|
(21), (22) Заявка: 2004129048/02, 04.10.2004
(24) Дата начала отсчета срока действия патента:
04.10.2004
(45) Опубликовано: 27.03.2006
(56) Список документов, цитированных в отчете о поиске:
RU 2211207 С2, 27.08.2003. US 3892610 А, 01.07.1975. GB 1168691 A, 07.02.1968. US 4124418 A, 07.11.1978. DE 2353360 A1, 07.05.1975.
Адрес для переписки:
614113, г.Пермь, ул. Чистопольская, 16, ФГУП “НИИПМ”
|
(72) Автор(ы):
Куценко Геннадий Васильевич (RU), Колосов Герман Георгиевич (RU), Чернов Михаил Андреевич (RU), Семенова Лидия Ивановна (RU), Божья-Воля Николай Сергеевич (RU), Ермолаев Сергей Валерьянович (RU), Уткин Виктор Павлович (RU), Тудвасев Виктор Иванович (RU)
(73) Патентообладатель(и):
Федеральное государственное унитарное предприятие “Научно-исследовательский институт полимерных материалов” (RU), Федеральное государственное унитарное предприятие “Пермский завод им. С.М. Кирова” (RU)
|
(54) СПОСОБ ВЫДЕЛЕНИЯ ПЕРХЛОРАТА АММОНИЯ ИЗ СУСПЕНЗИИ
(57) Реферат:
Изобретение относится к способу выделения фракции сверхтонкого помола перхлората аммония из суспензии в легколетучей жидкой среде при непрерывной подаче перистальтическим насосом в обогреваемый барабан, отводом из него паров в холодильник, сбором и возвратом конденсата на фазу изготовления суспензии. Ведение процесса в присутствии полиуретановых цилиндров с высотой и диаметром от 30 до 40 мм исключает налипание продукта на стенки аппарата и комкообразование его. Удаление остатков жидкой среды в перхлорате аммония после температурной отгонки производят путем вакуумирования с установкой в линии системы фильтров перед масляным вакуум-насосом, обеспечивается безопасное выделение перхлората аммония из суспензии с сохранением его дисперсности, уловом жидкой среды и возвратом ее в технологический цикл. 2 з.п. ф-лы, 1 ил. 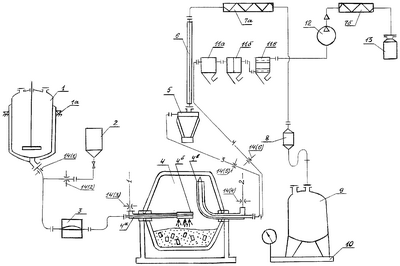
Изобретение относится к технике сушки паст, суспензий и влажных дисперсных материалов, в том числе взрывчатых веществ. Сушка дисперсных материалов является широко распространенным процессом, применяемым в различных областях промышленности. Наибольшее применение из способов сушки нашли: конвективная и контактная сушка в барабанных сушилках, метод распыления в кипящем слое, пневматическая в потоке горячего воздуха или газа.
Подробное описание теории сушки и аппаратурного оформления процессов дано авторами В.И.Муштаевым и В.М.Ульяновым в книге “Сушка дисперсных материалов”, Москва, “Химия”, 1988.
При изготовлении смесевого твердого ракетного топлива (СТРТ) в качестве окислителя используется перхлорат аммония (ПХА) с разной дисперсностью. Одним из способов получения фракции ПХА сверхтонкого помола со средним размером частиц менее 2 микрон является измельчение в бисерных мельницах в среде жидкого носителя, например хлористого метилена или жидких хладонов (фреонов). В качестве мелющих элементов применяют шарики из высокопрочного стекла.
В связи с тем, что ПХА в СТРТ вводится в сухом виде, требуется выделение его из суспензии.
Из анализа литературных источников и патентных материалов следует, что существующие способы и аппараты в основном разработаны для испарения и удаления паров воды при подаче горячего воздуха. При этом схемы процесса оформлены по открытому циклу, то есть удалением паров воды в атмосферу. Эти процессы неприемлемы при удалении многих легколетучих жидких сред, так как пары их загрязняют атмосферу, вредны для здоровья, при определенных концентрациях с воздухом образуют пожаровзрывоопасные смеси.
В связи с этим перспективной схемой выделения ПХА из суспензии является удаление паров жидкой среды с последующим уловом и возвратом в технологический цикл.
В применяемых в промышленности установках сушка с удалением влаги производится с подачей большого объема горячего воздуха. В этом случае эффективный улов жидких сред из смеси с воздухом затруднен. Кроме того, необходимость подачи большого объема воздуха приводит к созданию в аппарате значительного скоростного потока, приводящего к большому выносу частиц высушиваемого продукта из аппарата. Это создает напряженные условия работы фильтрующей системы при сушке особенно тонкоизмельченных продуктов, к которым относится фракция ПХА сверхтонкого помола.
