|
(21), (22) Заявка: 2003117900/04, 18.06.2003
(24) Дата начала отсчета срока действия патента:
18.06.2003
(43) Дата публикации заявки: 27.02.2005
(45) Опубликовано: 10.05.2006
(56) Список документов, цитированных в отчете о поиске:
RU 2156270 C1, 20.09.2000. RU 2167168 C1, 20.05.2001. RU 2125915 C1, 10.02.1999.
Адрес для переписки:
119991, Москва, В-296, ГСП-1, Ленинский пр-кт, 65, Российский государственный университет нефти и газа им. И.М. Губкина, зав.патентно-лицензионным отделом
|
(72) Автор(ы):
Чеботаревский Александр Эдуардович (RU), Винокуров Владимир Арнольдович (RU), Терентьев Евгений Викторович (RU), Сидоренко Дмитрий Олегович (RU), Овчинников Александр Иванович (RU)
(73) Патентообладатель(и):
Российский государственный университет нефти и газа им. И.М. Губкина (RU), Чеботаревский Александр Эдуардович (RU)
|
(54) СПОСОБ ПЕРЕРАБОТКИ ПРОМЫШЛЕННЫХ И БЫТОВЫХ ОТХОДОВ
(57) Реферат:
Изобретение относится к области термохимической переработки отходов, а точнее к способу переработки резиносодержащих и полимерсодержащих отходов путем термодеструкции в углеводородном растворителе в присутствии катализатора, проводимой, в частности параллельно с утилизацией отходов древесины. Способ переработки промышленных и бытовых отходов включает термодеструкцию резиносодержащих отходов и/или отходов пластмасс в среде углеводородного водорододонорного растворителя в присутствии катализатора при повышенных температуре и давлении. Согласно изобретению параллельно осуществляют термолиз древесных отходов, а процесс термодеструкции осуществляют при давлении 0,1-1,0 МПа путем ступенчатого повышения температуры в шесть стадий в среде углеводородного растворителя, при массовом соотношении отходы: углеводородный растворитель от 1:1,5 до 1:3 в качестве катализатора используют хлориды железа или хлорид алюминия в количестве 0,1-2,0 мас.% на углеводородный растворитель, в батарее, состоящей, по крайней мере, из пяти параллельно работающих реакторов, соединенных с установкой термолиза древесных отходов, при этом на первой стадии при температуре 20-65°С осуществляют набухание отходов в течение 25-30 минут, на второй – термодеструкцию отходов с одновременным отбором эфирных и бензольной фракций при 66-90°С, на третьей – термодеструкцию и отбор летучих фракций при 91-112°С, на четвертой – термодеструкцию и отбор среднелетучих фракций при температуре 113-144°С, на пятой термодеструкцию и отбор маслянистых фракций при температуре 145-280°С, на шестой, заключительной стадии, – термодеструкцию и отбор тяжелых фракций при температуре 281-320°С с последующей выдержкой остатков термодеструкции отходов при 320-350°С в течение 15-30 минут. Причем в углеводородный растворитель вводят 15-25 мас.% маслянистых и/или тяжелых фракций термодеструкции отходов с пятой и/или шестой стадий процесса, при этом в процессе проведения термодеструкции отходов используют тепло, получаемое от термолиза древесных отходов, осуществляемого с добавлением части маслянистых и/или тяжелых фракций с пятой и шестой стадий процесса термодеструкции отходов в печь дожига горючих газов, получаемых при термолизе древесных отходов, и/или непосредственно в печь термолиза древесных отходов, в количестве, соответствующем массовому соотношению маслянистые и/или тяжелые фракции: древесные отходы от 1:100 до 100:1. Целесообразно в качестве растворителя использовать фракции ароматических углеводородов или о-, п-, м-ксилолы или их смеси. Способ по изобретению позволяет повысить эффективность процесса переработки отходов за счет повышения выхода легкокипящих фракций и снижения энергозатрат. 1 табл., 1 ил., 1 з.п.ф-лы.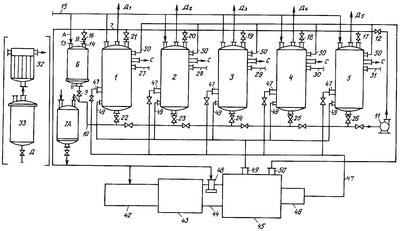
Изобретение относится к области термохимической переработки отходов, а точнее к способу переработки резиносодержащих и полимерсодержащих отходов путем термодеструкции в углеводороном растворителе в присутствии катализатора, проводимой, в частности, параллельно с утилизацией отходов древесины.
