|
(21), (22) Заявка: 2004113324/04, 29.04.2004
(24) Дата начала отсчета срока действия патента:
29.04.2004
(43) Дата публикации заявки: 10.10.2005
(45) Опубликовано: 20.03.2006
(56) Список документов, цитированных в отчете о поиске:
RU 2109033 C1, 20.04.1998. RU 2120464 C1, 20.10.1998. US 3250697 A, 10.05.1966. RU 2167187 C1, 20.05.2001. GB 1566052 A1, 30.04.1980.
Адрес для переписки:
420045, г.Казань, ул. Н. Ершова, 35а, ГУП РТ ВНИИУС
|
(72) Автор(ы):
Мазгаров Ахмет Мазгарович (RU), Гарифуллин Ришат Гусманович (RU), Шакиров Фоат Гафиевич (RU), Хрущева Ирина Константиновна (RU), Вильданов Азат Фаридович (RU), Аюпова Нэля Ринатовна (RU)
(73) Патентообладатель(и):
ГУП РТ Всероссийский научно-исследовательский институт углеводородного сырья (RU)
|
(54) СПОСОБ ОЧИСТКИ ТЯЖЕЛОЙ НЕФТИ ОТ СЕРОВОДОРОДА
(57) Реферат:
Изобретение относится к способам очистки нефти и газоконденсата от сероводорода и меркаптанов и может быть использовано в газонефтедобывающей и нефтеперерабатывающей промышленности. Способ ведут путём окисления кислородом воздуха, растворенного в нефти под давлением до 2,5 МПа, при 20-70°С в присутствии раствора аммониевых солей сульфофталоцианинов кобальта в 20-30%-ном водном растворе аммиака. В сырье вводят из расчета на 1 моль сероводорода 0,1-1,6 молей NH4OH; 0,01-0,5 г фталоцианинового катализатора и 0,05-0,1 м3 воздуха. Используют аммониевые соли сульфо-, дисульфо-, тетрасульфо-, дихлордисульфо- и дихлордиоксидисульфофталоцианинов кобальта. Часть отработанного аммиачного катализаторного раствора отделяют от очищенного сырья и возвращают в процесс. Способ позволяет дезодорирующую очистку сырья проводить с минимальными расходами реагентов и с низкими энергетическими затратами непосредственно в промысловых условиях. 9 з.п. ф-лы, 2 табл., 1 ил. 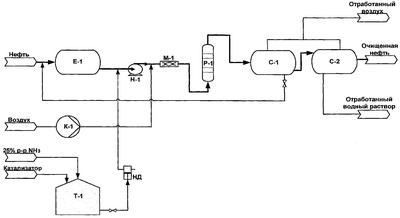
Изобретение относится к способам очистки углеводородного сырья от сероводорода и меркаптанов и может быть использовано в газонефтедобывающей и нефтеперерабатывающей промышленности.
В тяжелой высокосернистой нефти даже после сепарации и стабилизации может присутствовать до 0,06% (600 ppm) сероводорода. Присутствие высокотоксичного сероводорода создает неприятный запах и экологические проблемы при добыче, хранении и транспортировке нефти. По ГОСТ Р 51858-2002 «Нефть. Общие технические условия» массовая доля сероводорода в нефти сорта 1 не должна превышать 0,002% (20 ppm).
Преимуществом этого способа являются одностадийность и простота процесса, а также возврат отработанного щелочного раствора в процесс для повторного использования. Недостатками способа являются повышенные расходы реагентов, проведение процесса под высоким давлением, длительная (до 180 мин) выдержка сырья с растворенным воздухом под таким давлением и загрязнение очищенного сырья отработанным раствором щелочи.
По технической сущности и достигаемому результату наиболее близким к предлагаемому изобретению является способ очистки нефти и газоконденсата от сероводорода путем окисления кислородом воздуха в присутствии 0,05-1,0% водно-щелочного раствора фталоцианинового катализатора. В этом способе в качестве щелочного агента применяют NaOH, аммиак и соду. На 1 моль сероводорода нефти берут 0,5-1,6 молей щелочного агента и 0,1-0,2 нм3
Щелочной вариант этого способа, в котором используют растворы NaOH и натриевые соли сульфофталоцианинов кобальта, в настоящее время нашел практическое применение на нефтепромыслах.
