|
(21), (22) Заявка: 2003114304/02, 16.11.2000
(24) Дата начала отсчета срока действия патента:
16.11.2000
(30) Конвенционный приоритет:
16.11.2000 GB GB 00/04365
(43) Дата публикации заявки: 20.01.2005
(45) Опубликовано: 27.06.2005
(56) Список документов, цитированных в отчете о поиске:
US 5938862 А, 17.08.1999. WO 9709455 A1, 13.03.1997. WO 9904048 A1, 28.01.1999. SU 183037 A, 09.06.1966. SU 664796 А, 30.05.1979.
(85) Дата перевода заявки PCT на национальную фазу:
16.06.2003
(86) Заявка PCT:
GB 00/04365 (16.11.2000)
(87) Публикация PCT:
WO 02/40213 (23.05.2002)
Адрес для переписки:
107023, Москва, ул. Б.Семеновская, 49, оф.404, Центр “ИННОТЭК”, пат.пов. О.В.Аргасову
|
(72) Автор(ы):
МЕДДЛ Элан Ленард (GB), УОН Дженни С. (US), ГУО Шеньфен (US)
(73) Патентообладатель(и):
СИНГАПУР АСАХИ КЕМИКАЛ ЭНД СОУЛДЕР ИНДАСТРИЗ ПТЭ. ЛТД. (SG)
|
(54) БЕССВИНЦОВЫЙ ПРИПОЙ
(57) Реферат:
Изобретение может быть использовано для получения соединений низкотемпературной пайкой, в частности в микроэлектронике. Припой содержит ингредиенты в следующем соотношении, мас.%: Sn 76-96, Cu 0,2-0,5, Ag 2,5-4,5, In>0-12, Bi 0,5-5,0, Sb 0,01-2. Припой имеет удовлетворительный для производства электронных устройств диапазон температуры плавления 175-210°С, высокий предел прочности и высокую усталостную прочность, легко смачивает металлические подложки. 1 ил.
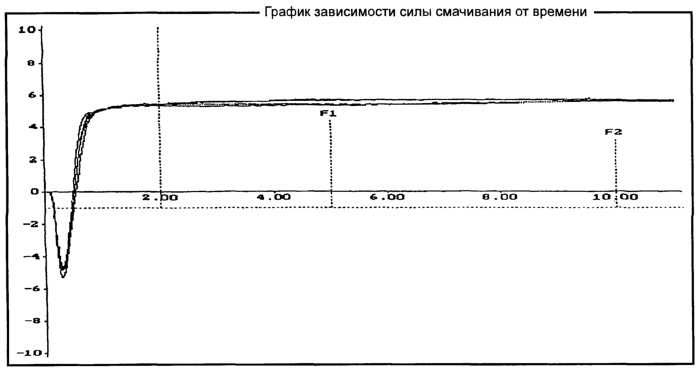
Настоящее изобретение относится к бессвинцовым припоям, предназначенным для осуществления низкотемпературной пайки и получения паяных соединений. Более конкретно, настоящее изобретение относится к бессвинцовым композициям, содержащим эффективные количества олова, меди, серебра, висмута, сурьмы и/или индия и имеющим температуру плавления, находящуюся в диапазоне 175-215°С. Такой припой особенно пригоден для применения в микроэлектронике и электронике.
Несмотря на успехи, достигнутые в настоящее время в электронной промышленности, припои, получаемые на основе сплава свинец-олово (Pb-Sn), имеют ограниченное будущее вследствие токсичности свинца или ограничений применения свинца в общей перспективе. Следовательно, придется предпринять международные инициативы, направленные на разработку бессвинцовых альтернатив припоям, получаемым на основе сплава свинец-олово (Pb-Sn). Между тем, существует необходимость высокого предела прочности и высокой усталостной прочности бессвинцового сплава, чтобы обеспечивать повышение уровня рабочих характеристик паяных соединений в соответствии с требованиями непрерывного совершенствования технологий интегральных схем и упаковки интегральных схем.