Проблема утилизации промышленных и бытовых отходов актуальна в связи со значительным ростом их количества, при этом отсутствуют эффективные технологии совместной переработки различных по химической природе отходов с получением ценных товарных продуктов.
Кроме того, имеющиеся способы утилизации отходов отличаются высокими энергозатратами и ориентированы на применение элекроэнергии, стоимость которой в последнее время возросла в 5-8 раз.
В то же время имеется ряд производств, где в условиях проведения технологического процесса выделяется значительное количество тепла, выбрасываемого в атмосферу. При этом известны способы переработки, например, древесных отходов, где возможно за счет получаемого горючего газа использовать получаемое тепло для проведения другого техпроцесса – утилизации резиносодержащих и полимерсодержащих отходов со значительным уменьшением потребления электроэнергии при комплексном использовании.
Известен способ переработки резиносодержащих отходов, при котором осуществляют термодеструкцию отходов при температуре 200-400°С в среде высококипящего углеводорода с образованием парогазовой смеси и тяжелой фракции термодеструктированной резины с последующим их разделением и конденсированием парогазовой смеси. При этом наиболее ценным продуктом, как считают авторы, является тяжелая фракция деструктированной резины, которая используется в качестве добавок к сотавам различных строительных и резиносодержащих материалов [Макаров В.М., Дроздовский В.Ф., Использование амортизированных шин и отходов производства резиновых изделий. Л., Химия, 1986 г, стр.16-27].
Известны также способы переработки отходов резин и пластмасс для получения бензина и дизельного топлива (US 4.851.601, US 5.414,169, EP-A-0607862) путем пиролиза. Получаемые продукты разжижают, и в конце процесса используют стадию каталитического крекинга в жидкой среде. Перечисленные способы характеризуются многостадийностью, сложностью технологии и высокими энергозатратами.
Известен также способ переработки отработанных резиновых автошин (US 3896059), включающий измельчение отработанных автопокрышек до размеров 0,8-4,0 мм, смешение их с нефтепродуктами, нагревание полученной смеси в реакторе при температуре 65-370°С в течение времени, достаточного для растворения материала, проведение каталитического крекинга полученного раствора в реакторе при температуре не ниже 450°С и повышенном давлении, равном 5-8 МПа, выгрузку кокса из реактора и дистилляцию с образованием газообразных продуктов, бензиновой фракции, легких и тяжелых масел. Такой способ отличается многостадийностью, высокими энергозатратами, что недопустимо в настоящее время для промышленного применения из-за высокой стоимости электроэнергии.
Наиболее близким по технической сущности к предлагаемому способу является метод переработки резиносодержащих и органических промышленных и бытовых отходов в химическое сырье и в компоненты моторного топлива (RU 2156270).
Способ включает термокаталитическое сжижение отходов при повышенных температурах и давлении в углеводородном растворителе с последующим отделением жидких продуктов и их ректификацией с получением целевых продуктов, в котором процесс термодеструкции ведут в присутствии инициатора – свободного йода и/или йодосодоржащих соединений, взятых в количестве 0,01-0,5 вес % от растворителя, при температуре 220-360°С и давлении 1-3 МПа.
В качестве растворителя в известном решении используют алкилбензол, смесь алкилбензолов или алкилсодержащие углеводородные смеси (толуол, бензол, тетраметилбензол, диэтилбензолы или их смеси). Способ проводят при массовом соотношении отходы: растворитель, равном 1:2-4.
Указанный способ характеризуется многостадийностью, высокими энергозатратами и малым выходом легкокипящих фракций – наиболее ценных и дорогостоящих продуктов термодеструкции.
Задачей изобретения является повышение эффективности процесса переработки отходов за счет повышения выхода легкокипящих фракций и снижения энергозатрат.
