61, 62, 63 и 64 перемещают к бункеру-накопителю 1, загружают и подают в камеру 8 загрузки. Из накопителя 59 пневмотранспортом с помощью воздуходувки 65 углеродный остаток в количестве 400 кг/ч подают через эжектор 66 в циклонный реактор 67.
Одновременно из теплообменника 29 летучие продукты разложения резины (после отделении 375 кг/ч масла) в количестве 125 кг/ч и 710,2 кг/ч водяной пар подают в реактор 67 и смесь (летучие продукты – углеродный остаток) сжигают при избытке воздуха 0,4 от теоретически необходимого, т.е. того количества воздуха, которое необходимо для полного сгорания данной смеси.
В нашем случае теоретически необходимое количество воздуха для сжигания 125 кг/ч продуктов разложения составляет 1600 кг/ч (12,8 кг воздуха на 1 кг продуктов разложения), а для сжигания 400 кг/ч углеродного остатка теоретически необходимое количество воздуха составляет 3200 кг/ч (8 кг воздуха на 1 кг углеродного остатка). Таким образом, для полного сжигания смеси необходимо 3200 кг/ч+1600 кг/ч=4800 кг/ч, а сжигание при избытке воздуха 0,4 потребует 4800 кг/ч·0,4=1920 кг/ч воздуха.
Количество воздуха, подаваемого на сжигание смеси, регулируют с помощью эжектора 66 и устанавливают равным 1920 кг /ч.
В реакторе 67 протекает неполное сгорание смеси, в результате чего за счет выделяющейся теплоты происходит термическое разложение углеводородов, содержащихся в парогазовых продуктах, выделяется сажа в количестве 40% от массы, т.е. 125 кг/ч·0,4=50 кг/ч и газы в количестве 35% от массы, т.е. 125 кг/ч·0,35=43,75 кг/ч. Часть углеводородов парогазовых продуктов сгорает, т.е. 25% от массы (125 кг/ч·0,25=31,25 кг /ч сгорает).
Углерод твердого остатка частично сгорает в количестве 400 кг/ч·0,3=120 кг/ч, а частично нагревается до температуры 900°С, и при этом из углеродного остатка удаляются сернистые соединения и развивается удельная поверхность за счет реагирования углерода с водяным паром, который содержится в парогазовых продуктах. Таким образом, образуется из углеродного остатка сажа в количестве 400 кг/ч·0,6=240 кг/ч, а 40 кг/ч углеродного остатка реагирует с водяным паром (расходуется 27 кг/ч водяного пара) с образованием горючих газов, в состав которых входит оксид углерода, водород, сероводород и небольшие количества углеводородов метанового ряда.
Из реактора 67 продукты сгорания в смеси с сажей подают в холодильник 68, куда одновременно из емкости 38 подают воду и распыляют ее. Охлажденную смесь далее подают в фильтр 69, где путем фильтрации отделяют сажу и подают ее в микроизмельчитель 70, из которого пневмотранспортом с помощью воздуходувки 71 сажу в количестве 50 кг/ч+240 кг/ч=290 кг/ч загружают в накопитель 72.
Очищенные от сажи газы в количестве (710,2-27)=683,2 кг/ч (водяной пар)+1920 кг/ч (воздух)+67 кг/ч (летучие продукты)=2670,2 кг/ч (парогазовая смесь) через кран 73 и 44 подают в топку 15 и сжигают. Удельная теплота сгорания такой парогазовой смеси составит величину 1 МДж/кг и поэтому сжигание 2670,2 кг/ч парогазовой смеси эквивалентно сжиганию 40 кг/ч масла. Поэтому количество подаваемого в топку 15 масла из емкости 17 снижают с 70 кг/ч до 30 кг/ч.
Таким образом, при переработке по данному способу резиновых отходов в количестве 1000 кг/ч получают 240 кг/ч+50 кг/ч+94,4 кг/ч=384,4 кг/ч сажи, 70 кг/ч-25 кг/ч=45 кг/ч масла. При этом энергообеспечение всего процесса переработки осуществляется за счет применения в качестве энергоресурсов части резиновых отходов – 1000 кг/ч-384,4 кг/ч-40 кг/ч-100 кг/ч=475,6 кг/ч, где 100 кг/ч – металл, содержащийся в отходах.
