|
(21), (22) Заявка: 2004113739/11, 05.05.2004
(24) Дата начала отсчета срока действия патента:
05.05.2004
(43) Дата публикации заявки: 20.10.2004
(45) Опубликовано: 10.05.2006
(56) Список документов, цитированных в отчете о поиске:
RU 11191 U1, 16.09.1999. SU 1446094 А1, 23.12.1988. RU 25734 U1, 20.10.2002. RU 9213 U1, 16.02.1999. SU 1618728 A1, 07.01.1991. SU 1093684 A, 23.05.1984. RU 2129524 С1, 22.04.1997. US 5730305 A, 24.03.1998.
Адрес для переписки:
454119, г.Челябинск, ул. Машиностроителей, 10Б, НПП “Резонанс”, В.А. Коровину
|
(72) Автор(ы):
Коровин Владимир Андреевич (RU), Коровин Константин Владимирович (RU)
(73) Патентообладатель(и):
Общество с ограниченной ответственностью “Научно-производственное предприятие “Резонанс” (RU)
|
(54) СПОСОБ ЗАЩИТЫ ГРУЗОПОДЪЕМНОГО КРАНА ОТ ПЕРЕГРУЗОК
(57) Реферат:
Изобретение относится к подъемно-транспортному оборудованию, а именно к устройствам защиты грузоподъемных кранов от перегрузок. При защите грузоподъемного крана от перегрузок предварительно определяют величины нагрузок, допустимые для различных пространственных положений его стрелы или грузозахватного органа, и их запоминают. В процессе работы крана измеряют параметры, характеризующие текущую нагрузку крана и текущее пространственное положение стрелы или грузозахватного органа, и сравнивают текущую нагрузку крана с запомненной допустимой нагрузкой. В случае, если текущая нагрузка превышает допустимую, отключают механизмы крана, блокируя его работу. Перед началом работы крана задают предельные значения, по меньшей мере, одного диагностического параметра, характеризующего техническое состояние грузоподъемного крана. В процессе работы крана определяют текущее значение, по меньшей мере, одного диагностического параметра, сравнивают его с предельно допустимым и в зависимости от результатов этого сравнения формируют предупреждающие сигналы для крановщика или осуществляют изменение величины нагрузки, допустимой для текущего пространственного положения стрелы или грузозахватного органа. В качестве диагностического параметра могут принимать собственные магнитные поля рассеяния наиболее нагруженных узлов крана, значение люфта или зазора в подвижном соединении и это значение записывать в энергонезависимую память с возможностью считывания. Изобретение повышает эффективность защиты грузоподъемного крана от перегрузок и повреждений, повышает срок службы крана, а также повышает оперативность контроля технического состояния крана. 4 з.п. ф-лы, 1 ил.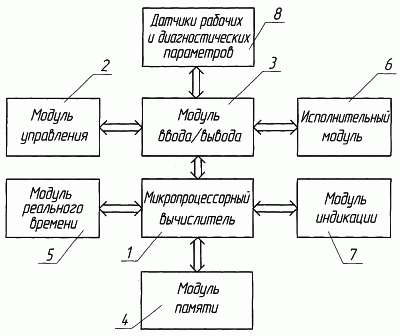
Изобретение относится к области машиностроения и может быть использовано в системах управления и защиты от перегрузок и повреждений грузоподъемных кранов.
Известен способ защиты грузоподъемного крана от перегрузок и повреждений путем установки зоны допустимых значений (пороговых уровней) для выбранных рабочих параметров грузоподъемного крана, характеризующих грузовой момент и положение грузоподъемного (стрелового) оборудования крана, контроля в процессе работы грузоподъемного крана значений выбранных параметров, сравнения этих значений с пороговыми уровнями и формирования предупреждающих сигналов и сигналов управления исполнительными устройствами грузоподъемного крана в зависимости от результатов этого сравнения [1, 2].
