|
(21), (22) Заявка: 2003127659/02, 11.09.2003
(24) Дата начала отсчета срока действия патента:
11.09.2003
(43) Дата публикации заявки: 10.04.2005
(45) Опубликовано: 10.11.2005
(56) Список документов, цитированных в отчете о поиске:
СТАЛЬ МАРКИ 20ХМ. МАРОЧНИК СТАЛЕЙ И СПЛАВОВ П/Р А.С.ЗУБЧЕНКО, М., МАШИНОСТРОЕНИЕ. 06.03.2003. С.240. SU 375997 A, 07.10.1981. SU 158296 A, 25.09.1963. CN 1405353 A, 26.03.2003.
Адрес для переписки:
398007, г.Липецк, пл. Заводская, 1, ОАО ЛМЗ “Свободный сокол”, Директору по новым технологиям И.Б. Лужанскому
|
(72) Автор(ы):
Лужанский И.Б. (RU)
(73) Патентообладатель(и):
Открытое акционерное общество Липецкий металлургический завод “Свободный сокол” (ОАО ЛМЗ “Свободный сокол”) (RU), Лужанский Илья Борисович (RU)
|
(54) СТАЛЬ ДЛЯ ИЗГОТОВЛЕНИЯ МЕТАЛЛОФОРМ
(57) Реферат:
Изобретение относится к разработке конструкционных теплоустойчивых сталей, которые могут быть использованы при изготовлении металлоформ для центробежного литья труб из высокопрочного чугуна. Сталь содержит компоненты в следующем соотношении, в мас.%: углерод 0,15 – 0,17; кремний 0,15 – 0,37; марганец 0,40 – 0,80; хром 2,10 – 2,50; никель 0,35 – 0,50; молибден 0,40 – 0,60; ванадий 0,17 – 0,20; алюминий 0,025 – 0,040; сера не более 0,025; фосфор не более 0,025; медь не более 0,25; железо – остальное. При этом отношение содержания хрома к содержанию углероду составляет 14,0 – 14,7, а отношение содержания ванадия к содержанию углерода составляет 1,0 – 1,33. Кроме того, отношение суммы легирующих элементов ферритизаторов к сумме легирующих элементов аустенизаторов определяется следующим соотношением: Техническим результатом изобретения является повышение эксплуатационных характеристик металлоформ путем повышения прочности, теплостойкости и ударной вязкости стали. 1 з.п. ф-лы, 10 табл.
Изобретение относится к области конструкционных сталей, в частности теплоустойчивых сталей для изготовления металлоформ центробежного литья груб из высокопрочного чугуна.
Металлоформы работают в тяжелых температурно-деформационных условиях. В то время как во внутреннюю полость формы заливают жидкий чугун при температуре 1260-1320°С, наружную ее поверхность охлаждают водой, циркулирующей в системе охлаждения. Такой перепад температур приводит к образованию значительных термических напряжений. Затем следует очередная заливка и следующий тепловой удар. После 500-800 заливок металлоформы выходят из строя по причине образования трещин (исчерпание ресурса пластичности) и сетки разгара (характеристики жаропрочности и жаростойкости).
Кроме того, работоспособность металлоформ обусловлена:
– температурой отпуска, которая должна быть выше 560°C – максимальной температуры разогрева внутренней стенки металлоформы,
– содержание углерода в стали не должно превышать 0,17% для обеспечения хорошей свариваемости: отсутствие трещин при ремонте металлоформ наплавкой,
– в целях экономии затрат на закалку и обеспечения противопожарных требований, сталь должна закаливаться в воде,
– как показали наши исследования, прочность стали для изготовления металлоформ должна быть не ниже 800 МПа, а текучесть 0.2 максимально приближена к значению в, что обеспечивает конструкционную прочность и релаксацию температурно-деформационных напряжений.
Для изготовления металлоформ в мировой практике в основном применяют хромомолибденовые стали. В качестве прототипа нами выбрана сталь 20ХМ по ГОСТ4543-71 «Сталь легированная конструкционная. Технические условия».
