|
(21), (22) Заявка: 2003118430/03, 10.09.2001
(24) Дата начала отсчета срока действия патента:
10.09.2001
(30) Конвенционный приоритет:
21.11.2000 (пп.1-7) RU 2000129403
(43) Дата публикации заявки: 20.11.2004
(45) Опубликовано: 27.02.2006
(56) Список документов, цитированных в отчете о поиске:
WO 99/12866 A1, 18.03.1999. RU 2151814 C1, 27.06.2000. RU 2151126 C1, 20.06.2000. SU 1639915 A1, 07.04.1991. WO 99/18030 A1, 15.04.1999.
(85) Дата перевода заявки PCT на национальную фазу:
21.06.2003
(86) Заявка PCT:
EP 01/10439 (10.09.2001)
(87) Публикация PCT:
WO 02/42240 (30.05.2002)
Адрес для переписки:
129010, Москва, ул. Б. Спасская, 25, стр.3, ООО “Юридическая фирма Городисский и Партнеры”, пат.пов. Ю.Д.Кузнецову, рег.№ 595
|
(72) Автор(ы):
ЭКСТРЕМ Томми (SE), ЧЖЭН Цзе (SE), КЛОУБ Каутхар (SE), ГОРДЕЕВ Сергей Константинович (RU), ДАНЧУКОВА Лия Владимировна (RU)
(73) Патентообладатель(и):
СКЕЛЕТОН ТЕКНОЛОДЖИЗ АГ (CH)
|
(54) ТЕПЛОПРОВОДЯЩИЙ МАТЕРИАЛ
(57) Реферат:
Изобретение относится к алмазосодержащим композитным материалам, которые имеют высокую теплопроводность и высокую температуропроводность и применяются в поглотителях тепла, распределителях тепла и в других областях, где требуются теплопроводящие материалы. Материал содержит, об. %: 58-81 алмазных частиц, 3-39 карбида кремния и до 41 кремния и имеет теплопроводность в, по меньшей мере, 400 Вт/(м·К) и температуропроводность в по меньшей мере 2,1 см2/сек. Алмазные частицы состоят, по меньшей мере, из двух фракций с различным размером частиц, причем, по меньшей мере, 50 мас.% частиц имеют диаметр 80 мкм и более. Технический результат изобретения – повышение теплопроводности материала. 6 з.п. ф-лы, 3 табл., 2 ил. 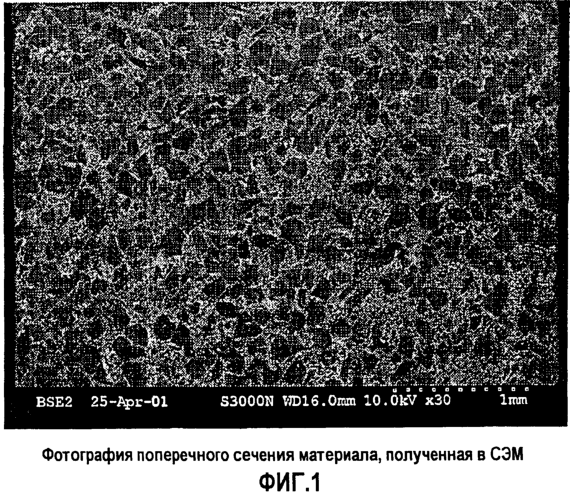
Область техники
Настоящее изобретение относится к теплопроводящему композитному материалу, изготовленному из смеси алмазных частиц и содержащему алмазные частицы, карбид кремния, а также кремний или сплав кремния.
Уровень техники
Материалы, имеющие высокую удельную теплопроводность, широко используются в теплообменных устройствах, таких как поглотители тепла, теплообменники и другие, и обычно состоят из металлов с высокой удельной теплопроводностью, таких как алюминий, медь и серебро, причем удельная теплопроводность этих металлов составляет соответственно от 120 до 220 Вт/(м·К), 400 Вт/(м·К) и 430 Вт/(м·К). Серебро является достаточно дорогим и не используется в тех же масштабах, что и медь. Использование меди имеет несколько недостатков. Один из них заключается в достаточно высокой плотности (8,9 г/см3), что делает устройства, в которых используется медь, тяжелыми. Высокая плотность меди также приводит к довольно низкому значению температуропроводности =1,2 см2/сек ( = /Ср* , где представляет собой коэффициент температуропроводности, представляет собой коэффициент теплопроводности, Ср представляет собой теплоемкость, а представляет собой плотность). Низкая температуропроводность ограничивает применение меди в тех изделиях, где не требуется быстрая теплопередача. Другой недостаток меди состоит в склонности меди к окислению. Оксид меди, образованный на поверхности теплообменного устройства, значительно снижает термические свойства всего устройства. Еще один недостаток состоит в том, что медь имеет высокий коэффициент теплового расширения относительно материала, используемого в интегральных схемах, а различие в коэффициентах теплового расширения вызывает напряжения и опасность образования трещин в месте соединения между схемой и поглотителем тепла, если медь используется в качестве поглощающего тепло материала. Недостатками алюминия являются умеренная теплопроводность и высокий коэффициент теплового расширения.
В электронной промышленности потребность в более хороших поглотителях тепла растет из-за разработки более быстрых и меньших по размеру схем. Тепловыделяющие элементы в настоящее время могут быть более плотно упакованы. Следовательно, теплопередача должна быть более эффективной, т.е. избыток тепла от локальных точек перегрева необходимо отводить быстро. Основные требования для теплопоглощающего материала – это высокая теплопроводность, коэффициент теплового расширения, близкий к коэффициенту теплового расширения Si, и низкий удельный вес (см., MRS Bulletin, Volume 26, №6, июнь 2001). В данном случае алмаз мог бы быть использован сам по себе в качестве очевидного материала для поглотителей тепла.
