|
(21), (22) Заявка: 2004102738/04, 03.02.2004
(24) Дата начала отсчета срока действия патента:
03.02.2004
(45) Опубликовано: 10.07.2005
(56) Список документов, цитированных в отчете о поиске:
US 5824214 А, 20.10.1998. RU 2095394 C1, 10.11.1997. RU 2181751 А1, 27.04.2002. RU 2208625 С1, 20.07.2003. US 6004454 A, 21.12.1999. US 5948721 А1, 07.09.1999.
Адрес для переписки:
123100, Москва, ул. Рочдельская, 11/5, кв.89, А.А.Озеренко
|
(72) Автор(ы):
Заманов В.В. (RU), Кричко А.А. (RU), Озеренко А.А. (RU), Озеренко Е.А. (RU), Фросин С.Б. (RU)
(73) Патентообладатель(и):
Озеренко Алексей Анатольевич (RU)
|
(54) СПОСОБ ПЕРЕРАБОТКИ НЕФТИ
(57) Реферат:
Использование: нефтепереработка, нефтехимия. В сырую нативную нефть с содержанием воды 2-10% вес. вводят катализатор, проводят активацию доноров водорода и гидрогенизацию сырой нефти. Катализатор используют в виде водорастворимых соединений металлов VI и VIII групп элементов периодической системы, растворяют в воде, содержащейся в сырой нефти, с образованием истинного раствора. В качестве доноров водорода используют собственные фракции сырой нефти и полученные из собственных фракций сырой нефти. Технический результат: упрощение процесса переработки с повышением глубины переработки нефти. 9 з.п. ф-лы, 1 табл., 1 ил.
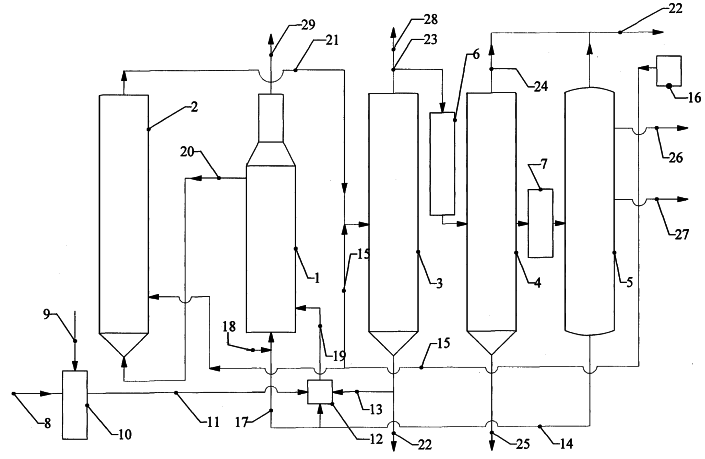
Изобретение относится к облагораживанию нефтяного сырья как на нефтеперерабатывающих предприятиях, так и на нефтепромыслах и к увеличению глубины его переработки с получением дистиллятных фракций, используемых при производстве топлив и смазочных масел. Изобретение может быть использовано также в нефтехимической промышленности.
Известен способ переработки тяжелых нефтяных остатков. В соответствии с этим способом, водо- или маслорастворимую соль молибдена в растворителе диспергируют в исходную нефть. Диспергирование проводится до создания стабильной эмульсии с диаметром капель 0,5-5,0 мкм. Далее производят перегонку нефти. Остаток перегонки с содержанием молибдена 0,001-1,000 мас.% вводят в реактор гидрогенизации (см. патент РФ №2208625, опубл. 2003 г., МПК7, C 10 G 47/02).
Известен способ гидрогенизации нефти в присутствии катализатора, в котором сырую нефть деметаллизируют и гидрогенизируют с дальнейшей перегонкой для получения нефтяных фракций (см. патент США №6342152, опубл. 2002 г., НКИ 208/108).
В вышеназванных известных способах перед гидрогенизацией и дистилляцией сырая нефть подвергается термической обработке на предшествующих стадиях переработки. В этом случае происходит необратимая трансформация высококипящих фракций нефти с образованием соединений, для дальнейшей переработки которых необходимы значительные давления и температуры, кроме того, в этом случае получается невысокая глубина переработки нефти.
Наиболее близким к настоящему изобретению является способ переработки нефти, включающий введение в сырую нефть катализатора и гидрогенизацию сырой нефти (см патент США 5824214, опубл. 1998 г., НКИ 208/107).