Большинство материалов в процессе сушки, особенно в тонкоизмельченном состоянии, склонно к налипанию на стенки сушильного аппарата и комкообразованию. Эти факторы приводят к нарушению устойчивого режима сушки, забивке аппарата и к получению некондиционного продукта по дисперсности. Следует отметить, что при изготовлении СТРТ предъявляются жесткие требования по однородности гранулометрического состава.
Для устранения налипания продукта на стенки сушилок и разрушения комков, например, в барабанных сушилках внутри аппарата устанавливают скребки, лопатки, гребки и другие механизмы (Обзорная информация “Новая сушильная техника” в серии “Химическое и нефтяное машиностроение”, ЦНТИ Химнефтемаш, Москва, 1983 г., патент Великобритании №1168691, класс F4G, В1с, F4U, Р26в, заявл. 7.02.68 г.; патент России №1474411, класс Р26в, заявл.26.05.87 г.).
Наиболее близким к заявляемому объекту является патент Великобритании №1168691, класс F4G, В1с, F4U, F26в, заявл. 7.02.68 г. (прототип).
По этому патенту для сушки используется вращающийся горизонтальный обогреваемый барабан, внутри которого для рыхления и предотвращения налипания материала на стенки расположены продольные подвижные скребки. Перхлорат аммония является чувствительным к механическим воздействиям веществом (к удару и трению). Чувствительность его с уменьшением размера частиц повышается. При определенных механических воздействиях, что не исключается при наличии подвижных механизмов в аппарате, возможно возникновение очагов быстрораспространяющихся процессов объемного горения или взрыва с разрушением аппарата. Возможность механического воздействия усугубляется тем, что для съема налипшего продукта на стенки требуется обеспечение минимального зазора между ней и скребками. Необходимость в этом условии диктуется тем, что для обеспечения требуемых и воспроизводимых баллистических и физико-механических свойств СТРТ крайне необходимо сохранение дисперсности ПХА в процессе удаления жидкой среды.
Технической задачей изобретения является разработка безопасного способа выделения перхлората аммония из суспензии с сохранением его дисперсности, уловом жидкой среды и возвратом ее в технологический цикл. Технический результат достигается за счет того, что суспензию перхлората аммония в жидкой среде непрерывно подают в барабан перистальтическим насосом из расходной емкости, установленной на станине с тензодатчиками, фиксирующими массу, по трубопроводу, входящему до середины барабана охлаждаемой частью и насаженной на его конец эластичной насадке с продольными прорезями, и разбрызгивают в начале на полиуретановые цилиндры диаметром и высотой 30-40 мм, а в последующем и на постепенно накапливаемый слой перхлората аммония до соотношения между загрузками полиуретановых цилиндров и перхлората аммония
при непрерывном удалении паров жидкой среды из обогреваемого барабана при температуре теплоносителя выше температуры кипения жидкой среды с направлением ее паров через циклон в холодильник, из которого конденсат поступает в приемную емкость, установленную на весах с дистанционной передачей информации на пульт управления. Процесс продолжают после окончательной остановки подачи суспензии до полного прекращения поступления кондесата в приемную емкость при периодическом включении барабана на вращение на 5-10 минут через каждые 45 минут.
Перед началом подачи суспензии, а также после прекращения подачи ее перед вынужденными длительными остановками продолжительностью более 30 минут и после окончательной остановки подачи суспензии, для вытеснения суспензии из трубопровода в него до полного заполнения подают жидкую среду перистальтическим насосом, при этом трубопровод охлаждают холодной водой. Окончательное удаление жидкой среды производят путем вакуумирования до остаточного давления в барабане не более 20 мм рт. ст. масляным вакуум-насосом через систему фильтров с конденсацией паров в холодильнике по циклу:
– вращение барабана в течение 3-5 минут,
– выдержка в течение 10-15 минут,
– вакуумирование в течение 40-45 минут.