Алмаз, как известно, имеет хорошие теплопроводящие свойства (500-2000 Вт/(м·К)) и был бы идеальным материалом для поглотителя тепла, если бы не его стоимость и проблемы производства подходящих форм. По-прежнему много поглотителей тепла производится с использованием алмаза. Существуют различные способы введения алмаза: в виде монокристаллов алмаза, алмазных CVD-покрытий и алмазных композитов.
В патенте США №6031285 (Sumitomo) описан поглотитель тепла для полупроводников, имеющий структуру, которая содержит по меньшей мере один металл (А), выбранный из группы, включающей в себя Cu, Ag, Au, Al, Mg и Zn; карбид (B’), полученный из по меньшей мере одного металла (В), выбранного из группы, включающей в себя группы 4а и 5а Периодической таблицы и хром; и множество частиц алмаза. Поглотитель тепла имеет структуру, в которой более четверти поверхности отдельных алмазных частиц покрыта карбидом металла (B’), и алмазные частицы, покрытые карбидом металла (B’), отделены друг от друга металлом (А). Теплопередача осуществляется от алмаза к металлу (А). Теплопроводящие характеристики находятся в интервале от 230 до 730 Вт/(м·К), причем наименьшее значение достигается тогда, когда металл А состоит из Ag, Cu и Mg, а наибольшее значение достигается тогда, когда металл А состоит преимущественно из Ag и небольшого количества Cu. Недостатками изобретения являются: низкие теплопроводящие свойства при использовании Al, Mg и Zn, и высокая стоимость при использовании Ag и Au.
В патенте США №6171691 (Sumitomo) описан материал, в котором частицы алмаза окружены карбидом металла, карбид металла и алмазы образуют скелет, а промежутки в этом скелете заполнены металлом. Вначале первый металлический сплав, содержащий небольшое количество образующего карбид компонента, проникает между алмазами, которые помещены в форму. Образующий карбид компонент реагирует с алмазами и образует карбид на поверхности алмазов. Карбид вместе с алмазом образует связанную структуру. «Носитель» в металлическом сплаве либо отверждается между покрытыми карбидом алмазами, либо испаряется. Затем второй металлический сплав просачивается в свободные промежутки пористого тела. После этого тело вынимают из формы. Металл представляет собой по меньшей мере один металл из Ag, Cu, Au и Al, а образующий карбид компонент представляет собой по меньшей мере один металл из Ti, Zr и Hf. Теплопередача осуществляется от алмаза через карбид к металлу. Теплопроводящие свойства находятся в интервале от 300 до 900 Вт/(м·К). Недостатками этого материала являются сложная технология и высокая стоимость продукта.
Как патент США №6031285, так и патент США №6171691 предупреждают против использования образующего карбид компонента в качестве единственного наполняющего элемента, причем причиной является то, что образующий карбид элемент сам по себе имеет низкую теплопроводность, что снижало бы теплопроводность заявляемого материала в целом.
В патенте США №5783316 (University of California Oakland) раскрыт композит алмаз-медь-серебро. Материал состоит из алмазных частиц, связанных вместе медью или медными сплавами. Теплопроводность этого материала находится между теплопроводностью алмазных частиц и теплопроводностью меди. Для того чтобы получить более высокую адгезию медного сплава к алмазным частицам, последние покрывают тонким слоем карбидобразующего металла. Недостатками этого материала являются довольно высокая плотность, обусловленная медью, и высокий коэффициент линейного теплового расширения, который также определяется медью. Высокое тепловое расширение приводит к значительной деформации изделия при повышенных температурах. Кроме того, данный материал, как и чистая медь сама по себе, не устойчив к окислению.
Существует ряд патентов, описывающих алмазные композиты, которые не предназначены для применения преимущественно в теплообменных процессах. Основные области применения материалов такого типа составляют инструменты для резки и абразивной обработки. Несколько патентов описывают методики получения материалов, содержащих алмазы, карбид кремния и кремний, с использованием методов высокого давления.
В патенте США №4151686 описан один такой высокотемпературный метод высокого давления, в котором высокое давление используется на стадии спекания для того, чтобы остаться в области стабильности алмаза на фазовой диаграмме при 1300-1600°С, причем спекание проводят в камерах высокого давления с давлением 30000-60000 атм. Только специально изготовленные прессы и пресс-формы обеспечивают требуемое экстремально высокое давление. Следствием этого является высокая стоимость производства, ограниченная производительность и ограниченные формы и размеры тел из алмазных композитов. Материал, получаемый в соответствии с указаниями патента США №4151686, содержит по меньшей мере от 80 до 95 об.% алмазов с большим количеством связей алмаз-алмаз. Высокое содержание алмаза делает материал твердым, но также хрупким и чувствительным к механическим ударам.
Другой материал, производимый высокотемпературными методами высокого давления, представляет собой Syndax3 фирмы De Beers. Это материал предназначен для абразивной обработки (истирания), такого как сверление камня. Материал состоит из алмазных частиц и SiC, спеченных вместе. Согласно публикации «The Industrial Diamond Review», №6, 1985, материал Syndax3 имеет контакт алмаз-алмаз. Можно предположить, что контакт алмаз-алмаз мог бы быть полезен для теплопроводящих свойств. Несмотря на это, согласно проведенным Заявителем измерениям Syndax3 имеет коэффициент температуропроводности не более 1,442 см2/сек и теплопроводность не более 265 Вт/(м·К).
