|
(21), (22) Заявка: 2004122183/02, 19.07.2004
(24) Дата начала отсчета срока действия патента:
19.07.2004
(45) Опубликовано: 27.03.2006
(56) Список документов, цитированных в отчете о поиске:
WO 9518238 A1, 06.07.1995. RU 2135611 C1, 27.08.1999. SU 1802531 A1, 27.09.1996. RU 2031130 C1, 20.03.1995. RU 2158768 C1, 10.11.2000. US 6146437 A, 14.11.2000.
Адрес для переписки:
654007, Кемеровская обл., г. Новокузнецк, ул. Кирова, 42, СибГИУ, патентный отдел, Н.В. Галаниной
|
(72) Автор(ы):
Цымбал Валентин Павлович (RU), Мочалов Сергей Павлович (RU)
(73) Патентообладатель(и):
Цымбал Валентин Павлович (RU), Мочалов Сергей Павлович (RU)
|
(54) СПОСОБ ПОЛУЧЕНИЯ МЕТАЛЛОВ ИЗ РУДНЫХ МАТЕРИАЛОВ И АГРЕГАТ ДЛЯ ЕГО ОСУЩЕСТВЛЕНИЯ
(57) Реферат:
Изобретение относится к металлургии, в частности к получению металла в жидкофазных агрегатах непрерывного действия. Техническим результатом изобретения является комплексное извлечение из железорудных концентратов и пылевидных металлосодержащих отходов всех металлов, имеющих сродство к кислороду меньше чем алюминий, повышение до 100% доли переработки твердых железосодержащих материалов с устранением из состава шихты жидкого чугуна, снижение энергетических затрат. Способ включает подачу в реакционную камеру сыпучих материалов, ввод кислорода и восстановителя, полный перевод металла и шлака в пенистую эмульсию, создание в реакционной камере повышенного пульсирующего давления в пределах 0,4-3,0 МПа и значительного отклонения системы от термодинамического равновесия путем организации истечения двухфазной среды из реакционной камеры в рафинирующий отстойник с критической скоростью, разделение в нем металла и шлака и отвод газа через высокий слой эмульсии с определенной скоростью. Для разделения железосодержащей и обогащенной легирующими элементами составляющих в реакционную камеру через встречно расположенные фурмы подают спутные потоки кислорода и восстановителя, а соотношение кислорода и восстановителей, подаваемых в реакционную камеру и рафинирующий отстойник, рассчитывают из условия получения в верхних слоях газошлаковой эмульсии содержания оксидов железа в пределах 5-8% от массы шлака. Обедненный железом шлак в виде эмульсии подают в копильник шлакоприемника, куда подают углесодержащий восстановитель в стехиометрическом соотношении, обеспечивающем полное восстановление оксида железа из подаваемого шлака, а восстановление всех остающихся в шлаке оксидов металлов, кроме кремния и алюминия, ведут алюмотермическим или комбинированным алюмосиликатотермическим методом. А если в качестве конечной продукции задают титансодержащий или какой-либо другой шлак, обогащенный легирующими элементами, то его подают из шлакоприемника непосредственно на гранулятор. Агрегат для осуществления способа включает сферическую реакционную камеру с устройством подачи сыпучих материалов, устройством для подачи спутных потоков кислорода и газообразного или пылевидного восстановителя, соединительный канал, рафинирующий отстойник с фурмой, встречно расположенной с соединительным каналом, первый копильник с леткой для отвода первичного металла, устройством для подачи углеродсодержащих и других сыпучих материалов. Последовательно с рафинирующим отстойником установлен шлакоприемник, соединенный с рафинирующим отстойником двумя каналами: нижний наклонный канал служит для отвода верхних слоев газошлаковой эмульсии в нижнюю часть шлакоприемника, верхний канал служит для отвода газа через верхнюю часть шлакоприемника в котел-утилизатор, при этом к нижней части шлакоприемника, в зависимости от вида конечной продукции, пристыковываются второй копильник с устройством для подачи карбо- и металлотермических восстановителей и с леткой для выпуска металла и шлака или валковый гранулятор. 2 н.п. ф-лы, 2 ил. 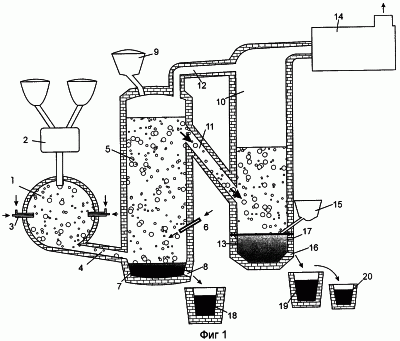
Изобретение относится к металлургии, в частности к получению металла в жидкофазных агрегатах непрерывного действия.
