|
(21), (22) Заявка: 2003138014/02, 29.12.2003
(24) Дата начала отсчета срока действия патента:
29.12.2003
(45) Опубликовано: 20.06.2005
(56) Список документов, цитированных в отчете о поиске:
SU 1389147 A1, 27.08.2002. SU 812486 A1, 15.03.1981. SU 1817400 A1, 27.10.1996. SU 1105289 А, 30.07.1984.
Адрес для переписки:
400131, г.Волгоград, пр. Ленина, 28, ВолгГТУ, начальнику отдела интеллектуальной собственности Н.Н. Кондратьевой
|
(72) Автор(ы):
Соколов Г.Н. (RU), Цурихин С.Н. (RU), Лысак В.И. (RU), Зорин И.В. (RU)
(73) Патентообладатель(и):
Волгоградский государственный технический университет (ВолгГТУ) (RU)
|
(54) ПОРОШКОВАЯ ПРОВОЛОКА ДЛЯ НАПЛАВКИ
(57) Реферат:
Порошковая проволока может быть использована для электрошлаковой наплавки инструмента и др. изделий, работающих в условиях высокотемпературного износа при длительном температурно-силовом воздействии. Никелевая оболочка и алюминий в шихте взяты в количестве 70…75 мас.% и 10…12 мас.% соответственно, от массы порошковой проволоки. Шихта содержит компоненты в следующем соотношении, мас.%: циркон 1,5-2,5, цирконий 2,5-7,0, вольфрам 12,5-16,0, кремний 0,19-0,25, фтористый кальций 1,5-2,5, хром 12,5-16,0, молибден 4,0-10,0, ниобий 3,5-4,5, титан 0,2-0,3, тантал 2,5-7,0, графит 1,0-2,0, бор 0,1-0,2, алюминий 31,75-58,01. Проволока обеспечивает высокую твердость наплавленного металла при высоких температурах и стойкость его к разупрочнению при длительной выдержке при температуре 1200°С. 3 ил., 2 табл. 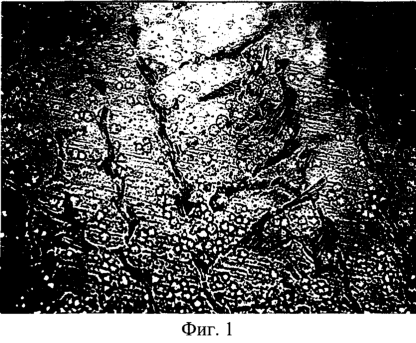
Изобретение относится к наплавочным материалам, в частности к порошковым проволокам преимущественно для электрошлаковой наплавки инструментов и изделий, работающих при температурах до 1200°С, в условиях высокотемпературного износа при длительном температурно-силовом воздействии (ТСВ).
Известен состав порошковой проволоки для наплавки (авторское свидетельство СССР №596404, В 23 К 35/368, опубл. Б.И. №9, 1978 г.) в состав шихты входят, мас.%: хром 24-30, марганец азотированный 0,3-1,5, фторополимеры 0,3-0,6, железный порошок 18-24, лигатура (Аl – V – Мо – Ti) 3-6, низкокремистый фторидный безокислительный флюс 3,6-8,4, двуокись циркония 3,6-6, редкоземельные металлы 0,03-0,3, оболочка из сплава на основе никеля – остальное.
Повышенная горячая твердость до температуры 800°С обеспечиваемого такой проволокой наплавленного металла достигается за счет небольшого содержания в никелевой матрице интерметаллидной фазы Ni3Al. С увеличением рабочей температуры свыше 800°С эксплуатационные свойства металла при ТСВ сильно снижаются.
Известна порошковая проволока для наплавки (авторское свидетельство СССР №312719, В 23 К 35/04, опубл. Б.И. №26, 1971 г.), содержащая никелевую оболочку и порошкообразную шихту, мас.%: алюминий 2-4, титан 1,5-4, хром 15-22, вольфрам 3-6, бор 0,01-0,03.
