|
(21), (22) Заявка: 2004125995/02, 30.08.2004
(24) Дата начала отсчета срока действия патента:
30.08.2004
(45) Опубликовано: 20.03.2006
(56) Список документов, цитированных в отчете о поиске:
SU 1425245 А1, 23.09.1988. SU 986995 А, 07.01.1983. BG 51734 А, 16.08.1993. US 4547221 А, 15.10.1985. JP 2001-279368 А, 10.10.2001.
Адрес для переписки:
455002, г. Магнитогорск, ул. Кирова, 93, ОАО “ММК”, отдел рационализации, изобретательства и патентной работы
|
(72) Автор(ы):
Морозов Андрей Андреевич (RU), Колокольцев Валерий Михайлович (RU), Вдовин Константин Николаевич (RU), Петроченко Елена Васильевна (RU), Молочков Павел Александрович (RU), Ширяев Олег Петрович (RU), Пономарев Андрей Федорович (RU), Носов Василий Леонидович (RU), Новицкий Руслан Витальевич (RU)
(73) Патентообладатель(и):
Открытое акционерное общество “Магнитогорский металлургический комбинат” (RU)
|
(54) ЧУГУН
(57) Реферат:
Изобретение относится к металлургии, в частности к легированным чугунам. Может использоваться для изготовления деталей, работающих в условиях интенсивного изнашивания при высоких температурах до 900°С, например валков горячей прокатки, бандажей и роликов проволочных и ленточных станов и др. Чугун содержит, мас.%: углерод 2,8-3,2; кремний 0,2-0,6; марганец 0,2-0,6; хром 20,0-26,0; молибден 0,8-1,2; титан 0,2-0,4; ванадий 3,5-4,2; медь 0,5-0,8; бор 0,01-0,03; вольфрам 1,8-2,2; железо – остальное. Техническим результатом является повышение износостойкости, жаростойкости и теплостойкости. 2 табл.
Изобретение относится к металлургии, а именно к легированным чугунам, используемым для изготовления деталей, работающих в условиях интенсивного изнашивания при высоких температурах до 900°С, и может быть использовано для изготовления бандажей и роликов проволочных и ленточных станов, валков горячей прокатки и т.п.
Известен чугун, содержащий углерод, кремний, марганец, хром, ванадий, молибден, алюминий, кальций, церий, иттрий и железо при следующем соотношении компонентов, мас.%:
Углерод |
2,00-3,50 |
Кремний |
0,80-1,00 |
Марганец |
0,30-0,60 |
Хром |
12,0-20,0 |
Ванадий |
3,20-4,00 |
Молибден |
0,50-0,90 |
Алюминий |
0,05-0,15 |
Кальций |
0,001-0,05 |
Церий |
0,11-0,20 |
Иттрий |
0,05-0,09 |
Железо |
остальное |
(см. авт.св. СССР №1280039; С 22 С 37/10).
Недостатком известного чугуна являются низкие тепло-, жаро-, износостойкие свойства, так как он содержит редкоземельные металлы, которые образуют неметаллические включения (оксиды, сульфиды, оксисульфиды и др.) с высокой плотностью, трудноудалимые из расплава. Кроме того, при охлаждении уже твердого чугуна кристаллические оксисульфиды РЗМ (например, церия) вследствие уменьшения растворимости расстекловываются, приобретают остроугольную форму, что также приводит к снижению свойств деталей.
Наиболее близким аналогом к заявляемому чугуну является износостойкий чугун, используемый для изготовления деталей, работающих в условиях абразивного износа, содержащий следующие компоненты, мас.%:
Углерод |
2,2-3,6 |
Кремний |
0,5-1,5 |
Марганец |
3,0-4,0 |
Хром |
13,0-24,0 |
Молибден |
0,3-0,4 |
Титан |
0,2-0,4 |
Ванадий |
6,5-9,0 |
Медь |
1,0-1,5 |
Бор |
0,005-0,02 |
(см., авт.св. СССР №1425245, С 22 С 37/10).
Чугун не обладает достаточной износостойкостью из-за высокого содержания марганца, который приводит к снижению точки начала мартенситного превращения. При этом стабильность и количество остаточного аустенита возрастают, а износостойкость и твердость снижаются. Кроме того, пониженное содержание молибдена и хрома и высокое содержание кремния, углерода, ванадия уменьшает прокаливаемость чугуна, приводит к образованию крупных заэвтектических карбидов и обеднению металлической основы легирующими элементами, что снижает устойчивость чугуна к высокотемпературному абразивному изнашиванию, тепло- и жаростойкость.