Среди известных процессов и агрегатов жидкофазного восстановления наиболее характерными являются агрегаты Корекс и Ромелт [1]. В агрегате Корекс [2] восстановление оксидов осуществляется в два этапа: в первом агрегате осуществляется твердофазное восстановление оксидов, этот полупродукт передается шнековыми питателями во второй агрегат жидкофазного действия, в котором получают чугун. Этот процесс и агрегат доведен до промышленной реализации, однако отличается достаточно сложной конструкцией, большой капиталоемкостью и энергоемкостью.
Сложность конструкции в значительной степени определяется наличием шнекового транспорта-полупродукта, что является также причиной дополнительных энергозатрат, а также тем, что процессы во втором жидкофазном агрегате находятся недалеко от состояния термодинамического равновесия, а металл и шлак длительное время находятся в контакте друг с другом, поэтому в этом агрегате возможно только получение чугуна, легирующие же примеси распределяются между металлом и шлаком в соответствии с константами распределения и большинство ценных составляющих безвозвратно теряется со шлаком.
В процессе Ромелт [3] все процессы прямого восстановления совмещены в одном агрегате, однако процессы, так же как и в агрегате Корекс, находятся близко к состоянию термодинамического равновесия, поэтому здесь также можно получать только чугун с содержанием углерода порядка 2%, в котором может содержаться некоторое, относительно небольшое, количество легирующих элементов: марганца, ванадия, титана и др. Однако подавляющая часть легирующих элементов уходит в шлак.
Известны многолетние попытки разработки технологий комплексной переработки руд, содержащих легирующие элементы, однако эффективных решений пока не найдено. Например [4], предложена технология практически безотходной переработки титаномагнетитовых концентратов с получением легированного ванадием и некоторыми другими элементами чугуна и кондиционного по оксидам титана шлака с содержанием TiO2 порядка 45%. Эту технологию предлагается реализовать в небольшой высокоавтоматизированной доменной печи, в которой можно было бы точно поддерживать состав шлака, поскольку шлак с высоким содержанием оксидов титана обладает весьма узким диапазоном текучести и обладает способностью к сворачиванию в связи с интенсивным карбидообразованием при снижении суммы оксидов железа и марганца ниже 5%. Реализация такой технологии в доменной печи сопряжена со значительными трудностями, поскольку опять же из-за близкого к термодинамически равновесному характеру процесса содержание оксидов железа в доменном шлаке обычно попадает в пределы 2-3%, то есть находится в опасной области с точки зрения карбидообразования и сворачивания шлака, что может приводить к аварийным остановкам печи.
Известные технологии карботермического и металлотермического получения ферросплавов, в том числе ферромарганца, ферросилиция и особенно ферротитана [5], обладают большой энергоемкостью, невысокой полнотой и некомплексностью извлечения легирующих элементов.
Наиболее близким к предлагаемому является [6] способ получения металла путем непрерывного рафинирования, включающий подачу в реакционную камеру жидкого металла, ввод газообразных и твердых окислителей, добавку сыпучих материалов, полный перевод металла и шлака в пенистую эмульсию, создание в реакционной камере повышенного пульсирующего давления и значительного отклонения системы от термодинамического равновесия путем создания самоорганизующейся системы химических реакций с газовыделением и отвода эмульсии в рафинирующий отстойник с критической скоростью истечения двухфазной жидкости, разделение в рафинирующем отстойнике металла и шлака и отвод газа через высокий слой эмульсии с определенной скоростью.
Этот способ реализуется в агрегате [6], содержащем сферическую реакционную камеру с каналом для подачи жидкого металла и сыпучих материалов, устройством для подачи газообразного кислорода, выполненным в виде встречно расположенных фурм, цилиндрический соединительный канал, рафинирующий отстойник с летками для отвода металла и шлака, а также патрубком для отвода газа.
