|
(21), (22) Заявка: 2004100463/02, 05.01.2004
(24) Дата начала отсчета срока действия патента:
05.01.2004
(45) Опубликовано: 20.05.2005
(56) Список документов, цитированных в отчете о поиске:
RU 2190044 C1, 27.09.2002. RU 2066716 C1, 20.09.1996. SU 1180409 А, 23.09.1985. JP 57-210996 A, 24.12.1982.
Адрес для переписки:
302019, г.Орел, ул. Ген. Родина, 69, ОГАУ, проректору по НР В.Т.Лобкову
|
(72) Автор(ы):
Кузнецов Ю.А. (RU), Батищев А.Н. (RU), Студенников Н.Н. (RU), Гринев А.Ю. (RU)
(73) Патентообладатель(и):
Орловский государственный аграрный университет (ОГАУ) (RU)
|
(54) УСТРОЙСТВО ДЛЯ МИКРОДУГОВОГО ОКСИДИРОВАНИЯ МЕТАЛЛОВ И ИХ СПЛАВОВ
(57) Реферат:
Изобретение относится к оборудованию для электролитической обработки поверхности металлов и их сплавов путем оксидирования для повышения износостойкости, коррозионностойкости, теплостойкости, получения декоративных и электроизоляционных покрытий и может быть использовано в машиностроении, авиационной, химической промышленности, медицине, а также в ремонтном производстве при упрочнении и восстановлении деталей. Устройство содержит электроды, в качестве одного из которых использована оксидируемая деталь, источник питания, электролитическую ванну. Второй электрод выполнен в виде стакана с рубашкой охлаждения с циркулирующим в ней хладагентом, при этом по внутренней поверхности электрода и внешней поверхности рубашки охлаждения установлены перфорированные трубки, предназначенные для барботирования сжатым воздухом электролита в зоне оксидирования. Изобретение позволяет повысить производительность микродугового оксидирования и физико-механических свойств формируемого покрытия. 3 ил., 1 табл.
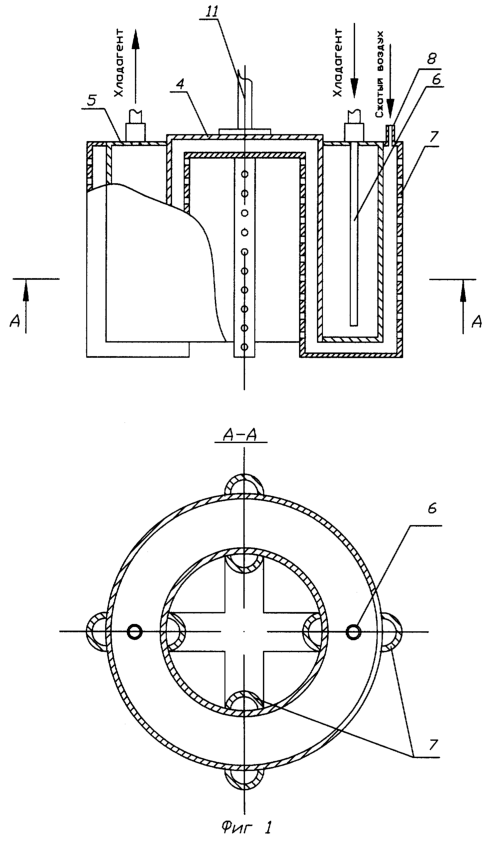
Изобретение относится к оборудованию для электролитической обработки поверхности металлов и их сплавов путем оксидирования для повышения износостойкости, коррозионностойкости, теплостойкости, получения декоративных и электроизоляционных покрытий и может быть использовано в машиностроении, авиационной, химической промышленности, медицине, а также в ремонтном производстве при упрочнении и восстановлении деталей.
Известно устройство для микродугового оксидирования металлов и их сплавов, содержащее электроды, источник питания, систему прокачки электролита, ванну для электролита, воронку с фильтром, соединенную с ванной для электролита посредством трубопровода, при этом в качестве одного из электродов использована оксидируемая деталь, а в качестве второго – сопло-электрод, закрепленный на траверсе штанги с возможностью перемещения в вертикальной и горизонтальной плоскостях, а порошковый питатель закреплен на сопле-электроде [1].
При оксидировании детали типа “вал” оксидируемая деталь установлена между воронкой и соплом-электродом. При оксидировании детали типа “полый цилиндр” сопло-электрод выполнен в виде спрейера, при этом оксидируемая деталь установлена на оправке с возможностью вращательного и возвратно-поступательного движения в вертикальной плоскости, а сопло-электрод установлен внутри оксидируемой детали.
Однако известное устройство микродугового оксидирования обладает невысокой производительностью.
Задачей изобретения является повышение производительности микродугового оксидирования и физико-механических свойств формируемого покрытия.
Поставленная задача достигается благодаря тому, что в известном устройстве для микродугового оксидирования металлов и их сплавов, содержащем электроды, в качестве одного из которых использована оксидируемая деталь, источник питания, электролитическую ванну, согласно изобретению второй электрод выполнен в виде стакана с рубашкой охлаждения с циркулирующим в ней хладагентом, при этом по внутренней поверхности электрода и внешней поверхности рубашки охлаждения установлены перфорированные трубки, предназначенные для барботирования сжатым воздухом электролита в зоне оксидирования.
Сущность изобретения поясняется чертежами, где на фиг.1 изображена конструкция электрода; на фиг.2 – устройство для микродугового оксидирования поверхности деталей типа “вал”; на фиг.3 – устройство для микродугового оксидирования поверхности деталей типа “полый цилиндр”.
