|
(21), (22) Заявка: 2004111349/06, 13.04.2004
(24) Дата начала отсчета срока действия патента:
13.04.2004
(45) Опубликовано: 10.11.2005
(56) Список документов, цитированных в отчете о поиске:
RU 2166660 C1, 10.05.2001. RU 2117810 C1, 20.08.1998. RU 2117811 C1, 20.08.1998. RU 2216641 C1, 20.11.2003. JP 49-25324 A, 26.09.1974. DE 2444930 A1, 01.04.1976. US 4601862 A, 22.07.1986.
Адрес для переписки:
614113, г.Пермь, ул. Чистопольская, 16, Федеральное государственное унитарное предприятие “Научно-исследовательский институт полимерных материалов”
|
(72) Автор(ы):
Валеев Н.С. (RU), Барсукова С.П. (RU), Ямпольская В.Д. (RU), Зверева И.Г. (RU), Балабанов Г.К. (RU), Державинский Н.В. (RU), Колесников В.И. (RU), Талалаев А.П. (RU)
(73) Патентообладатель(и):
Федеральное государственное унитарное предприятие “Научно-исследовательский институт полимерных материалов” (RU)
|
(54) ЗАРЯД РАКЕТНОГО ТВЕРДОГО ТОПЛИВА
(57) Реферат:
Заряд ракетного твердого топлива содержит корпус, топливный заряд, прочноскреплённый с корпусом, и защитно-крепящий слой. Защитно-крепящий слой выполнен по всей поверхности заряда вплоть до канала с переменной толщиной 0.1·10-2-7.75·10-2 наружного диаметра заряда и выполняет роль теплозащиты, крепящего слоя, торцевых эластичных вставок и манжет. Защитно-крепящий слой представляет собой листовой каландрованный материал на основе цис-бутадиенового и цис-изопренового каучуков с наполнителем из технического углерода в количестве 78-100 массовых частей, в которую введены ди-(2-этилгексил) себацинат в количестве 10-20 массовых частей и дополнительно – сера 1-3 массовых части, окись цинка 3-8 массовых части, альтакс 1-3 массовых части, рубракс 4-6 массовых части. Изобретение повысит технологичность изготовления заряда твердого топлива, пригодного как для металлических корпусов, так и для корпусов из композиционных материалов. 1 табл., 3 ил. 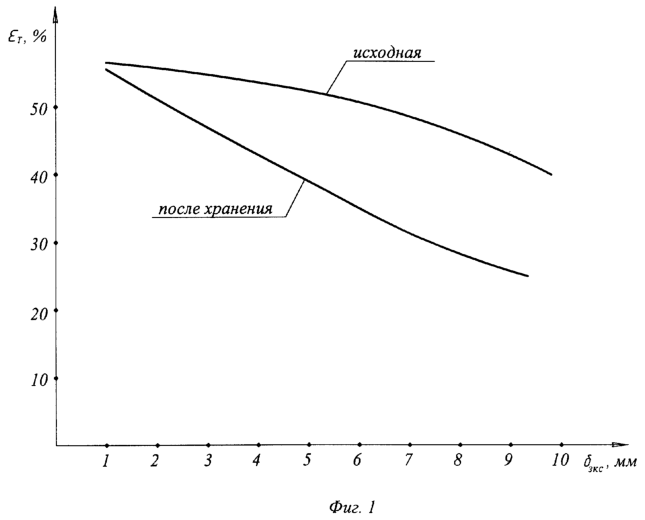
Изобретение относится к военной технике, и в частности к ракетным двигателям (РД) с зарядами из смесевых твердых топлив (СТТ), прочноскрепленных с корпусом РД с помощью защитно-крепящих слоев (ЗКС).
Объект изобретения представляет собой прочноскрепленный с корпусом РД заряд из СТТ, предназначенный для эксплуатации в широком диапазоне температур (от минус 60 до 60°С).
