(21), (22) Заявка: 2004117922/12, 15.06.2004
(24) Дата начала отсчета срока действия патента:
15.06.2004
(45) Опубликовано: 27.02.2006
(56) Список документов, цитированных в отчете о поиске:
SU 771230 А, 15.10.1980. SU 833017 А, 30.06.1986. SU 59699 А, 30.04.1941. SU 114324 А, 09.04.1959. ЕР 0406783 А2, 09.01.1991. US 3654076 А, 04.04.1972. ЕР 0728868 А2, 28.08.1996.
Адрес для переписки:
109316, Москва, Остаповский пр-д, 13, В.Н. Мартынову
|
(72) Автор(ы):
Мартынов Владимир Николаевич (RU), Ланьков Александр Эльбертович (RU), Мартынов Сергей Николаевич (RU)
(73) Патентообладатель(и):
Общество с ограниченной ответственностью “Научно-производственная Компания “РАНКО” (RU)
|
(54) СПОСОБ ИЗГОТОВЛЕНИЯ ФОРМОВАННЫХ ИЗДЕЛИЙ ИЗ ВОЛОКНИСТОЙ МАССЫ
(57) Реферат:
Изобретение относится к производству изделий из волокнистой массы. Способ включает приготовление водной суспензии требуемой концентрации из волокнистых материалов, формование влажного изделия путем осаждения волокон на формующем основании и удаление остаточной влаги путем сушки. В приготовленную водную суспензию дозировано подают жидкие и твердые модификаторы для придания материалу требуемых физико-механических качеств, осаждение волокон осуществляют на поверхность твердотельных форм, изготовленных из пористого материала. Образование влажного изделия осуществляют на нижней поверхности формующего основания по схеме “снизу-вверх” путем наращивания волокнистого материала фильтрованием воды из суспензии через поры формующего основания за счет перепада давления, создаваемого на нем. Одновременно с сушкой изделие подвергают подпрессовке, причем сушку изделия ведут в нагреваемой разъемной твердотельной форме с одновременным удалением паров воды за счет вакуумной откачки из верхней и нижней частей указанной формы. Обеспечивается получение качественной поверхности изделия с различными потребительскими качествами и плотной структуры материала при упрощении технологической оснастки и снижении затрат на ее эксплуатацию. 1 з.п. ф-лы, 4 ил. 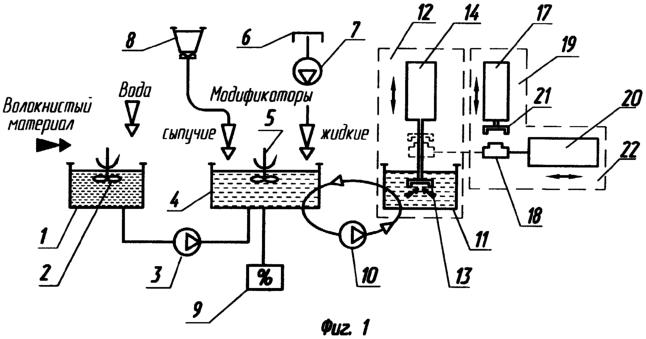
Настоящее предлагаемое изобретение относится к области производства изделий из волокнистой массы и непосредственно касается технологического процесса изготовления оболочковых изделий из водной суспензии нужной концентрации из исходных материалов, таких как бумажная макулатура, торф, солома, отходы текстильного производства и т.п.
Известны способы изготовления формованных изделий из волокнистой массы, включающие приготовление водной суспензии нужной концентрации из волокнистых материалов, формование влажного изделия на поверхности технологической оснастки методом осаждения волокон и удаление остаточной влаги из изделия методом сушки (см., например, авт. св. СССР №1048015, кл. D 21 J 7/00, 02.02.82 г.; авт. св. СССР №1416589, кл. D 21 J 7/00, 26.01.87; авт. св. СССР №1509477, кл. D 21 J 7/00, 08.10.87 г., авт. св. №2033844, кл. В 01 D 39/18, 09.06.92 г.).