Недостатками известного способа являются:
1. Большой расход дорогостоящего фталоцианинового катализатора (0,05-0,2 г на 1 моль или на 34 г H2S). По этому способу при содержании в нефти 500 ppm Н2S расход катализатора составляет 0,73-2,9 г на 1 т нефти.
2. Большой расход воздуха: 0,1-0,2 нм3 на 1 моль сероводорода. При содержании в нефти 500 ppm H2S расход воздуха составляет 1,47-2,94 нм3 на 1 т нефти. Чем больше расход воздуха, тем больше количество выбрасываемого после окисления отработанного воздуха и тем больше унос легких углеводородов с отработанным воздухом. Содержание легких углеводородов в газах, уходящих с отработанным воздухом, при 45°С составляет около 50%, то есть унос углеводородов с отработанным воздухом примерно равен количеству отработанного воздуха.
3. Известный способ не позволяет полностью очистить сырье при содержании в нем более 420 ppm сероводорода, так как для окисления 420 ppm H2S требуется воздуха. Для растворения такого количества воздуха в тяжелой нефти (плотность более 880 кг/м3) при 40-60°С необходимо давление 1,5-3,0 МПа. В известном способе максимальное давление равно 1,5 МПа.
4. Воднощелочной раствор катализатора в нефть вводят в количестве 0,05-1%, следовательно, в случае образования стабильной эмульсии массовая доля воды в очищенной нефти может достигать 1%. По ГОСТ Р 51858-2002 массовая доля воды в товарной нефти не должна превышать 0,5%.
Предлагаемым изобретением решаются следующие задачи;
1. Снижение расхода фталоцианинового катализатора.
2. Снижение расхода воздуха и снижение потерь углеводородов (унос) с отработанным воздухом.
3. Снижение массовой доли воды и солей в очищенной нефти.
4. Расширение области применения способа на нефти, содержащей более 420 ppm сероводорода.
5. Проведение процесса окисления сероводорода (речь идет об одном и том же количестве сероводорода) при относительно более низких давлениях, чем в известном способе.
Для получения указанных технических результатов в предлагаемом способе очистки высокосернистой нефти от сероводорода путем окисления кислородом воздуха в присутствии водно-щелочных растворов фталоцианиновых катализаторов применяют в качестве катализаторного раствора 0,01-0,1%-ные растворы аммониевых солей сульфокислот фталоцианинов кобальта в 20-30%-ном водном растворе аммиака. Процесс окисления проводят при температуре 20-70°С и давлении до 2,5 МПа.
Аммиачный катализаторный раствор вводят в сырье в количестве 0,02-0,2%. Расход фталоцианинового катализатора на 1 моль сероводорода составляет 0,01-0,05 г; воздуха – 0,05-0,1 нм3.
В случае отделения от нефти при отстаивании водно-аммиачный раствор катализатора используют многократно, то есть отработанный раствор после отделения от очищенной нефти укрепляют свежим раствором катализатора в 20-30%-ном растворе аммиака и используют повторно. В случаях образования эмульсии отработанного катализаторного раствора и нефти эту эмульсию возвращают в процесс для повторного использования.
Отработанный воздух отделяют от очищенного сырья в две стадии: в первом сепараторе давление снижают до 0,2-0,6 МПа, во втором – до 0,1-0,15 МПа.
Отличительными признаками предлагаемого способа являются:
1. Использование в качестве катализатора растворов аммониевых (аммонийных) солей сульфокислот фталоцианинов кобальта в 20-30%-ном водном растворе аммиака. Об использовании аммонийных солей сульфофталоцианинов кобальта в патентной и научной литературе сведения отсутствуют.
2. В предлагаемом способе на один моль сероводорода берут:
– фталоцианинового катализатора |
– 0,01-0,05 г |
– воздуха |
– 0,05-0,1 нм3 |
В известном способе расходы составляют:
– фталоцианинового катализатора |
– 0,05-0,2 г |
– воздуха |
– 0,1-0,2 нм3 |
Кроме того, в предлагаемом способе водно-аммиачный раствор катализатора берут в количестве 0,02-0,2% к нефти, а в известном способе берут 0,05-1,0%, то есть в 2,5-5 раз больше. Соответственно, очищенная нефть в предлагаемом способе в случае образования устойчивых эмульсий содержит в 2,5-5 раз меньше воды, чем в известном способе.