Несколько патентов раскрывают технологии получения материалов, содержащих алмаз, карбид кремния и кремний, без использования высокого давления. Существует ряд вариантов процесса, связанных главным образом с использованием различных углеродистых материалов (здесь и далее относимых ко всем неалмазным углеродным материалам типа углеродной сажи, углеродных волокон, кокса, графита, пироуглерода и т.д.). В принципе, проводятся следующие стадии.
А. Не покрытые алмазные частицы или, что бывает чаще, покрытые углеродом алмазные частицы, а также углеродистые материалы используются в качестве материалов-предшественников. Согласно примерам патента США №4220455 способ начинается с нанесения тонкого слоя (500-1000 Ангстрем) углерода на алмазы с помощью пиролитической реакции. Пиролиз проводят в вакууме в течение нескольких минут путем подачи природного газа или метана в печи с алмазными частицами при 1200°С. Иногда используют алмазы без слоя пиролитического углерода, как в патенте США №4381271, ЕРО 0043541, ЕРО 0056596 и JP 6-199571 А. Как покрытые углеродом, так и не покрытые алмазы смешивают с углеродистыми материалами в качестве основного источника углерода, например, с углеродной сажей, короткими углеродными волокнами или тканью и связующим веществом, до того, как формируется сырое тело.
В. Формирование сырых тел из смеси алмазные частицы/углеродистый материал проводят в форме. Сырые тела содержат дополнительные растворители и временные или постоянные связующие вещества для облегчения формования и повышения прочности сырых тел.
С. Заготовки получают тепловой обработкой сырых тел. Некоторые связующие вещества испаряются без всяких остатков, например парафин, в то время как другие связующие вещества отверждаются, оставляя углеродистый остаток в заготовке, например фенол-формальдегидные и эпоксидные смолы.
D. Просачивание в пористую заготовку расплавленного кремния проводят с образованием карбида кремния по реакции между углеродом и кремнием. Тепловую обработку проводят таким образом, чтобы свести до минимума превращение алмаза в графит, которое считается вредным. В примерах патента США №4220455 просачивание кремния проводят в вакууме, когда тело находится в форме, при температуре между 1400 и 1550°С в течение 15 мин, причем в течение указанного времени реакция между кремнием и углеродом заканчивается. В патенте США №4242106 во время просачивания используют вакуум 0,01-2,0 мм рт.ст. Требуемое время, в зависимости главным образом от размера тела, определяют эмпирически, и оно составляет приблизительно 15-20 мин при температуре выше 1400°С или 10 минут при 1500°С. В патенте США №4381271 используют углеродное волокно для того, чтобы ускорить просачивание жидкого кремния за счет действия капиллярных сил. В большинстве патентов просачивание проводят в форме. В некоторых более ранних патентах просачивание проводят вне формы, как в патенте ЕРО 0043541.
Ни в одном из описанных выше способов получения композитов алмаз/карбид кремния/кремний не используется умышленная графитизация.
В патенте RU 2036779 из алмазного порошка сначала формируют предварительную заготовку, при необходимости вместе с водой или этиловым спиртом. Предварительную заготовку помещают в печь и пропитывают жидким кремнием при 1420-1700°С в аргоне или вакууме. В этом способе поверхность алмазных зерен подвергается минимальной графитизации, так что большая часть алмаза остается неизменной. Это небольшое количество графита реагирует при контакте с просочившимся кремнием, создавая тонкий слой карбида кремния, который предупреждает любое дополнительное превращение алмаза в графит во время используемого процесса. Недостаток этого способа заключается в плохом контроле и отсутствии способа регулирования количества получаемого SiC, остаточного кремния или остаточной пористости, остающейся в композите.
В публикациях WO 99/12866 и WO 00/18702 раскрыты способы получения композита алмаз-SiC-Si. Получаемые композиты состоят из алмазных частиц в матрице SiC и Si или сплава Si в следующих пропорциях: алмазные частицы составляют по меньшей мере 20 об.%, а SiC составляет по меньшей мере 5 об.%. Композит имеет прекрасное сочетание свойств, таких как низкая плотность, высокий модуль упругости, низкий коэффициент теплового расширения, при этом он устойчив к окислению. Однако теплопроводность материала не является достаточно высокой для того, чтобы решить проблему потребности в более хороших поглотителях тепла для электронной промышленности.
Цель настоящего изобретения состоит в создании материала, который имел бы при комнатной температуре коэффициент теплопроводности по меньшей мере 400 Вт/(м·К) и температуропроводность по меньшей мере 2,1 см2/сек, который мог бы быть получен эффективным с точки зрения стоимости способом в виде изделия желаемой формы.
Сущность изобретения
Указанная цель в соответствии с настоящим изобретением достигается с помощью теплопроводящего композитного материала, изготовленного из смеси алмазных частиц и содержащего алмазные частицы, карбид кремния и кремний или сплав кремния, при этом карбид кремния образует взаимосвязанную скелетную структуру, окружающую каждую отдельную алмазную частицу, а кремний или сплав кремния заполняет промежутки скелета из карбида кремния, причем преобразованный алмаз является единственным источником углерода в материале, и указанный теплопроводящий материал имеет содержание алмаза по меньшей мере 58 об.% и самое большее 81 об.%, содержание карбида кремния по меньшей мере 3 об.% и самое большее 39 об.%, и содержание кремния или сплава кремния самое большее 41 об.%, а алмазные частицы состоят по меньшей мере из двух фракций с различным размером частиц, причем по меньшей мере 50 масс.% частиц в смеси алмазных частиц, из которых изготовлен теплопроводящий материал, имеют диаметр 80 мкм или более, в результате чего теплопроводящий материал имеет температуропроводность по меньшей мере 2,1 см2/сек и теплопроводность по меньшей мере 400 Вт/(м·К).