В данном способе обеспечивается защита грузоподъемного крана как от перегрузок, так от столкновений стрелы с препятствиями (координатная защита) при работе крана в стесненных условиях. Однако при этом не учитываются наработка и техническое состояние грузоподъемного крана, что существенно снижает эффективность его защиты.
Более совершенным и наиболее близким к предложенному является способ защиты грузоподъемного крана от перегрузок, от повреждений и контроля его технического состояния, включающий предварительное, например расчетным путем при проектировании крана, определение величин нагрузок, допустимых для различных пространственных положений его стрелы, и их запоминание, измерение в процессе работы крана параметров текущего пространственного положения стрелы, последующее извлечение запомненной величины допустимой нагрузки для этих параметров и измерение текущей нагрузки крана, их последующее сравнение и отключение механизмов крана, если последняя превышает допустимую, а также задание перед началом эксплуатации крана показателя его группы, определяемого как третья степень от наибольшей номинальной грузоподъемности, задание ряда предельных значений наработок, соответствующих видам регламентных работ, и минимально значимой величины нагрузки, запоминание их, а затем, в процессе работы крана, фиксацию последовательных циклов нагружения, при которых происходит увеличение текущей нагрузки выше минимально значимой величины, замер в каждом цикле пикового значения текущей нагрузки крана, возведение его в третью степень, деление на показатель группы крана, определение наработки в каждом цикле нагружения и общей наработки и последующее определение и сигнализацию срока предстоящих регламентных работ посредством сравнения общей наработки крана с предварительно заданными предельными значениями [3].
В известном способе также обеспечивается как защита грузоподъемного крана от перегрузок, так и координатная защита. Кроме того, дополнительно определяется наработка крана и сигнализируются сроки проведения соответствующих регламентных работ.
Однако при этом реальное техническое состояние грузоподъемного крана не контролируется, не учитывается в работе системы защиты и не документируется (не записывается в долговременную память), а сроки проведения регламентных работ определяются исходя не из фактического технического состояния крана, а из прогноза этого технического состояния расчетным путем исходя из количества циклов нагружения и пиковой нагрузки в каждом цикле.
Это приводит к снижению эффективности защиты грузоподъемного крана от перегрузок и снижению срока его службы, поскольку результаты расчета/прогноза технического состояния крана могут существенно отличаться от реальных показателей ввиду несовершенства методики и погрешностей расчета и отсутствия учета множества факторов, влияющих на техническое состояние узлов и деталей крана – коррозии, производственных допусков и заводского брака, разброса характеристик металла, ослабления клепаных и болтовых соединений, появления трещин и деформаций вследствие посторонних воздействий на металлоконструкции крана и т.д.
Задачами, на решение которых направлено предложенное техническое решение, являются повышение эффективности защиты грузоподъемного крана от перегрузок и повреждений путем учета его технического состояния непосредственно при работе системы защиты и управления, повышение срока службы крана путем снижения нагрузок на кран при ухудшении его технического состояния, а также повышение оперативности контроля технического состояния крана путем диагностики его дефектов непосредственно в процессе работы крана.
В предложенном способе защиты грузоподъемного крана от перегрузок путем предварительного определения величин нагрузок, допустимых для различных пространственных положений его стрелы или грузозахватного органа, их запоминания, измерения в процессе работы крана параметров, характеризующих текущую нагрузку крана и текущее пространственное положение стрелы или грузозахватного органа, сравнения текущей нагрузки крана с запомненной допустимой нагрузкой для текущего пространственного положения его стрелы или грузозахватного органа и, если текущая нагрузка превышает допустимую, отключения механизмов крана с блокированием его работы решение поставленных технических задач достигается тем, что дополнительно перед началом работы крана задают предельные значения, по меньшей мере, одного диагностического параметра, характеризующего техническое состояние грузоподъемного крана, запоминают их, а в процессе работы крана определяют текущее значение, по меньшей мере, одного диагностического параметра, сравнивают его с запомненным предельно допустимым и, в зависимости от результатов этого сравнения, формируют предупреждающие сигналы для крановщика или осуществляют изменение величины нагрузки, допустимой для текущего пространственного положения стрелы или грузозахватного органа.