Этот способ и агрегат имеют ряд существенных преимуществ по сравнению с рассмотренными выше [1-4]: малый удельный объем агрегата, низкая капиталоемкость и энергоемкость, высокие скорости химических реакций и возможность раздельного управления составом металла и шлака за счет изменения времени их пребывания в агрегате в условиях значительного отклонения процессов от термодинамического равновесия.
Однако и в этом агрегате возможно извлечение из рудных материалов главным образом железа, содержание же других элементов в железе составляет десятые или даже сотые доли процента, большинство же ценных элементов теряется со спускным шлаком. Кроме того, здесь возможна переработка лишь ограниченной доли железорудных материалов, поскольку из-за рафинировочного характера процесса роль основного восстановителя играет углерод чугуна.
Задачей изобретения является комплексное извлечение из железорудных концентратов и пылевидных металлосодержащих отходов всех металлов, имеющих сродство к кислороду меньше чем алюминий, повышение до 100% доли переработки твердых железосодержащих материалов с устранением из состава шихты жидкого чугуна, снижение энергетических затрат.
Сущность изобретения заключается в том, что в способе получения металлов из рудных материалов, включающем подачу в реакционную камеру сыпучих рудных материалов, ввод кислорода и восстановителя, перевод металла и шлака в пенистую эмульсию, создание в реакционной камере повышенного пульсирующего давления в пределах 0,4-3,0 МПа и организацию истечения двухфазной среды из реакционной камеры в рафинирующий отстойник с критической скоростью для значительного отклонения системы от термодинамического равновесия, разделение в рафинирующем отстойнике металла и шлака и отвод газа через высокий слой эмульсии с определенной скоростью, отличающийся тем, что получение металлов ведут при комплексной переработке титаномагнетитовых и других природнолегированных руд и концентратов, для разделения железосодержащей составляющей и легирующих элементов, содержащихся в шихте, кислород и восстановитель вводят в реакционную камеру через встречно расположенные фурмы спутными потоками, а соотношение кислорода и восстановителя, подаваемых в реакционную камеру и рафинирующий отстойник, рассчитывают из условия получения в верхних слоях газошлаковой эмульсии содержания оксидов железа в пределах 5-8% от массы шлака и корректируют его путем дополнительной подачи мелкого коксика или угля на верхний слои эмульсии в рафинирующем отстойнике, обедненный железом шлак в виде эмульсии подают в копильник шлакоприемника, куда подают углесодержащий восстановитель в стехиометрическом соотношении, обеспечивающем полное восстановление оксида железа из подаваемого шлака, а для восстановления всех остающихся в шлаке оксидов металлов, кроме кремния и алюминия, ведут алюмотермическое или комбинированное алюмосиликотермическое восстановление путем добавки алюминия или ферросилиция в стехиометрических или избыточных над ними соотношениях в соответствии с заданным составом получаемого ферросплава или для получения в качестве заданной конечной продукции титаносодержащего или шлака, обогащенного легирующими элементами, его подают из шлакоприемника непосредственно на гранулятор.
Способ осуществляется в агрегате для получения металлов из рудных материалов, включающем сферическую реакционную камеру с устройством подачи сыпучих рудных материалов, фурму для подачи кислорода, соединительный канал, рафинирующий отстойник с фурмой, встречно расположенной с соединительным каналом, копильником с леткой для отвода металла, отличающийся тем, что для получения металлов при комплексной переработке титаномагнетитовых и других природнолегированных руд и концентратов он имеет встречно расположенные фурмы для подачи кислорода, газообразного или пылевидного восстановителя спутными потоками, последовательно с рафинирующим отстойником установлен шлакоприемник, соединенный с рафинирующим отстойником двумя каналами: нижним наклонным каналом для отвода верхних слоев газошлаковой эмульсии в нижнюю часть шлакоприемника и верхним каналом для отвода газа через верхнюю часть шлакоприемника в котел-утилизатор, при этом к нижней части шлакоприемника в зависимости от вида конечной продукции пристыкован или второй копильник с устройством для подачи углеродсодержащего восстановителя и алюминия или ферросилиция, леткой для выпуска металла и шлака, или валковый гранулятор.
