|
(21), (22) Заявка: 2004126113/15, 30.08.2004
(24) Дата начала отсчета срока действия патента:
30.08.2004
(45) Опубликовано: 27.07.2005
(56) Список документов, цитированных в отчете о поиске:
RU 2051094 C1, 27.12.1995. RU 2090500 C1, 20.09.1997. RU 2154605 C1, 20.08.2000. RU 2023966 С1, 30.11.1994.
Адрес для переписки:
119991, Москва, Ленинский пр-кт, 29, Институт горючих ископаемых, Д.т.н. М.А. Передерий
|
(72) Автор(ы):
Передерий М.А. (RU), Двоскин Г.И. (RU), Старостин А.Д. (RU)
(73) Патентообладатель(и):
Передерий Маргарита Алексеевна (RU), Двоскин Григорий Исакович (RU), Старостин Алексей Дмитриевич (RU)
|
(54) СПОСОБ ПОЛУЧЕНИЯ АКТИВНОГО УГЛЯ
(57) Реферат:
Способ относится к области термической переработки твердых углеродсодержащих материалов с целью получения активных углей. Способ включает процесс нагрева и карбонизации сырья в горизонтальной вращающейся печи в непрерывном режиме в течение 1,0-3,0-х часов при температуре 650-850°С со скоростью нагрева материала до конечной температуры не более 10°С в минуту, подачу образовавшегося карбонизата без охлаждения в виде порций в вертикальную печь активации, активацию каждой порции в течение <30 минут, при температуре 750-950°С в режиме слоя, взвешенного “острой” струей газообразного активирующего агента, подачу новой порции карбонизата в печь активации после выгрузки из нее порции готового продукта, подачу парогазовой смеси из печи активации в печь карбонизации в режиме противотока движению карбонизуемого материала, направление парогазовой смеси из печи карбонизации на дожигание в котел-утилизатор, получение в нем необходимого для приготовления активирующего агента водяного пара низкого давления, обезвреживание образующихся в котле-утилизаторе дымовых газов. Изобретение позволяет обеспечить интенсификацию процесса теплообмена и улучшение качества активного угля, а также улучшение экономических показателей за счет экономии топлива и сокращения времени технологического процесса. 4 з.п. ф-лы, 1 ил., 2 табл.
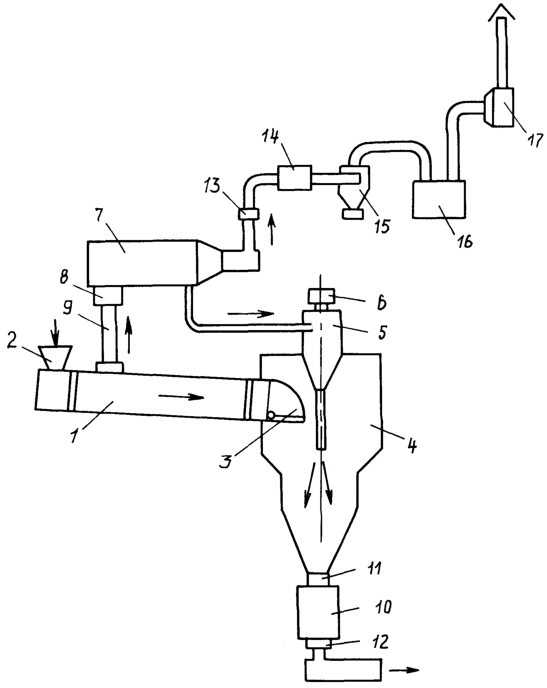
Настоящее изобретение относится к области производства активных углей из углеродсодержащего сырья.
Известен способ получения активного угля (АУ) путем карбонизации и активации углеродсодержащего материала, проводимых в вертикальном аппарате, разделенном на соответствующие камеры горизонтальными газораспределительными решетками, причем карбонизация происходит в две стадии при 400-500°С и 750-850°С соответственно, а активация – при 850-950°С, при этом из камер карбонизации и активации производят частичный отбор газов на рециркуляцию и дожигание (SU 46777761, 25.04.1975).
Известен также способ, согласно которому углеродсодержащее сырье, например бурый уголь, дробят до класса 2-10 мм, карбонизуют во вращающейся печи с внешним обогревом в среде выделяющихся собственных летучих при температуре 520±20°С со скоростью нагрева 20-30 град/мин и выдержкой при конечной температуре 20-25 минут. Активацию карбонизованного угля проводят во вращающейся барабанной печи с электрообогревом при температуре 830±20°С до обгара 50%. Выход на стадии карбонизации равен 40%, на стадии активации – 45%, общий выход – 18%. В результате получают активный уголь, имеющий адсорбционную способность по йоду 74%, механическую прочность 71% (RU 2090500, 20.09.1997).