В иерархии производства электронной техники припой используют для получения металлургического соединения безкорпусных интегральных схем или корпусных интегральных схем на следующем уровне подложки посредством образования требуемых интерметаллических соединений. Мгновенное растекание и полное смачивание припоем металлических контактных площадок, например меди, серебра, золота, палладия, никеля (Сu, Аg, Аu, Pd, Ni) и других металлических поверхностей, является предпосылкой образования надежных соединений припоя в условиях высокоскоростного автоматизированного производственного технологического процесса при использовании мягких флюсов, которые являются приемлемыми для применения в электронных системах.
Технология поверхностного монтажа стала критической технологией производства для более быстрого получения меньших печатных плат с более высокой плотностью монтажа, которая сделала возможной получение современных электронных систем. Эвтектический припой на основе сплава свинец-олово (Pb-Sn) 63Sn/37Pb нашел наиболее широкое применение при сборке электронных систем, в частности печатных плат с компонентами поверхностного монтажа. Этот припой обеспечивает другое критическое физическое свойство, то есть умеренную температуру плавления, в частности температуру менее 210°С. Температура плавления сплава, за исключением эвтектической композиции, часто находится в диапазоне, определяемом температурой ликвидуса и солидуса. Сплав начинает размягчаться при его температуре солидуса и завершает плавление при его температуре ликвидуса. Низкотемпературная пайка должна быть выполнена при температуре выше температуры ликвидуса припоя.
Практическая температура технологического процесса низкотемпературной пайки в случае применения технологии поверхностного монтажа навесных электронных компонентов может быть достигнута при температуре, составляющей температуру приблизительно, по меньшей мере, на 25°С выше температуры ликвидуса припоя, например припой, имеющий температуру ликвидуса, составляющую 210°С, должен быть нагрет, как минимум, до температуры 235°С. Температура плавления припоя является критической, поскольку слишком высокая температура плавления будет в процессе пайки приводить к повреждению электронных приборов и разрушению печатных плат на полимерной основе, тогда как слишком низкая температура плавления будет оказывать отрицательное влияние на надежность паяных соединений при длительной эксплуатации. Для производства печатных плат на основе стандартных полимеров, например FR-4, температура технологического процесса не может практически превышать температуру 240°С. Таким образом, бессвинцовый припой, который может заменить припой 63Sn/37Pb и использоваться в технологическом производственном процессе поверхностного монтажа навесных электронных компонентов, должен иметь температуру ликвидуса менее 215°С, а предпочтительно приблизительно 210°С.
Паяные соединения работают как электрические, тепловые и механические соединения в электронных системах, например в системах связи, вычислительной технике, авиационных и автомобильных электронных устройствах. В течение срока службы паяные соединения неизбежно подвергаются воздействию термических напряжений в результате колебания температуры, приложения и снятия электрической мощности и/или суровых условий окружающей среды. Несогласованность теплового расширения соединяемых материалов полупроводника, керамики, металла и полимера в системе приводит в результате к термомеханической усталости паяных соединений. Когда плотность монтажа электронных компонентов становится значительно больше, а тактовая частота микропроцессоров продолжает достигать более высоких значений, одним из очевидных эффектов такой конструкции и материала, используемого для электронной системы, должно быть увеличение теплоотвода.
Кроме того, число паяных соединений на каждой печатной плате продолжает расти. Наличие нескольких тысяч или десятков тысяч паяных соединений на печатной плате не является необычным. Однако отказ любого одного паяного соединения в результате ведет к отказу системы. Следовательно, требования, предъявляемые к пределу прочности и усталостной прочности паяных соединений, повышаются. Недавние разработки корпусов интегральных схем с высоким числом внешних выводов, например корпусов больших интегральных схем с матрицей шариковых выводов, корпусов с размерами безкорпусной интегральной схемы, и технологий непосредственного присоединения интегральной схемы, например перевернутых бескорпусных интегральных схем, соединяемых с металлизированными соединениями за одну технологическую операцию, дополнительно требуют более высоких величин усталостной прочности для противодействия воздействию усталостных напряжений припоев.
