|
(21), (22) Заявка: 2004108609/15, 22.03.2004
(24) Дата начала отсчета срока действия патента:
22.03.2004
(45) Опубликовано: 10.07.2005
(56) Список документов, цитированных в отчете о поиске:
КОРСАКОВ-БОГАТКОВ С.М., Химические реакторы как объекты математического моделирования, Москва, Химия, 1967, с.с. 3-34, рис. П-9. SU 1611911 A1, 07.12.1990. SU 874636 A, 23.10.1981. RU 2077486 C1, 20.04.1997. RU 2182115 C2, 10.05.2002. RU 2058408 C1, 20.04.1996. GB 1313640 A, 18.04.1973.
Адрес для переписки:
690950, Приморский край, г.Владивосток, ГСП, ул. Пушкинская, 10, ДВГТУ, Патентный отдел
|
(72) Автор(ы):
Гордиенко П.С. (RU)
(73) Патентообладатель(и):
Гордиенко Павел Сергеевич (RU), Синьков Геннадий Викторович (RU)
|
(54) РЕАКТОРНАЯ УСТАНОВКА
(57) Реферат:
Изобретение может быть использовано в процессах фторидной технологии переработки титансодержащего сырья, например ильменитовых концентратов, при производстве диоксида титана. Реакторная установка содержит реактор, связанный с источниками реагентов, который посредством разгрузочного узла связан с аппаратами последующей переработки продуктов реакции, при этом реактор, аппараты и детали установки выполнены из материала стойкого к воздействию контактирующих с ними реакционных материалов, причем в качестве источников реагентов использованы бункер для твердого титансодержащего материала, например ильменита, и источник фторида аммония, разгрузочный узел содержит фильтратный, шламовый и газоотводящий выходы, при этом газоотводящий выход реактора связан с питателем аммиака, фильтратный выход реактора связан с первым фильтром, фильтратный выход которого связан со вторым фильтром, фильтратный выход которого связан с полостью реактора гидролиза, выход которого, в свою очередь, связан с третьим фильтром, шламовый выход которого связан с сушилкой-диспергатором, шламовый выход которой связан с загрузочным узлом реактора пирогидролиза, выход которого связан с емкостью для хранения белого пигмента, при этом газоотводящие выходы второго фильтра, сушилки-диспергатора, третьего фильтра и реактора пирогидролиза связаны с источником фторида аммония, кроме того, питатель аммиака связан со вторым фильтром и полостью реактора гидролиза, при этом источник фторида аммония дополнительно связан с полостью реактора гидролиза, кроме того, шламовые выходы реактора и первого фильтра связаны с емкостью для хранения шлама, при этом полость реактора пирогидролиза связана с источником пара посредством паропровода. Изобретение позволяет повысить надежность и работоспособность установки в условиях применения высокоагрессивных фторидсодержащих материалов в процессах переработки титансодержащего сырья с получением белого пигмента, обеспечить высокую полноту использования сырья, высокий выход и белизну продукта и упростить технологический процесс. 4 з.п. ф-лы, 4 ил.
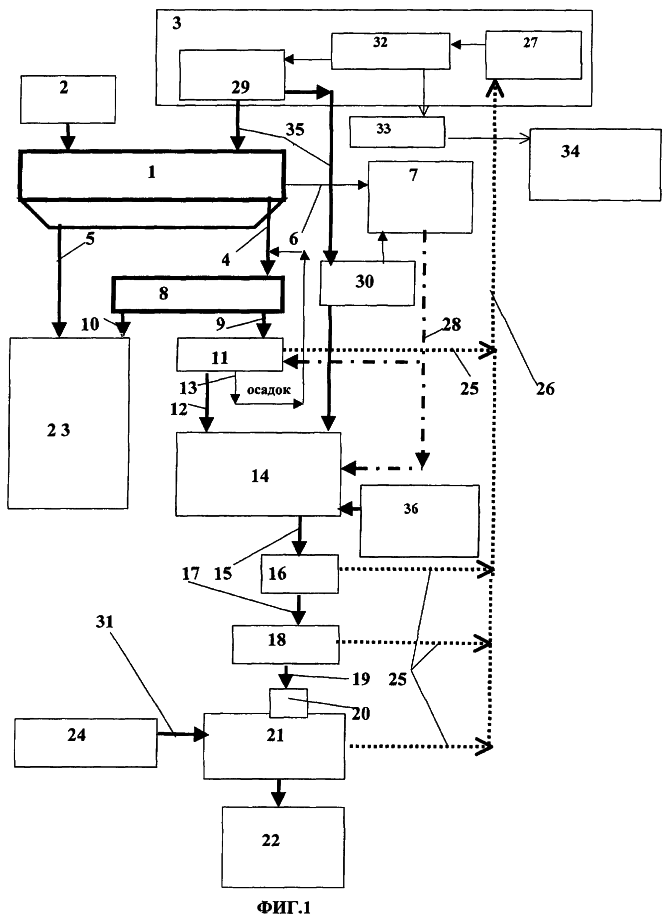
Изобретение относится к химическим реакторам и может быть использовано в процессах фторидной технологии переработки титансодержащего сырья, например ильменитовых концентратов, при производстве диоксида титана.