Такой состав порошковой проволоки обеспечивает наплавленный металл стойкий до температуры 850°С за счет легированного -твердого раствора, содержащего интерметаллидные фазы Ni3(Аl, Ti).
Основным недостатком такого состава порошковой проволоки является недостаточная износостойкость наплавленного металла при температурах свыше 850°С.
Наиболее близкой к заявленному составу является порошковая проволока для наплавки (авторское свидетельство СССР №1389147, В 23 К 35/368, опубл. Б.И. №9, 2002 г.), состоящая из никелевой оболочки и порошкообразной шихты, содержащей компоненты при следующем соотношении, мас.%: цирконий 1,61-6,78, вольфрам 5,88-8,47, кремний 1,61-5,08, фтористый кальций 4,25-4,84, хром 37,3-58,08, молибден 6,45-10,16, ниобий 3,22-5,08, титан 1,61-1,92, тантал 9,52-13,56, алюминий 1,61-1,69, графит 4,84-5,94. Данное соотношение компонентов в порошковой проволоке обеспечивает хорошие сварочно-технологические свойства. При таком содержании компонентов проволоки наплавленный металл имеет структуру сложнолегированного твердого раствора на основе никеля, карбидной эвтектики и труднорастворимых карбидов М23С6, М7С, содержащих вольфрам, молибден, хром, а также мелкодисперсных монокарбидов ZrC, NbC, TiC, TaC. Эксплуатационные свойства такого типа наплавленного металла при длительном ТСВ исчерпываются из-за усиливающегося влияния на его разупрочнение диффузионного фактора. Вследствие ускоренной диффузии примесных атомов легирующих элементов в никелевую матрицу и в результате длительной выдержки при температуре до 1200°С карбиды коагулируют и частично растворяются, что обуславливает разупрочнение наплавленного металла.
Задачей предлагаемого изобретения является получение такого состава порошковой проволоки, который обеспечивал бы наплавленный металл с матрицей на основе интерметаллида – никелида алюминия (Ni3Аl), диффузия легирующих элементов в котором замедлена, упрочненной труднорастворимыми при температуре до 1200°С субдисперсными фазами.
Технический результат заключается в получении повышенной, в сравнении с прототипом, высокотемпературной твердости наплавленного металла и его повышенной стойкости к разупрочнению при длительной выдержке при температуре 1200°С.
Технический результат достигается тем, что порошковая проволока для наплавки, преимущественно электрошлаковой, инструмента горячего деформирования, состоящей из никелевой оболочки и порошкообразной шихты, содержащей хром, молибден, ниобий, титан, тантал, алюминий, графит, цирконий, кремний, вольфрам, фтористый кальций, причем никелевая оболочка и алюминий в шихте взяты в количестве 70…75 мас.% и 10…12 мас.% соответственно от массы порошковой проволоки, а шихта дополнительно содержит бор и циркон при следующем соотношении компонентов порошковой проволоки, мас.%:
циркон |
1,5-2,5 |
цирконий |
2,5-7 |
вольфрам |
12,5-16 |
кремний |
0,19-0,25 |
фтористый кальций |
1,5-2,5 |
хром |
12,5-16 |
молибден |
4-10 |
ниобий |
3,5-4,5 |
титан |
0,2-0,3 |
тантал |
2,5-7 |
графит |
1-2 |
бор |
0,1-0,2 |
алюминий |
31,75-58,01 |
Отличительной особенностью изобретения является то, что никелевая оболочка в проволоке в количестве 70-75 мас.% и порошок алюминия в шихте в количестве 10-12 мас.% соответственно от массы порошковой проволоки берутся в стехиометрическом соотношении из расчета получения матрицы металла на основе интерметаллида – никелида алюминия Ni3Al ( ‘-фаза), а в шихту проволоки дополнительно вводятся бор, циркон (ZrSiO4).
С введением новых компонентов в шихту и при новом соотношении компонентов шихты обеспечиваются высокие сварочно-технологические свойства порошковой проволоки, при которых наблюдается устойчивый электрошлаковый процесс, наплавленный металл отлично формируется, не имеет дефектов в виде пор, трещин и шлаковых включений при достаточной для условий ТСВ высокотемпературной твердости при 1200°С и низкой склонности к разупрочнению при длительной выдержке при температуре 1200°С.