Решение поставленных технических задач может также достигаться тем, что в качестве предельного значения указанного диагностического параметра принимают предельное значение перемещения или деформации, по меньшей мере, одного узла крана при воздействии нагрузок или собственные магнитные поля рассеяния наиболее нагруженных узлов крана, люфта или зазора в подвижном соединении.
Кроме того, для решения поставленных задач значения, по меньшей мере, одного диагностического параметра крана могут дополнительно записываться в энергонезависимую память с возможностью считывания в случае необходимости.
При этом определение значений, по меньшей мере, одного диагностического параметра крана, необходимых для решения поставленных задач, может осуществляться расчетным путем в процессе работы крана по априорно известной зависимости с использованием результатов измерения параметров, характеризующих текущую нагрузку и текущее пространственное положение стрелы, грузозахватного органа или другого узла крана.
Существенные отличительные признаки независимого пункта формулы заявленного изобретения, а именно предварительное задание предельных значений диагностических параметров, характеризующих техническое состояние грузоподъемного крана, запоминание этих параметров на грузоподъемном кране, определение диагностических параметров в процессе работы крана, их сравнение с предельно допустимым и формирование предупреждающих сигналов для крановщика или отключение механизмов крана, если текущее значение диагностического параметра превышает допустимое, а также отличительные признаки зависимых пунктов формулы – изменение величины нагрузки, допустимой для текущего пространственного положения стрелы или грузозахватного органа, в зависимости от текущей величины диагностического параметра, запись значений диагностических параметров в энергонезависимую память, а также определение значений диагностических параметров крана расчетным путем в процессе работы крана с использованием результатов измерения его рабочих параметров находятся в непосредственной причинно-следственной связи с достигаемым техническим результатом, поскольку обеспечивают реализацию защиты грузоподъемного крана с учетом его реального технического состояния.
На чертеже в качестве примера приведена функциональная схема устройства, реализующего предложенный способ защиты грузоподъемного крана от перегрузок.
Устройство безопасности (или защиты) грузоподъемного крана содержит микропроцессорный вычислитель (цифровую вычислительную машину) 1, модуль управления 2, модуль ввода/вывода информации 3, модуль памяти 4, модуль реального времени 5, исполнительный модуль 6, модуль индикации 7 и датчики рабочих и диагностических параметров 8, соединенные с первыми входами/выходами модуля ввода/вывода информации 3, вторые входы/выходы которого соединены с первыми входами/выходами микропроцессорного вычислителя 1, вторые, третьи и четвертые входы/выходы которого соединены с входами/выходами соответственно модуля памяти 4, модуля реального времени 5 и модуля индикации 7. Входы/выходы (или выходы) модуля управления 2 подключены к третьим входам/выходам (или входам) модуля ввода/вывода информации 3, четвертые входы/выходы (или выходы) которого соединены с входами/выходами (или входами) исполнительного модуля 6.
Датчики рабочих параметров 8 в общем случае включают в себя датчик угла подъема (или наклона) стрелы, датчик длины стрелы, датчик массы груза (датчик силы или датчики давления), датчик угла поворота крана (датчик азимута), датчик предельного подъема грузозахватного органа и другие датчики, необходимость установки которых определяется конструкцией конкретного грузоподъемного крана, на который устанавливается устройство безопасности.
В случае, если диагностические параметры, характеризующие техническое состояние крана, не могут быть определены путем обработки выходных сигналов датчиков рабочих параметров крана, использующихся для реализации защиты от перегрузки и координатной защиты, в систему безопасности вводятся дополнительные датчики, специально предназначенные для измерения диагностических параметров. Например, может быть установлен датчик прогиба или скручивания стрелы или любой другой металлоконструкции крана, феррозондовые преобразователи для диагностики металлоконструкций по методу магнитной памяти металла, магнитные датчики для диагностики по методу изменения коэрцитивной силы металла и т.д.