Выделение перхлората аммония из суспензии ведут по технологической схеме, приведенной на чертеже. Основную операцию по выделению перхлората аммония из суспензии проводят в обогреваемом барабане 4. Суспензию из расходной емкости 1, установленной на станине с тензодатчиками 1а, при открытом затворе 14(1) перистальтическим насосом 3 подают по трубопроводу в барабан 4 после его предварительного прогрева. Перед подачей суспензии трубопровод заполняют жидкой средой, используемой при изготовлении суспензии, подачей ее при помощи перистальтического насоса из бачка 2 при открытом затворе 14(2). На конце трубопровода установлена трубчатая насадка 4б из эластичного полиуретана с прорезями, проходя которые суспензия разбрызгивается. При поступлении суспензии в горячую полость барабана она попадает в начале процесса на полиуретановые элементы, а затем по мере накопления на слой перхлората аммония с температурой выше температуры кипения жидкой среды. Последняя легко испаряется. Пары жидкой среды из-за повышенной упругости паров по коленообразному соплу 4в линии 3 при открытом затворе 14(5) поступают в обогреваемый циклон 5, далее по вертикальному обогреваемому трубопроводу следуют в холодильник 7а. В циклоне 5 происходит отделение и высаживание уносимых парами частиц перхлората аммония. Конденсат жидкой среды, проходя гидрозатвор 8, поступает в сборник 9, установленный на весах 10, показания которых передаются на пульт управления. Жидкую среду периодически из сборника сливают и направляют на начальную фазу изготовления суспензии перхлората аммония. В случае прекращения поступления жидкой среды в сборник в процессе подачи суспензии, что свидетельствует о забивке сопла, последнее продувают подачей сжатого воздуха по линии 2, открыв затвор 14(4).
После прекращения подачи суспензии и прекращения поступления жидкой среды в сборник 9 линию 3 отсоединяют от барабана и подсоединяют к нему линию 4 вакуумирования. При включенном вакуум-насосе и открытом затворе 14(6) остатки паров жидкой среды по линии 4 проходят через систему фильтров, состоящую из вакуум-ловушки 11а, каплеуловителя 11б и фильтра 11в. В системе фильтров происходит отделение уносимых из барабана частиц перхлората аммония парами жидкого носителя. Пары жидкого носителя из вакуум-насоса поступают в холодильник 7б, где конденсируются, а конденсат поступает в приемную емкость 13. Конденсат из приемной емкости 13 подвергается регенерации (очистке от примесей масла) и используется при изготовлении суспензии перхлората аммония.
В начале процесса проводят следующие подготовительные операции:
– В барабан через люк загружают цилиндры диаметром и высотой от 30 до 40 мм из износостойкого полиуретана. Их используют для предотвращения налипания перхлората аммония на стенки барабана и исключения комкования. При наличии полиуретановых цилиндров разбрызгиваемые капли будут падать не на голые стенки барабана, а на цилиндры, тем самым исключается возможность налипания и коркообразования. За счет развитой поверхности цилиндров толщина слоя суспензии уменьшается, что будет способствовать более быстрому удалению жидкой среды. В то же время цилиндры, находясь в постоянном движении и трении как между собой, так и со стенкой барабана, способствуют диспергированию перхлората аммония и предотвращению образования комочков. Упругость полиуретановых цилиндров исключает жесткие удары и трение, что важно при переработке чувствительных к механическим воздействиям тонкоизмельченных частиц перхлората аммония. Экспериментальными работами показано минимально допустимое количество цилиндров по отношению к максимальной загрузке перхлората аммония в барабан по массе соответственно 1: 10. В производственных условиях возникает необходимость изготовления партий перхлората аммония сверхтонкого помола с меньшей массой до 2,5 раз. Таким образом, соотношение между загрузками полиуретановых цилиндров и перхлората аммония составит 
– Перед началом подачи суспензии производят прогрев барабана. При этом находящийся в полости барабана трубопровод также нагревается. В связи с этим при поступлении первых порций суспензии с легколетучей жидкостью последняя при контакте с горячей поверхностью интенсивно испаряется. При этом произойдет быстрое повышение концентрации в переднем фронте суспензии с забивкой трубопровода. Это можно исключить, если непосредственно перед подачей суспензии по линии транспортировать с охлаждением чистую жидкую среду, которая приведет к охлаждению трубопровода. При последующей подаче суспензии по трубопроводу исключается преждевременное подсыхание.
В процессе ведения технологического процесса возможны вынужденные остановки. В этом случае, если продолжительность остановки будет превышать 30 минут, при остатке суспензии в трубопроводе будет происходить улетучивание жидкой среды с забивкой линии сухим перхлоратом аммония. При этом для дальнейшего возобновления процесса потребуется чистка трубопровода. Этого можно избежать, если остающуюся порцию суспензии в трубопроводе вытеснить подачей чистой жидкой среды вслед за прекращением подачи суспензии. Аналогично следует поступить после полного окончания подачи суспензии, т.е. опорожнения расходной емкости, чтобы сохранить чистоту трубопровода для последующих циклов работы. При поступлении суспензии в зону с высокой температурой, выше температуры кипения, происходит быстрое испарение жидкой среды с парообразованием. Упругость паров растет с повышением температуры. За счет упругости паров последние по открытому каналу (трубопроводу) выходят за пределы барабана и в дальнейшем при поступлении и охлаждении в холодильнике упругость паров падает. При соединении барабана и холодильника трубопроводом из-за перепада упругости паров происходит самопроизвольный отток паров из барабана. Для сохранения упругости паров вертикальные участки трубопровода необходимо нагревать, в противном случае произойдет конденсация паров с закупоркой линии жидкостью. При непрерывной подаче суспензии формируется непрерывный поток паров с определенной скоростью. Восходящий поток захватывает часть мелких частиц перхлората аммония. Концентрация пылевоздушной смеси, как правило, убывает с увеличением высоты. Для уменьшения уноса частиц перхлората аммония из аппарата вывод паров следует производить из верхней зоны барабана. Для дополнительной очистки паров от частиц перхлората аммония в линии отгонки паров необходимо установить обогреваемый циклон. Конденсированную жидкость после холодильника представляется возможным собирать в емкость, установив ее на весы с циферблатной головкой с передачей показаний массы на пульт управления.