В предпочтительном варианте содержание азота в алмазной фракции с наибольшим диаметром составляет 300 ч/млн (частей на миллион по массе) или менее, а теплопроводность составляет по меньшей мере 430 Вт/(м·К).
В другом предпочтительном варианте изобретения содержание азота в алмазной фракции с наибольшим диаметром составляет 130 ч/млн или менее, а теплопроводность составляет по меньшей мере 490 Вт/(м·К).
В еще одном предпочтительном варианте изобретения содержание азота в алмазной фракции с наибольшим диаметром составляет 80 ч/млн или менее, а теплопроводность составляет по меньшей мере 550 Вт/(м·К).
В еще одном предпочтительном варианте изобретения сплав кремния содержит по меньшей мере один металл из группы, включающей в себя Ti, Zr, Hf, V, Nb, Ta, Cr, Mo, W, Mn, Re, Fe, Co, Ni, Cu, Ag, Al, Ge, причем в материал может быть включено небольшое количество соединения металл-углерод, содержащего по меньшей мере один металл из группы, включающей в себя Ti, Zr, Hf, V, Nb, Ta, Cr, Mo, W, Mn, Re, Fe, Co, Ni, Cu, Ag, Al, Ge. В этом варианте изобретения содержание азота в алмазной фракции с наибольшим диаметром составляет предпочтительно 100 ч/млн или менее, а теплопроводность составляет по меньшей мере 500 Вт/(м·К).
Краткое описание чертежей
Изобретение далее описано с помощью чертежей, из которых:
Фиг.1 представляет собой полученную с помощью сканирующего электронного микроскопа (СЭМ) фотографию поперечного сечения разломленного материала в соответствии с одним из вариантов осуществления изобретения.
Фиг.2 представляет собой полученную с помощью СЭМ фотографию в увеличенном масштабе поперечного сечения разломленного материала в соответствии с одним из вариантов осуществления изобретения.
Описание вариантов осуществления изобретения
Материал в соответствии с настоящим изобретением получен способами, представленными в публикациях WO 99/12866 и WO 00/18702. Эти способы включают в себя следующие стадии:
1. Формирование пористой заготовки из смеси, содержащей алмазные частицы.
2. Тепловая обработка заготовки и регулирование температуры нагревания и времени нагревания так, чтобы за счет графитизации алмазных частиц образовывалось некоторое желаемое количество графита, в результате чего образуется промежуточное тело.
3. Просачивание расплавленного кремния или, альтернативно, сплава кремния в промежуточное тело.
4. Взаимодействие расплавленного кремния и графита с образованием SiC.
С помощью производственного процесса, описанного выше, получают изделие заранее определенной формы. Во время процесса от формирования заготовки до конечного продукта на макроскопическом уровне отсутствуют усадка, набухание и деформация (перекашивание). Упомянутые выше публикации WO 99/12866 и WO 00/18702 описывают дополнительные детали способов, и их содержание включено в данную работу.
В дальнейшем:
Сырая плотность = масса сырого тела/объем сырого тела.
Относительная сырая плотность=сырая плотность/теоретическая плотность алмаза; и
Пористость = 1 – относительная сырая плотность.
Заготовку формируют из смеси алмазных частиц, имеющих минимальный размер 6 мкм, причем заготовку готовят с относительной сырой плотностью в по меньшей мере 60%. Алмазная смесь состоит по меньшей мере из двух фракций с различными размерами алмазных частиц. Из содержащегося в заготовке алмаза по меньшей мере 50% должны иметь диаметр 80 мкм или более. Использование по меньшей мере двух различных фракций с разными размерами алмазных частиц необходимо для того, чтобы достичь степени упаковки в заготовке, которая в спеченной прессовке дает достаточно высокую концентрацию алмаза (то есть имеет место короткий путь перемещения фононов между алмазами), что обеспечивает желаемый уровень температуропроводности и теплопроводности. Содержание алмаза в заготовке составляет по меньшей мере 95 масс.%, то есть может быть использовано небольшое количество связующего вещества.
Формование заготовки осуществляют известными способами, такими как литье прессованной ленты, шликерное литье или формование геля, с использованием обычного оборудования.
Суммарная продолжительность тепловой обработки алмазного тела составляет столько времени, сколько необходимо для того, чтобы масса алмаза в указанном теле уменьшилась на желаемую величину вследствие графитизации алмазных частиц. Примером тепловой обработки является нагревание заготовки до температуры между 1000 и 1900°С в вакууме или в инертной атмосфере.
Пропитку расплавленным Si или сплавом Si проводят такими известными способами, как плавление твердого образца на поверхности заготовки и подача уже расплавленного Si или сплава Si на поверхность заготовки, или же путем погружения заготовки в расплав Si или сплав кремния. По мере просачивания расплава в заготовку он реагирует с графитом и образует SiC или фазу SiC, включающую в себя элементы, являющиеся компонентами сплава. Образовавшаяся фаза карбида кремния и небольшое количество фазы непрореагировавшего кремния или сплава кремния заполняют пористое пространство заготовки.