Датчики рабочих и диагностических параметров 8 могут быть выполнены с общей мультиплексной линией связи и, соответственно, объединены через эту линию либо могут подключаться к модулю ввода/вывода информации 3 при помощи отдельных проводов.
Микропроцессорный вычислитель (электронный блок) 1 может быть выполнен на микроконтроллере, модуль управления 2 – в виде клавиатуры (набора кнопок-клавиш). Модуль ввода/вывода информации 3, обеспечивающий согласование логических уровней входных и выходных сигналов микропроцессорного вычислителя 1 с модулем управления 2, с датчиками рабочих параметров 8 и с исполнительным модулем 6, может быть выполнен на базе интерфейсных микросхем.
Модуль памяти 4 может быть выполнен на базе микросхем Flash-памяти, модуль индикации 7 – в виде набора светодиодов и символьных жидкокристаллических индикаторов, модуль реального времени 5 – на основе специализированной микросхемы, со встроенным кварцевым резонатором и литиевой батарей питания, а исполнительный модуль 6 – в виде набора силовых электромагнитных реле или защищенных силовых электронных ключей, подключенных к электрогидравлической системе управления грузоподъемного крана.
Поясним суть предложенного способа на примере работы реализующего его устройства.
Перед началом работы грузоподъемного крана крановщик при помощи органов управления 2 осуществляет установку пороговых уровней рабочих параметров грузоподъемного крана, характеризующих его геометрию, условия или режим работы. К ним относятся ограничения по координатной защите, вид используемого стрелового оборудования (наличие, длина и угол наклона гуська), характеристики опорного контура и т.д. Количество и вид этих параметров определяются конструкцией конкретного грузоподъемного крана и нормативными требованиям к безопасной эксплуатации крана. Эти параметры сохраняются в памяти микропроцессорного вычислителя 1 или в модуле памяти 4.
Кроме того, в память микропроцессорного вычислителя 1 или в модуль памяти 4 предварительно (до начала работы крана) записываются величины нагрузок, допустимых для различных пространственных положений стрелы или грузозахватного органа крана. Эти величины определяются, как правило, расчетным путем при проектировании крана и представлены в виде его грузовых характеристик.
Одновременно в память микропроцессорного вычислителя 1 или в модуль памяти 4 предварительно (до начала работы крана) записываются предельные значения диагностических параметров, характеризующих техническое состояние крана. Примером такого параметра является величина деформации, в частности прогиб (изгиб), стрелы грузоподъемного крана. В этом случае перед началом работы крана, например, расчетным путем при проектировании крана или путем предварительных измерений прогиба с контрольными грузами определяют и задают предельные значения деформации – прогиб стрелы крана при воздействии нагрузок при различных пространственных положениях его стрелы. Т.е. в каждой точке грузовой характеристики крана, представляющей собой зависимость максимальной нагрузки от длины стрелы и вылета грузозахватного органа, дополнительно определяют и запоминают максимально допустимую величину прогиба стрелы.
Микропроцессорный вычислитель 1 работает по программе, записанной в его встроенной памяти программ или в модуле памяти 4, и через модуль ввода/вывода информации 3 осуществляет обмен с датчиками рабочих и диагностических параметров 8 по общей мультиплексной линии связи или по отдельным проводам. После получения информации от датчиков 8 микропроцессорный вычислитель 1 определяет действительные значения рабочих параметров крана – текущую нагрузку крана и фактическое положение его грузоподъемного (стрелового) оборудования. При необходимости, для определения текущей нагрузки крана, текущего положения его стрелы или грузозахватного органа, осуществляются преобразования выходных сигналов датчиков рабочих параметров 8. Это имеет место в случае, когда текущая нагрузка крана, положение его стрелы или грузозахватного органа измеряются косвенным образом, например при определении нагрузки стрелового гидравлического крана по давлениям в штоковой и поршневой полостях гидроцилиндра подъема стрелы. Эти преобразования реализуются программно-микропроцессорным вычислителем 1.