Сероводород в присутствии фталоцианиновых катализаторов в слабощелочной среде, в том числе в аммиачных растворах, окисляется по реакции:

На 1 моль сероводорода требуется 0,5 молей или 16 г кислорода. Отсюда теоретически расход воздуха составляет:

где 0,231 – массовая доля кислорода в воздухе,%;
1,293 – плотность воздуха, кг/м3.
Часть сероводорода нейтрализуется аммиаком:

Образующийся гидросульфид растворяется в отработанном водном растворе и удаляется с отработанным водно-аммиачным раствором.
Поэтому нижний предел расхода воздуха взять равным 0,05 нм3 на один моль сероводорода.
Вводить в нефть воздуха более 0,1 м3 на 1 моль сероводорода нет необходимости. С увеличением количества введенного в нефть воздуха увеличивается количество отработанного воздуха и количество легких углеводородов, уносимых с отработанным воздухом, то есть увеличиваются потери нефти.
В известных способах применяют сильные щелочи (NaOH) или берут щелочной агент в большом количестве (0,1-1,0% от количества нефти). Растворы имеют плотность 1020-1150 кг/м3. В сильнощелочной среде (рН>12,5) сероводород окисляется до тиосульфата по реакции:

Кислород в известных способах расходуется в два раза больше, соответственно расход воздуха требуется в 2 раза больше.
Пределы давления 0,3-2,5 МПа установлены с учетом растворимости воздуха в нефти. При давлениях 0,3 МПа растворимость воздуха составляет 0,2-0,3 нм3 на 1 м3 нефти, что при расходе 0,1 нм3 воздуха на 1 моль H2S обеспечивает полное окисление 1-1,5 молей или 34-51 ppm сероводорода. В случаях еще более низких концентраций сероводорода в нефти просто нет необходимости очистки, то есть внедрения установки очистки. Для растворения 0,5 нм3 воздуха в тяжелой нефти (d 880 кг/м3) необходимо давление около 0,6 МПа, для растворения 1 нм3– около 1,3 МПа. Для окисления 600 ppm или 17,647 моля сероводорода требуется 0,882-1,765 нм3 воздуха, а для растворения в нефти таких количеств воздуха необходимо давление 1,1-2,2 МПа. Поэтому за верхний предел взято давление 2,5 МПа. В повышении давления выше 2,5 МПа нет необходимости.
В предлагаемом изобретении используют 20-30%-ные растворы аммиака. Высокосернистые тяжелые карбоновые нефти имеют плотность 880-900 кг/м3. Концентрированные 20-30% растворы аммиака имеют плотность 900-910 кг/м3. Чем ближе плотности нефти и водных растворов, тем легче создавать однородную эмульсию водно-щелочного раствора катализатора в нефти. Поэтому в предлагаемом способе достигается более эффективное перемешивание. Кроме того, 25-28% растворы аммиака выпускаются Российской промышленностью.
Необходимый расход катализатора установлен на основании экспериментов. Расход ниже 0,01 г на 1 моль H2S не обеспечивает необходимую скорость окисления, а в повышении количества дорогостоящего катализатора (цена 1 г 2-3 руб.) выше 0,05 г на 1 моль H2S нет необходимости.
В известных способах применяют натриевые соли сульфофталоцианинов кобальта, которые в сильнощелочных растворах (рН>13,5) при 40°С и выше не устойчивы, быстро разлагаются. Поэтому в щелочные растворы вынуждены вводить повышенные количества фталоцианиновых катализаторов. В предлагаемом способе применяют аммониевые соли сульфофталоцианинов кобальта, растворенные в водном растворе аммиака с рН<12,5. В таких растворах стабильность аммониевых солей почти в 10 раз выше, чем стабильность натриевых солей в известном способе. Поэтому расход фталоцианинового катализатора в 4-5 раз ниже, чем в известном способе.