Известна реакторная установка, выполненная в виде каскада реакторов и аппаратов, содержащая теплообменник, трубопроводную систему и управляющие клапаны (см. книгу С.М.Корсакова-Богаткова Химические реакторы как объекты математического моделирования. М., “Химия”, 1967, с.64-69,рис.Ш-18).
Недостаток этих решений – невозможно эффективное использование для реализации фторидной технологии переработки титансодержащего сырья, например ильменитовых концентратов, при производстве диоксида титана из-за недостаточного ресурса работы оборудования.
Известна также реакторная установка, содержащая реактор, связанный с источниками реагентов, который посредством разгрузочного узла связан с аппаратами последующей переработки продуктов реакции, при этом реактор, аппараты и детали установки выполнены из материала, стойкого к воздействию контактирующих с ними реакционных материалов (см. книгу С.М.Корсакова-Богаткова Химические реакторы как объекты математического моделирования. М., “Химия”, 1967 с.64-69, рис. Ш-19).
Однако и это техническое решение также невозможно эффективно использовать для реализации фторидной технологии переработки титансодержащего сырья, например ильменитовых концентратов, при производстве диоксида титана из-за недостаточного ресурса работы оборудования. При этом решение проблемы обеспечения химической стойкости установки осложняется не только агрессивностью рабочей среды, но и термическим режимом работы (порядка 800-900°С), необходимым для получения качественного продукта (диоксида титана высокой степени белизны).
Задачей, на решение которой направлено предлагаемое техническое решение, является обеспечение возможности использования реакционной установки для реализации фторидной технологии переработки титансодержащего сырья с получением белого пигмента.
Технический результат, получаемый при решении поставленной задачи, выражается в повышении надежности и работоспособности установки в условиях применения высокоагрессивных фторидсодержащих материалов в процессах переработки титансодержащего сырья с получением белого пигмента. Кроме того, обеспечивается высокая полнота использования сырья, высокий выход и белизна продукта. Кроме того, по сравнению с “хлоридной” технологией переработки упрощается технологический процесс (исключается необходимость этапа металлургического передела, получения хлора и других энергоемких операций, а по сравнению с “сульфатной” технологией переработки существенно более высокое качество продукта и отсутствие отходов, объем которых существенно превышает выход готового продукта (на 1 тонну диоксида титана получается до 3 тонн сернокислого железа и до 4 м3 гидролизной серной кислоты, регенерация которой очень трудна).
Поставленная задача решается тем, что реакторная установка, содержащая реактор, связанный с источниками реагентов, который посредством разгрузочного узла связан с аппаратами последующей переработки продуктов реакции, при этом реактор, аппараты и детали установки выполнены из материала, стойкого к воздействию контактирующих с ними реакционных материалов, отличается тем, что в качестве источников реагентов использованы бункер для твердого титансодержащего материала, например ильменита, и источник фторида аммония, разгрузочный узел содержит фильтратный, шламовый и газоотводящий выходы, при этом газоотводящий выход реактора связан с питателем аммиака, фильтратный выход реактора связан с первым фильтром, фильтратный выход которого связан со вторым фильтром, фильтратный выход которого связан с полостью реактора гидролиза, выход которого в свою очередь связан с третьим фильтром, шламовый выход которого связан с сушилкой-диспергатором, шламовый выход которой связан с загрузочным узлом реактора пирогидролиза, выход которого связан с емкостью для хранения белого пигмента, при этом газоотводящие выходы второго фильтра, сушилки-диспергатора, третьего фильтра и реактора пирогидролиза связаны с источником фторида аммония, кроме того, питатель аммиака связан со вторым фильтром и полостью реактора гидролиза, при этом источник фторида аммония, дополнительно связан с полостью реактора гидролиза, кроме того, шламовые выходы реактора и первого фильтра связаны с емкостью для хранения шлама, при этом полость реактора пирогидролиза связана с источником пара посредством паропровода.