За счет использования части резиновых отходов для энергообеспечения процесса переработки достигается эффект снижения энергоемкости, так как в сравнении с известными технологиями получения сажи из резиновых отходов отпадает необходимость в дополнительном топливе. Сжигание части резиновых отходов (475,6 кг/ч) в газифицированном виде и в виде измельченной углеродной составляющей обеспечивает более полное сгорание и снижение образования токсичных соединений в сравнении с технологиями прямого сжигания резиновых отходов.
Пример 2
Из бункера-накопителя 1 в вагонетки 2 загружают разрезанные на куски резиновые отходы, например обрезиненный металлический лом, в количестве 1000 кг (по 500 кг в каждую вагонетку). С помощью привода 3 смещают в сторону заслонку 4 шлюзового затвора 5 и толкателем 6 по рельсовому пути 7 заталкивают вагонетки 2 в камеру 8 загрузки, после чего заслонкой 4 закрывают вход в камеру 8 загрузки. Далее с помощью поворотного механизма 9 поднимают заслонку 10 камеры 8 загрузки и с помощью толкателя 11 по рельсовому пути заталкивают вагонетки 2 в камеру 12 термического разложения. Опускают заслонку 10.
После установки вагонеток 2 в камере 12 термического разложения от парогенератора 13 в пароперегреватель 14, размещенный в топке 15, подают водяной пар (Т=140°С) с расходом 279,2 кг/ч. Одновременно в горелку 16 топки 15 из емкости 17 через кран 18 подают жидкое топливо (масло) с расходом 80 кг/ч и сжигают его.
Жидкое топливо также подают через кран 19 в горелку 20 парогенератора. Водяной пар, проходя через пароперегреватель 14, нагревается до температуры 700°С (температуру нагрева пара контролируют по показаниям датчика 21).
Перегретый водяной пар через кран 22 подают в камеру 12 термического разложения. Продукты сгорания топлива в топке 15 при температуре 1000°С подают в рубашку 23 камеры 12 термического разложения в количестве 1024 кг/ч (при сгорании 1 кг топлива образуется 12,8 кг продуктов сгорания).
Проходя через рубашку камеры термического разложения, продукты сгорания охлаждаются до температуры 600°С. При этом количество тепла, передаваемого от продуктов сгорания в камеру термического разложения, составит величину:
Qпрод.сгорания=Mпрод.сгоранияCпрод.сгорания(T2-T1)=1024 кг/ч·1,34 кДж/кгС(1000°C-550°C)=617472 кДж/ч.
где Мпрод.сгорания – количество продуктов сгорания, кг/ч;
Спрод.сгорания – удельная теплоемкость продуктов сгорания, кДж/кгС;
T1 и T2 – температура входа продуктов сгорания в рубашку 23 камеры 12 термического разложения и температура выхода их из рубашки 23.
Далее продукты сгорания с Т=600°С из рубашки 23 камеры 12 термического разложения подают в рубашку 24 камеры 8 загрузки. Проходя через рубашку 24 камеры загрузки, продукты сгорания охлаждаются от Т=550°С до Т=200°С. При этом тепло охлаждения расходуется на нагрев камеры 8 загрузки, теплопотери и нагрев вагонеток 2 с отходами. Количество тепла охлаждения продуктов сгорания в нашем случае будет равно:
Qпрод.сгорания2=Mпрод.сгоранияCпрод.сгорания(T3-T4)=1024 кг/ч·1,34 кДж/кгС(550°С-200°С)=480256 кДж/ч.
где Т3-Т4 – температура входа продуктов сгорания в рубашку 24 камеры 8 загрузки и температуры выхода их из рубашки 24.
Пусть в установившемся режиме, когда камера 8 загрузки и камера 12 термического разложения нагреты до температуры 200°С и 500°С соответственно, величина теплопотерь в камере 8 загрузки равна 40%, а в камере 12 термического разложения равна 20% от количества подводимого в камеру тепла. В этом случае на нагрев вагонеток с отходами будет расходоваться за 1 ч следующее количество тепла продуктов сгорания:
3. В камере загрузки: (480256 кДж/ч)·0,6=288154 кДж/ч=Q1.