Однако и в этом способе происходит необратимая трансформация высококипящих фракций, содержащих смолы, асфальтены и другие высокомолекулярные образования, в малореакционноспособные, конденсированные соединения, образованные валентными связями, для последующей переработки которых в светлые нефтепродукты необходимо применять высокие давление водорода и температуру, большое количество дорогостоящих катализаторов.
Так, для гидрогенизации нефтяных остатков в светлые нефтепродукты способом, указанным выше (см. патент США №6342152), применяют давление до 20 МПа, соотношение сырье:катализатор 1:1, что является экономически нецелесообразным. В связи с этим мощность таких промышленных установок в мире не превышает 10 млн. т/год. Нефтяные остатки используют, как правило, в качестве компонентов котельного топлива, битума или, частично, для производства нефтяного кокса. Глубина переработки нефти в светлые нефтепродукты на лучших заводах не превышает 70-75%, а на заводах России составляет 60-65%.
Это обусловлено высокой реакционной способностью нативных (не подвергнутых термическому воздействию) высокомолекулярных соединений нефти при нагреве до температуры 260-400°С, что обусловлено спецификой их химического состава и строения.
Индивидуальные макромолекулы высококипящих фракций нефти представлены ассоциатами (мультимерами) макромолекул, связанных посредством невалентных взаимодействий. Существенное участие невалентных связей в образовании мультимеров обусловлено неравномерностью распределения электронной плотности по атомам и связям углеводородных и гетероциклических кластеров, образованных валентными связями. Эти кластеры не содержат заметных количеств полициклических ароматических углеводородов типа полифениленов, полинафтиленов и др.
В зависимости от соотношения количества смол, асфальтенов и насыщенных углеводородов в составе высококипящих фракций нефти существуют мультимеры с общей молекулярной массой до 104-105, представленные суперкомплексами на основе высокомолекулярных гидро- и ароматических, парфириноподобных фрагментов, соединенных метиленовыми, сульфидными и др. мостиками.
Мультимеры нефти имеют сложную структуру с диаметром частиц в слое 5-20 нм и толщиной образований 0,6-0,8 нм. Для превращения таких образований в светлые нефтепродукты со средней молекулярной массой 1·102-2·102 необходимо обеспечить проникновение в структуры реагентов с аналогичным физическим размером, например, молекул водорода и катализаторов, без которых при нагревании до умеренных температур произойдет необратимая трансформация их в малореакционноспособные, высокомолекулярные образования, что и наблюдается, например, при ректификации сырой нефти. Известно, что величины электроно-донорно-акцепторных взаимодействий не велики, составляя 20-40 кДж/моль, поэтому такие трансформации в сырой нефти легко протекают при непродолжительном нагревании, воздействии атмосферного воздуха при хранении, электростатической обработке, при обезвоживании и обессоливании нефти и пр.
Изменения реакционной способности нефти при нагревании для ректификации можно иллюстрировать следующим фактом. При гидрогенизации смеси (1:1) угля и нефтепродукта глубина превращения угля под давлением 10 МПа в жидкие продукты была в 1,4 раза выше при использовании остатка арланской нефти с температурой кипения выше 260°С по сравнению с остатком с температурой кипения выше 350°С, причем добавление к нему отогнанной фракции с температурой кипения 260-350°С не восстанавливало активности растворителя. Природа исходной нефти также оказывала существенное влияние, а именно – с остатком арланской нефти превращение угля составляло 89%, а западно-сибирской – 79%.
Настоящим изобретением решается задача – упрощение переработки нефти с повышением глубины переработки нефти вплоть до 95,0% в светлые нефтепродукты.
При решении вышеназванной задачи достигается технический результат – исключение при перабатке нефти необратимых процессов образования высокомолекулярных продуктов с малой реакционной способностью.
Поставленная задача решается за счет того, что в известном способе переработки нефти, включающем введение в сырую нефть катализатора, активацию доноров водорода и гидрогенизацию сырой нефти, гидрогенизации подвергают нативную сырую нефть с содержанием воды 2-10% вес., катализатор используют в виде водорастворимых соединений металлов VI и VIII групп элементов периодической системы и растворяют его в воде, содержащейся в сырой нефти, с образованием истинного раствора, и в качестве доноров водорода используют собственные фракции сырой нефти и полученные из собственных фракций нефти.