Кроме того, источник фторида аммония содержит накопитель фторида аммония, связанный с питателем фторида аммония, через испаритель, паровой выход которого через конденсатор связан с емкостью для хранения аммиачной воды, при этом в качестве выходов источника фторида аммония использованы выходы питателя фторида аммония, а в качестве входов источника фторида аммония использованы входы накопителя фторида аммония. Кроме того, питатель фторида аммония связан с питателем аммиака через нагреватель. Кроме того, шламовый выход второго фильтра связан со входом первого фильтра. Кроме того, полость реактора гидролиза связана с источником модификаторов.
Сопоставительный анализ признаков заявленного решения с признаками прототипа и аналогов свидетельствует о соответствии заявленного решения критерию “новизна”.
Признаки отличительной части формулы изобретения обеспечивают решение следующих функциональных задач.
Признаки “в качестве источников реагентов использованы бункер для твердого титансодержащего материала, например ильменита, и источник фторида аммония” обеспечивают реализацию первого этапа фторидной технологии переработки титансодержащего сырья – “вскрытие” исходного продукта (его перевод в физико-химическое состояние, обеспечивающее возможность реализации последующего этапа переработки).
Признаки “разгрузочный узел содержит фильтратный, шламовый и газоотводящий выходы” обеспечивают коммутацию узлов установки – передачу продуктов реакции в соответствующие “технологические цепочки”, при этом последний (вместе с признаком – “газоотводящий выход реактора связан с питателем аммиака”) исключает потерю аммиака (отхода на первом этапе переработки, но в то же время одного из реагентов, используемых на следующих этапах).
Признаки “фильтратный выход реактора связан с первым фильтром, фильтратный выход которого связан со вторым фильтром, фильтратный выход которого связан с полостью реактора гидролиза” описывают “линию тонкой очистки фильтрата” от соединений железа в технологической цепочке получения белого пигмента, т.е. обеспечивают удаление тех примесей, присутствие которых в готовом продукте не позволит обеспечить высокую степень его белизны.
Признаки, указывающие, что выход реактора гидролиза связан с “третьим фильтром, шламовый выход которого связан с сушилкой-диспергатором, шламовый выход которой связан с загрузочным узлом реактора пирогидролиза”, описывают “узел обезвоживания” оксофторотитаната аммония в технологической цепочке получения белого пигмента, обеспечивающий его подготовку к пирогидролизу.
Наличие реактора пирогидролиза обеспечивает (вместе с признаком, регламентирующим подключение полости реактора к источнику пара) возможность переработки оксофторотитаната аммония в белый пигмент и передачу его в емкость для хранения белого пигмента.
Признаки “газоотводящие выходы второго фильтра, первой сушилки-диспергатора, третьего фильтра и реактора пирогидролиза связаны с источником фторида аммония” обеспечивают многократность использования этого реагента, снижая его расход и, тем самым, улучшают технико-экономические показатели процесса получения белого пигмента.
Признаки “питатель аммиака связан со вторым фильтром и полостью реактора гидролиза” обеспечивают осаждение железосодержащих компонентов из раствора оксофторотитаната аммония и, тем самым, полноту его отделения при фильтрации.
Признаки “источник фторида аммония дополнительно связан с полостью реактора гидролиза” обеспечивают гидролиз оксофторотитаната аммония.
Признаки “шламовые выходы реактора и первого фильтра связаны с емкостью для хранения шлама” позволяют накопить шлам и утилизировать его, например дальнейшей переработкой в красный пигмент, тем самым может обеспечиваться высокая полнота использования исходного материала за счет расширения спектра получаемых из него продуктов.
Признаки второго пункта формулы описывают возможный вариант конструктивной реализации источника фторида аммония, кроме того, они позволяют утилизовать избыток воды, содержащей аммиак, с получением из него дополнительной продукции.
