|
(21), (22) Заявка: 2004113856/02, 05.05.2004
(24) Дата начала отсчета срока действия патента:
05.05.2004
(45) Опубликовано: 10.06.2005
(56) Список документов, цитированных в отчете о поиске:
SU 1523287 A1, 23.11.1989. RU 2145364 C1, 10.02.2000. GB 1440968 A, 30.06.1976. GB 910235 A, 14.11.1962.
Адрес для переписки:
236000, г.Калининград, Советский пр-т, 1, Калининградский государственный технический университет, патентный отдел, пат.пов.Т.Н.Бакряшовой, рег. № 532
|
(72) Автор(ы):
Тарасов А.Н. (RU), Тилипалов В.Н. (RU), Шевченко П.Р. (RU)
(73) Патентообладатель(и):
Калининградский государственный технический университет (RU)
|
(54) СПОСОБ ХИМИКО-ТЕРМИЧЕСКОЙ ОБРАБОТКИ ДЕТАЛЕЙ ЭЛЕКТРОМАГНИТНЫХ КЛАПАНОВ ИЗ МАГНИТОМЯГКОЙ СТАЛИ
(57) Реферат:
Изобретение относится к области металлургии, в частности к термической и химико-термической обработке деталей из магнитомягкой высокохромистой стали, используемой для изготовления корпусов, магнитопроводов, сердечников электромагнитных клапанов подачи рабочих газов в электрических реактивных двигателях малой тяги. Предложенный способ включает стабилизирующий отжиг, перед которым проводят механическую обработку деталей, в процессе отжига проводят карбонитрирование в древесноугольных смесях с активизирующими азото- и углеродсодержащими добавками со ступенчатым нагревом сначала при температуре выше точки Кюри 780-820°С в течение 3-4 часов, а затем при температуре ниже точки Кюри 680-700°С в течение 2-3 часов с охлаждением в упаковочном контейнере со скоростью 50-80°С/ч. В частных случаях выполнения изобретения в качестве механической обработки проводят абразивно-струйную обработку. Техническим результатом изобретения является повышение износостойкости деталей клапанных пар при сокращении трудоемкости, а также улучшение технологичности и увеличение ресурса работы электромагнитных малогабаритных электроклапанов при сохранении коррозионной стойкости. 1 з.п. ф-лы, 5 ил., 1 табл.
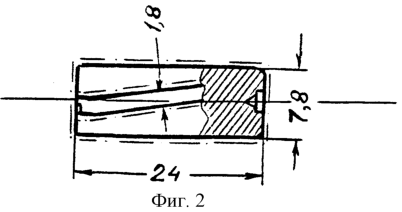
Изобретение относится к области металлургии, в частности к термической и химико-термической обработке деталей из магнитомягкой высокохромистой стали (16Х-ВИ), используемой для изготовления корпусов, магнитопроводов, сердечников электромагнитных клапанов подачи рабочих тел – газов в электрических реактивных двигателях малой тяги, а также технологический источник плазмы.
Известен способ изготовления и термической обработки деталей из магнитомягкой стали 16Х-ВИ, предусматривающий проведение вакуумного высокотемпературного отжига при 1175°С по ГОСТ 10160-75 и стабилизирующего вакуумного отжига при 525±25°С после механической обработки деталей по ОСТ 92-1311-77. Способ позволяет получать высокие магнитные свойства, минимальную коэрцитивную силу и максимальную магнитную индукцию, но низка износостойкость контактирующих в процессе работы деталей, как следствие, недостаточен ресурс работы изделий.
Известен способ, предусматривающий дополнительную зонную химико-термическую нитроцементацию уплотнительных полостей в активированной древесноугольной смеси и зонную лазерную обработку (а.с. №1523287, МПК В 23 К 26/00, С 21 D 1/78, опубл. 23.11.89, БИ№43).
Способ достаточно трудоемок, недостаточно технологичен, применим к ограниченным модификациям микроклапанов, неэффективен для клапанов с удлиненными сердечниками и значительным рабочим ходом.