В основу изобретения поставлена задача – разработать состав чугуна, обладающего одновременно комплексом высоких технических свойств: износостойкостью, жаростойкостью, теплостойкостью.
Поставленная задача решается тем, что известный чугун, содержащий углерод, кремний, марганец, хром, молибден, титан, ванадий, медь, бор и железо, согласно изобретению дополнительно содержит вольфрам при следующем соотношении компонентов, мас.%:
Углерод |
2,8-3,2 |
Кремний |
0,2-0,6 |
Марганец |
0,2-0,6 |
Хром |
20,0-26,0 |
Молибден |
0,8-1,2 |
Титан |
0,2-0,4 |
Ванадий |
3,5-4,2 |
Медь |
0,5-0,8 |
Бор |
0,01-0,03 |
Вольфрам |
1,8-2,2 |
Железо |
остальное |
Известно применение вольфрама в чугунах в качестве легирующего элемента (См. Ри Хосен, Ри Э.Х. Комплексно-легированные чугуны специального назначения. – Владивосток: Дальнаука, 2000 г., 287 с.).
В заявляемом чугуне вольфрам, также как и в известном чугуне, предназначен для легирования. Однако наравне с известным техническим свойством вольфрам проявляет новое техническое свойство, заключающееся в обеспечении чугуну требуемой тепло-, жаро-, износостойкости за счет комплексного воздействия на его структуру: инвертирующее, твердорастворное, композиционное и дисперсионное упрочнение.
На основании вышеизложенного можно сделать вывод, что для специалиста заявляемый чугун не следует явным образом из известного уровня техники, а следовательно, соответствует условию патентоспособности “изобретательский уровень”.
Введение вольфрама (W) в заявляемый чугун в количестве 1,8-2,2 мас.% придает чугуну комплекс высоких технических свойств: тепло- и жаростойкость при одновременном повышении износостойкости. Это обеспечивается за счет того, что в чугуне вольфрам легирует металлическую матрицу и образует сложные, устойчивые карбиды типа М6С, содержащие, кроме вольфрама, молибден, хром, ванадий. Вольфрам, молибден, ванадий при совместном присутствии в чугуне в заявляемых количествах затрудняют распад мартенсита, обеспечивая высокие тепло- и жаростойкость. Одновременно с этим нерастворенная часть карбида М6С приводит к повышению износостойкости чугуна. Наличие в чугуне вольфрама в количестве более 2,2 мас.% приводит к ухудшению его теплопроводности, а следовательно, к увеличению склонности отливок к образованию горячих и холодных трещин, а также карбидной неоднородности. При содержании вольфрама менее 1,8 мас.% снижаются тепло- и жаростойкость чугуна.
Введение в чугун углерода (С) в заявляемом количестве обеспечивает образование карбидов типа М7С3, которые способствуют повышению износостойкости чугуна. Введение в чугун углерода в количестве менее 2,8 мас.% приводит к увеличению доли первичного аустенита, а в количестве более 3,2 мас.% приводит к уменьшению содержания легирующих компонентов в твердом растворе, нарушению однородности литой структуры за счет выделения крупных разветвленных карбидов. И то, и другое отрицательно сказывается на свойствах чугуна.
Кремний (Si) в заявляемом количестве, являясь технологической добавкой, распределяется при кристаллизации между аустенитом и эвтектическим расплавом, улучшает жидкотекучесть чугуна. Содержание кремния в количестве менее 0,2 мас.% не обеспечивает достаточной жидкотекучести чугуна, а более 0,6 мас.% снижает прокаливаемость, увеличивает верхнюю критическую скорость отбеливания чугуна, уменьшая его отбеливаемость, а также приводит к увеличению хрупкости отливок.
Марганец (Mn) в заявляемом количестве повышает прокаливаемость и жаростойкость чугуна. Увеличение содержания марганца более 0,6 мас.% приводит к понижению точки начала мартенситного превращения и возрастанию стабильности остаточного аустенита, обеднению металлической основы чугунов углеродом и хромом, что снижает тепло-, жаро- и абразивостой кость. При содержании марганца менее 0,2 мас.% снижаются прокаливаемость и жаростойкость чугуна.