Недостатками известного способа являются: высокая скорость нагрева обрабатываемого материала, вследствие чего получаемый АУ имеет низкую механическую прочность; технологическая сложность осуществления изотермической выдержки в процессе карбонизации во вращающейся печи, что приводит к нестабильности качества продукта.
Известен способ получения АУ, при котором карбонизацию высушенного исходного материала проводят топочными газами во вращающейся печи при температуре 550-600°С. Карбонизированный материал охлаждают и далее активируют во вращающейся печи активации парогазовой смесью при температуре 850-980°С в течение 4-6 ч (ТР 6-16-14-58-81. Производство активных гранулированных углей. Пермь: ПХМЗ, 1981. 179 с.).
Недостатками способа являются: необходимость затраты дополнительной тепловой энергии на повторный нагрев карбонизата до температуры активации; большая продолжительность процесса активации вследствие низкой эффективности тепло-, массообменных процессов, что обусловлено конструктивными особенностями горизонтальной вращающейся печи активации, обеспечивающей “квазистационарный” режим взаимодействия парогазовой смеси со слоем активируемых частиц материала.
Известен также способ получения АУ путем карбонизации и активации сырья без промежуточного охлаждения с использованием горизонтальных вращающихся муфельных печей карбонизации и активации, при этом карбонизацию осуществляют в течение 2-2,5 ч топочными газами с температурой на входе 600-700°С, а активацию проводят в течение 4-5 ч при температуре 780-860°С за счет обогрева продуктами сгорания природных газов (Мухин В.М., Тарасов В.Н., Клушин А.В. Активные угли России. М.: Металлургия, 2000, стр.36).
Недостатком способа является высокая продолжительность и, следовательно, низкая производительность процесса, а также его высокая энергозатратность, вследствие того что для обогрева печей сжигается природный газ.
Кроме того, “квазистационарный” режим взаимодействия газовой и твердой фаз в горизонтальных печах карбонизации и активации не способен обеспечить одинаковые условия обработки всех частиц обрабатываемого материала, возможно получение только усредненного результата, что обусловливает неоднородность качества получаемого продукта.
Наиболее близким к предлагаемому является способ получения активного угля, включающий пневмосепарацию и одновременно сушку частиц исходного материала в слое, взвешенном “острой” струей газообразных продуктов карбонизации, карбонизацию высушенного материала “острой” струей газообразных продуктов активации и далее активацию карбонизованного материала “острой” струей водяного пара; при этом на стадии карбонизации, проводимой в вертикальной печи, сырье нагревают до 550-600°С и без охлаждения подают на активацию, проводимую в вертикальной печи при 750-800°С. Способ предусматривает дожигание газообразных продуктов карбонизации и использование для нагрева сырья парогазовой смеси, подаваемой противотоком со стадии активации (RU 2051094, 27.12.1995).
Недостатком способа является то, что сушка и карбонизация в режиме слоя, взвешенного “острой” струей газообразных продуктов, протекает при высокоскоростном нагреве частиц исходного материала, что происходит к интенсивному одновременному выделению большого объема влаги и летучих продуктов из обрабатываемой частицы, сопровождаемому ее растрескиванием, разрушением структуры пор, что предопределяет низкую прочность конечного продукта – активного угля.
Задачей изобретения является получение прочного, высокопористого активного угля путем обеспечения наиболее благоприятных условий для проведения каждой из стадий технологического процесса, а также достижение экономического эффекта за счет уменьшения продолжительности процесса и сокращения затрат тепла на его проведение.
Поставленная задача решается описываемым способом получения активного угля, который включает нагрев углеродсодержащего сырья в атмосфере парогазовой смеси, подаваемой со стадии активации в режиме противотока, карбонизацию, дожигание газообразных продуктов карбонизации, подачу карбонизата без охлаждения в вертикальную печь на активацию, активацию в режиме взвешенного слоя с помощью острой струи газообразного активирующего агента и выгрузку активного угля, при этом нагрев углеродсодержащего сырья проводят при скорости подъема температуры не более 10°С в минуту до температуры карбонизации, равной 650-850°С, нагрев и карбонизацию осуществляют в горизонтальной вращающейся печи карбонизации в непрерывном режиме, подачу карбонизата в печь активации производят порционно после выгрузки из нее предыдущей партии активированного угля и активацию проводят при 750-950°С не более 30 минут.