Одним из наиболее сложных вопросов разработки РД является обеспечение надежного скрепления заряда твердого топлива с корпусом ракетного двигателя.
Надежность скрепления определяется прочностью и долговечностью адгезионного соединения топлива с корпусом и во многом зависит от схемы защитно-крепящего слоя и способа скрепления заряда с корпусом, а также применяемых при этом материалов.
Важное значение для надежного скрепления заряда с корпусом имеет также правильно выбранная толщина ЗКС, которая зависит от конструкции заряда и материала корпуса.
В зарубежной и отечественной практике широко используются заряды ракетного твердого топлива, содержащие корпус, прочноскрепленный с ним топливный заряд, защитно-крепящий слой со следующей схемой крепления зарядов твердого топлива к стенкам ракетного двигателя: вначале на внутреннюю поверхность корпуса наносится теплозащитное покрытие (ТЗП) требуемой толщины, а затем на это покрытие наносится крепящий слой, обеспечивающий прочное крепление заряда к корпусу двигателя в процессе отверждения топлива (см. патент Японии №49-25324, кл. С 06 D 1/04, 1975 г., заявка ФРГ №2444930, кл. С 06 D 5/00, 1978 г., патент США №4601862, кл. С 06 D 21/00, 1987 г.).
Данные технические решения предусматривают двухслойное защитно-крепящее покрытие: наличие теплозащитного и адгезионного слоев, крепящих заряд твердого топлива к теплоизолированной внутренней поверхности корпуса РД. Наличие двух слоев усложняет конструкцию, технологию изготовления зарядов твердого топлива и ведет к увеличению их стоимости производства.
Общими признаками с предлагаемым авторами зарядом ракетного твердого топлива является наличие в составе заряда корпуса прочноскрепленного с ним топливного заряда, защитно-крепящего слоя.
Значительный технико-экономический эффект может быть достигнут при выполнении защитно-крепящего покрытия из одного материала, сочетающего функции теплозащитного покрытия и крепящего слоя. В этом случае материал должен обладать высокой адгезионной способностью как к материалу корпуса, так и к заряду твердого ракетного топлива, обеспечивать защиту корпуса от воздействия продуктов сгорания топлива, т.е. иметь определенную толщину покрытия, в том числе и переменную по длине корпуса, включая участки со сложной конфигурацией.
В настоящее время для зарядов РД широко используются топлива на основе полидиенуретанэпоксидного каучука, сохраняющие эластичное состояние до температуры минус 60°С. Для крепления зарядов из таких топлив к корпусам РД необходим ЗКС, обеспечивающий требуемый уровень адгезии топлива к поверхности корпуса в интервале температур от минус 60 до 60°С. Наиболее близкой по техническому результату к заявляемому техническому решению является конструкция заряда ракетного твердого топлива по патенту России №2166660, кл. F 02 К 9/32, 2000 г., принятая авторами за прототип. Конструкция заряда по принятому прототипу содержит корпус, прочноскрепленный с топливным зарядом. Топливный заряд скреплен с корпусом одним защитно-крепящим составом постоянной толщины и торцевыми манжетами, основа которых по химическому составу соответствует основе топливного заряда и выполнена из полидиенуретанэпоксида.
Общими признаками с предлагаемой авторами конструкцией заряда ракетного твердого топлива являются: наличие корпуса, топливного заряда и защитно-крепящего слоя, а также одинаковая схема крепления топливного заряда к корпусу РД с помощью ЗКС, выполняющего одновременно функции теплозащиты корпуса и крепящего состава.
