|
(21), (22) Заявка: 2004105625/02, 24.02.2004
(24) Дата начала отсчета срока действия патента:
24.02.2004
(45) Опубликовано: 10.07.2005
(56) Список документов, цитированных в отчете о поиске:
RU 2089652 C1, 10.09.1997. RU 2006518 C1, 30.01.1994. SU 1730194 A1, 30.04.1992. GB 1489618 А, 26.10.1977.
Адрес для переписки:
162600, Вологодская обл., г. Череповец, ул. Мира, 30, ОАО “Северсталь”, Начальнику управления качества А.М. Ламухину
|
(72) Автор(ы):
Кувшинников О.А. (RU), Голованов А.В. (RU), Краев А.Д. (RU), Титлянов А.Е. (RU), Радюк А.Г. (RU), Гейер В.В. (RU), Кузнецов А.А. (RU), Дубинин И.В. (RU)
(73) Патентообладатель(и):
Открытое акционерное общество “Северсталь” (ОАО “Северсталь”) (RU)
|
(54) СПОСОБ НАПЫЛЕНИЯ АЛЮМИНИЕВОГО ГАЗОТЕРМИЧЕСКОГО ПОКРЫТИЯ НА ЗАГОТОВКИ ДЛЯ НАГРЕВА ИХ ПОД ПРОКАТКУ
(57) Реферат:
Изобретение относится к области металлургии и может быть использовано при нагреве непрерывнолитых слябов из низколегированной стали под прокатку и последующей их прокатке. Предложенный способ напыления алюминиевого газотермического покрытия на прямоугольные стальные слябы для нагрева их под прокатку характеризуется тем, что покрытие напыляют на верхнюю широкую грань толщиной, определяемой из зависимости: где Нпв – толщина покрытия, наносимого на верхнюю широкую грань сляба, мм; Нc – толщина сляба, мм; а на нижнюю широкую грань сляба напыляют покрытие толщиной, определяемой из зависимости: где Нпн – толщина покрытия, наносимого на нижнюю широкую грань сляба, мм; R – радиус роликов транспортного рольганга, мм. Техническим результатом изобретения является снижение толщины дефектного слоя на широких гранях листа, особенно на его нижней грани, путем выбора рациональных значений толщины газотермического напыления на сляб. 2 табл.
Изобретение относится к области металлургии и может быть использовано при нагреве непрерывнолитых слябов из низколегированной стали под прокатку и последующей их прокатке. При получении листов из таких сталей на их поверхности образуется дефектный слой и листы приходится подвергать сплошной зачистке. Для снижения толщины данного слоя и уменьшения трудоемкости зачистки предлагается наносить алюминиевое газотермическое покрытие на слябы. Известен способ напыления алюминиевого газотермического покрытия (ГТП) на прямоугольные стальные заготовки для защиты их поверхности при нагреве под прокатку (Полухин В.П., Титлянов А.Е., Гриднев И.М. и др. Теория и технология деформации металлов. М.: Металлургия, 1982, МИСиС. Сб. №145. с.39-43). Однако в работе отсутствует связь между толщиной напыленного покрытия, толщиной заготовки и толщиной дефектного слоя на поверхности листов после прокатки.
Наиболее близким к предложенному способу является способ напыления алюминиевого ГТП на прямоугольные стальные заготовки для нагрева их под прокатку (патент №2089652, РФ, кл. С 23 С 4/00), в котором предлагается толщину напыленного ГТП определять из соотношения:

где Нп – толщина покрытия, наносимого на грани заготовки, мм;
Нз – толщина заготовки, мм;
– вытяжка заготовки при прокатке.
Предлагаемое соотношение для определения толщины ГТП, наносимого на продольные широкие грани сляба, дает заниженные значения толщины ГТП, не обеспечивающие защиту сляба при нагреве в печах. Например, при толщине сляба 200 мм, его нагреве под прокатку до температуры 1150… 1200° С и величине вытяжки при горячей прокатке. равной 8, толщина ГТП лежит в диапазоне 0,120… 0,168 мм, что не обеспечивает даже устранение сквозной пористости ГТП после напыления. При этом нельзя считать, как это сделано в данном соотношении, что исходная толщина ГТП, соответствующая минимальной толщине дефектного слоя на поверхности листа, зависит от вытяжки при прокатке листов. Это объясняется тем, что хотя толщина этого слоя зависит от вытяжки, но каждый из этих факторов действует независимо друг от друга. Кроме того, в известном решении не учитывается необходимость дифференцированного подхода к толщине покрытия, наносимого на верхнюю и нижнюю широкие грани заготовки, с целью уменьшения толщины дефектного слоя, остающегося в первую очередь на нижней широкой гране заготовки. Напыление алюминиевого ГТП по известным режимам приводит к тому, что в результате нагрева и последующей горячей прокатки листовых заготовок из некоторых марок стали на готовых листах остается дефектный слой, состоящий из интерметаллидов типа Fen Alm, который удаляют абразивной зачисткой широких граней листов. При этом толщина этого слоя на нижней широкой грани в 1,2… 2,0 раза превышает толщину этого слоя на верхней грани. Это объясняется тем, что при движении заготовки с напыленным покрытием по рольгангу происходит его уплотнение, что приводит при нагреве к образованию более толстого диффузионного слоя, состоящего из интерметаллидов типа Fen Alm.
Техническим результатом предлагаемого решения является снижение толщины дефектного слоя на широких гранях листа, особенно на его нижней грани, путем выбора рациональных значений толщины напыления ГТП на сляб.
Поставленная задача достигается тем, что в способе напыления алюминиевого ГТП на прямоугольные слябы для нагрева их под прокатку толщина алюминиевого ГТП, наносимого на верхнюю широкую грань сляба, определяется из зависимости:

где Нпв – толщина покрытия, наносимого на верхнюю грань сляба, мм;
НС – толщина сляба, мм.
Толщина алюминиевого ГТП, наносимого на нижнюю широкую грань сляба, определяется из неравенства:

где Нпн – толщина покрытия, наносимого на нижнюю широкую грань сляба, мм;
R – радиус роликов транспортного рольганга, мм.
Толщина покрытия, удовлетворяющая приведенным неравенствам, позволяет сформировать защитный слой, который обеспечивает при нагреве и последующей прокатке слябов получение листов с минимальным дефектным слоем на их поверхности, подлежащий удалению при зачистке. При этом покрытие, нанесенное на нижнюю широкую грань, подвергается уплотнению при транспортировке по рольгангу за счет воздействия собственного веса, и чем больше толщина сляба и меньше радиус ролика рольганга, тем больше давление, действующее со стороны ролика на покрытие. Уплотненное покрытие за счет уменьшения пористости является более эффективным, чем исходное покрытие после напыления.
Напыление алюминиевого ГТП на широкие грани с меньшими, чем по неравенствам (1) и (2), приводит к недостаточности защитных свойств образовавшихся при нагреве окисного и интерметаллидных слоев и образованию дефектного слоя повышенной толщины на листах после прокатки. Напыление алюминиевого ГТП толщиной большей, чем это следует из неравенств, приводит к тому, что в результате нагрева на напыленных гранях сляба образуется интерметаллидный слой повышенной толщины, что приводит к завышенной толщине дефектного слоя на листах.
Расчеты проводили для толщин слябов, равных 150… 300 мм, что соответствует толщинам слябов с УНРС, используемым для получения толстых листов. Зависимости для выбора толщины ГТП были получены на основании экспериментальных результатов. На широкие грани сляба из низколегированной стали различного сечения напыляли алюминиевое ГТП металлизатором ЭМ-14. Сляб нагревали в методической печи при температурах, изменяющихся по зонам в интервале 1000… 1240° С, и прокатывали на лист различной толщины. Чем толще слябы, тем больше время их нагрева под прокатку, тем толще напыляли покрытие перед нагревом под прокатку. Параметры эксперимента приведены в таблицах 1 и 2.
В результате обработки экспериментальных данных получили зависимости (1) и (2). Рассмотрим конкретно применение предлагаемого способа для выбора толщины покрытия, наносимого на непрерывнолитые слябы из низколегированной стали при их нагреве под прокатку, при получении толстого листа на стане 2800/1700 ОАО “Северсталь”.
Пример 1. Сляб из низколегированной стали сечением 200× 1300 мм2 по транспортному рольгангу с диаметром роликов 200 мм подавали в методическую печь, в которой его нагревали течение 5,5 ч при температурах, изменяющихся по зонам в интервале 1000… 1240° С, и прокатывали на лист толщиной 30 мм на стане 2800/1700. Для устранения дефектного слоя на листах проводили сплошную абразивную зачистку их поверхности. Толщина снятого слоя при зачистке на верхней широкой грани листа была 1,5 мм, а на нижней 1,8 мм.
Пример 2. Отличие от примера 1 заключалось в том, что на широкие грани сляба напыляли алюминиевое ГТП металлизатором ЭМ-14. Согласно зависимости (1) следует напылять покрытие на верхнюю грань толщиной:
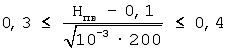
что составляет 0,232 Нпв 0,276 (мм),
а на нижнюю грань согласно зависимости (2) и с учетом того, что радиус ролика транспортного рольганга 200 мм:

что составляет 0,6Hпв Hпн 0,8Hпв или 0,139 Hпн 0,220 (мм).
Покрытие напыляли на верхнюю широкую грань толщиной 0,240 мм, а на нижнюю – 0,150 мм.
Для устранения дефектного слоя на листах проводили сплошную абразивную зачистку их поверхности. Толщина снятого слоя при зачистке на обеих широких гранях листа была одинаковой и равнялась 1 мм.
Пример 3. Отличие от примера 1 заключалось в том, что покрытие напыляли на верхнюю широкую грань толщиной 0,300 мм, а на нижнюю широкую грань толщиной 0,250 мм. При зачистке поверхности полученного листа толщина снятого дефектного слоя на верхней грани составила 1,4 мм, а на нижней 1,6 мм.
Пример 4. Отличие от примера 1 заключалось в том, что покрытие напыляли на верхнюю широкую грань толщиной 0,180 мм, а на нижнюю широкую грань толщиной 0,100 мм. При зачистке поверхности полученного листа толщина снятого дефектного слоя на верхней грани составила 1,3 мм, а на нижней 1,5 мм.
Из табл. 1 и 2 и приведенных примеров видно, что толщины покрытий, выбранные на основании данных неравенств, обеспечивают получение минимальной толщины дефектного слоя.
Таблица 1 |
Влияние толщины покрытия на верхней широкой грани сляба (Нпв) на толщину дефектного слоя на этой грани листа (Ндв) |
Нс, мм |
Нпв, ММ |
 |
Ндв, мм |
150 |
0,197 |
0,25 |
1,5 |
150 |
0,217 |
0,30 |
1,0 |
150 |
0,236 |
0,35 |
1,0 |
150 |
0,256 |
0,40 |
1,0 |
150 |
0,275 |
0,45 |
1,5 |
300 |
0,235 |
0,25 |
2,0 |
300 |
0,262 |
0,30 |
1,5 |
300 |
0,289 |
0,35 |
1,5 |
300 |
0,316 |
0,40 |
1,5 |
300 |
0,343 |
0,45 |
2,0 |
Таблица 2 |
Влияние толщины покрытия на нижней широкой грани сляба (Нпн) на толщину дефектного слоя на этой грани листа (Ндн) |
Нс, мм |
R, мм |
Нпв, мм |
Нпн, мм |
 |
Ндн, мм |
200 |
200 |
0,240 |
0,120 |
0,5 |
1,6 |
200 |
200 |
0,240 |
0,144 |
0,6 |
1,1 |
200 |
200 |
0,240 |
0,168 |
0,7 |
1,1 |
200 |
200 |
0,240 |
0,192 |
0,8 |
1,1 |
200 |
200 |
0,240 |
0,216 |
0,9 |
1,6 |
200 |
250 |
0,240 |
0,134 |
0,5 |
1,6 |
200 |
250 |
0,240 |
0,169 |
0,6 |
1,1 |
200 |
250 |
0,240 |
0,187 |
0,7 |
1,1 |
200 |
250 |
0,240 |
0,214 |
0,8 |
1,1 |
200 |
250 |
0,240 |
0,241 |
0,9 |
1,6 |
Примечание: Под значениями Нпн и Нпв понимают среднюю толщину покрытия, полученную как среднее арифметическое не менее 10 измерений толщины покрытия вдоль длины сляба. Толщину измеряли магнитным толщиномером МТ-41НЦ. |
Формула изобретения
Способ напыления алюминиевого газотермического покрытия на прямоугольные стальные слябы для нагрева их под прокатку, отличающийся тем, что покрытие напыляют на верхнюю широкую грань толщиной, определяемой из зависимости
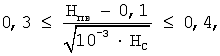
где Нпв – толщина покрытия, наносимого на верхнюю грань сляба, мм;
Нc – толщина сляба, мм;
а на нижнюю широкую грань сляба напыляют покрытие толщиной, определяемой из зависимости

где Нпн – толщина покрытия, наносимого на нижнюю широкую грань сляба, мм;
R – радиус роликов транспортного рольганга, мм.
|
|