Аммонийные соли сульфокислот фталоцианинов кобальта получают растворением соответствующих сульфокислот в 20-30%-ном растворе аммиака или путем растворения натриевых солей сульфокислот в 20-30%-ном растворе аммиака в присутствии хлорида аммония – NH4Cl по реакции:
RSO3Na+NH4Cl RSO3NH4+NaCl
0,01-0,1%-ные растворы аммониевых солей сульфофталоцианинов можно готовить в один прием, но с точки зрения технологии более рационально сначала приготовить концентрированные 1,5±0,5%-ные растворы аммониевых солей сульфофталоцианинов, потом эти растворы разбавлять до рабочей концентрации 0,01-0,05%. Для растворения порошкообразных сульфокислот фталоцианинов, их натриевых солей и хлористого аммония требуется аппарат (реактор) с механическим перемешиванием, для полного растворения необходимо время перемешивания 20-30 мин, а для разбавления концентрированных растворов в 100 раз водным аммиаком достаточно перемешивание путем циркуляции циркуляционным насосом в любой емкости. Для приготовления концентрированного раствора можно использовать реактор с механической мешалкой небольшого объема. В этом варианте капитальные и энергетические затраты будут меньше, чем в случае установки больших реакторов с механической мешалкой для приготовления 0,01-0,05%-ных растворов катализатора в один прием.
При 45-70°С сероводород полностью окисляется за 15-30 мин, и в повышении температуры выше 70°С нет необходимости. При 18-20°С для полноты реакции требуется время около 1,5 часов. Ограничение нижнего предела температуры 20°С связано с замедлением скорости реакции и повышением вязкости нефти, что затрудняет эмульгирование аммиачного раствора катализатора в нефти.
Двухстадийная сепарация отработанного воздуха путем снижения давления в первом сепараторе до 0,2-0,6 МПа и во втором сепараторе – до 0,1-0,12 МПа дает следующие положительные эффекты:
1. Уменьшаются потери легких углеводородов, уносимых с отработанным воздухом, выделяющимся из нефти, так как основное количество отработанного воздуха выделяется (сепарируется) в первом сепараторе при снижении давления, например, с 2 до 0,6 МПа или с 1 до 0,2 МПа. При сепарации под давлением 0,2-0,6 МПа газовая фаза содержит паров углеводородов значительно меньше, чем в случае сепарации отработанного воздуха при атмосферном давлении.
2. При испарении отработанного воздуха из нефти при снижении давления до 0,2-0,6 МПа выделяется в основном азот, а кислород остается в растворе, так как растворимость кислорода в нефти почти в 2 раза выше, чем растворимость азота. Оставшийся в нефти в растворенном виде кислород продолжает процессы окисления H2S и в сепараторах. В результате достигается более полная очистка нефти от сероводорода.
Предлагаемый способ очистки нефти прост в осуществлении и может быть реализован на нефтепромыслах и нефтеперерабатывающих заводах.
Предлагаемый способ поясняется прилагаемой технологической схемой (см. чертеж) и примерами ее осуществления.
В емкости Т-1 готовят катализаторный раствор путем растворения 0,02% хлористого аммония и 0,04% динатриевой соли дисульфофталоцианина кобальта, получают раствор диаммониевой соли дисульфофталоцианина кобальта.
Нефть, прошедшая подготовку (сепарацию, обессоливание, обезвоживание) и содержащая 300-600 ppm сероводорода с температурой 20-65°С (предпочтительно 40-55°С), поступает в буферную емкость Е-1. Из этой емкости насосом Н-1 нефть под давлением 0,3-2,5 МПа подают в реактор окисления колонного типа Р-1. На всас насоса Н-1 из емкости Е-4 дозировочным насосом НД подают расчетное количество (предпочтительно 0,5-1,0 кг/т) раствора фталоцианинового катализатора в 25%-ном водном растворе аммиака. В поток нефти после насоса Н-1 компрессором К-1 подают под давлением 0,4-2,5 МПа сжатый воздух, который растворяется в нефти. Далее смесь поступает в реактор Р-1 колонного типа. В реакторе происходит окисление сероводорода кислородом растворенного в нефти воздуха:

После реактора нефть поступает в сепаратор С-1, где давление снижается до 0,20-0,5 МПа, и основная часть отработанного воздуха отсепарируется от нефти. Далее нефть поступает во второй сепаратор С-2, где давление снижается до атмосферного, и происходит сепарация оставшейся части отработанного воздуха. В сепараторах С-1 и С-2 часть отработанного катализаторного раствора отделяется от очищенной нефти в виде эмульсии. По технологической схеме предусмотрена возможность возврата этой эмульсии на смешение с неочищенной нефтью.