А также за счет того, что:
– в качестве нативной сырой нефти используют нефть, не прошедшую предварительные стадии обработки, сопровождающиеся ее нагреванием при температуре более 200°С;
– в качестве катализатора используют водорастворимые соли молибдена в количестве 0,01-1,0 вес% в расчете на металл;
– в качестве катализатора используют водорастворимые соли никеля в количестве 0,01-1,0 вес% в расчете на металл;
– в качестве катализатора используют водорастворимые соли железа в количестве 0,01-1,0 вес% в расчете на металл;
– доноры водорода используют в виде собственных фракций сырой нативной нефти с температурой кипения 200-400°С;
– доноры водорода получают из собственных фракций сырой нативной нефти, нефти с температурой кипения 300-400°С, прошедших дополнительную гидроочистку;
– гидрогенизацию сырой нативной нефти осуществляют под давлением 3,5-7,0 МПа и температуре 410-450°С;
– выполняют совместную гидрогенизацию сырой нативной нефти и рециркулирующего остатка с температурой кипения более 330-360°С, содержащего введенный ранее катализатор;
– при получении товарных нефтепродуктов гидроочистке подвергается продукт из горячего сепаратора с последующей дистилляцией;
– под донорами водорода, полученными из фракций сырой нефти, понимают фракции, полученные в результате дистилляции продуктов гидрогенизации сырой нефти и гидроочистки фракций с температурой кипения 300-400°С в отдельной стадии производства.
Изобретение поясняется чертежом, на котором представлена блок-схема переработки сырой нефти.
В соответствии с этим чертежом блок-схема пеработки сырой нефти содержит трубчатую печь 1, реактор 2, горячий сепаратор 3, холодный сепаратор 4, ректификационную колонну 5, холодильник 6, подогреватель 7, трубопровод 8 для подачи сырой нативной нефти, ввод 9 для подачи катализатора, смеситель 10 для перемешивания и растворения катализатора и сырой нативной нефти. Через трубопровод 11 сырая нативная нефть подается во второй смеситель 12. Ко второму смесителю 12 подключены также трубопровод 13 из низа горячего сепаратора 3 и трубопровод 14 из низа ректификационной колонны 5. Для подачи водородсодержащего газа предназначен трубопровод 15, подключенный к выходу источника 16 очищенного водорода.
Способ переработки нефти осуществляется следующим образом. Сырая нативная нефть поступает по трубопроводу 8 и смешивается в смесителе 10 с катализатором, поступающим через ввод 9, при этом в исходном сырье содержится вода в количестве 2-10%. В сырую нативную нефть, смешанную с катализатором, во втором смесителе 12 подмешивается рециркулят, который поступает по трубопроводу 13 из низа горячего сепаратора 3 и по трубопроводу 14 из ректификационной колонны 5 в балансовом количестве 20-40%.
Для нагрева трубчатой печи 1 по трубопроводу 17 поступает остаток ректификации, а по трубопроводу 18 воздух.
Полученная в смесителе 12 смесь по трубопроводу 19 поступает в трубчатую печь 1, где осуществляется нагрев смеси. Далее по трубопроводу 20 она поступает в реактор 2, где выдерживается при давлении 3,5-7 МПа и при температуре 410-450°С в течение 20-30 минут, где и осуществляется гидрогенизация. Полученная в реакторе 2 смесь по трубопроводу 21 подается в горячий сепаратор 3. Температура этой смеси регулируется подачей водородсодержащего газа по трубопроводу 15 и охлаждается добавлением водородсодержащего газа до температуры 320-350°С. Продукт низа сепаратора 3, содержащий катализатор после дросселирования и охлаждения, по трубопроводу 13 возвращается в трубчатую печь 1. Около 1% продукта низа сепаратора 3 выводится через трубопровод 22 для регенерации.
Продукт верха горячего сеператора 3 по трубопроводу 23 поступает в холодильник 6, где охлаждается. В холодном сепараторе 4 продукт разделяется на водородсодержащий газ, который поступает в трубопровод 24, воду, которая поступает в трубопровод 25, гидрогенизат, который поступает в подогреватель 7, после которого направляется для ректификации в ректификационную колонну 5 для получения бензиновой и дизельной фракций. Эти фракции подаются через трубопроводы 26 и 27 в отдельные блоки, где проходят гидрооблагораживание с получением товарного бензина и дизельного топлива.
Часть продуктов по трубопроводу 28 может быть направлена на гидроочистку. Трубопровод 29 предназначен для выхлопа отработанных газов.
