(21), (22) Заявка: 2004112262/02, 12.04.2004
(24) Дата начала отсчета срока действия патента:
12.04.2004
(43) Дата публикации заявки: 10.10.2005
(45) Опубликовано: 10.03.2006
(56) Список документов, цитированных в отчете о поиске:
RU 2002111545 А, 10.11.2003. RU 2103138 C1, 27.01.1998. SU 1292965 A1, 28.02.1987. GB 1529421 A, 18.10.1978. JP 01-273671 A, 01.11.1989.
Адрес для переписки:
400009, г.Волгоград, пр. Ленина, 153, кв.45, Н.Д. Засульскому
|
(73) Патентообладатель(и):
Засульский Николай Данилович (RU)
|
(54) УСТРОЙСТВО ДЛЯ СВАРКИ СЕКЦИОННЫХ ОТВОДОВ ТРУБОПРОВОДОВ
(57) Реферат:
Изобретение относится к области сварки, а именно к устройствам для установки и вращения секционных отводов большого веса и диаметра. Устройство содержит смонтированный на станине основания поворотный шпиндель, узел для закрепления отвода, смонтированные на шпинделе и обойме узлы с электропроводными элементами для подключения к отводу сварочного напряжения источника электротока, опорный узел с подвижным по высоте верхним корпусом, роликоопору с роликом и трубчатую балку. Поворотный шпиндель кинематически связан с узлом для закрепления отвода. Узел для закрепления отвода выполнен в виде корпуса и обоймы с зажимами, установленной в корпусе с возможностью поворота вокруг оси, ориентированной под углом к продольной оси шпинделя. Ролик роликоопоры смонтирован с возможностью регулируемого усилия взаимодействия с секцией отвода, геометрическая ось которой соосна со шпинделем. Трубчатая балка жестко связана одним концом с поворотным шпинделем, а другим – с корпусом узла для закрепления отвода. Подвижный по высоте верхний корпус опорного узла с закрепленной на нем площадкой смонтирован в опорах нижнего корпуса с возможностью взаимодействия с закрепленной на трубчатой балке опорной площадкой при остановке вращения шпинделя. Это позволит упростить конструкцию устройства и снизить его металлоемкость. 3 з.п. ф-лы, 6 ил. 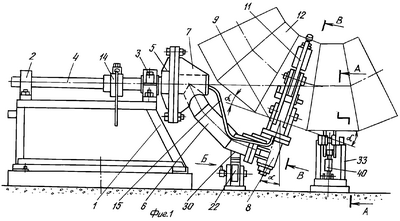
Устройство для сварки отводов предназначено для установки и вращения в процессе сварки секционных отводов трубопроводов преимущественно большого веса и диаметра, приблизительно до 1,6 м.
Известно устройство для сварки секционных отводов трубопроводов, содержащее смонтированный на основании поворотный шпиндель, жестко закрепленную на шпинделе дугообразную консоль, несущую узел для закрепления отвода, выполненный в виде корпуса и обоймы с зажимами, установленной в корпусе с возможностью поворота, смонтированные на шпинделе и обойме узлы с электропроводными элементами для подключения к отводу сварочного напряжения источника электротока, при этом узел для закрепления отвода выполнен обеспечивающим соосность шпинделя с геометрической осью одной из секций отвода, а на основании смонтированы дополнительные узлы, один из которых выполнен в виде опоры с верхней подвижной частью, смонтированной с возможностью взаимодействия с дугообразной консолью, а другой узел – в виде роликоопоры с роликом, смонтированным с возможностью регулируемого усилия взаимодействия с одной упомянутой секцией отвода, геометрическая ось которой сосна со шпинделем (заявка №2002111545/02, опубл. 10.11.2003). Без упомянутых дополнительных узлов для обеспечения надежности при сварке отводов большого веса и диаметра потребовалось бы увеличить не только размеры по длине и в поперечном сечении дугообразной консоли, но и диаметр шпинделя, его подшипниковых опор и других элементов устройства, на которых смонтирован поворотный шпиндель. Другими словами: существенным недостатком устройства без дополнительных узлов является неэффективное использование металла основных элементов устройства (дугообразной консоли, шпинделя, подшипниковых опор и других элементов) при сварке отводов большого веса и диаметра.
Известно устройство, содержащее смонтированное на опорных роликах основания поворотное кольцо, смонтированный на основании поворотный шпиндель, кинематически связанный закрепленной на шпинделе и поворотном кольце рамой с узлом для закрепления отвода (патент РФ №2103138, МПК В 23 К 37/04, опубл. 27.01.1998 г.).