Большинство нефтей при перемешивании с щелочными растворами образуют эмульсии. Образующиеся соли нафтеновых кислот являются эмульгаторами. Чем больше соотношение углеводородное сырье : раствор аммиака, тем больше получается концентрация нафтенатов в водной фазе и тем выше стойкость образующейся эмульсии. Тяжелые карбоновые нефти, которые содержат много нафтеновых кислот, образуют стойкие, трудно разделяющиеся эмульсии. Из таких нефтей отработанный водно-аммиачный раствор обычно отстаивается в виде эмульсии с содержанием 3-30% воды. При отстаивании образуется три слоя: вверху слой очищенного сырья, внизу слой водного раствора и в середине слой эмульсии. Для полного разделения эмульсии отстаиванием требуется время от нескольких часов до нескольких суток. Присутствие солей и повышение температуры ускоряют процесс разделения эмульсии. В предлагаемом способе применяют описанный в патенте РФ 2120464 прием возврата эмульсии отработанного раствора и нефти в процесс окисления, т.е. смешивают ее с исходным сырьем. Возврат катализаторного раствора на повторное использование позволяет экономить расход катализатора и аммиака.
Часть отработанного щелочного раствора в случае отстаивания его из нефти в сепараторе С-2 периодически выводится из технологического процесса. Отработанный раствор может быть утилизирован путем смешения с пластовыми водами с последующей закачкой их в пласт. Объем пластовых вод в 10-1000 раз больше, чем объем отработанных щелочных растворов, поэтому добавка их в пластовые воды не изменяет состав последних.
Предлагаемый способ проверен в лабораторных условиях.
Пример 1. Готовят растворы различных сульфокислот (моно-, ди- и тетра) фталоцианинов кобальта в 20-30%-ном растворе аммиака. Сульфокислот фталоцианинов вводят из расчета получения 0,01-0,05% аммонийных солей. Полученные растворы используют в качестве катализаторного раствора. В колбу вместимостью 120 мл берут навеску катализаторного раствора, добавляют 30-45 г охлажденной до -5-0°С нефти, воздушное пространство колбы заполняют кислородом (70-87 мл). Колбу закрывают резиновой пробкой и при температуре 20-65°С дают выдержку при перемешивании встряхиванием в течение 15-90 мин. При нагревании охлажденной нефти в закрытой колбе создается избыточное давление. По содержанию растворенного кислорода в нефти эти опыты имитируют процессы окисления кислородом воздуха, растворенного под давлением 0,6-0,9 МПа, что по расчетам соответствует 0,05-0,1 нм3 воздуха на один моль H2S. После выдержки 15 мин из колбы шприцом отбирают пробы нефти ( 0,5 мл) на анализ, через еще 30-60 мин отбирают вторую пробу. Анализируют пробы на содержание сероводорода потенциометрическим титрованием по ГОСТ 17323-76. В опытах табл.1 использованы аммониевые соли следующих фталоцианиновых катализаторов:
– сульфокислоты фталоцианина кобальта (СФК);
– дисульфокислоты фталоцианина кобальта (ДСФК);
– тетрасульфокислоты фталоцианина кобальта (ТСФК);
– диоксидихлордисульфокислоты фталоцианина кобальта (ДОДХДСФК);
– дихлордисульфокислоты фталоцианина кобальта (ДХДСФК).
Пример 2. Первые два опыта проводят, как в примере 1. После окисления очищенную нефть в опыте №2 отсепарируют от отработанного воздуха и смешивают со следующей порцией подлежащей очистке нефти в соотношении 1:1. В эту смешанную порцию нефти в опыте №3 вводят столько же катализаторного раствора, сколько в опыте №1, затем проводят процесс окисления, как в примере 1. Очищенную нефть после опыта №3 делят на две равные части, одну часть 25 г смешивают с таким же количеством неочищенной нефти и смесь используют в опыте №4. Следующий опыт №5 проводят аналогично опыту №4. В опыте №6 количество очищенной нефти на приготовление смеси нефтей берут в два раза меньше. Результаты опытов приведены в табл.2. Степень очистки нефти (X,%) от сероводорода рассчитывается по формуле: 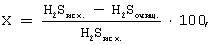
где Н2Sисх – массовая доля сероводорода в исходной неочищенной нефти, %;
H2Sочищ – массовая доля сероводорода в очищенной нефти, %.