Тепловую обработку и пропитку можно успешно проводить в той же самой печи.
Используемый просачивающийся расплав может представлять собой сплав кремния, содержащий по меньшей мере один металл, выбранный из группы, включающей в себя Ti, Zr, Hf, V, Nb, Ta, Cr, Mo, W, Mn, Re, Fe, Co, Ni, Cu, Ag, Al и Ge. В этом случае могут образоваться небольшие количества вторичной фазы из таких соединений, как силициды металлов, карбиды металлов и т.д.
Таким образом, спеченный композитный материал состоит из трех основных фаз: алмазной фазы, фазы карбида кремния вокруг алмазных частиц и фазы непрореагировавшего кремния или сплава кремния между областями карбида кремния. На Фиг.1 представлен вид обычного поперечного сечения материала, полученного с помощью способа, описанного выше в соответствии с вариантом настоящего изобретения, наблюдаемый с помощью обратного рассеивания электронов в сканирующем электронном микроскопе. Темные частицы представляют собой алмаз, серый скелет представляет собой SiC, и белые пятна соответствуют участкам кремния. Начальный состав алмазного порошка был таким: 75 масс.% D8(150 мкм) + 20 масс.% D31(20 мкм + 5 масс.% D32(7 мкм), где обозначения D8, D31 и D32 представляют собой сокращенные названия различных используемых алмазов, а различные средние размеры используемых частиц указаны в скобках. Карбид кремния, который образуется по реакции между графитизированным алмазом и расплавом, покрывает и окружает каждую отдельную частицу алмаза. Фаза SiC образует взаимосвязанную скелетную структуру, которая охватывает со всех сторон частицы алмаза. На Фиг.2 представлен более увеличенный вид типичного поперечного сечения второго варианта материала в соответствии с настоящим изобретением, содержащего 200-250 мкм алмазы (диаметры наиболее крупных частиц), для иллюстрации плотной (тесной) связи алмазов и SiC, окружающего алмазы. В композитном материале фактически нет контактов алмаз-алмаз. Из-за того, что SiC имеет больший коэффициент теплового расширения, чем коэффициент термического расширения алмаза, SiC в процессе охлаждения по окончании тепловой обработки стремится к сокращению в большей степени, чем алмазные частицы. При температурах ниже той температуры, при которой образуется SiC, окружающий отдельные алмазные частицы SiC будет оказывать сжимающее усилие на каждую частицу. Полагают, что это вносит некоторый вклад в неожиданно хорошую теплопроводность материала в соответствии с настоящим изобретением. Кремний или непрореагировавший сплав кремния вместе с возможными небольшими количествами соединений вторичной фазы, такими как карбиды металлов, силициды металлов и другие, расположены на участках внутри или между карбидом кремния, который охватывает алмазные частицы. Спеченный композитный материал содержит указанные фазы в следующих пропорциях: алмазы 58-81 об.%, Si или сплав Si максимально 39 об.%, и SiC 3-41 об.%.
Границы содержания алмаза были определены эмпирически. Концентрация алмаза ниже 58 об.% в конечном теле приводит к слишком низкой теплопроводности. Концентрацию алмаза свыше 79 об.% трудно получить с помощью используемой технологии формования. Более того, концентрация алмаза свыше 79 об.% создает проблемы во время просачивания расплава, так как вся заготовка не может быть полностью заполнена расплавом, и это приводит к плохим свойствам конечного композита, как термическим, так и механическим. Однако с помощью специальных технологий формования и технологий просачивания при содействии умеренного давления концентрация алмаза в конечной основе может быть немного повышена, при этом может быть получена концентрация алмаза 81 об.%.
Для получения высокого значения теплопроводности композитного материала критической является хорошая адгезия между различными фазами (см., Handbook of industrial diamonds and diamond films, pages 184). Графитовый слой, образованный на поверхности алмазных частиц, имеет очень хорошую адгезию к алмазу, так как графит является преобразованным алмазом. Когда расплав кремния реагирует с указанным графитом, образованный карбид кремния наследует очень хорошую адгезию к алмазу, при этом образуется прочная связь между карбидом и алмазом. Когда зародышеобразование карбида кремния происходит на поверхности графита, который образован в результате графитизации алмаза, получаемый карбид кремния растет эпитаксиально, то есть растущий на алмазе кристалл карбида кремния следует (соответствует) кристаллографической ориентации алмаза. Модель, по которой образуется карбид кремния, а также прочная связь между алмазными частицами и окружающим их карбидом кремния, как полагают, являются решающими факторами для получения удивительно высокой теплопроводности материала в соответствии с настоящим изобретением. В материале согласно настоящему изобретению получают длинный свободный путь для переноса фононов. В таблице 3 показано, что теплопроводность зависит от того, как углерод, который образует карбид кремния, введен в материалы с идентичными по всем другим позициям исходными составами.
Хорошее качество исходных материалов, алмазов, а также кремния является существенным для достижения максимальных уровней температуропроводности и теплопроводности. Примеры важных параметров качества алмаза являются низкие содержания кобальта, никеля и азота в объеме алмаза. Хорошо известно, что низкий уровень азота обеспечивает хорошую теплопроводность. Положительный результат наблюдается, если содержание азота в алмазных частицах крупного размера составляет 300 ч/млн или менее, предпочтительно 100 ч/млн или менее. Очень высокие значения теплопроводности достигаются, когда содержание азота составляет 80 ч/млн или менее.