В известном уровне техники было предложено несколько бессвинцовых припоев. Краткое описание этих бессвинцовых сплавов приведено в пятнадцатой главе книги “Современная технология пайки для конкурентоспособных электронных систем”.
В патенте США № 5328660, выданном Гонья на “БЕССВИНЦОВЫЙ ВЫСОКОТЕМПЕРАТУРНЫЙ ПРИПОЙ, МНОГОКОМПОНЕНТНЫЙ ПРИПОЙ НА ОСНОВЕ ОЛОВА”, описана композиция 78,4Sn2Ag9,8Bi9,8In. Однако усталостная прочность этого сплава является низкой.
В патенте США № 5527628, выданном Андерсону на “БЕССВИНЦОВЫЙ ТРОЙНОЙ ЭВТЕКТИЧЕСКИЙ ПРИПОЙ КОМПОЗИЦИИ SN-AG-CU”, описана композиция 93,6Sn4,7Ag1,7Cu, имеющая температуру плавления, составляющую 217°С. Температура плавления этого сплава еще относительно высока, а усталостная прочность является посредственной.
В патенте США № 5520752, выданном Льюси и др. на “КОМПОЗИТНЫЕ ПРИПОИ”, описан бессвинцовый припой, содержащий 86-97% Sn, 0,3-4,5% Ag, 0-9,3% Bi и 0-5% Сu. Однако усталостная прочность этого сплава является плохой. Усталостная прочность этого сплава является посредственной или низкой.
В патенте США № 5538686, выданном Чену на “ИЗДЕЛИЕ, СОДЕРЖАЩЕЕ БЕССВИНЦОВЫЙ ПРИПОЙ, ИМЕЮЩИЙ УЛУЧШЕННЫЕ МЕХАНИЧЕСКИЕ СВОЙСТВА”, описан бессвинцовый припой, имеющий температуру плавления, находящуюся в диапазоне от 173°С до 193°С, и содержащий >70% Sn, 6-10% Zn, 3-10% In, <10% Bi, >5% Ag и <5% Сu. Эти сплавы не могут смачивать стандартные подложки в производственной окружающей среде при корпусном монтаже электронных устройств.
В патенте США № 5580520, выданном Слаттери и др., на “БЕССВИНЦОВЫЙ СПЛАВ, СОДЕРЖАЩИЙ ОЛОВО, СЕРЕБРО И ИНДИЙ”, описана композиция 77,2Sn2,8Ag20In, имеющая температуру плавления, находящуюся в диапазоне от 179°С до 189°С. Усталостная прочность этого сплава является низкой.
Суммируя, можно сказать, что каждый из этих известных из уровня техники бессвинцовых припоев находится, по меньшей мере, в одной области для функционирования адекватно в образовании надежных паяных соединений при корпусном монтаже электронных устройств в электронной промышленности.
КРАТКОЕ ИЗЛОЖЕНИЕ СУЩНОСТИ НАСТОЯЩЕГО ИЗОБРЕТЕНИЯ
В соответствии с вышеизложенным основной задачей настоящего изобретения является получение бессвинцового припоя. Преимуществом настоящего изобретения является получение бессвинцового припоя, который имеет высокий предел прочности и высокую усталостную прочность для сопротивления воздействию повышенных вредных и суровых условий при использовании в микроэлектронных и электронных системах.
Дополнительным преимуществом настоящего изобретения является получение бессвинцового припоя, который имеет удовлетворительный диапазон температуры плавления (175-210°С), пригодный для производства основных электронных устройств.
Другим преимуществом настоящего изобретения является получение бессвинцового припоя, который может легко смачивать обычные металлические подложки, например олово, медь, серебро, золото, палладий и никель (Sn, Сu, Аg, Аu, Pd и Ni) в производстве микроэлектронных и электронных устройств.
Еще одним преимуществом настоящего изобретения является получение бессвинцового припоя, который может быть приготовлен для установленного технологического процесса и инфраструктуры электронных устройств, не требуя существенных изменений материалов, технологических процессов и компонентов.
