|
(21), (22) Заявка: 2003133309/02, 14.11.2003
(24) Дата начала отсчета срока действия патента:
14.11.2003
(45) Опубликовано: 10.08.2005
(56) Список документов, цитированных в отчете о поиске:
АНДРЕЕВА А.Г. и др. “Финишная антифрикционная безобразивная обработка как средство повышения срока службы машин и оборудования”, Долговечность трущихся деталей машин: Сборник научн.статей, Вып.№ 4, под редак. Д.Н.Гаркунова, М., Машиностроение, 1990, с.34-59. SU 852518 А, 07.08.1981. RU 2060300 C1, 20.05.1996. RU 2209852 С1, 10.08.2003.
Адрес для переписки:
427430, Удмуртия, г. Воткинск, ул. Кирова, 2, ФГУП “Воткинский завод”, отдел 126
|
(72) Автор(ы):
Исупов М.Г. (RU)
(73) Патентообладатель(и):
Федеральное Государственное Унитарное Предприятие “Воткинский завод” (RU)
|
(54) СПОСОБ ФРИКЦИОННОГО ЛАТУНИРОВАНИЯ ПОВЕРХНОСТЕЙ ТРЕНИЯ
(57) Реферат:
Изобретение относится к технологии финишной обработки прецизионных пар трения, преимущественно тел вращения, требующих высокого качества обработки и точных размеров, например, проходных пробок-калибров для измерения точных отверстий, плунжеров топливной аппаратуры, игл распылителей форсунок дизельных двигателей и аналогичных деталей. Способ включает операции обезжиривания, нанесения технологической жидкости и фрикционного латунирования. Перед фрикционным латунированием производят струйно-абразивную обработку поверхностей трения с суммарным расходом абразива на единицу поверхности обрабатываемой детали 0,06…0,07 г/мм2. В результате гарантировано получение медесодержащей пленки на поверхностях трения при Ra 0,04 мкм. 2 ил. 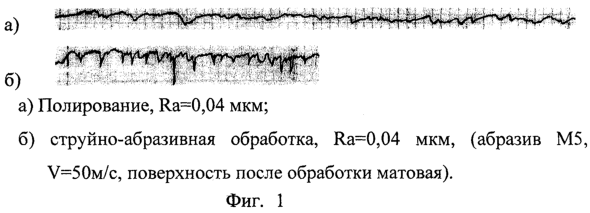
(56) (продолжение):
CLASS=”b560m”WO 0202844 A, 10.01.2002. JP 2000178595 A, 27.06.2000.
Изобретение относится к технологии финишной обработки прецизионных пар трения, преимущественно тел вращения, требующих высокого качества обработки и точных размеров, например, проходных пробок-калибров для измерения точных отверстий (допуск несколько микрометров), плунжеров топливной аппаратуры, игл распылителей форсунок дизельных двигателей, ходовых винтов металлообрабатывающих станков, например гаммы фрезерных станков ВМ 133, задвижек, для нефтяной и газовой промышленности.
Известен способ абразивной обработки поверхностей деталей [1], включающий подачу на поверхность детали абразива с размерами абразивных частиц 0,5 и 10 мкм и скоростью 30 м/с.
Недостатком аналога является то, что вопросы сохранения исходной шероховатости поверхности детали и исходного размера в нем не ставятся и не решаются. В приведенном примере №1 аналога (удаление старого ЛКП – эпоксидной эмали ЭП-140 со съемной детали планера самолета) указано, что исходная толщина анодной пленки (30 мкм) уменьшилась на 5 мкм. Последнее обстоятельство – уменьшение размеров обрабатываемой детали при струйно-абразивной обработке – совершенно неприемлемо для деталей прецизионных пар трения, поскольку, например, радиальный рабочий зазор распылителя форсунки дизельного двигателя КаМАЗ должен быть равен 2 мкм, а при зазоре 4 мкм эксплуатационные характеристики распылителя существенно ухудшаются.
В качестве прототипа взят способ фрикционного латунирования [2], включающий в себя операции струйно-абразивной обработки поверхности трения абразивом, последующего обезжиривания, нанесения покрытия. Недостатком является то, что его осуществление возможно при Ra>0,04 мкм. Эксперименты, проведенные автором, показали, что, начиная с Ra<0,1 мкм, процесс фрикционного латунирования становится неустойчивым вследствие того, что вершины микронеровностей слишком сглажены и латуни не за что “зацепиться”. На латунируемой детали появляются участки, где латуни нет, толщина пленки латуни становится переменной. Увеличение удельного давления латунного прутка сверх величин давления, указанного в аналоге, приводит к замене диффузионного процесса втирания латуни в стальную поверхность к ее намазыванию на поверхность трения. Разнотолщинность покрытия латуни увеличивается, а ее адгезия к металлу поверхности трения уменьшается.
Технической задачей, стоящей перед автором, является обеспечение возможности гарантированного получения медесодержащей пленки на поверхностях трения при Ra 0,04 мкм.
Технический результат достигается тем, что в известном способе, включающем в себя операции их обезжиривания, нанесения технологической жидкости и операции фрикционного латунирования, перед фрикционным латунированием производят их струйно-абразивную обработку с суммарным расходом абразива на единицу поверхности обрабатываемой детали 0,06…0,07 г/мм2.
