|
(21), (22) Заявка: 2003136629/02, 19.12.2003
(24) Дата начала отсчета срока действия патента:
19.12.2003
(45) Опубликовано: 10.07.2005
(56) Список документов, цитированных в отчете о поиске:
ГРАБАРНИК Л.М., НАГАЙЦЕВ А.А. Прессование цветных металлов и сплавов, Москва, Металлургия, 1991, с.38. SU 927356 А1, 15.05.1982. SU 1281317 A1, 07.01.1987. RU 2218223 С2, 10.12.2003. US 5095734 А1, 17.03.1992. GB 1520517 A1, 09.08.1978.
Адрес для переписки:
121552, Москва, ул. Оршанская, 3, “МАТИ”, патентный отдел
|
(72) Автор(ы):
Петров А.П. (RU), Еремеев В.В. (RU), Кириянко А.Д. (RU), Колобнев Н.И. (RU), Хохлатова Л.Б. (RU), Волошина Е.Е. (RU)
(73) Патентообладатель(и):
Федеральное государственное унитарное предприятие “Всероссийский научно-исследовательский институт авиационных материалов” (ФГУП “ВИАМ”) (RU), Российский государственный технологический университет им. К.Э. Циолковского (“МАТИ”) (RU)
|
(54) СПОСОБ ПРЕССОВАНИЯ ПРЯМОУГОЛЬНЫХ ПРОФИЛЕЙ ИЗ АЛЮМИНИЕВЫХ СПЛАВОВ И МАТРИЦА ДЛЯ РЕАЛИЗАЦИИ ДАННОГО СПОСОБА
(57) Реферат:
Изобретение относится к области обработки металлов давлением, в частности к способам прессования профилей из сплавов на основе алюминия и конструкциям прессового инструмента. Способ включает получение заготовки, нагрев, горячее прессование путем выдавливания заготовки через матрицу и последующую термообработку профиля. В процессе выдавливания заготовку в верхней части матрицы дополнительно подвергают сдвиговым деформациям за счет закручивания её на угол от 40 до 50° к оси матрицы. Матрица содержит деформирующий конус, рабочий поясок прямоугольной формы и выходной участок. Деформирующий конус выполнен с двумя винтовыми выступами, имеющими форму трапеции. Верхнее основание трапеции выполнено равным длине прямоугольника рабочего пояска, а нижнее основание составляет 1,5-2 частей этой длины. Угол поворота верхнего сечения выступа относительно нижнего сечения составляет 40-50° к оси матрицы. В долевом сечении выступы имеют форму параболы. В результате обеспечивается создание способа прессования, позволяющего получать прямоугольные профили из алюминиевых сплавов, обладающие повышенными механическими характеристиками, низкой анизотропией свойства, и матрицы, позволяющей реализовать данный способ. 2 н.п. ф-лы, 4 ил., 1 табл.
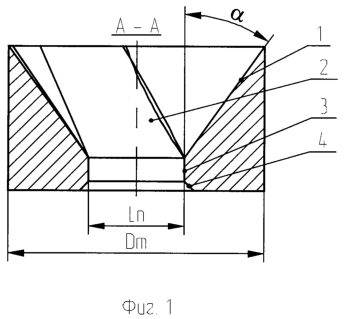
Изобретение относится к области обработки металлов давлением, в частности к способам прессования профилей из сплавов на основе алюминия и конструкциям прессового инструмента.
Качество профилей из алюминиевых сплавов зависит от степени деформации и равномерности ее распределения по объему заготовки.
Известен способ получения металлической полосы путем прессования, в котором матрица для прессования полос содержит заходную воронку прямоугольного сечения и формирующий участок, большие стороны которого выполнены с выпуклостями в направлении вертикальной и горизонтальной осей матрицы, причем кривизна выпуклости к горизонтальной оси уменьшается по направлению к калибрующему пояску [Авторское свидетельство СССР №867445, В 21 J 5/04, 1981].
Прессование полос через подобную матрицу позволяет получать в значительной степени стабильное распределение деформаций по длине полосы за счет выравнивания скоростей истечения. Однако такой способ не обеспечивает равномерную проработку центральных и периферийных слоев заготовки, что приводит к анизотропии свойств полосы в поперечном сечении, а также не достигается высокий уровень сдвиговых деформаций, необходимых для получения изделия с высокими механическими характеристиками.
Известен способ получения металлических прутков экструдированием заготовки через матрицу, содержащую заходную часть, формирующую часть со спиральными канавками, и калибрующий поясок, причем на заходной части матрицы выполнены спиральные канавки с наклоном к образующей ее поверхности, противоположным наклону канавок формирующей части матрицы, при этом концы канавок заходной части смещены относительно начала канавок формирующей части [Авторское свидетельство СССР №776692, кл. В 21 С 25/02, 1980.].
