(21), (22) Заявка: 2003103261/06, 03.02.2003
(24) Дата начала отсчета срока действия патента:
03.02.2003
(43) Дата публикации заявки: 10.09.2004
(45) Опубликовано: 10.04.2005
(56) Список документов, цитированных в отчете о поиске:
SU 1250827 A1, 15.08.1986. SU 453554 A, 30.05.1975. RU 2137053 C1, 10.09.1999. JP 57150799 A, 17.09.1982.
Адрес для переписки:
607190, Нижегородская обл., г. Саров, пр-кт Мира, 37, ФГУП РФЯЦ-ВНИИЭФ, начальнику ОПИНТИ А.А. Кимачеву или зам. начальника ОПИНТИ Н.А. Волковой
|
(72) Автор(ы):
Ермичев С.Г. (RU)
(73) Патентообладатель(и):
Российская Федерация в лице Министерства Российской Федерации по атомной энергии – Минатом РФ (RU), Федеральное государственное унитарное предприятие Российский федеральный ядерный центр – Всероссийский научно-исследовательский институт экспериментальной физики ФГУП РФЯЦ ВНИИЭФ (RU)
|
(54) СПОСОБ ИЗГОТОВЛЕНИЯ ТЕПЛООБМЕННОЙ ТРУБЫ
(57) Реферат:
Изобретение предназначено для применения в теплотехнике, а именно может быть использовано при производстве оребренных труб холодильных аппаратов или контейнеров, предназначенных для хранения отработавшего топлива ядерных реакторов, а также других материалов или объектов, являющихся мощными источниками тепла. Способ изготовления теплообменной трубы заключается во вводе внутрь трубчатой заготовки сердечника и ребер, причем на внутренней поверхности заготовки и внешней поверхности заранее выполненного полым сердечника выполняют продольные пазы, а ребра, выполненные отдельно от сердечника, изготавливают в виде полосы, состоящей из двух слоев, соединенных между собой по краям в продольном направлении, или в виде полых труб овального сечения, которые перед установкой в пазы деформируют, создавая внутри избыточное давление, после чего устанавливают в пазы и сбрасывают давление, при этом давление выбирают таким образом, чтобы относительное изменение максимального габаритного размера ребра в поперечном направлении составляло:
  min,
где – относительное изменение максимального габаритного размера ребра в поперечном направлении,
min – минимальное значение относительного изменения максимального габаритного размера ребра в поперечном направлении, при котором обеспечивается сборка трубы и создание упругих деформаций в ребрах. Изобретение позволяет обеспечить эффективный теплоотвод в крупногабаритных трубах с внутренним оребрением с одновременным упрощением технологии их изготовления. 1 ил.
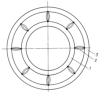
Изобретение относится к теплотехнике и может быть использовано при производстве оребренных труб, холодильных аппаратов или контейнеров, предназначенных для хранения отработавшего топлива ядерных реакторов, а также других материалов или объектов, являющихся мощными источниками тепла.
Известен способ изготовления оребренной поверхности (патент РФ № 2141615 от 14.04.98, F 28 F 3/02, опубликован 20.11.99. Бюл. № 32). Способ включает укладывание дисков оребрения в кондуктор, предварительное охлаждение трубы в среде жидкого азота, затем введение ее во внутренние отверстия дисков оребрения и нагрев теплом окружающей среды, после чего оребренную поверхность вынимают из кондуктора в виде готового изделия.
При нагреве трубы теплом окружающей среды происходит ее тепловое расширение, в результате чего обеспечивается необходимый контакт между трубой и ребрами.
Недостатками данного способа являются:
1) существенные технологические трудности, возникающие при охлаждении жидким азотом крупногабаритных труб (диаметром порядка 1…3 м и длиной 2…4 м);
2) невозможность изготовления трубы с продольными ребрами.
Известен способ изготовления теплообменной трубы с внутренним оребрением (а. с. № 1250827 от 25.02.85, F 28 F 1/40, В 21 С 37/22, опубликован 15.08.86. Бюл. № 30). По данному способу внутрь трубчатой заготовки вводят оребренный сердечник с диаметром описанной окружности, превышающим внутренний диаметр заготовки. Предварительно сердечник охлаждают жидким азотом до 100-140 К, а заготовку нагревают до 570-1130 К. После введения сердечника внутрь заготовки последнюю фиксируют в зажимах и выдерживают до выравнивания температур, в результате чего происходит термическая деформация, обеспечивающая необходимый контакт между сердечником и трубчатой заготовкой.
Недостатками данного способа являются:
1) существенные технологические трудности, возникающие при охлаждении жидким азотом до 100-140 К и нагревании до 570-1130 К крупногабаритных труб (диаметром порядка 1…3 м и длиной 2…4 м);
2) ограничение времени сборки (не более 30 с), вызванное выравниванием температур сердечника и заготовки.
Способ изготовления теплообменной трубы с внутренним оребрением по а. с. № 1250827 выбран в качестве прототипа.
Задачей предлагаемого изобретения является обеспечение эффективного теплоотвода в крупногабаритных трубах с внутренним оребрением с одновременным упрощением технологии их изготовления.
Технический результат выражается в создании упруго-напряженного состояния ребер, исключающего наличие зазоров между сердечником и трубчатой заготовкой. Этим самым обеспечивается необходимая тепловая проводимость между контактирующими деталями, способствующая эффективной передаче тепла. Способ создания упруго-напряженного состояния ребер путем их предварительного деформирования перед установкой за счет создания в них избыточного давления позволяет повысить технологичность производства, снизить трудоемкость и затраты при изготовлении крупногабаритных теплообменных труб.