Одним из существенных недостатков ЗКС на основе полидиенуретанэпоксида, принятого за прототип, является то, что, представляя собой жидкую композицию с вязкостью 100-150 пуаз при температуре 60°С, он наносится на корпуса методом заливки с последующим отверждением при вращении корпуса, что неприемлемо для корпусов сложной геометрической формы (конус, сфера и т.п.) и больших габаритов, а также корпусов, имеющих переменную толщину ЗКС и сложные торцевые манжеты. Кроме того, для нанесения ЗКС на корпус ракетного двигателя необходимо специальное оборудование, включающее установку для нанесения и установку для непрерывного вращения корпусов, исключающую стекание состава со стенок корпуса при его отверждении. Другим недостатком такого ЗКС является то, что одинаковая связующая основа топлива и ЗКС, обеспечивая благоприятные условия для формирования прочного адгезионного соединения между ними, в то же время предопределяет значительную миграцию в ЗКС пластификатора, входящего в состав топлива. Следует отметить, что область применения защитно-крепящих составов на основе полидиенуретанэпоксида ограничена, как правило, ракетными двигателями с непродолжительным временем работы (5-10 с), корпуса которых имеют цилиндрическую форму.
В отличие от прототипа в предлагаемой авторами конструкции заряда ракетного твердого топлива крепление заряда к корпусу осуществляется при помощи адгезионноспособного материала с высокой термо- и морозостойкостью, обеспечивающего крепление зарядов из топлив на основе полидиенуретанэпоксидных каучуков к корпусам любой конфигурации, включая корпуса с переменной толщиной ЗКС и сложной конфигурацией манжет, позволяет полностью торец заряда до канала. При этом предлагаемый материал представляет собой каландровый листовой невулканизованный материал (резиновая смесь), которым выкладывается внутренняя поверхность корпуса с одновременной вклейкой эластичных вставок сложной конфигурации, выполненных из этого же материала, с последующей вулканизацией резиновой смеси при повышенных температурах (140-170°С) и давлении (5-15 кгс/см2) с одновременным приклеиванием его к корпусу РД.
Технической задачей заявляемого изобретения является разработка конструкции заряда ракетного твердого топлива, обладающего более высокими техническими характеристиками во всех условиях эксплуатации, повышенной технологичностью и меньшей трудо- и энергоемкостью по сравнению с прототипом и пригодного как для металлических корпусов, так и корпусов из композиционных материалов.
Технический результат достигается за счет того, что топливный заряд скреплен с корпусом одним защитно-крепящим слоем толщиной 0.1·10-2-7.75·10-2 наружного диаметра заряда, которая может изменяться по всей поверхности заряда в этих же пределах, и выполняет одновременно роль теплозащиты, крепящего слоя, торцевых эластичных вставок и манжет, защищающих торцы заряда вплоть до канала.
Основа ЗКС по своему химическому составу родственна основе топливного заряда и представляет собой смесь бутадиенового и изопренового каучуков, взятых в соотношении от 50-65 до 50-35 мас.ч. соответственно. Как известно, в молекулярную цепь полидиенуретанэпоксида, являющеюся связующей основой топлива, входят изопреновые и бутадиеновые звенья, что создает предпосылки для обеспечения достаточно высокой адгезии между соответствующим топливом и ЗКС на основе бутадиенового и изопренового каучуков без применения специальных адгезионных добавок.
Введение в состав ЗКС пластификатора ди-2(этилгексил)себацината ДОС в количестве 10-20 мас.ч. позволяет в значительной степени подавить миграцию пластификатора из топлива в ЗКС и обеспечить сохранение механических свойств прилегающего к покрытию слоя топлива на требуемом уровне.
Новое конструктивное исполнение отдельных узлов и деталей заряда ракетного твердого топлива, а также применение нового композиционного материала приводят к получению положительного эффекта по сравнению с прототипом, а именно:
– применение в качестве полимерной основы материала ЗКС смеси неполярных цис-бутадиенового и цис-изопренового каучуков с использованием вулканизующей системы: сера 1-3 мас.ч., окись цинка 3-8 мас.ч., альтакс 1-3 мас.ч. – позволяет расширить диапазон его применения для ракетных двигателей с более продолжительным временем работы до (20-30 с);
– введение в рецептуру ЗКС увеличенного в 3-6,7 раза, по сравнению с прототипом, содержания технического углерода марок ПМ-75 и ТГ-18, взятых в соотношении примерно 3:1, позволяет получить состав в виде каландрованного листового материала и использовать его для термозащиты и скрепления корпусов любой конфигурации, включая корпуса с переменной толщиной слоя ЗКС (0.1·10-2-7.75·10-2 наружного диаметра заряда) по длине корпуса.