Дополнительные задачи и преимущества настоящего изобретения будут изложены частично в следующем описании, а частично станут очевидными из следующего описания или могут быть выявлены при практическом применении настоящего изобретения. Задачи и преимущества настоящего изобретения могут быть реализованы и достигнуты посредством содействий и комбинаций, указанных, в частности, в прилагаемых пунктах формулы изобретения.
Для решения вышеуказанных задач и в соответствии с целями настоящего изобретения, как подробно и широко описано в этой заявке, припои, соответствующие настоящему изобретению, имеют олово (Sn) в качестве основного компонента и эффективные количества меди, серебра, висмута, индия и сурьмы (Сu, Аg, Bi, In и Sb). Этот припой демонстрирует совместимую температуру плавления, хорошую смачиваемость, высокий предел прочности и высокую усталостную прочность.
КРАТКОЕ ОПИСАНИЕ ЧЕРТЕЖА
Чертеж показывает зависимость силы смачивания (мН) от времени смачивания припоем: 82,3Sn0,5Cu3Ag2,2Bi12In на медном образце при температуре 235°С.
ПОДРОБНОЕ ОПИСАНИЕ ОСУЩЕСТВЛЕНИЯ НАСТОЯЩЕГО ИЗОБРЕТЕНИЯ
Хотя настоящее изобретение будет описано в связи с предпочтительным вариантом его осуществления, очевидно, что настоящее изобретение не ограничено описанным вариантом осуществления.
Настоящее изобретение обеспечивает получение высокого предела прочности, высокую усталостную прочность, высокую смачивающую способность, причем получаемый бессвинцовый припой имеет совместимую температуру плавления с установленной инфраструктурой производства печатных плат. Припой, соответствующий настоящему изобретению, содержит приблизительно 76-96 мас.% Sn, 0,2-2,5 мас.% Сu, 2-4,5 мас.% Аg, 0-12 мас.% In, 0-5,0 мас.% Bi и 0-2 мас.% Sb. Предпочтительно, чтобы композиция содержала, по меньшей мере, 2,0 мас.% индия. Предпочтительно, чтобы композиция содержала, по меньшей мере, 0,5 мас.% висмута. Предпочтительно, чтобы композиция содержала более 0 мас.% сурьмы. Более предпочтительно, чтобы сурьмы было более 0,01 мас.%.
В особенно предпочтительном варианте осуществления композиция, соответствующая настоящему изобретению, содержит приблизительно 81-93 мас.% Sn, 0,2-1,0 мас.% Сu, 2,5-4,5 мас.% Аg и 6-12 мас.% In. В дополнительном варианте осуществления настоящего изобретения композиция содержит приблизительно 81-90 мас.% Sn, >0-1 мас.% Си, 2,5-4,5 мас.% Аg, 6-12 мас.% In и >0 мас.% Sb. В альтернативном варианте осуществления настоящего изобретения композиция содержит 81-85 мас.% Sn, > 0-1 мас.% Сu, 2,5-4,5 мас.% Аg, 6-12 мас.% In и 0,5-3,5 мас.% Bi. В еще одном варианте осуществления настоящего изобретения композиция содержит 90-96 мас.% Sn, >0-2,5 мас.% Сu, 2,0-3,5 мас.% Аg и 0,5-5,0 мас.% Bi. Если дополнительно не указано в описании и формуле изобретения, то все доли и проценты являются массовыми.