В соответствии с настоящим изобретением гидрогенизацию нефти осуществляют под давлением водорода 3,5-7,0 МПа, при температуре 410-450°С, скорости подачи 1,5-3 кг/л·час, и соотношении водородосодержащий газ: сырье 800-1200 л/кг, содержание катализатора в сырье 0,01-1,0% в расчете на металл – Мо, Ni, Co, Fe. Катализатор вводится в нефть в виде водорастворимых солей и растворяется в системе нефть – вода, с образованием истинного раствора, при содержании воды в нефти 2-10%.
Катализатор вводится в систему однократно и циркулирует вместе с остатком с температурой кипения выше 350°С после обезвоживания и дистилляции гидрогенизата. Переработке подвергается смесь сырой нефти и рециркулирующего остатка с температурой кипения выше 350°С, содержание которого составляет в смеси 20-40% в зависимости от качества нефти и условий процесса, а также в присутствии дополнительного донора водорода с температурой кипения 300-400°С после гидроочистки.
Результаты гидрогенизации приведены в таблице.
Выход жидких продуктов при однократном пропуске нефти в условиях проточной пилотной установки составлял около 95%, в т.ч. газообразование – 5-7%, расход водорода на реакции – 0,5-1%. Газ состоит в основном из углеводородов C1-C4. Главным образом С3-С4.
В результате гидрогенизации высококипящих фракций нефти и рециркулирующего остатка с температурой кипения выше 350°С из нефти получено до 35% бензиновых фракций с температурой кипения н. к. – 180°С, дизельных – до 60%. Расход водорода извне около 1% при полной переработке в светлые нефтепродукты.
В отличие от полученных результатов, при гидрогенизации нефтяного гудрона в аналогичных условиях, помимо светлых нефтепродуктов (до 60%), образуется до 30% фракций с температурой кипения 350-520°С вакуум-газойля, которые неодходимо выводить из системы и подвергать дополнительной переработке методами каталитического крекинга, гидрокрекинга и др.
Более глубокая переработка в настоящем изобретении высококипящих фракций в светлые нефтепродукты обусловлена присутствием в реакционной смеси донороводородных фракций с температурой кипения 200-400°С, в присутствии которых происходит межмолекулярное гидрирование и деструкция вакуум-газойлевых фракций в светлые нефтепродукты. Передача водорода от этих фракций сопровождается частичным их дегидрированием и содержание ароматических углеводородов во фракциях с температурой кипения 180-350°С увеличивается на 25-30%.
Бензиновые фракции в составе гидрогенизатов содержат 12-14% ароматических углеводородов, в основном C8-C9, 20-22% нормальных парафинов, 30-35% изопарафинов и 25-30% пяти- и шестичленных нафтенов. Содержание серы составляет 0,15-0,3%, октановое число по моторному методу 80-90 пунктов. После гидрообессеривания (давление 2,5-5,0 МПа, температура 300-360°С) получается бензин с содержанием серы 0,01%, бензола – менее 1%. Октановое число по исследовательскому методу 90-95 пунктов.
Фракции с температурой кипения 180-350°С после гидрооблагораживания (давление 2,0-3,5 МПа, температура 300-350°С, катализатор WS2) содержат серы менее 0,04%, ароматических углеводородов 20-22% и имеют цетановое число 50-51 пункта.
Кроме того, способ позволяет напрямую использовать фракцию из горячего сепаратора для гидроочистки с последующей дистилляцией на товарные нефтепродукты.