Известная сталь 20ХМ (Марочник сталей и сплавов п/р А.С.Зубченко, М., Машиностроение, 2003, стр.240) содержит элементы, мас.%:
Углерод |
0,15-0,25 |
Кремний |
0,17-0,37 |
Марганец |
0,40-0,70 |
Хром |
0,80-1,10 |
Никель |
не более 0,30 |
Молибден |
0,15-0,25 |
Сера |
не более 0,035 |
Фосфор |
не более 0,035 |
Медь |
не более 0,30 |
Механические свойства при 20°С после термообработки по режиму: закалка 880°С, масло и отпуск 500°С, воздух (сечение до 80 мм): 0.2 590 МПа, в 780 МПа,  12%,  50%, KCU 88 Дж/см2, НВ 179.
Однако эта сталь неоптимальна для изготовления металлоформ по причине:
– низкой теплостойкости: снижение прочности до 520 МПа уже при 550°С,
– недостаточной жаростойкости: 0,07 мм/год при 600°С и 0,11 мм/год при 700°С,
– низкой стабильности свойств при закалке в воде.
Цель и задачи изобретения – устранение недостатков стали 20ХМ.
Для повышения прочности и теплостойкости стали увеличено содержание хрома (до 2,1-2,5%) и дополнительно введен ванадий (до 0,17-0,20%).
Для достижения требуемых эксплуатационных характеристик суть важно соотношение хрома и углерода, образующих высокотемпературные карбиды Cr7С3 и Cr23С6, обеспечивающие высокую теплостойкость стали, таблицы 1 и 2.
Эффект повышения прочностных характеристик и их стабильности при температурах эксплуатации металлоформ (до 560°С) увеличивается при дополнительном легировании стали 20ХМ – прототип ванадием (0,17-0,20%).
При этом важно соблюдать соотношение ванадия и углерода (таблица 3), обеспечивающих образование специальных теплостойких карбидов.
Легирование стали никелем (0,35-0,50%) стабилизирует уровень механических характеристик (особенно, ударной вязкости при определении на образцах тип 11), повышает жаропрочность и жаростойкость стали – таблицы 4-6.
Для обеспечения возможности закалки стали в воде: существенное сокращение затрат на закалочную среду и обеспечение противопожарных требований, сталь дополнительно легирована экспериментально установленным количеством алюминия (0,025-0,040%).
Легирование стали 17Х2НМФ алюминием (0,025-0,040%) и термическая обработка по разработанному нами режиму: закалка 910°С, 1,5 ч, вода, отпуск 610°С, 2 ч – стабильно обеспечивают существенное превышение заданного (на основе анализа технической и патентной литературы) уровня механических характеристик: в 800 МПа, 0.2 600 МПа, 1 100 кДж/м2 и, как следствие, высокий ресурс металлоформ (таблица 7). Сталь 20ХМ на заданные параметры стабильно закаливается только в масле. Достигнутая за счет выбора системы и уровня легирования возможность проведения высокотемпературного отпуска обеспечивает стабильность свойств при эксплуатации металлоформ до 580°С (температура отпуска стали 20ХМ – прототипа – 500°С, что предопределяет низкую ее теплостойкость).
Таблица 8 иллюстрирует влияние содержания молибдена на механические характеристики при Т=500°С и ресурс стали 17Х2НМФЮ. Сталь сохраняет высокий уровень прочностных характеристик, в то время как у прототипа (композиция Cr-Мо) служебные характеристики при высоких температурах существенно снижаются.
Свариваемость (технологичность при ремонте металлоформ наплавкой) стали в первую очередь определяется содержанием углерода. Ограничение верхнего уровня содержания С 0,17% позволяет уменьшить протяженность зоны термического влияния и ее твердость, тем самым предупреждая образование трещин в наплавленном металле и металлоформе (таблица 9).
Безусловно, важную роль играет теоретически обоснованная и экспериментально подобранная композиция других легирующих элементов.
Попытка снижения содержания углерода в стали 20ХМ – прототип приводит к падению прочностных характеристик ( в. до 520 МПа и 0.2 до 380 МПа) и как следствие, уменьшению ресурса металлоформ – до 600 отлитых труб.
Необходимое условие достижения сталью 17Х2НМФЮ максимального уровня эксплуатационных характеристик – контроль отношения суммы феррити-заторов (эквивалент Cr) к сумме аустенизаторов (эквивалент Ni).