Графитизация поверхностей алмаза оказывает положительный эффект с точки зрения физических дефектов поверхности алмазных частиц, вызываемых различными видами механической обработки типа измельчения или просеивания. Графитизация преобразует дефектные слои на поверхности алмаза, в результате обеспечивая улучшение пути переноса фононов.
Неожиданно установлено, что прямое связывание между алмазами не является необходимым для достижения хорошей теплопроводности. Более существенным является наличие пути переноса фононов высокого качества. Это иллюстрируется приведенными ниже примерами.
В таблицах 1 и 2 представлены значения температуропроводности и теплопроводности для ряда композиций с различными фазами. В таблице 1 сделан акцент на установленные уровни алмаза, а в таблице 2 важным является размер алмазных частиц. Обозначения D1, D2 и так далее представляют собой сокращенные названия различных алмазов, а средний размер частиц указан в скобках.
Фазовый состав спеченных образцов, приведенный в таблицах 1 и 2, является рассчитанным значением. Использованы следующие четыре уравнения.
D=(1- 0)(1- )
SiC=(1- 0)(MSiC* D/MC* SiC)
Si=1-( D+ SiC)
=( ScD+1,18* 0-3,51)/(2,03(1- 0)),
где 0 представляет собой исходную пористость, ScD, D и SiC представляют собой плотности соответственно спеченного композита, алмаза и карбида кремния, MSiC и MC представляют собой молекулярные массы карбида кремния и углерода, и, наконец, представляет собой степень графитизации.
Материал в соответствии с изобретением проявляет коэффициент теплового расширения в интервале между 1,8×10-6 до 2,3×10-6 К-1. Это очень низкий уровень теплового расширения, который хорошо соответствует коэффициентам теплового расширения плат с интегральными схемами.
Как указывалось ранее, тип источника углерода или, иными словами, способ введения углерода для получения карбида играет важную роль с точки зрения обеспечения высокого уровня теплопроводности. Проведен ряд опытов для того, чтобы количественно охарактеризовать это явление. Углерод добавляют в заготовку или он образуется в заготовке тремя путями. Затем заготовку пропитывают расплавом кремния и измеряют температуропроводность спеченного композита. Алмазная смесь, образующая заготовку, является полностью одинаковой и представлена составом образца А. Источники углерода для образования карбида получали графитизацией алмазов, осаждением пироуглерода в заготовке и смешением угольного порошка с алмазным порошком, который образует заготовку. Условия и результаты опытов представлены в таблице 3.
Очевидно, что образец А, в котором нет внешнего источника углерода, имеет наиболее высокую температуропроводность. Для расчета уровня теплопроводности фазовые составы образцов в данном случае определены с помощью анализа СЭМ-изображения поверхностей разлома.
Существуют некоторые различия в фазовых составах между четырьмя различными группами образцов. Причиной таких различий в конечном продукте являются трудности в достижении точно одинакового конечного состава при использовании различных способов производства. При добавлении внешнего углерода (В; С; D) остаточное количество кремния в конечном образце снижается приблизительно от 10% для образца А. Это особенно заметно в случае добавления пироуглерода (В;С), где наблюдается менее 1% кремния. Впоследствии образование карбида кремния увеличивается до некоторой степени, но общие фазовые сдвиги приводят к умеренным различиям в значениях Ср, используемых для расчета уровня теплопроводности различных образцов, см. Таблицу 3.
Описанные выше колебания не являются достаточно большими для того, чтобы ими можно было объяснить большие отличия в измеренной температуропроводности при добавлении внешнего углерода. Важным является наличие углерода, формирующегося именно из алмаза и образующего окружающий алмаз SiC-слой, который простирается в виде скелетной структуры по всему композиту и обеспечивает оптимальный решеточный механизм переноса фононов. В таблице 3 показано большое влияние природы источника углерода на температуропроводность. Когда композит готовят в соответствии с настоящим изобретением, конечное значение теплопроводности превышает теплопроводность металлов, наилучшим из которых является медь с =400 Вт/(м·К) и =1,16 см2/сек.
Температуропроводность измеряют с использованием технологии лазерной вспышки. Верхнюю поверхность образца в виде диска облучают лазером, который дает мгновенный энергетический импульс. Энергия лазера абсорбируется верхней поверхностью и проходит через образец. Сразу после излучения лазерной вспышки температуру задней поверхности проверяют на тепловое излучение, которое определяют с использованием фотоэлектрического инфракрасного детектора. Лазерный импульс повышает температуру образца только на несколько градусов. Температуропроводность ( ) рассчитывают, исходя из толщины (L) образца и времени, необходимого для того, чтобы температура задней поверхности достигла половины общего повышения температуры (t1/2) с использованием уравнения =kL2/t1/2, где k представляет собой константу. Используемое оборудование для создания лазерной вспышки представляет собой ULVAC Sinku-Rico TC-700/Melt с лазером на основе неодимового стекла, который имеет колебательную длину волны 1,064 мкм, и индий-сурьмяным ИК-детектором, который охлаждается жидким азотом. Образцы представляют собой диски диаметром 10 мм и толщиной 4-5 мм. Измерения проводят при комнатной температуре, ширина импульса составляет 0,88 мсек, продолжительность импульса составляет 0,3 мсек, диаметр импульса 15 мм, энергия импульса 15 Дж/импульс и напряжение 2,4 кВ.
Затем рассчитывают теплопроводность с использованием уравнения = /Ср , где Ср представляет собой теплоемкость и представляет собой плотность. Теплоемкость рассчитывают в соответствии с уравнением Ср= ( i iCi)/ ScD, где ScD представляет собой плотность спеченного композита, i представляет собой плотность каждой фазы, i представляет собой объемную долю каждой фазы, а Ci представляет собой теплоемкость каждой фазы.