Таблица Результаты гидрогенизации нефти и характеристика жидких продуктов |
№ п/п |
Исходное сырье |
Западно-сибирская нефть (ЗСН) |
Смесь (70:30) ЗСН:остаток с т.к. выше 350°С |
Удмурдская нефть |
Арланская нефть |
исходная |
исходная + 25% фракции 300-400°С |
|
Температура процесса, °С |
430 |
440 |
440 |
450 |
450 |
|
Давление, МПа |
4,5 |
4,5 |
4,5 |
6,0 |
7,0 |
1 |
Выход жидких продуктов, % мас. (без учета воды) в том числе, с т.кип. – до |
95,5 |
95,2 |
95,6 |
94,8 |
94,9 |
|
…180°С |
20,5 |
21,0 |
24,0 |
20,0 |
22,0 |
|
…180-350°С |
47,1 |
53,5 |
42,6 |
44,8 |
41,0 |
|
… выше 350°С |
27,0 |
20,3 |
28,0 |
29,0 |
30,9 |
|
Тяжелый остаток |
0,9 |
0,4 |
1,0 |
1,0 |
1,0 |
2 |
Выход газа % мас. |
5,0 |
4,8 |
5,5 |
5,8 |
5,6 |
3 |
Расход Н2 % мас. |
0,5 |
0,7 |
1,1 |
0,6 |
0,5 |
4 |
Характеристика жидких продуктов |
|
|
|
|
|
|
4.1 Гидрогенизат плотность, элементный состав, % мас. |
0,8613 |
0,8570 |
0,8612 |
0,9030 |
0,8932 |
|
С |
85,02 |
85,16 |
85,88 |
84,92 |
84,91 |
|
Н |
13,01 |
13,31 |
12,90 |
12,10 |
12,25 |
|
S |
1,21 |
1,22 |
1,28 |
2,20 |
2,14 |
|
N |
0,02 |
менее 0,02 |
0,02 |
0,14 |
0,18 |
|
4.2 Фракция н.к. -180°С |
|
|
|
|
|
|
плотность, углеводородный состав, % мас. |
0,7456 |
0,7419 |
0,7486 |
0,7490 |
0,7488 |
|
ароматические |
12,1 |
11,6 |
14,1 |
17,2 |
18,3 |
|
н-парафиновые |
23,5 |
19,2 |
22,6 |
20,1 |
20,2 |
|
i-парафиновые |
30,8 |
33,1 |
36,1 |
29,0 |
30,0 |
|
нафтеновые |
30,0 |
34,1 |
25,1 |
31,9 |
34,3 |
|
непредельные |
2,3 |
2,0 |
2,1 |
1,8 |
3,2 |
|
Октановое число (моторный метод) |
82 |
84 |
83 |
80 |
81 |
|
4.3 Фракция 180-350°С |
|
|
|
|
|
|
плотность, содержание, % мас. |
0,8601 |
0,8521 |
0,8630 |
0,8651 |
0,842 |
|
аромат, углеводородов |
62,4 |
61,2 |
65,1 |
66,8 |
67,4 |
|
серы |
0,21 |
0,18 |
0,29 |
1,2 |
1,4 |
Формула изобретения
1. Способ переработки нефти, включающий введение в сырую нефть катализатора, активацию доноров водорода и гидрогенизацию сырой нефти, отличающийся тем, что активации и гидрогенизации подвергают нативную сырую нефть с содержанием воды 2-10 вес.%, катализатор используют в виде водорастворимых соединений металлов VI и VIII групп элементов Периодической системы и растворяют его в воде, содержащейся в сырой нефти, с образованием истинного раствора и в качестве доноров водорода используют собственные фракции сырой нефти и полученные из собственных фракций нефти.
2. Способ по п.1, отличающийся тем, что в качестве нативной сырой нефти используют нефть, не прошедшую предварительные стадии обработки, сопровождающиеся ее нагревом при температуре более 200°С.
3. Способ по п.1, отличающийся тем, что в качестве катализатора используют водорастворимые соли молибдена в количестве 0,01-1,0 вес.% в расчете на металл.
4. Способ по п.1, отличающийся тем, что в качестве катализатора используют водорастворимые соли никеля в количестве 0,01-1,0 вес.% в расчете на металл.
5. Способ по п.1, отличающийся тем, что в качестве катализатора используют водорастворимые соли железа в количестве 0,01-1,0 вес.% в расчете на металл.
6. Способ по п.1, отличающийся тем, что доноры водорода используют в виде фракций сырой нативной нефти с температурой кипения 200-400°С.
7. Способ по п.1, отличающийся тем, что доноры водорода получают из собственных фракций сырой нативной нефти с температурой кипения 300-400°С, прошедших дополнительную гидроочистку.
8. Способ по п.1, отличающийся тем, что активацию и гидрогенизацию сырой нативной нефти осуществляют под давлением 3,5-7,0 МПа и температуре 410-450°С.
9. Способ по п.1, отличающийся тем, что выполняют совместную гидрогенизацию сырой нативной нефти и рециркулирующего остатка с температурой кипения более 330-360°С, содержащего введенный ранее катализатор.
10. Способ по п.1, отличающийся тем, что при получении товарных нефтепродуктов гидроочистке подвергают продукт из горячего сепаратора с последующей дистилляцией.
РИСУНКИ
|
|