Признаки третьего пункта позволяют восполнять потерю аммиака по мере его расходования (удаления с парами воды).
Признаки четвертого пункта позволяют исключить потерю исходного материала, пригодного для получения красного пигмента.
Признаки пятого пункта позволяют “управлять” качеством получаемой продукции.
На фиг.1 показана схема установки; на фиг.2 показан разрез реактора вскрытия; на фиг.3 показан разрез первой ступени реактора пирогидролиза; на фиг.4 показан разрез второй ступени реактора пирогидролиза.
На чертежах показаны реактор 1, связанный с бункером 2 и источником 3 фторида аммония. Также показаны фильтратный 4, шламовый 5 и газоотводящий 6 выходы реактора 1, питатель аммиака 7, первый фильтр 8 с фильтратным 9 и шламовым 10 выходами, второй фильтр 11 с фильтратным 12 и шламовым 13 выходами, реактор гидролиза 14, выход 15 которого связан с третьим фильтром 16, шламовый выход 17 которого связан с сушилкой-диспергатором 18, шламовый выход 19 которой связан с загрузочным узлом 20 реактора пирогидролиза 21, выход которого связан с емкостью 22 для хранения белого пигмента. Фильтратный выход 4 реактора 1 связан с первым фильтром 8, а его шламовый выход 5 связан с емкостью для хранения шлама 23. Газоотводящий 6 выход реактора 1 связан с питателем аммиака 7. При этом фильтратный выход 9 первого фильтра связан со вторым фильтром 11, а его шламовый выход 10 связан с емкостью для хранения шлама 23. Причем фильтратный выход 12 второго фильтра связан с реактором гидролиза 14, а его шламовый выход 13 связан со входом первого фильтра (фильтратным выходом 4 реактора 1). Кроме того, показаны источник пара 24, газоотводящие выходы 25 второго фильтра, сушилки-диспергатора, третьего фильтра и реактора пирогидролиза, которые посредством сборного газопровода 26 связаны с накопителем 27 источника 3 фторида аммония, кроме того, показан питатель аммиака 7, который посредством газопровода 28 связан со вторым фильтром 11 и полостью реактора гидролиза 14, при этом питатель 29 источника 3 фторида аммония связан и с полостью реактора гидролиза 14 и с полостью реактора 1 и с нагревателем 30. Источник пара 24 связан с полостью реактора пирогидролиза посредством паропровода 31. Кроме того, источник 3 фторида аммония содержит накопитель 27 фторида аммония, связанный с питателем 29 фторида аммония, через испаритель 32, паровой выход которого через конденсатор 33 связан с емкостью для хранения аммиачной воды 34. При этом в качестве выходов источника 3 фторида аммония используют выходы питателя 29 фторида аммония, выполненные в виде трубопроводов 35, а в качестве входа источника фторида аммония использован вход накопителя 27 фторида аммония, выполненный в виде сборного газопровода 26. Кроме того, питатель 29 фторида аммония связан с питателем аммиака 7 через нагреватель 30. Кроме того, полость реактора гидролиза связана с источником модификаторов 36.
Поскольку заявляемая реакционная установка предназначена для реализации фторидной технологии переработки титансодержащего сырья, все ее узлы – реактор, реакторы пирогидролиза, гидролиза, фильтры, сушилки-дезинтеграторы, трубопроводы и другие элементы, контактирующие с агрессивными, фторидсодержащими реагентами и реакционными материалами, выполнены из материала, имеющего стойкость к воздействию контактирующих с ними реакционных материалов (в пределах рабочих температурных диапазонов).
Целесообразно использовать вертикальную (нисходящую) компоновку установки, при которой аппараты, обеспечивающие первые технологические операции, размещаются выше аппаратов, обеспечивающих последующие технологические операции, что позволит легко перемещать шламовидные реакционные материалы по технологической цепочке под действием их веса.