Таблица 1 |
Начальный состав (масс.%) |
Размер частиц каждого типа алмаза (мкм) |
Относительная сырая плотность% |
Плотность (г/см3) |
Расчетное значение Ср(Дж/(кг·К)) |
Фазовый состав спеченного композита (об.фракция) |
измеренное значение a±5% (см2/сек) |
Расчетное значение (Вт/(м·К) |
D |
SiC |
Si |
65%D1+25% D23+10%D32 |
D1(420), D23(53), D32(7) |
77 |
3,293 |
538 |
0,79 |
0,03 |
0,18 |
3,455 |
612 |
65%D2+25% D23+10%D32 |
D2(420), D23(53), D32(7) |
77 |
3,283 |
539 |
0,78 |
0,03 |
0,19 |
3,333 |
590 |
65%D34+25% D24+10%D32 |
D34(300), D24(50), D32(7) |
79 |
3,332 |
544 |
0,75 |
0,13 |
0,12 |
3,408 |
618 |
65%D5+25% D31+10%D32 |
D5(150), D31(20), D32(7) |
79 |
3,394 |
547 |
0,73 |
0,23 |
0,04 |
3,389 |
630 |
65% D11+35% D25 |
D11(200), D25(28) |
75 |
3,230 |
549 |
0,72 |
0,06 |
0,23 |
2,642 |
468 |
75%D8+20% D31+5%D32 |
D8(150), D31(20), D32(7) |
74 |
3,369 |
558 |
0,66 |
0,30 |
0,04 |
3,362 |
632 |
75%D9+15% D31+5%D32 |
D9(88), D31(20), D32(7) |
72 |
3,306 |
559 |
0,65 |
0,24 |
0,11 |
2,642 |
488 |
75%D26+20% D31+5%D32 |
D26(91), D31(20), D32(7) |
70 |
3,302 |
562 |
0,63 |
0,26 |
0,11 |
2,176 |
404 |
50,7% D3+49,3%D29 |
D3(420), D29(10) |
71 |
3,345 |
563 |
0,62 |
0,32 |
0,06 |
2,713 |
511 |
70%D37+15% D24+5%D31 |
D37(200), D24(50), 31(20) |
70 |
3,338 |
565 |
0,61 |
0,33 |
0,06 |
2,759 |
521 |
70%D24+30%D30 |
D24(50), D30(5) |
70 |
3,340 |
566 |
0,60 |
0,34 |
0,06 |
2,036 |
385 |
70%D10+25% D31+5%D29 |
D10(80), D31(20), D29(10) |
68 |
3,300 |
567 |
0,60 |
0,30 |
0,10 |
2,282 |
427 |
80%D7+15% D24+5%D31 |
D7(125), D24(50), D31(20) |
65 |
3,227 |
569 |
0,58 |
0,24 |
0,18 |
2,704 |
497 |
100% D23 |
D23(53) |
64 |
3,277 |
573 |
0,55 |
0,33 |
0,12 |
1,869 |
351 |
60%D24+40% D29 |
D24(50), D29(10) |
65 |
3,295 |
578 |
0,55 |
0,36 |
0,09 |
1,762 |
336 |
Таблица 2 |
Начальный состав (масс.%) |
Размер частиц каждого типа алмаза (мкм) |
Относительная сырая плотность, % |
Плотность (г/см3) |
Расчетное значение Ср(Дж/(кг·К)) |
Фазовый состав спеченного композита (об.фракция) |
измеренное значение a±5% (см2/сек) |
Расчетное значение (Вт/(м·К) |
D |
SiC |
Si |
|
|
65% D4+25% D24+10%D32 |
D4(500), D24(50),D32(7) |
79 |
3,345 |
545 |
0,75 |
0,15 |
0,10 |
3,590 |
657 |
65% D1+25% D28+10%D27 |
D1(420), D28(53),D27(6) |
79 |
3,318 |
541 |
0,77 |
0,09 |
0,14 |
4,076 |
732 |
65% D3+25% D24+10%D32 |
D3(420), D24(50),D32(7) |
79 |
3,339 |
544 |
0,75 |
0,14 |
0,11 |
3,372 |
613 |
50,7% D3+49,3% D29 |
D3(420), D29(10) |
74 |
3,361 |
558 |
0,66 |
0,29 |
0,05 |
2,851 |
535 |
65% D34+25% D24+10%D32 |
D34(300), D24(50),D32(7) |
79 |
3,332 |
544 |
0,75 |
0,13 |
0,12 |
3,408 |
618 |
65% D12+35% D31 |
D12(160), D31(20) |
75 |
3,329 |
553 |
0,69 |
0,21 |
0,10 |
2,993 |
551 |
75% D8+20% D31+5%D32 |
D8(150), D31(20),D32(7) |
74 |
3,369 |
558 |
0,66 |
0,30 |
0,04 |
3,362 |
632 |
65% D14+35% D31 |
D14(180), D31(20) |
74 |
3,307 |
554 |
0,69 |
0,19 |
0,12 |
2,822 |
517 |
65% D13+25% D31+10%D32 |
D13(160), D31(20),D32(7) |
77 |
3,364 |
551 |
0,71 |
0,23 |
0,06 |
2,793 |
517 |
70% D15+30% D35 |
D15(150), D35(8) |
70 |
3,314 |
565 |
0,62 |
0,29 |
0,09 |
2,182 |
408 |
75% D36+20% D31+5%D32 |
D36(125), D31(20),D32(7) |
74 |
3,332 |
557 |
0,68 |
0,24 |
0,08 |
2,562 |
475 |
75% D22+25% D29 |
D22(125), D29(10) |
32 |
3,273 |
565 |
0,61 |
0,25 |
0,14 |
2,351 |
435 |