Было обнаружено, что Сu и Аg, скомбинированные в соответствующих дозировках, не только увеличивают усталостную прочность, но также уменьшают температуру плавления. В предпочтительном варианте осуществления настоящего изобретения единственно 0,5 мас.% меди является наиболее эффективным количеством для уменьшения температуры плавления сплавов. Вариации температур плавления сплавов при 0,5-2,5 мас.% Сu находятся в пределах 1°С. Сu при более 2,5 мас.% препятствует текучести расплава, вызывая дефект отливки. Например, температуры плавления (185-195°С) сплава (83,4Sn/0,5Cu/4,1 Аg/12In), имеющего содержание меди 0,5 мас.%, приблизительно на 5°С ниже, чем температуры плавления (190-200°С) сплава (83,9Sn/4,1Ag/12In), не содержащего меди. Температуры плавления (195-201°С) сплава (87,4Sn/0,5Cu/4,1Ag/8In), имеющего содержание меди 0,5 мас.%, аналогичны температурам плавления (195-201°С) сплава (87Sn/2Cu/3Ag/8In), имеющего содержание меди 2 мас.%. Единственно 0,5 мас.% меди являются также наиболее эффективным количеством для увеличения усталостной прочности. Пластичность линейно уменьшается, а усталостная долговечность экспоненциально уменьшается при дополнительном увеличении содержания меди до приблизительно 2 мас.%. Например, пластичность и усталостная долговечность сплава (87,4Sn/0,5Cu/4,1Ag/8In), имеющего содержание меди 0,5 мас.%, на 206% и 146% выше, чем пластичность и усталостная долговечность сплава (86,1Sn/1,6Cu/4,3Ag/8In), имеющего содержание меди 1,6 мас.%. Пластичность и усталостная долговечность сплава (83,4Sn/0,5Cu/4,1Ag/12In), имеющего содержание меди 0,5 мас.%, на 250% и 174% выше, чем пластичность и усталостная долговечность сплава (82,4Sn/1,5Cu/4,1Ag/12In), имеющего содержание меди 1,5 мас.%.
Приблизительно единственно 3 мас.% Аg являются наиболее эффективными для понижения температур плавления сплавов. Вариации температур плавления сплавов, имеющих содержание серебра 34,5 мас.%, находятся в пределах 1°С. Например, температуры плавления (196-202°С) сплава (88,5Sn0,5Cu/3Ag/8In), имеющего содержание серебра 3 мас.%, приблизительно на 10°С ниже, чем температуры плавления (208-212°С) сплава (91,5Sn/0,5Cu/8In), не содержащего серебра, но приблизительно аналогичны температурам плавления (195-201°С) сплава (87,4Sn/0,5Cu/4,1Ag/8In), имеющего содержание серебра 4,1 мас.%.
Добавки индия линейно уменьшают температуры плавления в соотношении, составляющем приблизительно 1,8°С на массовый процент до приблизительно 12%. Прочность сплавов линейно увеличивается, а усталостная долговечность увеличивается экспоненциально с увеличением содержания индия до приблизительно 8 мас.%. Содержание 8-10 мас.% индия является оптимальным для более высокой усталостной прочности. Например, сплав (87,4Sn/-0,5Cu/4,1Ag/8In), имеющий содержание индия 8 мас.%, имеет меньшую на 6°С температуру плавления, на 126% более высокий предел прочности и на 175% более высокую усталостную долговечность, чем сплав (91,4Sn/0,5Cu/4,1Ag/4In), имеющий содержание индия 4 мас.%. 12 мас.% индия является критической точкой для ощутимого присутствия более мягкой второй фазы индия при 113°С. Например, сплав (83,4Sn/0,5Cu/4,1Ag/12In), имеющий содержание индия 12 мас.%, имеет на 219% более низкую продолжительную усталостную долговечность и на 118% более низкий предел прочности, чем сплав (85,4Sn/0,5Cu/4,1Ag/10In), имеющий содержание индия 10 мас.%.
Сплавы с относительно более высокими содержаниями (6-12 мас.%) индия могут быть дополнительно упрочнены висмутом для наименьших возможных температур плавления с допустимой усталостной прочностью для некоторых критических случаев применения. Например, сплав (82,3Sn/0,5Cu/3Ag/2,2Bi/12In), имеющий содержание индия 12 мас.% и содержание висмута 2,2 мас.%, имеют на 130% более высокий предел прочности и приблизительно на 20°С более низкую температуру плавления (183-193°С), чем сплав (83,4 Sn/0,5Cu/4,1Ag/12In), имеющий содержание индия 12 мас.% и не содержащий висмута. Максимально возможное содержание висмута должно быть менее 5 мас.% для допустимой пластичности и усталостной прочности. Например, пластичность и усталостная долговечность сплава (79,5Sn/0,5Cu/3Ag/5Bi/12In) значительно ухудшаются до уровня, который ниже уровня 63Sn/37Pb.