В известных технических решениях (см., например, авт. св. СССР №771230, кл. D 21 J 7/00, 31.07.78 – прототип; пат. Великобритании №1511185, кл. D 21 J 7/00, 1978 г. и др.) волокнистая суспензия подается на технологическую оснастку по схеме сверху-вниз. Это на практике приводит (особенно для изделий сложной формы и с мелким рельефом поверхности) к неравномерному осаждению суспензии на сетке и образованию наплывов, т.к. процесс осаждения происходит из-за действия двух факторов: гравитации и принудительного создания перепада давления.
В отдельных случаях применяют дополнительную операцию, выполняемую до или после сушки, заключающуюся в подпрессовке влажного изделия для получения ровной поверхности с целью нанесения на нее логотипа или маркировки.
К вспомогательным операциям, обеспечивающим основной процесс, относятся: переносы изделия между исполнительными механизмами, выполняющими отдельные дискретные функции; промывка технологической оснастки; съем и пакетирование готовых изделий и др.
Как правило, решение этих технологических задач требует создания, как минимум, полуавтоматической линии, состоящей из отдельных функциональных блоков, выполняющих отдельные функции, и согласование их взаимодействия.
Известные решения технологической оснастки для выпуска формованных изделий сетчатых матрицы имеют существенные недостатки:
1) технологически сложное изготовление, обусловленное тем, что основа матрицы подлежит высокоточной механообработке, последующему сверлению отверстий для отвода фильтрата из суспензии и размещению на поверхности мелкоячеистой сетки. Для изделий сложной формы (особенно с мелким рельефом) технологическая оснастка весьма дорогостоящая, сложна в изготовлении и эксплуатации;
2) неравномерное осаждение волокон на сетке из-за невозможности выполнения большого количества мелких отверстий в теле матрицы. На практике диаметры отверстий в теле сетчатых матрицы составляют около 2 мм, а размер ячеек сетки, размещаемой на поверхности матрицы, 300 мкм.
В известном техническом решении (пат. РФ №2129630, кл. 6 D 21 J 7/00, 20.05.98) способ формования изделия из волокнистой суспензии предусматривает на этапе сушки влажного изделия операцию горячей подпрессовки с помощью сетчатого пуансона, нагретого проходящим горячим воздухом, как вариант, под изделием одновременно могут создавать разряжение. В этом случае изделие “работает” как проницаемая мембрана. Избыточное давление горячего воздуха, приложенное с одной из сторон изделия, не может не воздействовать на структуру материала изделия и его пористость, что во многих случаях не приемлемо с точки зрения потребительских свойств готового изделия.
Указанные технические решения не предусматривают подачу в водную суспензию жидких и твердых компонентов для придания материалу, из которого формуется изделие, специальных свойств, таких как теплостойкость, огнестойкость, влагонепроницаемость, химстойкость и др.
Заявляемый способ направлен на устранение указанных недостатков и, в частности:
– обеспечение направленного, без наплывов, равномерного распределения волокон бумажной массы на поверхности технологической оснастки, формирующей профиль оболочковых изделий, что особо важно при изготовлении изделий рельефной формы;
– получение качественной поверхности изделия и плотной структуры материала;
– возможность придания изделиям различных потребительских качеств за счет модификации базового волокнистого материала жидкими или твердыми порошкообразными присадками;
– упрощение технологической оснастки и снижение затрат на ее эксплуатацию.
Таким образом, заявляемый способ направлен на решение задач, которые сводятся к следующему:
– оптимизация технических решений по узлам, выполняющим отдельные дискретные функции и операции, а также совмещение операций во времени, определяющие во многом производительность оборудования по готовым изделиям;
– оптимизация технологии формования изделия и конструкции оснастки, определяющих стоимость изделия, качество поверхности оболочковых изделий, упрощение конструкции оборудования.