Сущность изобретения, следовательно, сводится к тому, что для решения задачи необходимо изменение конструкции агрегата таким образом, чтобы она позволяла разделить потоки восстанавливаемого железа и обедненного железом шлака, содержащего легирующие элементы, а также способа и режима подачи окислителей и восстановителей таким образом, чтобы в местах отбора соответствующих продуктов была создана преимущественно восстановительная атмосфера.
Способ получения металлов из рудных материалов реализуется в представленном на фиг.1 агрегате, на фиг.2 изображена нижняя часть шлакоприемника с валковым гранулятором.
Агрегат включает сферическую реакционную камеру 1 с устройством 2 подачи сыпучих материалов, фурмами 3 для подачи спутных потоков кислорода и газообразного или пылевидного восстановителя, соединительный канал 4, рафинирующий отстойник 5 с фурмой 6, встречно расположенной с соединительным каналом 4, первым копильником 7 с леткой 8 для отвода металла, устройством 9 для подачи углеродосодержащих и других сыпучих материалов, последовательно с рафинирующим отстойником 5 установлен шлакоприемник 10, к нижней части которого, в зависимости от вида конечной продукции, пристыковывается второй копильник 13 (фиг.1) или валковый гранулятор 21 (фиг.2), шлакоприемник 10 соединён с рафинирующим отстойником двумя каналами 11 и 12, нижний наклонный канал 11 служит для отвода верхних слоев газошлаковой эмульсии в нижнюю часть шлакоприемника 10, в центр верхнего среза второго копильника 13, верхний канал служит для отвода газа через верхнюю часть шлакоприемника 10 в котел-утилизатор 14, второй копильник 13 имеет устройство 15 для подачи карбо- и металлотермических восстановителей (кремния и алюминия), летки 16 и 17 для выпуска соответственно металла и шлака, а также емкости 18, 19 и 20 для приема соответственно первичного, вторичного металла и шлака. Валковый гранулятор 21 с конвейером 22 пристыковывается к нижней части шлакоприемника 10, если стоит задача получения кондиционного титансодержащего или какого-либо другого шлака.
Способ получения металлов из рудных материалов в соответствии с поставленной задачей осуществляется следующим образом. Порошкообразная шихта, состоящая из смеси оксидов железа и других металлов, вместе с частью твердых восстановителей подается в центральную зону реакционной камеры 1, где в месте встречи спутных потоков кислорода и природного газа, подаваемых через фурмы 3, образуется диск уплотнения, на котором в результате динамического взаимодействия происходит интенсивная турбулизация потока шихты и образование больших поверхностей для гетерогенного химического взаимодействия. При этом за счет неполного сжигания в реакционной камере части природного газа или другого восстановителя в соответствии с долей поданного кислорода происходит нагрев и частичное восстановление оксидов.
Соотношение восстановителей и кислорода, подаваемых в реакционную камеру и рафинирующий отстойник, рассчитывают из условий получения в верхних слоях газошлаковой эмульсии, находящейся в рафинирующем отстойнике, содержания оксидов железа в пределах 5-8% от массы шлака и корректируют путем дополнительной подачи коксика или угля на верхний слой эмульсии. Такое содержание оксидов железа обусловлено необходимостью устранения сворачивания шлака.
Образовавшаяся в реакционной камере 1 газовзвесь с объемным газосодержанием 0,98-0,99 через соединительный канал 4 подается в нижнюю часть рафинирующего отстойника 5 над верхним срезом первого копильника 7. При этом выходящая из соединительного потока двухфазная струя играет роль своеобразной динамической подушки или провальной решетки, отделяющей столб пенной газошлаковой эмульсии, играющей одновременно роль мокрой газоочистки, от металла, накапливающегося в первом копильнике 7 благодаря опусканию по вертикальным пристенным слоям капель металла, получающихся в результате восстановительных процессов в газошлаковой эмульсии. Таким образом, с учетом противодействия гравитационных и аэродинамических сил в рафинирующем отстойнике происходит сепарация металла и шлака, а также образуется неравномерное (по плотности, газосодержанию и химсоставу) распределение параметров по высоте агрегата. Распределенность содержания оксидов железа по высоте обуславливается также термодинамически неравновесным характером процессов, протекающих в реакционной камере и рафинирующем отстойнике, в том числе интенсивными потоками вещества и энергии, поступающими снизу через соединительный канал 4 из реакционной камеры 1.