Устройство содержит источник питания и блок управления 1 процессом микродугового оксидирования, электролитическую ванну 2. Первым электродом является оксидируемая деталь 3 типа “вал”, а вторым – электрод, выполненный в виде стакана 4 с рубашкой охлаждения 5, в котором циркулирует хладагент. Через штуцер 6 в рубашку охлаждения 5 поступает хладагент. Применение штуцера 6 обеспечивает равномерную циркуляцию хладагента в рубашке охлаждения 5. По внутренней поверхности электрода 4 и внешней поверхности рубашки охлаждения 5 установлены перфорированные трубки 7 для обеспечения непрерывного барботирования сжатым воздухом электролита в зоне оксидирования, пересекающиеся и сообщающиеся между собой на днище электрода 4 под углом 90°. Воздух подается через штуцер 8 компрессором (на чертеже не показан) (фиг.1).
Для обработки детали 3 типа “вал” электролитическая ванна 2 снабжена фиксирующей втулкой 9. Электрод 4 устанавливают во фторопластовой пластине 10 кронштейном 11 так, чтобы внутренняя поверхность электрода 4 и внешняя поверхность детали 3 были равноудалены. Фиксирующая втулка 9, в которой закрепляется деталь 3, изолирована от электролитической ванны 2 фторопластовой прокладкой 12 (фиг.2).
При обработке детали 13 типа “полый цилиндр” ее помещают в электролитическую ванну 2 и закрепляют в фиксирующей втулке 9. Электрод 4 установлен внутри детали 13 так, чтобы его внешняя поверхность и внутренняя поверхность детали 13 были равноудалены (фиг.3).
Устройство для микродугового оксидирования металлов и их сплавов работает следующим образом.
Оксидируемую деталь 3 (фиг.2) типа “вал” устанавливают в фиксирующую втулку 9, к ней присоединяется первый контакт источника питания 1, а второй – к электроду 4. Микродуговые разряды формируются между электродом 4 и поверхностью детали 3. В рубашку охлаждения 5 (фиг.1) через штуцер 6 системой подачи хладагента (на чертеже не показана) подается хладагент. Одновременно с подачей хладагента включается компрессор (на чертеже не показан) и сжатый воздух через штуцер 8 (фиг.1) подается в перфорированные трубки 7. Для уменьшения энергетических затрат и достижения максимально локального процесса фиксирующая втулка 9 изолирована от электролитической ванны 2 фторопластовой прокладкой 12 (фиг.2).
Деталь 13 (фиг.3) типа “полый цилиндр” устанавливают в фиксирующей втулке 9. Электрод 4 установлен внутри детали 13 так, чтобы внутренняя поверхность детали 13 и внешняя поверхность электрода 4 были равноудалены. Первый контакт источника питания 1 присоединен к фиксирующей втулке 9, а второй – к электроду 4. Микродуговые разряды формируются между электродом 4 и внутренней поверхностью детали 13.
Применение электрода 4 с рубашкой охлаждения 5 позволяет отказаться от водяной рубашки охлаждения электролитической ванны. А использование в рубашке охлаждения 5 хладагента типа “Фреон-12” [2] дает возможность существенно снизить рабочую температуру электролита в зоне оксидирования. Снижение температуры электролита позволяет значительно увеличить плотность тока, что приводит к уменьшению продолжительности микродугового оксидирования, тем самым возрастает производительность процесса. Барботирование сжатым воздухом электролита способствует стабилизации температурного режима и увеличивает интенсивность образования на поверхности обрабатываемой детали мицелл геля оксидного покрытия, тем самым достигается снижение пористости и увеличение износостойкости получаемого покрытия (см. таблицу).
Показатели |
Величина показателей |
Прототип |
Предлагаемое устройство |
Температура электролита, °С |
20-22 |
7-10 |
Плотность тока, А/дм2 |
22 |
28 |
Толщина упрочненного слоя, мкм |
100 |
195 |
Пористость, % |
23-34 |
12-15 |
Износостойкость, % |
105 |
135 |
Продолжительность эксперимента, мин |
80 |
60 |
Скорость формирования покрытия, мкм/мин |
1,25 |
3,25 |
Как видно из таблицы, применение предлагаемого устройства позволяет увеличить на 21,4% – плотность тока, на 49% – толщину, на 22% – износостойкость, на 61% – скорость формирования покрытия упрочненного слоя.
Использование предлагаемого устройства для микродугового оксидирования металлов и их сплавов позволяет увеличить производительность микродугового оксидирования поверхностей деталей различной конфигурации и размеров за счет применения электрода, снабженного рубашкой охлаждения с циркулирующим в ней хладагентом, и регулирование режимов микродугового оксидирования.
Источники информации
1. Патент РФ 2190044, МПК C 25 D 11/02, 2002 г., прототип.
2. 3еликовский И.Х., Каплан Л.Г. Малые холодильные установки. М.: Пищевая промышленность, 2001 г.
Формула изобретения
Устройство для микродугового оксидирования металлов и их сплавов, содержащее электроды, в качестве одного из которых использована оксидируемая деталь, источник питания, электролитическую ванну, отличающееся тем, что второй электрод выполнен в виде стакана с рубашкой охлаждения с циркулирующим в ней хладагентом, при этом по внутренней поверхности электрода и внешней поверхности рубашки охлаждения установлены перфорированные трубки, предназначенные для барботирования сжатым воздухом электролита в зоне оксидирования.
РИСУНКИ
MM4A – Досрочное прекращение действия патента СССР или патента Российской Федерации на изобретение из-за неуплаты в установленный срок пошлины за поддержание патента в силе
Дата прекращения действия патента: 06.01.2006
Извещение опубликовано: 20.09.2007 БИ: 26/2007
|
|