Хром (Cr) в заявляемом количестве необходим для образования комплексных карбидов типа (Fe,Cr)7С3, придающих чугуну максимальную износостойкость. При содержании хрома менее 20 мас.% в структуре чугуна образуются наряду с карбидами (Fe,Cr)7С3 карбиды (Fe,Cr)3С, что снижает тепло-, жаро-, износостойкость чугуна. При содержании хрома более 26 мас.% в структуре чугуна появляются крупные и хрупкие карбиды типа (Fe,Cr)23С6, что приводит к снижению тепло-, жаро-, износостойких свойств. Кроме этого, увеличивается общая доля крупных первичных карбидов, что также приводит к снижению указанных свойств.
Титан (Ti) в заявляемом количестве способствует измельчению зерна, устраняет столбчатое строение отливок, модифицирует чугун, что позволяет получать однородные механические свойства по толщине отливок. Кроме того, титан способствует образованию эвтектоида с достаточно высокой твердостью и исключению цементитной эвтектики. Совокупность этих факторов приводит к увеличению вязкости чугуна и уменьшению выкрашивания эвтектики в процессе изнашивания. Влияние титана на свойства чугуна более эффективно при введении его совместно с ванадием, молибденом, бором.
При содержании титана менее 0,2 мас.% износостойкость чугуна будет незначительной, так как невелико количество карбидов TiC. При содержании титана свыше 0,4 мас.% в чугуне образуются карбонитриды титана и пленочные включения оксидов больших размеров, которые располагаются по границам аустенитных зерен, что снижает износостойкость и жидкотекучесть чугуна.
Легирование чугуна медью снижает необходимое (критическое) содержание ванадия в чугуне, обеспечивающее инверсию микроструктуры, что способствует полному устранению ледебурита. Медь также активно влияет на структурообразование отливок после затвердевания. Изменением условий охлаждения и содержания меди можно регулировать структуру основы чугуна от перлитной до мартенситно-аустинитной с различным количественным соотношением фаз и морфологию карбидной фазы. Увеличение скорости охлаждения при затвердевании (заливка в кокиль, изменение толщины стенки отливки и т.п.) данного чугуна с медью изменяет размеры и форму карбидов. Карбиды становятся менее разветвленными, увеличивается их дисперсность, а также измельчается эвтектика.
Введение меди в количестве 0,5-0,8 мас.% в заявляемый чугун устраняет продукты перлитного распада в литой структуре, повышает износо-, тепло- и химическую стойкость, прокаливаемость, теплопроводность. При введении в чугун меди в количестве менее 0,5 мас.% повышение указанных свойств не наблюдается, а увеличение количества меди свыше 0,8 мас.% приводит к появлению в структуре полей, обогащенных медью, что снижает износостойкость и жаростойкость чугуна.
Бор (В) в количестве (0,01-0,03%), являясь поверхностно-активным элементом, упрочняет и стабилизирует границы зерен, замедляет рост кристаллов, способствуя измельчению структуры, что повышает износостойкость чугуна в условиях абразивного износа и высоких температур.
Присадка бора меньше 0,01 мас.% малоэффективна, а больше 0,03 мас.% приводит к охрупчиванию вследствие выделения гексаборидов, образованию термических трещин, огрублению структуры и, следовательно, снижению свойств чугуна.
Молибден (Мо) в заявляемом количестве оказывает легирующее и модифицируемое воздействие на структуру чугуна, увеличивает его прокаливаемость и закаливаемость. Легирует твердый раствор, что повышает стабильность структуры в условиях эксплуатации и его износо-, тепло-, жаростойкость. Молибден повышает жаростойкость чугуна за счет увеличения содержания хрома в твердом растворе. Вводить молибден в чугун в количествах, выходящих за заявляемые пределы, нецелесообразно. Введение в чугун молибдена в количестве менее 0,2 мас.% неэффективно. При содержании молибдена более 1,2 мас.% возрастает склонность к раздельной кристаллизации эвтектических фаз и образованию конгломератных структур.