Таким образом, использование в качестве рафинирующего отстойника вертикального колонного реактора с нижней подачей реакционной газовзвеси в сочетании с существенным отклонением процессов от термодинамического равновесия является важнейшим фактором, который обуславливает возможность разделения потока железоуглеродистого металла, оседающего в первом копильнике 7, и потока, обедненного железом и обогащенного легирующими элементами шлака, отводимого по наклонному каналу 11 в шлакоприемник 10 со вторым копильником 13, где производится восстановление оксидов легирующих элементов алюмосиликотермическим методом с получением, например, ферротитана, ферромарганца, содержащих ряд других легирующих элементов с учетом их содержания в исходной руде, в том числе ванадия, хрома и др.
Для этого во второй копильник 13 подают углеродосодержащий восстановитель в стехиометрическом соотношении, обеспечивающем полное восстановление оксидов железа из подаваемого в копильник 13 шлака, а восстановление всех остающихся в шлаке оксидов, кроме оксида алюминия, ведут алюмотермическим или комбинированным алюмосиликотермическим методом, производя добавки алюминия или ферросилиция в стехиометрических или избыточных над ними соотношениях, если это необходимо в соответствии с заданным составом ферросплава.
При получении углеродистых ферросплавов большинство легирующих элементов может быть восстановлено углеродом, в этом случае расход алюминия или ферросилиция может быть минимальным.
В случае если ставится задача получения кондиционного титаносодержащего шлака с содержанием TiO2 более 45%, к нижней части шлакоприемника 10 вместо копильника 13 пристыковываются валковый гранулятор 21 и этот шлак выдается в качестве конечного продукта на конвейер 22. Таким же образом поступают при решении задачи обезжелезивания и обогащения ванадиевых и других шлаков.
Преимущества данного изобретения по сравнению с прототипом заключаются в том, что установка последовательно с рафинирующим отстойником шлакоприемника 10 с копильником 13, соединенных с рафинирующим отстойником каналами 11 и 12, дает ряд дополнительных эффектов при переработке титаносодержащих и других природнолегированных руд. За счет выбора соотношений площадей сечений этих каналов можно автоматически поддерживать уровень газошлаковой эмульсии в определенном состоянии, отбирать эту эмульсию из верхних слоев столба газошлаковой пены, где содержание оксидов железа может быть минимизировано, и подавать в копильник шлакоприемника, где становится возможным осуществлять карбо, алюмо- или силикотермическое восстановление титанистого или, например, марганцовистого шлака.
Описанные выше конструктивные решения создают возможность разделения потоков железоуглеродистого металла и титаносодержащего (или другой легирующей металлсодержащего) шлака и возможность гибкого раздельного управления химсоставом металла в первом копильнике (рафинирующем отстойнике), шлака в верхней зоне рафинирующего отстойника (в том числе подачей коксика определенного гранулометрического состава, согласованного со временем пребывания) и шлака, отводимого в шлакоприемник 10.
В данном агрегате реализована также идея своеобразного внутреннего пневмотранспорта промежуточных продуктов из реактора в реактор: из реакционной камеры в рафинирующий отстойник, а затем в шлакоприемник, котел-утилизатор и другие устройства для утилизации вторичных энергоресурсов. Выведение процессов в газофазную область в сочетании с повышенным давлением и замкнутостью процесса от атмосферы позволило полностью использовать работу расширения реакционных газов. Это привело к значительному сокращению удельного объема агрегата и капитальных затрат, позволило избавиться от необходимости использования ряда промежуточных механических устройств (например, шнековых питателей, как в агрегате Корекс), дымососов и т.д. При этом резко снижается энергоемкость.
Следствием отмеченного выше преимущества является также реализованная в этом агрегате возможность алюмотермии расплавленного титанистого или другого шлака, что позволяет существенно снизить расход алюминия путем замены его ферросилицием и углеродом по сравнению с алюмотермией холодного сырья. Это еще одна составляющая снижения энергозатрат, повышения экономичности и экологичности.