Припои, содержащие индий, могут быть также дополнительно упрочнены небольшим количеством сурьмы, например 0,5 мас.%, для достижения более высокой усталостной прочности без заметного увеличения температур плавления. Например, сплав (84Sn/0,5Cu/3Ag/2,2Bi/12In/0,5Sb), имеющий содержание 12 мас.% индия и 0,5 мас.% сурьмы, имеет на 113% более высокий предел прочности и на 160% более высокую усталостную долговечность, чем сплав (83,4Sn/0,5Cu/4,1Ag/12In), имеющий содержание индия 12 мас.% и не содержащий сурьмы. Однако слишком высокое содержание сурьмы для сплавов, содержащих индий, увеличит температуры плавления, уменьшит пластичность и усталостную долговечность и ухудшит смачиваемость на меди. Например, сплав (84Sn/0,5Cu/3Ag/12In/0,5Sb), имеющий содержание индия 12 мас.% и 0,5 мас.% сурьмы, имеет на 4°С более низкую температуру плавления, на 212% более высокую пластичность и на 125% более высокую усталостную долговечность, чем сплав (82,5Sn/0,5Cu/3Ag/12In/2Sb), имеющий содержание сурьмы 2 мас.%.
В зависимости от нижеописанных механизмов медь, серебро и сурьма образуют интерметаллические соединения с оловом. Медь образует частицы Cu6Sn5, серебро образует частицы Аg3Sn, а сурьма образует частицы SnSb. Эти интерметаллические частицы сами по себе намного прочнее матрицы олова и являются эффективными блоками распространению усталостной трещины. Косвенно, образование мультиинтерметаллических частиц разделяет более тонкую зернистую структуру матрицы олова. Более тонкие зерна интерметаллических соединений в матрице олова облегчают скольжение по границ зерен и продлевают усталостную долговечность.
Индий входит в кристаллическую решетку матрицы олова в качестве атомов раствора замещения. Индиевый раствор дает упрочнение твердого раствора и способствует более тонкому характеру скольжения для более высокой способности к предотвращению усталостного излома.
Висмут входит в кристаллическую решетку матрицы олова в качестве атомов раствора замещения до приблизительно 1 мас.%. При содержании более 1 мас.% висмут может выделяться в виде частиц второй фазы. Таким образом, висмут обеспечивает упрочнение твердого раствора и дисперсионное упрочнение. Часть упрочнения раствора висмута должна также способствовать более тонкому характеру скольжения для более высокой способности к предотвращению усталостного излома в матрице олова.
Содержание 2,5-3,5 мас.% серебра является критическим для припоев в системе Sn/Cu/Ag/Bi в противоположность содержанию 2,5-4,5 мас.% серебра для любых других систем, содержащих индий. Содержание серебра за 3,5 мас.% в системе Sn/Cu/Ag/Bi вызывает хрупкость сплава. Например, усталостная долговечность и пластичность сплава (93,3Sn/0,5Cu/3,1Ag/3,1Bi), имеющего содержание серебра 3,1 мас.%, приблизительно на 152% и 138% соответственно выше, чем у сплава (90,5Sn/1,7Cu/4,7Ag/3,1Bi), имеющего содержание серебра 4,7 мас.%. Содержание серебра 2,5 мас.% является минимальным для обеспечения превосходной усталостной прочности. При содержании серебра ниже 2,5 мас.% усталостная прочность понижается. Например, усталостные долговечности сплавов 93,3Sn/0,5Cu/3,1Ag/3,1Bi и 92,2Sn/1,5Cu/3,2Ag/3,1Bi и 91,5Sn/2Cu/3,4Ag/3,1Bi приблизительно на 538%, 366% и 281% соответственно выше, чем у сплава (93Sn/2Cu/2Ag/3Bi), имеющего содержание серебра 2 мас.%.