– топливный заряд может скрепляться с корпусом, выполненным из металла и любого органо- или стеклопластикового материала.
Указанные границы толщины ЗКС установлены расчетным путем и подтверждены эксперементально результатами многочисленных исследований и испытаний. При толщине слоя ЗКС ниже установленной величины возможны оголения поверхности корпуса при механической обработке (шероховке). Превышение толщины ЗКС выше установленного значения может привести к снижению относительных деформаций прилегающего к ЗКС слоя топлива из-за обеднения его пластификатором. Зависимость деформации топлива от толщины ЗКС приведена на фиг.1. Уменьшение относительной деформации ( ) прилегающего к ЗКС слоя топлива ниже установленной для топлива нормы приводит к снижению вероятности безотказной работы заряда вплоть до возможности его прочностного разрушения;
– технологическая добавка рубракс 4-6 мас.ч. в сочетании с неозоном 0.8-1.5 мас.ч. позволяют придать резине оптимальные технологические свойства (каландруемость и сохранение полотном формы и размеров при длительном хранении). Изготовление «сырой» каландрованной резиновой смеси в виде полотна, которое до нанесения на корпус может храниться до 6 месяцев, в достаточном количестве для изготовления большого количества корпусов позволяет значительно расширить технологические возможности производства;
– все компоненты, входящие в состав резины на основе цис-изопренового и цис-бутадиенового каучуков в комплексе, наряду с высокой адгезией к топливу на основе полидиенуретанэпоксида позволили получить значения прочности и относительного удлинения резины в 4-6 раз выше, чем у прототипа, и использовать ее как для металлических, так и органо- и стеклопластиковых корпусов сложного профиля (корпус, сфера и т.п.) одновременно в качестве защитно-крепящего слоя, эластично торцевых вставок и манжет, защищающих торец заряда вплоть до канала.
Сущность изобретения заключается в том, что заряд ракетного твердого топлива (фиг.2) содержит корпус 1, прочноскрепленный с ним топливный заряд 2, защитно-крепящий слой 3, эластичные вставки 4 и торцевые манжеты 5 и в случае необходимости теплозащитное покрытие (ТЗП) 6.
В отличие от прототипа в предлагаемом изобретении основу защитно-крепящего слоя, эластичных вставок и торцевых манжет составляет цис-бутадиеновый и цис-изопреновый каучуки, в который введены наполнители – технический углерод марок ПМ-75 и ТГ-70, пластификатор ди-(2-этилгексин)себацинат и дополнительные компоненты – сера, альтакс, рубракс, окись цинка, при этом толщина защитно-крепящего слоя составляет от 0.1·10-2 до 7.75·10-2 наружного диаметра заряда и может изменяться по длине корпуса в этих же пределах.
Предлагаемая резиновая смесь в целом и входящие в ее состав компоненты хорошо совмещаются с конструкционными материалами в составе корпуса, например, с резиновой смесью на основе этиленпропиленовых каучуков и сохраняет работоспособность в контакте с этими материалами.
Сравнительные свойства предлагаемого ЗКС и прототипа представлены в таблице.
Сущность изобретения поясняется фиг.3, на которой приведен график зависимости вероятности безотказной работы (ВБР) от отношения толщины ЗКС к наружному диаметру заряда. Указанный график построен на базе данных, полученных в результате многочисленных экспериментальных исследований.