Решение поставленной технической задачи достигается тем, что способ изготовления формованных изделий из волокнистой массы включает приготовление водной суспензии требуемой концентрации из волокнистых материалов, формование влажного изделия путем осаждения волокон на формующем основании и удаление остаточной влаги путем сушки. Его характерной особенностью является то, что в приготовленную водную суспензию дозированно подают жидкие и твердые модификаторы для придания материалу требуемых физико-механических и эксплуатационных качеств, таких как теплостойкость, огнестойкость, влагонепроницаемость, химстойкость и пр. При этом осаждение волокон осуществляют на поверхности форм со сменными твердотельными вставками, изготовленными из пористого материала. Образование влажного изделия осуществляют на нижней поверхности формующего основания по схеме “снизу-вверх” путем наращивания волокнистого материала фильтрованием воды из суспензии через поры формующего основания за счет перепада давления, создаваемого на нем.
Одновременно с сушкой изделие подвергают подпрессовке. При этом сушку ведут в нагреваемой разъемной форме с твердотельными пористыми вставками с одновременным удалением паров воды за счет вакуумной откачки из верхней и нижней частей указанной разъемной формы.
Технические признаки заявляемого способа могут быть реализованы известными в производстве изделий из волокнистых суспензий средствами, а отличительные признаки, отраженные в формуле изобретения, необходимы и достаточны для его осуществления, т.к. обеспечивают решение поставленной выше задачи.
В дальнейшем настоящее предлагаемое изобретение поясняется примером его выполнения, схематически изображенным на прилагаемых чертежах, на которых:
Фиг.1 – схема технологического процесса изготовления формованных оболочковых изделий из волокнистой массы в соответствии с заявляемым способом;
Фиг.2 – схема формования влажного изделия на формующем основании (матрице) в соответствии с заявляемым способом;
Фиг.3 – схема переноса влажного изделия на пуансон;
Фиг.4 – схема сушки изделия с дополнительным прессованием (подпрессовкой).
Согласно заявляемому способу в блоке пульпера 1 (фиг.1) производят предварительное приготовление водной суспензии волокнистого материала базового состава. Водная суспензия может приготовляться различными известными способами, например за счет интенсивного перемешивания механическими мешалками 2 исходного материала с водой. Приготовленная суспензия насосом 3 перекачивается в блок 4 приготовления суспензии требуемой концентрации с перемешивающим устройством 5. В этот блок могут добавляться различные модификаторы для придания материалу будущего изделия требуемых потребительских качеств (теплостойкость, огнестойкость, влагонепроницаемость, химстойкость и пр.). Это добавление осуществляют путем дозированной подачи из емкости 6 насосом 7 соответствующих жидких компонентов или из бункера 8 с дозировочным устройством сыпучих материалов. Блок 4 снабжен устройством 9 известной конструкции, контролирующим концентрацию суспензии. Из блока 4 приготовленная суспензия насосом 10 подается в емкость 11 блока формования изделия 12. Блок 12 включает формующее основание (матрицу) 13. Формование влажного изделия осуществляется следующим образом.
Матрица 13 (фиг.1, 2) погружается в емкость 11 с помощью механизма подачи 14 (фиг.1) известного типа.
Матрица снабжена съемной твердотельной пористой вставкой 15, поверхность которой соответствует форме будущего оболочкового изделия 16. Вставка 15 может быть изготовлена, например (но без ограничения), путем спекания металлического порошка необходимого фракционного состава (из гранул сферической формы) или она может быть получена методом прессования.
В твердотельных формах из пористого материала за счет подбора исходного порошка (диаметра гранул) легко обеспечивается требуемая равномерная пористость для эффективного отвода фильтрата из суспензии, что приводит к равномерному осаждению волокон на поверхности формы.
Осаждение волокон из водной суспензии на рабочую поверхность матрицы осуществляется по схеме снизу-вверх за счет перепада давления, создаваемого путем подвода вакуума к верхней части пористой вставки или подвода давления воздуха (Ризб) в емкость с суспензией блока формования, или путем сочетания этих способов.