Предпочтительно нагрев сырья и его карбонизацию осуществляют в течение 1-3 часов.
Способ предусматривает, что дожигание газообразных продуктов карбонизации осуществляется в котле-утилизаторе с получением водяного пара низкого давления, используемого для приготовления активирующего агента, а образующиеся при дожигании дымовые газы подвергают каталитической очистке и пылеулавливанию.
Способ предусматривает возможность проведения технологическиго цикла под разряжением, создаваемым дымососом, предназначенным для удаления отходящих газообразных продуктов процесса.
Обеспечение получения высокого техническиго результата обусловлено следующим:
1. Карбонизация в горизонтальной муфельной вращающейся печи в непрерывном режиме в течение 1,0-3,0 ч при температуре 650-850°С со скоростью нагрева материала до конечной температуры <10°С/мин обеспечивает спокойное выгазовывание летучих продуктов из обрабатываемого материала. Нагрев материала в печи карбонизации парогазовой смесью, поступающей из печи активации в режиме противотока, обеспечивает позонный нагрев частиц от низкой до заданной температуры, благодаря чему материал прогревается и обезлетучивается постепенно. Все это предотвращает растрескивание карбонизируемого материала, разрушение его пористой структуры и потерю прочности карбонизата (табл.1).
2. Подача карбонизата в печь активации без охлаждения позволяет избежать затрат топлива на его повторный нагрев до температуры активации.
3. Подача карбонизата в печь активации в виде порций и активация порции в течение 30 минут при температуре 750-950°С в режиме слоя, взвешенного острой струей газообразного активирующего агента, характеризующегося высокой эффективностью тепло-, массообменных процессов, обеспечивает: а) хороший доступ активирующего агента к каждой частице активируемого материала и получение однородного по качеству активного угля; б) резкое сокращение времени, необходимого для получения активных углей требуемого качества (табл.2).
4. Выгрузка активного угля из печи активации перед подачей в него очередной порции карбонизата делает невозможным контакт и смешивание этих материалов, что обеспечивает требуемое качество конечной продукции.
5. Направление горючей парогазовой смеси из печи карбонизации на дожигание в котел-утилизатор обеспечивает получение тепла, необходимого для проведения процессов сушки и для получения водяного пара низкого давления, необходимого для приготовления активирующего агента.
Обезвреживание образующихся в котле-утилизаторе дымовых газов в каталитическом дожигателе и их комплексная “сухая” и “мокрая” пылеочистка обеспечивают их экологическую безопасность.
Ведение всего технологического процесса под разрежением, создаваемым дымососом, расположенным в конце технологической цепочки, обеспечивает увеличение глубины термических превращений при пиролизе исходного материала, а также исключает возможность попадания газообразных продуктов пиролиза и активации в окружающую среду.
Ниже приведены примеры, подтверждающие возможность проведения способа с получением эффекта, и сравнительные примеры.
Способ в объеме заявленной совокупности признаков был осуществлен на установке, схема которой приведена на чертеже.
Установка для получения активного угля содержит горизонтальную печь карбонизации /1/ с узлом ввода сухого материала /2/ и дозирующим устройством /3/, вертикальную печь активации /4/ с камерой сгорания /5/ и горелочным устройством /6/, котел-утилизатор /7/, снабженный горелкой /8/, контуром /9/ для парогазовой смеси, охладитель готового продукта /10/ с узлом загрузки /11/ и вызрузки /12/, каталитический дожигатель /13/, теплообменник /14/, циклон /15/, скруббер /16/ и дымосос /17/.
Установка работает следующим образом. Запускают горелки 6 и 8 и прогревают установку до рабочей температуры. Предварительно подготовленное (дробление, рассев и др.) высушенное исходное сырье загружают в торцевую “холодную” часть карбонизатора через узел ввода 2. Материал, благодаря вращению и некоторому наклону печи в сторону выгрузки, медленно перемещается по длине печи, прогреваясь по мере продвижения из менее нагретой в более нагретые зоны. Первоначально сырье подвергается дополнительной сушке, затем, по мере прогревания – карбонизации с выделением газообразных продуктов термического разложения, которые вместе с парами воды отводятся через канал 9 и поступают во внешний контур горелки 8, конструкция которой обеспечивает сжигание низкокалорийных газов за счет их предварительного смешения с горячим окислителем. Горючие компоненты отходящих газов сжигают совместно с топливом, подаваемым в горелку для поддержания процесса.