В качестве реактора 1 (см.фиг.2) используется реактор известной конструктивной схемы, включающий неподвижный герметичный цилиндрический корпус с вертикальной продольной осью, в полости которого размещен вращающийся вал с мешалками 37, снабженый приводом с регулятором скорости вращения. Через крышку корпуса реактора пропущены патрубки – загрузочный 38 (связанный с бункером 2) и реагентный 39 (связанный с источником 3 фторида аммония), а также фильтратный 4, газоотводящий 6 выходы реактора. Шламовый 5 выход реактора устроен в днище реактора. Реактор рассчитан на температуры 100-120°С. Заданный температурный режим обеспечивает теплоподводящий узел 40, выполненный в виде рубашки (дополнительной оболочки), размещенной на нижней части корпуса и днище реактора, подключенной к источнику теплоносителя (на чертежах не показан). Корпус реактора выполнен из конструкционного материала – химически стойкого хромоникелевого сплава типа 06ХН28МДТ, а его внутренняя поверхность, контактирующая с реагентами, и другие детали и узлы, размещенные в полости корпуса реактора, выполнены из магния или из графитопласта или стеклоуглерода или же снабжены защитным покрытием из названных материалов.
Первый фильтр 8 и второй фильтр 11 по конструкции не отличаются от известных аппаратов аналогичного назначения (кроме материала, использованного для их выполнения и герметичности рабочего пространства). Друг от друга они отличаются только рабочими параметрами фильтрующих узлов (второй фильтр 11 обеспечивает более тонкую фильтрацию), кроме того, второй фильтр подключен к питателю 7 аммиака и снабжен газоотводящим выходом 25).
Реактор гидролиза 14 не отличается от известных аппаратов аналогичного назначения (кроме материала, использованного для его выполнения, герметичности рабочего пространства, а также количества и назначения узлов ввода-вывода реакционных материалов и продуктов).
Третий фильтр 16 по конструкции не отличается от известных аппаратов аналогичного назначения (кроме материала, использованного для их выполнения, герметичности рабочего пространства и наличия газоотводящего выхода 25), выполненных на основе центрифуги, что диктуется консистенцией материала, подаваемого на его вход.
Сушилка-диспергатор 18 не отличается от известных аппаратов аналогичного назначения (кроме материала, использованного для ее выполнения, герметичности рабочего пространства и наличия газоотводящего выхода 25).
Загрузочный узел 20 реактора пирогидролиза 21 выполнен в виде герметичной емкости, связанной герметичным наклонным каналом, обеспечивающим “самотечную” подачу сыпучих материалов в реактор пирогидролиза (ее назначение – стабилизация во времени потока загружаемого реакционного материала). Реактор пирогидролиза отличается от реактора 1 конструктивной схемой (размещением его продольной оси под углом до 10° к горизонтали) и вращающимся вокруг этой оси корпусом цилиндрической формы, установленным на неподвижных цапфах (образующих собой неподвижные торцовые стенки корпуса). Из-за трудностей подбора материала для изготовления внутренних поверхностей реактора, который должен одновременно иметь высокую химическую стойкость к фторидсодержащим материалам и сохранять прочность при высоких (до 900°С) рабочих температурах, целесообразнее всего проводить процесс пирогидролиза в два этапа (первый – при пониженных до 300-350°С температурах, в условиях максимальных концентраций фторидсодержащих компонентов, с последующей обработкой полученного на первом этапе материала (концентрация фторидсодержащих компонентов в котором снижена на порядок и более) при более высоком уровне температур – до 900°С). Для этого можно использовать каскад из двух последовательно связанных реакторных блоков пирогидролиза 41 и 42 одинаковой конструкции (отличающихся только облицовкой внутреннего пространства). Корпус первого из них выполнен из конструкционного материала – химически стойкого хромоникелевого сплава типа 06ХН28МДТ, а его внутренняя поверхность, контактирующая с реагентами, и другие детали и узлы, размещенные в полости корпуса реактора, выполнены из магния или из графитопласта или стеклоуглерода или же снабжены защитным покрытием из названных материалов. Корпус второго из них выполнен из конструкционного материала – химически стойкого хромоникелевого сплава типа 06ХН28МДТ, а его внутренняя поверхность, контактирующая с реагентами, выполнена из оксида кремния (прессованного дисперсного кварца). Каждый из реакторных блоков подключен паропроводом 31 к источнику пара 24 (выполненному в виде генератора перегретого пара известной конструкции). Каждый из них также подключен газоотводящим выходом 25 к сборному газопроводу 26. Привод 43 вращения корпуса реактора пирогидролиза выполнен в виде электродвигателя с редуктором, выходная шестерня 44 которого установлена с возможностью взаимодействия с зубчатым венцом 45, жестко закрепленным на цилиндрической части корпуса каждого из реакторных блоков. Исходный материал загружается в первый реакторный блок 41, готовый продукт выгружается из второго реакторного блока 42. В связи с подвижностью корпусов каждого из реакторных блоков теплоподводящий узел 46 должен обеспечивать бесконтактный нагрев, поэтому в отличие от реактора 1 целесообразно, чтобы он был индукционного типа (например, из электромагнитных индукторов, установленных на кольцевых рамах, обхватывающих обечайку и осуществляющих бесконтактный высокочастотный прогрев внешней оболочки реактора).