70% D17+30% D29 |
D17(125), D29(10) |
69 |
3,311 |
566 |
0,61 |
0,30 |
0,09 |
2,230 |
418 |
70% D16+30% D35 |
D16(106), D35(8) |
70 |
3,322 |
565 |
0,62 |
0,30 |
0,08 |
2,226 |
418 |
75% D26+20% D31+5%D32 |
D26(91), D31(20),D32(7) |
70 |
3,265 |
561 |
0,65 |
0,20 |
0,15 |
2,228 |
408 |
75% D9+15% D31+10%D32 |
D9(88), D31(20),D32(7) |
72 |
3,306 |
559 |
0,65 |
0,24 |
0,11 |
2,642 |
488 |
70% D10+25% D31+5%D29 |
D10(80), D31(20),D32(7) |
66 |
3,290 |
570 |
0,58 |
0,32 |
0,10 |
2,300 |
449 |
70% D18+30% D30 |
D18(75),D30(5) |
71 |
3,315 |
562 |
0,64 |
0,27 |
0,09 |
2,020 |
376 |
70% D19+30% D30 |
D19(63),D30(5) |
70 |
3,340 |
566 |
0,60 |
0,34 |
0,06 |
2,036 |
385 |
60% D24+40% D29 |
D24(50), D29(10) |
65 |
3,295 |
578 |
0,55 |
0,36 |
0,09 |
1,762 |
336 |
70% D20+30% D33 |
D20(45),D33(3) |
70 |
3,318 |
564 |
0,62 |
0,30 |
0,08 |
1,948 |
365 |
70% D21+30% D33 |
D21(38),D33(3) |
70 |
3,328 |
564 |
0,62 |
0,30 |
0,08 |
1,946 |
365 |
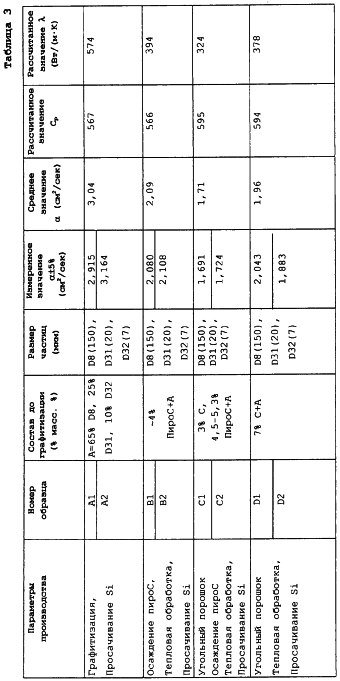
Формула изобретения
1. Теплопроводящий композитный материал, изготовленный из смеси алмазных частиц и содержащий алмазные частицы, карбид кремния и кремний или сплав кремния, при этом карбид кремния образует взаимосвязанную скелетную структуру, окружающую каждую отдельную алмазную частицу, а кремний или сплав кремния заполняет промежутки скелета карбида кремния, причем преобразованный алмаз является единственным источником углерода в материале, и указанный теплопроводящий материал имеет содержание алмаза по меньшей мере 58 об.% и самое большее 81 об.%, содержание карбида кремния по меньшей мере 3 об.% и самое большее 39 об.% и содержание кремния или сплава кремния самое большее 41 об.%, а алмазные частицы состоят по меньшей мере из двух фракций с различным размером частиц, причем по меньшей мере 50 мас.% частиц в смеси алмазных частиц, из которых изготовлен теплопроводящий материал, имеют диаметр 80 мкм или более, в результате чего теплопроводящий материал имеет температуропроводность по меньшей мере 2,1 см2/с и теплопроводность по меньшей мере 400 Вт/(м·К).
2. Теплопроводящий материал по п.1, в котором содержание азота в алмазной фракции с самым большим диаметром составляет 300 ч/млн или менее, а теплопроводность составляет по меньшей мере 430 Вт/(м·К).
3. Теплопроводящий материал по п.2, в котором содержание азота в алмазной фракции с самым большим диаметром составляет 130 ч/млн или менее, а теплопроводность составляет по меньшей мере 490 Вт/(м·К).
4. Теплопроводящий материал по п.3, в котором содержание азота в алмазной фракции с самым большим диаметром составляет 80 ч/млн или менее, а теплопроводность составляет по меньшей мере 550 Вт/(м·К).
5. Теплопроводящий материал по п.1, в котором сплав кремния содержит по меньшей мере один металл из группы, состоящей из Ti, Zr, Hf, V, Nb, Ta, Cr, Mo, W, Mn, Re, Fe, Co, Ni, Cu, Ag, Al, Ge.
6. Теплопроводящий материал по п.5, который включает в себя небольшое количество соединения металл – углерод, содержащего по меньшей мере один металл из группы, состоящей из Ti, Zr, Hf, V, Nb, Ta, Cr, Mo, W, Mn, Re, Fe, Co, Ni, Cu, Ag, Al, Ge.
7. Теплопроводящий материал по п.5, в котором содержание азота в алмазной фракции с самым большим диаметром составляет 100 ч/млн или менее, а теплопроводность составляет по меньшей мере 500 Вт/(м·К).
РИСУНКИ
|
|