Поставленная задача достигается тем, что в способе переработки промышленных и бытовых отходов, включающем термодеструкцию резиносодержащих отходов и/или отходов пластмасс в среде углеводородного водорододонорного растворителя в присутствии катализатора при повышенных температуре и давлении, согласно изобретению, параллельно осуществляют термолиз древесных отходов, а процесс термодеструкции осуществляют при давлении 0,1-1,0 МПа путем ступенчатого повышения температуры в шесть стадий в среде углеводородного растворителя, при массовом соотношении отходы: углеводородный растворитель от 1:1,5 до 1:3, а в качестве катализатора используют хлориды железа или хлорид алюминия в количестве 0,1-2,0 мас.% на углеводородный растворитель, в батарее, состоящей, по крайней мере, из пяти параллельно работающих реакторов, соединенных с установкой термолиза древесных отходов, при этом на первой стадии при температуре 20-65°С осуществляют набухание отходов в течение 25-30 минут, на второй – термодеструкцию отходов с одновременным отбором эфирных и бензольной фракций при 66-90°С, на третьей – термодеструкцию и отбор летучих фракций при 91-112°С, на четвертой – термодеструкцию и отбор среднелетучих фракций при температуре 113-144°С, на пятой – термодеструкцию и отбор маслянистых фракций при температуре 145-280°С, на шестой, заключительной стадии, – термодеструкцию и отбор тяжелых фракций при температуре 281-320°С с последующей выдержкой остатков термодеструкции отходов при 350°С в течение 15-30 минут, причем в углеводородный растворитель вводят 15-25 мас.% маслянистых и/или тяжелых фракций термодеструкции отходов с пятой и/или шестой стадий процесса, при этом в процессе проведения термодеструкции отходов используют тепло, получаемое от термолиза древесных отходов, осуществляемого с добавлением части маслянистых и/или тяжелых фракций с пятой и шестой стадий процесса термодеструкции отходов в печь дожига горючих газов, получаемых при термолизе древесных отходов, и/или непосредственно в печь термолиза древесных отходов, в количестве, соответствующем массовому соотношению маслянистые и/или тяжелые фракции: древесные отходы от 1:100 до 100:1.
Целесообразно в качестве растворителя использовать фракции ароматических углеводородов ФАУ (ТУ 38-401-58-207-97) или о-, п-, м-ксилолы или их смеси.
Сущность способа заключается в следующем и отражена на принципиальной схеме (чертеж).
Способом по изобретению перерабатывают отходы пластмасс (в том числе и использованную сельскохозяйственную пленку) и любые резиносодержащие отходы (автопокрышки, отходы резинотехнической, авиационной промышленности и т.п.).
Переработку резиносодержащих и полимерсодержащих отходов (далее – отходы) осуществляют в интервале температур 20-350°С и давлении 0,1-1,0 МПа в шесть стадий в углеводородном растворителе в присутствии катализатора. В качестве углеводородного растворителя используют, например, фракции ароматических углеводородов ФАУ (ТУ 38-401-58-207-97) или о-, п-, м-ксилолы или их смеси. В качестве катализатора – хлориды железа или хлорид алюминия. В способе по изобретению используют 0,1-2,0 мас.% катализатора (на растворитель) при массовом соотношении отходы: растворитель, находящемся в интервале от 1:1,5 до 1:3.
На первой стадии способа по изобретению осуществляют набухание отходов при температуре 20-65°С в течение 25-30 мин; на второй стадии – термодеструкцию и отбор эфирных и бензольной фракций при температуре 66-90°С; на третьей – термодеструкцию и отбор легких фракций при температуре 91-112°С, на четвертой – термодеструкцию и отбор среднелетучих фракций при температуре 113-144°С; на пятой – термодеструкцию и отбор маслянистых фракций при температуре 145-280°С, на шестой, заключительной стадии, температуру поднимают от 280 до 350°С с целью отбора тяжелых фракций, образующихся при термодеструкции отходов, и выдерживают 15-30 минут в интервале температур от 320 до 350°С для улучшения процесса отделения кокса от металлокорда, с последующей выгрузкой кокса, легко отделяемого (встряхиванием) от металлокорда.
В углеводородный растворитель до введения его в реакторы наряду с катализатором вводят 15-25 мас.% (на растворитель) предварительно полученных маслянистых и/или тяжелых фракций с пятой и/или шестой стадий процесса термодеструкции отходов для ускорения процесса, поскольку именно эти фракции наиболее агрессивны по отношению к полимерным материалам из-за наличия в составе их молекул серы.
Каждая стадия характеризуется заданным интервалом температур, обеспечивающим набухание и последующую термодеструкцию отходов, сопровождающуюся отбором определенных фракций – целевых продуктов.
Продукты, отобранные на каждой стадии процесса, при необходимости могут быть подвергнуты последующей перегонке в кубовых и ректификационных аппаратах.