Никель и алюминий для получения твердого раствора на основе ‘-фазы вводятся в количестве, определяемом их атомным соотношением, которое составляет три. Соотношение никеля и алюминия более трех ведет к появлению избыточного количества -твердого раствора, что снижает высокотемпературную твердость наплавленного металла. При уменьшении этого соотношения менее трех количество ‘-фазы уменьшается, что также снижает высокотемпературную твердость.
Введение в состав порошковой проволоки бора позволяет повысить пластичность матрицы, предотвращает зарождение и рост межзеренных трещин, увеличивает когезию границ зерен, что обеспечивает пограничную передачу скольжения. Также возможно повышение износостойкости за счет образования боридов железа и хрома типа (Fe, Сr)2В, которые равномерно распределяются в матрице сплава. Кроме того, бор влияет на критическое соотношение легирующих карбидообразователей и углерода, что ускоряет образование специальных карбидов.
При содержании бора в шихте проволоки менее 0,1 мас.% его влияние на свойства наплавленного металла незначительно, а при увеличении его количества более 0,2 мас.% в наплавленном металле по границам зерен образуется боридная эвтектика, что снижает его стойкость к образованию трещин как в процессе наплавки, так и в условиях ТСВ.
Циркон введен с целью повышения межфазной активности шлака, что способствует улучшению смачиваемости жидким металлическим расплавом основного металла. При уменьшении содержания циркона в шихте проволоки менее 1,5 мас.% его влияние на межфазную активность шлака несущественно, а при увеличении его количества свыше 2,5 мас.% увеличивается окислительная способность шлака, что обуславливает низкий коэффициент перехода алюминия, титана, тантала, циркония и бора в наплавленный металл и ухудшается его формирование.
Цирконий, тантал, ниобий введены с целью увеличения износостойкости и сопротивления металла пластической деформации при рабочих температурах, так как они образуют субдисперсные монокарбиды, выделяющиеся преимущественно на дефектах кристаллической решетки. Цирконий в наплавленном металле также связывает кислород, что предотвращает окисление алюминия и способствует оксидному упрочнению. Он образует с никелем и алюминием интерметаллид Ni77Al22,65Zr0,25, способствующий улучшению пластичности наплавленного металла. Содержание циркония, ниобия и тантала установлено из расчета соотношения их с количеством углерода, при котором образуются монокарбиды ZrC, TaC, NbC. При увеличении содержания в шихте проволоки циркония, тантала и ниобия менее нижнего предела (2,5; 2,5 и 3,5 мас.% соответственно) моннокарбидов не наблюдается, а при увеличении их содержания (свыше 7; 7 и 4,5 мас.% соответственно) не обеспечивает существенного прироста высокотемпературной твердости наплавленного металла.
Хром введен с целью повышения жаростойкости наплавленного металла, так как при этом обеспечивается термодинамически стабильная, самозалечивающаяся пленка оксидов хрома. Кроме того, за счет образования хромитов (NiАl1,03Сr0,14 и CrAl1,19Ni0,04) достигается более высокая стойкость металла к разупрочнению при длительном ТСВ. При содержании хрома менее 12,5 мас.% оксидной пленки не образуется, а увеличение количества хрома более 16 мас.% не дает увеличение жаростойкости наплавленного металла.
Оставшееся после процесса образования интерметаллидов и карбидов легирующие Zr, Ti, Та, Nb, W, Mo, Cr образуют стабилизированный в равновесии с никелидом алюминия эвтектический твердый раствор с неупорядоченной кристаллической ГЦК решеткой на основе никеля (в количестве 5-10 об.%) или замещают в Ni2Аl позиции в подрешетках никеля или алюминия.
Вольфрам и молибден, входя в состав карбидов и твердого раствора, способствуют увеличению сопротивления металла пластической деформации при рабочих температурах. Их содержание установлено исходя из стехиометрического соотношения с углеродом для получения специальных карбидов.