На фиг.1 представлены профилограммы поверхностей, полученных разными видами обработки. На фиг.2 – экспериментальные данные по изменению размера деталей вследствие наплыва металла по краям лунок, образующихся при ударе абразивных зерен об обрабатываемую поверхность (поверхность трения).
1 – абразив зернистостью М5 (размеры зерна 3…5 мкм)
2 – абразив зернистостью М40 (размеры абразива 28…40 мкм).
Поверхность, подлежащую латунированию, подвергают обезжириванию, например, бензином. Затем на нее наносится технологическая жидкость и далее осуществляется собственно процесс фрикционного латунирования, режимы которого приведены в аналоге [2]. При натирании поверхности трения латунью (бронзой) происходит процесс микрорезания, частицы латуни втираются в поверхность трения. Толщина образовавшейся пленки латуни не превышает 0,5 мкм.
Предлагаемый способ был использован для фрикционного латунирования рабочих поверхностей проходных калибров-пробок. Шероховатость поверхности рабочей части калибра равна Ra=0,01…0,02 мкм. Устойчивая пленка латуни образовывалась после 3 проходов латунным прутком Л62 по поверхности детали. Фрикционное латунирование производилось на приспособлении, схема которого приведена в аналоге. Деталь (пробка-калибр) закрепляется в патроне токарного станка, приспособление – в его суппорте. Струйно-абразивная обработка поверхностей трения перед фрикционным латунированием проводилась на специальном стенде, основой которого являлось пневматическое сопло с подачей в него абразива М5, деталь (пробка-калибр) вращалась с помощью электромотора постоянного тока. Обработка проводилась до тех пор, пока рабочая поверхность калибра-пробки не становилась визуально однородно матовой. Контрольные записи профилограмм поверхности до и после струйно-абразивной обработки позволили подобрать режимы струйно-абразивной обработки, не изменяющие среднюю высоту шероховатости и диаметр детали. Эти режимы следующие: скорость удара частиц 30…50 м/с, угол между осями сопла и детали равен 90°, суммарный расход абразива, приходящегося на 1 мм2 обрабатываемой детали 0,06…0,07 г/мм2.
Скорость удара частиц в диапазоне 30…50 м/с выбрана из следующих соображений. Экспериментальные исследования автора показали, что при скорости удара меньше 25 м/с абразив М5 не оказывает заметного влияния на поверхность из закаленных сталей (HRC60) за приемлемое, с точки зрения организации технологического процесса, время обработки. При скорости удара частиц абразива больше 50 м/с шероховатость поверхности возрастает. Скорость удара частиц принималась равной скорости воздуха в зоне контакта его с обрабатываемой поверхностью. Последнее допущение правомерно, так как при малых размерах частиц абразива ( =1…5 мкм) скорость частиц близка к скорости воздуха. Скорость воздуха измерялась трубкой полного напора (трубкой Пито), одновременно измерялся расход воздуха с помощью ротаметров марки РС-5.
На фиг.2. показано изменение размеров детали при струйно-абразивной обработке в зависимости от суммарного расхода абразива, приходящегося на 1 мм2 обрабатываемой детали для двух абразивов: М5 и М40. Измерения размера детали (иглы распылителей форсунки) производилось пружинной измерительной головкой типа 01 ИГПВ с ценой деления 0,1 мкм, ГОСТ 6933-81. В начальный момент обработки размер увеличивался за счет наплыва металла по краям лунок, образующихся при ударе абразивных зерен об обрабатываемую поверхность. Далее, по мере увеличения суммарного объема абразива, приходящегося на 1 мм2 обработки, размер детали уменьшался и для абразива М5 в диапазоне расходов абразива G=0,06…0,07 г/мм2 размер детали становился равным исходному и при дальнейшей обработке уменьшался. Время обработки определяется расходом абразива. Высота шероховатости при этом остается неизменной. С увеличением размера зерна абразива высота наплывов металла по краям лунок увеличивается, размер детали возрастает больше, а затем уменьшается. Суммарный расход абразива, при котором размер детали возвращается к исходному, также возрастает. В качестве примера, на фиг.2. приведена кривая 2 для абразива М40. При суммарном расходе абразива G=0,1 г/мм2 размер детали возвращается к исходному, который был перед струйно-абразивной обработкой.
Долговечность калибров после фрикционного латунирования по предлагаемому способу увеличивается в 1,3…1,5 раза.
Таким образом, новая совокупность существенных признаков, а именно введение операции струйно-абразивной обработки на режимах с суммарным расходом абразива М5 на единицу поверхности обрабатываемой детали 0,06…0,07 г/мм2, позволяет создать требуемый микрорельеф без изменения размеров обрабатываемой детали.
Источники информации
Формула изобретения
Способ фрикционного латунирования поверхности трения, включающий в себя операции струйно-абразивной обработки поверхности трения абразивом, последующего обезжиривания, нанесения технологической жидкости и операции фрикционного латунирования, отличающийся тем, что суммарный расход абразива на единицу поверхности обрабатываемой детали при струйно-абразивной обработке составляет 0,06 – 0,07 г/мм2.
РИСУНКИ
MM4A Досрочное прекращение действия патента Российской Федерации на изобретение из-за неуплаты в установленный срок пошлины за поддержание патента в силе
Дата прекращения действия патента: 15.11.2005
Извещение опубликовано: 27.01.2007 БИ: 03/2007
|
|