Для осуществления всех стадий процесса используют тепло, получаемое с установки параллельно проводимого процесса термолиза древесных отходов (любые смеси древесных бытовых и промышленных отходов, включая макулатуру), технологически связанной с реакторами термодеструкции, причем часть маслянистых и тяжелых фракций с пятой и шестой стадий процесса термодеструкции вводят в печь дожига горючих газов, получаемых при термолизе древесных отходов, и/или в печь термолиза, также соединенных с реакторами (чертеж), в массовом соотношении от 1:100 до 100:1, при оптимальном соотношении 60:40.
Количество реакторов в батарее определяется требуемой в каждом конкретном случае производительностью установки по переработке отходов.
Использование в способе переработки отходов по изобретению указанных катализаторов и растворителей совместно с маслянистыми и тяжелыми фракциями, позволяет ускорить процесс термодеструкции отходов, снизить температуру и давление процесса, увеличить количество получаемых при термодеструкции легкокипящих фракций.
Проведение процесса термодеструкции резиносодержащих и полимерсодержащих отходов параллельно с термолизом древесных отходов в установках, реализующих вышеуказанные процессы, технологически связанных друг с другом, позволяет существенно снизить потребление дорогой, в ряде случаев недоступной в необходимых количествах электроэнергии, или исключить полностью.
Принципиальная технологическая схема утилизации вышеназванных отходов автопокрышек и/или пластмасс методом термодеструкции с получением тепла от утилизируемой древесины представлена на чертеже.
Установка содержит батарею реакторов 1, 2, 3, 4 и 5 термодеструкции автопокрышек, отходов резин и/или отходов пластмассы, например полиэтиленовой пленки, соединение с емкостью – 6 водорододонорного растворителя, например фракции ароматических углеводородов (ФАУ) по ТУ 38-406-58-207-97 или п- или о- или м-ксилола, или их смеси и емкостью 7А для суспензии тяжелых фракций термодеструктированной резины в ФАУ или в ксилоле или бензоле по насосной магистралью 7, на которой установлен на выходе 8 промежуточной емкости 6 через вентиль 9 по магистрали 10 к насосу 11 и вентиля 12. Входы 13 и 14 промежуточной емкости 6 подсоединены, соответственно, магистралью 15 подачи водорододонарного растворителя по направлению стрелки А и магистралью 7 и вентиля 16 подачи по направлению стрелки В смеси маслянистых и тяжелых фракций термодеструктированной резины в растворителе, соединенную через насосную магистраль 10 с реакторами 1, 2, 3, 4 и 5. На магистралях 7 и 10 установлены вентили 17-21 и 22-26, соответственно.
Реакторы 1, 2, 3, 4 и 5 термодеструкции автопокрышек и/или отходов пластмасс также сообщены по магистралям 27, 28, 29, 30 и 31 через теплообменники (холодильники и дефлегматоры, повторяющиеся у каждого реактора 1-5), 32, 33, представленные на схеме – 34, 35 и 36 с емкостями приемниками 37, 38, 39, 40 и 41 (не указаны) отдельных фракций продуктов термодеструкции резин и пластмассовых отходов.
Кроме того, реакторы 1, 2, 3, 4 и 5 термодеструкции резин и/или отходов пластмасс технологически соединены с установкой утилизации древесных отходов (поз. 42-50) – источником (генератором газа) тепла, включающий топочную печь – 42 и сырьевой бункер – 43 с древесными или полимерными отходами и печь дожига горючего газа – 44 с теплообменником – 45, и воздуходувки с раструбом – 46 и магистрали 47 подачи горючих газов (тепла) в реакторе 1-5. Получаемые маслянистые тяжелые фракции термодеструкции частично подают в печь дожига 44 через форсунку – 48, где сжигаются вместе с горючими газами, с целью получения дополнительного высококалорийного тепла и повышения эффективности переработки древесных отходов. Тепло подается в реакторы 1, 2, 3, 4 и 5 теплоносителем по имеющимся теплопроводам – 47 и – 49,- 50.
Изобретение иллюстрируется следующим описанием техпроцесса.