Процесс выделения перхлората аммония из суспензии после прекращения подачи ее и промывки жидкой средой продолжают до полного прекращения поступления ее после холодильника в приемную емкость. При этом барабан включают на вращение на 5-10 минут через каждые 45 минут. Этот процесс необходим для разрыхления перхлората аммония и обновления нижних слоев для полноты отгонки жидкой среды. После прекращения отгонки жидкой среды она частично остается в объеме барабана и в слое перхлората аммония. Для полного освобождения от остатков жидкой среды подсоединяют линию 4 вакуумирования и проводят вакуумирование включением масляного вакуум-насоса с установленной системой фильтров. Система фильтров служит для улова частиц перхлората аммония с целью исключения попадания их в масляный насос. Попадание перхлората аммония в масляный насос представляет опасность, так как смесь перхлората аммония имеет повышенную чувствительность к механическим воздействиям.
Процесс вакуумирования ведут до достижения остаточного давления в системе не более 20 мм рт. ст. по циклу:
1. Вращение барабана в течение 3-5 минут.
2. Остановка барабана и выдержка в течение 10-15 минут.
3. Вакуумирование в течение 40-45 минут при остановленном барабане.
Пары жидкой среды после насоса охлаждают в холодильнике и принимают в тару.
Периодическое и кратковременное вращение барабана необходимо для рыхления перхлората аммония и полноты удаления жидкой среды. Более длительное вращение приведет к большей запыленности частицами перхлората аммония пространства над слоем его в барабане. Для снижения процентного содержания перхлората аммония в свободном объеме барабана и тем самым уменьшения уноса необходима выдержка после остановки аппарата в течение 10÷15 минут. На начальном этапе вакуумирования при наличии паров жидкой среды в объеме барабана уровень остаточного давления достаточно большой. По мере уменьшения содержания паров значение остаточного давления уменьшается, достигая уровня не более 20 мм рт. ст, что свидетельствует о полноте вакуумирования. Дополнительно полноту отсоса паров жидкой среды контролируют по отсутствию поступления ее в приемную тару.
Технологический процесс выделения перхлората аммония из суспензии отработан на ФГУП “Пермский завод им. С.М.Кирова”.
Формула изобретения
1.Способ выделения перхлората аммония из суспензии, включающий подачу суспензии в обогреваемый и вращающийся барабан, удаление жидкой среды, отличающийся тем, что суспензию перхлората аммония в жидкой среде непрерывно подают в барабан перистальтическим насосом из расходной емкости, установленной на грузоприемные тензодатчики, по трубопроводу, входящему до середины барабана охлаждаемой частью, и насаженной на его конец эластичной насадке с продольными прорезями, и разбрызгивают сначала на полиуретановые цилиндры диаметром и высотой от 30 до 40 мм, а в последующем и на постепенно накапливаемый слой перхлората аммония до соотношения между загрузками полиуретановых цилиндров и перхлората аммония 1:4÷10 при непрерывном удалении паров жидкой среды из обогреваемого барабана при температуре теплоносителя выше температуры кипения жидкой среды, с направлением паров через циклон в холодильник, из которого конденсат поступает в приемную емкость, установленную на весах с дистанционной передачей информации на пульт управления, процесс продолжают после окончательной остановки подачи суспензии до полного прекращения поступления конденсата в приемную емкость при периодическом включении барабана на вращение в течение 5-10 мин через каждые 45 мин.
2. Способ по п.1, отличающийся тем, что перед началом подачи суспензии, а также после прекращения подачи ее перед вынужденными длительными остановками продолжительностью более 30 мин и после окончательного прекращения подачи суспензии для вытеснения ее из трубопровода в него до полного заполнения подают перистальтическим насосом жидкую среду, при этом трубопровод охлаждают холодной водой.
3. Способ по п.1 или 2, отличающийся тем, что окончательное удаление жидкой среды производят путем вакуумирования до остаточного давления в барабане не более 20 мм рт. ст. масляным вакуум-насосом через систему фильтров с конденсацией паров в холодильнике по циклу: вращение барабана от 3 до 5 мин, выдержка от 10 до 15 мин, вакуумирование от 40 до 45 мин.
РИСУНКИ
|
|