Изобретение решает задачу повышения износостойкости деталей клапанных пар при сокращении трудоемкости и улучшения технологичности и увеличения ресурса работы электромагнитных малогабаритных электроклапанов при сохранении коррозионной стойкости.
Для обеспечения необходимого технического результата предлагается проводить перед стабилизирующим отжигом механическую обработку, а в процессе отжига проводить карбонитрирование в древесноугольных смесях с активизирующими азото- и углеродосодержащими добавками со ступенчатым нагревом сначала при температуре выше точки Кюри 780-820°С в течение 3-4 часов, а затем при температуре ниже точки Кюри 680-700°С в течение 2-3 часов. Охлаждение проводят в упаковочном контейнере со скоростью 50-80°С/ч. В качестве механической обработки используют абразивно-струйную обработку.
Сущность предложенного решения и влияние каждого из температурного и временного параметров состоит в том, что детали магнитных систем клапанов изготавливаются из отожженных прутков стали 16Х-ВИ механической обработкой в окончательные размеры с припуском на доводку полированием в пределах 10-15 мкм и при стабилизирующем отжиге нагреваются и карбонитрируются ступенчато при температурах выше, затем ниже точки Кюри. При этом скорость формирования износостойких карбонитридных слоев существенно повышается, достигая 35 – 45 мкм/ч при отсутствии тепловой и структурной деформации при подстуживании до второй ступени и охлаждении деталей после завершения химико-термической обработки в контейнере со скоростью не выше 80°С/ч.
На прилагаемых к описанию графических материалах и фотографиях изображено:
фиг.1 – микроструктура диффузионного слоя, полученного по предложенному способу; фиг.2 – эскиз сердечника электромагнитного клапана (схема насыщения рабочих поверхностей при карбонитрировании); фиг.3 – изменение износостойкости сердечников из стали 16Х-ВИ при обработке по известному (3) и разработанному способам (1, 2); фиг.4 – макроструктура карбонитрированного слоя на тороиде из стали 16Х-ВИ; фиг.5 – микроструктура карбонитридного слоя после обработки по режиму примера 2.
На первом этапе при 780-820°С в древесноугольных активированных смесях активно протекает диффузионное насыщение слоя углеродом и азотом, а на второй ступени при 680-700°С завершается формирование трехзонного слоя – поверхностного тончайшего “внутреннего” окисления толщиной не более 5-7 мкм, далее светлотравящегося слоя карбонитридов (Fe, Сr)7(NС)3 и переходного темнотравящегося с содержанием углерода выше 1,2 мас.% с мелкодисперсными карбидами (Fe, Сr)3(NC), микротвердостью Н0,5н=540-720 с плавным переходом к мягкой основе Н0,5н=156-167.
Время выдержки на каждой из ступеней нагрева и суммарное при проведении карбонитрирования высокохромистой магнитомягкой стали 16Х-ВИ выбрано исходя из условия формирования диффузионных износостойких слоев толщиной 200-300 мкм, обеспечивающих минимальное влияние на магнитные свойства основного металла, сохраняющиеся на уровне требуемых по стандартам. Вместе с тем формирование поверхностного слоя более магнитотвердого по сравнению с сердцевиной улучшает условия движения сердечников микроклапанов в их магнитомягком корпусе, что приводит к стабильности работы клапанов и повышает ресурс их работы до 107-108 циклов, на порядок выше, чем при изготовлении и обработке по известным и стандартизированным схемам термической обработки.
Изобретение иллюстрируется практическими примерами осуществления способа обработки в условиях мелкосерийного производства электрических реактивных двигателей малой тяги и технологических источников плазмы с электромагнитными клапанами подачи рабочих тел – инертных газов: азота, аргона, ксенона и других газовых смесей.