Обсуждение результатов опытов по примерам 1 и 2
Из литературных данных известно, что скорость окисления сероводорода в щелочной среде на 3-4 порядка выше, чем в кислой среде. Следовательно, введенное в нефть количество аммиака должно быть достаточным для создания щелочной среды. Как видно из табл.1, скорость окисления сероводорода с увеличением количества введенного аммиака, то есть соотношения NH3:Н2S, заметно возрастает (опыты №1, 2 и 13). Сероводород можно окислять и без применения фталоцианиновых катализаторов» однако в этом случае требуется большой расход аммиака (опыт №2).
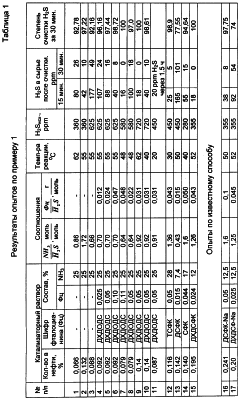
Введение 0,25% аммониевой соли ДОДХДСФК в водный раствор аммиака приводит к снижению концентрации H2S в очищенном продукте почти в два раза (опыты №3 и 4). Чем больше количество введенного катализатора, тем выше степень очистки сырья от сероводорода (опыты №4-6). Однако введение больших количеств дорогостоящего фталоцианинового катализатора не выгодно экономически. Оптимальной для окисления сероводорода является температура 40-60°С. Процесс можно проводить и при 20-30°С, но в этих случаях требуется или длительное время окисления (опыт №11), или большой расход аммиака (опыт №12). В опытах №4-12, в которых параметры процесса находятся в пределах, предлагаемых в изобретении, содержание Н2S в очищенной нефти после 30 мин окисления при достаточном количестве кислорода не превышает установленных норм – 20 ppm.
В опытах №14 и 15, где используют катализаторный раствор с пониженной концентрацией аммиака, удовлетворительные результаты достигаются, но с большим расходом аммиака. В опыте №13, где применяют разбавленный раствор аммиака и количество аммиака ниже 0,5 молей на моль сероводорода, требуемая степень очистки не достигается.
В известном способе (опыт №16) достигается требуемая степень очистки, но с большим расходом аммиака и в 2-3 раза большим расходом катализатора – динатриевой соли дисульфофталоцианина кобальта (ДСФК-Na).
Как видно из табл.2 (опыт №1), при введении в нефть 0,605 молей аммиака и 0,02 г аммиачной соли ДОДХДСФК на 1 моль сероводорода за 20 мин при 50°С массовая доля H2S в нефти снижается с 420 до 83 ppm. Для очистки нефти до содержания H2S 20 ppm требуется расход NH3 и фталоцианинового катализатора в два раза больше (опыт №2). В опытах №3-5 в случае смешения исходной неочищенной нефти с очищенной нефтью в массовом соотношении 1:1 удовлетворительная очистка смеси достигается при тех же расходах аммиака и фталоцианинового катализатора, что и в опыте №1. Уменьшение количества очищенной нефти, взятой на смешение, соответственно уменьшение количества отработанного катализаторного раствора, возвращаемого с очищенной нефтью, приводит к ухудшению качества очистки (опыт №6).
Таким образом, возврат части отработанного катализаторного раствора или его эмульсии с очищенной нефтью дает возможность снизить (экономить) расходы водного аммиака и фталоцианинового катализатора.
Пример 3. Опыты проводят, как в примере 1. Берут 75 мл нефти и 45 мл воздуха и 0,2 г катализаторного раствора, содержащего 0,018% катализатора, что составляет 0,05 г катализатора на один моль сероводорода. В первую колбу вводят раствор, содержащий аммониевую соль ДСФК в 20%-ном растворе аммиака, во вторую вводят раствор натриевой соли ДСФК в 20%-ном растворе щелочи (как в известном способе). На окисление 355 ppm H2S до S по реакции 1 на 1 т нефти требуется не менее 177,5 г O2 или 0,598 нм3 воздуха. Для окисления H2S в 75 мл или 67,5 г нефти требуется не менее 40 мл воздуха. Расход воздуха на моль H2S равен 0,06 нм3. Окисление проводят при 50°С в течение 60 мин. По анализу в колбе №1 – H2S – менее 10 ppm, в колбе №2 – 132 ppm. Это объясняется нехваткой кислорода в опыте №2 из-за окисления Н2S до тиосульфата.