Введение фтористого кальция компенсирует его недостаток в шлаке при ЭШН, так как содержание последнего снижается в процессе наплавки по причине избирательной кристаллизации в гарнисаж. Уменьшение содержания фтористого кальция менее 1,5 мас.% не приводит к заметному увеличению его в шлаке, а превышение содержания его в шихте более 2,5 мас.% ухудшает качество электрошлакового процесса.
На фиг.1 показана микроструктура наплавленного металла, полученного по заявляемому способу (×400); на фиг.2 – график влияния температуры испытаний на высокотемпературную твердость наплавленного металла; на фиг.3 – график влияния времени выдержки при 1200°С на высокотемпературную твердость наплавленного металла.
Порошковую проволоку получали известным способом.
Оболочку изготовляли из никелевой ленты НП2, в качестве шихты использовали смесь порошков хрома, молибдена, циркония, тантала, вольфрама, алюминия, титана, ниобия, кремния, фтористого кальция, графита, бора, циркона.
Диаметр проволоки 4 мм, коэффициент заполнения 39-52%. Изготовили три состава предлагаемой порошковой проволоки. Кроме того, были изготовлены порошковые проволоки с содержанием компонентов, выходящим за заявляемые пределы.
Наплавленный металл получали путем ЭШН на флюсе АНФ-6, режим ЭШН – ток постоянный, прямой полярности, силой 190-210 А, напряжение на шлаковой ванне 20-22 В. В указанном диапазоне режимов предлагаемая проволока показала отличные сварочно-технологические свойства, заключающиеся в устойчивом электрошлаковом процессе, отличном формировании наплавленного металла, отсутствии трещин и хорошей отделимости шлака. Наплавленный прелагаемой проволокой металл характеризовался повышенными свойствами при температурах до 1200°С. Состав предлагаемой проволоки с различным содержанием компонентов и результаты сравнительных испытаний представлены соответственно в таблицах 1 и 2.
Таблица 1 |
Состав шихты предлагаемой проволоки и результаты сравнительных испытаний |
Состав |
Содержание компонентов шихты, масс.% |
ZrSiO4 |
Zr |
W |
Si |
CaF2 |
Cr |
Мо |
Nb |
Ti |
Та |
С |
В |
Аl |
Предлагаемый |
1 |
2,2 |
5,87 |
14,95 |
0,23 |
2 |
14,99 |
7,86 |
4,15 |
0,26 |
5,89 |
1,66 |
0,16 |
39,78 |
2 |
1,5 |
2,5 |
12,5 |
0,19 |
1,5 |
12,5 |
4 |
3,5 |
0,2 |
2,5 |
1 |
0,1 |
58,01 |
3 |
2,5 |
7 |
16 |
0,25 |
2,5 |
16 |
10 |
4,5 |
0,3 |
7 |
2 |
0,2 |
31,75 |
4 |
1 |
1,94 |
11,63 |
0,187 |
1,2 |
11,63 |
2,97 |
3,49 |
0,19 |
1,94 |
0,97 |
0,099 |
62,654 |
5 |
3 |
7,28 |
16,66 |
0,31 |
2,8 |
17 |
10,55 |
4,94 |
0,31 |
7,38 |
2,29 |
0,28 |
27,2 |
Прототип |
– |
4,76 |
5,88 |
4,08 |
4,76 |
47,60 |
9,52 |
4,76 |
1,92 |
9,52 |
5,51 |
– |
1,69 |
Таблица 2 |
Состав |
Коэффициент заполнения ПП Кз, % |
Сварочно-технологические свойства |
Процесс |
Формирование наплавленного металла |
НВ при 20°С |
НВ при 1200°С |
НВ после выдержки при 1200°С четыре часа |
Предлагаемый |
1 |
45 |
устойчивый |
отличное |
310 |
140 |
120 |
2 |
39 |
устойчивый |
хорошее |
260 |
153 |
135 |
3 |
52 |
устойчивый |
хорошее |
510 |
125 |
100 |
4 |
29 |
выплески |
неудовлетворительное |
240 |
100 |
60 |
5 |
59 |
неустойчивый |
удовлетворительно |
590 |
80 |
35 |
Прототип |
42 |
устойчивый |
отличное |
300 |
135 |
50 |
Примечание: составы 1-3 находятся в пределах изобретения; состав 4 и 5 – за пределами изобретения. |
Исследование свойств наплавленного металла производили известными методами. Коррелирующую с сопротивлением пластической деформации высокотемпературную твердость измеряли на приборе ТШ-2, оборудованном электропечью, твердосплавным бериллизованным шариком диаметром 5 мм при нагрузке 7,35 кН.