4. В камере термического разложения: (617472 кДж/ч)·0,8=493978 кДж/ч=Q2.
Пусть вес каждой вагонетки с отходами составляет 1500 кг (1000 кг весит сама тележка и 500 кг весят отходы). Удельная теплоемкость резиновых отходов Ср.отходов=1,4 кДж/кгС. Удельная теплоемкость материала вагонеток Ср.вагонеток=0,5 кДж/кгС. Начальная температура вагонеток с отходами Т – 20°С. Вагонетки с отходами находятся в камере загрузки 120 мин (2 ч). В этом случае 2 вагонетки с отходами нагреются до температуры:
Tнагр1=2Q1/(Ср.отходовMотходов+Cр.вагонетокMвагонеток)+20°C=(2·288154 кДж/ч)/{(1,4 кДж/кгС·1000 кг+0,5 кДж/кгС·2000 кг)}+20°С=260°С,
где Мвагонеток – масса вагонеток;
Q1 – количество тепла, подводимого в камеру 8 загрузки от продуктов сгорания в течение 1 ч;
Q2 – количество тепла, подводимого в камеру 12 термического разложения от продуктов сгорания в течение 1 ч.
Из рубашки 24 камеры 8 загрузки продукты сгорания с помощью дымососа 25 выводят в дымовую трубу 26.
Низкотемпературные продукты сгорания (Т=200-250°С) топлива из парогенератора 13 подают в дымовую трубу 26.
Суммарное количество тепла, необходимого для термического разложения отходов в камере 12, определяется следующим образом:
Qобщ=Qнагр+Qразд+Qпотерь,
т.е. Qобщ=1,2{(Cр.отходовMотходов(T2-T1)+Cр.вагонетокMвагонеток(T2-T1)+qMотходов)}.
Qобщ=1,2{(1,4 кДж/кг·1000 кг(450°С-260°С)+0,5 кДж/кгС·2000 кг
(450°С-260°С)+600 кДж/кг·2000 кг)}=1267200 кДж,
где Qобщ – общее количество необходимого для термического разложения тепла;
Qнагр – тепло нагревания отходов и вагонеток до 450°С;
Qразд – тепло, затрачиваемое на разложение отходов;
Qпотерь – тепловые потери, составляющие 20% от тепла нагревания и разложения;
q – удельное тепло разложения, составляющее для резиновых отходов 600 кДж/кг;
Мотходов – масса отходов;
T1 и Т2 – начальная и конечная температура вагонеток с отходами.
Так как часть тепла (за 2 ч будет подведено 987956 кДж) подводится через стенки реактора, то количество тепла (1267200-987956) кДж=279244 кДж необходимо подвести с перегретым паром. Следовательно, расход перегретого пара Gпара (Твхода=700°С, а Твыхода=450°С, Спара=2 кДж/кгС) составит величину:
Gпара={(279266 кДж)/2 кДж/кгС(700°С-450°С)}/2 ч=279,2 кг/ч.
Проходя через рубашку 23 камеры 12 термического разложения, продукты сгорания топлива нагревают стенки камеры 12, от которых тепло передается резиновым отходам, которые при нагреве до 280°С начинают претерпевать термическое разложение на парогазовые продукты (50% от массы резиновых отходов, т.е. в нашем случае выход парогазовых продуктов составит 1000 кг) и углеродный остаток. Температуру в камере 12 контролируют по показаниям датчика 27.
Парогазовые продукты через кран 28 поступают в теплообменник 29. В теплообменнике 29 в результате теплообмена с потоком воздуха, продуваемым с помощью воздуходувки 30, происходит охлаждение парогазовых продуктов до температуры 200°С, что контролируют по показаниям датчика 31 температуры.
Часть парогазовых продуктов конденсируется и поступает в емкость 17.