Однако в любых других системах, содержащих индий, индий будет вступать в химическую реакцию с серебром или абсорбировать некоторое количество серебра, образуя интерметаллическое соединение Agln2 или даже тройное интерметаллическое соединение AgSnIn. Таким образом, максимальное содержание серебра в любых других системах, содержащих индий, может быть 4,5 мас.% для обеспечения хорошей пластичности и усталостной долговечности.
Любое дополнительное содержание не будет дополнительно уменьшать температуру плавления, но увеличит хрупкость. Например, при одной температуре плавления пластичность сплава (84Sn/0,5Cu/13Ag/12,5Sb) на 131% выше, чем у сплава (81,1Sn/1,7Cu/4,7Ag/12In/0,5Sb).
Для ссылки укажем, что измеренная температура плавления припоя 63Sn/37Рb составляла приблизительно 183°С, предел прочности при растяжении составлял 47 МПа, а долговечность при малоцикловой усталости при растяжении 0,2% составляла 3650 циклов. Температура плавления, предел прочности при растяжении и усталостная долговечность известного припоя 99,3Sn0,7Cu составляли 227°С, 24 МПа и 1125 циклов соответственно. Температура плавления, предел прочности при растяжении и усталостная долговечность известного припоя 96,5Sn3,5Ag составляли 221°С, 35 МПа и 4186 циклов соответственно.
Припой, соответствующий настоящему изобретению, имеет прочность при растяжении, составляющую, по меньшей мере, 50 МПа, предпочтительно 60 МПа; долговечность при малоцикловой усталости при растяжении 0,2%, по меньшей мере, 5000 циклов, предпочтительно 10000 циклов; температуру солидуса в диапазоне 175-215°С, предпочтительно менее 210°С; и температуру ликвидуса в диапазоне 185-215°С, предпочтительно менее 210°С.
В предпочтительном варианте осуществления настоящего изобретения обеспечивается припой, содержащий приблизительно 87,4 мас.% Sn, 0,5 мас.% Сu, 4,1 мас.% Аg и 8 мас.% In. Этот сплав имеет температуру плавления в диапазоне от приблизительно 195°С до 201°С. Предел прочности при растяжении и усталостная долговечность этого сплава составляют 63 МПа и 17152 циклов соответственно. Усталостная долговечность припоя, соответствующего настоящему изобретению, на 470% выше, чем у припоя 63Sn/37Pb, а предел прочности при растяжении на 134% выше, чем у припоя 63Sn/37Pb.
В одном предпочтительном варианте осуществления настоящего изобретения обеспечивается получение припоя, содержащего приблизительно 85,4 мас.% Sn, 0,5 мас.% Сu, 4,1 мас.% Аg и 10 мас.% In. Этот сплав имеет температуру плавления в диапазоне от приблизительно 194°С до 199°С. Предел прочности при растяжении и усталостная долговечность этого сплава составляют 66 МПа и 17378 циклов соответственно. Усталостная долговечность припоя, соответствующего настоящему изобретению, на 476% выше, чем у припоя 63Sn/37Pb, а предел прочности при растяжении на 140% выше, чем у припоя 63Sn/37Pb.
В другом предпочтительном варианте осуществления настоящего изобретения обеспечивается получение припоя, содержащего приблизительно 84 мас.% Sn, 0,5 мас.% Сu, 3 мас.% Аg, 0,5 мас.% Sb и 12 мас.% In. Этот сплав имеет температуру плавления в диапазоне от приблизительно 186°С до 196°С. Предел прочности при растяжении и усталостная долговечность этого сплава составляют 58 МПа и 12345 циклов соответственно. Усталостная долговечность припоя, соответствующего настоящему изобретению, на 338% выше, чем у припоя 63Sn/37Pb, а предел прочности при растяжении на 123% выше, чем у припоя 63Sn/37Pb.
В еще одном предпочтительном варианте осуществления настоящего изобретения обеспечивается получение припоя, содержащего приблизительно 82,3 мас.% Sn, 0,5 мас.% Сu, 3 мас.% Аg, 2,2 мас.% Bi и 12 мас.% In. Этот сплав имеет температуру плавления в диапазоне от приблизительно 183°С до 193°С. Предел прочности при растяжении и усталостная долговечность этого сплава составляют 77 МПа и 8722 циклов соответственно.