За счет исключения влияния на процесс осаждения волокон гравитационного фактора обеспечивается равномерное и регулируемое (за счет величины вакуума и времени фильтрации) формование изделия.
После осаждения на поверхности твердотельной пористой вставки матрицы слоя волокон необходимой толщины влажное изделие передается на подводимый приводом 17 под матрицу пуансон 18, повторяющий поверхность изделия, изготовленный также из твердотельного пористого материала.
Перенос изделия происходит путем подвода давления воздуха в матрицу 13 (фиг.3) сверху изделия и одновременно вакуума в пуансон 18 (снизу изделия).
Затем влажное изделие переносится на пуансоне 18 в блок подпрессовки и сушки 19.
Перемещение матрицы в вертикальной плоскости и пуансона в горизонтальной плоскости для их совмещения осуществляется соответственно механизмами перемещения 17 и 20.
Дополнительное прессование (подпрессовка) волокнистого изделия с совмещением операции сушки производится в блоке подпрессовки и сушки 22, состоящем из нагреваемой матрицы 21 с твердотельной пористой вставкой и аналогичной поз. 15 в матрице блока формования.
Влажное изделие подводится на пуансоне 18 под нагреваемую матрицу 21 блока подпрессовки и сушки, после чего матрица опускается вниз, осуществляя подпрессовку влажного изделия. Одновременно полости матрицы и пуансона соединяются с вакуумом для удаления паров воды, образующихся при сушке влажного изделия.
Удаление готового изделия с пуансона (не показано) осуществляется за счет подачи в его нижнюю часть давления воздуха, одновременно происходит продувка пористой вставки.
В это же время на стадии отвода матрицы 21 в верхнее положение производится также ее продувка воздухом во избежание появления осадка в порах пористой вставки за счет подачи давления воздуха сверху.
В известном техническом решении (пат РФ №2129630, кл. 6 D 21 J 7/00, 1998 г.) на этапе сушки влажного изделия операцию горячей подпрессовки проводят с помощью сетчатого пуансона, нагретого проходящим горячим воздухом, как вариант, под изделием одновременно могут создавать разрежение. В этом случае изделие “работает” как проницаемая мембрана. Избыточное давление горячего воздуха, приложенное с одной из сторон изделия, не может не воздействовать на структуру материала изделия и его пористость, что во многих случаях не приемлемо с точки зрения потребительских свойств.
В заявляемом техническом решении влажное изделие сжимается с 2-х сторон приводом матрицы, испаряемая из изделия вода отводится одновременно с 2-х сторон за счет вакуума, ускоряя цикл сушки и обеспечивая плотную структуру материала изделия.
Формула изобретения
1. Способ изготовления формованных изделий из волокнистой массы, включающий приготовление водной суспензии требуемой концентрации из волокнистых материалов, формование влажного изделия путем осаждения волокон на формующем основании и удаление остаточной влаги путем сушки, отличающийся тем, что в приготовленную водную суспензию дозированно подают жидкие и твердые модификаторы для придания материалу требуемых физико-механических качеств, осаждение волокон осуществляют на поверхность твердотельных форм, изготовленных из пористого материала, а образование влажного изделия осуществляют на нижней поверхности формующего основания по схеме “снизу вверх” путем наращивания волокнистого материала фильтрованием воды из суспензии через поры формующего основания за счет перепада давления, создаваемого на нем, при этом одновременно с сушкой изделие подвергают подпрессовке, причем сушку изделия ведут в нагреваемой разъемной твердотельной форме с одновременным удалением паров воды за счет вакуумной откачки из верхней и нижней частей указанной разъемной формы.
2. Способ по п.1, отличающийся тем, что к физико-механическим качествам относятся такие, как теплостойкость, огнестойкость, влагонепроницаемость, химическая стойкость.
РИСУНКИ
|