Микропроцессорный вычислитель 1 осуществляет сравнение текущего положения стрелы или грузозахватного органа с пороговыми уровнями, заданными крановщиком при введении параметров координатной защиты, а также сравнение текущей нагрузки крана с запомненной допустимой нагрузкой для текущего пространственного положения стрелы или грузозахватного органа. Далее в зависимости от результатов этого сравнения, т.е. при приближении стрелы крана к границам разрешенной зоны работы по координатной защите или в случае превышения максимально допустимой нагрузки крана, микропроцессорный вычислитель 1 формирует предупреждающие сигналы для крановщика, поступающие на модуль индикации 7 или сигналы управления исполнительными устройствами грузоподъемного крана, которые через модуль ввода/вывода 3 поступают на исполнительный модуль 6, блокируя работу крана. Благодаря этому осуществляется координатная защита и защита крана от перегрузки.
Дополнительно в процессе работы крана микропроцессорный вычислитель 1 при помощи модуля индикации 7 обеспечивает отображение основных параметров работы крана.
Одновременно микропроцессорный вычислитель 1 при помощи датчиков 8 осуществляет измерение диагностического параметра, например прогиба стрелы. Прогиб стрелы может быть определен на основании результатов измерения рабочих параметров крана, например вылета грузозахватного органа, или измерен отдельным датчиком 8. Далее микропроцессорный вычислитель 1 сравнивает измеренный прогиб стрелы с предельно допустимым для данного пространственного положения стрелы, предварительно записанным в его памяти или в модуле памяти 4, и, в зависимости от результатов этого сравнения, при помощи модуля индикации 7 формирует предупреждающие сигналы для крановщика или при помощи исполнительного модуля 7 отключает механизмы крана, если текущее значение данного диагностического параметра превышает допустимое.
Использование прогиба стрелы в качестве диагностического параметра базируется на том, что ухудшение технического состояния крана – уменьшение толщины стенок стрелы вследствие коррозии, ослабление сварных (клепаных) соединений, наличие трещин, деформаций и т.п., неизбежно приводит к увеличению прогиба стрелы крана под нагрузкой. Соответственно, путем контроля величины прогиба стрелы осуществляется оперативный контроль технического состояния крана и автоматическое отключение грузоподъемных механизмов при превышении предельно допустимой величины прогиба.
Аналогичным образом в качестве диагностического параметра может быть использован прогиб моста мостового крана. В этом случае величина максимально допустимого прогиба записывается в память микропроцессорного вычислителя 1 или в модуль памяти в виде известной функции положения грузовой тележки и нагрузки на кран. Далее алгоритм реализации дополнительной функции защиты мостового крана по прогибу его моста аналогичен описанному алгоритму для стрелового крана.
Контролируя величину диагностического параметра, микропроцессорный вычислитель 1 может программно реализовать автоматическое уменьшение грузоподъемности крана при ухудшении его технического состояния. Если, например, под воздействием нагрузки при каком-либо положении грузозахватного органа прогиб стрелы или моста крана превышает установленную величину в К раз, то микропроцессорный вычислитель может автоматически уменьшить допустимую нагрузку крана в К раз в любом режиме его работы. Это также обеспечивает повышение эффективности защиты крана и увеличение его срока службы.
В качестве диагностических параметров могут быть приняты собственные магнитные поля рассеяния наиболее нагруженных узлов крана (метод неразрушающего контроля, основанный на использовании магнитной памяти металла, позволяющий выполнить интегральную оценку состояния узлов крана с учетом качества металла, фактических условий эксплуатации и конструктивных особенностей этих узлов), скорость просадки груза из-за утечек в гидросистеме, скручивание стрелы крана, одностороннее или диагональное прижатие колес к рельсам кранового пути башенного крана, люфты и зазоры в подвижных соединениях и т.д.