Источник модификаторов 36 выполнен в виде бункера, герметизированного от окружающей среды, снабженного средством подачи модификаторов (тонкодисперсной смеси солей цинка, алюминия, циркона, кремния) в реактор гидролиза 14 (например, выполненным в виде наклонной трубы, обеспечивающей самотечную подачу сыпучего материала).
Емкости 22 и 23 для хранения, соответственно белого пигмента и шлама, емкость для хранения аммиачной воды 34 по конструкции подобны (отличие в средствах разгрузки емкостей, а также в материале – поверхность емкости 22, соприкасающаяся с белым пигментом, выполнена из материала либо не окисляющегося, либо дающего бесцветные продукты окисления). Питатель 29 и накопитель 27 фторида аммония выполнены в виде герметичных емкостей для хранения растворов фторида аммония, снабженных соответствующими насосными средствами (на чертежах не показаны). Питатель 7 аммиака выполнен в виде герметично закрывающейся емкости, снабженной раздаточными узлами известной конструкции, выполненными, например, в виде кранов из материала, стойкого к воздействию аммиака.
Испаритель 32, конденсатор 33 и нагреватель 30 выполнены в виде теплообменных аппаратов, обеспечивающих либо подвод тепла к прокачиваемым через них жидкостям (испаритель 32 и нагреватель 30), либо отбор тепла от прокачиваемых через них парожидкостных потоков (конденсатор 33).
Разъемные детали корпусов реактора, реакторов пирогидролиза, других аппаратов установки и контактные поверхности подвижных соединений герметизированы с использованием уплотнителей (на чертежах не показаны) из достаточно упругого, химически стойкого материала, предпочтительно, полимерного на основе углепластов или полипропилена, если последний выдерживает рабочие температуры реактора.
Кроме того, в состав установки входит комплект контрольно-измерительной аппаратуры известной конструкции, не показанный на чертежах, обеспечивающий контроль за режимом работы (температурой, объемом загрузки, кислотностью среды и другими рабочими параметрами).
Заявленная установка работает следующим образом.
В полость реактора 1 из бункера 2 через загрузочный патрубок 38 загружают порцию титаносодержащего сырья, например ильменитового концентрата, основой которого является ильменит (FеТiO3), и через реагентный патрубок 39 из питателя 29 источника 3 фторида аммония вводят водный раствор фтористого аммония (NH4F) (с большим избытком последнего), включают в работу привод вала мешалок 37, обеспечивая непрерывное перемешивание реакционных компонентов, и производят подачу теплоносителя в теплоподводящий узел 40. Внешняя поверхность реактора 1, контактирующая с теплоносителем, нагревается и отдает тепло в полость реактора, доводя температуру внутри него до 90-110°С. Пары аммиака и воды отгоняются через газоотводящий выход 6. По истечении времени, которое определяется например эмпирически с учетом температурных параметров, концентрации реагентов и т.п., для концентратов, различающихся по содержанию полезного компонента или отбором проб из реактора и их экспресс-анализом, из реактора удаляют образовавшуюся жидкую фракцию (через фильтратный выход 4), содержащую тонкую взвесь нерастворимых фтороферратов аммония в растворе фторотитанатов аммония.
Далее в реактор загружают новую порцию компонентов, и все повторяется. С учетом цикличности процесса “вскрытия” исходного титансодержащего материала целесообразно иметь в работе несколько реакторов либо использовать промежуточные накопительные емкости, объем которых позволяет обеспечивать постоянный по времени объем подачи продукта вскрытия исходного материала.
Если осуществлять ввод водного раствора фтористого аммония под объем загрузки твердого реакционного компонента (концентрата ильменита), это будет дополнительно способствовать перемешиванию реагентов газовыми пузырьками выделяющегося аммиака.