Пусть в нашем случае конденсируется 75% парогазовых продуктов, т.е. 0,75·250 кг/ч=187,5 кг/ч (процесс конденсации парогазовых продуктов протекает 2 ч.). Теплота конденсации данных продуктов составляет 300 кДж/кг, а теплоемкость их в газообразном состоянии 3 кДж/кгС.
В этом случае в теплообменнике 29 в результате охлаждения и конденсации части парогазовых продуктов выделится следующее количество тепла:
Q=Cп.пMп.п(Tвх.п.п+Tвых.п.п)+qконд.п.пMп.п=3 кДж/кгС·187,5 кг/ч(450-200)°С+300 кДж/кг·187,5 кг/ч=196875 кДж/ч,
где Сп.п – удельная теплоемкость парогазовых продуктов;
Мп.п – масса парогазовых продуктов;
Твх.п.п и Твых.п.п – температура входа парогазовых продуктов в теплообменник 29 и температуры выхода их из теплообменника 29;
qконд.п.п – удельная теплота конденсации парогазовых продуктов.
Данное количество тепла в теплообменнике 29 передается охлаждающему воздуху, который используют для обогрева помещения, где находится установка.
Из емкости 17 через кран 32 конденсат (масло) подают в циклонный реактор 33 с расходом 187,5 кг/ч-50 кг/ч-27 кг/ч=110,5 кг/ч, куда одновременно с помощью вентилятора 34 нагнетают воздух. 50 кг/ч масла сжигают в топке 15. Масло в количестве 27 кг/ч сжигают в парогенераторе для получения 279,2 кг/ч рабочего водяного пара.
В циклонном реакторе 33 сжигают конденсат (масло) при недостатке воздуха и температуре 2000°С. Тепло, выделившееся при сгорании части масла, вызывает термический распад оставшегося масла с образованием сажи и газов (горючих газов с теплотой сгорания 24 МДж/кг).
В нашем случае часть масла распадается с образованием сажи (образуется 20% от массы масла, т.е. 110,5 кг/ч·0,2=22,1 кг/ч), часть масла сгорает (40% от массы масла, т.е. 110,5 кг/ч·0,4=44,3 кг/ч), остальная часть масла (40% от массы масла, т.е. 110,5 кг/ч·0,4=44,2 кг) термически разлагается с образованием горючих газов с теплотой сгорания 35 МДж/кг.
Температуру в реакторе 33 контролируют по показаниям датчика 35 и регулировкой подачи воздуха от вентилятора 34 (увеличивают подачу при снижении температуры и уменьшают подачу воздуха при росте температуры) устанавливают температуру 900°С. Поток продуктов сгорания и сажи из реактора 33 выводят в холодильник 36, куда с помощью насоса 37 из емкости 38 распыляют воду, в результате чего температура продуктов сгорания и сажи снижается до Т=150°С. Охлажденную смесь из холодильника 36 подают в фильтр 39, где из газового потока выделяют сажу в количестве 94,4 кг/ч, которую подают в микроизмельчитель 40, а затем пневмотранспортом с помощью вентилятора 41 сажу подают в накопитель 42.
Очищенные в фильтре от сажи газы в количестве 44,2 кг/ч+567 кг/ч (продукты сгорания 44,3 кг/ч масла)=611,2 кг/ч из фильтра через кран 36 и кран 13 подают в топку 15 и сжигают. Сжигание газов в топке позволяет полезно использовать теплоту сгорания газов и предотвратить их выброс в окружающую среду.
Поскольку теплота сгорания газов составляет 2 МДж/кг и сжигают их 611,2 кг/ч (это эквивалентно по теплоте сгорания сжиганию 30 кг масла с удельной теплотой сгорания 40 МДж/кг), то количество сжигаемого масла в топке 15 снижают на 30 кг/ч и устанавливают равным (80 кг/ч-30 кг/ч)=50 кг/ч. Углеродный остаток разложения резиновых отходов в количестве 500 кг выводят из камеры 12 термического разложения. Для этого с помощью привода 45 поднимают заслонку 46 и с помощью толкателя 47 по рельсовому пути вагонетки 2 выводят в камеру 48 охлаждения, после чего заслонку 46 опускают. Из емкости 49 с водой насосом 50 в распылитель 51 подают воду. Вода распыляется над вагонетками 2 и охлаждает углеродный остаток и вагонетки до температуры 120°С. Температуру охлаждения контролируют по показаниям датчика 52.