Еще один положительный эффект достигается за счёт того, что через фурмы 3 подают спутный поток кислорода и восстановительного газа, например природного. Это дает возможность более гибко управлять тепловым балансом и восстановительными процессами и позволяет довести долю восстанавливаемых сыпучих материалов до 100%, устраняя необходимость применения в шихте жидкого чугуна.
Таким образом, сочетание перечисленных выше конструктивных решений и технологических операций позволило соединить одновременно в едином технологическом потоке и предельно малых его размерах возможности нескольких металлургических агрегатов и технологий, в том числе: доменной печи или агрегата типа «Корекс», агрегата для обезжелезивания титанистого концентрата в титановой промышленности (например, дуговой электропечи); агрегата для алюмотермического получения металлов, сродство которых к кислороду меньше, чем у алюминия.
Каждый из этих агрегатов имеет удельный объем значительно больший, чем у предлагаемого агрегата, который позволяет осуществлять комплексную переработку титаносодержащих и других природнолегированных полиметаллических руд на основе железа с максимальным извлечением легирующих элементов и минимальными отходами. Вариант же технологии переработки титаномагнетитовых концентратов с одновременным получением железоуглеродистого металла и титаносодержащего шлака с содержанием TiO2 более 45% является вообще безотходным.
Вариант реализации изобретения рассматривается на примере безотходной технологии переработки титаномагнетитового концентрата.
Пример
Способ реализуется в агрегате, представленном на фиг.1 и 2, следующим образом. Пылевидный титаномагнетитовый концентрат, имеющий следующий состав по основным компонентам, %:
FeO |
Fe2O3 |
Feобщ |
MnO |
SiO2 |
CaO |
MgO |
Al2O3 |
S |
P2O5 |
TiO2 |
27,0 |
46,4 |
53,5 |
0,6 |
2,8 |
0,8 |
2,0 |
2,3 |
0,4 |
0,03 |
17,6 |
в смеси с твердым или жидким восстановителем (коксиком, мазутом) с помощью вертикального шнекового питателя-дозатора 2 подается в сферическую реакционную камеру 1. Массовый расход концентрата составляет 4 кг/с, а массовый расход твердого восстановителя 1,1 кг/с. Этот поток шихты попадает на диск уплотнения, который создается в центре камеры, в месте встречи спутных потоков кислорода и газообразного или жидкого топлива – восстановителя, образуемых устройствами 3. Расход кислорода и природного газа составляет соответственно 1,4 м3/с и 0,38 м3/с. В результате взаимодействия вертикального потока сыпучих материалов с диском уплотнения и встречными спутными потоками создается высокая степень турбулизации и образуется газовзвесь с объемным газосодержанием 0,98-0,99, которая через соединительный канал 4 подается в рафинирующий отстойник 5.
Существование критической скорости истечения двухфазной среды и зависимость скорости этой среды от ее газосодержания позволяет использовать соединительный канал 4 в качестве динамического затвора. За счет изменения диаметра соединительного канала 4, а также соотношения притока и стока веществ можно изменять рабочее давление в реакционной камере 1, которое в данном случае меняется в диапазоне 2-3 атмосферы.
Пульсирующий характер давления в реакционной камере 1 с учетом принципа Ле-Шателье создается в результате того, что при достижении критической скорости истечения начинает расти давление в камере, при этом тормозятся реакции с газовыделением, изменяется газосодержание и объем смеси, что в свою очередь отражается на скорости истечения через соединительный канал 4.
Сжигание топлива в реакционной камере 1 осуществляется с недостатком кислорода, здесь происходит нагрев и частичное восстановление оксидов, но главная задача, решаемая в этой камере, – создание газовзвеси.
Большая часть восстановительных процессов завершается в рафинирующем отстойнике. Здесь же осуществляется частичное дожигание оксида углерода до диоксида. При этом дожигание происходит внутри газошлаковой эмульсии путем подачи кислорода через фурму 6. Расход кислорода выбирается в соответствии с тепловым балансом и составляет порядка 0,2-0,3 м/с.