Ванадий (V) в заявляемом количестве образует с углеродом специальные карбиды типа VC с высокой микротвердостью (HV 3000). Кроме того, в структуре чугуна заявляемого химического состава образуются два вида ванадиевых эвтектик: двойная аустенитно-ванадиево-карбидная и тройная аустенитно-хромо-ванадиево-карбидная, которые, являясь композиционными упрочнителями, значительно повышают тепло- и жаростойкие свойства чугуна и износостойкость.
При содержании ванадия менее 3,5 мас.% доля эвтектик в структуре чугуна уменьшается, что снижает указанные выше свойства, а при содержании ванадия более 4,2 мас.% наблюдается его переизбыток, который препятствует приросту свойств чугуна, а также способствует выделению крупных конгломератов карбидов.
Пример. В индукционной тигельной печи емкостью 60 кг с основной футеровкой выплавляли опытные составы заявляемого чугуна (составы №1-5, табл.1) и чугуна, взятого за прототип (составы №6, 7, табл.№1), по общепринятой технологии. Титан, бор, ванадий, хром, вольфрам, медь, молибден вводили в чугун в виде ферротитана ФТи 35, ферробора ФБи 20, феррованадия ФВд 38, феррохрома ФХ 72, ферровольфрама ФВ 65, меди М1, ферромолибдена ФМ 65.
Износостойкость определяли согласно ГОСТ 23.208-79. Износостойкость исследуемых образцов оценивали путем сравнения их износа с износом эталонного образца. В качестве эталона использовали сталь 45.
Для определения теплостойкости чугуна проводили 4-х часовой нагрев образцов при температуре 650, 680, 710°С в соляной ванне, после чего измеряли твердость по Роквеллу (HRC.)
Жаростойкость оценивали по ГОСТ 6130-71 после выдержки в печи в течение заданного времени (100 ч) при постоянной температуре (900°С) весовым методом по увеличению массы образца.
Результаты испытаний образцов, изготовленных из заявляемого чугуна (составы №1-5) и чугуна, взятого за прототип (составы №6 и 7), приведены в таблице №2.
Полученные результаты позволяют сделать вывод о том, что заявляемый чугун по сравнению с прототипом имеет в среднем:
– на 36,8% выше износостойкость;
– на 21,8% выше жаростойкость;
– на 17,8% выше теплостойкость при 650°С, на 28,4% – при 680°С, на 19,0% – при 710°С.
Использовать составы чугунов с содержанием компонентов, выходящих за заявляемые пределы (состав №1 и 5), нецелесообразно, так как в этих случаях у чугунов наблюдается снижение вышеуказанных свойств.
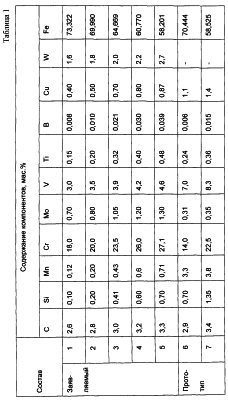
Таблица 2 |
Образцы, изготовленные |
Теплостойкость HRCэ при температуре, °С |
Жаростойкость  |
Относительная износостойкость |
из чугуна |
650 |
680 |
710 |
Заявляемого состава |
1 |
42 |
35 |
30 |
30,2 |
9,7 |
|
45 |
41 |
35 |
26,4 |
10,5 |
2 |
48 |
45 |
36 |
24,1 |
11,8 |
|
|
50 |
47 |
38 |
23,6 |
12,6 |
|
3 |
|
|
|
|
|
|
4 |
44 |
38 |
33 |
30,7 |
10,1 |
|
5 |
|
|
|
|
|
Состава прототипа |
6 |
39 |
32 |
30 |
32,3 |
8,1 |
|
42 |
37 |
31 |
30,9 |
8,9 |
7 |
|
|
|
|
|
Формула изобретения
Чугун, содержащий углерод, кремний, марганец, хром, молибден, ванадий, титан, медь, бор и железо, отличающийся тем, что он дополнительно содержит вольфрам при следующем соотношении компонентов, мас.%:
Углерод |
2,8-3,2 |
Кремний |
0,2-0,6 |
Марганец |
0,2-0,6 |
Хром |
20,0-26,0 |
Молибден |
0,8-1,2 |
Титан |
0,2-0,4 |
Ванадий |
3,5-4,2 |
Медь |
0,5-0,8 |
Бор |
0,01-0,03 |
Вольфрам |
1,8-2,2 |
Железо |
Остальное |
|
|