Регулируя скорость вращения вала мешалок 37, добиваются того, чтобы перемешивание реакционных компонентов происходило без излишнего взмучивания образующейся жидкой фракции (т.е. без перевода частиц твердого компонента, имеющих достаточно большую гидравлическую крупность – не полностью прореагировавших, во взвешенное состояние).
Поскольку, кроме полезного компонента в составе ильменитового концентрата присутствуют и балластные компоненты, по мере работы реактора балластные компоненты (шламы) накапливаются в реакторе, периодически, после удаления образовавшейся жидкой фракции шламы удаляют из полости реактора, открывая для этого шламовый выход 5.
Далее взвесь нерастворимых фтороферратов аммония в растворе фторотитанатов аммония подают на первый фильтр 8, осуществляющий первичное разделение раствора на шламовую фракцию (содержащую фтороферраты аммония) и фильтратную фракцию (содержащую фторотитанаты аммония) и соответствующее коммутирование названных материалов, соответственно в технологическую цепочку получения красного пигмента или технологическую цепочку получения белого пигмента.
В технологической цепочке получения белого пигмента фильтратная фракция (содержащая фторотитанаты аммония) поступает на второй фильтр 11, осуществляющий вторую (более тонкую) степень очистки, при этом подача во второй фильтр аммиака (из питателя аммиака 7) способствует коагуляции солей железа и выпадению их в осадок. При этом шламовую фракцию возвращают на вход первого фильтра 8, а фильтратную подают в реактор гидролиза 14, где вводят в контакт с водным раствором фтористого аммония (NH4F), аммиаком и модифицирующими добавками, подаваемыми соответственно из источника 3 фторида аммония, питателя 7 аммиака и источника модификаторов 36. В результате, на выходе 15 реактора гидролиза 14 получают шлам (пастовидную массу) оксофторотитаната аммония. Этот материал обезвоживают, отгоняя водный раствор фторида аммония на третьем фильтре 16 и досушивая и измельчая его на сушилке-дезинтеграторе 18. Затем через загрузочный узел 20 сыпучий оксофторотитанат аммония пропускают через реакторные блоки пирогидролиза 41 и 42 реактора пирогидролиза, куда одновременно подают перегретый пар и поддерживают температуру (до 300-350°С – в реакторном блоке пирогидролиза 41, а в реакторном блоке пирогидролиза 42 – до 900°С).
Перемещение материала в полости реакторных блоков осуществляется за счет того, что при вращении их корпусов частицы твердого компонента пересыпаются, скатываясь под действием силы тяжести с поверхности, образованной частицами материала в полости реакторного блока. Эта поверхность имеет форму наклонной плоскости, верхний конец которой расположен со стороны, в которую “идет вращение”, и, как только эти частицы выходят на уровень поверхности естественного откоса, они скатываются вниз. Поскольку продольная ось имеет наклон, движение частиц происходит не в пределах поперечной плоскости обечайки, а имеет вектор, направленный от входа к выходу. Таким образом перегретый водяной пар все время имеет возможность контакта с “самоперемешивающимися” частицами твердого компонента. Работа теплоподводящего узла 46 обеспечивает заданный температурный режим работы реактора за счет бесконтактного нагрева внешней поверхности реакторных блоков и передачи тепла на внутреннюю поверхность полости реактора и последующих излучения тепла в полость реакторного блока и передачи тепла частицам твердого компонента, контактирующим с ней, доводя температуру в полости реактора до 300-350°С. NH4F и HF, образующиеся в процессе реакции оксофторотитаната аммония и перегретого пара, вместе с парами воды отгоняются через газоотводящий патрубок 25. Твердый компонент перегружается в реакторный блок пирогидролиза 42. Он рассчитан на температурный режим до 800-900°С и работает аналогично только что описанному, но в качестве исходного продукта в него вводят материал, содержащий TiO2 и оставшуюся часть оксофторотитаната аммония (до 10% от исходного количества). В процессе перемещения твердого компонента по облицовке из прессованного дисперсного кварца ее материал вступает в реакцию с HF (выделяющейся в процессе реакции), с образованием тетрафторида кремния (легколетучего соединения), удаляемого с отходящими газами через газоотводящий выход 25. Контакт подаваемого в полость реактора перегретого пара с оставшейся частью непрореагировавшего оксофторотитаната аммония при температуре до 800-900°С приводит к тому, что он полностью вступает в реакцию. Это обеспечивает на выходе получение качественного оксида титана (TiO2). Его выгружают в емкость 22 для хранения белого пигмента. В процессе работы установки NH4F и HF, образующиеся во втором фильтре 11, сушилке-диспергаторе 18, третьем фильтре 16, реакторе пирогидролиза 21, через их газоотводящие выходы 25 сбрасываются вместе с парами воды в сборный газопровод 26 и далее в накопитель 27 фторида аммония. Для восстановления концентрации фторида аммония собранный таким образом материал подвергают упариванию в испарителе 32. Испаряющиеся при этом пары воды содержат до 2% аммиака. После их конденсации полученную аммиачную воду сбрасывают в емкость для ее хранения.