Технический результат достигается за счет того, что в способе изготовления теплообменной трубы путем ввода внутрь трубчатой заготовки сердечника и ребер на внутренней поверхности заготовки и внешней поверхности заранее выполненного полым сердечника выполняют продольные пазы, а ребра, выполненные отдельно от сердечника, изготавливают в виде полосы, состоящей из двух слоев, соединенных между собой по краям в продольном направлении или в виде полых труб овального сечения, которые перед установкой в пазы деформируют, создавая внутри избыточное давление, после чего устанавливают в пазы и сбрасывают давление, при этом давление выбирают таким образом, чтобы относительное изменение максимального габаритного размера ребра в поперечном направлении составляло:
  min,
где – относительное изменение максимального габаритного размера ребра в поперечном направлении,
min – минимальное значение относительного изменения максимального габаритного размера ребра в поперечном направлении, при котором обеспечивается сборка теплообменной трубы и создание упругих деформаций в ребрах.
Выборка зазоров между сопрягаемыми деталями и формирование в ребрах упруго-напряженного состояния обеспечивается за счет деформирования ребер перед установкой путем создания внутри избыточного давления, которое затем стравливается после установки ребер. Выполнение этих мероприятий позволяет создать необходимый контакт между сердечником, ребрами и трубчатой заготовкой, что, в свою очередь, позволяет обеспечить эффективный теплообмен между сердечником и заготовкой и повысить технологичность изготовления оребренной трубы. Способ поясняется чертежом 1, где:
1 – сердечник полый,
2 – ребро,
3 – трубчатая заготовка,
4 – продольный паз на внешней поверхности сердечника,
5 – продольный паз на внутренней поверхности заготовки.
Теплообменную трубу с внутренним оребрением изготавливают из трубчатой заготовки 3, сердечника 1 и ребер 2.
Процесс изготовления теплообменной трубы выполняют в следующей последовательности.
Предварительно устанавливают трубчатую заготовку 3. Затем вводят внутрь заготовки 3 сердечник 1. Далее ориентируют трубчатую заготовку 3 относительно сердечника 1 так, чтобы положение продольных пазов 4 и 5 совпадало в радиальном направлении. Затем деформируют ребра 2 путем создания в них избыточного давления, после чего вводят их в пазы 4 и 5. После этого сбрасывают давление из ребер. Во время сбрасывания давления ребра 2 стремятся принять первоначальную форму, при этом исчезают зазоры между ребрами 2, сердечником 1 и заготовкой 3 и возникает упруго-напряженное состояние ребер, обеспечивающее необходимый контакт и тепловую проводимость между сопрягаемыми деталями.
В качестве подтверждения промышленной применимости рассмотрим пример теплообменной трубы с внутренним оребрением.
Материал сердечника 1 и трубчатой заготовки 3 – сталь 20, а ребер 2 – сталь 45.
Значения размеров деталей:
– Наружный диаметр сердечника – 89 мм,
– Внутренний диаметр трубчатой заготовки – 194 мм,
– Глубина пазов на сердечнике и трубчатой заготовке – 2 мм,
– Максимальный габаритный размер ребра в поперечном сечении в исходном состоянии 57,1 мм.
Ребра представляли собой полосу, состоящую из двух слоев, соединенных между собой по краям в продольном направлении. Толщина каждого слоя составляла 0,5 мм, а общее количество ребер – 8 шт.
При сборке сначала установили сердечник, затем трубчатую заготовку, при этом обеспечили совпадение положения пазов в радиальном направлении и равномерность зазора между наружной поверхностью сердечника и внутренней поверхностью трубчатой заготовки. Далее создали в ребрах давление 1,2 кГс/см2 и установили их в пазы, после чего давление сбросили.
Выполнение описанных выше операций позволило создать эффективную тепловую проводимость между сердечником и трубчатой заготовкой. При этом существенно упростилась технология, что привело к снижению трудоемкости и затрат изготовления оребренной трубы.
Формула изобретения
Способ изготовления теплообменной трубы путем ввода внутрь трубчатой заготовки сердечника и ребер, отличающийся тем, что на внутренней поверхности заготовки и внешней поверхности заранее выполненного полым сердечника выполняют продольные пазы, а ребра, выполненные отдельно от сердечника, изготавливают в виде полосы, состоящей из двух слоев, соединенных между собой по краям в продольном направлении или в виде полых труб овального сечения, которые перед установкой в пазы деформируют, создавая внутри избыточное давление, после чего устанавливают в пазы и сбрасывают давление, при этом давление выбирают таким образом, чтобы относительное изменение максимального габаритного размера ребра в поперечном направлении составляло
  min,
где – относительное изменение максимального габаритного размера ребра в поперечном направлении,
min – минимальное значение относительного изменения максимального габаритного размера ребра в поперечном направлении, при котором обеспечивается сборка трубы и создание упругих деформаций в ребрах.
РИСУНКИ
MM4A – Досрочное прекращение действия патента СССР или патента Российской Федерации на изобретение из-за неуплаты в установленный срок пошлины за поддержание патента в силе
Дата прекращения действия патента: 04.02.2007
Извещение опубликовано: 20.02.2008 БИ: 05/2008
|