Оптимальное соотношение суммы этих элементов предопределяет структуру стали 17Х2НМФЮ как в литом (или кованом) состоянии, так и (особенно) после термической обработки.
Структура (оптимум – бейнит + мартенсит) определяет механические свойства и ресурс металлоформ (таблица 10). Наличие в структуре феррита снижает эксплуатационную надежность металлоформ.
Влияние содержания хрома, углерода и их соотношения на механические свойства и ресурс стали 17Х2НМФЮ
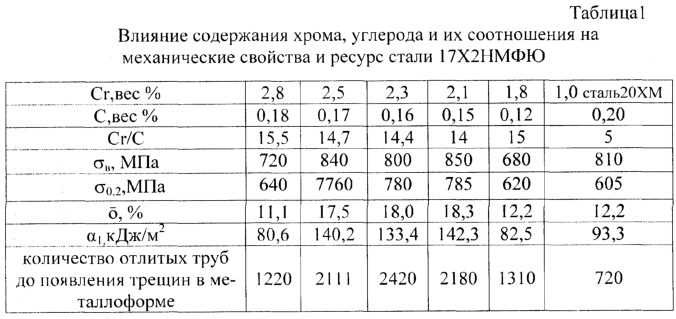
Кроме того, отношение предопределяет склонность стали к образованию горячих трещин. Особенно при восстановлении наплавкой размеров раструба металлоформы.
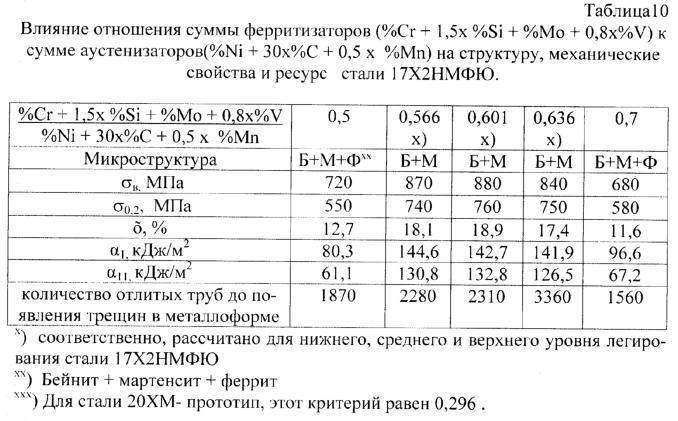
Технический результат изобретения – повышение эксплуатационных характеристик металлоформ путем повышения прочности, теплостойкости, жаростойкости и технологичности при закалке в воде разработанной стали 17Х2НМФЮ.
Формула изобретения
1. Сталь для изготовления металлоформ для центробежного литья, содержащая углерод, кремний, марганец, хром, никель, молибден, серу, фосфор, медь и железо, отличающаяся тем, что она дополнительно содержит ванадий и алюминий при следующем содержании компонентов, мас.%:
Углерод |
0,15 – 0,17 |
Кремний |
0,15 – 0,37 |
Марганец |
0,40 – 0,80 |
Хром |
2,10 – 2,50 |
Никель |
0,35 – 0,50 |
Молибден |
0,40 – 0,60 |
Ванадий |
0,17 – 0,20 |
Алюминий |
0,025 – 0,040 |
Сера |
Не более 0,025 |
Фосфор |
Не более 0,025 |
Медь |
Не более 0,25 |
Железо |
Остальное |
при этом отношение содержания хрома к содержанию углерода составляет 14,0 – 14,7, а отношение содержания ванадия к содержанию углерода составляет 1,0 – 1,33.
2. Сталь по п. 1, отличающаяся тем, что отношение суммы легирующих элементов ферритизаторов к сумме легирующих элементов аустенизаторов определяется следующим соотношением:

MM4A – Досрочное прекращение действия патента СССР или патента Российской Федерации на изобретение из-за неуплаты в установленный срок пошлины за поддержание патента в силе
Дата прекращения действия патента: 12.09.2006
Извещение опубликовано: 20.08.2007 БИ: 23/2007
|
|