Количество аммиака в питателе 7 аммиака восполняют сбросом в него аммиака из реактора 1, а если этого недостаточно, то за счет работы нагревателя 30 разлагают соответствующую часть фторида аммония (отбирая его из трубопровода, связывающего питатель 29 фторида аммония и реактор гидролиза 14) с получением аммиачных паров, которые также сбрасывают в питатель 7 аммиака.
Шламовую фракцию (содержащую фтороферраты аммония), получаемую на шламовых выходах 5 и 10 соответственно реактора 1 и фильтра 8, подают в емкость 23 для хранения, и, по мере накопления, вывозят для утилизации с переработкой в красный пигмент.
Формула изобретения
1. Реакторная установка, содержащая реактор, связанный с источниками реагентов, который посредством разгрузочного узла связан с аппаратами последующей переработки продуктов реакции, при этом реактор, аппараты и детали установки выполнены из материала, стойкого к воздействию контактирующих с ними реакционных материалов, отличающаяся тем, что в качестве источников реагентов использованы бункер для твердого титансодержащего материала, например ильменита, и источник фторида аммония, разгрузочный узел содержит фильтратный, шламовый и газоотводящий выходы, при этом газоотводящий выход реактора связан с питателем аммиака, фильтратный выход реактора связан с первым фильтром, фильтратный выход которого связан со вторым фильтром, фильтратный выход которого связан с полостью реактора гидролиза, выход которого, в свою очередь, связан с третьим фильтром, шламовый выход которого связан с сушилкой-диспергатором, шламовый выход которой связан с загрузочным узлом реактора пирогидролиза, выход которого связан с емкостью для хранения белого пигмента, при этом газоотводящие выходы второго фильтра, сушилки-диспергатора, третьего фильтра и реактора пирогидролиза связаны с источником фторида аммония, кроме того, питатель аммиака связан со вторым фильтром и полостью реактора гидролиза, при этом источник фторида аммония дополнительно связан с полостью реактора гидролиза, кроме того, шламовые выходы реактора и первого фильтра связаны с емкостью для хранения шлама, при этом полость реактора пирогидролиза связана с источником пара посредством паропровода.
2. Реакторная установка по п.1, отличающаяся тем, что источник фторида аммония содержит накопитель фторида аммония, связанный с питателем фторида аммония через испаритель, паровой выход которого через конденсатор связан с емкостью для хранения аммиачной воды, при этом в качестве выходов источника фторида аммония использованы выходы питателя фторида аммония, а в качестве входов источника фторида аммония использованы входы накопителя фторида аммония.
3. Реакторная установка по п.1, отличающаяся тем, что питатель фторида аммония связан с питателем аммиака через нагреватель.
4. Реакторная установка по п.1, отличающаяся тем, что шламовый выход второго фильтра связан со входом первого фильтра.
5. Реакторная установка по п.1, отличающаяся тем, что полость реактора гидролиза связана с источником модификаторов.
РИСУНКИ
MM4A – Досрочное прекращение действия патента СССР или патента Российской Федерации на изобретение из-за неуплаты в установленный срок пошлины за поддержание патента в силе
Дата прекращения действия патента: 23.03.2006
Извещение опубликовано: 20.02.2007 БИ: 05/2007
NF4A Восстановление действия патента СССР или патента Российской Федерации на изобретение
Дата, с которой действие патента восстановлено: 27.02.2009
Извещение опубликовано: 27.02.2009 БИ: 06/2009
|
|