Первая основная задача – разделение железосодержащей и титаносодержащей (вместе со всеми остальными оксидами) составляющих – решается в рафинирующем отстойнике 5 (вертикальном колонном реакторе) следующим образом. Поднимающийся сквозь высокий порядка 4-5 метров слой газошлаковой эмульсии (шлаковой пены) газ по высоте теряет вертикальную составляющую скорости. При этом возрастает гравитационная составляющая, действующая на частицы конденсированной фазы. Вследствие этого содержание более тяжелых оксидов, в первую очередь оксидов железа, уменьшается по высоте снизу вверх, что позволяет выдавать обедненные оксидами железа верхние слои газошлаковой эмульсии в шлакоприемник через наклонный канал 11.
Для обеспечения удовлетворительной текучести титанистого шлака содержание оксидов железа поддерживается в пределах 5-8%, что достигается путем выбора углеродосодержащих восстановителей в соотношении 0,95 от стехиометрически необходимого для реакции
(FeO)+Cmв=[Fe]+{CO}.
Корректировка степени восстановления оксидов железа в верхних слоях шлака в случае необходимости осуществляется подачей мелкого коксика или угля через устройство 9.
Восстановленное железо, имеющее плотность приблизительно в три раза большую, чем оксиды, опускается в первый копильник 7, главным образом через периферию рафинирующего отстойника 5, в связи с тем, что из-за параболического распределения вертикальной составляющей скорости эмульсии по диаметру рафинирующего отстойника и трения в пристенных слоях здесь наблюдается отрицательная (преимущественно гравитационная) составляющая скорости тяжелых частиц восстановленного железа. Таким образом, рафинирующий отстойник 5 (вертикальный колонный реактор) одновременно играет роль сепаратора шлака, отводящегося через наклонный канал 11 в шлакоприемник 10, металла, оседающего в первом копильнике 7, и газа, который отводится через канал 12.
Получающийся в первом копильнике 7 железоуглеродистый сплав с массовым расходом 2,08 кг/с имеет следующий состав, %:
Выпускается непрерывно или периодически в емкость 18.
Поступающий в шлакоприемник титанистый шлак с массовым расходом 1,42 кг/с имеет следующий состав, %:
FeO |
Fe2О3 |
MnO |
SiO2 |
CaO |
MgO |
Al2O3 |
S |
P2O5 |
TiO2 |
8,03 |
0,00 |
1,06 |
12,57 |
12,54 |
5,87 |
8,66 |
1,54 |
0,13 |
49,61 |
Шлак такого состава может служить ценным сырьем для титановой промышленности, поскольку он близок по составу к ильменитовому концентрату. Поэтому, если ставится задача выдачи этого шлака как товарного продукта, то к нижней части шлакоприемника пристыковывается валковый гранулятор 21 с конвейером 22, превращающий этот шлак в конечный продукт. На этом технологический процесс заканчивается. Подобная же технология может быть использована для обезжелезивания и обогащения ванадиевого шлака и т.п.
Если же ставится задача получения из этого шлака ферротитана, то к нижней части шлакоприемника пристыковывается вместо гранулятора второй копильник 13. Тогда шлак из рафинирующего отстойника 5 поступает по наклонному каналу 11 в шлакоприемник 10, в центр верхнего среза второго копильника 13. Сюда же из устройства 15 подаются мелкий коксик, ферросилиций и алюминий.
Порядок подачи и соотношение указанных восстановителей зависит от состава получаемого ферросплава и от теплового баланса системы металл – шлак во втором копильнике 13. Избыточное тепло реакций восстановления оксидов титана алюминием и кремнием отводится через гарнисажное охлаждение второго копильника 13, а также путем подачи баластных шлаковых составляющих, содержащих оксиды кремния и алюминия.