Это устройство характеризуется высокой сложностью и металлоемкостью. Несмотря на то что шпиндель в этом устройстве не нагружен консольной нагрузкой, металл несущих элементов использован неэффективно, что обусловило значительную металлоемкость конструкции.
Задача предлагаемого изобретения – снижение суммарной металлоемкости устройства путем устранения консольной нагрузки на шпиндель с помощью дополнительных узлов, элементы которых взаимодействуют с дугообразной консолью и с закрепляемым в обойме отводом.
Сущность предлагаемого изобретения состоит в том, что устройство для сварки секционных отводов содержит смонтированный на основании поворотный шпиндель, кинематически связанный с узлом для закрепления отвода, выполненным в виде корпуса и обоймы с зажимами, установленной в корпусе с возможностью поворота, смонтированные на шпинделе и обойме узлы с электропроводными элементами для подключения к отводу сварочного напряжения источника электротока, опорный узел с подвижным по высоте верхним корпусом и роликоопору, ролик которой смонтирован с возможностью регулировать усилие взаимодействия с секцией отвода, геометрическая ось на которой сосна со шпинделем, что обеспечивается расположением узла для закрепления отвода.
Устройство с вышеуказанными признаками выполнено со следующими отличиями.
Отличием является то, что устройство снабжено трубчатой балкой, жестко связанной одним концом с поворотным шпинделем, а другим – с корпусом узла для закрепления отвода, а подвижный по высоте верхний корпус опорного узла с закрепленной на ней площадкой смонтирован в опорах нижнего корпуса с возможностью взаимодействия с закрепленной на трубчатой балке опорной площадкой при остановке вращения и шпинделя.
Отличием является и то, что опорный узел содержит смонтированную в опорах поворотную ось с закрепленным на ней осеэксцентрично цилиндрическим кулачком, а закрепленная на верхнем корпусе опорного узла площадка выполнена с вогнутой по окружности поверхностью для взаимодействия с выпуклой поверхностью площадки трубчатой балки.
Другим отличием является то, что роликоопора дополнительно снабжена поворотным рычагом с установленным на нем упругим элементом, верхняя часть которого взаимодействует со свободным концом рычага, несущим смонтированный в подшипниковых опорах ролик.
На фиг.1 изображено предлагаемое устройство, общий вид; на фиг.2 – разрез А-А на фиг.1; на фиг.3 – вид Б на фиг.1; на фиг.4 изображен частично ролик с электроизоляцией металлического обода; на фиг.5 – ролик с обрезиненным ободом на фиг.1; на фиг.6 – разрез В-В на фиг.1.
Устройство содержит установленную на основании станину 1, на которой в подшипниковых опорах 2 и 3 смонтирован шпиндель 4 с закрепленной на нем планшайбой 5. На планшайбе закреплена трубчатая балка 6, ориентированная под углом к продольной оси шпинделя, приблизительно, 45 градусов. Балка выполнена с фланцевым узлом 7, который с помощью крепежных винтовых элементов жестко соединен с планшайбой. На балке закреплен корпус 8 с установленной на нем с возможностью поворота обоймой 9 с закрепленной на обойме осью 10. Обойма содержит пару кронштейнов 11, установленных с возможностью поворота и фиксирования в рабочем положении при закреплении в обойме свариваемого отвода 12. Закрепление отвода осуществляется с помощью смонтированных на кронштейнах 11 винтовых прижимов 13.
Устройство оснащено смонтированным на станине и шпинделе узлом 14, содержащим электропроводные элементы, соединенные проложенным во внутренней полости шпинделя электрическим кабелем 15 с электропроводными элементами узла 16.
Узел 16, смонтированный на корпусе 8 и обойме 9, выполнен с электропроводящим контактным узлом 17, подключаемым к отводу в момент установки отвода в обойму. На фланце 18 корпуса 8 закреплена пара электропроводных пластин 19, размещенных диаметрально оси поворота обоймы. Возле каждой пластины 19 на фланце смонтирован поворотный винтовой прижим 20, с помощью которых осуществляется электрическое соединение закрепленной на обойме и связанной с узлом 17 пластины 21 с одной из пластин 19 и с электрическим кабелем 15.
Устройство оснащено установленным на основании опорным узлом 22 для взаимодействия его подвижных элементов с трубчатой балкой при остановке вращения шпинделя.