Прессование через подобную матрицу обеспечивает достаточно высокий уровень сдвиговых деформаций и равномерность их распределения при получении изделий цилиндрической формы. Однако при прессовании профилей прямоугольной формы подобный эффект невозможен, так как при такой конфигурации, расположении и количестве канавок произойдет неравномерное распределение деформаций по периметру прямоугольного профиля. Поверхностные слои заготовки будут срезаться и тормозить истечение материала заготовки, что приведет к значительному росту удельных давлений, а также невозможно формообразование на выходе из калибрующего пояска матрицы прямоугольного профиля.
Наиболее близким по технической сущности и назначению к предлагаемому способу является способ прессования профилей из алюминиевых сплавов, в том числе и прямоугольных, включающий получение заготовки, нагрев и горячее прессование путем выдавливания заготовки через матрицу с последующей термообработкой профиля [Л.М.Грабарник, А.А.Нагайцев. Прессование цветных металлов и сплавов. М.: Металлургия, 1991, с.338 с ил.]. Матрица для реализации данного способа содержит деформирующий конус, рабочий поясок, соответствующий профилю изделия, и выходной участок.
Недостатком данного способа является то, что процесс прессования нестационарен на всем протяжении. Это приводит к неравномерности деформации и, как следствие, к неравномерности и нестабильности структуры и механических свойств по длине и сечению профилей. Конструкция матриц, применяемых для реализации данного способа, не обеспечивает равномерных скоростей истечения материала заготовки, поверхностные слои профиля и особенно углы и участки резких переходов при прессовании подвергаются значительным деформациям, что при последующей термообработке приводит к интенсивной собирательной рекристаллизации и образованию у профилей из сплавов, проявляющих пресс-эффект, крупнокристаллического ободка с пониженными прочностными характеристиками по сравнению с центральными участками, в которых металл не рекристаллизован.
Технической задачей изобретения является создание способа прессования, позволяющего получать прямоугольные профили из алюминиевых сплавов, обладающие повышенными механическими характеристиками, низкой анизотропией свойств, и матрицы, позволяющей реализовать предложенный способ.
Для реализации поставленной задачи предложен.
Способ прессования прямоугольных профилей из алюминиевых сплавов, включающий получение заготовки, нагрев, горячее прессование путем выдавливания заготовки через матрицу и последующую термообработку, отличающийся тем, что заготовку в верхней части матрицы подвергают дополнительным сдвиговым деформациям за счет закручивания на угол от 40 до 50° к оси матрицы.
Матрица для прессования прямоугольных профилей из алюминиевых сплавов, содержащая деформирующий конус, рабочий поясок прямоугольной формы и выходной участок, отличающаяся тем, что деформирующий конус выполнен с двумя винтовыми выступами, имеющими форму трапеции, верхнее основание которой выполнено равным длине прямоугольника рабочего пояска, а нижнее составляет от (1,5÷2.0) частей этой длины, угол поворота верхнего сечения выступа относительно нижнего сечения составляет 40-50° к оси матрицы, причем в долевом сечении выступы имеют форму параболы, вершина которой удалена от плоскости деформирующего конуса на (0,15÷0,2)Dm, где Dm – наружный диаметр матрицы.
На чертеже представлены эскизы матрицы (фиг.1, 2 – виды матрицы сбоку; фиг.3 – вид сверху), где
1 – деформирующий конус;
2 – винтовые выступы;
3 – рабочий поясок;
4 – выходной участок.
На фиг.4 представлен общий вид матрицы.
Матрица для прессования профилей прямоугольного сечения из алюминиевых сплавов содержит деформирующий конический участок 1, выполняемый под углом от 30° до 60° исходя из литературных источников, а также данных проводимых ранее исследований, позволяющих сделать вывод, что данный интервал конусности деформирующего участка является оптимальным для размещения винтовых выступов и обеспечения при этом максимума сдвига. Два винтовых выступа 2 изготавливаются на деформирующем участке конуса матрицы и имеют форму трапеции, верхнее основание которой равно длине прямоугольника рабочего пояска, а нижнее основание составляет от (1,5÷2,0) частей этой длины. Винтовые выступы выполнены с углом поворота верхнего сечения выступа относительно нижнего от 40 до 50° к оси матрицы, причем в долевом сечении выступы имеют форму параболы, вершина которой удалена от плоскости деформирующего конуса на 0,15÷0,2 диаметра матрицы. Рабочий поясок 3 выполняется в форме прямоугольника, соответствующего профилю изделия, необходимого к получению.
Такое конструктивное решение позволяет в процессе прессования ввести дополнительные сдвиговые деформации за счет закручивания материала заготовки в деформирующем коническом участке матрицы, а также обеспечить равномерность скоростей истечения металла заготовки.
Увеличение предложенных величин винтовых выступов матрицы приведет к срезу внешних слоев заготовки и соответственно к образованию застойных зон, заполненных материалом заготовки. Процесс будет проходить, как при прессовании в конусную матрицу, только с меньшим углом деформирующего конуса и при более высоких энергосиловых параметрах. Уровень сдвиговых деформаций в данном случае будет определятся не профилем матрицы, а профилем застойных зон, в результате чего они локализуются на поверхностных слоях деформируемого материала, приводя к анизотропии механических свойств.