После этого пространство над нефтью в колбе №2 продувают свежим воздухом, перемешивают и дают выдержку еще 60 мин. Проводят анализ нефти; содержание H2S = 16 ppm. Значит, для окисления Н2S в опыте №2 требуется воздуха почти в 2 раза больше.
Чем больше взято количество воздуха на окисление, тем больше образуется отработанного воздуха, содержащего 50-70% углеводородов. Поэтому в заявляемом способе потери углеводородов меньше, чем в известном способе.
Таблица 2 Результаты опытов по примеру 2 |
№п/п |
Количество нефтей в смеси, г |
Н2Sисх, ppm |
Количество катализаторного раствора,% |
Отношения вновь введенных реагентов к 1 молю сероводорода |
Темп-ра окисления, °С |
H2Sочищ, ppm, через 20 мин окисления |
неочищен. |
очищен. |
неочищен. нефть |
смесь нефтей |
в неочищен. нефти |
в смеси нефтей |
 моль/моль |
 г/моль |
1 |
25 |
– |
420 |
– |
0,054 |
0,054 |
0,605 |
0,02 |
45 |
83 |
2 |
25 |
– |
420 |
– |
0,108 |
0,108 |
1,21 |
0,04 |
45 |
20 |
3 |
25 |
25 |
420 |
220 |
0,054 |
0,027 |
0,60 |
0,02 |
45 |
18 |
4 |
25 |
25 |
420 |
219 |
0,054 |
0,027 |
0,60 |
0,02 |
45 |
24 |
5 |
25 |
25 |
420 |
222 |
0,054 |
0,027 |
0,60 |
0,02 |
45 |
20 |
6 |
25 |
12,5 |
420 |
321 |
0,054 |
0,040 |
0,60 |
0,02 |
45 |
33 |
Формула изобретения
1. Способ очистки тяжелой высокосернистой нефти от сероводорода путем окисления кислородом воздуха в присутствии водно-щелочных растворов сульфированных фталоцианинов кобальта при температуре 15-70°С под давлением, отличающийся тем, что в качестве катализаторного раствора используют растворы аммониевых солей сульфокислот фталоцианинов кобальта в 20-30%-ном водном растворе аммиака; на один моль сероводорода берут 0,05-0,1 нм3 воздуха и 0,01-0,05 г аммониевой соли сульфокислоты фталоцианина кобальта.
2. Способ по п.1, отличающийся тем, что применяют 0,01-0,1%-ные растворы аммониевых солей сульфокислот фталоцианинов кобальта.
3. Способ по пп.1 и 2, отличающийся тем, что катализаторный раствор вводят в нефть в количестве 0,02-0,2%.
4. Способ по п.1, отличающийся тем, что используют аммонийные соли моно, – ди, – тетрасульфокислоты, дихлордисульфокислоты и дихлорди-оксидисульфокислоты фталоцианина кобальта.
5. Способ по пп.1 и 4, отличающийся тем, что катализаторный раствор получают путем растворения натриевых солей сульфофталоцианинов кобальта и хлористого аммония в водном растворе аммиака.
6. Способ по п.1, отличающийся тем, что катализаторный раствор после окисления сероводорода отделяют от очищенной нефти и используют многократно.
7. Способ по п.1, отличающийся тем, что эмульсию отработанного катализаторного раствора и нефти отделяют от очищенной нефти и смешивают с неочищенной нефтью.
8. Способ по п.1, отличающийся тем, что процесс проводят под давлением 0,3-2,5 МПа.
9. Способ по п.1, отличающийся тем, что сепарацию отработанного воздуха от очищенной нефти проводят в две стадии: в первом сепараторе давление снижают до 0,2-0,6 МПа, во втором сепараторе до 0,1-0,15 МПа.
10. Способ по пп.2, 5, отличающийся тем, что сначала готовят концентрированные 1-2%-ные растворы аммониевых солей сульфофталоцианинов, потом эти растворы разбавляют водным раствором аммиака до содержания аммониевых солей 0,01-0,1%.
РИСУНКИ
|
|