Установлено, что при среднем содержании компонентов в составе предлагаемой порошковой проволоки наблюдаются улучшенные свойства наплавленного металла при ТСВ и температурах до 1200°С.
Структура наплавленного металла состоит из столбчатых выделений ‘-фазы, которые образуют каркасную структуру, а упрочняющие фазы располагаются как в приграничных объемах зерен, так и внутри их. Создается композиционная структура металла, состоящая из нескольких типов упрочняющих элементов (карбиды, бориды, интерметаллиды), ‘-фазы (твердого раствора), в котором имеется вязкая составляющая – -твердый раствор на основе никеля в количестве 5-10 об.% (фиг.1).
Содержание химических элементов с высокой энергией активации диффузии, а также матрицы сплава из никелида алюминия определяют низкую диффузионную подвижность примесных атомов в наплавленном металле, что позволяет ему длительно сохранять свойства и сопротивляться износу при высокотемпературном нагружении (фиг.2).
Формирование наплавленного металла и отделимость шлака отличные. Трещины отсутствуют.
Порошковые проволоки с соотношениями компонентов, выходящими за предлагаемые границы, показали более низкие свойства при неудовлетворительных результатах испытаний по сварочно-технологическим характеристикам.
Известная порошковая проволока (прототип) по сравнению с предлагаемой обеспечила наплавленный металл с пониженной твердостью при длительной выдержке с температурой 1200°С (фиг.3).
Использование предлагаемой порошковой проволоки дает в сравнении с известными порошковыми проволоками следующий положительный эффект:
1. Возможность использования порошковой проволоки для получения в наплавленном металле матрицы на основе Ni3Al, упрочненной субдисперсными фазами.
2. Повышается продолжительность использования наплавленных изделий при температурах до 1200°С в условиях высокотемпературного износа при длительном ТСВ.
3. Снижается цена материала за счет уменьшения содержания в порошковой проволоке дорогих и редких элементов.
Формула изобретения
Порошковая проволока для наплавки, преимущественно электрошлаковой, инструмента горячего деформирования, состоящая из никелевой оболочки и порошкообразной шихты, содержащей хром, молибден, ниобий, титан, тантал, алюминий, графит, цирконий, кремний, вольфрам, фтористый кальций, отличающийся тем, что никелевая оболочка и алюминий в шихте взяты в количестве 70-75 мас.% и 10-12 мас.% соответственно от массы порошковой проволоки, а шихта дополнительно содержит бор и циркон при следующем соотношении компонентов, мас.%:
циркон |
1,5-2,5 |
цирконий |
2,5-7,0 |
вольфрам |
12,5-16,0 |
кремний |
0,19-0,25 |
фтористый кальций |
1,5-2,5 |
хром |
12,5-16,0 |
молибден |
4,0-10,0 |
ниобий |
3,5-4,5 |
титан |
0,2-0,3 |
тантал |
2,5-7,0 |
графит |
1,0-2,0 |
бор |
0,1-0,2 |
алюминий |
31,75-58,01 |
РИСУНКИ
MM4A – Досрочное прекращение действия патента СССР или патента Российской Федерации на изобретение из-за неуплаты в установленный срок пошлины за поддержание патента в силе
Дата прекращения действия патента: 30.12.2006
Извещение опубликовано: 20.02.2008 БИ: 05/2008
|
|