Опорный узел содержит установленный на основании нижний корпус 23, на котором в опорах 24 смонтирована поворотная ось 25. На оси закреплен цилиндрический кулачок 26, выполненный с осеэксцентричным расположением рабочей поверхности, и рукоятка 27. Кулачок сочленен с подвижным верхним корпусом 28 с закрепленной на нем площадкой 29, верхняя поверхность которой выполнена вогнутой по окружности. Площадка 29 взаимодействует в рабочем положении узла (при неподвижном шпинделе) с выпуклой поверхностью опорной площадки 30 балки. Радиус кривизны поверхности площадок 29 и 30 выполнен равным расстоянию от поверхности площадки 30 до оси шпинделя приблизительно.
На верхнем корпусе 28 закреплены упоры 31, которые взаимодействуют с плитой 32 нижнего корпуса в крайнем нижнем положении верхнего корпуса и площадки 29.
Устройство оснащено установленным на основании узлом-роликоопорой 33 с роликом 34, взаимодействующим при вращении шпинделя с поверхностью одной из секций отвода, геометрическая ось которой совпадает (в пределах допуска) с осью вращения шпинделя.
Роликоопора содержит суппорт 35, закрепленную на суппорте ось 36 с установленным на оси с возможностью поворота рычагом 37, несущим смонтированный в подшипниковых опорах ролик 34. Роликоопора снабжена установленным на оси 36 дополнительным рычагом 38, несущим установленный на рычаге упругий элемент 39, верхняя часть которого взаимодействует со свободным концом рычага 37.
Роликоопора снабжена винтовым механизмом 40, выполненным в виде смонтированной в корпусе 41 винтовой пары 42. Корпус 41 шарнирно соединен с закрепленной на суппорте опорой 43, а винт – с рычагом 38.
Ролик может быть выполнен в двух вариантах. В одном из них (фиг.4) ролик выполнен с металлическим ободом 44 и содержит внутренние обечайки 45 и 46. Между ними установлена обечайка 47, выполненная из электроизоляционного материала (пластмассы). В другом варианте (фиг.5) металлический обод 44 ролика выполнен с резиновым покрытием 48, выполняющим функцию электроизоляции от остальных элементов роликоопоры и обеспечивающим плавное вращение отвода, секция которого выполнена с погрешностями изготовления или при погрешности установки отвода в обойме. Наружная поверхность ролика выполнена из слоя термостойкой ткани 49, предохраняющего резиновое покрытие от высокой температуры свариваемого отвода.
На суппорте 35 роликоопоры установлена с возможностью настроечного регулирования по высоте пластина-указатель 50, с помощью которой определяют необходимое, соосное со шпинделем, положение секции отвода.
Устройство работает следующим образом.
Перед установкой собранного на электроприхватках отвода на обойме устанавливают необходимой высоты опоры 51 для обеспечения соосного со шпинделем положения секции отвода, которая будет взаимодействовать с роликом роликоопоры. В узел 17 с электропроводными элементами устанавливают необходимой высоты сменный электропроводный элемент для контактирования с поверхностью отвода.
Перемещение подвижного корпуса 28 опорного узла 22 осуществляется следующим образом.
В нерабочем положении узла (отвод не установлен в обойму) дугообразная щель между опорной площадкой 30 балки и площадкой 29 верхнего корпуса наибольшая по величине, и оба упора 31 контактируют с корпусом 23. При повороте оси с кулачком на угол приблизительно 100-110 градусов площадка корпуса 28 контактирует с опорной площадкой 30 балки, и при ее нагружении устанавливаемым в обойму отводом опорный узел работает как дополнительная опора трубчатой балки.
Для возврата опорного узла в нерабочее положение рукояткой 27 осуществляют поворот оси с кулачком в прежнее положение (на фиг.3 – против часовой стрелки). При этом в крайнем нижнем положении корпуса 28 дугообразная щель будет меньшей величины, но не препятствующей вращению балки совместно со шпинделем.
Установку отвода в обойму осуществляют грузоподъемным механизмом с помощью захвата, обеспечивающим положение отвода на крюке приблизительно таким же, как и в обойме (фиг.1). Это достигается различной длиной ветвей двухветвевого захвата (не показано). При установке отвода на опоры 51 визуально, с помощью установленной на суппорте пластины-указателя 50, определяют необходимое положение закрепляемой секции и затем осуществляют закрепление отвода винтовыми прижимами 13.
В исходном положении, перед включением привода вращения шпинделя, обойма зафиксирована относительно корпуса 8 одним из поворотных винтовых прижимов 20, обеспечивающим одновременно электрическое соединение пластин 19 и 21. Включение в работу роликоопоры осуществляют воздействием винтовым механизмом 40 на рычаг 38, который через упругие элементы 39 прижимает ролик к поверхности секции отвода. Заданное усилие прижима, равное, например, половине веса установленного отвода, определяют по величине деформации упругого элемента 39. (При использовании вместо винтовой пары силового гидроцилиндра (не показано) величину усилия прижима ролика определяют по величине давления рабочей жидкости, то есть по показаниям манометра.)