Образующийся при карбонизации обрабатываемого углеродсодержащего материала карбонизат непрерывно поступает в дозирующее устройство (например, поворотный лоток), где он накапливается в виде порции определенной массы, при достижении которой дозирующим устройством направляется во внутренний объем печи 4.
В размещенную на крышке камеры активации камеру сгорания 5 поступают дымовые газы – газообразные продукты сгорания топлива, сжигаемого в горелочном устройстве. Одновременно в поток дымовых газов подается водяной пар, количеством которого регулируется температура образующейся парогазовой смеси. Смесь водяного пара с дымовыми газами является активирующим агентом.
Подача активирующего агента на поверхность полукокса в виде “острой струи” обеспечивает его перевод в состояние взвешенного слоя, что создает условия для интенсивного тепло- и массопереноса. Карбонизат быстро прогревается до требуемой температуры, углерод карбонизата вступает во взаимодействие с водяным паром и активируется в течение заданного времени без добавления свежего материала, с получением высокопористого активного угля. После завершения процесса активации порция АУ выводится из камеры активации в охладитель 10 через загрузочный узел 11 и после охлаждения выводится через узел выгрузки 12.
Газообразные продукты сгорания газов карбонизации (дымовые газы) из котла-утилизатора выводятся в каталитический дожигатель 13, где происходит полное окисление оставшейся в них органики. Далее дымовые газы охлаждаются в теплообменнике 14 и очищаются от несгоревшей угольной пыли в циклоне 15, окончательно охлаждаются в скруббере 16, отдавая тепло воде, идущей на приготовление пара, и через дымосос 17 выбрасываются в атмосферу.
Пример 1. Два образца одного и того же материала (антрацит) фракционного состава 1-3 мм (100%) подвергали карбонизации при 800°С: а) в вертикальной печи в слое, взвешенном “острой” струей газа, в течение 20 мин; б) в горизонтальной вращающейся печи в “квазистационарном” слое – со скоростью подъема температуры 10°С/мин в течение 90 мин. Для карбонизованных образцов определяли прочность, насыпную плотность, суммарный объем пор и содержание (%) исходной фракции 1-3 мм (табл.1).
Температурный контроль процессов позволил установить, что время нагрева материала до конечной температуры карбонизации в опыте “а” составляло ~8 мин, т.е. скорость подъема температуры – ~100°С/мин, остальные 12 мин образец обрабатывался в изотермическом режиме процесса карбонизации; время изотермической выдержки для опыта “б” составило 10 минут.
Пример 2. Опыт по примеру 1 с той разницей, что время изотермической выдержки увеличили по каждому из опытов до 15 мин.
Пример 3. Опыт по примеру 1 с той разницей, что изотермической выдержки не проводили (0 мин).
Таблица 1 |
Условия проведения карбонизации |
Время карбонизации, мин |
Выход фракции, % |
Насыпная пл., г/см3 |
Суммарн. Vпор, см3/г |
Прочность, % |
а). Изотерм. выдержка: |
|
|
|
|
|
пример 1 12 мин |
20 |
73 |
0.65 |
0.27 |
75 |
пример 2 30 мин |
38 |
69 |
0.67 |
0.25 |
76 |
пример 3 0 |
8 |
78 |
0.62 |
0.29 |
74 |
б) Изотерм, выдержка: |
|
|
|
|
|
пример 1 10 мин |
90 |
92 |
0.71 |
0.23 |
92 |
пример 2 30 мин |
110 |
89 |
0.72 |
0.22 |
93 |
пример 3 0 |
80 |
94 |
0.70 |
0.24 |
92 |
Из результатов таблицы следует, что для образца, карбонизируемого в горизонтальной вращающейся печи в условиях “квазистационарного” слоя (б) при скорости подъема температуры 10°С/мин, формирование структурных и прочностных характеристик полностью завершается за время нагревания до конечной температуры карбонизации (80 мин, пример 36). Благодаря “щадящему” режиму обработки не происходит измельчения материала (высокий выход исходной фракции 1-3 мм=94%), карбонизованный материал приобретает высокую прочность и насыпную плотность. Введение изотермической выдержки, т.е. дополнительной термообработки при конечной температуре карбонизации (примеры 1б, 2б), незначительно уменьшает содержание исходной фракции в карбонизате за счет истирания; прочность, насыпная плотность и суммарная пористость остаются стабильными (незначительное увеличение первых 2-х показателей и уменьшение 3-го за счет дополнительной усадки).