При соотношениях параметров винтовых выступов менее перечисленных не произойдет закручивания материала заготовки в очаге деформации, и процесс будет осуществляться как и при прессовании в конусную матрицу, но с еще большей неравномерностью распределения деформаций по сечению заготовки.
Пример осуществления.
Процесс прессования осуществляется со смазкой контейнера пресса, деформирующего конуса и рабочего пояска матрицы. Полученную заготовку, нагретую до заданной температуры, помещают в контейнер пресса, под воздействием давления, приложенного на пресс-штемпель, материал заготовки заполняет деформирующий конус 1 с винтовыми выступами 2, при этом происходит закручивание внешних слоев заготовки. Это обеспечивается благодаря конфигурации винтовых выступов, а также минимальным силам трения в начальный момент за счет введения смазки. На следующем этапе материал заготовки заполняет калибрующий поясок 3 матрицы и выпрессовывается в форме прямоугольного профиля заданных размеров, соответствующих рабочему пояску. Дальнейший процесс прессования проходит в стационарном режиме, при этом происходит дополнительный сдвиг и выравнивание скоростей истечения как внешних, так и внутренних слоев заготовки за счет формы и конфигурации винтовых выступов, что обеспечивает значительную всестороннюю и равномерную проработку заготовки и, как следствие, высокое качество изделия в термообработанном состоянии.
Для оценки сравнительных результатов были проведены эксперименты по прессованию прямоугольного профиля размером в поперечном сечении 10×30 мм из сплава АД37 с применением предлагаемой и известной матриц, угол деформирующего конуса в обоих случаях составлял =40°.
Прессование проводили на вертикальном гидравлическом прессе усилием 2,5 МН с диаметром контейнера Dк=82 мм, диаметром заготовки Dз=80 мм. Температура нагрева заготовок перед деформированием Тз=460°С, контейнера Тк=400°С. Состав применяемой смазки 70% вапор Т, 25% графит, 5% силиконовой смазки. Деформирующий конус предлагаемой матрицы был выполнен с двумя винтовыми выступами, имеющими форму трапеции с соотношением верхнего основания к нижнему а) – 30 мм: 45 мм; б) – 30 мм: 60 мм. Угол поворота верхнего сечения выступа относительно нижнего к оси матрицы равнялся а) – =40°; б) – =50°. Высота трапеции в максимальной точке изгиба винтового выступа, которая также является вершиной параболы, в долевом сечении матрицы равнялась а) – h=12 мм; б) – h=16 мм. Таким образом, по двум технологическим схемам были отпрессованы прямоугольные профили с размером в поперечном сечени 10×30 мм, при этом вытяжка составила =17,6, из которых были изготовлены образцы.
Результаты испытаний образцов, термообработанных по одному режиму, представлены в таблице.
Таблица испытаний образцов |
Способ |
Место вырезки образца по длине |
Предел прочности в, МПа |
Относительное удлинение , % |
продольное сечение |
поперечное сечение |
продольное сечение |
поперечное сечение |
Прототип |
Начало |
375 |
368 |
6,3 |
5,8 |
Середина |
387 |
372 |
9,3 |
9,0 |
Конец |
378 |
370 |
6,3 |
6,0 |
Предлагаемый. Варианты а) и б) близки по своим значениям |
Начало |
433 |
431 |
14,3 |
14,1 |
Середина |
435 |
435 |
14,5 |
14,4 |
Конец |
435 |
433 |
14,5 |
14,2 |
Таким образом, предлагаемое изобретение позволяет получать прессованные прямоугольные профили из алюминиевых сплавов с повышенными механическими свойствами и низкой анизотропией свойств, при стабильном давлении прессования и равномерной скорости истечения слоев заготовки. Процесс не требует конструктивных изменений традиционного оборудования, а также позволяет снизить энергосиловые параметры прессования.
Формула изобретения
1. Способ прессования прямоугольных профилей из алюминиевых сплавов, включающий получение заготовки, нагрев, горячее прессование путем выдавливания заготовки через матрицу и последующую термообработку профиля, отличающийся тем, что в процессе выдавливания заготовку в верхней части матрицы дополнительно подвергают сдвиговым деформациям за счет закручивания её на угол от 40 до 50° к оси матрицы.
2. Матрица для прессования прямоугольных профилей из алюминиевых сплавов, содержащая деформирующий конус, рабочий поясок прямоугольной формы и выходной участок, отличающаяся тем, что деформирующий конус выполнен с двумя винтовыми выступами, имеющими форму трапеции, верхнее основание которой выполнено равным длине прямоугольника рабочего пояска, а нижнее основание составляет от 1,5 до 2 частей этой длины, угол поворота верхнего сечения выступа относительно нижнего сечения составляет 40÷50° к оси матрицы, причем в долевом сечении выступы имеют форму параболы, вершина которой удалена от плоскости деформирующего конуса на (0,15÷0,2)Dm, где Dm – наружный диаметр матрицы.
РИСУНКИ
|
|