Последнюю операцию перед включением электропривода – перевод элементов опорного узла 22 в нерабочее положение осуществляют поворотом рукоятки 27, как было изложено выше.
Сварщик производит поочередно сварку двух стыков секций отвода, одна из которых расположена соосно со шпинделем. При этом вышеуказанные электропроводящие элементы узлов 14 и 16 обеспечивают надежный электрический контакт отвода с одним из полюсов источника сварочного электротока.
После завершения сварки двух упомянутых стыков производят поворот обоймы относительно корпуса на угол 180 градусов.
Перед осуществлением поворота обоймы элементы опорного узла 22 переводят в рабочее положение, как излагалось выше, и винтовым механизмом роликоопоры прекращают прижим ролика к секции отвода.
Для осуществления поворота производят расфиксирование обоймы (прекращение сжатия электроконтактных пластин 19 и 21) винтовым прижимом 20 и фиксирование обоймы после поворота во второй рабочей позиции другим винтовым прижимом. После поворота обоймы подлежащие сварке стыки секций займут такое же положение, что и предыдущие с соосным со шпинделем расположением другой секции.
Указанное совпадение обеспечивается требованиями к параметрам конструкции секционного отвода, а именно: должно соблюдаться равенство и постоянная величина углов для всех свариваемых на устройстве отводов (фиг.1).
После завершения сварки останавливают вращение шпинделя при положении, изображенном на фиг.1, переводят винтовые прижимы 13 и кронштейны 11 обоймы в нерабочее положение и снимают отвод с устройства грузоподъемным механизмом с помощью захватного приспособления (не показано). Предварительно элементы опорного узла 22 переводят в рабочее положение.
Таким образом, закрепленный в обойме отвод и трубчатая балка, на которой смонтированы корпус и обойма, являются по сути единым узлом, жестко закрепленным одной стороной на шпинделе, а другой – опирающейся на ролик роликоопоры.
Такая совокупность связанных между собой элементов создает экономически выгодную (с точки зрения экономии металла) схему нагружения шпинделя и жестко закрепленной на шпинделе балки. При этом жесткое закрепление балки, оснащенной фланцевым узлом с увеличенным диаметром фланца, обеспечивает устойчивое положение отвода (одной из секций отвода) на ролике роликоопоры и не требует использования широко известной роликоопоры с двумя разнесенными по ширине роликами.
Формула изобретения
1. Устройство для сварки секционных отводов трубопроводов, содержащее смонтированный на станине основания поворотный шпиндель, кинематически связанный с узлом для закрепления отвода, выполненным в виде корпуса и обоймы с зажимами, установленной в корпусе с возможностью поворота вокруг оси, ориентированной под утлом к продольной оси шпинделя, смонтированные на шпинделе и обойме узлы с электропроводными элементами для подключения к отводу сварочного напряжения источника электротока, опорный узел с подвижным по высоте верхним корпусом и роликоопору, ролик которой смонтирован с возможностью регулируемого усилия взаимодействия с секцией отвода, геометрическая ось которой соосна со шпинделем, при этом узел для закрепления отвода выполнен обеспечивающим соосность шпинделя с геометрической осью секции отвода, закрепленного в обойме, отличающееся тем, что оно снабжено трубчатой балкой, жестко связанной одним концом с поворотным шпинделем, а другим – с корпусом узла для закрепления отвода, а подвижный по высоте верхний корпус опорного узла с закрепленной на нем площадкой смонтирован в опорах нижнего корпуса с возможностью взаимодействия с закрепленной на трубчатой балке опорной площадкой при остановке вращения шпинделя.
2. Устройство по п.1, отличающееся тем, что закрепленная на верхнем корпусе опорного узла площадка выполнена с вогнутой по окружности поверхностью для взаимодействия с выпуклой поверхностью площадки трубчатой балки.
3. Устройство по п.1, отличающееся тем, что опорный узел содержит смонтированную в опорах поворотную ось, на которой закреплен цилиндрический кулачок, выполненный с осеэксцентричным расположением рабочей поверхности.
4. Устройство по п.1, отличающееся тем, что роликоопора дополнительно снабжена поворотным рычагом с установленным на нем упругим элементом, верхняя часть которого взаимодействует со свободным концом рычага, несущим смонтированный в подшипниковых опорах ролик.
РИСУНКИ
|