В реакторы 1, 2, 3, 4 и 5 последовательно загружают автопоркрышки без их измельчения через загрузочное окно. Процесс термообработки отходов начинают последовательно-параллельно в каждом реакторе. По магистралям 47 в реакторы 1, 2, 3, 4 и 5 подают горячий воздух от установки 42, 43, 44 утилизации термолизом отходов древесины для ускоренного подогрева автопокрышек, а затем тепло подается в реакторы 1, 2, 3, 4 и 5 по каналам 49 и 50 от теплообменника 45 установки утилизации древесных отходов. Затем в реактор, например, 1 по магистралям 15 подают фракции ароматических углеводородов ФАУ в массовом соотношении отходы: растворитель 1:2, в смеси с ранее полученной маслянистой фракцией в количестве 20 мас.ч на 100 мас.ч. растворителя и добавляют треххлористое железо в количестве 0,1 мас.ч. на 100 мас.ч. растворителя ФАУ и доводят температуру до 65°С до достижения степени набухания 50-95 мас.% при непрерывной циркуляции растворителя по обводной трубе у каждого реактора в течение 30 мин. Проводимая обработка резины до степени набухания 50-95 мас.% при температуре 65°С обеспечивает оптимальные условия начала термодеструкции резины, а наличие в растворителе треххлористого железа ускоряет процесс термодеструкции резины. После проведения обработки резины в течение 30 мин при температуре 65°С, в реакторе 1 дискретно повышают температуру до 66-90°С, при этом легколетучие фракции продуктов термодеструкции резины улавливают через холодильник 32 и дефлегматор 33, установленные у каждого реактора 1, 2, 3, 4 и 5 с дополнительным охлаждением и поддержанием давления в реакторах от 0,1 до 1,0 МПа. Сконденсированные легкие фракции термодеструктированной резины направляют в отдельную накопительную емкость или в аппарат для дополнительной очистки. А температуру в реакторе, например, 1 дискретно повышают до 91-112°С с одновременным отбором среднелетучих фракций растворителя и продуктов термодеструкции в холодильнике 32 и дефлегматоре 33. Отбор фракций термодеструкции резины и растворителя продолжают вести в течение 30-40 мин при заданной температуре, а сконденсированные фракции термодеструктированной резины направляют в отдельную накопительную емкость или в аппарат для дополнительной очистки. После отгонки легких фракций продуктов термодеструкции резин температуру в реакторе, например, 1 дискретно повышают до 113-140°С и непрерывно осуществляют отбор среднелетучих маслянистых фракций. Далее процесс ведут при дискретном повышении температуры (140-280°С) в реакторе, например, 1 с одновременным отбором маслянистых фракций продуктов термодеструкции резин их конденсацией в холодильнике и дефлегматоре и сбора продуктов в отдельной емкости. Эти фракции термодеструкции резин наиболее агрессивны по отношению к резинам и пластмассе, т.к. содержат серосодержащие продукты термодеструкции, поэтому их добавляют в качестве ускоряющей добавки к основному растворителю, содержащий еще и катализатор термодеструкции отходов.
Маслянистые и тяжелые фракции продуктов термодеструкции резин в количестве соответствующем массовому соотношению маслянистых и тяжелых фракций: древесные отходы от 1:100 или, например, используют в равных соотношениях 50:50 или до использования одной из фракций в качестве топлива в чистом виде направляют по магистрали 7 через форсунку 48 в печь дожига 44, что позволяет получить дополнительное высококалорийное тепло в установке 42 термолиза отходов деревообработки.
После отбора маслянистых фракций продуктов термодеструкции резин температуру в реакторе, например, 1 повышают до 281-320°С для окончательного выделения очень тяжелых фракций и получения кокса и улучшения выделения металлического корда из остатков. После достижения заданной температуры в реакторе и выдержки при температуре 281-330°С в течение 15-30 мин реактор, например 1, продувают горячими отходящими газами от установки 42, 46 термолиза отходов древесины по магистрали 47 и его разгерметизируют.
Из реактора, например 1, вынимают поддон, возможно после нескольких циклов трмодеструкции, на котором собран кокс с остатками металлокорда, который легко от кокса отделяется встряхиванием и направляется для сбора и на утилизацию как высокоценный углеродистый металл и технический углерод. А кокс представляет собой ценный продукт как для получения чистого техуглерода, так и для получения сорбента, например, при сборе пролитых на землю нефтепродуктов.