Усталостная долговечность припоя, соответствующего настоящему изобретению, на 239% выше, чем у припоя 63Sn/37Pb, а предел прочности при растяжении на 164% выше, чем у припоя 63Sn/37Pb.
В другом предпочтительном варианте осуществления настоящего изобретения обеспечивается получение припоя, содержащего приблизительно 92 мас.% Sn, 2 мас.% Сu, 3 мас.% Аg и 3 мас.% Bi. Этот сплав имеет температуру плавления в диапазоне от приблизительно 209°С до 212°С. Предел прочности при растяжении и усталостная долговечность этого сплава составляют 89 МПа и 8135 циклов соответственно. Усталостная долговечность припоя, соответствующего настоящему изобретению, на 223% выше, чем у припоя 63Sn/37Pb, а предел прочности при растяжении на 189% выше, чем у припоя 63Sn/37Pb.
В дополнительном предпочтительном варианте осуществления настоящего изобретения обеспечивается получение припоя, содержащего приблизительно 83,4 мас.% Sn, 0,5 мас.% Сu 4,1 мас.% Аg и 12 мас.% In. Этот сплав имеет температуру плавления в диапазоне от приблизительно 185°С до 195°С, предел прочности при растяжении и усталостную долговечность 56 МПа и 7950 циклов соответственно. Усталостная долговечность припоя, соответствующего настоящему изобретению, на 218% выше, чем у припоя 63Sn/37Pb, а предел прочности при растяжении на 140% выше, чем у припоя 63Sn/37Pb.
В каждом из вышеуказанных вариантов осуществления имело место мгновенное растекание и хорошее соединение, как подтверждено испытаниями на баланс смачиваемости (фиг.1), превосходя требования в смачивающей способности со ссылкой на промышленные стандарты, например стандарты ANSI-STD-002 и ANSI-STD-003 Американского национального института стандартов, Смачивающим флюсом была неактивированная канифоль или слабоактивированная канифоль или неочищенный флюс.
В соответствии со стандартами ANSI-STD-002 и ANSI-STD-003 Американского национального института стандартов, относящимися к требованию, предъявляемому к смачивающей способности, сила смачивания при 2,0 сек (F1) и при 5,0 сек (F2) должна превышать 4809 мН, а время смачивания (t2/3), необходимое для достижения 2/3 величины максимальной силы смачивания, должно быть не более 1,0 сек. Площадь отсутствия способности смачиваться должна быть менее 5%. В качестве примера, иллюстрируемого на фиг.1, припой композиции (82,3%Sn/0,5Cu/3%Ag/2,2%Bi/12%In), соответствующей настоящему изобретению, имел следующие характеристики: F1=5,98 мН, F2=6,10 мН, t2/3=0,72 сек, площадь отсутствия способности смачиваться=0%.
Вышеуказанные бессвинцовые припои, соответствующие настоящему изобретению, могут быть получены в расплавленных состояниях основных компонентов с помощью технологии общего нагрева, известной из предшествующего уровня техники. Эти сплавы могут быть также использованы в различных физических состояниях, например, в виде паст, порошков, брусков и проволок или в любых технологических процессах пайки, например в печах пайки оплавлением, в установке пайки волной и при ручной пайке или при получении любых материалов, например, с помощью технологий осаждения и нанесения покрытия.
Хотя настоящее изобретение было описано со ссылкой на предпочтительные варианты осуществления, квалифицированным в этой области техники специалистам будут очевидны различные изменения и модификации. Вышеприведенное описание не предназначено для ограничения объема настоящего изобретения.
Формула изобретения
Бессвинцовый припой, состоящий из 76-96 мас.% Sn, 0,2-0,5 мас.% Cu, 2,5-4,5 мас.% Ag, >0-12 мас.% In, 0,5-5,0 мас.% Bi и 0,01-2 мас.% Sb.
РИСУНКИ
|
|