Восстановленный комбинированным углероднотермическим и металлотермическим методом ферротитан с массовым расходом 0,53 кг/с, имеющий состав, %:
Fe |
С |
Mn |
Si |
S |
P |
Ti |
Al |
23,45 |
0,20 |
0,99 |
0,97 |
0,00 |
0,02 |
74,38 |
0,00 |
выпускается в емкость 19, непрерывно или периодически. При этом расходы коксика, ферросилиция и алюминия составляют соответственно 0,014 кг/с; 0,21 кг/с и 0,14 кг/с. Образующийся при этом алюмосиликатный шлак с массовым расходом 1,25 кг/с при непрерывном выпуске выдается через летку 17 в емкость 20, а при периодическом выпуске – вместе с ферротитаном через летку 16. Этот шлак имеет следующий состав, %:
FeO |
Fe2O3 |
CaO |
SiO2 |
Al2O3 |
MgO |
MnO |
P2O5 |
S |
TiO2 |
0,05 |
0,01 |
14,75 |
37,55 |
32,15 |
6,90 |
0,81 |
0,14 |
1,81 |
5,83 |
Таким образом, выше рассмотрена непрерывная комплексная технология переработки титаномагнетитовых концентратов с предельно низкими энергетическими затратами, поскольку здесь осуществляется сначала практически полное разделение железосодержащей и титаносодержащей составляющих, а затем производится комплексное углероднотермическое, силикотермическое или алюмотермическое восстановление расплавленного горячего шлака. Таким образом, нет необходимости тратить кремний и особенно алюминий на нагрев шихты, как это делается во всех известных процессах получения ферротитана и других ферросплавов. Подобная же технология может быть использована для извлечения марганца, ванадия и других элементов.
Принципиальная возможность реализации способа подтверждена на опытно-промышленном агрегате производительностью 4 килограмма в секунду или 240 кг в минуту по металлосодержащей части шихты.
Источники информации
Формула изобретения
1. Способ получения металлов из рудных материалов, включающий подачу в реакционную камеру сыпучих рудных материалов, ввод кислорода и восстановителя, перевод металла и шлака в пенистую эмульсию, создание в реакционной камере повышенного пульсирующего давления в пределах 0,4-3,0 МПа и организацию истечения двухфазной среды из реакционной камеры в рафинирующий отстойник с критической скоростью для значительного отклонения системы от термодинамического равновесия, разделение в рафинирующем отстойнике металла и шлака и отвод газа через высокий слой эмульсии с определенной скоростью, отличающийся тем, что получение металлов ведут при комплексной переработке титаномагнетитовых и других природно-легированных руд и концентратов, для разделения железосодержащей составляющей и легирующих элементов, содержащихся в шихте, кислород и восстановитель вводят в реакционную камеру через встречно расположенные фурмы спутными потоками, а соотношение кислорода и восстановителя, подаваемых в реакционную камеру и рафинирующий отстойник, рассчитывают из условия получения в верхних слоях газошлаковой эмульсии содержания оксидов железа в пределах 5-8% от массы шлака и корректируют его путем дополнительной подачи мелкого коксика или угля на верхний слой эмульсии в рафинирующем отстойнике, обедненный железом шлак в виде эмульсии подают в копильник шлакоприемника, куда подают углесодержащий восстановитель в стехиометрическом соотношении, обеспечивающем полное восстановление оксида железа из подаваемого шлака, а для восстановления всех остающихся в шлаке оксидов металлов, кроме кремния и алюминия, ведут алюмотермическое или комбинированное алюмосиликотермическое восстановление путем добавки алюминия или ферросилиция в стехиометрических или избыточных над ними соотношениях в соответствии с заданным составом получаемого ферросплава или для получения в качестве заданной конечной продукции титансодержащего шлака или шлака, обогащенного легирующими элементами, его подают из шлакоприемника непосредственно на гранулятор.
2. Агрегат для получения металлов из рудных материалов, включающий сферическую реакционную камеру с устройством подачи сыпучих рудных материалов, фурму для подачи кислорода, соединительный канал, рафинирующий отстойник с фурмой, встречно расположенной с соединительным каналом, копильником с леткой для отвода металла, отличающийся тем, что для получения металлов при комплексной переработке титаномагнетитовых и других природно-легированных руд и концентратов он имеет встречно расположенные фурмы для подачи кислорода, газообразного или пылевидного восстановителя спутными потоками, последовательно с рафинирующим отстойником установлен шлакоприемник, соединенный с рафинирующим отстойником двумя каналами: нижним наклонным каналом для отвода верхних слоев газошлаковой эмульсии в нижнюю часть шлакоприемника и верхним каналом для отвода газа через верхнюю часть шлакоприемника в котел-утилизатор, при этом к нижней части шлакоприемника, в зависимости от вида конечной продукции, пристыкован второй копильник с устройством для подачи углеродсодержащего восстановителя и алюминия или ферросилиция и с леткой для выпуска металла и шлака или валковый гранулятор.
РИСУНКИ
|
|