Выбор этих параметров и соответствующего набора датчиков для их измерения осуществляется разработчиком системы безопасности, зависит от конструкции конкретного грузоподъемного крана.
Отдельные диагностические параметры могут быть определены расчетным путем в процессе работы крана по априорно известным зависимостям с использованием результатов измерения параметров, характеризующих текущую нагрузку и текущее пространственное положение стрелы, грузозахватного органа или другого узла крана. Например, люфты и зазоры в приводе любого поворотного узла крана могут быть определены по гистерезису датчика углового перемещения этого узла, техническое состояние гидросистемы – по скорости изменения давления под нагрузкой или по изменению положения стрелы или груза при отсутствии управляющих воздействий, прогиб стрелы – по изменению вылета и т.д.
Для документирования работы грузоподъемного крана устройство может содержать встроенный регистратор параметров, реализованный на основе модуля памяти 4 и модуля реального времени 5. В модуль памяти 4 регистратора микропроцессорный вычислитель 1 записывает также диагностические параметры крана с целью их последующего считывания для анализа и для расследования причин аварий.
Реализация отличительных признаков предложенного технического решения обеспечивает контроль технического состояния крана непосредственно в процессе его работы, а не во время периодического освидетельствования, что обеспечивает своевременность выявления дефектов и существенно повышает эффективность защиты крана, а также позволяет повысить срок службы крана за счет своевременного снижения нагрузок на кран при ухудшении его технического состояния.
Источники информации, использованные при составлении заявки
1. Патент RU 2151732 С1, МПК7 В 66 С 15/00, 23/88, 27.06.2000.
2. Патент US 5730305 А, МПК6 В 66 С 13/16, 13/18, 24.03.1998.
3. Заявка RU 98113676 А, МПК7 В 66 С 1/00, 20.05.2000.
Формула изобретения
1. Способ защиты грузоподъемного крана от перегрузок, заключающийся в том, что предварительно определяют величины нагрузок, допустимых для различных пространственных положений его стрелы или грузозахватного органа, их запоминают, измеряют в процессе работы крана параметры, характеризующие текущую нагрузку крана и текущее пространственное положение стрелы или грузозахватного органа, сравнивают текущую нагрузку крана с запомненной допустимой нагрузкой для текущего пространственного положения его стрелы или грузозахватного органа и, если текущая нагрузка превышает допустимую, отключают механизмы крана, блокируя его работу, отличающийся тем, что дополнительно перед началом работы крана задают предельные значения, по меньшей мере, одного диагностического параметра, характеризующего техническое состояние грузоподъемного крана, запоминают их, а в процессе работы крана определяют текущее значение, по меньшей мере, одного диагностического параметра, сравнивают его с запомненным предельно допустимым и, в зависимости от результатов этого сравнения, формируют предупреждающие сигналы для крановщика или осуществляют изменение величины нагрузки, допустимой для текущего пространственного положения стрелы или грузозахватного органа.
2. Способ по п.1, отличающийся тем, что в качестве предельного значения диагностического параметра принимают предельное значение перемещения или деформации, по меньшей мере, одного узла крана при воздействии нагрузки.
3. Способ по п.1, отличающийся тем, что в качестве диагностического параметра принимают собственные магнитные поля рассеяния наиболее нагруженных узлов крана, люфта или зазора в подвижном соединении.
4. Способ по п.1, отличающийся тем, что значения, по меньшей мере, одного диагностического параметра крана дополнительно записывают в энергонезависимую память с возможностью считывания в случае необходимости.
5. Способ по п.1, отличающийся тем, что текущее значение, по меньшей мере, одного диагностического параметра крана определяют расчетным путем в процессе работы крана по априорно известной зависимости с использованием результатов измерения параметров, характеризующих текущую нагрузку и текущее пространственное положение стрелы, грузозахватного органа или другого узла.
РИСУНКИ
|
|