При практическом осуществлении способа детали микроклапанов сердечники, якоря, корпуса магнитопроводов изготавливали из прутков стали 16Х-ВИ по ГОСТ 10994, ГОСТ 10160-75. Для проведения карбонитрирования в малоэнергоемких печах СНОЛ-1,6.2,5.1/9 и ПЛ-12 с упаковкой деталей по схеме контейнер в контейнере использовали составы на основе активированного и гранулированного древесного угля по ГОСТ 20 464-77, ГОСТ 62-17-77 с введением активирующих азотоуглеродосодержащих добавок карбамида по ГОСТ 6691-77 и трилона-Б по ГОСТ 10652-737.
Конкретные примеры осуществления способа
Пример 1. Сердечники электромагнитного клапана изготавливали из горячекатаных отожженных прутков стали 16Х-ВИ диаметром 16 мм в окончательный размер с припуском на притирку по цилиндрической части 5-6 мкм на сторону. Карбонитрирование проводили по 16 деталей в садке с упаковкой в состав, содержащий 80% гранулированного древесного угля 12% карбамида и 8% трилона Б, с укладкой деталей в малый контейнер, установкой его в контейнер с засыпкой из отработанного карбюризатора.
После прогрева садки до температуры 780°С и выдержки в течение 4 часов снижали температуру до 680°С и выдерживали садку в течение 3 часов, дальнейшее охлаждение вели со скоростью 80°С/ч и при температуре 120°С выгружали контейнер из печи.
Обработка позволила сформировать на рабочих поверхностях сердечников износостойкий слой толщиной 280-300 мкм, имеющий износостойкость при контактном износе в три раза выше, чем при обработке по известной технологии высокотемпературного и стабилизирующего вакуумного отжига. После притирки, полирования по торцевым и боковым поверхностям со снятием поверхностного окисленного слоя 4-5 мкм электромагнитные клапаны с названными сердечниками имели ресурс более 107 циклов, обеспечивали надежную работу без зависаний и надиров, характерных для обычно изготавливаемых по серийной технологии. Одновременно сократилась в 1,5 раза трудоемкость изготовления и термической обработки деталей.
Пример 2. Корпуса электромагнитных клапанов из стали 16Х-ВИ подвергали после токарной механической обработки с классом чистоты обработки Ra=1,25 мкм химико-термической обработке карбонитрированию в активированной древесноугольной смеси из березового древесного угля с добавками трилона-Б и карбамида с нагревом и выдержкой вначале при 820°С в течение 3 часов, а затем ниже точки Кюри при 700°С в течение 2 часов с охлаждением в печи, в контейнере со скоростью 50°С/ч до 80°С и выгрузкой на воздух.
Толщина карбонитридного слоя с микротвердостью Н0,5н=660-720 составила 320-330 мкм, микроструктура сердцевины осталась крупнозернистой, что обеспечивало оптимальные магнитные свойства основного металла на уровне Н коэрцитивную силу Нс=35-40 А/м и магнитную индукцию на уровне B2500=1,30-1,35 Тл. При структуре основы крупнозернистого феррита в структуре диффузионного карбонитридного слоя сформированы светлотравящаяся область карбидов (Fe, Сr)7С3, (Fe, Сr)7(NС)3 с подслоем -фазы и карбонитридным (Fe, Сr)3(N, С)3 слоем. В таблице приведены состав и свойства диффузионных слоев на стали 16Х-ВИ при обработке по предложенному и известному способам.