Указанный положительный эффект подтвержден испытаниями изделий, изготовленных в соответствии с предлагаемым изобретением.
Таким образом, все перечисленные конструктивные особенности заявляемой конструкции заряда ракетного твердого топлива и примененные в нем новые, современные композиционные материалы позволяют обеспечить его высокую надежность, расширить диапазон его применения, включая наряду с металлическими корпусами и корпуса на основе композиционных материалов, а также повысить технологичность процесса изготовления зарядов при снижении загрязнения окружающей среды при производстве.
В настоящее время разработана конструкторская документация и начато изготовление зарядов.
Таблица Сравнительные свойства предлагаемого ЗКС и прототипа |
Параметр |
Прототип |
Предлагаемый состав ЗКС |
Пример 1 |
Пример 2 |
Пример 3 |
Компонентный состав, мас.ч. |
|
|
|
|
цис-Бутадиеновый каучук |
– |
50 |
60 |
65 |
цис-Изопреновый каучук |
– |
50 |
40 |
35 |
Технический углерод |
|
|
|
|
(смесь марок ПМ-75 и ТГ-18) |
– |
78 |
85 |
100 |
ДОС |
– |
10 |
15 |
20 |
Сера |
– |
1.0 |
2.0 |
3.0 |
Окись цинка |
– |
3.0 |
5.0 |
8.0 |
Неозон Д |
1.0-1.5 |
0.8 |
1.0 |
1.5 |
Альтакс |
– |
1.0 |
1.8 |
3.0 |
Рубракс |
– |
4.0 |
5.0 |
6.0 |
Полидиенуретанэпоксидный |
|
|
|
|
Каучук |
100 |
|
|
|
Технический углерод марки П-803 |
|
|
|
|
15-30 |
|
|
|
Малеиновый ангидрид |
1-3 |
|
|
|
Изометилтетрагидрофталиевый ангидрид |
1-3 |
|
|
|
Глицидол |
0.75-1.5 |
|
|
|
Свойства: |
|
|
|
|
Прочность при разрыве при температуре (23±2)°С, МПа |
|
|
|
|
2.09-2.22 |
7.5-14.0 |
7.5-15.0 |
7.5-15.0 |
Относительное удлинение при разрыве при температуре (23±2)°С, % |
|
|
|
|
246-267 |
250-360 |
250-400 |
250-400 |
Температура стеклования, °С |
ниже минус 70 |
минус 74 |
минус 77 |
минус 77 |
Температура хрупкости, °С |
ниже минус 70 |
ниже минус 75 |
ниже минус 75 |
ниже минус 75 |
Прочность адгезионного соединения ЗКС-топливо, МПа при температуре испытания, °С |
|
|
|
|
50 |
0.3-0.5 |
0.57-1.28 |
0.58-1.38 |
0.57-1.3 |
23±2 |
0.58-1.00 |
0.62-1.80 |
0.68-2.0 |
0.62-1.9 |
минус 50 |
1.5-1.8 |
3.2-5.71 |
3.4-6.08 |
3.7-5.9 |
Формула изобретения
Заряд ракетного твердого топлива, содержащий корпус, прочно скрепленный с ним топливный заряд и защитно-крепящий слой, отличающийся тем, что защитно-крепящий слой выполнен по всей поверхности заряда вплоть до канала с переменной толщиной 0.1·10-2-7.75·10-2 наружного диаметра заряда и представляет собой листовой каландрованный материал на основе цис-бутадиенового и цис-изопренового каучуков с наполнителем из технического углерода в количестве 78-100 мас.ч., в который введены ди-(2-этилгексил) себацинат в количестве 10-20 мас.ч. и дополнительно – сера 1-3 мас.ч., окись цинка 3-8 мас.ч., альтакс 1-3 мас.ч., рубракс 4-6 мас.ч., и выполняет роль теплозащиты крепящего слоя, торцевых эластичных вставок и манжет.
РИСУНКИ
|
|