Установка утилизации отходов древесины и макулатуры изображена на чертеже (поз.42-50), включающая 42 – топочная печь (где ведется термолиз древесины и получение горючего газа); 43 – бункер для отходов древесины и макулатуры; 44 – печь дожига горючих газов; 45 – теплообменник; 46 – воздуходувка; 47 – линия подачи горячих газов (тепла) в реактора 1-5; 48 – линия ввода тяжелых фракций термодеструкции отходов на дожиг в печи – 44 и 49, 50 – выводы трубопровода для подачи тепла из обменника – 45 в реактора 1-5.
Изобретение иллюстрируется следующими конкретными примерами.
Пример 1.
В реакторы (1-5), количество которых выбирают в зависимости от производительности процесса, загружают автопокрышки без их измельчения. Для ускоренного подогрева автопокрышек в реакторы подают горячий газ с температурой до 60°С с выхода установки утилизации термолизом отходов древесины по технологически соединенным трубопроводам. Затем в каждый из реакторов подают углеводородный растворитель в смеси с ранее полученной маслянистой и/или тяжелой фракцией и катализатором и доводят температуру до 65°С, а давление – до 0,1-1,0 МПа и выдерживают в течение 30 мин (при этом степень набухания покрышек составляет 50-95 мас.%). Проводимая обработка резины до степени набухания 50-95 мас.% при указанных условиях обеспечивает оптимальные условия начала термодеструкции резины. Затем температуру в реакторах повышают и поддерживают в интервале 66-90°С в течение времени, необходимом для улавливания летучих продуктов деструкции, которые направляют на дополнительную очистку, а температуру в реакторах повышают до 91-112°С с одновременным отбором легколетучих фракций растворителя и продуктов термодеструкции в течение 30-40 мин. После отгонки легколетучих фракций продуктов термодеструкции отходов температуру в реакторе повышают до 113-144°С с непрерывно осуществляемым отбором среднелетучих фракций. Далее процесс термодеструкции ведут при повышении температуры от 145 до 280°С с одновременным отбором маслянистых фракций продуктов термодеструкции отходов, их конденсацией и сбором продуктов в отдельные емкости.
На шестой заключительной стадии температуру в реакторах поднимают от 280 до 320°С, с целью отбора тяжелых фракций, образующихся при термодеструкции отходов, и выдерживают в течение 15-30 минут в интервале температур 320-350°С для облегчения процесса отделения кокса от металлокорда.
Затем реактор продувают горячими отходящими газами с установки термолиза отходов древесины и разгерметизируют для удаления остатков металлокорда и техуглерода и для последующей загрузки реактора отходами резин и пластмасс.
Из реактора вынимают поддон, на котором собран кокс с металлокордом, который легко отделяется от кокса встряхиванием. Металлокорд направляют для сбора и на утилизацию как высокоценную специальную сталь.
Кокс может использоваться как для получения чистого технического углерода, так и в качестве абсорбента, например, при сборе пролитых на землю нефтепродуктов, а также в производстве строительных материалов.
После удаления из реактора кокса и металлокорда реактор охлаждают. Затем технологический процесс термодеструкции отходов в каждом реакторе повторяют.
Весь технологический процесс автоматизирован и ведется по разработанной программе с управлением компьютером, а проведение предварительной обработки резиновых отходов (автопокрышек) или полимерных, или их смеси продуктами конденсации парогазовым конденсатом (тяжелые и маслянистые фракции) в сочетании с чистым углеводородным растворителем, содержащим треххлористое железо, позволяет ускорить термодеструкцию. В результате технологический процесс ускоряется в 1,5 раза.
Предлагаемый способ позволяет повысить степень конверсии резиносодержащих отходов, увеличить выход легколетучих ценных продуктов (эфиры, легкие бензины). Кроме того, способ позволяет получить жидкие продукты, отличающиеся низким содержанием серосодержащие и непредельных соединений, упростить технологию процесса термоожижения резиновых отходов, рационально использовать отходы коксохимического производства и наряду с технологией утилизации резиновых отходов, что улучшает экологическую обстановку среды обитания, получить ценные продукты:
– легкие фракции эфиров – для повышения октанового числа бензинов;
– чистые продукты растворителей – бензол, толуол, ксилол и т.д.;
– жидкие продукты термодеструкции резин для получения ингибированных грунтовок и мастик при гидроизоляции ж/б конструкций и защиты металлоизделий от коррозии;
– жидкие продукты термодеструкции резин, возвращающиеся в технологический процесс и ускоряющие термодеструкцию резин за счет присутствия повышенного содержания серосодержащих добавок – ускорителей деструкции резин;
– технического углерода из образующегося кокса для получения пигментов и сорбентов;
– металлокорда для получения высокоуглеродистых сталей.