Иная картина наблюдается для продуктов карбонизации материала в слое, взвешенном “острой” струей газа, в вертикальной печи (а). Низкие показатели прочности, насыпной плотности и выхода исходной фракции характерны для карбонизата, полученного без изотермической выдержки (пример 3а); введение изотермической выдержки (примеры 1а, 2а), незначительно увеличивая первые два показателя, заметно снижает пористость за счет дополнительной усадки и выход целевой фракции за счет истирания продуктов карбонизации.
Результаты проведенного эксперимента наглядно подтверждают преимущества проведения процесса карбонизации в мягких условиях “квазистационарного” слоя, которые обеспечивает горизонтальная вращающаяся печь карбонизации.
Пример 4. Два образца карбонизата, полученного по примеру 3б, подвергали активации в “квазистационарном” (горизонтальная печь) и взвешенном (вертикальная печь) слоях материала при различной продолжительности процесса при температуре 800°С. В табл.2 представлены характеристики близких по качеству АУ, полученных при разном времени активации в условиях стационарного и взвешенного слоев материала.
Таблица 2 Условия активации и показатели качества АУ |
Условия |
, |
нас., |
П, |
Объемы пор, см3/г |
активации |
% |
г/см3 |
% |
V |
Ws |
Vма |
Стационарный слой: |
|
|
|
|
|
|
120 мин |
37.4 |
0.57 |
78.7 |
0.306 |
0.229 |
0.077 |
180 мин |
46.2 |
0.49 |
72.0 |
0.390 |
0.296 |
0.094 |
Взвешенный слой: |
|
|
|
|
|
|
15 мин |
35.2 |
0.59 |
81.0 |
0.285 |
0.235 |
0.050 |
30 мин |
44.0 |
0.51 |
75.6 |
0.427 |
0.315 |
0.112 |
Условные обозначения в табл.2: – обгар при активации; П – прочность на истирание; нас. – насыпная плотность.; V – суммарный объем пор; Ws – объем сорбирующих пор; Vма – объем макропор.
Как видно из полученных результатов таблицы, скорость активации карбонизата во взвешенном слое несравнимо выше скорости активации в стационарном слое. Для достижения показателей качества, сопоставимых с качеством сорбента 3-часовой активации карбонизата в стационарном слое, достаточно 30 мин его активации во взвешенном слое; 15 мин активации во взвешенном слое позволяют получать прочный сорбент с развитой структурой пор. Это объясняется лучшим контактом активирующего агента с частицей активируемого материала, что исключает внешний обгар материала с образованием макропор. Подтверждением этому могут служить меньшие объемы макропор у сорбентов, полученных активацией во взвешенном слое антрацита.
Таким образом, предложенный способ обеспечивает качественное приготовление карбонизата, интенсификацию процесса теплообмена и улучшение качества активного угля, а также улучшает экономические показатели за счет экономии топлива и сокращения времени.
Формула изобретения
1. Способ получения активного угля, включающий нагрев углеродсодержащего сырья в атмосфере парогазовой смеси, подаваемой со стадии активации в режиме противотока, карбонизацию, дожигание газообразных продуктов карбонизации, подачу карбонизата без охлаждения в вертикальную печь на активацию, активацию в режиме взвешенного слоя с помощью острой струи газообразного активирующего агента и выгрузку активного угля, отличающийся тем, что нагрев углеродсодержащего сырья проводят при скорости подъема температуры не более 10°С в минуту до температуры карбонизации 650-800°С, нагрев и карбонизацию осуществляют в горизонтальной вращающейся печи карбонизации в непрерывном режиме, подачу карбонизата в печь активации производят порционно после выгрузки из нее предыдущей партии активированного угля и активацию проводят при 750-950°С не более 30 мин.
2. Способ по п.1, отличающийся тем, что нагрев сырья и его карбонизацию осуществляют в течение 1-3 ч.
3. Способ по п.1, отличающийся тем, что дожигание газообразных продуктов карбонизации осуществляют в котле-утилизаторе с получением водяного пара низкого давления, используемого для приготовления активирующего агента.
4. Способ по п.1, отличающийся тем, что образующиеся при дожигании дымовые газы подвергают каталитической очистке и пылеулавливанию.
5. Способ по п.1, отличающийся тем, что технологический цикл осуществляют под разрежением, создаваемым дымососом, предназначенным для удаления отходящих газообразных продуктов процесса.
РИСУНКИ
MM4A – Досрочное прекращение действия патента СССР или патента Российской Федерации на изобретение из-за неуплаты в установленный срок пошлины за поддержание патента в силе
Дата прекращения действия патента: 31.08.2007
Извещение опубликовано: 10.03.2009 БИ: 07/2009
|
|