Способ и режим химико-термической обработки х) |
Толщина слоя, мкм |
Содержание в слое 100 мкм, % |
Микротвердость, Н0,5Н |
Магнитные свойства |
Тн, I ступ., °С |
выд., ч |
Тн, II ступ., °С |
выд., ч |
Нс, А/м |
В2500, Тл |
С |
N |
Предложенный |
1. |
780 |
3,0 |
680 |
2,0 |
290 |
1,45 |
0,17 |
690 |
56 |
1,11 |
2. |
820 |
4,0 |
700 |
3,0 |
330 |
1,55 |
0,18 |
710 |
48 |
1,19 |
3. |
800 |
3,0 |
700 |
3,0 |
300 |
1,61 |
0,14 |
720 |
57 |
1,14 |
4. |
820 |
3,5 |
690 |
2,5 |
280 |
1,43 |
0,17 |
710 |
47 |
1,21 |
Известный |
1150 |
0,5 |
Лазерная 1070 |
Отпуск 2 часа |
120 зонная |
1,11 |
0,03 |
580 |
33 |
1,20 |
х) Карбюризатор на основе древесного угля с добавкой карбоната натрия и азотосодержащих – карбамида и трилона-Б, подготовка поверхности при восстановлении абразивно-струйной обработкой с шероховатостью Ra=1,25 мкм (№4), токарной механической обработкой (№№1-3). |
Установлено также, что карбонитридные диффузионные слои после карбонитрирования по предложенной технологии имеют высокую коррозионную стойкость в атмосфере 98% влажности, при этом после доводки по рабочей поверхности на глубину 3-5 мкм ресурс работы в составе клапанов достигает 108 циклов против 106 циклов для деталей, обработанных по известной технологии. Исключено зонное выкрашивание по тонким уплотнительным буртикам, характерное для якорей микроклапанов при нитроцементации и лазерной закалкой с оплавлением.
Пример 3. Якоря цилиндрические диаметром 12 мм из стали 16Х-ВИ из отожженных прутков диаметром 16 мм механически обрабатывали на токарных станках с формированием по рабочим поверхностям концентрического микрорельефа классом чистоты Ra=1,10 мкм, а затем карбонитрировали в процессе стабилизирующего отжига в активированных древесно-угольных смесях с добавкой активаторов – карбамида, трилона-Б, карбоната натрия. Без введения добавок эффективное насыщение слоя углеродом и азотом для сталей с содержанием хрома выше 13% практически затруднено. Нагрев садки вначале проводили при 800°С с выдержкой 3,5 часа, затем снижали температуру ниже точки Кюри и выдерживали садку при 690°С в течение 3 часов с последующим охлаждением со скоростью 70°С/ч.
Диффузионный слой толщиной 220 мкм с высоким содержанием карбонитридов был однороден и равномерен по рабочим поверхностям. Микротвердость составила Н0,5H=735-740 и после притирки и доводки со снятием микронеровностей и слоя внутреннего окисления 7-10 мкм якоря имели высокие магнитные свойства в пределах требований стандарта, а также износостойкость при ресурсных испытаниях на уровне 10 циклов или на порядок выше известного способа упрочнения.
После ресурсных наработок проводилось восстановление пары сердечник, якорь, корпус клапана путем повторного карбонитрирования якорей и сердечников по разработанной технологии. Перед химико-термической обработкой проводили опескоструивание – абразивно-струйную обработку рабочих поверхностей дисперсным карбидом бора В4С по рабочим поверхностям. Карбонитрирование по вышеприведенному режиму позволило получить диффузионный слой суммарной толщиной более 240 мкм с повышенной износостойкостью, ресурс работы пары трения повысился в 2 раза.
Таким образом, как показали проведенные эксперименты и производственные испытания, разработанный способ химико-термической обработки деталей электромагнитных клапанов из высокохромистой магнитомягкой стали 16Х-ВИ, при минимальных затратах на электроэнергию, вспомогательные материалы и при снижении трудоемкости обработки, позволяет существенно повысить надежность и ресурс работы клапанов подачи рабочих тел для электрических реактивных двигателей малой тяги и технологических источников плазмы.
Формула изобретения
1. Способ химико-термической обработки деталей электромагнитных клапанов из магнитомягкой стали, включающий стабилизирующий отжиг, отличающийся тем, что перед отжигом проводят механическую обработку, в процессе отжига проводят карбонитрирование в древесноугольных смесях с активизирующими азото- и углеродсодержащими добавками со ступенчатым нагревом сначала при температуре выше точки Кюри 780-820°С в течение 3-4 ч, а затем при температуре ниже точки Кюри 680-700°С в течение 2-3 ч с охлаждением в упаковочном контейнере со скоростью 50-80°С/ч.
2. Способ по п.1, отличающийся тем, что в качестве механической обработки осуществляют абразивно-струйную обработку.
РИСУНКИ
|
|