При этом используется тепло, получаемое из термолиза отходов древесины, что значительно снижает потребление электроэнергии.
Пример 2.
В реакторы 1-5 загружают отходы полиолефинов, например сельскохозяйственную полиэтиленовую пленку без измельчения, снятую с парников. Для ускорения подогрева полимерных пленок в реакторы подают горячий газ с температурой 100°С с выхода установки утилизации термолизом отходов древесины и доводят температуру в реакторе до 60°С. Затем в каждый из реакторов подают углеводородный растворитель, например ФАУ, и далее процесс ведут согласно описанному в примере 1.
Пример 3.
В реакторы 1-5 загружают отходы полиамидной пленки и подают горячий газ с температурой 90°С с выхода установки утилизации термолизом отходов древесины и доводят температуру в реакторе до 60°С. Затем в каждый из реакторов подают углеводородный растворитель, например, бензол, в смеси с ранее полученной маслянистой и/или тяжелой фракцией и доводят температуру до 60°С, а давление до 1 МПа и выдерживается в течении 30 мин. Далее процесс ведут аналогично описанному в примере 1.
Пример 4.
В реакторы 1-5 загружают отходы дробленых автопокрышек, отходы полистирола и пластические массы на его основе, например, пенополистирола. В реакторы подают горячий газ с температурой 120°С с выхода установки утилизации термолизом отходов древесины и доводят температуру в реакторах до 60°С. Затем в каждый из реакторов подают углеводородный растворитель, например ксилол, в смеси с ранее полученной маслянистой фракцией термолиза и доводят температуру до 60°С, а давление до 0,5 МПа и выдерживают в течении 30 мин. Далее процесс ведут аналогично описанному в примере 1.
Пример 5.
В реакторы 1-5 загружают отходы полихлорвиниловой изоляции, снятой с электрокабелей, набухание ПВХ-отходов ведут аналогично примерам 1-4, с последующей термодеструкцией и выделением продуктов термодеструкции аналогично примеру №1.
Пример 6.
В реакторы 1-5 загружают отходы полиолефиновых пленок и смесь полистирольных и полиэтилентерефталатовых отходов. Далее процесс набухания и термодеструкции ведут по примеру №1.
Пример 7.
В реакторы 1-5 загружают отходы резинотехнических изделий РТИ и смесевые отходы полимерных пленок и изделий из пластмассы (сломанную тару, летники), затем в реакторы 1-5 подают горячий газ из установки термодеструкции древесины и углеводородный растворитель ФАУ. При температуре в реакторах 60°С их выдерживают в течении 30 мин, а затем процесс ведут по технологии, описанной в примере 1.
Пример 8.
В реакторы 1-5 загружают автопокрышки (цельные) и отходы полиолефиновой пленки, затем подают горючий газ из установки термодеструкции древесины и углеводородный растворитель ФАУ и проводят стадию набухания. При температуре в реакторах 60°С в их объем вводят полученный на отдельной установке-озонаторе (не показан) газ озон в объеме 0,05-1 мас.% от растворителя, а затем процесс термодеструкции ведут по технологии, описанной в примере 1.
Отбор проб для анализа осуществляют через вентиль пробоотборника, установленного на каждом реакторе.
В процессе исследования отобранных проб фракций термодеструкции отходов использован метод газовой хроматографии. Предварительно образцы фракций были подвергнуты перегонке с дефлегматором при атмосферном давлении, при этом отогнаны легкие фракции, по пределам выкипания соответствующие бензинам широкого фракционного состава. Газохроматографический анализ проводился на приборе Cambrige C95 m no оригинальной методике, использующей аппаратурно-программный комплекс «ЭКОХРОМ».
Параллельно был определен фракционный состав образцов по методике Ст СЭВ 758-77 на приборе АРНС-3, выполненном по ГОСТ 12997-76.
Примеры осуществления способа и составы получаемых продуктов по изобретению представлены в таблице 1.
Технический и технологический результат предложенного способа состоит в возможности изменения технологических операций таким образом, чтобы резко увеличить выход легких фракций жидких компонентов – эфиры, легкие бензины и индивидуальных раствортелей – бензола, толуола, ксилола, являющихся ценными товарными продуктами, извлекаемые из отходов автопокрышек и отходов полимерных материалов и, что еще очень важно, улучшить экологию среды обетания и сократить энергозатраты на утилизацию за счет использования выделяемого горючего газа, получаемого при термодеструкции отходов деревообработки.