В результате охлаждения углеродного остатка и вагонеток от Т=450°С до Т=120°С в охладителе снимается следующее количество тепла:
Qохладителя=Cу.оMу.о(450°C-120°C)+Cр.вагонетокMвагонеток(450°C-120°C)=0,8 кДж/кгС·500 кг/ч·330°С+0,5 кДж/кгС·2000 кг·330°С=462000 кДж/ч,
где Qохладителя – снимаемое в охладителе тепло;
Су.о – теплоемкость углеродного остатка;
Му.о – масса углеродного остатка.
Известно, что на нагрев и испарение 1 кг воды (начальная температура воды равна 20°С) необходимо следующее количество тепла:
Qи.воды=Ср.воды(100°С-20°С)Мводы+rфМводы=4,18 кДж/кгС·80°С·1 кг+2250 кДж/кг·1 кг=2584,4 кДж,
где Qи.воды – количество тепла, необходимое для испарения 1 кг воды;
Мводы – масса воды;
rф – теплота испарения воды;
Ср.воды – удельная теплоемкость воды.
Таким образом, для охлаждения вагонеток с углеродистым остатком необходимо следующее количество воды:
Мводы=Qохладителя/Qи.воды=(462000 кДж/ч)/(2584,4 кДж/кг)=178,8 кг/ч.
После охлаждения углеродный остаток в вагонетках выводят из камеры 48 охлаждения. Для этого с помощью поворотного механизма 53 поднимают заслонку 54, включают толкатель 55 и перемещают вагонетки 2 к месту выгрузки.
Опрокидывают вагонетки 2, и углеродный остаток выгружают в сепаратор 56, где отделяют металл от самого углеродного остатка. Металл 200 кг подают в накопитель 57, а углеродный остаток 800 кг подают в мельницу 58, размалывают и выгружают в накопитель 59. Вагонетки 2 после разгрузки по рельсовому пути 60 через поворотные платформы 61, 62, 63 и 64 перемещают к бункеру-накопителю 1, загружают и подают в камеру 8 загрузки. Из накопителя 59 пневмотранспортом с помощью воздуходувки 65 углеродный остаток в количестве 400 кг/ч подают через эжектор 66 в циклонный реактор 67.
Одновременно из теплообменника 29 летучие продукты разложения резины (после отделении 187,5 кг/ч масла) в количестве 62,5 кг/ч и 279,2 кг/ч водяной пар подают в реактор 67 и смесь (летучие продукты – углеродный остаток) сжигают при избытке воздуха 0,9 от теоретически необходимого, т.е. того количества воздуха, которое необходимо для полного сгорания данной смеси.
В нашем случае теоретически необходимое количество воздуха для сжигания 62,5 кг/ч продуктов разложения составляет 800 кг/ч (12,8 кг воздуха на 1 кг продуктов разложения), а для сжигания 200 кг/ч углеродного остатка теоретически необходимое количество воздуха составляет 1600 кг/ч (8 кг воздуха на 1 кг углеродного остатка). Таким образом, для полного сжигания смеси необходимо 1600 кг/ч+800 кг/ч=2400 кг/ч, а сжигание при избытке воздуха 0,9 потребует 2400 кг/ч·0,9=2160 кг/ч воздуха.
Количество воздуха, подаваемого на сжигание смеси, регулируют с помощью эжектора 66 и устанавливают равным 2160 кг/ч.
В реакторе 67 протекает неполное сгорание смеси, в результате чего за счет выделяющейся теплоты происходит термическое разложение углеводородов, содержащихся в парогазовых продуктах, выделяется сажа в количестве 20% от массы, т.е. 62,5 кг/ч·0,2=12,5 кг/ч и газы в количестве 40% от массы, т.е. 62,5 кг/ч·0,4=25 кг/ч. Часть углеводородов парогазовых продуктов сгорает, т.е. 40% от массы (62,5 кг/ч·0,4=25 кг/ч сгорает).