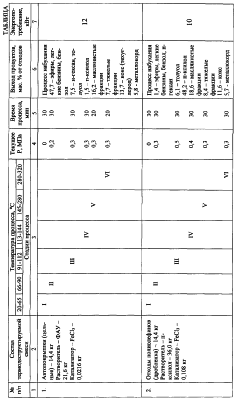 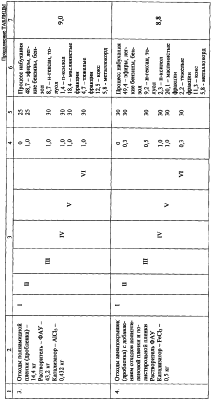 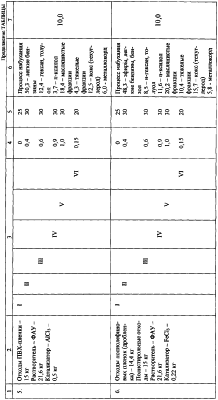 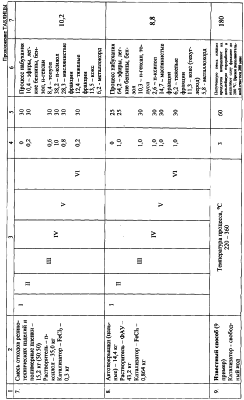
Формула изобретения
1. Способ переработки промышленных и бытовых отходов, включающий термодеструкцию резиносодержащих отходов и/или отходов пластмасс в среде углеводородного, водорододонорного растворителя в присутствии катализатора при повышенных температуре и давлении, отличающийся тем, что параллельно осуществляют термолиз древесных отходов, а процесс переработки осуществляют в шесть стадий при давлении 0,1-1,0 МПа путем ступенчатого повышения температуры при массовом соотношении отходы: углеводородный растворитель от 1,0:1,5 до 1:3, а в качестве катализатора используют хлориды железа или хлорид алюминия в количестве 0,1-2,0 мас.% на углеводородный растворитель, в батарее, состоящей, по крайней мере, из пяти параллельно работающих реакторов, соединенных с установкой термолиза древесных отходов, при этом на первой стадии при температуре 20-65°С осуществляют набухание отходов в течение 25-30 мин, на второй – термодеструкцию отходов с одновременным отбором эфирных и бензольной фракций при 66-90°С, на третьей – термодеструкцию и отбор летучих фракций при 91-112°С, на четвертой – термодеструкцию и отбор среднелетучих фракций при температуре 113-144°С, на пятой термодеструкцию и отбор маслянистых фракций при температуре 145-280°С, на шестой, заключительной стадии – термодеструкцию и отбор тяжелых фракций при температуре 281-320°С с последующей выдержкой остатков термодеструкции отходов в интервале температур от 320 до 350°С в течение 15-30 мин, причем в углеводородный растворитель вводят 15-25 мас.% маслянистых и/или тяжелых фракций термодеструкции отходов с пятой и/или шестой стадий процесса, при этом в процессе проведения термодеструкции отходов используют тепло, получаемое от термолиза древесных отходов, осуществляемого с добавлением части маслянистых и/или тяжелых фракций с пятой и шестой стадий процесса термодеструкции отходов в печь дожига горючих газов, получаемых при термолизе древесных отходов, и/или непосредственно в печь термолиза древесных отходов, в количестве, соответствующем массовому соотношению маслянистые и/или тяжелые фракции: древесные отходы от 1:100 до 100:1.
2. Способ по п.1, отличающийся тем, что в качестве углеводородного растворителя используют фракции ароматических углеводородов ФАУ, о-, п-, м-ксилолы или их смеси.
РИСУНКИ
MM4A – Досрочное прекращение действия патента СССР или патента Российской Федерации на изобретение из-за неуплаты в установленный срок пошлины за поддержание патента в силе
Дата прекращения действия патента: 19.06.2006
Извещение опубликовано: 20.06.2007 БИ: 17/2007
NF4A Восстановление действия патента СССР или патента Российской Федерации на изобретение
Дата, с которой действие патента восстановлено: 20.07.2007
Извещение опубликовано: 20.07.2007 БИ: 20/2007
|
|