Углеродная составляющая твердого остатка частично сгорает в количестве 200 кг/ч·0,4=80 кг/ч, а частично нагревается до температуры 2000°С, и при этом из углеродной составляющей удаляются сернистые соединения и развивается ее поверхность за счет реагирования углерода с водяным паром, который содержится в летучих продуктах.
Таким образом, из углеродной составляющей получают сажу в количестве 200 кг/ч·0,2=40 кг/ч, а 80 кг/ч углеродного остатка реагирует с водяным паром (расходуется 53 кг/ч водяного пара) с образованием горючих газов, в состав которых входит оксид углерода, водород, сероводород и небольшие количества углеводородов метанового ряда.
Из реактора 67 продукты сгорания в смеси с сажей подают в холодильник 68, куда одновременно из емкости 38 подают воду и распыляют ее. Охлажденную смесь далее подают в фильтр 69, где путем фильтрации отделяют сажу и подают ее в микроизмельчитель 70, из которого пневмотранспортом с помощью воздуходувки 71 сажу в количестве 12,5 кг/ч+80 кг/ч=92,5 кг/ч загружают в накопитель 72.
Очищенные от сажи газы в количестве (279,2-53)=226,2 кг/ч (водяной пар)+2160 кг/ч (воздух)+133 кг/ч (летучие продукты)=2519,2 кг/ч (парогазовая смесь) через кран 73 и 44 подают в топку 15 и сжигают. Удельная теплота сгорания такой парогазовой смеси составит величину 1 МДж/кг и поэтому сжигание 2519,2 кг/ч парогазовой смеси эквивалентно сжиганию 30 кг/ч масла. Поэтому количество подаваемого в топку 15 масла из емкости 17 снижают с 50 кг/ч до 20 кг/ч.
Таким образом, при переработке по данному способу резиновых отходов в количестве 500 кг/ч получают 80 кг/ч+12,5 кг/ч+22,1 кг/ч=114,6 кг/ч сажи, 50 кг/ч-20 кг/ч=30 кг/ч масла. При этом энергообеспечение всего процесса переработки осуществляется за счет применения в качестве энергоресурсов части резиновых отходов – 500 кг/ч – 3114,6 кг/ч – 30 кг/ч – 50 кг/ч=305,4 кг/ч, где 50 кг/ч – металл, содержащийся в отходах.
За счет использования части резиновых отходов для энергообеспечения процесса переработки достигается эффект снижения энергоемкости, так как в сравнении с известными технологиями получения сажи из резиновых отходов отпадает необходимость в дополнительном топливе. Сжигание части резиновых отходов (305,4 кг/ч) в газифицированном виде и в виде измельченной углеродной составляющей обеспечивает более полное сгорание и снижение образования токсичных соединений в сравнении с технологиями прямого сжигания резиновых отходов.
Формула изобретения
1. Способ получения сажи из резиновых отходов, включающий их термическое разложение в реакторе в парогазовой среде, разделение продуктов разложения на парогазовые продукты и твердый углеродный остаток, измельчение углеродного остатка, отличающийся тем, что из парогазовых продуктов путем конденсации выделяют масло и подвергают его термическому разложению на сажу и газы при температуре 900-2000°С, а парогазовые продукты после выделения масла сжигают совместно с измельченным углеродным остатком и путем фильтрации из продуктов сгорания выделяют сажу.
2. Способ по п.1, отличающийся тем, что сжигание парогазовых продуктов после выделения масла совместно с измельченным углеродным остатком осуществляют при коэффициенте избытка воздуха 0,4-0,9.
3. Способ по п.1, отличающийся тем, что предварительно перед измельчением из углеродного остатка путем магнитной сепарации выделяют металл.
4. Способ по п.1, отличающийся тем, что газы термического разложения масла сжигают и продукты сгорания используют в качестве теплоносителя для внешнего обогрева реактора.
РИСУНКИ
MM4A – Досрочное прекращение действия патента СССР или патента Российской Федерации на изобретение из-за неуплаты в установленный срок пошлины за поддержание патента в силе
Дата прекращения действия патента: 30.04.2009
Извещение опубликовано: 20.05.2010 БИ: 14/2010
|